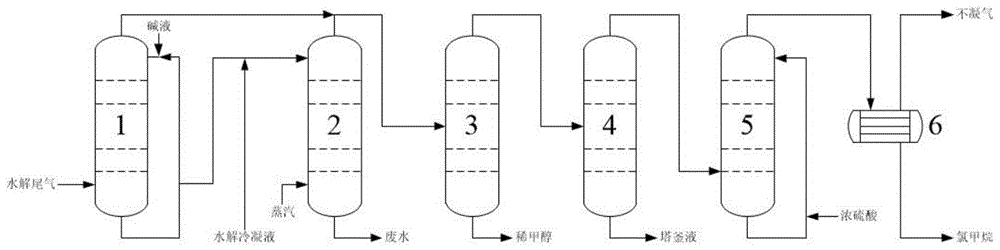
本实用新型属于化工
技术领域:
,尤其涉及一种草甘膦生产尾气中氯甲烷的清洁回收系统。
背景技术:
:草甘膦是一种高效、低毒、广谱、灭生性、非选择性除草剂,具有优良的生物特性。目前国内草甘磷主流生产工艺有两条路线:烷基酯法(甘氨酸法)和亚氨基二乙酸法(ida法)。国外的生产工艺则主要是美国孟山都公司的亚氨基二乙酸法。我国草甘膦主要采用以甘氨酸和亚磷酸二甲酯为主要原料的烷基酯法生产,该方法以甲醇为反应溶剂,在催化剂三乙胺的存在下,甘氨酸首先和聚甲醛反应形成n,n-二羟甲基甘氨酸,再与亚磷酸二甲酯反应后加盐酸水解生成草甘膦以及副产物甲缩醛和氯甲烷。甘氨酸法草甘膦合成液水解尾气主要成分为水、甲缩醛、甲醇、氯化氢及氯甲烷混合物,该尾气的回收过程在草甘膦行业简称为溶剂回收。而合成液是指由甲醇、多聚甲醛(或其他甲醛源)、甘氨酸(或以氯乙酸为起点原料的其他原料)、亚磷酸二甲酯(或其他烷基磷酸酯)等原材料经解聚、缩合、酯化反应得到的主要成分为n-甲氧基烷基酯甲基甘氨酸等有机磷中间体(草甘膦前体)的混合溶液。专利cn101012146b公开了一种由氯甲烷混合气体分离回收氯甲烷的方法,通过在至少由两个装填有吸附剂的吸附塔系统中,对含氯甲烷的混合气体以在时序上交错的方式在各吸附塔中分别经吸附、均压和解吸的变压吸附过程除去杂质获得氯甲烷产品,但该方法对吸附设备的压力及吸附剂的要求较高,分离回收是效率及效果低,对设备要求较高。为解决吸附法回收氯甲烷存在的种种问题,现有技术开始采用精馏法回收草甘膦生产尾气中的氯甲烷,但目前精馏获得的氯甲烷粗品存在水分、甲醇、甲缩醛等组分偏高的问题,提高了后续粗品精制的难度。技术实现要素:有鉴于此,本实用新型的目的在于提供一种草甘膦生产尾气中氯甲烷的清洁回收系统,本实用新型解决了现有工艺在回收草甘膦生产尾气的过程中存在的氯甲烷粗品中水分、甲醇、甲缩醛等组分偏高的问题,减少了干燥工序的硫酸使用量和废硫酸的处理量。本实用新型提供了一种草甘膦生产尾气中氯甲烷的清洁回收系统,包括:中和塔;与所述中和塔的塔釜液出口相连接的汽提塔,所述中和塔的塔釜液出口与所述汽提塔的连接管路上设置有水解冷凝液进液口;分别与所述中和塔的出气口和所述汽提塔的出气口相连接的分离塔;与所述分离塔的塔顶出料口相连接的脱氯甲烷塔;与所述脱氯甲烷塔的塔顶出料口相连接的浓硫酸干燥塔;与所述浓硫酸干燥塔的出气口相连接的冷凝装置。优选的,所述浓硫酸干燥塔包括串联设置的多级浓硫酸干燥塔,上一级浓硫酸干燥塔的出气口与下一级浓硫酸干燥塔的进气口相连接。优选的,所述冷凝装置包括串联设置的多级冷凝器,上一级冷凝器的不凝气出口与下一级冷凝器的气口相连接。优选的,还包括设置在所述脱氯甲烷塔的塔顶出料口与所述浓硫酸干燥塔之间的氯甲烷缓冲罐,所述氯甲烷缓冲罐的进料口与所述脱氯甲烷塔的塔顶出料口相连接,所述氯甲烷缓冲罐的出料口与所述浓硫酸干燥塔的进气口相连接。本实用新型提供了一种草甘膦生产尾气中氯甲烷的清洁回收工艺,包括以下步骤:a)草甘膦合成液水解尾气在中和塔中与碱液混合反应,得到中和塔塔釜液和中和尾气;b)所述中和塔塔釜液与草甘膦酸化合成液水解冷凝液混合后,在汽提塔中进行汽提,得到气相产物和汽提塔塔釜液;c)所述中和尾气和所述气相产物在分离塔中进行精馏分离,得到分离塔塔顶气相和分离塔塔釜液;d)所述分离塔塔顶气相在脱氯甲烷塔中进行精馏分离,得到气态氯甲烷粗品和脱氯甲烷塔塔釜液;e)所述气态氯甲烷粗品在浓硫酸干燥塔中进行干燥,得到干燥的气态氯甲烷;f)所述干燥的气态氯甲烷在冷凝装置中进行冷凝,得到液态氯甲烷。优选的,步骤a)中,所述混合反应的温度为70~90℃;所述混合反应的压力为-5~10kpa;所述草甘膦合成液水解尾气在中和塔中的停留时间为5~20s。