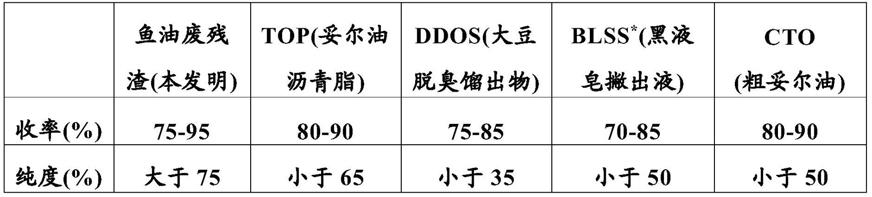
1.本发明涉及由鱼油加工废残渣生产胆固醇含量超过75wt%的组合物的方法。
背景技术:2.us 10,196,583(markovits and“fish oil cholesterol”)公开了一种由鱼油生产医药级胆固醇的方法。所公开方法的缺点在于应用溶剂分离胆固醇与脂肪酸皂。与待提取的物质量相比,溶剂或溶剂混合物的应用比例非常大,并且在有价值产品的提取和预浓缩过程中,需要额外的过程来脱除和/或循环溶剂。另外,如果应用溶剂混合物,回收和循环的成本会急剧增加。上述原因使得溶剂基方法及其最终产品都很昂贵。另外,由鱼油回收胆固醇的收率一般小于70%。
3.us 6,846,941(resitec industria quimica ltda.“process for separating non
‑
saponifiable valuable products from raw materials”)公开了一种方法,其中有价值的非皂化物质与大量动物或植物源的原料以及动物或植物产品加工(如食品加工、纤维素加工等)的副产品、残渣和废产品分离。当鱼油为原料时,有价值的非皂化物质为胆固醇。该方法包括用氢氧化钠或氢氧化钾使原料皂化,将钠或钾皂转化为金属皂如镁或锌皂,蒸馏金属皂混合物,和当起始材料为鱼油时,馏出物包含胆固醇和残渣包含金属皂。
4.发明人认为,将碱性皂转化为金属皂的原因在于碱性皂化混合物的蒸馏过程存在问题和困难。
5.us 6,846,941的方法具有若干缺点,特别是当初始原料为鱼油时,其中:胆固醇分离使得有价值的鱼油转化为金属皂;胆固醇馏出物包含鱼油中大部分有毒和/或有害的人为污染物(pop);要获得65%或更高纯度的胆固醇,需要进一步结晶胆固醇馏出物。
6.wo 2016096989公开了一种由鱼油废残渣提取胆固醇的方法,所述方法在naoh/koh的存在下皂化,随后用至少一种水不可混溶溶剂如脂族或芳族烃在温度高于30℃下提取。所述方法包括重复的溶剂提取、结晶和反洗以提取胆固醇。在wo 2016096989中描述的方法是需要大量溶剂的多步骤繁琐的溶剂提取方法。
7.wo 2019/053744 a1也公开了一种由鱼油废残渣提取胆固醇的方法,所述方法在催化剂4
‑
二甲基氨基吡啶(dmap)的存在下用naoh皂化,随后用酸的水溶液中和以获得无酯的胆固醇,加热在2
‑
丁酮(甲基乙基酮)中用溴化钙皂化的物质,以获得胆固醇加合物,用甲苯分离加合物中的胆固醇,蒸发甲苯,将胆固醇溶解在甲醇中,然后使溶液结晶以获得胆固醇。所公开方法的一个缺点是使用不同的溶剂分离胆固醇,例如甲醇、2
‑
丁酮、甲苯。溶剂以大比例使用,和在有价值产品的提取和预浓缩过程中,需要额外的过程来脱除和/或循环溶剂。另外,回收和循环的成本也急剧增加。另一个缺点是使用了4
‑
二甲基氨基吡啶(dmap)。dmap具有相对高的毒性,并且由于其能够通过皮肤吸收而特别危险。最后,该方法产生大量的废残渣。
技术实现要素:8.本发明的实施方案提供由鱼油加工废残渣生产胆固醇含量超过75wt%的组合物的方法。
9.通过所公开的方法获得的组合物,适合作为水产养殖中虾和对虾饲料的添加剂,以及用于生产维生素d2、d3、激素和作为化妆品和药物制剂中w/o乳液的乳化剂。
10.正如这里所应用,术语“鱼油加工废残渣”包括用于降低鱼油中环境污染物含量的鱼油馏出物或减压气提馏分,例如在us 8,258,330和us 7,718,698中所公开,和这种气提馏分还包含胆固醇,或如us 7,678,930中公开的用于降低鱼油中胆固醇含量的鱼油减压气提馏分,和这种气提馏分除鱼油的环境污染物外,通常包含5
‑
15%的胆固醇。显然,这些馏分的主要部分构成气提过程应用的流体,最通常为一种或多种脂肪酸的乙酯。如果需要,可用漂白粘土、活性炭或其它漂白剂将这种气提馏分漂白。由此开始,这种残渣被称为“轻废残渣”。
11.鱼油加工废残渣还包含最终残渣或来自用于用乙醇酯交换鱼油而生产ω
‑
3浓缩物的两步或更多步短程/分子蒸馏过程最后一步的残渣。鱼油酯交换的收率通常小于95%,这使得在多步短程蒸馏过程的最终残渣中存在部分甘油酯。最后的残渣是鱼油废残渣,通常含5
‑
25%的胆固醇(游离胆固醇或酯化胆固醇)和其它酯交换鱼油的高沸点馏分,其中包括c
18
‑
c
22
ω
‑
3脂肪酸如epa、dha和dpa(22:5n3)的单甘油酯和双甘油酯以及少量c
18
碳原子以上的多不饱和脂肪酸的部分甘油酯。us 10,050,704描述了由用乙醇酯交换的鱼油生产ω
‑
