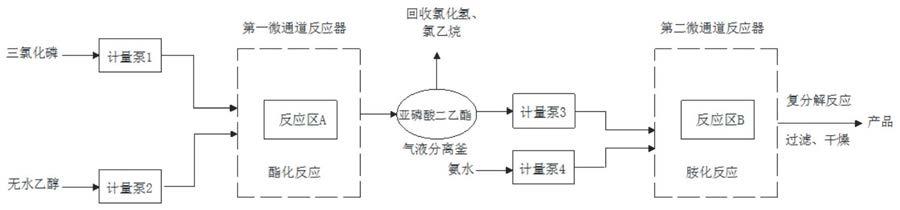
1.本发明涉及农药合成领域,具体地涉及一种制备三乙膦酸铝方法及系统。
背景技术:2.三乙膦酸铝是一种有机磷类高效、广谱、内吸性低毒杀菌剂,具有双向内吸传导作用。三乙膦酸铝适用作物非常广泛,可防治果树、蔬菜、花卉及经济作物由单轴霉属、霜霉属、疫霉属引起的病害,如蔬菜、果树霜霉病、疫病、菠萝心腐病、柑橘根腐病、茎溃病、草霉茎腐病、红髓病等,市场需求量大。
3.目前制备三乙膦酸铝原药的方法是以三氯化磷、乙醇为起始原料,经酯化、与氨水反应的胺化、胺化物与硫酸铝进行复分解反应合成,其中:
4.第一步反应是三氯化磷和乙醇发生酯化反应生成亚磷酸二乙酯,国内外多采用滴加或者简单连续混合的方式(参见us4272448,cn102766157a)由于此步反应放热剧烈,易造成局部过热或系统飞温现象,存在反应失控风险。生产上需要用使用冷冻盐水进行降温,能源消耗大,对设备参数要求高。在有水、酸性和温度高的条件下,随着反应时间的延长,亚磷酸二乙酯极易分解,副产物多。反应方程式如下:
5.pcl3+3c2h5oh
→
(c2h5o)2poh+2hcl
↑
+c2h5cl
↑
6.第二步反应是亚磷酸二乙酯和氨水进行胺化反应生成胺化物,目前工艺多采用滴加氨水或亚磷酸二乙酯的间歇式生产方式,反应是放热反应且反应时间长达6~9小时(参见cn101955497a,cn102766157a),影响生产效率的提高。反应方程式如下:
[0007][0008]
第三步反应是胺化物与硫酸铝进行复分解反应生成三乙膦酸铝,同时生成副产物硫酸铵。过量的硫酸铝和副产物硫酸铵容易在产物三乙膦酸铝中积留,造成产物含量低。反应式如下:
[0009][0010]
目前市场报道产品总收率最高的为95%,含量98%(参见cn102766157a),原料的不充分反应造成三废排放量大,给环保处理造成困难,不利于绿色清洁化生产。
[0011]
综上所述,目前方法普遍存在反应时间长、设备利用率低、能耗大、产品含量收率低、生产效率低下等缺点,不能实现安全高效地连续化生产,影响生产的本质安全。
[0012]
微通道反应器是具有特殊微通道结构的小型反应器的统称,与常规反应器相比,微通道反应器具有比表面积大,体积小,过程连续,易数增放大,快速混合效果好,传热效果好等特点,其优异的传质、传热性能被应用于制备三乙膦酸铝的工艺中。
技术实现要素:[0013]
为了解决现有技术中存在的缺陷,本发明的目的在于提供一种制备三乙膦酸铝方
法及系统,利用微通道反应器在传质和传热方面的优势,减少副反应的发生,在提升生产的本质安全的同时提高产品的收率。
[0014]
为实现上述目的,本发明的制备三乙膦酸铝方法,包括以下步骤:
[0015]
1)将三氯化磷和无水乙醇按摩尔比1:3,分别泵入第一微通道反应器的反应区中进行酯化反应;反应结束,酯化粗产物从出料口进入气液分离釜,同时回收氯化氢气体和氯乙烷气体,得到亚磷酸二乙酯;
[0016]
2)将所述亚磷酸二乙酯和12%氨水按摩尔比1:1.05,分别泵入第二微通道反应器的反应区中进行胺化反应;反应结束,得到胺化物,胺化物与1.05摩尔当量的硫酸铝进行复分解反应,经过滤、干燥后得到三乙膦酸铝原药。
[0017]
进一步地,步骤1)所述的酯化反应,温度为
‑
10~80℃,停留反应时间为1s~30s。
[0018]
