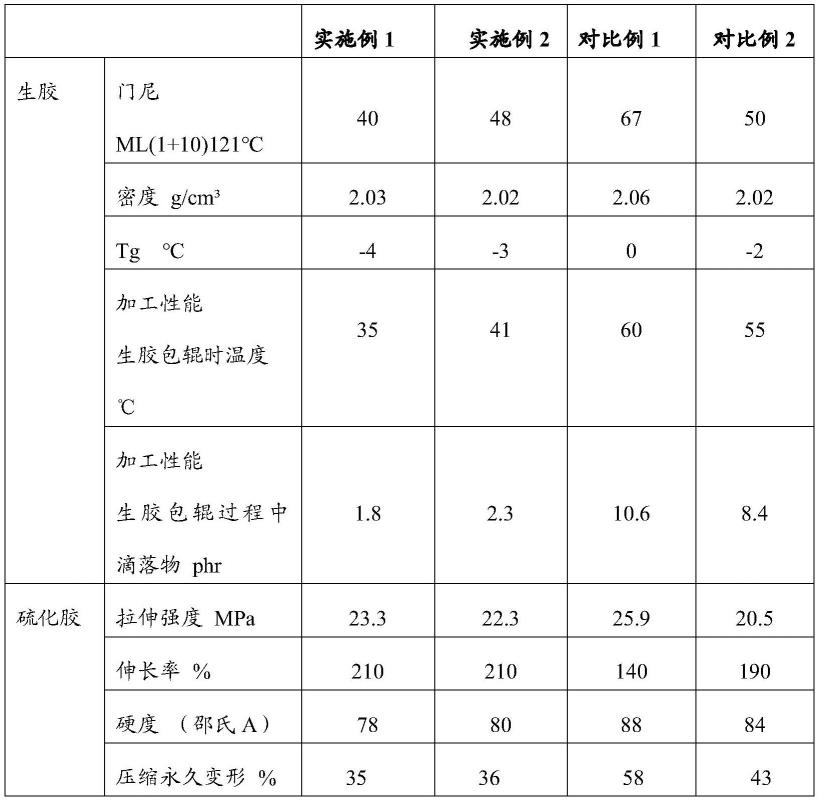
1.本发明属于含氟材料技术领域,具体涉及一种全氟醚弹性体乳液,以及乳液的制备方法,同时还涉及由该乳液制备得到的全氟醚弹性体。
背景技术:2.全氟醚弹性体由美国杜邦公司于1968年首先研制成功,是一种完全不含c-h键的弹性体,主要由四氟乙烯、全氟烷基乙烯基醚为单体,使用含氰基全氟烯烃、(全氟)苯氧基烯烃、含溴全氟烯烃、含碘全氟烯烃为硫化点单体共聚而成。全氟醚弹性体如其名称所示那样,聚合物中所有碳原子上的氢原子全被氟原子所取代,可耐已知溶剂1600余种,且可在300℃甚至320℃高温领域长期使用。
3.目前国内全氟醚弹性体尚处于中试或小批量生产阶段,虽然填补了该领域国内的空白,但是制得的全氟醚弹性体的力学性能指标与国外尚有一定的差距。例如存在硫化胶硬度偏高,伸长率偏低,耐高温永久压缩形变偏大等缺陷。
4.公开号为cn106317290a的专利申请中公开了一种全氟醚弹性体的制备方法及所得的全氟醚弹性体,该全氟醚弹性体本身硬度较高,加工翻炼困难,硫化胶配方中加入20phr的炭黑硫化后氟橡胶硬度(邵氏a)接近80,填料的填充率低。
5.因此,需要对目前的全氟醚弹性体制备进行研究改进,获得性能更佳的全氟醚弹性体,以扩大全氟醚橡胶的推广应用。
技术实现要素:6.针对现有技术存在的不足,本发明的目的在于提供一种全氟醚弹性体乳液及其制备方法,同时还提供了一种由制得的乳液制备而成的全氟醚弹性体。制得的全氟醚弹性体硬度低,填料填充率高,加工性能好。
7.为达此目的,本发明采用以下技术方案。
8.第一方面,本发明提供了一种全氟醚弹性体乳液的制备方法,共聚单体在水介质中,在引发剂、链转移剂、乳化剂的存在下进行乳液聚合反应制备全氟醚弹性体乳液;所述共聚单体包括初始混合单体、第一补加混合单体和第二补加混合单体;
9.所述初始混合单体包括四氟乙烯(tfe)和全氟甲基乙烯基醚(pmve);所述第一补加混合单体包括硫化点单体(csm)、四氟乙烯和全氟甲基乙烯基醚;所述第二补加混合单体包括硫化点单体、四氟乙烯、全氟甲基乙烯基醚和全氟氧杂烷基乙烯基醚(poave);
10.所述制备方法包括步骤:初始混合单体在水、引发剂、链转移剂、乳化剂的存在下进行乳液聚合反应;
11.在聚合反应累积反应到最终产量的70~80%之前向聚合反应体系中补加第一补加混合单体;以及,
12.在聚合反应累积反应到最终产量的70~80%之后向聚合反应体系中补加第二补加混合单体,至聚合反应结束。
13.作为本发明一种优选的实施方案,在聚合反应累积反应到最终产量的70~80%之前,聚合压力控制为2.0~3.0mpa,优选为2.2~2.5mpa。
14.作为本发明一种优选的实施方案,在聚合反应累积反应到最终产量的70~80%之后,聚合压力控制为3.0~3.5mpa,优选为3.0~3.3mpa。
15.作为本发明一种优选的实施方案,聚合反应的温度为70~90℃,优选为80~85℃。
