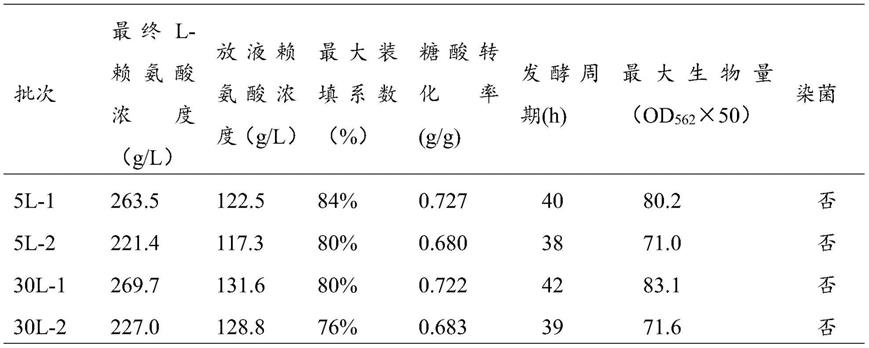
一种高密度发酵生产l
‑
赖氨酸的培养基及其方法
技术领域
1.本发明属于生物工程技术领域,尤其涉及一种高密度发酵生产l
‑
赖氨酸的培养基及其方法。
背景技术:2.赖氨酸(2、6
‑
二氨基己酸或α、ε
‑
二氨基己酸,lysine),具有l
‑
型和d
‑
型两种光学异构体,是生物体自身不能合成的必需氨基酸,必须从食物中补充,而且是8种必需氨基酸中唯一的仅l
‑
型成分才能有效利用的氨基酸。赖氨酸在动物性食物和豆类中含量丰富,在谷类食物中含量很低,因此l
‑
赖氨酸被广泛用于饲料添加剂、食品强化剂、除臭剂和医药产品等方面,其中90%以上的赖氨酸产品用作饲料添加剂。
3.为考虑生产经济性、尽可能节约发酵成本,目前微生物发酵生产赖氨酸使用的有机氮源多为玉米浆干粉、豆粕水解液等,但因其成分复杂,大分子蛋白居多,携带芽孢杆菌,个别成分如玉米浆中植酸含量高会抑制菌体生长等原因,常常会对发酵造成负面影响。为降低染菌几率,玉米浆干粉在使用前常需要进行多步灭菌操作,既增加了成本,又增加了工作量,反复多次灭菌也会造成有机氮源营养成分的缺失;发酵过程中玉米浆中不可溶性物质附着在罐体与搅拌轴上,既会影响视线,又会造成搅拌阻力增大,产生过多机械热的同时对设备造成损害;发酵过程中大分子蛋白的吸收利用需要耗费过多时间与能量,极大程度上影响了菌体的产酸效率,延长了发酵周期。同时,过多的蛋白导致发酵过程中大量产生泡沫,增加了消泡剂的使用,增大了成本,且消泡剂本身对微生物的毒害作用也会放大,过多的泡沫降低了发酵罐的装填系数,降低了设备的利用率。现有的直接利用小分子营养物质如成品小分子肽、氨基酸等发酵的方法因其价格高昂,并不适合工业化发展。
4.因此,如何得到一种能够适用于高密度发酵生产l
‑
赖氨酸的培养基,提高l
‑
赖氨酸糖酸转化率与产量、降低发酵染菌几率成为本领域迫切需要解决的一个技术问题。
技术实现要素:5.有鉴于此,本发明的目的在于提供一种高密度发酵生产l
‑
赖氨酸的培养基及其方法,有利于提高l
‑
赖氨酸发酵过程中的糖酸转化率与产量,降低发酵过程中染菌几率。
6.为了实现上述发明目的,本发明提供了以下技术方案:
7.本发明提供了一种高密度发酵生产l
‑
赖氨酸的培养基,所述培养基氮源包括有机氮源酶解得到的小分子多肽水溶液。
8.优选的,所述有机氮源包括玉米浆干粉和豆粕水解液。
9.优选的,所述玉米浆干粉制成玉米浆溶液后,依次添加胃蛋白酶、酸性植酸酶和碱性蛋白酶进行酶解。
10.优选的,所述玉米浆溶液的酶解条件为:胃蛋白酶酶解温度50~70℃,反应时间0.5~3.0h,反应ph1.5~5.0;酸性植酸酶酶解温度40~70℃,反应时间0.5~3.0h,反应ph3.0~6.0;碱性蛋白酶酶解温度45~70℃,反应时间0.5~3.0h,反应ph7.0~10.0。
11.优选的,所述豆粕水解液用碱性蛋白酶:中性蛋白酶质量比为1:0.5~2的复合酶进行酶解。
12.优选的,所述豆粕水解液的酶解条件为:酶解温度40~60℃,酶解时间10~200min,酶解ph7.0~9.0。
13.优选的,酶解后对酶解液进行过滤得到澄清肽溶液。
14.优选的,所述培养基用于种子培养,其原料包括:玉米浆干粉5~50g/l,豆粕水解液5~50ml/l,酵母粉2
‑
8g/l,葡萄糖20~60g/l,硫酸铵1~6g/l,硫酸镁0.5~4g/l,磷酸二氢钾2~8g/l,硫酸亚铁5~30mg/l,硫酸锰5~30mg/l,vb混合液1~3ml/l,硫酸锌2~10mg/l,五水硫酸铜1~7mg/l,生物素0.1~3.0mg/l。
15.优选的,所述培养基用于发酵培养,其原料包括:玉米浆干粉5~50g/l,豆粕水解液10~30ml/l,葡萄糖10~80g/l,硫酸铵1~10g/l,硫酸镁0.3~2.0g/l,磷酸二氢钾1~5g/l,氯化钾0.3~5.0g/l,硫酸亚铁5~30mg/l,硫酸锰5~30mg/l,vb混合液1~5ml/l,硫酸锌0.2~2.0mg/l,五水硫酸铜0.1~5.0mg/l,生物素0.02~1.0mg/l。
16.本发明还提供了一种利用上述培养基高密度发酵生产l
‑
赖氨酸的方法,包括:在发酵过程中同步流加添加小分子多肽水溶液和溶菌酶的混合液。
17.与现有技术相比,本发明具有如下有益效果:
18.本发明通过对发酵培养基中的玉米浆、豆粕水解液等复杂的有机氮源利用蛋白酶与酸性植酸酶酶解成分子量较小的多肽、氨基酸、磷酸盐等,经过滤等操作得到含有小分子多肽的水溶液,并将其用于后续发酵生产,小分子多肽水溶液的流加添加保证了菌体在各个生长阶段均处于最适营养浓度,避免了营养浪费,提高了营养物质利用率。