优选的,步骤b)中,所述汽提塔的塔釜温度为100~108℃;所述汽提塔的塔顶温度为70~100℃;所述汽提塔的压力为-5~30kpa。优选的,步骤c)中,所述分离塔的回流比为1~4;所述分离塔的塔釜温度为65~85℃;所述分离塔的塔顶温度为50~70℃;所述分离塔的压力为-10~10kpa。优选的,步骤d)中,所述脱氯甲烷塔的回流比为1~3.5;所述脱氯甲烷塔的塔釜温度为55~70℃;所述脱氯甲烷塔的塔顶温度为-10~-20℃;所述脱氯甲烷塔的压力为0~80kpa。优选的,步骤e)中,所述浓硫酸干燥塔的压力为0~15kpa。与现有技术相比,本实用新型提供了一种草甘膦生产尾气中氯甲烷的清洁回收系统。本实用新型提供的清洁回收系统包括:中和塔;与所述中和塔的塔釜液出口相连接的汽提塔,所述中和塔的塔釜液出口与所述汽提塔的连接管路上设置有水解冷凝液进液口;分别与所述中和塔的出气口和所述汽提塔的出气口相连接的分离塔;与所述分离塔的塔顶出料口相连接的脱氯甲烷塔;与所述脱氯甲烷塔的塔顶出料口相连接的浓硫酸干燥塔;与所述浓硫酸干燥塔的出气口相连接的冷凝装置。在本实用新型中,草甘膦生产过程中水解工序产生的尾气首先在中和塔中与碱液混合反应,得到中和塔塔釜液和中和尾气;然后,利用草甘膦酸化合成液水解冷凝液(稀甲醇)对所述中和塔排出的塔釜液进行ph值调节(ph值控制在6~14),完成ph值调节的中和塔塔釜液在汽提塔中进行汽提,得到气相产物和汽提塔塔釜液;接着,所述中和尾气和所述气相产物在分离塔中进行精馏分离,得到分离塔塔顶气相和分离塔塔釜液;之后,所述分离塔塔顶气相在脱氯甲烷塔中进行精馏分离,得到气态氯甲烷粗品和脱氯甲烷塔塔釜液;接着,所述气态氯甲烷粗品在浓硫酸干燥塔中进行干燥,得到干燥的气态氯甲烷;最后,所述干燥的气态氯甲烷在冷凝装置中进行冷凝,得到液态氯甲烷产品。本实用新型提供的回收系统通过对草甘膦生产尾气进行中和、汽提和多效精馏,不但提高了氯甲烷的回收率,还大幅降低了氯甲烷粗品中的水分、甲醇和甲缩醛含量,精馏后的氯甲烷气体粗品中除了氯甲烷、二甲醚、空气之外基本上不含有其它组分,提高了氯甲烷粗品的品质,可避免由于甲醇、甲缩醛等低沸物混入氯甲烷气体中所造成的氯甲烷粗品后续进行硫酸干燥时硫酸消耗较高的问题,可使下游硫酸干燥工艺的硫酸使用量和废硫酸的处理量降低55%以上;同时,精馏后的氯甲烷粗品不再需要水洗、碱洗工序,可减少废水量,以及减少相应工序的设备、电仪投入,降低投资成本。附图说明为了更清楚地说明本实用新型实施例或现有技术中的技术方案,下面将对实施例或现有技术描述中所需要使用的附图作简单地介绍,显而易见地,下面描述中的附图仅仅是本实用新型的实施例,对于本领域普通技术人员来讲,在不付出创造性劳动的前提下,还可以根据提供的附图获得其他的附图。图1是本实用新型实施例提供的氯甲烷清洁回收系统流程简图;图2是本实用新型实施例提供的氯甲烷清洁回收系统前半段工艺流程图;图3是本实用新型实施例提供的氯甲烷清洁回收系统后半段工艺流程图。具体实施方式下面将结合本实用新型实施例中的附图,对本实用新型实施例中的技术方案进行清楚、完整地描述,显然,所描述的实施例仅仅是本实用新型一部分实施例,而不是全部的实施例。基于本实用新型中的实施例,本领域普通技术人员在没有做出创造性劳动前提下所获得的所有其他实施例,都属于本实用新型保护的范围。本实用新型提供了一种草甘膦生产尾气中氯甲烷的清洁回收系统,包括:中和塔;与所述中和塔的塔釜液出口相连接的汽提塔,所述中和塔的塔釜液出口与所述汽提塔的连接管路上设置有水解冷凝液进液口;分别与所述中和塔的出气口和所述汽提塔的出气口相连接的分离塔;与所述分离塔的塔顶出料口相连接的脱氯甲烷塔;与所述脱氯甲烷塔的塔顶出料口相连接的浓硫酸干燥塔;与所述浓硫酸干燥塔的出气口相连接的冷凝装置。