3浓缩物的典型的两步短程/分子蒸馏方法获得最终残渣的方法。如果需要,可用漂白粘土、活性炭或其它漂白剂将这种最终残渣漂白。由此开始,这种残渣被称为“重废残渣”。
12.因此,正如这里所应用,术语“鱼油加工废残渣”包括“轻废残渣”或“重废残渣”或两种废残渣的任意混合物。
13.在一个方面,所公开的实施方案涉及由鱼油加工废残渣生产含胆固醇的组合物的方法,所述方法包括如下步骤:(a)使鱼油加工废残渣与碱接触,以获得皂化混合物,(b)使皂化混合物经历蒸馏步骤,以获得第一馏出物和第一残渣,(c)使第一残渣经历真空蒸馏步骤,以获得第二馏出物和第二残渣,和(d)使第二残渣经历真空蒸馏步骤,以获得第三馏出物和第三残渣,其中第三馏出物为包含至少75wt%胆固醇的组合物。
14.在一个实施方案中,在步骤(a)中碱为naoh或koh,优选为naoh和最优选为naoh的水溶液。在另一个实施方案中,在步骤(a)中,鱼油加工废残渣与碱如naoh或koh在包含水和极性溶剂(如甲醇或乙醇或所述溶剂的混合物)的溶液中接触。在另一个实施方案中,在步骤(a)中碱在压力搅拌反应器中与鱼油加工废残渣接触。在另一个实施方案中,在步骤(a)中碱与鱼油加工废残渣接触1
‑
120分钟的时间间隔。在另一个实施方案中,在步骤(a)中碱在50
‑
200℃的温度区间与鱼油加工废残渣接触。在另一个实施方案中,在步骤(a)中碱在1
‑
20bar的压力区间与鱼油加工废残渣接触。在一个优选的实施方案中,在步骤(a)中碱在压力搅拌反应器中在50
‑
200℃的温度区间和1
‑
20bar的压力区间与鱼油加工废残渣接触1
‑
120分钟的时间间隔。
15.在另一个实施方案中,步骤(b)在短程蒸馏塔或分子蒸馏塔或薄膜蒸馏塔中实施。在另一个实施方案中,步骤(b)中皂化混合物的进料流量为10
‑
350kg/h/m2。在另一个实施方案中,步骤(b)中的温度区间为150
‑
400℃。在另一个实施方案中,步骤(b)中的压力小于
2bar。在一个优选的实施方案中,步骤(b)在短程蒸馏塔中实施,皂化混合物的进料流量为10
‑
350kg/h/m2,温度区间为150
‑
400℃和压力小于2bar。
16.在另一个实施方案中,步骤(c)在短程蒸馏塔或分子蒸馏塔中实施。在另一个实施方案中,步骤(c)中第一残渣的进料流量为10
‑
350kg/h/m2。在另一个实施方案中,步骤(c)中的温度区间为200
‑
400℃。在另一个实施方案中,步骤(c)中的压力小于500mbar。在一个优选的实施方案中,步骤(c)在短程蒸馏塔中实施,第一残渣的进料流量为10
‑
350kg/h/m2,温度区间为200
‑
400℃,和压力小于500mbar。
17.在另一个实施方案中,步骤(d)在短程蒸馏塔或分子蒸馏塔中实施。在另一个实施方案中,步骤(d)中第二残渣的进料流量为10
‑
350kg/h/m2。在另一个实施方案中,步骤(d)中的温度区间为200
‑
400℃。在另一个实施方案中,步骤(d)中的压力小于10mbar。在本发明最优选的实施方案中,步骤(d)在短程蒸馏塔中实施,第二残渣的进料流量为10
‑
350kg/h/m2,操作温度的区间为200
‑
400℃和压力小于10mbar。
18.在另一个方面,所公开的实施方案涉及由鱼油加工废残渣生产含胆固醇的组合物的方法,所述方法包括如下步骤:(i)真空蒸馏鱼油加工废残渣,以获得第一馏出物和第一残渣,(ii)使第一残渣与碱接触,以获得皂化混合物,(iii)使皂化混合物经历蒸馏步骤,以获得第二馏出物和第二残渣,(iv)使第二残渣经历真空蒸馏步骤,以获得第三馏出物和第三残渣,和(v)使第三残渣经历真空蒸馏步骤,以获得第四馏出物和第四残渣,和第四馏出物为包含至少75wt%胆固醇的组合物。
19.在一个实施方案中,在步骤(ii)中碱为naoh或koh,优选为naoh和最优选为naoh的水溶液。在另一个实施方案中,在步骤(ii)中,第一残渣与碱如naoh或koh在包含水和极性溶剂(如甲醇或乙醇或所述溶剂的混合物)的溶液中接触。在另一个实施方案中,在步骤(ii)中碱在压力搅拌反应器中与第一残渣接触。在另一个实施方案中,在步骤(ii)中碱与第一残渣接触1
‑
120分钟的时间间隔。在另一个实施方案中,在步骤(ii)中碱在温度区间50
‑
200℃下与第一残渣接触。在另一个实施方案中,在步骤(ii)中碱在压力区间1
‑
20bar下与第一残渣接触。在一个优选的实施方案中,在步骤(ii)中碱在压力搅拌反应器中在温度区间50
‑
200℃和压力区间1
‑
20bar下与第一残渣接触1
‑
120分钟的时间间隔。