更进一步地,步骤2)所述的胺化反应温度为20~80℃,停留反应时间为10s~60s。
[0019]
为实现上述目的,本发明还提供一种制备三乙膦酸铝系统,包括第一微通道反应器以及第二微通道反应器,其中:
[0020]
所述第一微通道反应器用于酯化反应,所述第二微通道反应器用于胺化反应;
[0021]
所述第一微通道反应器和所述第二微通道反应器的反应流道内径为0.1mm~5mm。
[0022]
进一步地,所述第一微通道反应器的反应区a总体积为32ml~160ml,所述第二微通道反应器的反应区b总体积为32ml~160ml。
[0023]
进一步地,所述第一微通道反应器的材质为哈氏合金、钛合金、锆合金或碳化硅材质;所述第二微通道反应器的材质为316l不锈钢、哈氏合金、钛合金、锆合金或碳化硅材质。
[0024]
进一步地,所述第一微通道反应器的反应器模块数为4~20块,所述第二微通道反应器的反应器模块数为4~20块。
[0025]
本发明方法与现有技术相比,其有益效果在于:
[0026]
1、由于微通道反应器特殊的微通道尺寸和结构,利用其在传质和传热方面的优势,实现了三氯化磷和无水乙醇按照化学反应摩尔比进料,降低了原料成本;在非常广泛及温和的温度范围内(
‑
10~80℃),30s内即可完成酯化反应,且不会发生热量积聚而产生飞温、冲料现象,有效减少了副反应的发生,实现生产的本质安全。
[0027]
2、将胺化反应的时间从6~9小时缩短至60s以内,极大提高了生产效率,减少了三废排放量,降低了原料、能源成本;使三乙膦酸铝的含量提高至98.5%以上,收率提高至98%以上(以三氯化磷计)。
[0028]
3、微通道反应器采用“数增放大”的方式,不存在放大效应问题,可根据产量要求并行增加通道数量、缩短停留时间,实现连续化生产,达到万吨级的年通量。
附图说明
[0029]
图1为根据本发明的制备三乙膦酸铝方法流程图。
具体实施方式
[0030]
以下结合具体实施例对本发明做进一步详细说明。
[0031]
图1为根据本发明的制备三乙膦酸铝方法流程图,下面将参考图1,对本发明的制备三乙膦酸铝方法进行详细描述。
[0032]
(1)将三氯化磷和无水乙醇按摩尔比1:3,分别泵入第一微通道反应器的反应区a中进行酯化反应,第一微通道反应器的夹套用换热介质预先设置一定的反应温度,经过预定的停留反应时间,反应结束,酯化粗产物从出料口进入气液分离釜,同时回收氯化氢气体和氯乙烷气体,得到亚磷酸二乙酯;
[0033]
(2)将步骤1)制得亚磷酸二乙酯和12%氨水按摩尔比1:1.05,分别泵入第二微通道反应器的反应区b中进行胺化反应,第二微通道反应器的夹套用换热介质预先设置一定的反应温度,经过预定的停留反应时间,反应结束,得到胺化物,胺化物与1.05摩尔当量(以三氯化磷计)的硫酸铝进行复分解反应,经过滤、干燥后得到三乙膦酸铝原药。
[0034]
实施例1
[0035]
(1)微通道反应系统:第一微通道反应器和第二微通道反应器为碳化硅材质,反应流道内径为0.1mm。
[0036]
(2)酯化反应区a反应器模块数为4块,反应区a总体积32ml,第一微通道反应器夹套用换热介质设置反应温度为
‑
10℃。三氯化磷和无水乙醇摩尔比为1:3,同时分别泵入反应区a混合反应,控制流速,停留时间30s,出料,酯化粗产品进入气液分离釜,同时回收氯化氢和氯乙烷气体,得到亚磷酸二乙酯,分析含量为99.6%。