19.本发明利用酶解后的肽溶液作为氮源,可减少菌体生长的耗能,加快菌体生长繁殖,提高生物量。同时本发明高密度发酵过程中采用小分子多肽水溶液与溶菌酶混合流加添加,溶菌酶的添加增加了细胞膜的通透性,加速了产物排出;并在生物量稳定期添加一定量的携氧剂正十二烷,携氧剂正十二烷的添加保证了高菌体密度下溶氧的需求,最终达到提高l
‑
赖氨酸糖酸转化率与产量、降低发酵染菌几率等目的。
具体实施方式
20.本发明提供了一种高密度发酵生产l
‑
赖氨酸的培养基,所述培养基氮源包括有机氮源酶解得到的小分子多肽水溶液。
21.本发明中的有机氮源包括玉米浆干粉,玉米浆干粉内在质量与玉米浆相同,蛋白质和微量元素含量高,是微生物生长培育普遍应用的有机氮源。本发明对玉米浆干粉的具体来源不作限定。
22.本发明中的有机氮源还包括豆粕水解液,豆粕水解液又称微生物dn制剂、豆浓,可替代酵母粉、蛋白胨等发酵行业现用的高价原辅料,是微生物发酵过程中普遍应用的有机氮源,主要用于氨基酸发酵。本发明对豆粕水解液的具体来源不作限定。
23.本发明对玉米浆干粉进行酶解。本发明将玉米浆干粉用去离子水溶解,制成玉米浆溶液,玉米浆溶液质量分数优选为5~10%,进一步优选为质量分数7%。
24.本发明在玉米浆溶液中依次添加胃蛋白酶、酸性植酸酶和碱性蛋白酶进行酶解。本发明利用胃蛋白酶将玉米浆溶液中的蛋白质分解为小的肽片段,利用酸性植酸酶将玉米
浆溶液中的植酸及其盐类水解为肌醇与磷酸(盐),利用碱性蛋白酶进一步水解蛋白质分子肽链生成更小的肽片段或氨基酸。其中,胃蛋白酶酶解温度为50~70℃,优选为60~65℃,反应时间为0.5~3.0h,优选为1.5~2.0h,反应ph为1.5~5.0,优选为2.0~3.5,加酶量为10~100u/g,优选为30~50u/g;酸性植酸酶酶解温度40~70℃,优选为55~60℃,反应时间为0.5~3.0h,优选为1.5~2.0h,反应ph为3.0~6.0,优选为4.0~5.0,加酶量为10~500u/g,优选为100~260u/g;碱性蛋白酶酶解温度为45~70℃,优选为55~60℃,反应时间为0.5~3.0h,优选为1.5~2.0h,反应ph为7.0~10.0,优选为8.5~9.0,加酶量为5000
‑
50000u/g,优选为20000~35000u/g。
25.本发明对豆粕水解液进行酶解。本发明将豆粕水解液用去离子水稀释,制成豆粕蛋白溶液,豆粕蛋白溶液质量分数优选为5~20%,进一步优选为质量分数为15%;在豆粕蛋白溶液中添加复合酶酶解,复合酶中碱性蛋白酶:中性蛋白酶的质量比为1:0.5~2.0,优选为1:1.5。本发明利用上述复合酶对豆粕水解液中的蛋白质大分子充分水解为小分子肽片段或氨基酸。其中,酶解温度为40~60℃,优选为50~55℃,酶解时间为10~200min,优选为85~105min,酶解ph为7.0~9.0,优选为7.5~8.0,酶添加量为5000~20000u/g,优选为10000~15000u/g。
26.本发明对上述酶解得到的酶解液分别进行过滤处理,得到澄清肽溶液。作为一种可选的实施方式,酶解液可采用陶瓷膜或金属微滤膜过滤,截留分子量为1000
‑
5000mw,优选为3000mw。本发明对酶解液的具体过滤方式不作限定,保证过滤后得到澄清肽溶液即可。
27.本发明可以先对有机氮源进行大批量酶解处理,再根据处理前后微生物可利用营养物质含量不变的原则,将有机氮源的使用量换算成处理后肽溶液的使用体积(v3):
28.对玉米浆干粉(固体有机氮源)处理得到的肽溶液添加量(v3)的换算方法:
[0029][0030]
式中m表示培养基中应添加的有机氮源质量,ρ2表示酶解后氮源密度,m1表示待酶解氮源质量,v2表示酶解后肽溶液体积,ρ1表示底物浓度,v1表示底物体积。
[0031]
对豆粕水解液(液体有机氮源)处理得到的肽溶液添加量(v3)的换算方法:
[0032][0033]
式中v表示培养基中应添加的有机氮源体积,ρ2表示酶解后氮源密度,v1表示待酶解液体积,v2表示酶解后肽溶液体积,ρ1表示底物浓度,v1表示底物体积。
[0034]
本发明中培养基包括种子培养基和发酵培养基,两种培养基对玉米浆干粉和豆粕水解液的处理方式完全相同。
[0035]
本发明对酶解玉米浆干粉过程作出详细说明:
[0036]
取一定量的玉米蛋白粉,用去离子水溶解,将其制成一定质量分数的玉米浆溶液,采用凯氏定氮法粗测溶液中蛋白总量,并确定用酶量;用hcl溶液调节ph值至胃蛋白酶作用的最适ph值,加热至胃蛋白酶作用的温度。将一定量酶用磷酸二氢钾缓冲液溶解活化后加入到蛋白液中,启动反应。反应每隔一定时间测定并调节ph值至起始值,达到预定时间后停止加热搅拌,酶解结束;
[0037]