20.在另一个实施方案中,步骤(iii)在短程蒸馏塔或分子蒸馏塔或薄膜蒸馏塔中实施。在另一个实施方案中,步骤(iii)中皂化混合物的进料流量为10
‑
350kg/h/m2。在另一个实施方案中,步骤(iii)的温度为150
‑
400℃。在另一个实施方案中,步骤(iii)中的压力小于2bar。在一个优选的实施方案中,步骤(iii)在短程蒸馏塔中实施,皂化混合物的进料流量为10
‑
350kg/h/m2,温度区间为150
‑
400℃和压力小于2bar。
21.在另一个实施方案中,步骤(iv)在短程蒸馏塔或分子蒸馏塔中实施。在另一个实施方案中,步骤(c)中第二残渣的进料流量为10
‑
350kg/h/m2。在另一个实施方案中,步骤(c)中的温度区间为200
‑
400℃。在另一个实施方案中,步骤(iv)中的压力小于500mbar。在一个优选的实施方案中,步骤(iv)在短程蒸馏塔中实施,第二残渣的进料流量为10
‑
350kg/h/m2,温度区间为200
‑
400℃,和压力小于500mbar。
22.在另一个实施方案中,步骤(v)在短程蒸馏塔或分子蒸馏塔中实施。在另一个实施方案中,步骤(v)中第三残渣的进料流量为10
‑
350kg/h/m2。在另一个实施方案中,步骤(d)中的温度区间为200
‑
400℃。在另一个实施方案中,步骤(v)中的压力小于10mbar。在本发明
最优选的实施方案中,步骤(v)在短程蒸馏塔中实施,第三残渣的进料流量为10
‑
350kg/h/m2,操作温度的区间为200
‑
400℃和压力小于10mbar。
23.在另一个实施方案中,步骤(i)在短程蒸馏塔或分子蒸馏塔中实施。在另一个实施方案中,步骤(i)中鱼油加工废残渣的进料流量为10
‑
350kg/h/m2。在另一个实施方案中,步骤(a)的操作温度为100
‑
250℃。在另一个实施方案中,步骤(i)中的压力小于0.5mbar。在一个优选的实施方案中,步骤(i)在短程蒸馏塔中实施,鱼油加工废残渣的进料流量为10
‑
350kg/h/m2,温度区间为100
‑
250℃和压力小于0.5mbar。在最优选的实施方案中,步骤(a)在双馏出液短程蒸发器中实施,其中在内部冷凝器底部收集的下部馏出物馏分与步骤(i)中进料至该塔的鱼油加工废残渣接触。
24.短程蒸馏塔也称为短程蒸发器,通常包括一个立式的圆柱体或塔,带有加热套、转子和内部靠近加热表面的冷凝器。在转子的支撑结构上安装有可移动的精密刮板,用于推送并搅拌进料物质至加热壁上。蒸发发生在加热的刮拭膜上。当原料进入圆柱体时,它遇到旋转的刮板或辊,在受热面上产生薄膜。设备中间的冷凝器用冷却液冷却,并使馏出物冷凝。接收容器在底部收集馏出物和高温残渣。一些短程蒸馏塔还包括与冷凝器同心的、位于冷凝器一定高度处的馏出物收集盘。这种设计允许将馏出物分为两个馏分:一个馏分在收集盘上方冷凝,包含经受蒸馏的混合物的较高蒸汽压组分,该点以上称为“上部凝液”,另一个馏分在收集盘下方冷凝,包含经受蒸馏的混合物的较低蒸汽压组分,该点以下称为“下部凝液”。从塔中分别抽出这两种馏分。这种塔也称为双馏出液短程蒸发器(dd
‑
spe)。
25.蒸馏操作条件包括塔温、塔压和进料流量,指的是加热表面的温度、塔压和进入塔顶的进料流量(质量/时间/加热表面积)。
26.当在操作条件下蒸馏塔的受热表面与内部冷凝器表面之间的距离与馏出物分子的平均自由路径相当时,短程蒸馏塔也称为分子蒸馏塔,因此,在一些实施方案中,短程蒸馏和分子蒸馏意味着实施蒸馏的蒸馏塔中受热表面附近有内部冷凝器。薄膜蒸馏塔是带有外部冷凝器的蒸馏塔。蒸馏塔也称为蒸发器。
具体实施方式
27.本发明实施方案共同的令人惊奇和意外的特征是:通过本发明方法仅通过蒸馏步骤而不需要任何进一步的纯化步骤(例如从溶剂中结晶的步骤)即可获得高纯度胆固醇。下表a给出了没有us 6,846,941的结晶步骤时本发明方法的胆固醇收率和纯度。
28.表a没有结晶步骤时胆固醇的收率和纯度
29.*kraft硫酸纸制浆方法的脱脂皂渣。
30.对本发明的实施方案来说,共同的有利特征还有:除了高纯度胆固醇外,还获得以ω
‑
3脂肪酸形式存在的有价值副产品。
31.在一些实施方案中,本发明提供由鱼油加工废残渣生产含胆固醇的组合物的方法,所述方法包括如下步骤:
32.(a)使鱼油加工废残渣与碱接触,以获得皂化混合物,
33.(b)使皂化混合物经历蒸馏步骤,以获得第一馏出物和第一残渣,
34.(c)使第一残渣经历真空蒸馏步骤,以获得第二馏出物和第二残渣,和
35.(d)使第二残渣经历真空蒸馏步骤,以获得第三馏出物和第三残渣,和第三馏出物为包含大于75wt%胆固醇的组合物。