16.作为本发明一种优选的实施方案,聚合反应过程中,聚合生成的共聚物在水介质中的含量为每100重量份水介质含15~40重量份共聚物,优选每100重量份水介质含20~35重量份共聚物。聚合反应中,反应釜内形成的含氟弹性体的量近似等于加入的补加混合单体的加料量,其范围为每100重量份水介质含有15~40重量份共聚物,优选每100重量份水介质含有20~35重量份共聚物。因为如果水介质中共聚物的重量份小,则产率太低,成本增加,而如果重量份太高,则固含量会变得太高,乳液很粘,乳液稳定性降低,很容易出现破乳、粘壁现象,造成传热效率差。初始混合单体组成和补加的混合单体的单体组成由行业内传统气相色谱仪测定。
17.作为本发明一种优选的实施方案,所述初始混合单体中四氟乙烯和全氟甲基乙烯基醚的摩尔比为(30~50):(50~70);和/或,
18.所述第一补加混合单体中硫化点单体、四氟乙烯和全氟甲基乙烯基醚的摩尔比为(1~2):(60~70):(25~40);和/或,
19.所述第二补加混合单体中硫化点单体、四氟乙烯、全氟甲基乙烯基醚和全氟氧杂烷基乙烯基醚的摩尔比为(1~2):(60~70):(10~20):(10~20)。
20.作为本发明一种优选的实施方案,所述硫化点单体(csm)选自全氟非共轭二烯烃、全氟含溴烯烃、全氟含溴烯烃烯醚、全氟含碘烯烃、全氟含碘烯烃烯醚中的一种或多种的组合,优选为碘代全氟乙基乙烯基醚(csm-i)。
21.作为本发明一种优选的实施方案,所述全氟氧杂烷基乙烯基醚(poave)为含有n个氧杂短链的全氟烷基乙烯基醚,其中n≥2;进一步优选为全氟甲氧基乙基乙烯基醚(cf3ocf2cf2ocf=cf2)。
22.作为本发明一种优选的实施方案,所述引发剂为过硫酸钾、过硫酸钠、过硫酸铵、硫代硫酸钠中的一种或多种的组合,优选为过硫酸钾;引发剂的加入方式为一次性加入、分批次加入或者连续加入,优选引发剂以水溶液的形式在聚合反应开始后每间隔20~40min补充一次。引发剂分批加入反应体系,可以更好的发挥其作用。
23.作为本发明一种优选的实施方案,所述链转移剂为i(cf2)ni,其中n=2~7,优选地,所述链转移剂选自(全氟)1,2-二碘乙烷、全氟丁基二碘、全氟戊基二碘、全氟己基二碘中的一种或多种的组合,更优选为全氟己基二碘;优选链转移剂的加入量与水介质的质量比为(0.01~0.5):100,更优选为(0.1~0.2):100。在反应体系中添加链转移剂i(cf2)ni烷烃,不仅达到了端基非离子化及调节相对分子质量的作用,还提高了端点数,加快硫化速度,使制得的生胶具有优良的加工性和贮存稳定性,使硫化氟橡胶具有优异的低压缩永久变形性和弹性。
24.作为本发明一种优选的实施方案,所述乳化剂为全氟聚醚过氧化物与辛基磺酸钠的混合物,优选全氟聚醚过氧化物与辛基磺酸钠的质量比为1:1;优选乳化剂的加入量与水介质的质量比为(0.01~0.5):100,更优选为(0.02~0.03):100。
25.作为本发明一种优选的实施方案,所述聚合反应在反应釜中进行,反应釜中添加水介质后所留空间为接受气态单体的蒸汽空间,所述蒸汽空间为反应釜容积的30~50%,优选为40%;优选水介质为无离子水介质。
26.作为本发明一种优选的实施方案,本发明提供的制备方法,包括如下步骤:
27.(1)在反应釜中加入水,用氮气置换反应釜中的空气,之后向反应釜中加入初始混合单体置换氮气,之后加入乳化剂、链转移剂,加热至70~90℃;