利用高效液相色谱检测植酸含量,再次用hcl溶液调节ph值至酸性植酸酶作用的
最适ph值,加热至酸性植酸酶最适反应温度,可加适量硫酸镁加速反应,酶解结束;
[0038]
将酶解液用naoh溶液调节至碱性蛋白酶的最适ph值,加热至碱性蛋白酶最适反应温度,水解一定时间至酶解结束。
[0039]
取酶解液置于过滤器中,循环过滤,得澄清肽溶液,测量体积后低温(4℃)保存待用。
[0040]
本发明对酶解豆粕水解液过程作出详细说明:
[0041]
取一定体积的豆粕水解液,用去离子水稀释,制成一定质量分数的豆粕蛋白溶液,采用凯氏定氮法粗测溶液中蛋白总量,并确定用酶量;用naoh溶液调节至复合酶作用的最适ph值,加热至复合酶最适反应温度,将适量复合酶用磷酸二氢钾缓冲液溶解活化后加入到蛋白液中,启动反应。反应每隔一定时间测定并调节ph值至起始值,达到预定时间后加热至酶失活温度,自然降温,酶解结束。
[0042]
取酶解液置于过滤器中,循环过滤,得澄清肽溶液,测量体积后低温(4℃)保存待用。
[0043]
上述对玉米浆干粉酶解过程和豆粕水解液酶解过程的说明仅作为对酶解过程的解释,并非本发明对酶解过程的限定。
[0044]
本发明用于种子培养的培养基包括:玉米浆干粉5~50g/l,豆粕水解液5~50ml/l,酵母粉2~8g/l,葡萄糖20~60g/l,硫酸铵1~6g/l,硫酸镁0.5~4g/l,磷酸二氢钾2~8g/l,硫酸亚铁5~30mg/l,硫酸锰5~30mg/l,vb混合液1~3ml/l,硫酸锌2~10mg/l,五水硫酸铜1~7mg/l,生物素0.1~3.0mg/l。
[0045]
优选的,本发明用于种子培养的培养基包括:玉米浆干粉15~35g/l,豆粕水解液15~35ml/l,酵母粉4
‑
6g/l,葡萄糖35~50g/l,硫酸铵2~4g/l,硫酸镁2~3g/l,磷酸二氢钾4~6g/l,硫酸亚铁18~25mg/l,硫酸锰18~25mg/l,vb混合液1.5~2ml/l,硫酸锌4~8mg/l,五水硫酸铜3~5mg/l,生物素1~1.5mg/l。
[0046]
更优选的,本发明用于种子培养的培养基为:玉米浆干粉15~35g/l,豆粕水解液15~35ml/l,酵母粉4
‑
6g/l,葡萄糖35~50g/l,硫酸铵2~4g/l,硫酸镁2~3g/l,磷酸二氢钾4~6g/l,硫酸亚铁18~25mg/l,硫酸锰18~25mg/l,vb混合液1.5~2ml/l,硫酸锌4~8mg/l,五水硫酸铜3~5mg/l,生物素1~1.5mg/l。
[0047]
本发明用于发酵培养的培养基包括:玉米浆干粉5~50g/l,豆粕水解液10~30ml/l,葡萄糖10~80g/l,硫酸铵1~10g/l,硫酸镁0.3~2.0g/l,磷酸二氢钾1~5g/l,氯化钾0.3~5.0g/l,硫酸亚铁5~30mg/l,硫酸锰5~30mg/l,v
b
混合液1~5ml/l,硫酸锌0.2~2.0mg/l,五水硫酸铜0.1~5.0mg/l,生物素0.02~1.0mg/l。
[0048]
优选的,本发明用于发酵培养的培养基包括:玉米浆干粉15~25g/l,豆粕水解液15~25ml/l,葡萄糖40~60g/l,硫酸铵4~6g/l,硫酸镁1~1.5g/l,磷酸二氢钾2~3g/l,氯化钾2~5g/l,硫酸亚铁15~20mg/l,硫酸锰15~20mg/l,v
b
混合液2~3ml/l,硫酸锌1~1.5mg/l,五水硫酸铜2~3mg/l,生物素0.5~0.8mg/l。
[0049]
更优选的,本发明用于发酵培养的培养基为:玉米浆干粉15~25g/l,豆粕水解液15~25ml/l,葡萄糖40~60g/l,硫酸铵4~6g/l,硫酸镁1~1.5g/l,磷酸二氢钾2~3g/l,氯化钾2~5g/l,硫酸亚铁15~20mg/l,硫酸锰15~20mg/l,v
b
混合液2~3ml/l,硫酸锌1~1.5mg/l,五水硫酸铜2~3mg/l,生物素0.5~0.8mg/l。
[0050]
本发明利用上述培养基进行高密度发酵生产l
‑
赖氨酸。本发明中高密度发酵生产l
‑
赖氨酸的发酵罐内生物量(od
562
×
50)≥80,溶氧为30%
‑
50%,优选为45%。
[0051]
本发明利用上述培养基进行高密度发酵生产l
‑
赖氨酸的过程包括菌株活化、种子培养、发酵培养。
[0052]
菌株活化包括:将生产菌从甘油保菌管中接到一代斜面培养基上,30~35℃恒温培养22~24h,再取一代斜面上少量菌体接到二代斜面30~35℃恒温培养22~24h,并取二代斜面所有菌体用于种子罐培养。
[0053]
种子培养条件包括:选取上述种子培养基,通过流加氨水控制ph为7.0~7.2,温度为32~34℃,溶氧为30~50%;当溶氧低于30%时交替提高转速和风量,种子成熟指标为od