参见图1,图1是本实用新型实施例提供的草甘膦合成液水解尾气回收系统流程简图。其中,1表示中和塔,2表示汽提塔,3表示分离塔,4表示脱氯甲烷塔,5表示浓硫酸干燥塔,6表示冷凝装置。本实用新型提供的回收系统包括中和塔1、汽提塔2、分离塔3、脱氯甲烷塔4、浓硫酸干燥塔5和冷凝装置6。其中,中和塔1用于去除草甘膦生产尾气中的氯化氢,其上设置有水解尾气进口、碱液进口、出气口和塔釜液出口。在本实用新型提供的一个实施例中,中和塔1为喷淋塔,所述喷淋塔设置有塔釜液循环喷淋管道,使塔釜液可对水解尾气进行循环吸收。在本实用新型中,汽提塔2用于对上游工序产生的草甘膦酸化合成液水解冷凝液(稀甲醇)和中和塔1外排的塔釜液进行汽提分离,其上设置有进液口、蒸汽进口、出气口和废水出口,汽提塔2的进液口与中和塔1的塔釜液出口相连接,其连接管道上设置有水解冷凝液进液口。在本实用新型中,上游工序产生的草甘膦酸化合成液水解冷凝液可通过所述水解冷凝液进液口进入到系统中,与中和塔1外排的塔釜液进行混合,以实现对中和塔1塔釜液的ph值调节(ph值控制在6~14)。在本实用新型中,分离塔3用于对中和塔1排出中的中和尾气和汽提塔2排出的气相产物进行精馏分离,其上设置有进气口、塔顶出料口和塔釜液出口,分离塔3的进气口分别与中和塔1的出气口和汽提塔2的出气口相连接。在本实用新型中,脱氯甲烷塔4用于对分离塔3分离出的塔顶气相进行精馏分离,回收其中的氯甲烷。脱氯甲烷塔4上设置有进料口、塔顶出料口和塔釜液出口,脱氯甲烷塔4的进料口与分离塔3的塔顶出料口相连接。在本实用新型中,浓硫酸干燥塔5用于对脱氯甲烷塔4分离出的气态氯甲烷粗品进行浓硫酸干燥,其上设置有进气口、出气口、浓硫酸进口和塔釜液出口。在本实用新型提供的一个实施例中,浓硫酸干燥塔5为喷淋塔,所述喷淋塔设置有塔釜液循环喷淋管道,使塔釜液可对气态氯甲烷粗品进行循环干燥。在本实用新型提供的一个实施例中,浓硫酸干燥塔5包括串联设置的多级浓硫酸干燥塔,上一级浓硫酸干燥塔的出气口与下一级浓硫酸干燥塔的进气口相连接。在本实用新型中,冷凝装置6用于对浓硫酸干燥塔5排出的干燥气态氯甲烷进行冷凝,使其成为液态氯甲烷。冷凝装置6上设置有进气口、冷凝液出口和不凝气出口。在本实用新型提供的一个实施例中,冷凝装置6包括串联设置的多级冷凝器,上一级冷凝器的不凝气出口与下一级冷凝器的气口相连接。参见图2和图3,图2是本实用新型实施例提供的氯甲烷清洁回收系统前半段工艺流程图,图3是本实用新型实施例提供的氯甲烷清洁回收系统后半段工艺流程图。其中,1表示中和塔,2表示汽提塔,2-1表示汽提塔一级预热器,2-2表示汽提塔二级预热器,2-3表示汽提塔三级预热器,2-4表示汽提塔冷却器,3表示分离塔,3-1表示分离塔冷凝器,3-2表示分离塔回流罐,3-3表示低沸风机,3-4表示风机后冷凝器,3-5表示低沸物中间罐,3-6表示分离塔再沸器,4表示脱氯甲烷塔,4-1表示脱氯甲烷塔冷凝器,4-2表示脱氯甲烷塔回流罐,4-3表示脱氯甲烷塔再沸器,5-1表示氯甲烷缓冲罐,5-2表示浓硫酸干燥塔前换热器,5-3表示一级浓硫酸干燥塔,5-4表示二级浓硫酸干燥塔,5-5表示三级浓硫酸干燥塔,5-6表示四级浓硫酸干燥塔,5-7表示浓硫酸干燥塔后除沫器,5-8表示干燥氯甲烷缓冲罐,6-1表示氯甲烷压缩机,6-2表示一级冷凝器,6-3表示二级冷凝器,6-4表示三级冷凝器,6-5表示氯甲烷冷凝液罐,6-6表示冷凝装置后除沫器,ls(lowpressuresteam)表示低压蒸汽。在本实用新型提供的一个实施例中,所述回收系统还包括汽提塔一级预热器2-1、汽提塔二级预热器2-2和汽提塔三级预热器2-3。