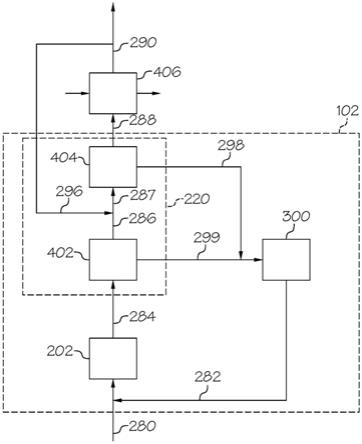
包括使用冷却的产物作为再循环的骤冷流的形成轻质烯烃的方法
1.相关申请的交叉引用
2.本技术要求于2019年6月28日提交的美国临时专利申请序列号62/868,340的优先权,所述专利申请以全文引用的方式并入本文中。
技术领域
3.本公开大体上涉及化学处理系统,并且更具体地说涉及脱氢化学处理系统。
背景技术:4.轻质烯烃可以作为生产许多类型的商品和材料的基础材料。举例来说,乙烯可以用于制造聚乙烯、氯化乙烯或环氧乙烷。这类产物可以用于产物包装、建筑、纺织品等。因此,工业上需要轻质烯烃,如乙烯、丙烯和丁烯。轻质烯烃可以视给定的化学进料流而定通过不同的反应方法产生,所述化学进料流可以是来自原油精炼操作的产物流。许多轻质烯烃可以通过催化方法来生产,如催化脱氢,在所述催化脱氢中使进料流与促进进料流转化成轻质烯烃的流化催化剂接触。在这类系统中,轻质烯烃的反应选择性对于整体工艺效率可能很重要。
技术实现要素:5.持续需要用于生产轻质烯烃的改进系统和方法。已经观察到脱氢产物流的升高的温度可能导致产物流的不希望的热裂化,这可能降低系统对所需轻质烯烃的选择性。举例来说,在产物流被例如热交换器冷却前,产物流中未反应的烷烃和/或所需的产物烯烃可以在催化剂分离部分和反应器系统的其他下游部分中热裂化。为了减轻或完全纠正这种现象,本文所公开的系统在产物流的一部分被例如热交换器冷却后使其再循环。冷却的产物的再循环流(即骤冷流)将高温产物流的温度降低至中温,其具有降低的不希望的热裂化速率。举例来说,在本文公开的一些反应系统中,在产物流离开将大部分固体催化剂与产物流气体分离的初级分离装置之后不久,将冷却的产物流再循环以接触高温产物流。适合用于本文的固体/气体分离装置的实例包括但不限于旋流分离装置(即旋风分离器)、过滤器或适合于从固体中分离气体的任何其他装置。通过这种骤冷流的接触将产物流冷却到与在与骤冷流接触前的产物流相比具有降低的热裂化速率的中温。因此,至少从再循环流(即骤冷流)与高温产物流接触的点到产物流被例如热交换器冷却的点,热裂化减少。
6.根据一个或多个实施例,用于形成轻质烯烃的方法可以包含将烃进料流引入反应器中,使烃进料流与反应器中的脱氢催化剂反应以形成高温脱氢产物,所述脱氢产物包含烃进料流的未催化反应的至少一部分,在初级分离装置中从高温脱氢产物中分离脱氢催化剂的至少一部分,其中初级分离装置中脱氢产物和脱氢催化剂的温度为至少550℃。所述方法可以进一步包含在高温脱氢产物从初级分离装置中离开后,将高温脱氢产物与骤冷流合并以冷却高温脱氢产物并形成中温脱氢产物,其中骤冷流为气流,并且其中中温脱氢产物
的温度比高温脱氢产物的温度低至少10℃。所述方法可以进一步包含冷却中温脱氢产物以形成冷却的脱氢产物,其中冷却的脱氢产物的一部分用作骤冷流的至少一部分。
7.根据一个或多个附加实施例,用于形成轻质烯烃的方法可以包含将烃进料流引入反应器中,使烃进料流与反应器中的脱氢催化剂反应以形成高温脱氢产物,所述脱氢产物包含烃进料流的未催化反应的至少一部分,以及在初级分离装置中从高温脱氢产物中分离脱氢催化剂的至少一部分,其中在初级分离装置中脱氢产物和脱氢催化剂的温度为至少550℃。所述方法可以进一步包含在高温脱氢产物从初级分离装置中离开后,将高温脱氢产物与骤冷流合并以冷却高温脱氢产物并形成中温脱氢产物,其中骤冷流为气流,并且其中中温脱氢产物的温度比高温脱氢产物的温度低至少10℃。所述方法可以进一步包含将中温产物传递到二级分离装置,在所述二级分离装置中从中温产物中去除脱氢催化剂的剩余部分,以及冷却中温脱氢产物以形成冷却的脱氢产物,其中冷却的脱氢产物的一部分用作骤冷流的至少一部分。