562
×
50≥30。
[0054]
发酵培养条件包括:选取上述发酵培养基,通过流加氨水控制ph为7.0~7.2,温度为35~37℃,溶氧为30~50%;当溶氧低于30%时交替提高转速和风量,当发酵罐残糖降到0.5~1.0g/l时开始补流加葡萄糖,整个发酵过程糖控制在3~10g/l,葡萄糖浓度为750~850g/l。
[0055]
优选的,本发明在上述发酵过程中还可以流加添加小分子多肽水溶液和溶菌酶。本发明对高密度发酵过程小分子多肽水溶液与溶菌酶的流加方式作出详细解释:
[0056]
本发明发酵过程中对小分子多肽水溶液与溶菌酶混匀后同步添加:按发酵培养基配方比例取所需体积的玉米浆干粉酶解小分子多肽水溶液与豆粕水解液小分子多肽水溶液,混匀后等体积分成2份,一份与发酵培养基中其他成分一同灭菌后一次性倒入发酵罐内,另一份调节ph至6.4~6.6,灭菌并冷却后无菌操作下与溶菌酶混合,在发酵过程中流加使用。所述混合液中溶菌酶用量为0.08~0.12mg/l,进一步优选为0.1mg/l。所述流加方式为无反馈式定量流加,优选为连续脉冲式流加;所述流加量为每小时流加发酵液体积的0.4~0.6%,优选为0.5%。本发明发现,通过该流加方式可以有效解除发酵初期的高营养浓度对菌体生长反馈抑制,通过营养分割后连续流加,在没有增加总体营养的条件下,提高了发酵后期菌种活性和营养物质利用率,解决了因发酵中后期因营养缺乏造成菌体活力下降的问题,进而提高l
‑
赖氨酸发酵过程中的糖酸转化率与产量,降低发酵过程中染菌几率。
[0057]
本发明在发酵过程刚刚进入生物量稳定期时添加携氧剂,添加方式为灭菌后无菌操作下一次性倒入发酵罐。作为一种可选的实施方式,携氧剂可为正十二烷,携氧剂的添加量为30~70mg/l,进一步优选为50~55mg/l。本发明所述生物量稳定期即为菌种生长稳定期。本发明对生物量稳定期的判断方式不作限定。本发明在生物量稳定期添加携氧剂,保证了高菌体密度下溶氧的需求,进而达到提高l
‑
赖氨酸糖酸转化率与产量、降低发酵染菌几率的目的。
[0058]
本发明在具体实施例中选择的菌种为谷氨酸棒杆菌(corynebacterium glutamicum),购自天津科技大学代谢工程实验室。本发明对谷氨酸棒杆菌的具体来源不作限定。
[0059]
本发明在具体实施例中选择的玉米浆干粉购自山东大凯生物科技有限公司;豆粕水解液购自山东玉宝生物科技股份有限公司。本发明对玉米浆干粉和豆粕水解液的具体来源不作限定。
[0060]
本发明在具体实施例中选择的酶为:碱性蛋白酶(50000
‑
100000u/g),购自四川省
山野生物科技有限公司;中性蛋白酶(100000
‑
500000u/g),购自南宁庞博生物工程有限公司;胃蛋白酶(1000
‑
5000u/g),购自苏州科铭生物技术有限公司;酸性植酸酶(5000
‑
20000u/g),购自上海鼓臣生物有限公司;溶菌酶(50000
‑
100000u/g),购自山东尊宏生物科技有限公司;正十二烷,购自上海阿拉丁生化科技股份有限公司。本发明对各类酶及试剂的具体来源不作限定。
[0061]
下面结合实施例对本发明提供的技术方案进行详细的说明,但是不能把它们理解为对本发明保护范围的限定。
[0062]
实施例1
[0063]
取100g的玉米浆干粉,用去离子水溶解,将其制成质量分数为7%的玉米浆溶液,采用凯氏定氮法粗测溶液中蛋白总量为47.5g。玉米浆溶液用hcl溶液调节至ph值2.5,于恒温水浴锅中加热至60℃。将0.23g胃蛋白酶用10ml磷酸二氢钾缓冲液(0.1m)溶解活化后加入到玉米浆溶液中,启动反应。反应每隔20min测定并调节ph值至起始值,反应2.5h后,停止加热搅拌,酶解结束;
[0064]
利用高效液相色谱检测植酸含量为0.3g,再次用hcl溶液调节ph值至4.0,于恒温水浴锅中加热至55℃,加入0.016g酸性植酸酶,并加0.05%(重量体积比)的硫酸镁加速反应1h,酶解结束;
[0065]
将酶解液用naoh溶液调节ph值至8.0,于恒温水浴锅中加热至55℃,加入9.5g碱性蛋白酶水解2h,酶解结束。
[0066]
取酶解液置于截留分子量为3000mw的陶瓷膜过滤器中,循环过滤,得澄清肽溶液1.02l,低温(4℃)保存待用。
[0067]
实施例2
[0068]
本实施例与实施例1的区别在于:
[0069]
玉米浆溶液用hcl溶液调节至ph值2,于恒温水浴锅中加热至65℃,加入胃蛋白酶反应2h后,停止加热搅拌,酶解结束;
[0070]
再次用hcl溶液调节ph值至5.0,于恒温水浴锅中加热至60℃,加入酸性植酸酶和硫酸镁反应0.5h,酶解结束;
[0071]