在本实用新型中,中和塔1外排的塔釜液与草甘膦酸化合成液水解冷凝液混合后依次经过汽提塔一级预热器2-1、汽提塔二级预热器2-2和汽提塔三级预热器2-3预热后,再进入汽提塔2中进行汽提分离。其中,汽提塔一级预热器2-1的热源优选为下游的低压甲醇精馏塔分离出的甲醇产品,汽提塔二级预热器2-2的热源优选为下游的高压甲醇精馏塔分离出的甲醇产品,汽提塔三级预热器2-3的热源优选为蒸汽冷凝水。在本实用新型提供的一个实施例中,所述回收系统还包括汽提塔冷却器2-4,汽提塔2外排的塔釜液(废水)经过汽提塔冷却器2-4冷却后,用泵输送至下游的废水处理装置。在本实用新型提供的一个实施例中,所述回收系统还包括分离塔冷凝器3-1、分离塔回流罐3-2、低沸风机3-3、风机后冷凝器3-4和低沸物中间罐3-5。在本实用新型中,分离塔3塔顶气相经分离塔冷凝器3-1部分冷凝,冷凝液收集至分离塔回流罐3-2后用泵输送,部分回流,部分进脱氯甲烷塔4;未被分离塔冷凝器3-1冷凝的气相经低沸风机3-3提压后,输送至风机后冷凝器3-4,冷凝液收集至低沸物中间罐3-5;未被风机后冷凝器3-4冷凝的气相输送至脱氯甲烷塔4,低沸物中间罐3-5中的冷凝液也用泵输送至脱氯甲烷塔4。在本实用新型提供的一个实施例中,所述回收系统还包括分离塔再沸器3-6,用于对分离塔3的塔釜液进行加热,使塔釜液升温气化。分离塔再沸器3-6的热源优选为下游的低压甲醇精馏塔塔顶排出的甲醇蒸汽。在本实用新型提供的一个实施例中,所述回收系统还包括脱氯甲烷塔冷凝器4-1和脱氯甲烷塔回流罐4-2。在本实用新型中,脱氯甲烷塔4塔顶部分气体通过管道输送至脱氯甲烷塔冷凝器4-1中进行冷凝,冷凝产生的冷凝液回收至脱氯甲烷塔回流罐4-2,之后回流至脱氯甲烷塔4;未被冷凝的不凝性气体与脱氯甲烷塔4塔顶采出气相一起作为氯甲烷产品输送至浓硫酸干燥塔5。在本实用新型提供的一个实施例中,所述回收系统还包括脱氯甲烷塔再沸器4-3,用于对脱氯甲烷塔4的塔釜液进行加热,使塔釜液升温气化。脱氯甲烷塔再沸器4-3的热源优选为蒸汽冷凝水。在本实用新型提供的一个实施例中,所述回收系统还包括氯甲烷缓冲罐5-1,用于对脱氯甲烷塔4塔顶排出气态氯甲烷粗品进行缓存,氯甲烷缓冲罐5-1的进料口与脱氯甲烷塔4的塔顶出料口相连接,氯甲烷缓冲罐5-1的出料口与浓硫酸干燥塔5的进气口相连接。在本实用新型提供的一个实施例中,所述回收系统还包括浓硫酸干燥塔前换热器5-2,待进入浓硫酸干燥塔5的气态氯甲烷粗品通过浓硫酸干燥塔前换热器5-2与浓硫酸干燥塔5排出的干燥气态氯甲烷进行换热。在本实用新型提供的一个实施例中,所述回收系统中的浓硫酸干燥塔5具体包括串联设置的一级浓硫酸干燥塔5-3,二级浓硫酸干燥塔5-4,三级浓硫酸干燥塔5-5和四级浓硫酸干燥塔5-6,一级浓硫酸干燥塔5-3的出气口与二级浓硫酸干燥塔5-4的进气口相连接,二级浓硫酸干燥塔5-4的出气口与三级浓硫酸干燥塔5-5的进气口相连接,三级浓硫酸干燥塔5-5的出气口与四级浓硫酸干燥塔5-6的进气口相连接。在本实用新型中,来自脱氯甲烷塔4的气态氯甲烷粗品依次在一级浓硫酸干燥塔5-3,二级浓硫酸干燥塔5-4,三级浓硫酸干燥塔5-5和四级浓硫酸干燥塔5-6中进行浓硫酸干燥处理,上述四个浓硫酸干燥塔的塔釜通过管道相连通,塔釜的浓硫酸可通过所述管道进入到上一级浓硫酸干燥塔的塔釜中。在本实用新型提供的一个实施例中,所述回收系统还包括浓硫酸干燥塔后除沫器5-7和干燥氯甲烷缓冲罐5-8。在本实用新型中,浓硫酸干燥塔5排出的干燥气态氯甲烷经浓硫酸干燥塔后除沫器5-7除沫后进入干燥氯甲烷缓冲罐5-8中,浓硫酸干燥塔后除沫器5-7和干燥氯甲烷缓冲罐5-8中收集的液相返回到浓硫酸干燥塔5中,干燥氯甲烷缓冲罐5-8中的气相(干燥气态氯甲烷)进入到冷凝工序。