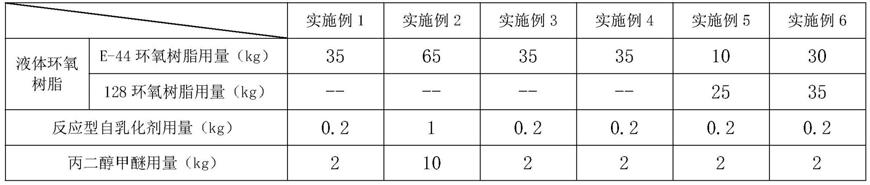
1.本申请涉及乳液制备工艺的技术领域,尤其是涉及一种环氧树脂乳液的绿色制备工艺。
背景技术:2.环氧树脂是一种高分子聚合物,是指分子中含有两个以上环氧基团的一类聚合物的总称。由于环氧基的化学活性,可用多种含有活泼氢的化合物使其开环,固化交联生成网状结构,因此环氧树脂与固化剂可制成环氧树脂胶,被广泛作为涂料和胶黏剂使用。
3.环氧树脂乳液作为环氧树脂胶的原料,是环氧树脂在乳化剂的作用下在水中形成的一种乳浊液。一般的制备工艺为,将固体环氧树脂预先磨成微米级的环氧树脂粉末,然后将环氧树脂和乳化剂混合,加热到适当的温度,在搅拌下加入水而形成乳液。
4.在现有的工艺中,在乳化过程中需要进行加热,在制备过程中能耗较高。
技术实现要素:5.为了降低环氧树脂乳液制备过程中的能耗,本申请提供环一种氧树脂乳液的绿色制备工艺。
6.一种环氧树脂乳液的绿色制备工艺,包括以下步骤:s1:将质量份数为35
‑
65份的液体环氧树脂、0.2
‑
1份的反应型自乳化剂和2
‑
10份的醇醚溶剂进行混合,并低速搅拌30
‑
40min,得油相溶液;s2:控制搅拌速度为1000
‑
1200r/min,将质量份数为35
‑
60份的去离子水分多次添加到油相溶液中,添加完成后继续搅拌1
‑
2h,得混合液;s3:将混合液静置,过滤后出料,得环氧树脂乳液;所述反应型自乳化剂为同时含有氨基和环氧基的植物类可降解反应型自乳化剂。
7.通过采用上述技术方案,由于采用了同时含有氨基和环氧基的植物类可降解反应型自乳化剂,乳化剂在进行乳化作用的同时,自身的氨基和环氧基也可进行反应,从而在环氧树脂胶粒外围形成一层交联状的表面活性层,其乳化能力远强于普通乳化剂,因此无需进行加热活化就可使环氧树脂在水中充分乳化形成胶粒。
8.步骤s1中,先将环氧树脂和乳化剂在醇醚中混合,醇醚可作为环氧树脂的溶剂,可降低环氧树脂的黏性,有利于后续的乳化步骤。而醇醚自身又可与水互溶,因此不会对胶粒的形成产生影响。
9.步骤s2中,逐渐往油相溶液中添加水,在高速搅拌条件下,油相充分分散于水相中,环氧树脂形成细小的胶粒,在此过程中,在油相和水相的双重作用力下,乳化剂在环氧树脂表面形成一层致密的表面活性层,表面活性层中的乳化剂其自身的高密度的氨基和环氧基可充分接触,从化学动力学层面使氨基和环氧基之间的反应成为可能,因此表面活性层内的乳化剂分子产生交联。并且由于乳化剂中含有与环氧树脂相同结构,根据相似相溶原理,乳化剂可起到“锚固作用”,使乳化剂与油相之间具有更强的结合能力。因此该乳化剂
具有极强的乳化能力,无需进行加热就可达到极好的乳化效果。并且在其优异的乳化作用下,可将环氧树脂乳化成粒径更小的胶粒,从而还可提高环氧树脂固化后的耐水性和、韧性、硬度和光泽度。
10.在完成乳化后,通过步骤s3的静置,过滤后出料,就可制得环氧树脂乳液。
11.优选的,所述植物类可降解反应型自乳化剂为基于腰果酚聚氧乙烯醚合成的非离子反应型自乳化剂。
12.通过采用上述技术方案,腰果酚为从腰果壳油中提取的天然成分,具有环保无污染的优点,而基于腰果酚聚氧乙烯醚合成的非离子反应型自乳化剂可进行生物降解,可防止生产制备过程中产生废料污染,使工艺更加绿色环保。
13.优选的,所述腰果酚聚氧乙烯醚的聚合度为14