28.(2)继续加入所述初始混合单体使反应釜的压力达到2.0~3.0mpa,加入引发剂开始聚合反应;在聚合反应中向反应釜内加入第一补加混合单体,维持反应釜内压力为2.0~3.0mpa,每间隔20~40min补加一次引发剂,聚合反应累积到最终产量的70~80%时停止加入所述第一补加混合单体,并回收反应釜中未反应的单体;
29.(3)向反应釜中通入所述初始混合单体,使反应釜的压力达到3.0~3.5mpa,加入引发剂开始聚合反应,在聚合反应中向反应釜内加入第二补加混合单体,每间隔20~40min补加一次引发剂,聚合反应达到最终产量后停止加入所述第二补加混合单体,回收反应釜中未反应的单体,得到全氟醚弹性体乳液。
30.作为本发明一种优选的实施方案,聚合反应时,聚合反应体系中还添加有ph调节剂,所述ph调节剂选自碳酸铵、碳酸氢铵、磷酸氢二钾、磷酸氢二钠中的一种或多种的组合,优选为磷酸氢二钾;优选ph调节剂的加入量与水介质的质量比为(0.01~0.5):100,更优选为(0.05~0.1):100。ph调节剂可以控制介质的ph值在一定的范围内,保证引发剂的反应活性。
31.第二方面,本发明提供了一种全氟醚弹性体乳液,所述乳液由上述的制备方法制备得到。
32.第三方面,本发明提供了一种全氟醚弹性体,由上述制备方法制备得到的乳液制备而成。
33.作为本发明一种优选的实施方案,所述全氟醚弹性体是将所述乳液凝聚、洗涤处理,之后真空干燥制得。
34.进一步优选地,所述乳液采用氯化镁进行凝聚处理。
35.真空干燥温度为95~105℃,更优选100℃。
36.在制备全氟醚弹性体时,乳液的凝聚、洗涤和干燥采用的是本领域常规工艺进行,在此不做赘述。
37.本发明提供的全氟醚弹性体乳液的制备方法,通过在不同的反应阶段采用不同的反应单体配料,可以对制得的共聚物进行结构的控制和调整,获得性能更佳的乳液产品。
38.具体地,本发明采用在不同的反应阶段连续补加不同组分配比成的混合单体的方法,更具体地,是首先将初始混合单体加入反应釜,启动乳液聚合反应;之后在聚合反应累积反应到最终产量的70~80%之前向聚合反应体系中补加第一补加混合单体;在聚合反应累积反应到最终产量的70~80%之后向聚合反应体系中补加第二补加混合单体,直到聚合反应结束。采用以上方法,不仅可以有效控制共聚物单体单元的比值,还能使每个反应阶段组成分布均匀,并保持基本不变。反应开始的初始混合单体中四氟乙烯的摩尔浓度低,则聚合形成的共聚物组成中四氟乙烯分布趋于短序列分布;通过不断补加第一补加混合单体,由于提高了其它组分的量,最终改善了全氟醚弹性体的加工性能,降低了弹性体硫化后硬
度,达到了降低共聚物硬度的目的。在反应累积到一定阶段后加入含有改性柔性单体的第二补加混合单体,其中的全氟氧杂烷基乙烯基醚中侧链结构上的氧杂烷基基团的引入可有效降低分子链的刚性,增加分子链的柔顺性,可使制备得到的橡胶粒子具有硬核软壳形态,具有良好的加工性能,同时降低了全氟醚弹性体的硬度。
39.在全氟醚弹性体乳液的制备过程中,聚合单体通常是以机械搅拌的方式使单体混合物分散于水介质中,在搅拌反应混合物时,加入引发剂。初始混合单体气体加料的时候,每种单体的相对量由反应动力学决定,其设定量要根据共聚单体单元所需的摩尔比确定,即反应活性的单体必须比在所产生的含氟弹性体组成中所需的气体单体有更高的摩尔量。本发明中初始混合单体中四氟乙烯和全氟甲基乙烯基醚的摩尔比为(30~50):(50~70)。