在本实用新型中,浓硫酸干燥塔后除沫器5-7的运行温度优选控制在≤-5℃。在本实用新型提供的一个实施例中,所述回收系统还包括氯甲烷压缩机6-1,待进入冷凝装置6的气态氯甲烷先在氯甲烷压缩机6-1中进行压缩,然后再在冷凝装置6中进行冷凝。在本实用新型提供的一个实施例中,所述回收系统中的冷凝装置6具体包括串联设置的一级冷凝器6-2、二级冷凝器6-3和三级冷凝器6-4,一级冷凝器6-2的不凝气出口与二级冷凝器6-3的进气口相连接,二级冷凝器6-3的不凝气出口与三级冷凝器6-4的进气口相连接。在本实用新型中,来自浓硫酸干燥塔5或者氯甲烷压缩机6-1的干燥气态氯甲烷进入到一级冷凝器6-2中进行冷凝,未被冷凝的不凝气进入到二级冷凝器6-3中继续进行冷凝,未被冷凝的不凝气进入到三级冷凝器6-4中继续进行冷凝,每一级冷凝器冷凝得到的冷凝液即为本实用新型回收得到液态氯甲烷产品。在本实用新型提供的一个实施例中,所述回收系统还包括氯甲烷冷凝液罐6-5,用于对冷凝装置6产生的冷凝液(液态氯甲烷)进行收集。在本实用新型提供的一个实施例中,所述回收系统还包括冷凝装置后除沫器6-6,用于对冷凝装置6外排的不凝气进行除沫,冷凝装置6中产生的液相通过管道输送到氯甲烷冷凝液罐6-5中。在本实用新型中,冷凝装置后除沫器6-6的运行温度优选控制在≤-5℃。为更清楚起见,以图2和图3所述的氯甲烷清洁回收系统为例,所述回收系统的具体工作过程如下:来自草甘膦生产过程中产生的水解尾气通过管道输送至中和塔1,与新鲜液碱、循环碱液在塔中进行气液中和反应,塔顶气相通过管道输送至分离塔3,塔釜液输送至汽提塔2。来自中和塔1的塔釜液与草甘膦酸化合成液水解冷凝液混合后用泵输送至汽提塔一级预热器2-1,用热甲醇预热后,用管道输送至汽提塔二级预热器2-2,用热甲醇进行预热后,用管道输送至汽提塔三级预热器2-3,用蒸汽冷凝水预热后,用管道输送至汽提塔2。汽提塔2塔釜接入低压蒸汽(ls),对塔内物料进行汽提,塔顶气相用管道输送至分离塔3,塔釜废水经过汽提塔冷却器2-4冷却后,用泵输送至下游的废水处理装置。来自中和塔1和汽提塔2的气相在分离塔3中进行分离,塔顶气相经分离塔冷凝器3-1部分冷凝,冷凝液收集至分离塔回流罐3-2后用泵输送,部分回流,部分进脱氯甲烷塔4;未被冷凝的气相进低沸风机3-3提压后,用管道输送至风机后冷凝器3-4,冷凝液收集至低沸物中间罐3-5,气相用管道输送至脱氯甲烷塔4,低沸物中间罐3-5中的收集的冷凝液也用泵输送至脱氯甲烷塔4。分离塔3的塔釜稀甲醇在分离塔再沸器3-6中用甲醇蒸汽进行加热后,用泵输送至下游的低压甲醇精馏塔。来自分离塔3的不凝性气体和低沸物在脱氯甲烷塔4中进行精馏,塔顶部分气体输送至脱氯甲烷塔冷凝器4-1,冷凝液回收至脱氯甲烷塔回流罐4-2,不凝性气体与塔顶采出气相作为氯甲烷粗品一起用管道输送至氯甲烷缓冲罐5-1;脱氯甲烷塔回流罐4-2收集的冷凝液回流至脱氯甲烷塔4。塔釜液在脱氯甲烷塔再沸器4-3中用蒸汽冷凝水进行加热后,用泵输送至下游的甲缩醛精馏塔。来自脱氯甲烷塔4塔顶的氯甲烷粗品通过管道输送至氯甲烷缓冲罐5-1,缓冲罐内的氯甲烷粗品通过管道进入浓硫酸干燥塔前换热器5-2与进氯甲烷压缩机6-1前氯甲烷热交换后进入一级浓硫酸干燥塔5-3,塔内氯甲烷通过浓硫酸酸洗后由管道输送至二级浓硫酸干燥塔5-4,之后再依次通过三级浓硫酸干燥塔5-5和四级浓硫酸干燥塔5-6后,进入浓硫酸干燥塔后除沫器5-7;浓硫酸干燥塔后除沫器5-7中的气相进入干燥氯甲烷缓冲罐5-8,液相返回到四级浓硫酸干燥塔5-6中;干燥氯甲烷缓冲罐5-8中的液相返回到四级浓硫酸干燥塔5-6中,气相在浓硫酸干燥塔前换热器5-2中进行热交换后进入氯甲烷压缩机6-1。