8.应理解,前述发明内容和以下具体实施方式两者呈现本技术的实施例,并且旨在提供用于理解如所要求保护的技术的本质和特征的综述或框架。包括附图以提供对技术的另外理解,并且所述附图被并入本说明书中并且构成本说明书的一部分。图式说明各种实施例,并且连同描述一起用以解释技术的原理和操作。另外,图式和描述意味着仅为说明性的,并且并不旨在以任何方式限制权利要求书的范围。
9.本文公开的技术的额外特征和优点将在下文具体实施方式中阐述,并且将部分地由本领域的技术人员从所述描述而容易地显而易见或通过实践如本文所述的技术(包括下文具体实施方式、权利要求书以及附图)而认识到。
附图说明
10.以下对本公开的具体实施例的详细描述在结合以下附图阅读时可以最佳地理解,其中相似的结构用相似的附图标记指示,并且其中:
11.图1描绘了根据本文所述的一个或多个实施例的具有下游冷却和再循环骤冷流的反应器系统的通用流程图;
12.图2示意性地描绘了根据本文所述的一个或多个实施例的反应器系统的一部分;
13.图3示意性地描绘了根据本文所述的一个或多个实施例的反应系统的一部分;
14.图4示意性地描绘了根据本文所述的一个或多个实施例的反应系统的一部分;
15.图5a和5b以图形方式描绘了根据一个或多个实施例的温度骤冷之后的反应速率相对于温度骤冷之前的反应速率的比率(其中后者表示每种反应物在相应目标温度下的速率);
16.图6以图形方式描绘了根据一个或多个实施例的将产物流骤冷不同的量所需的计算出的蒸汽和粗丙烯相对于产物流的百分比(体积/体积);
17.图7以图形方式描绘了根据一个或多个实施例的计算出的累积丙烯选择性(%)作为与骤冷流混合之后的温度下降、骤冷介质(蒸汽或粗丙烯)以及初级分离装置的出口和气体-气体热交换器的入口之间的停留时间的函数;和
18.图8以图形方式描绘了根据一个或多个实施例的计算出的累积丙烷转化率(%)作为与骤冷流混合之后的温度下降、骤冷介质(蒸汽或粗丙烯)以及初级分离装置的出口和气
体-气体热交换器的入口之间的停留时间的函数。
19.应理解,图式在本质上为示意性的,并且不包括本领域中通常采用的反应器系统的一些部件,如但不限于温度变送器、压力变送器、流量计、泵、阀等。已知这些部件在所公开的本发明的实施例的精神和范围内。然而,操作部件(如本公开中所述的部件)可以被添加到本公开中所述的实施例中。
20.现在将更详细地参考各种实施例,其中一些实施例在附图中进行说明。在可能的情况下,整个附图将使用相同的附图标记来指代相同或类似的部件。
具体实施方式
21.目前公开的技术的实施例是关于几个附图进行描述的。图1描绘了表示根据目前公开的一个或多个实施例的反应器系统的实例流程图。应注意,在本文中参考图2-4描述图1的系统的一个或多个实施例的许多过程和设备细节。应了解,考虑到其他附图,图1的一个或多个组件可能是整体或彼此相邻的,并且一些流可能只是描绘材料移动的表示,并且物理管道或其他输送工具可能实体上不存在(例如,流直接从反应器传递到彼此相邻的分离器)。
22.仍然参考图1,反应器系统102可以包括反应器202、分离装置220和催化剂处理部分300。通常,主要反应,如脱氢反应,在反应器202中发生,其中来自所描绘的系统外部的反应物流280(在本文中有时称为烃进料流)与来自催化剂处理部分的流282的再生催化剂合并传递到反应器202中。在反应后,催化剂、未反应的化学品和产物化学品经由流284转移到分离装置220。应当理解,“产物流”可以包括来自反应物流280的反应产物和未反应的组分。反应物流280可以包含丙烷、正丁烷、异丁烷、乙烷或乙苯中的一种或多种。