40.聚合过程中,以可控速率加入第一补加混合单体和第二补加混合单体,以保持聚合反应在可控温度下的恒定反应压力。因为聚合速率在反应过程中恒定增加,所以气态混合单体的流量也必须在反应过程中增加,以保持反应釜中恒定压力。气态混合单体在阶段增加进料中的相对量(即摩尔比)与要制备的含氟弹性体中共聚单元的选定的摩尔比相近似,形成的聚合物的重量近似于阶段增量进料的重量。通过控制补加混合单体的流量来保持反应釜在整个聚合反应期间的恒定压力在工业上是容易实现的。在聚合反应的早期阶段,当聚合速率低时,聚合反应釜压力下降慢,气态混合单体的阶段进料增量非常小,以维持反应釜恒定压力。当聚合速率增加时,聚合反应釜压力下降快,可以增加进入反应釜的气态混合单体的流量以维持反应釜的恒定压力。在反应釜和混合单体源之间可以安装流量计量器和恒压器,以准确控制流量,并由此保持反应釜的恒压。
41.本发明中,控制在聚合反应的前期(即聚合反应累积到最终产量的70~80%之前)聚合压力为2.0~3.0mpa,优选2.2~2.5mpa;聚合反应的后期(即聚合反应累积到最终产量的70~80%之后)聚合压力为3.0~3.5mpa,优选3.0~3.3mpa。所需的聚合压力开始时是通过调节在初始加料中的气态单体的量达到的,反应开始后,压力由控制气态单体的阶段增量加料来调节。聚合压力设定在上述范围内,因为如果压力低于2.0mpa,则聚合反应体系的除四氟乙烯以外单体浓度太低,反应活性也较低,不能达到满意的反应速率;如果反应速率慢也容易出现破乳现象,从而造成粘壁,增加反应釜检修维护成本。如果压力高于3.5mpa,则在反应釜中液化的单体量增加,由此不仅增加了被消耗的单体量,而且使转化率低,增加物料成本。此外,如果压力高于3.5mpa,对设备及系统、管线的要求较高,增加了生产成本。
42.在聚合过程中,可以通过调整聚合温度实现聚合速度的稳定。聚合反应过程中反应温度保持在70~90℃,优选为80~85℃。如果温度低于70℃,共聚速度太慢,不适合工业规模的有效生产。但是如果温度高于90℃,引发剂分解速度快,从而会造成引发剂的浪费;引发剂分解速度快还会导致聚合反应速度快,反应过程不易控制,且不能有效控制聚合物的链段结构,导致聚合物中四氟乙烯含量过高,弹性体刚度大,硬度高。同时反应温度高也会造成反应釜内部结壁,从而影响产品质量,增加劳动成本。所以必须将反应温度控制在有效的范围内。
43.本发明通过控制聚合压力和温度及通过加入引发剂量来控制聚合速度,通常情况下,本发明的聚合时间为6~10小时。
44.本发明合成的全氟醚弹性体具有硫化速度快,硬度低、且拉伸强度高、压变低的优点。本发明制得的全氟醚弹性体较常规全氟醚弹性体橡胶弹性更佳,在开炼机上进行二次
加工的时候更容易包辊,提高加工效率。相比采用相同配方、直接混合进行乳液聚合反应得到的全氟醚弹性体,本发明制得的全氟醚弹性体硫化后的氟橡胶硬度更低,具有更高的填料填充率。由于全氟醚弹性体价格高昂,更高的填料填充率对于下游使用客户而言就可以明显降低成本,因此可以扩大全氟醚橡胶的推广应用。
具体实施方式