[0037]
(3)胺化反应区b反应器模块数为20块,反应区b总体积160ml,第二微通道反应器夹套用换热介质设置反应温度为20℃。亚磷酸二乙酯和12%氨水摩尔比为1:1.05,同时分别泵入反应区b混合反应,控制流速,停留时间10s,出料,胺化物进入合成釜与1.05摩尔当量(以三氯化磷计)的硫酸铝进行复分解反应,经过滤、干燥后得到三乙膦酸铝117.8g,含量98.5%,总收率98.3%(以1mol三氯化磷计)。
[0038]
实施例2
[0039]
(1)微通道反应系统:第一微通道反应器和第二微通道反应器为哈氏合金材质,反应流道内径均为5mm。
[0040]
(2)酯化反应区a反应器模块数为20块,反应区a总体积160ml,第一微通道反应器夹套用换热介质设置反应温度为80℃。三氯化磷和无水乙醇摩尔比为1:3,同时分别泵入反应区a混合反应,控制流速,停留时间1s,出料,酯化粗产品进入气液分离釜,同时回收氯化氢和氯乙烷气体,得到亚磷酸二乙酯,分析含量为99.9%。
[0041]
(3)胺化反应区b反应器模块数为4块,反应区b总体积32ml,第二微通道反应器夹套用换热介质设置反应温度为80℃。亚磷酸二乙酯和12%氨水摩尔比为1:1.05,同时分别泵入反应区b混合反应,控制流速,停留时间60s,出料,胺化物进入合成釜与1.05摩尔当量(以三氯化磷计)的硫酸铝进行复分解反应,经过滤、干燥后得到三乙膦酸铝117.8g,含量98.6%,总收率98.4%(以1mol三氯化磷计)。
[0042]
实施例3
[0043]
(1)微通道反应系统:第一微通道反应器为碳化硅材质,第二微通道反应器为316l材质,反应流道内径均为1mm。
[0044]
(2)酯化反应区a反应器模块数为10块,反应区a总体积80ml,第一微通道反应器夹套用换热介质设置反应温度为0℃。三氯化磷和无水乙醇摩尔比为1:3,同时分别泵入反应区a混合反应,控制流速,停留时间5s,出料,酯化粗产品进入气液分离釜,同时回收氯化氢和氯乙烷气体,得到亚磷酸二乙酯,分析含量为99.8%。
[0045]
(3)胺化反应区b反应器模块数为10块,反应区b总体积80ml,第二微通道反应器夹套用换热介质设置反应温度为30℃。亚磷酸二乙酯和12%氨水摩尔比为1:1.05,同时分别泵入反应区b混合反应,控制流速,停留时间20s,出料,胺化物进入合成釜与1.05摩尔当量(以三氯化磷计)的硫酸铝进行复分解反应,经过滤、干燥后得到三乙膦酸铝117.6g,含量98.8%,总收率98.5%(以1mol三氯化磷计)。
[0046]
实施例4
[0047]
(1)微通道反应系统:第一微通道反应器为钛合金材质,第二微通道反应器为316l材质,反应流道内径均为3mm。
[0048]
(2)酯化反应区a反应器模块数为12块,反应区a总体积96ml,第一微通道反应器夹套用换热介质设置反应温度为20℃。三氯化磷和无水乙醇摩尔比为1:3,同时分别泵入反应区a混合反应,控制流速,停留时间10s,出料,酯化粗产品进入气液分离釜,同时回收氯化氢和氯乙烷气体,得到亚磷酸二乙酯,分析含量为99.7%。
[0049]
(3)胺化反应区b反应器模块数为12块,反应区b总体积96ml,第二微通道反应器夹套用换热介质设置反应温度为40℃。亚磷酸二乙酯和12%氨水摩尔比为1:1.05,同时分别泵入反应区b混合反应,控制流速,停留时间40s,出料,胺化物进入合成釜与1.05摩尔当量(以三氯化磷计)的硫酸铝进行复分解反应,经过滤、干燥后得到三乙膦酸铝117.9g,含量98.7%,总收率98.6%(以1mol三氯化磷计)。