36.在一些实施方案中,本发明提供由鱼油加工废残渣生产含胆固醇的组合物的方法。所述方法包括如下步骤:
37.(i)真空蒸馏鱼油加工废残渣,以获得第一馏出物和第一残渣,
38.(ii)使第一残渣与碱接触,以获得皂化混合物,
39.(iii)使皂化混合物经历蒸馏步骤,以获得第二馏出物和第二残渣,
40.(iv)使第二残渣经历真空蒸馏步骤,以获得第三馏出物和第三残渣,和
41.(v)使第三残渣经历真空蒸馏步骤,以获得第四馏出物和第四残渣,和第四馏出物为包含大于75wt%胆固醇的组合物。
42.步骤(a)
43.在一些实施方案中,在步骤(a)中,鱼油加工废残渣与包括naoh或koh水溶液的碱接触,以形成皂化混合物。鱼油加工废残渣与碱水溶液的重量比为1:0.01
‑
1:1,优选为1:0.1
‑
1:0.3。替代地,鱼油加工废残渣与碱如naoh或koh在包含水和极性溶剂(如甲醇或乙醇或所述溶剂的任意混合物)的溶液中接触,以形成皂化混合物。在一些实施方案中,鱼油加工废残渣与所述溶液的重量比为1:0.01
‑
1:1,优选为1:0.1
‑
1:0.5。
44.在一些实施方案中,水或溶液中的碱量等于鱼油加工废残渣的皂化值,优选为第一馏出物的皂化值的0.9
‑
1.2倍,最优选为鱼油加工废残渣的皂化值的0.97
‑
1.05倍。
45.在一些实施方案中,形成皂化混合物的皂化反应在封闭搅拌容器或连续反应器中在温度为50
‑
200℃、优选为100
‑
180℃和压力为1
‑
20bar、优选为2
‑
10bar的条件下通过使鱼油加工废残渣与碱接触1
‑
120分钟、优选2
‑
30分钟而实施。
46.步骤(b)
47.在一些实施方案中,在步骤(a)之后,在步骤(b)中蒸馏所述皂化混合物。在一个实施方案中,步骤(b)在短程蒸馏塔或分子蒸馏塔或薄膜蒸馏塔中实施。在另一个实施方案中,皂化混合物的进料流量为10
‑
350kg/h/m2,优选为75
‑
220kg/h/m2。在另一个实施方案中,步骤(b)的温度为150
‑
400℃,优选为200
‑
300℃。在另一个实施方案中,步骤(b)中的压力小于2bar,优选为0.5
‑
1.5bar。在一个优选的实施方案中,步骤(b)在短程蒸馏塔中实施和皂化混合物的进料流量为10
‑
350kg/h/m2,温度区间为150
‑
400℃和压力小于2bar。在另一个优选的实施方案中,步骤(b)在短程蒸馏塔中实施,皂化混合物的进料流量为75
‑
220kg/h/m2,温度区间为200
‑
300℃和压力区间为0.5
‑
1.5bar。
48.在一些实施方案中,步骤(b)的蒸馏过程使得第一馏出物与第一残渣分离,它们各自单独离开蒸馏塔。
49.步骤(c)
50.在一些实施方案中,在步骤(b)之后,在步骤(c)中蒸馏第一残渣。在一个实施方案
中,步骤(c)在短程蒸馏塔或分子蒸馏塔中实施。在另一个实施方案中,步骤(c)中第一残渣的进料流量为10
‑
350kg/h/m2,优选为75
‑
220kg/h/m2。在另一个实施方案中,步骤(c)中的温度区间为200
‑
400℃,优选为250
‑
350℃。在另一个实施方案中,步骤(c)中的压力小于500mbar,优选为1
‑
100mbar。在一个优选的实施方案中,步骤(c)在短程蒸馏塔中实施,和第一残渣的进料流量为10
‑
350kg/h/m2,温度区间为200
‑
400℃,和压力小于500mbar。在另一个优选的实施方案中,步骤(c)在短程蒸馏塔中实施,第一残渣的进料流量为75
‑
200kg/h/m2,温度区间为250
‑
350℃,和压力区间为1
‑
100mbar。替代地,在另一个实施方案中,步骤(c)可以在闪蒸罐中在压力低于500mbar下实施。
51.在一些实施方案中,步骤(c)的蒸馏过程使得第二馏出物与第二残渣分离,它们各自单独离开蒸馏塔。
52.步骤(d)
53.在一些实施方案中,在步骤(c)之后,在步骤(d)中蒸馏第二残渣,以获得第三馏出物和第三残渣。在一些实施方案中,第三馏出物包含大于75wt%的胆固醇。在一个实施方案中,步骤(d)在短程蒸馏塔或分子蒸馏塔中实施。在另一个实施方案中,第二残渣的进料流量为10
‑
350kg/h/m2,优选为75
‑
220kg/h/m2。在另一个实施方案中,步骤(d)的操作温度区间为200
‑
400℃,优选为280
‑
380℃。在另一个实施方案中,步骤(d)中的压力小于10mbar,优选为0.001
‑
1mbar。在一个优选的实施方案中,步骤(d)在短程蒸馏塔中实施,第二残渣的进料流量为10
‑
350kg/h/m2,温度区间为200
‑