45.下面通过具体实施方式来进一步说明本发明的技术方案。本领域技术人员应该明了,所述具体实施方式仅仅是帮助理解本发明,不应视为对本发明的具体限制。若未特别指明,以下实例中所用技术手段为本领域技术人员所熟知的常规手段,所用原料均为市售常规商品。
46.实施例1
47.本实施例提供了一种全氟醚弹性体乳液,具体制备方法如下:
48.(1)在附带搅拌装置的50l反应釜中加入30kg无离子水,先用氮气置换出反应釜中的空气,再采用隔膜压缩机向反应釜内加入初始混合单体四氟乙烯tfe/全氟甲基乙烯基醚pmve=30/70(摩尔比),置换氮气,并使釜中氧含量小于30ppm;加入乳化剂6g,乳化剂为全氟聚醚过氧化物与辛基磺酸钠质量比1:1的混合物,以及ph调节剂磷酸氢二钾15g、链转移剂全氟己基二碘30g,并加热至80℃;
49.(2)启动搅拌装置,继续加入初始混合单体tfe/pmve=30/70(摩尔比),使反应釜的压力达到2.2mpa,加入引发剂过硫酸钾30g开始聚合反应;然后通过隔膜压缩机向反应釜中加入第一补加混合单体tfe/pmve/csm-i=60/39/1(摩尔比),维持反应釜内压力恒定;并每隔20min补加引发剂过硫酸钾10g,维持反应有效进行,聚合反应累积到最终产量的80%,停止加入第一补加混合单体,并回收反应釜中未反应的单体;
50.(3)重新向反应釜中通入初始混合单体tfe/pmve=30/70(摩尔比),待反应釜内的压力为3.3mpa时,开启搅拌装置,加入引发剂过硫酸钾20g,进行聚合反应;连续通入第二补加混合单体tfe/pmve/csm-i/poave=60/19/1/20(摩尔比),并在聚合反应过程中,每隔20min补加引发剂过硫酸钾10g,维持反应有效进行,待聚合反应达到最终产量时,停止加入第二补加混合单体,关停搅拌装置,回收反应釜中未反应的单体,制备得到全氟醚弹性体乳液。
51.其中全氟氧杂烷基乙烯基醚(poave)具体为全氟甲氧基乙基乙烯基醚(cf3ocf2cf2ocf=cf2)。
52.向制得的全氟醚弹性体乳液中加入氯化镁进行凝聚,然后洗涤,再在100℃真空干燥24h,得到12.5kg全氟醚弹性体产品。
53.实施例2
54.本实施例提供了一种全氟醚弹性体乳液,具体制备方法如下:
55.(1)在附带搅拌装置的50l反应釜中加入30kg无离子水,先用氮气置换出反应釜中的空气,再采用隔膜压缩机向反应釜内加入初始混合单体tfe/pmve=50/50(摩尔比)置换氮气,并使釜中氧含量小于30ppm;之后加入乳化剂9g,乳化剂为全氟聚醚过氧化物与辛基磺酸钠质量比1:1的混合物,以及ph调节剂磷酸氢二钾30g、链转移剂全氟己基二碘60g,并加热至85℃;
56.(2)启动搅拌装置,继续加入初始混合单体tfe/pmve=50/50(摩尔比),使反应釜的压力达到2.5mpa,然后加入引发剂过硫酸钾25g,开始聚合反应;然后通过隔膜压缩机向釜中加入第一补加混合单体tfe/pmve/csm-i=70/28/2(摩尔比),维持反应釜压力恒定;并每隔40min补加引发剂过硫酸钾15g,维持反应有效进行,聚合反应累积到最终产量的70%时,停止加入第一补加混合单体,并回收反应釜中未反应的单体;