来自干燥氯甲烷缓冲罐5-8的干燥气态氯甲烷进行换热后在氯甲烷压缩机6-1中进行压缩,压缩气在一级冷凝器6-2中进行水冷,冷凝液输送到氯甲烷冷凝液罐6-5中,不凝气进入二级冷凝器6-3;不凝气在二级冷凝器6-3中进行盐冷,冷凝液输送到氯甲烷冷凝液罐6-5中,不凝气进入三级冷凝器6-4;不凝气在三级冷凝器6-4中进行深冷,冷凝液输送到氯甲烷冷凝液罐6-5中,不凝气进入冷凝装置后除沫器6-6;不凝气在冷凝装置后除沫器6-6中进行除沫,产生的液相送到氯甲烷冷凝液罐6-5中,气体放空。本实用新型还提供了一种草甘膦生产尾气中氯甲烷的清洁回收工艺,包括以下步骤:a)草甘膦合成液水解尾气在中和塔中与碱液混合反应,得到中和塔塔釜液和中和尾气;b)所述中和塔塔釜液与草甘膦酸化合成液水解冷凝液混合后,在汽提塔中进行汽提,得到气相产物和汽提塔塔釜液;c)所述中和尾气和所述气相产物在分离塔中进行精馏分离,得到分离塔塔顶气相和分离塔塔釜液;d)所述分离塔塔顶气相在脱氯甲烷塔中进行精馏分离,得到气态氯甲烷粗品和脱氯甲烷塔塔釜液;e)所述气态氯甲烷粗品在浓硫酸干燥塔中进行干燥,得到干燥的气态氯甲烷;f)所述干燥的气态氯甲烷在冷凝装置中进行冷凝,得到液态氯甲烷。在本实用新型提供的回收工艺中,草甘膦合成液水解尾气首先在中和塔中与碱液混合反应,得到中和塔塔釜液和中和尾气。其中,所述中和塔优选为本实用新型上述技术方案所介绍的回收系统中的中和塔;所述混合反应的温度优选为70~90℃,更优选为74℃,具体可为70℃、71℃、72℃、73℃、74℃、75℃、76℃、77℃、78℃、79℃、80℃、81℃、82℃、83℃、84℃、85℃、86℃、87℃、88℃、89℃或90℃;所述混合反应的压力优选为-5~10kpa,更优选为0kpa,具体可为-5kpa、-4kpa、-3kpa、-2kpa、-1kpa、0kpa、1kpa、2kpa、3kpa、4kpa、5kpa、6kpa、7kpa、8kpa、9kpa或10kpa;所述碱液的循环流量优选为20~40m3/h,更优选为28m3/h,具体可为20m3/h、21m3/h、22m3/h、23m3/h、24m3/h、25m3/h、26m3/h、27m3/h、28m3/h、29m3/h、30m3/h、31m3/h、32m3/h、33m3/h、34m3/h、35m3/h、36m3/h、37m3/h、38m3/h、39m3/h或40m3/h;所述草甘膦合成液水解尾气在中和塔中的停留时间优选为5~20s,具体可为5s、6s、7s、8s、9s、10s、11s、12s、13s、14s、15s、16s、17s、18s、19s或20s。在本实用新型提供的回收工艺中,从所述中和塔排出的塔釜液与草甘膦酸化合成液水解冷凝液(稀甲醇)进行混合,之后混合液在汽提塔中进行汽提,得到气相产物和汽提塔塔釜液。其中,所述混合的目的是利用草甘膦酸化合成液水解冷凝液对所述中和塔排出的塔釜液进行ph值调节,所述ph值优选控制在6~14;所述汽提塔优选为本实用新型上述技术方案所介绍的回收系统中的汽提塔;所述汽提塔的塔釜温度优选为100~108℃,更优选为100~105℃,最优选为103℃,具体可为100℃、101℃、102℃、103℃、104℃、105℃、106℃、107℃或108℃;所述汽提塔的塔顶温度优选为70~100℃,具体可为70℃、75℃、80℃、85℃、90℃、92℃、95℃或100℃;所述汽提塔的压力优选为-5~30kpa,更优选为0~10kpa,最优选为5kpa,具体可为-5kpa、-2kpa、0kpa、5kpa、10kpa、15kpa、20kpa、25kpa或30kpa。在本实用新型提供的回收工艺中,所述中和尾气和所述气相产物在分离塔中进行精馏分离,得到分离塔塔顶气相和分离塔塔釜液。