将酶解液用naoh溶液调节ph值至9.0,于恒温水浴锅中加热至60℃,加入碱性蛋白酶水解1.5h,酶解结束。
[0072]
取酶解液置于截留分子量为4000mw的陶瓷膜过滤器中,循环过滤,得澄清肽溶液970ml,低温(4℃)保存待用。
[0073]
实施例3
[0074]
取100ml豆粕水解液,用去离子水稀释,制成质量分数为15%的豆粕蛋白溶液,采用凯氏定氮法粗测溶液中蛋白总量为16.6g,复合酶中碱性蛋白酶:中性蛋白酶的质量比为1:1.5,碱性蛋白酶用量为0.474g,中性蛋白酶用量为0.711g;用naoh溶液调节ph值至8.0,于恒温水浴锅中加热至50℃,将复合酶用10ml磷酸二氢钾缓冲液(0.1m)溶解活化后加入到蛋白液中,启动反应。反应每隔10min测定并调节ph值至起始值,反应1h后加热至90℃使酶失活,自然降温,酶解结束。
[0075]
取酶解液置于截留分子量为3000mw的陶瓷膜过滤器中,循环过滤,得澄清肽溶液530ml,低温(4℃)保存待用。
[0076]
实施例4
[0077]
本实施例与实施例3的区别在于:
[0078]
豆粕水解液用naoh溶液调节ph值至7.5,于恒温水浴锅中加热至55℃,将复合酶用磷酸二氢钾缓冲液溶解活化后加入到蛋白液中,启动反应。反应每隔10min测定并调节ph值至起始值,反应150min后加热至酶失活,自然降温,酶解结束。
[0079]
取酶解液置于截留分子量为4000mw的陶瓷膜过滤器中,循环过滤,得澄清肽溶液510ml,低温(4℃)保存待用。
[0080]
实施例5
[0081]
种子培养基包括:玉米浆干粉20g/l,豆粕水解液20ml/l,酵母粉4g/l,葡萄糖40g/l,硫酸铵4g/l,硫酸镁2g/l,磷酸二氢钾4g/l,硫酸亚铁20mg/l,硫酸锰20mg/l,vb混合液2ml/l,硫酸锌6mg/l,五水硫酸铜4mg/l,生物素1.5mg/l。
[0082]
玉米浆干粉和豆粕水解液分别采用实施例1和实施例3中的方法进行酶解。
[0083]
种子培养基制备(1l用量):
[0084]
(1)按上述培养基配方(1l),分别称量除玉米浆干粉、豆粕水解液和葡萄糖之外的培养基原料,混合后用去离子水溶解;
[0085]
(2)按上述公式量取玉米浆干粉酶解液0.204l和豆粕水解液酶解液0.106l,加入到步骤(1)的混合液中,用去离子水定容至0.8l,于121℃灭菌15min,备用;
[0086]
(3)称量40g葡萄糖,用去离子水定容至0.1l,于121℃灭菌15min,备用;
[0087]
(4)将步骤(2)
‑
(3)中的溶液混合即为种子培养基。
[0088]
(上述种子培养基在具体使用时还需要添加0.1l二代种子清洗液。)
[0089]
实施例6
[0090]
种子培养基为:玉米浆干粉24g/l;豆粕水解液20ml/l;酵母粉5g/l;葡萄糖40g/l;硫酸铵1.5g/l;硫酸镁3g/l;磷酸二氢钾6g/l;硫酸亚铁20mg/l;硫酸锰20mg/l;vb混合液2ml/l;硫酸锌6mg/l;五水硫酸铜6mg/l;生物素1.5mg/l。
[0091]
玉米浆干粉和豆粕水解液分别采用实施例1和实施例3中的方法进行酶解。
[0092]
种子培养基制备(1l用量):
[0093]
(1)按上述培养基配方(1l),分别称量除玉米浆干粉、豆粕水解液和葡萄糖之外的培养基原料,混合后用去离子水溶解;
[0094]
(2)按上述公式量取玉米浆干粉酶解液0.2448l和豆粕水解液酶解液0.106l,加入步骤(1)的混合液中,用去离子水定容至0.8l,于121℃灭菌15min,备用;
[0095]
(3)称量40g葡萄糖,用去离子水定容至0.1l,于121℃灭菌15min,备用;
[0096]
(4)将步骤(2)
‑
(3)中的溶液混合即为种子培养基。
[0097]
(上述种子培养基在具体使用时还需要添加0.1l二代种子清洗液。)
[0098]
实施例7
[0099]
种子培养基为:玉米浆干粉24g/l;豆粕水解液20ml/l;酵母粉5g/l;葡萄糖40g/l;硫酸铵1.5g/l;硫酸镁3g/l;磷酸二氢钾6g/l;硫酸亚铁20mg/l;硫酸锰20mg/l;vb混合液2ml/l;硫酸锌6mg/l;五水硫酸铜6mg/l;生物素1.5mg/l。
[0100]
玉米浆干粉和豆粕水解液分别采用实施例2和实施例4中的方法进行酶解。
[0101]
种子培养基制备(1l用量):
[0102]
(1)按上述培养基配方(1l),分别称量除玉米浆干粉、豆粕水解液和葡萄糖之外的培养基原料,混合后用去离子水溶解;
[0103]
(2)按上述公式量取玉米浆干粉酶解液0.2328l和豆粕水解液酶解液0.102l,加入步骤(1)的混合液中,用去离子水定容至0.8l,于121℃灭菌15min,备用;