[0050]
实施例5
[0051]
(1)微通道反应系统:第一微通道反应器为锆合金材质,第二微通道反应器为碳化硅材质,反应流道内径均为0.5mm。
[0052]
(2)酯化反应区a反应器模块数为16块,反应区a总体积128ml,第一微通道反应器夹套用换热介质设置反应温度为40℃。三氯化磷和无水乙醇摩尔比为1:3,同时分别泵入反应区a混合反应,控制流速,停留时间20s,出料,酯化粗产品进入气液分离釜,同时回收氯化氢和氯乙烷气体,得到亚磷酸二乙酯,分析含量为99.8%。
[0053]
(3)胺化反应区b反应器模块数为10块,反应区b总体积80ml,第二微通道反应器夹套用换热介质设置反应温度为60℃。亚磷酸二乙酯和12%氨水摩尔比为1:1.05,同时分别泵入反应区b混合反应,控制流速,停留时间50s,出料,胺化物进入合成釜与1.05摩尔当量(以三氯化磷计)的硫酸铝进行复分解反应,经过滤、干燥后得到三乙膦酸铝117.9g,含量98.8%,总收率98.7%(以1mol三氯化磷计)。
[0054]
实施例6
[0055]
(1)微通道反应系统:第一微通道反应器为碳化硅材质,流道内径为0.5mm;第二微通道反应器为钛合金材质,反应流道内径为1mm。
[0056]
(2)酯化反应区a反应器模块数为18块,反应区a总体积144ml,第一微通道反应器夹套用换热介质设置反应温度为25℃。三氯化磷和无水乙醇摩尔比为1:3,同时分别泵入反应区a混合反应,控制流速,停留时间2s,出料,酯化粗产品进入气液分离釜,同时回收氯化氢和氯乙烷气体,得到亚磷酸二乙酯,分析含量为99.8%。
[0057]
(3)胺化反应区b反应器模块数为20块,反应区b总体积160ml,第二微通道反应器夹套用换热介质设置反应温度为35℃。亚磷酸二乙酯和12%氨水摩尔比为1:1.05,同时分别泵入反应区b混合反应,控制流速,停留时间10s,出料,胺化物进入合成釜与1.05摩尔当
量(以三氯化磷计)的硫酸铝进行复分解反应,经过滤、干燥后得到三乙膦酸铝117.9g,含量99.0%,总收率98.9%(以1mol三氯化磷计)。
[0058]
实施例7
[0059]
(1)微通道反应系统:第一微通道反应器为锆合金材质,反应流道内径为3mm;第二微通道反应器为锆合金材质,反应流道内径为1mm。
[0060]
(2)酯化反应区a反应器模块数为8块,反应区a总体积64ml,第一微通道反应器夹套用换热介质设置反应温度为
‑
5℃。三氯化磷和无水乙醇摩尔比为1:3,同时分别泵入反应区a混合反应,控制流速,停留时间10s,出料,酯化粗产品进入气液分离釜,同时回收氯化氢和氯乙烷气体,得到亚磷酸二乙酯,分析含量为99.7%。
[0061]
(3)胺化反应区b反应器模块数为10块,反应区b总体积80ml,第二微通道反应器夹套用换热介质设置反应温度为60℃。亚磷酸二乙酯和12%氨水摩尔比为1:1.05,同时分别泵入反应区b混合反应,控制流速,停留时间50s,出料,胺化物进入合成釜与1.05摩尔当量(以三氯化磷计)的硫酸铝进行复分解反应,经过滤、干燥后得到三乙膦酸铝117.3g,含量98.8%,总收率98.2%(以1mol三氯化磷计)。
[0062]
实施例8
[0063]