‑
18。
14.通过采用上述技术方案,使用此聚合度的腰果酚制得的乳化剂可具有更优的乳化能力,在保证了较优的乳化能力的同时,还可便于交联,可制得粒径更小的胶粒。
15.优选的,所述醇醚溶剂为丙二醇甲醚。
16.通过采用上述技术方案,丙二醇甲醚毒性低,没有刺激性气味,属于低毒醇醚类物质。在确保了对环氧树脂具有优良的溶解性以及降低黏度的能力的同时,还降低废料对环境的影响。
17.优选的,所述的液体环氧树脂由质量份数为25
‑
35份的环氧树脂a和10
‑
30份的环氧树脂b混合而成,所述环氧树脂a的环氧值为0.5
‑
0.55,环氧树脂b的环氧值为0.4
‑
0.45。
18.通过采用上述技术方案,通过使用不同环氧值的环氧树脂进行混合,可使乳化后的胶粒具有更小的粒径,在反应型自乳化剂的配合下可进一步提高乳化的效果,并使环氧树脂乳液在固化后具有更优的耐水性。
19.优选的,步骤s2中,先将质量份数为25
‑
40份的去离子水分3
‑
4次添加到油相溶液中,控制1
‑
2h添加完,保持1000
‑
1200r/min的转速持续搅拌,直至混合液黏度下降,再分2
‑
3次添加剩下的10
‑
20份去离子水,控制0.5
‑
1小时添加完。
20.通过采用上述技术方案,将去离子水分两阶段添加,且每一阶段又分成多次添加,可防止胶粒的过度聚集,使乳化后的胶粒具有更小的粒径,提高环氧树脂在水中的乳化效果。在第一阶段的添加过程中,水相进入到油相中,在此阶段内为油包水,在乳化剂的作用下,搅拌后在油相中逐渐形成水珠,而当添加足量的水后,再持续进行搅拌,水珠会逐渐结合,最后实现变相,形成水包油的结构,黏度会突然下降,至此乳液初步形成。完成变相后再进行第二阶段加水,此过程中主要就是调整胶粒在水中的分散度,使其在搅拌下能形成更小粒径的胶粒。
21.优选的,步骤s3中,在将混合液静置之前,先将混合液在500
‑
550r/min的转速下低速搅拌30
‑
35min。
22.通过采用上述技术方案,在完成乳化后,在进行低速搅拌,可除去高速搅拌乳化过程中产生的气泡,达到消泡的目的,使乳液更加均匀,防止气泡在乳液固化过程中对其产生影响。
23.优选的,步骤s1中,低速搅拌时搅拌速度为450
‑
500r/min。
24.通过采用上述技术方案,在此搅拌速度下,可使环氧树脂和乳化剂在醇醚溶剂中更好地产生分散,并且在此搅拌速度下,有助于乳液在初始阶段就产生部分的交联,为后续
的乳化提供有利条件,有助于制得粒径更小的胶粒。
25.综上所述,本申请包括以下至少一种有益技术效果:1.本申请通过使用同时含有氨基和环氧基的植物类可降解反应型自乳化剂,利用其高性能的乳化能力,可实现无需加热就可对环氧树脂进行乳化,并且通过控制乳化过程中的各项工艺参数以及各组分之间的用量比,就可制得高性能的乳化剂,并且制备过程更加绿色环保。
26.2.本申请的植物类可降解反应型自乳化剂具体选用基于腰果酚聚氧乙烯醚合成的非离子反应型自乳化剂,这种乳化剂可进行生物降解,减少制备过程中产生的废料污染,使制备工艺更加绿色环保。并且本申请还公布了腰果酚聚氧乙烯醚的优选聚合度,使制得粒径更小的胶粒。
27.3.本申请的工艺在往油相溶液中加水的过程中,通过分阶段多次加水,使制得的乳液具更优的性能,制得的胶粒具有更小的粒径。