[0104]
(3)称量40g葡萄糖,用去离子水定容至0.1l,于121℃灭菌15min,备用;
[0105]
(4)将步骤(2)
‑
(3)中的溶液混合即为种子培养基。
[0106]
(上述种子培养基在具体使用时还需要添加0.1l二代种子清洗液。)
[0107]
实施例8
[0108]
发酵培养基包括:玉米浆干粉20g/l,豆粕水解液25ml/l,葡萄糖40g/l,硫酸铵6g/l,硫酸镁1g/l,磷酸二氢钾2.5g/l,氯化钾1.5g/l,硫酸亚铁16mg/l,硫酸锰16mg/l,vb混合液2ml/l,硫酸锌1mg/l,五水硫酸铜1.5mg/l,生物素0.75mg/l。
[0109]
玉米浆干粉和豆粕水解液分别采用实施例1和实施例3中的方法进行酶解。
[0110]
发酵培养基制备(1l用量):
[0111]
(1)按上述培养基配方(1l),分别称量除玉米浆干粉、豆粕水解液和葡萄糖之外的培养基原料,混合后用去离子水溶解;
[0112]
(2)按上述公式量取玉米浆干粉酶解液0.204l和豆粕水解液的酶解液0.1325l,加入步骤(1)的混合液中,用去离子水定容至0.75l,于121℃灭菌15min,备用;
[0113]
(3)称量40g葡萄糖,用去离子水定容至0.04l,于121℃灭菌15min,备用;
[0114]
(4)将步骤(2)
‑
(3)中的溶液混合即为发酵培养基。
[0115]
(上述发酵培养基在具体使用时还需要添加0.21l种子液。)
[0116]
实施例9
[0117]
发酵培养基包括:玉米浆干粉20g/l,豆粕水解液25ml/l,葡萄糖40g/l,硫酸铵6g/l,硫酸镁1g/l,磷酸二氢钾2.5g/l,氯化钾1.5g/l,硫酸亚铁16mg/l,硫酸锰16mg/l,vb混合液2ml/l,硫酸锌1mg/l,五水硫酸铜1.5mg/l,生物素0.75mg/l。
[0118]
玉米浆干粉和豆粕水解液分别采用实施例1和实施例3中的方法进行酶解。
[0119]
发酵培养基制备(1l用量):
[0120]
(1)按上述公式量取玉米浆干粉酶解液0.204l和豆粕水解液的酶解液0.1325l,混匀后等体积分成两份,一份调节ph至6.5后装入补料瓶,另一份备用。
[0121]
(2)按上述培养基配方(1l),分别称量除玉米浆干粉、豆粕水解液和葡萄糖之外的培养基原料与步骤(1)中备用小分子多肽水溶液混匀,并用去离子水定容至0.537l。
[0122]
(3)称量40g葡萄糖,用去离子水定容至0.04l,于121℃灭菌15min,备用;
[0123]
将步骤(2)
‑
(3)中的溶液混合即为发酵培养基。
[0124]
(上述发酵培养基在具体使用时还需要添加0.25475l种子液;补料瓶中0.16825l酶解混合液按每小时发酵液体积的0.5%连续脉冲式流加)
[0125]
实施例10
[0126]
发酵培养基包括:玉米浆干粉30g/l;豆粕水解液20ml/l;葡萄糖30g/l;硫酸铵5g/l;硫酸镁0.87g/l;磷酸二氢钾2.5g/l;氯化钾0.53g/l;硫酸亚铁20mg/l;硫酸锰20mg/l;vb混合液3ml/l;硫酸锌0.6mg/l;五水硫酸铜0.6mg/l;生物素0.85mg/l
[0127]
玉米浆干粉和豆粕水解液分别采用实施例2和实施例4中的方法进行酶解。
[0128]
发酵培养基制备(1l用量):
[0129]
(1)按上述培养基配方(1l),分别称量除玉米浆干粉、豆粕水解液和葡萄糖之外的培养基原料,混合后用去离子水溶解;
[0130]
(2)按上述公式量取玉米浆干粉酶解液0.291l和豆粕水解液的酶解液0.102l,加入步骤(1)的混合液中,用去离子水定容至0.75l,于121℃灭菌15min,备用;
[0131]
(3)称量40g葡萄糖,用去离子水定容至0.04l,于121℃灭菌15min,备用;
[0132]
(4)将步骤(2)
‑
(3)中的溶液混合即为发酵培养基。
[0133]
(上述发酵培养基在具体使用时还需要添加0.21l种子液。)
[0134]
实施例11
[0135]
发酵培养基包括:玉米浆干粉30g/l;豆粕水解液20ml/l;葡萄糖30g/l;硫酸铵5g/l;硫酸镁0.87g/l;磷酸二氢钾2.5g/l;氯化钾0.53g/l;硫酸亚铁20mg/l;硫酸锰20mg/l;vb混合液3ml/l;硫酸锌0.6mg/l;五水硫酸铜0.6mg/l;生物素0.85mg/l
[0136]
玉米浆干粉和豆粕水解液分别采用实施例2和实施例4中的方法进行酶解。
[0137]
发酵培养基制备(1l用量):
[0138]