400℃和压力小于10mbar。在另一个优选的实施方案中,步骤(d)在短程蒸馏塔中实施,第二残渣的进料流量为75
‑
220kg/h/m2,温度区间为280
‑
380℃和压力区间为0.001
‑
1mbar。
54.在一些实施方案中,步骤(d)的蒸馏过程使得第三馏出物与第三残渣分离,它们各自单独离开蒸馏塔。
55.在一些实施方案中,使来自步骤(d)的第三馏出物经历造粒(也称为喷雾絮凝、喷雾激冷或熔融雾化),以获得胆固醇颗粒或小球。
56.在至少一个特定的实施方案中,通过在合适溶剂或溶剂混合物如己烷、甲醇、乙醇、丙酮、水或它们的混合物中使第三馏出物结晶可以获得含大于96%胆固醇的组合物。在另一个特别的实施方案中,通过在填料塔蒸馏单元中使来自步骤(d)的第三馏出物高真空蒸馏可以获得含超过96%胆固醇的组合物。在另一个特别的实施方案中,通过在高压液相色谱下蒸馏步骤(d)获得的第三馏出物组合物可以获得含超过99%胆固醇的组合物。
57.在一些实施方案中,用无机酸酸化步骤(d)的第三残渣,以形成含10
‑
70wt%ω
–
3脂肪酸的组合物,所述组合物含二十碳五烯酸(epa)、二十二碳六烯酸(dha)和二十二碳五烯酸(dpa)。在一些实施方案中,使所述组合物经历一个或多个分子蒸馏步骤,以获得适合于动物和人类消费的含40
‑
90%的ω
‑
3脂肪酸的浓缩物。
58.在一些实施方案中,用乙醇酯化由步骤(d)的第三残渣酸化获得的ω
‑
3脂肪酸的组合物,以获得含ω
‑
3脂肪酸乙酯的组合物。在一些实施方案中,使所述组合物经历一个或多个分子蒸馏步骤,以获得适合于动物和人类消费的含40
‑
90%的ω
‑
3脂肪酸乙酯的浓缩物。
59.步骤(i)
60.在本发明的一个实施方案中,在短程蒸馏塔或分子蒸馏塔中蒸馏所述鱼油加工废
残渣。在另一个实施方案中,鱼油加工废残渣的进料流量为10
‑
350kg/h/m2,优选为75
‑
220kg/h/m2。在另一个实施方案中,步骤(i)的温度为100
‑
250℃,优选为120
‑
220℃。在另一个实施方案中,步骤(i)中的压力小于0.5mbar,优选为0.001
‑
0.1mbar。在另一个实施方案中,步骤(i)在短程蒸馏塔中实施,鱼油加工废残渣的进料流量为10
‑
350kg/h/m2,温度区间为100
‑
250℃和压力小于0.5bar。在另一个实施方案中,步骤(i)在短程蒸馏塔中实施,鱼油加工废残渣的进料流量为75
‑
220kg/h/m2,温度区间为120
‑
220℃和压力区间为0.001
‑
0.1mbar。在一个优选的实施方案中,步骤(i)在双馏出液短程蒸发器中实施,其中在内部冷凝器底部收集的下部馏出物馏分与步骤(i)中进料至该塔的鱼油加工废残渣接触。
61.在一些实施方案中,步骤(i)的蒸馏过程使得第一馏出物与第一残渣分离,它们各自单独离开蒸馏塔。
62.如果需要,可用漂白粘土、活性炭或其它漂白剂将第一残渣漂白。
63.步骤(ii)
64.在一些实施方案中,在步骤(b)中步骤(i)的第一残渣与包括naoh或koh水溶液的碱接触,以形成皂化混合物。第一残渣与碱水溶液的重量比为1:0.01
‑
1:1,优选为1:0.05
‑
1:0.3。替代地,第一馏出物与碱如naoh或koh在包含水和极性溶剂(如甲醇或乙醇或所述溶剂的任意混合物)的溶液中接触,以形成皂化混合物。在一些实施方案中,第一馏出物与所述溶液的重量比为1:0.01
‑
1:1,优选为1:0.05
‑
1:0.5。
65.在一些实施方案中,水或溶液中的碱量等于第一残渣的皂化值,优选为第一残渣皂化值的0.9
‑
1.2倍,最优选为第一残渣皂化值的0.97
‑
1.05倍。
66.在一些实施方案中,形成皂化混合物的皂化反应通过在封闭搅拌容器或连续反应器中在温度为50
‑
200℃、优选为100
‑
180℃和压力为1
‑
20bar、优选为2
‑
10bar下使第一残渣与碱接触1
‑
120分钟、优选2
‑
30分钟而实施。
67.步骤(iii)
68.在一些实施方案中,在步骤(ii)之后,在步骤(iii)中蒸馏皂化混合物。在一个实施方案中,步骤(iii)在短程蒸馏塔或分子蒸馏塔或薄膜蒸馏塔中实施。在另一个实施方案中,皂化混合物的进料流量为10
‑
350kg/h/m2,优选为75
‑
220kg/h/m2。在另一个实施方案中,步骤(iii)中的温度为150
‑
400℃,优选为200
‑
300℃。在另一个实施方案中,步骤(iii)中的压力小于2bar,优选为0.5
‑
1.5bar。在一个优选的实施方案中,步骤(iii)在短程蒸馏塔中实施和皂化混合物的进料流量为10
‑
350kg/h/m2,温度区间为150
‑