28.4.本申请还公布了醇醚溶剂具体选用丙二醇甲醚,而液体环氧树脂为两种不同环氧值的环氧树脂的混合物,进一步提高了制得乳液的性能。
29.5.本申请完乳化后,还讲混合液在低速下进行搅拌,进而除去混合液中的气泡,提高制得的乳液的品质。
具体实施方式
30.制备例乳化剂的制备:s1:往腰果酚聚氧乙烯醚中添加浓度为30%的过氧乙酸,室温下搅拌1.5h,然后以中性氧化铅为吸附剂,四氢呋喃为洗脱剂进行分离提纯,得环氧化腰果酚聚氧乙烯醚。
31.s2:将环氧化腰果酚聚氧乙烯醚和等物质的量的二氯亚砜进行混合,以吡啶为催化剂,混合搅拌1h,再添加等物质的量的邻苯二甲酰亚胺钾盐,混合搅拌4h,过滤后洗涤固体中间产物。
32.s3:将固体中间产物添加到浓度为35%的盐酸醇溶液中,搅拌15h后减压过滤,洗涤后得基于腰果酚聚氧乙烯醚合成的非离子反应型自乳化剂。实施例
33.实施例1:一种环氧树脂乳液的绿色制备工艺,工艺步骤如下:s1:将35kg的液体环氧树脂、0.2kg反应型自乳化剂和2kg丙二醇甲醚添加到分散缸内,在搅拌速度为400r/min的速度下搅拌30min,得油相溶液;s2:将搅拌速度调整到1000r/min,将35kg去离子水在1h内分五次添加到分散缸中,添加完成后再搅拌1h,得混合液;s3:将混合液静置,过滤后出料,得环氧树脂乳液。
34.步骤s1中的液体环氧树脂具体选用e
‑
44环氧树脂(环氧值为0.44);反应型自乳化剂为选用聚合度为12的腰果酚聚氧乙烯醚,并通过制备例的步骤制得的基于腰果酚聚氧乙烯醚合成的同时具有氨基和环氧基的非离子反应型自乳化剂。
35.实施例2:一种环氧树脂乳液的绿色制备工艺,
与实施例1的区别在于,各组分的用量以及各项工艺参数不同,具体如下表1所示。
36.实施例3:一种环氧树脂乳液的绿色制备工艺,与实施例1的区别在于,制备非离子反应型自乳化剂的腰果酚聚氧乙烯醚的聚合度为14。各组分的用量以及各项工艺参数如下表1所示。
37.实施例4:一种环氧树脂乳液的绿色制备工艺,与实施例1的区别在于,制备非离子反应型自乳化剂的腰果酚聚氧乙烯醚的聚合度为18。各组分的用量以及各项工艺参数如下表1所示。
38.实施例5
‑
6:一种环氧树脂乳液的绿色制备工艺,与实施例1的区别在于,所用的液体环氧树脂为e
‑
44环氧树脂(环氧值为0.44)和128环氧树脂(环氧值为0.53)的混合物,两种树脂的用量及其余的工艺参数如下表1所示。
39.实施例7:一种环氧树脂乳液的绿色制备工艺,与实施例1的区别在于,步骤s2中去离子水分两批进行添加。
40.s2具体步骤为:控制搅拌速度为1000r/min,先将25kg的去离子水分3次添加到分散缸中,控制1h添加完,保持1000r/min的转速持续搅拌,直至混合液黏度下降,再将10kg去离子水分2次添加到分散缸中,控制0.5小时添加完,添加完成后再搅拌1h,得混合液。
41.其余步骤与实施例1相同。各组分的用量一其余工艺参数如下表1所示。
42.实施例8:一种环氧树脂乳液的绿色制备工艺,与实施例1的区别在于,步骤s2中去离子水分两批进行添加。
43.s2具体步骤为:控制搅拌速度为1000r/min,先将40kg的去离子水分4次添加到分散缸中,控制2h添加完,保持1000r/min的转速持续搅拌,直至混合液黏度下降,再将20kg去离子水分3次添加到分散缸中,控制1小时添加完,添加完成后再搅拌1h,得混合液。