(1)按上述公式量取玉米浆干粉酶解液0.291l和豆粕水解液的酶解液0.102l,混匀后等体积分成两份,一份调节ph至6.5后装入补料瓶,另一份备用。
[0139]
(2)按上述培养基配方,分别称量除玉米浆干粉、豆粕水解液和葡萄糖之外的培养基原料与步骤(1)中备用小分子多肽水溶液混匀,并用去离子水定容至0.537l。
[0140]
(3)称量40g葡萄糖,用去离子水定容至0.04l,于121℃灭菌15min,备用;
[0141]
(4)将步骤(2)
‑
(3)中的溶液混合即为发酵培养基。
[0142]
(上述发酵培养基在具体使用时还需要添加0.2265l种子液;补料瓶中0.1965l酶解混合液按每小时添加发酵液体积的0.5%连续脉冲式流加。)
[0143]
实施例12
[0144]
本实施例给出了高密度发酵生产l
‑
赖氨酸的方法,包括菌株活化、种子培养、发酵培养。
[0145]
菌株活化:取甘油保菌管中菌株置于斜面培养基上,用接种环在试管斜面上划匀,于32℃倒置恒温培养24h,为一代种子;用接种环取一环一代种子,在茄形瓶斜面化匀,于32℃倒置恒温培养24h,为二代种子。
[0146]
斜面培养基为:葡萄糖5g/l;牛肉膏10g/l;酵母粉10g/l;尿素2.5g/l;氯化钠2g/l;磷酸二氢钾1g/l;硫酸镁0.3g/l;琼脂粉25g/l。
[0147]
种子培养:初始发酵温度为34℃,通过流加氨水控制ph为7.2,溶氧40%,当溶氧低于30%时交替提高转速和风量,种子成熟指标为od
562
×
50≥30,即接发酵。
[0148]
发酵培养:发酵过程中溶氧控制在40%,发酵温度为37℃,当溶氧低于30%时交替提高转速和风量,通过流加氨水控制ph为7.0,当发酵罐残糖降到0.8g/l时开始补流加糖,整个发酵过程糖控制在6g/l。
[0149]
l
‑
赖氨酸产量采用薄层层析法测定,其中层析载体为层析硅胶(gf254)
‑
薄板,购自浙江省四甲生化塑料厂;层析液为正丁醇:水:冰乙酸=4:2:1。
[0150]
实施例13
[0151]
本实施例采用实施例12中的发酵条件进行高密度发酵生产l
‑
赖氨酸:采用实施例
5的种子培养基组分和实施例8的发酵培养基组分。
[0152]
种子培养采用5l发酵罐,配制2l用量种子培养基:除葡萄糖外组分混合液定容至1.6l灭菌,葡萄糖定容至200ml单独灭菌,用200ml无菌水将二代种子清洗,将灭菌后的混合液和二代种子清洗液在严格无菌操作下倒入罐内,同时倒入葡萄糖溶液,培养至种子成熟接发酵罐。
[0153]
发酵培养采用5l发酵罐,接种量为20%(600ml),配制3l用量发酵培养基:除葡萄糖外组分混合液定容至2.2l灭菌,葡萄糖定容至200ml单独灭菌,将灭菌后的混合液、种子液在严格无菌操作下倒入罐内,同时倒入葡萄糖溶液,进行发酵培养。
[0154]
进行两批重复发酵实验,取两次实验数据平均值记录并命名为5l
‑
1。测定最终l
‑
赖氨酸浓度、中途放液赖氨酸浓度、糖酸转化率、发酵周期、发酵罐最大装填系数、最大生物量。
[0155]
实施例14
[0156]
本实施例采用实施例12中的发酵条件进行高密度发酵生产l
‑
赖氨酸:采用实施例5的种子培养基组分和实施例8的发酵培养基组分。
[0157]
种子培养采用5l发酵罐,配制3l用量种子培养基:除葡萄糖外组分混合液定容至2.6l灭菌,葡萄糖定容至200ml单独灭菌,用200ml无菌水将二代种子清洗,将灭菌后的混合液和二代种子清洗液在严格无菌操作下倒入罐内,同时倒入葡萄糖溶液,培养至种子成熟接发酵罐。
[0158]
发酵培养采用30l发酵罐,接种量为20%(2.8l),配制14l用量发酵培养基:除葡萄糖外组分混合液定容至10.6l灭菌,葡萄糖定容至600ml单独灭菌,将灭菌后的混合液、种子液在严格无菌操作下倒入罐内,同时倒入葡萄糖溶液,进行发酵培养。
[0159]
同样进行两批重复发酵实验,取两次实验数据平均值记录并命名为30l
‑
1。测定最终l
‑
赖氨酸浓度、中途放液赖氨酸浓度、糖酸转化率、发酵周期、发酵罐最大装填系数、最大生物量。
[0160]
实施例15
[0161]
本实施例采用实施例12中的发酵条件进行高密度发酵生产l
‑
赖氨酸:采用实施例5的种子培养基组分和实施例8的发酵培养基组分,但是种子培养基和发酵培养基中有机氮源直接采用未经酶解的玉米浆干粉与豆粕水解液。
[0162]
种子与发酵培养步骤与方法与实施例13相同。
[0163]
同样进行两批重复发酵实验,取两次实验数据平均值记录并命名为5l
‑
2。测定最终l
‑
赖氨酸浓度、中途放液赖氨酸浓度、糖酸转化率、发酵周期、发酵罐最大装填系数、最大生物量。
[0164]
实施例16
[0165]
本实施例采用实施例12中的发酵条件进行高密度发酵生产l