(1)微通道反应系统:第一微通道反应器为碳化硅材质,反应流道内径为0.2mm;第二微通道反应器为316l材质,反应流道内径为1mm。
[0064]
(2)酯化反应区a反应器模块数为20块,反应区a总体积160ml,第一微通道反应器夹套用换热介质设置反应温度为60℃。三氯化磷和无水乙醇摩尔比为1:3,同时分别泵入反应区a混合反应,控制流速,停留时间5s,出料,酯化粗产品进入气液分离釜,同时回收氯化氢和氯乙烷气体,得到亚磷酸二乙酯,分析含量为99.6%。
[0065]
(3)胺化反应区b反应器模块数为18块,反应区b总体积144ml,第二微通道反应器夹套用换热介质设置反应温度为26℃。亚磷酸二乙酯和12%氨水摩尔比为1:1.05,同时分别泵入反应区b混合反应,控制流速,停留时间10s,出料,胺化物进入合成釜与1.05摩尔当量(以三氯化磷计)的硫酸铝进行复分解反应,经过滤、干燥后得到三乙膦酸铝117.6g,含量98.5%,总收率98.2%(以1mol三氯化磷计)。
[0066]
实施例9
[0067]
(1)微通道反应系统:第一微通道反应器为哈氏合金材质,反应流道内径为0.2mm;第二微通道反应器为316l材质,反应流道内径为1mm。
[0068]
(2)酯化反应区a反应器模块数为18块,反应区a总体积144ml,第一微通道反应器夹套用换热介质设置反应温度为26℃。三氯化磷和无水乙醇摩尔比为1:3,同时分别泵入反应区a混合反应,控制流速,停留时间5s,出料,酯化粗产品进入气液分离釜,同时回收氯化氢和氯乙烷气体,得到亚磷酸二乙酯,分析含量为99.6%。
[0069]
(3)胺化反应区b反应器模块数为20块,反应区b总体积160ml,第二微通道反应器夹套用换热介质设置反应温度为40℃。亚磷酸二乙酯和12%氨水摩尔比为1:1.05,同时分别泵入反应区b混合反应,控制流速,停留时间10s,出料,胺化物进入合成釜与1.05摩尔当量(以三氯化磷计)的硫酸铝进行复分解反应,经过滤、干燥后得到三乙膦酸铝117.4g,含量98.5%,总收率98.0%(以1mol三氯化磷计)。
[0070]
实施例10
[0071]
(1)微通道反应系统:第一微通道反应器为碳化硅材质,反应流道内径为0.2mm;第二微通道反应器为316l材质,反应流道内径为1mm。
[0072]
(2)酯化反应区a反应器模块数为20块,反应区a总体积160ml,第一微通道反应器夹套用换热介质设置反应温度为26℃。三氯化磷和无水乙醇摩尔比为1:3,同时分别泵入反应区a混合反应,控制流速,停留时间5s,出料,酯化粗产品进入气液分离釜,同时回收氯化氢和氯乙烷气体,得到亚磷酸二乙酯,分析含量为99.5%。
[0073]
(3)胺化反应区b反应器模块数为16块,反应区b总体积128ml,第二微通道反应器夹套用换热介质设置反应温度为26℃。亚磷酸二乙酯和12%氨水摩尔比为1:1.05,同时分别泵入反应区b混合反应,控制流速,停留时间10s,出料,胺化物进入合成釜与1.05摩尔当量(以三氯化磷计)的硫酸铝进行复分解反应,经过滤、干燥后得到三乙膦酸铝117.4g,含量98.5%,总收率98.0%(以1mol三氯化磷计)。
[0074]
应理解,这些实施例是用于说明本发明的基本原理、主要特征和优点,而本发明不受实施例的限制。实施例中采用的实施条件可以根据具体要求做进一步调整,未注明的实施条件通常为常规实验中的条件。