44.其余步骤与实施例1相同。各组分的用量一其余工艺参数如下表1所示。
45.实施例9
‑
10:一种环氧树脂乳液的绿色制备工艺,与实施例1的区别在于,步骤s1中的搅拌速度不同,具体参数如下表1所示。
46.实施例11:一种环氧树脂乳液的绿色制备工艺,与实施例1的区别在于,步骤s3中在将混合液静置之前,先将混合液进行低速搅拌一段时间。
47.s3具体步骤为:将混合液在500r/min的转速下低速搅拌30min,再将混合液静置,过滤后出料,得环氧树脂乳液。
48.其余步骤与实施例1相同。各组分的用量一其余工艺参数如下表1所示。
49.实施例12:一种环氧树脂乳液的绿色制备工艺,与实施例1的区别在于,步骤s3中在将混合液静置之前,先将混合液进行低速搅拌一段时间。
50.s3具体步骤为:将混合液在550r/min的转速下低速搅拌35min,再将混合液静置,过滤后出料,得环氧树脂乳液。
51.其余步骤与实施例1相同。各组分的用量一其余工艺参数如下表1所示。表1:实施例1
‑
12各组分用量及各项参数
52.对比例对比例1:一种环氧树脂乳液的制备工艺,工艺步骤如下:s1:将35kg的液体环氧树脂、0.2kg乳化剂和2kg丙二醇甲醚添加到分散缸内,在搅拌速度为400r/min的速度下搅拌30min,得油相溶液;s2:将搅拌速度调整到1000r/min,并将分散缸升温至80℃,将35kg去离子水在1h内分五次添加到分散缸中,添加完成后再搅拌1h,得混合液;s3:降温后将混合液静置,过滤后出料,得环氧树脂乳液。
53.步骤s1中的液体环氧树脂具体选用e
‑
44环氧树脂(环氧值为0.44);乳化剂为山梨醇酐脂肪酸酯。
54.对比例2:一种环氧树脂乳液的制备工艺,与对比例1的区别在于,乳化剂为山梨醇酐聚氧乙烯。具体用量以及工艺参数如下表2所示。
55.对比例3:一种环氧树脂乳液的制备工艺,工艺步骤如下:s1:将35kg的液体环氧树脂、0.2kg反应型自乳化剂和2kg丙二醇甲醚添加到分散缸内,在搅拌速度为400r/min的速度下搅拌30min,得油相溶液;s2:将搅拌速度调整到1000r/min,并将分散缸升温至80℃,将35kg去离子水在1h内分五次添加到分散缸中,添加完成后再搅拌1h,得混合液;
s3:降温后将混合液静置,过滤后出料,得环氧树脂乳液。
56.步骤s1中的液体环氧树脂具体选用e
‑
44环氧树脂(环氧值为0.44);反应型自乳化剂为选用聚合度为12的腰果酚聚氧乙烯醚,并通过制备例的步骤制得的基于腰果酚聚氧乙烯醚合成的同时具有氨基和环氧基的非离子反应型自乳化剂。
57.对比例4:一种环氧树脂乳液的制备工艺,与对比例3的区别在于,s2中分散缸的解热温度不同。各组分具体用量以及工艺参数如下表2所示。
58.对比例5
‑
6:一种环氧树脂乳液的制备工艺,与实施例1的区别在于,步骤s2中搅拌速度不同。各组分具体用量以及工艺参数如下表2所示。表2:对比例1
‑
6各组分用量及工艺参数
59.性能检测试验试验一:胶粒粒径检测试验试验原理:通过光学显微镜观测胶粒,并根据放大倍数计算粒径大小。
60.试验对象:实施例1
‑
12和对比例1
‑
6。
61.试验方法:根据中华人民共和国国家标准gb/t11175
‑