400℃和压力小于2bar。在另一个优选的实施方案中,步骤(b)在短程蒸馏塔中实施,皂化混合物的进料流量为75
‑
220kg/h/m2,温度区间为200
‑
300℃和压力区间为0.5
‑
1.5bar。
69.在一些实施方案中,步骤(iii)的蒸馏过程使得第二馏出物与第二残渣分离,它们各自单独离开蒸馏塔。
70.步骤(iv)
71.在一些实施方案中,在步骤(iii)之后,在步骤(iv)中蒸馏第二残渣。在一个实施方案中,步骤(iv)在短程蒸馏塔或分子蒸馏塔中实施。在另一个实施方案中,步骤(iv)中第二残渣的进料流量为10
‑
350kg/h/m2,优选为75
‑
220kg/h/m2。在另一个实施方案中,步骤(iv)的温度为200
‑
400℃,优选为250
‑
350℃。在另一个实施方案中,步骤(iv)中的压力小于500mbar,优选为100
‑
1mbar。在一个优选的实施方案中,步骤(iv)在短程蒸馏塔中实施和第
二残渣的进料流量为10
‑
350kg/h/m2,温度区间为200
‑
400℃,和压力小于500mbar。在另一个优选的实施方案中,步骤(iv)在短程蒸馏塔中实施,第二残渣的进料流量为75
‑
200kg/h/m2,温度区间为250
‑
350℃和压力区间为1
‑
100mbar。替代地,在另一个实施方案中,步骤(iv)可以在闪蒸罐中在压力小于500mbar下实施。
72.在一些实施方案中,步骤(iv)的蒸馏过程使得第三馏出物与第三残渣分离,它们各自单独离开蒸馏塔。
73.步骤(v)
74.在一些实施方案中,在步骤(iv)之后,在步骤(v)中蒸馏第三残渣,以获得第四馏出物和第四残渣。在一些实施方案中,第四馏出物包含超过75wt%的胆固醇。在一个实施方案中,步骤(v)在短程蒸馏塔或分子蒸馏塔中实施。在另一个实施方案中,第三残渣的进料流量为10
‑
350kg/h/m2,优选为75
‑
220kg/h/m2。在另一个实施方案中,步骤(v)的操作温度为200
‑
400℃,优选为280
‑
380℃。在另一个实施方案中,步骤(v)中的压力小于10mbar,优选为0.001
‑
1mbar。在一个优选的实施方案中,步骤(v)在短程蒸馏塔中实施,第三残渣的进料流量为10
‑
350kg/h/m2,温度区间为200
‑
400℃和压力小于10mbar。在另一个优选的实施方案中,步骤(v)在短程蒸馏塔中实施,第三残渣的进料流量为75
‑
220kg/h/m2,温度区间为280
‑
380℃和压力为0.001
‑
1mbar。
75.在一些实施方案中,步骤(v)的蒸馏过程使得第四馏出物与第四残渣分离,它们各自单独离开蒸馏塔。
76.在一些实施方案中,使来自步骤(v)的第四馏出物经历造粒(也称为喷雾絮凝、喷雾激冷或熔融雾化),以获得胆固醇颗粒或小球。
77.在至少一个特定的实施方案中,通过在合适溶剂或溶剂混合物如己烷、甲醇、乙醇、丙酮、水或它们的混合物中使第四馏出物结晶可以获得含大于96%胆固醇的组合物。在另一个特别的实施方案中,通过在填料塔蒸馏单元中使来自步骤(d)的第三馏出物高真空蒸馏可以获得含超过96%胆固醇的组合物。在另一个特别的实施方案中,通过在高压液相色谱下蒸馏步骤(v)获得的第四馏出物组合物可以获得含超过99%胆固醇的组合物。
78.在一些实施方案中,用无机酸酸化步骤(v)的第四残渣,以形成含10
‑
70wt%ω
–
3脂肪酸的组合物,所述组合物含二十碳五烯酸(epa)、二十二碳六烯酸(dha)和二十二碳五烯酸(dpa)。在一些实施方案中,使所述组合物经历一个或多个分子蒸馏步骤,以获得适合于动物和人类消费的含40
‑
90%的ω
‑
3脂肪酸的浓缩物。
79.在一些实施方案中,用乙醇酯化由步骤(v)的第四残渣酸化获得的ω
‑
3脂肪酸的组合物,以获得含ω
‑
3脂肪酸乙酯的组合物。在一些实施方案中,使所述组合物经历一个或多个分子蒸馏步骤,以获得适合于动物和人类消费的含40
‑
90%的ω
‑
3脂肪酸乙酯的浓缩物。
80.图1为由鱼油加工废残渣生产含胆固醇的组合物的连续方法的实施方案,其中步骤(i)在双馏出液短程蒸发器中实施。
81.参考图1,其中表示了步骤(i)的双馏出液短程蒸发器。经管线2收集的来自双馏出液短程蒸发器(i)的“下部凝液”与管线1中进入的“鱼油加工废残渣”接触,形成混合物,该混合物进料至蒸发器(i)。弃掉经管线3离开蒸发器(i)的“上部凝液”。步骤(i)的残渣,即上述方法的实施方案的第一残渣,经管线4离开塔。
82.经管线4向反应器(ii)进料残渣,同时经管线5向反应器(ii)进料氢氧化钠水溶液,从而形成经管线6离开反应器的皂化混合物。