其中,所述分离塔优选为本实用新型上述技术方案所介绍的回收系统中的分离塔;所述分离塔的回流比优选为1~4,更优选为2.2~2.3,具体可为1、1.2、1.5、1.8、2、2.2、2.3、2.5、2.8、3、3.2、3.5、3.7或4;所述分离塔的塔釜温度优选为65~85℃,具体可为65℃、70℃、75℃、80℃或85℃;所述分离塔的塔顶温度为50~70℃,具体可为50℃、55℃、60℃、65℃或70℃;所述分离塔的压力优选为-10~10kpa,更优选为5kpa,具体可为-10kpa、-5kpa、0kpa、5kpa或10kpa。在本实用新型提供的回收工艺中,所述分离塔塔顶气相在脱氯甲烷塔中进行精馏分离,得到气态氯甲烷粗品和脱氯甲烷塔塔釜液。其中,所述脱氯甲烷塔优选为本实用新型上述技术方案所介绍的回收系统中的脱氯甲烷塔;所述脱氯甲烷塔的回流比优选为1~3.5,更优选为1.2~1.5,具体可为1、1.2、1.5、1.7、2、2.3、2.5、2.7、3、3.2或3.5;所述脱氯甲烷塔的塔釜温度优选为55~70℃,更优选为60~65℃,具体可为55℃、58℃、60℃、62℃、65℃、67℃或70℃;所述脱氯甲烷塔的塔顶温度优选为-10~-20℃,更优选为-15~-17℃,具体可为-10℃、-11℃、-12℃、-13℃、-14℃、-15℃、-16℃、-17℃、-18℃、-19℃或-20℃;所述脱氯甲烷塔的压力优选为0~80kpa,更优选为55kpa,具体可为0kpa、5kpa、10kpa、15kpa、20kpa、25kpa、30kpa、35kpa、40kpa、45kpa、50kpa、55kpa、60kpa、65kpa、70kpa、75kpa或80kpa。在本实用新型提供的回收工艺中,所述气态氯甲烷粗品在浓硫酸干燥塔中进行干燥,得到干燥的气态氯甲烷。其中,所述气态氯甲烷粗品在进入浓硫酸干燥塔之前,优选先进入氯甲烷缓冲罐,所述氯甲烷缓冲罐的压力优选为0~50kpa,具体可为0kpa、5kpa、10kpa、15kpa、20kpa、25kpa、30kpa、35kpa、40kpa、45kpa或50kpa。在本实用新型中,所述浓硫酸干燥塔优选为本实用新型上述技术方案所介绍的回收系统中的浓硫酸干燥塔;所述浓硫酸干燥塔的塔顶温度优选≥10℃;所述浓硫酸干燥塔的压力优选为-20~50kpa,具体可为-20kpa、-15kpa、-10kpa、-5kpa、0kpa、5kpa、10kpa、15kpa、20kpa、25kpa、30kpa、35kpa、40kpa、45kpa或50kpa。在本实用新型提供的一个实施例中,所述气态氯甲烷粗品依次在一级至四级浓硫酸干燥塔中进行干燥,多级浓硫酸干燥塔的塔压逐步降低。在本实用新型提供的一个实施例中,一级浓硫酸干燥塔的压力优选为15~20kpa;二级浓硫酸干燥塔的压力优选为10~15kpa;三级浓硫酸干燥塔的压力优选为5~10kpa;四级浓硫酸干燥塔的压力优选为0~5kpa,更优选为1~2kpa。在本实用新型提供的回收工艺中,所述干燥的气态氯甲烷在冷凝装置中进行冷凝,得到液态氯甲烷。其中,所述冷凝装置优选为本实用新型上述技术方案所介绍的回收系统中的冷凝装置。在本实用新型中,所述干燥的气态氯甲烷在进入冷凝装置之前,优选先在氯甲烷压缩机中进行压缩;所述氯甲烷压缩机的压力优选控制在0.1~1mpa,具体可为0.1mpa、0.2mpa、0.3mpa、0.4mpa、0.5mpa、0.6mpa、0.7mpa、0.8mpa、0.9mpa或1mpa。本实用新型提供的回收系统和回收工艺通过对草甘膦生产尾气进行中和、汽提和多效精馏,提高了回收得到的氯甲烷粗品的品质和回收率,具有良好的经济和环保效益。