2002所记载的第5.9条粒径的测定方法,采用光学显微镜法进行检测,每个样品测定粒子数为60个并计算平均粒径(μm),计算结果保留一位小数,试验结果如下表3所示。表3:实施例1
‑
12和对比例1
‑
6的平均粒径
62.试验二:静置分层试验试验原理:将各试验样静置,记录各试验样出现分层的时间并进行对比,就可判断各试验样的稳定性。
63.试验对象:实施例1
‑
12,对比例1
‑
6。
64.试验方法:从实施例1
‑
12和对比例1
‑
6新制得的乳液中分别取出1l存放于相同的透明玻璃容器内,在室温下进行存放,每隔一天观察乳液的情况,直至乳液出现分层,记录各实施例和对比例的乳液出现分层的天数,试验结果如下表4所示。表4:实施例1
‑
12和对比例1
‑
6出现静置分层的天数
65.实验三:耐水性试验试验原理:将乳液与固化剂制成环氧树脂胶,将其涂覆在试板上并使其充分固化制得试样,将试样浸渍于水中,通过对比漆膜出现破损的时间,就可对比出由不同乳液固化而成的漆膜的耐水性。
66.试验对象:将实施例1
‑
12和对比例1
‑
6制得的环氧树脂乳液与bs
‑
782型固化剂进行混合制成环氧树脂胶,分别将其涂覆在15cm
×
15cm的钢板表面,并使其充分固化。每个实施例和对比例分别制备3个样品,并将各组与实施例1
‑
12和对比例1
‑
6对应的样品依次标号为试验组1
‑
12和对照组1
‑
6。
67.试验方法:在玻璃水槽内加入去离子水,并保持水温为25
±
2℃,将各试验组和对照组的样品长度的2/3浸泡于蒸馏水中,每隔一段时间取出观察各样品表面的漆膜状态。如果三片中至少有两块样品的漆膜出现失光、变色、气泡、起皱或脱落等现象,则判定为该组漆膜已经失效,记录各组试样漆膜失效的天数,试验结果如下表5所示。表5:试验组1
‑
12和对照组1
‑
6漆膜失效天数 试验组1试验组2试验组3试验组4试验组5试验组6漆膜失效天数190195234236215214 试验组7试验组8试验组9试验组10试验组11试验组12漆膜失效天数252253208206212208 对照组1对照组2对照组3对照组4对照组5对照组6漆膜失效天数10493193197176164
68.对试验一、试验二和试验三的结果进行结合分析:对比表3、表4和表5中实施例/试验组1
‑
2和对比例/对照组1
‑
2的数据,可发现实施例/试验组1
‑
2的平均粒径小于对比例/对照组1
‑
2,而出现分层的天数以及漆膜失效的天数均远大于对比例/对照组1
‑
2,这可说明由实施例1
‑
2制得的环氧树脂乳液其分散性更好,且更不易分层,固化后的耐水性也更好。从而说明了通过使用同时含有氨基和环氧基的植物类可降解反应型自乳化剂,在其高效的乳化能力的作用下,配合适当的工艺,就可制得更高性能的环氧树脂乳液。
69.对比表3、表4和表5中实施例/试验组1
‑
2和对比例/对照组3
‑
4的数据,可发现实施例/试验组1
‑
2和对比例/对照组3
‑
4的各项数值均相近。这可说明,在其余工艺相同的情况下通过使用同时含有氨基和环氧基的植物类可降解反应型自乳化剂,在不加热的情况下制
得的环氧树脂乳液,其乳化效果与加热情况下相近。从而说明这种乳化剂在常温下就可达到充分且良好的乳化效果,不必进行加热,因此制备过程更加节能环保。
70.对比表3、表4和表5中实施例/试验组1
‑
2和对比例/对照组5
‑