57.(3)重新通入初始混合单体tfe/pmve=50/50(摩尔比),待反应釜的压力为3.0mpa,开启搅拌装置,加入引发剂过硫酸钾40g,进行聚合反应;连续通入第二补加混合单体tfe/pmve/csm-i/poave=70/18/2/10(摩尔比),并在聚合反应过程中每隔40min补加引发剂过硫酸钾15g,维持反应有效进行,待聚合反应达到最终产量时,停止加入第二补加混合单体,关停搅拌装置,回收反应釜中未反应的单体,制备得到全氟醚弹性体乳液。
58.其中全氟氧杂烷基乙烯基醚(poave)具体为全氟甲氧基乙基乙烯基醚(cf3ocf2cf2ocf=cf2)。
59.向制得的全氟醚弹性体乳液中加入氯化镁进行凝聚,然后洗涤,再在100℃真空干燥24h,得到12.2kg的全氟醚弹性体产品。
60.对比例1
61.本对比例提供了一种全氟醚弹性体乳液,与实施例1的区别在于,不使用第二补加混合单体,具体制备方法如下:
62.(1)在附带搅拌装置的50l反应釜中加入30kg无离子水,先用氮气置换出反应釜中的空气,再采用隔膜压缩机向反应釜内加入初始混合单体四氟乙烯tfe/全氟甲基乙烯基醚pmve=30/70(摩尔比),置换氮气,并使釜中氧含量小于30ppm;加入乳化剂6g,乳化剂为全氟聚醚过氧化物与辛基磺酸钠质量比1:1的混合物,以及ph调节剂磷酸氢二钾15g、链转移剂全氟己基二碘30g,并加热至80℃;
63.(2)启动搅拌装置,继续加入初始混合单体tfe/pmve=30/70(摩尔比),使反应釜的压力达到2.2mpa,加入引发剂过硫酸钾30g开始聚合反应;然后通过隔膜压缩机向反应釜中加入第一补加混合单体tfe/pmve/csm-i=60/39/1(摩尔比),维持反应釜内压力恒定;并每隔20min补加引发剂过硫酸钾10g,维持反应有效进行,聚合反应累积到最终产量,停止加入第一补加混合单体,关停搅拌装置,并回收反应釜中未反应的单体,制备得到全氟醚弹性体乳液。
64.向制得的全氟醚弹性体乳液中加入氯化镁进行凝聚,然后洗涤,再在100℃真空干燥24h,得到12.4kg全氟醚弹性体产品。
65.对比例2
66.本对比例提供了一种全氟醚弹性体乳液,与实施例2的区别在于第二补加混合单体中的全氟氧杂烷基乙烯基醚(poave)由全氟甲氧基乙基乙烯基醚(cf3ocf2cf2ocf=cf2)改为全氟正丙基乙烯基醚(ppve,结构式cf3cf2cf2ocf=cf2),具体制备方法如下:
67.(1)在附带搅拌装置的50l反应釜中加入30kg无离子水,先用氮气置换出反应釜中的空气,再采用隔膜压缩机向反应釜内加入初始混合单体tfe/pmve=50/50(摩尔比)置换氮气,并使釜中氧含量小于30ppm;之后加入乳化剂9g,乳化剂为全氟聚醚过氧化物与辛基磺酸钠质量比1:1的混合物,以及ph调节剂磷酸氢二钾30g、链转移剂全氟己基二碘60g,并加热至85℃;
68.(2)启动搅拌装置,继续加入初始混合单体tfe/pmve=50/50(摩尔比),使反应釜的压力达到2.5mpa,然后加入引发剂过硫酸钾25g,开始聚合反应;然后通过隔膜压缩机向釜中加入第一补加混合单体tfe/pmve/csm-i=70/28/2(摩尔比),维持反应釜压力恒定;并每隔40min补加引发剂过硫酸钾15g,维持反应有效进行,聚合反应累积到最终产量的70%时,停止加入第一补加混合单体,并回收反应釜中未反应的单体;