83.经管线6向短程蒸馏塔(iii)进料皂化混合物,以生产经管线7离开蒸馏塔的馏出物和经管线8离开塔的残渣。
84.经管线8向短程蒸馏塔(iv)进料残渣,以产生经管线9离开塔的馏出物和经管线10离开塔的残渣。
85.经管线10向短程蒸馏塔(v)连续进料残渣,以产生经管线12离开塔的包含脂肪酸皂的残渣和经管线11离开蒸馏塔的包含胆固醇的馏出物。
86.实施例
87.在实施例中公开的分析数据基于欧洲药典9.0和9.2(european pharmacopeia 9.0and 9.2)中描述的分析方法,所述欧洲药典在此作为参考全文引入。
88.实施例1由“轻废残渣”生产胆固醇的方法
89.实施例1中应用的“轻废残渣”的胆固醇和环境污染物含量如下表1所示:
90.表1实施例1中应用的“轻废残渣”的组成
[0091][0092]
将1000kg“轻废残渣”以100kg/h的流量进料至蒸发表面为1m2的uic短程蒸馏塔,并在152℃和0.04mbar下蒸馏,得到660kg第一馏出物和340kg第一残渣。第一残渣含有24.5wt%的胆固醇。
[0093]
使150kg第一残渣与27kg naoh水溶液(50%)在145℃下在压力搅拌反应器中混合15分钟,以获得皂化混合物。
[0094]
然后将皂化混合物进料至由3个串联的在表2所示条件下操作的蒸馏塔或蒸发器组成的vta模块式真空蒸馏中试装置。
[0095]
表2:用于实施例1的皂化混合物蒸馏的vta模块式真空蒸馏中试装置的蒸发面积和操作参数
[0096][0097]
以10kg/h的流量向蒸馏塔i进料皂化混合物,得到1.3kg/h第二馏出物和进料至蒸馏塔ii的第二残渣,得到130g/h第三馏出物和进料至蒸馏塔iii的第三残渣,得到2.6kg/h第四馏出物和5.9kg/h包含脂肪酸皂的第四残渣。下表3给出了第四馏出物的组成。
[0098]
表3:实施例1的第四馏出物的组成
[0099][0100]
实施例1的胆固醇的胆固醇回收率为88.0%。
[0101]
实施例2:由“轻废残渣”生产胆固醇的方法
[0102]
在压力搅拌反应器中在145℃下使120kg实施例1的第一残渣与21.6kg naoh水溶液(50%)混合15分钟,以获得皂化混合物。
[0103]
然后将皂化混合物进料至由3个串联的在表4所示条件下操作的蒸馏塔或蒸发器组成的vta模块式真空蒸馏中试装置。
[0104]
表4:用于实施例2的皂化混合物蒸馏的vta模块式真空蒸馏中试装置的蒸发面积和操作参数
[0105][0106]
以10kg/h的流量向蒸馏塔i进料皂化混合物,得到1.3kg/h第二馏出物和进料至蒸馏塔ii的第二残渣,得到1.0kg/h第三馏出物和进料至蒸馏塔iii的第三残渣,得到1.8kg/h第四馏出物和5.9kg/h包含脂肪酸皂的第四残渣。下表5给出了第四馏出物的组成。
[0107]
表5:实施例2的第四馏出物的组成
[0108][0109][0110]
实施例2的胆固醇的胆固醇回收率为76.9%。
[0111]
实施例3在步骤(i)中用双馏出液短程蒸发器由“轻废残渣”生产胆固醇的方法
[0112]
将表1所示的1000kg“轻废残渣”以90kg/h的质量流量送入uic双馏出液短程蒸发器,所述蒸发器具有1m2的蒸发表面和位于冷凝器中部的收集盘。所述收集盘允许收集冷凝器上半部分的凝液,“上部凝液”与冷凝器下半部分的凝液分开,如图1所示,以60kg/h的流量收集的“下部凝液”再循环并与进入的“轻废残渣”接触,得到至蒸馏塔(i)的150kg/h的总质量流量。连续操作时,上部凝液的流量为60kg/h,和残渣(或第一残渣)的流量为30kg/h,胆固醇的浓度为27.1%。蒸馏在温度168℃和0.04mbar的真空下实施。
[0113]
在压力搅拌反应器中在140℃下使150kg第一残渣与25.9kg naoh水溶液(50%)混合15分钟,以获得皂化混合物。
[0114]
然后将皂化混合物进料至由3个串联的在表6所示条件下操作的蒸馏塔或蒸发器组成的vta模块式真空蒸馏中试装置。
[0115]
表6:用于实施例3的皂化混合物蒸馏的vta模块式真空蒸馏中试装置的蒸发面积和操作参数
[0116][0117]
以10kg/h的流量向蒸馏塔i进料皂化混合物,得到1.3kg/h第二馏出物和进料至蒸馏塔ii的第二残渣,得到1.2kg/h第三馏出物和进料至蒸馏塔iii的第三残渣,得到1.8kg/h第四馏出物和5.7kg/h包含脂肪酸皂的第四残渣。下表7给出了第四馏出物的组成。
[0118]
表7:实施例3的第四馏出物的组成
[0119][0120]
实施例3的胆固醇的胆固醇回收率为75.4%。