6的数据,可发现实施例/试验组1
‑
2的平均粒径小于对比例/对照组5
‑
6,而出现分层的天数以及漆膜失效的天数均大于对比例/对照组5
‑
6。这说明实施例1
‑
2的制备工艺中,乳化时采用的转速为更优的范围,这是因为当转速过低时,环氧树脂无法达到充分的分散,而当转速过快时,又会导致乳化剂在胶粒表面难以稳定得结合,从而影响乳化效果。
71.对比表3、表4和表5中实施例/试验组1
‑
2和实施例/试验组3
‑
4的数据,可发现实施例/试验组1
‑
2的平均粒径大于实施例/试验组3
‑
4,而出现分层的天数以及漆膜失效的天数均小于对比例/对照组3
‑
4。这说明实施例3
‑
4中使用腰果酚聚氧乙烯醚的聚合度为更优技术方案。使用此聚合度的腰果酚制得的乳化剂可具有更优的乳化能力,在保证了较优的乳化能力的同时,还可便于交联,可制得粒径更小的胶粒。
72.对比表3、表4和表5中实施例/试验组1
‑
2和实施例/试验组5
‑
6的数据,可发现实施例/试验组1
‑
2的平均粒径大于实施例/试验组5
‑
6,而出现分层的天数以及漆膜失效的天数均小于对比例/对照组5
‑
6。这说明实施例5
‑
6中使用环氧值分别为0.53和0.44的两种环氧树脂的混合物作为树脂原料,可制得具有更优性能的乳液。
73.对比表3、表4和表5中实施例/试验组1
‑
2和实施例/试验组7
‑
8的数据,可发现实施例/试验组1
‑
2的平均粒径大于实施例/试验组7
‑
8,而出现分层的天数以及漆膜失效的天数均小于对比例/对照组7
‑
8。这说明实施例7
‑
8中将去离子水分两批进行添加,在第一阶段水添加完成后,待体系完成变相后再添加第二阶段的水,这样的工艺操作可制得性能更优的乳液。在第一阶段的添加过程中,水相进入到油相中,在此阶段内为油包水,在乳化剂的作用下,搅拌后在油相中逐渐形成水珠,而当添加足量的水后,再持续进行搅拌,水珠会逐渐结合,最后实现变相,形成水包油的结构,黏度会突然下降,至此乳液初步形成。完成变相后再进行第二阶段加水,此过程中主要就是调整胶粒在水中的分散度,使其在搅拌下能形成更小粒径的胶粒。
74.对比表3、表4和表5中实施例/试验组1
‑
2和实施例/试验组9
‑
10的数据,可发现实施例/试验组1
‑
2的平均粒径大于实施例/试验组9
‑
10,而出现分层的天数以及漆膜失效的天数均小于对比例/对照组9
‑
10。这说明实施例9
‑
10的步骤s1中使用的搅拌速度为更优的技术方案,可制得性能更优的乳液。
75.对比表3、表4和表5中实施例/试验组1
‑
2和实施例/试验组11
‑
12的数据,可发现实施例/试验组1
‑
2与实施例/试验组11
‑
12的平均粒径相近,但是实施例/试验组1
‑
2出现分层的天数以及漆膜失效的天数均小于对比例/对照组11
‑
12。这是因为在实施例11
‑
12中在静置之前还对乳液进行一段时间的低速搅拌,出去乳液中的气泡。这些气泡虽然在初期对乳液粒径没什么影响,但是气泡的存在会导致乳液的不稳定以及固化后漆膜表面的均匀性。从而说明了实施例11
‑
12中采用低速搅拌的工艺为更优的技术方案。
76.本具体实施例仅仅是对本申请的解释,其并不是对本申请的限制,本领域技术人员在阅读完本说明书后可以根据需要对本实施例做出没有创造性贡献的修改,但只要在本申请的权利要求范围内都受到专利法的保护。