23.流284在本文中有时被称为高温脱氢产物。通常,流284的温度接近或等于反应器202中的温度。温度可以取决于反应和所用的催化剂体系。在一个或多个实施例中,流284的温度为至少550℃(如至少575℃、至少600℃、至少625℃、至少650℃、至少675℃、至少700℃或甚至至少725℃)。举例来说,当丙烷脱氢时,流284的温度可以为大约620℃(如600℃至640℃)。当乙苯脱氢时,流284的温度可以为大约595℃(如575℃至615℃)。当乙烷脱氢时,流284的温度可以为大约750℃(如730℃至770℃)。当丁烷脱氢时,流284的温度可以为大约600℃(如580℃至620℃)。
24.分离装置220可以包括初级分离装置402和二级分离装置404。然而,应当理解,在一些实施例中不存在二级分离装置404。在附加实施例中,初级分离装置402和/或二级分离装置404可以是但不限于旋风分离器、过滤器或用于从气体中分离固体如催化剂的其他合适的装置。在初级分离装置402中从气相反应物和产物化学品中分离流284的催化剂的至少一部分(通常是大部分)后,催化剂经由流299传递到催化剂处理部分300并且产物和反应物气体(有时仍称为高温脱氢产物)可以经由流286从初级分离装置402中传递出去。流286的温度可以约等于流284的温度。
25.在一个或多个实施例中,在高温脱氢产物经由流286从初级分离装置中离开后,高温脱氢产物可以与骤冷流296合并以冷却高温脱氢产物并形成流287(有时称为中温脱氢产物)。骤冷流可以是作为流286的下游部分的气流,这在本文中有详细解释。骤冷流可以包括乙烯、丙烯或丁烯异构体(例如,反应产物)中的一种或多种。
26.骤冷流296的温度可以显著低于流286的温度。举例来说,骤冷流296的温度可以低于150℃,如低于125℃、低于100℃、低于75℃或甚至低于50℃。骤冷流296可以与流290(热交换器406的出口)的温度大致相同。在一个或多个实施例中,骤冷流296的温度可以比流286的温度低至少200℃(如比流286的温度低至少250℃、低至少300℃、低至少350℃、低至少400℃、低至少450℃或甚至低至少500℃)。
27.骤冷流296与流286的混合在流287中形成中温脱氢产物。流287的温度可以比流286低至少10℃。举例来说,流287的温度可以比流286低至少15℃、20℃、25℃、30℃、35℃、40℃、45℃、50℃、60℃、70℃、80℃、90℃、100℃、110℃、120℃、130℃、140℃或甚至150℃。与流286相比,在流287中丙烷、正丁烷、乙烷或乙苯及其反应产物中的一种或多种的热裂化速率可以降低。举例来说,至少部分由于温度的降低,流287中这些组分的热裂化速率可以是流286中的热裂化速率的小于90%、小于85%、小于80%、小于75%、小于70%、小于65%、小于60%、小于55%、小于50%、小于45%、小于40%、小于35%、小于30%、小于25%、小于20%、小于15%、小于10%或甚至小于5%。
28.二级分离装置404可以进一步分离流287中的任何剩余固体如催化剂并且将它们经由管线298返回到催化剂处理部分300。流288可以含有很少或不含固体。流288仍可以称为中温脱氢产物,因为它与流287的温度大致相同。然后处理流288以经由例如热交换器406冷却其内容物。在附加实施例中,冷却可以通过液体骤冷系统或冷却流的其他已知方式来进行。热交换器406的产物流是流290,其可以被称为冷却的脱氢产物。流290的温度可以与关于骤冷流296所描述的温度大致相同。应当理解,流290和/或流296可以经受压缩,使得它们沿所需方向流动。举例来说,出于输送目的,流296通常可以具有比流287的压力更大的压力。