[0121]
实施例4:由“轻废残渣”生产胆固醇的方法
[0122]
在压力搅拌反应器中在143℃下使100kg实施例1的第一残渣与17.3kg naoh水溶液(50%)混合15分钟,以获得皂化混合物。
[0123]
然后将皂化混合物进料至由3个串联的在表8所示条件下操作的蒸馏塔或蒸发器组成的vta模块式真空蒸馏中试装置。
[0124]
表8:用于实施例4的皂化混合物蒸馏的vta模块式真空蒸馏中试装置的蒸发面积和操作参数
[0125][0126]
以10kg/h的流量向蒸馏塔i进料皂化混合物,得到1.3kg/h第二馏出物和进料至蒸馏塔ii的第二残渣,得到290g/h第三馏出物和进料至蒸馏塔iii的第三残渣,得到2.7kg/h第四馏出物和5.7kg/h包含脂肪酸皂的第四残渣。下表9给出了第四馏出物的组成。
[0127]
表9:实施例4的第四馏出物的组成
[0128][0129]
实施例4的胆固醇的胆固醇回收率为95.6%。
[0130]
实施例5:由“重废残渣”生产胆固醇的方法
[0131]
在压力搅拌反应器中在140℃下使150kg用于生产ω
‑
3乙酯浓缩物的传统两步短程分子蒸馏过程的包含12.5%胆固醇的“重废残渣”与31.5kg naoh水溶液(50%)混合15分钟,以获得皂化混合物。
[0132]
然后将皂化混合物进料至由3个串联的在表10所示条件下操作的蒸馏塔或蒸发器组成的vta模块式真空蒸馏中试装置。
[0133]
表10:用于实施例5的皂化混合物蒸馏的vta模块式真空蒸馏中试装置的蒸发面积和操作参数
[0134][0135]
以10kg/h的流量向蒸馏塔i进料皂化混合物,得到1.8kg/h第一馏出物和进料至蒸馏塔ii的第一残渣,得到410g/h第二馏出物和进料至蒸馏塔iii的第二残渣,得到1.0kg/h第三馏出物和6.8kg/h包含脂肪酸皂的第三残渣。下表11给出了第三馏出物的组成。
[0136]
表11:实施例5的第三馏出物的组成
[0137][0138][0139]
实施例5的胆固醇的胆固醇回收率为89.0%。
[0140]
在50mbar和101℃下在旋转蒸发器中蒸发来自蒸馏塔i的100g馏出物1。收集29.5g残渣,其甘油含量为99.4%。
[0141]
实施例6:游离脂肪酸浓缩物
[0142]
将10.0kg来自实施例1的脂肪酸皂的残渣溶解在装有30kg热水的搅拌反应器中,并用30kg浓度为10%的硫酸水溶液酸化。产生两相,弃掉下层相。上层相用热水洗涤、在真空下分离和干燥,以得到9.2kg游离脂肪酸的混合物。
[0143]
然后在表12所设条件下操作的vta模块式真空蒸馏中试装置中以5kg/h的进料流量蒸馏所述游离脂肪酸混合物,和以1.9kg/h的流量由蒸馏塔iii的馏出物获得脂肪酸浓缩物。在表13中给出了蒸馏塔iii的馏出物的分析。
[0144]
表12:实施例6中vta模块式真空蒸馏中试装置的蒸发面积和操作参数
[0145][0146]
表13:实施例6的蒸馏塔iii的馏出物的游离脂肪酸组成
[0147][0148]
实施例7:乙酯浓缩物
[0149]
将10.0kg来自实施例5的脂肪酸皂的残渣溶解在装有30kg热水的搅拌反应器中,并用16kg浓度为10%的硫酸水溶液酸化。产生两相,弃掉下层相。上层相用热水洗涤、在真空下分离和干燥,以得到9.2kg游离脂肪酸的混合物。
[0150]
用乙醇酯化干燥的游离脂肪酸,以生成粗乙酯。在一个70升的玻璃反应器中,用40kg乙醇和1kg 10%的硫酸溶液溶解9kg上述游离脂肪酸。混合物在500mbar下温和地蒸发,直到蒸发掉90%的乙醇。然后加入20kg水和100g氢氧化钠。搅拌混合物5min,然后倾析30min。弃掉下层相。加入20kg水,重复该过程。回收到9.7kg包含粗乙酯的油相。
[0151]
然后在表14所设条件下操作的vta模块式真空蒸馏中试装置中以5kg/h的进料流量蒸馏所述粗乙酯,和以1.2kg/h的流量由蒸馏塔iii的馏出物获得乙酯浓缩物。表15中给
出了蒸馏塔iii馏出物的分析。
[0152]
表14:实施例7中vta模块式真空蒸馏中试装置的蒸发面积和操作参数
[0153][0154]
表15:实施例7的乙酯浓缩物的完整表征
[0155]
[0156][0157]
注(a):基于larssen等人的sensory description of marine oils through development of a sensory wheel and vocabulary,food research international,106(2018)45
‑
53.