69.(3)重新通入初始混合单体tfe/pmve=50/50(摩尔比),待反应釜的压力为3.0mpa,开启搅拌装置,加入引发剂过硫酸钾40g,进行聚合反应;连续通入第二补加混合单体tfe/pmve/csm-i/ppve=70/18/2/10(摩尔比),并在聚合反应过程中每隔40min补加引发剂过硫酸钾15g,维持反应有效进行,待聚合反应达到最终产量时,停止加入第二补加混合单体,关停搅拌装置,回收反应釜中未反应的单体,制备得到全氟醚弹性体乳液。
70.向制得的全氟醚弹性体乳液中加入氯化镁进行凝聚,然后洗涤,再在100℃真空干燥24h,得到12kg的全氟醚弹性体产品。
71.实施例3
72.对以上各实例制得的全氟醚弹性体进行了检测,检测步骤如下:
73.(1)分别将全氟醚弹性体(生胶,100phr)在25℃开放式炼胶机上塑炼薄通6~8遍,观察生胶的加工性能;
74.(2)加入双二五硫化胶(4phr)、taic(3phr)、炭黑n990(30phr)进行混炼,混炼至胶料无明显差异,再以三角包形式薄通混炼8~12遍,混炼温度不超过60℃;
75.出片进行分段硫化,一段硫化:硫化条件177℃
×
10min;二段硫化:硫化条件230℃
×
4h;再进行以下数据测试分析。
76.(3)生胶门尼ml(1+10)121℃测试根据gb/t1232-2000;玻璃化转变温度(tg)测试根据gb/t19466-2004;
77.生胶的加工性能判定方法:观察生胶达到多少温度时能在开放式炼机上快速包辊,并用手持式红外感应测温仪测量生胶的温度;并称量生胶在全部包辊情况过程中的絮状、颗粒或块状滴落物(尺寸小于10x10x10mm)重量。
78.拉伸应力应变性能测试方法根据gb/t528-2009;硬度测试根据gb/t531-2008;压缩永久变形测试方法根据gb/t7759-1996,测定条件为a型试样300℃
×
70h。检测结果见表1所示。
79.表1
[0080][0081]
由表1数据可知,相比对比例方法制备的全氟醚弹性体制成的硫化胶,由本发明方法制备的全氟醚弹性体制成的硫化胶硬度明显更低。本发明中炭黑n990添加量为30phr,填充量高,而达到的硬度为78~80,硬度低,说明本发明方法制备的全氟醚弹性体具有更高的填料填充率。目前全氟醚弹性体的价格一般为8000~12000元/公斤,常用填料n990的价格约20元/公斤。因此,高的填料填充率可以有效降低生产成本。本发明制备的全氟醚弹性体可以实现配方高填充,有效的降低混炼胶材料成本,扩大材料的使用范围。
[0082]
由上表数据还可以看出,相比对比例方法制备的全氟醚弹性体即生胶,由本发明方法制备的全氟醚弹性体即生胶的加工性能更好。生胶在较低温度下就能在开放式炼机上快速包辊,该温度显著降低;生胶在全部包辊过程中的絮状、颗粒或块状滴落物重量也大幅度下降。以上说明由本发明方法制备的全氟醚弹性体即生胶的加工性能优良。
[0083]
虽然,上文中已经用一般性说明、具体实施方式及试验,对本发明作了详尽的描述,但在本发明基础上,可以对之作一些修改或改进,这对本领域技术人员而言是显而易见的。因此,在不偏离本发明精神的基础上所做的这些修改或改进,均属于本发明要求保护的范围。