29.为了形成骤冷流296,将流290的至少一部分再循环回到系统中。应当注意,流296的化学内容物可以与流286的化学内容物相似或相同(即,自反应器20中的反应后,除一些残余热裂化之外没有发生另外的反应)。通过与骤冷流296接触而使流286骤冷可以将流286的内容物冷却到显著降低热裂化反应速率的温度。流286可以处于发生热裂化的温度并且这类热裂化可以降低所需反应产物的选择性。
30.应当理解,骤冷流不包括任何显著量的蒸汽。举例来说,骤冷流包含小于3wt%蒸汽(如小于2wt%蒸汽、小于1wt%蒸汽,或在附加实施例中基本上没有蒸汽)。如以下实施例中所述,与使用蒸汽相比,使用脱氢产物流作为骤冷可以具有许多益处。
31.现在将参照图2详细讨论实例反应器系统和根据这类反应器系统的使用来处理化学流的方法。虽然在一些情况下,相对于图1,在图2中利用了类似的数字,但应当理解图1的实施例可以利用广泛多种反应器类型,并且图2的实施例仅是一种这类类型的实例。应当理解,本文所述的骤冷实施例可以适合与其他反应器系统配置一起使用,包括不包括通过如本文所述的循环催化剂移动再生的那些。
32.现参考图2,示意性地描绘实例反应器系统102。反应器系统102通常包含多个系统组件,如反应器部分200和催化剂处理部分300。如本文在图2的上下文中所使用的,反应器部分200通常指代反应器系统102的发生主要过程反应的部分。举例来说,反应器系统102可以是脱氢系统,其中在存在脱氢催化剂的情况下在反应器系统102的反应器部分200中对进料流进行脱氢。
33.反应器部分200包含反应器202,所述反应器可以包括下游反应器区段230和上游反应器区段250。根据一个或多个实施例,如图2所描绘,反应器部分200可以另外包括催化剂分离区段210,其用于将催化剂与反应器202中形成的化学产物分离。同样,如本文所用,催化剂处理部分300通常是指反应器系统102中以某种方式如通过燃烧来处理催化剂的部分。催化剂处理部分300可以包含燃烧器350和提升管330,并且可以任选地包含催化剂分离区段310。在一些实施例中,催化剂可以通过烧掉催化剂处理部分300中的污染物如焦炭而再生。在附加实施例中,催化剂可以在催化剂处理部分300中加热。如果在催化剂上没有形成焦炭或另一种可燃材料,或在催化剂上形成的焦炭量不足以燃烧以将催化剂加热到所需温度,则可以使用补充燃料来加热催化剂处理部分300中的催化剂。在一个或多个实施例中,催化剂分离区段210可以与燃烧器350流体连通(例如,通过竖管426),并且催化剂分离区段310可以与上游反应器区段250流体连通(例如,通过竖管424和输送提升管430)。
34.如关于图2所描述,进料流可以进入输送提升管430,并且产物流可以经由管道420离开反应器系统102。根据一个或多个实施例,反应器系统102可以通过将化学进料(例如,在进料流中)和流化催化剂进料到上游反应器区段250中来操作。化学进料与上游反应器区段250中的催化剂接触,并且每个化学进料向上流入并通过下游反应器区段230以产生化学产物。可以将化学产物和催化剂从下游反应器区段230中传递出到催化剂分离区段210中的分离装置220。催化剂在分离装置220中与化学产物分离。将化学产物输送出催化剂分离区段210。将分离的催化剂从催化剂分离区段210传递到燃烧器350。在燃烧器350中,催化剂可以通过例如燃烧来处理。例如但不限于,催化剂可以是脱焦的和/或可燃烧补充燃料以加热催化剂。