具体来说,本实用新型提供的回收系统和回收工艺至少具有如下优点:1)提高了氯甲烷的回收率;2)大幅降低了回收得到的氯甲烷粗品中的水分、甲醇和甲缩醛含量,精馏后的氯甲烷气体粗品中除了氯甲烷、二甲醚、空气之外基本上不含有其它组分,提高了氯甲烷粗品的品质,可避免由于甲醇、甲缩醛等低沸物混入氯甲烷气体中所造成的氯甲烷粗品后续进行硫酸干燥时硫酸消耗较高的问题,可使下游硫酸干燥工艺的硫酸使用量和废硫酸的处理量降低55%以上;3)回收得到的氯甲烷粗品在后续处理时不再需要水洗、碱洗工序,可减少废水量,以及减少相应工序的设备、电仪投入,降低投资成本。为更清楚起见,下面通过以下实施例进行详细说明。实施例在图2~3所示的回收系统中进行草甘膦生产尾气中氯甲烷的清洁回收,该回收系统所包括的装置设备,以及各装置设备的连接关系和工作过程在上文中已经介绍,在此不再赘述。具体回收过程包括:来水解工序的尾气进入中和塔,中和塔内通入碱液,通过循环液与水解尾气进行气液中和反应去除氯化氢,塔釜液循环流量为30m3/h,反应温度为80℃,塔内压力为3kpa;中和塔排出的塔釜液与草甘膦酸化合成液水解冷凝液进行混合,得到的混合液(ph=6~14)通过管道进入汽提塔进行汽提分离,汽提塔釜的温度为103℃,塔顶温度为92℃,塔内压力为-2kpa;汽提塔塔顶蒸出的气体(甲醇和水)与中和塔塔顶的气体通过管道送至分离塔进行精馏分离,分离塔的塔釜温度为76℃,塔顶温度为60℃,塔顶压力为-5kpa,回流比为2.2;分离塔塔顶蒸出的气体(甲醇、甲缩醛、氯甲烷等)进入脱氯甲烷塔中回收氯甲烷,脱氯甲烷塔的塔釜温度为75℃,塔釜压力70kpa,塔顶温度-14℃,塔顶压力55kpa,回流比1.5;脱氯甲烷塔塔顶分离出的气态氯甲烷粗品通过管道输送至氯甲烷缓冲罐,缓冲罐压力控制在15~18kpa,之后缓冲罐中的氯甲烷气体通过管道进入一级至四级浓硫酸干燥塔,塔压逐步下降,一级浓硫酸干燥塔的压力控制在15~20kpa,二级浓硫酸干燥塔的压力控制在10~15kpa,三级浓硫酸干燥塔的压力控制在5~10kpa,四级硫酸干燥塔的压力控制在1~2kpa;四级硫酸干燥塔塔顶排出的氯甲烷气体经浓硫酸干燥塔后除沫器除沫后进入干燥氯甲烷缓冲罐,再用管道输送至氯甲烷压缩机进行压缩,压缩后气体经过一级冷凝器水冷和二级冷凝器盐冷后,冷凝液进入氯甲烷冷凝液罐;不凝性气体经过级冷凝装置深冷后放空至工厂voc管道,冷凝液也回收至氯甲烷成品大槽。该工艺的氯甲烷回收率为>99%,纯度(不计空气)为≈97.5%;甲缩醛的回收率为>99%,纯度为≥85%。以氯甲烷的产量为基准,蒸汽消耗量为2.75t/t产品,硫酸消耗55kg/t产品。对比例水解系统的稀甲醇与40%的液碱在静态混合器中进行中和反应后,用回收甲醇、蒸汽冷凝水预热至至60~80℃后,通过气液两相进入间隔壁塔精馏,甲缩醛侧塔顶温度控制42℃,常压,回流比在5,塔顶采出气相经冷凝后得到甲缩醛产品,不凝性气体(粗氯甲烷)去氯甲烷回收装置;甲醇侧塔顶温度控制64℃,常压,回流比1.5,塔顶采出甲醇产品,塔中下侧采出甲醇和水的混合物至高压甲醇塔;塔釜废水换热后去环保站;高压甲醇塔塔顶温度控制120℃,压力控制0.55mpa,回流比3.5,塔顶气相给间隔壁塔做热源,冷凝液即为甲醇产品,塔釜废水经换热后去环保站。该工艺甲醇回收率为≈98%,纯度>99.5%;以氯甲烷的产量为基准,蒸汽消耗量为4.76t/t产品。对实施例和对比例得到的氯甲烷产品和甲缩醛产品进行成分分析,结果如表1和表2所示:表1氯甲烷产品成分对比表2甲缩醛产品成分对比氯甲烷甲缩醛甲醇水实施例<0.1%85%14.8%0.1%对比例≈3%85%11.9%0.1%以上所述仅是本实用新型的优选实施方式,应当指出,对于本
技术领域:
的普通技术人员来说,在不脱离本实用新型原理的前提下,还可以做出若干改进和润饰,这些改进和润饰也应视为本实用新型的保护范围。当前第1页12