‑
赖氨酸:采用实施例5的种子培养基组分和实施例8的发酵培养基组分,但是种子培养基和发酵培养基中有机氮源直接采用未经酶解的玉米浆干粉与豆粕水解液。
[0166]
种子与发酵培养步骤与方法与实施例14相同。
[0167]
同样进行两批重复发酵实验,取两次实验数据平均值记录并命名为30l
‑
2。测定最终l
‑
赖氨酸浓度、中途放液赖氨酸浓度、糖酸转化率、发酵周期、发酵罐最大装填系数、最大
生物量。
[0168]
表1各批次发酵结果对照
[0169][0170]
由表1可知,培养基有机氮源进行酶解处理的5l
‑
1和30l
‑
1的最终l
‑
赖氨酸浓度分别为263.5g/l和269.7g/l,比培养基有机氮源未经酶解处理的5l
‑
2和30l
‑
2分别提高了19.0%和18.8%;培养基有机氮源进行酶解处理的5l
‑
1和30l
‑
1的放液赖氨酸浓度浓度分别为122.5g/l和131.6g/l,比培养基有机氮源未经酶解处理的5l
‑
2和30l
‑
2分别提高了4.4%和2.2%;培养基有机氮源进行酶解处理的5l
‑
1和30l
‑
1的糖酸转化率分别为0.727g/g和0.722g/g,比培养基有机氮源未经酶解处理的5l
‑
2和30l
‑
2分别提高了6.9%和5.7%。并且培养基有机氮源进行酶解处理的5l
‑
1和30l
‑
1的最大装罐系数、发酵周期和最大生物量均比培养基有机氮源未经酶解处理的5l
‑
2和30l
‑
2高。
[0171]
表明:本发明所述方法发酵生产l
‑
赖氨酸可有效提高生物量、糖酸转化率与l
‑
赖氨酸产量,并且当发酵罐体积由5l增加至30l时,发酵反应的最大生物量、糖酸转化率与l
‑
赖氨酸产量并未降低,染菌几率也未增加,设备利用率具有较大的提升。
[0172]
实施例17
[0173]
本实施例对不同的种子培养基和发酵培养基组合进行高密度发酵(除培养基选择、溶菌酶和携氧剂是否添加外,其他发酵条件均相同)。
[0174]
对照组:采用实施例5的种子培养基组分和实施例8的发酵培养基组分,种子培养基和发酵培养基中有机氮源直接采用未经酶解的玉米浆干粉与豆粕水解液且发酵过程中不添加溶菌酶和携氧剂;
[0175]
实验组:采用实施例5/6/7的种子培养基配方,实施例8/9/10/11的发酵培养基配方及添加方法,在生物量稳定期添加/不添加携氧剂正十二烷,并对相应实验组进行编号。例:编号5
‑8‑
1、5
‑8‑
2、6
‑9‑
1分别代表:使用实施例5的种子培养基配方,实施例8的发酵培养基配方与添加方法,在生物量稳定期添加正十二烷;使用实施例5的种子培养基配方,实施例8的发酵培养基配方与添加方法,在生物量稳定期不添加正十二烷;使用实施例6的种子培养基配方,实施例9的发酵培养基配方与方法,在生物量稳定期添加正十二烷,以此类推得所有实验组编号。
[0176]
每组进行两批重复发酵实验,取两次实验数据平均值记录。测定最终l
‑
赖氨酸浓度、中途放液赖氨酸浓度、糖酸转化率、发酵周期、发酵罐最大装填系数、最大生物量,并记录是否染菌。
[0177]
表2不同批次发酵结果对照
[0178][0179][0180]
由表2可知,培养基使用小分子多肽水溶液替代传统玉米浆与豆浓使l
‑
赖氨酸产量、转化率、生物量均有较大程度的提升,设备利用率提升了4个百分点;优化后不同的种子培养基并未对最终发酵结果造成影响,因此可以遵循物料节省原则选择尽量少的方案。
[0181]
携氧剂正十二烷的添加对l
‑
赖氨酸产量与转化率均有较小提升,同时缩短了发酵
周期,提高了效率,如5
‑8‑
2较5
‑8‑
1l
‑
赖氨酸产量提升了1.2%,转化率提高了0.4%,发酵周期缩短了1h;溶菌酶与多肽水溶液的流加添加较大程度的提高了l
‑
赖氨酸的产量与转换率,如7
‑9‑
1较7
‑8‑
1产量提高了1.3%,转化率提高了2.5%;发酵培养基营养物质浓度提高并未提高转化率,甚至在一定程度上有所下降,产量与生物量出现了较大提升。如6
‑
11
‑
2较6
‑9‑
2产量提升了1.5%,生物量提升了1.2%,转化率下降了0.9%。除此之外,培养基有机氮源进行酶解处理的优化组均为出现染菌状况,对照组出现了染菌,极大地影响了发酵效率。
[0182]
综上,本发明发酵生产l
‑
赖氨酸可有效提高生物量、糖酸转化率与l
‑
赖氨酸产量,并能很好地控制染菌几率,设备利用率有了一定程度的提升,发酵周期提前了1h,这对工业化发酵生产l
‑
赖氨酸具有积极意义。
[0183]
以上所述仅是本发明的优选实施方式,应当指出,对于本技术领域的普通技术人员来说,在不脱离本发明原理的前提下,还可以做出若干改进和润饰,这些改进和润饰也应视为本发明的保护范围。