然后,将催化剂从燃烧器350中传递出去,并且通过提升管330到提升管终端分离器378,其中来自提升管330的气体和固体组分被至少部分地分离。蒸气和剩余固体被输送到催化剂分离区段310中的二级分离装置320,在所述二级分离装置中剩余催化剂与来自催化剂处理的气体(例如,通过燃烧废催化剂或补充燃料发出的气体)分离。分离的催化剂然后经由竖管424和输送提升管430从催化剂分离区段310传递到上游反应器区段250,其中所述催化剂进一步用于催化反应。因此,催化剂在操作中可以在反应器部分200和催化剂处理部分300之间循环。一般来说,包括进料流和产物流的经处理化学品流可以为气态,且催化剂可以为流化颗粒状固体。
35.如图2所描绘,上游反应器区段250可以定位在下游反应器区段230的下方。这样的配置可以称为反应器202中的上流式配置。反应器202也可以是下流式反应器,其中上游反应器区段250可以定位在下游反应器区段230的上方。对于反应器系统102的反应器部分200也设想了其他反应器配置。
36.如本文所述,上游反应器区段250可以包括容器、转鼓、机筒、桶,或适合于给定化学反应的其他容器。在一个或多个实施例中,上游反应器区段250的形状通常可以是圆柱形的(即,具有大体上圆形的横截面形状),或可以替代地是非圆柱形形状,如棱柱形状,所述棱柱形状的横截面形状为三角形、矩形、五边形、六边形、八边形、椭圆形、或其他多边形、或弯曲闭合形状、或其组合。如贯穿本公开所用,上游反应器区段250可以通常包括金属框架,并且可以另外包括耐火衬里或用于保护金属框架和/或控制处理条件的其他材料。如图2所描绘,上游反应器区段250可以包括下部反应器部分催化剂入口端口252,其限定了输送提升管430与上游反应器区段250的连接。
37.上游反应器区段250可以连接到输送提升管430,所述输送提升管在操作中可以将进料流中经处理的催化剂和/或反应物化学品提供到反应器部分200。经处理的催化剂和/或反应物化学品可以与容纳在上游反应器区段250中的分配器260混合。经由输送提升管430进入上游反应器区段250的催化剂可以通过竖管424传递到输送提升管430,由此从催化剂处理部分300到达。在一些实施例中,催化剂可以经由竖管422直接从催化剂分离区段210过来并且进入输送提升管430,其中催化剂进入上游反应器区段250。催化剂也可以经由422直接进料到上游反应器区段250。此催化剂可以稍微失活,但是在一些实施例中仍可以适合于在上游反应器区段250中反应。如本文所用,“失活”可以指被如焦炭的物质污染或温度比所需更低的催化剂。再生可以去除如焦炭的污染物、升高催化剂的温度、或两者。
38.仍然参考图2,反应器部分200可以包含用以将反应物、产物和/或催化剂从上游反应器区段250输送到催化剂分离区段210的下游反应器区段230。在一个或多个实施例中,下游反应器区段230的形状通常可以是圆柱形的(即,具有大体上圆形的横截面形状),或可以替代地是非圆柱形形状,如棱柱形状,所述棱柱形状的横截面形状为三角形、矩形、五边形、六边形、八边形、椭圆形、或其他多边形、或弯曲闭合形状、或其组合。如贯穿本公开所用,下游反应器区段230可以通常包括金属框架,并且可以另外包括耐火衬里或用于保护金属框架和/或控制处理条件的其他材料。
39.根据一些实施例,下游反应器区段230可以包括外部提升管区段232和内部提升管区段234。如本文所用,“外部提升管区段”是指提升管在催化剂分离区段210的外部的部分,并且“内部提升管区段”是指提升管在催化剂分离区段210内的部分。举例来说,在图2所描绘的实施例中,反应器部分200的内部提升管区段234可以定位在催化剂分离区段210内,而外部提升管区段232定位在催化剂分离区段210的外部。
40.如图2所描绘,上游反应器区段250可以经由过渡区段258连接到下游反应器区段230。上游反应器区段250通常可以包含比下游反应器区段230更大的横截面积。过渡区段258可以从上游反应器区段250的横截面的大小逐渐变细到下游反应器区段230的横截面的大小,使得过渡区段258从上游反应器区段250向内突出到下游反应器区段230。
41.在一些实施例中,如其中上游反应器区段250和下游反应器区段230具有类似横截面形状的那些,过渡区段258可以成型为平截头体。举例来说,对于包含圆柱形上游反应器区段250和圆柱形下游反应器区段230的反应器部分200的实施例,过渡区段258可以成型为圆锥形平截头体。然而,应当理解,本文设想了广泛多种上游反应器区段250形状,其连接各种形状和尺寸的上游反应器区段250和下游反应器区段230。
42.在一个或多个实施例中,基于形状、尺寸和其他处理条件,如上游反应器区段250和下游反应器区段230中的温度和压力,上游反应器区段250可以以等温或接近等温的方式操作,如在快速流化、湍流或鼓泡床上流式反应器中,而下游反应器区段230可以以更多的活塞流动方式操作,如在提升管反应器中。举例来说,图2的反应器202可以包含作为快速流化、湍流或鼓泡床反应器操作的上游反应器区段250和作为稀相提升管反应器操作的下游反应器区段230,结果是平均催化剂和气体流同时向上移动。如在本文中所用的术语,“平均流”是指净流,即,全部向上流减去逆流或反流,这一般来说是流化颗粒行为的典型特征。如本文所述,“快速流化”反应器可以指利用流化形态的反应器,其中气相的表观速度大于扼流速度并且在操作中可以为半致密的。如本文所述,“湍流”反应器可以指其中表观速度小
于扼流速度并且比快速流化形态更密集的流化形态。如本文所述,“鼓泡床”反应器可以指其中在高致密床中明确限定的气泡存在于两个明确划分的相中的流化形态。“扼流速度”是指在竖直运送管线中在稀相模式中维持固体需要的最小速度。如本文所述,“稀相提升管”可以指以输送速度操作的提升管反应器,其中气体和催化剂在稀相中具有大致相同的速度。
43.在一个或多个实施例中,反应器202中的压力可以在6.0至44.7平方英寸绝对磅的范围内(psia,约41.4千帕,kpa,至约308.2kpa),但是在一些实施例中,可以采用更窄的选择范围,如15.0psia至35.0psia(约103.4kpa至约241.3kpa)。举例来说,压力可以为15.0psia到30.0psia(约103.4kpa到约206.8kpa)、17.0psia到28.0psia(约117.2kpa到约193.1kpa)或19.0psia到25.0psia(约131.0kpa到约172.4kpa)。在本文中从标准(非si)到公制(si)表达的单位转化包括“约”以指示由于转化而可以存在于公制(si)表达中的舍入。
44.在附加实施例中,用于所公开方法的重时空速(whsv)在反应器中的范围可以为0.1磅(lb)到100lb化学进料每小时(h)每lb催化剂(lb进料/h/lb催化剂)。举例来说,在反应器202包含作为快速流化、湍流或鼓泡床反应器操作的上游反应器区段250和作为稀相提升管反应器操作的下游反应器区段230的情况下,上游反应器区段250中的表观气速的范围可以为2英尺/秒(约0.61米/秒)到10英尺/秒(约3.05米/秒),并且下游反应器区段230中的表观气速的范围可以为30英尺/秒(约9.14米/秒)到70英尺/秒(约21.31米/秒)。在附加实施例中,完全为提升管类型的反应器配置可以在单个高表观气速下操作,例如,在一些实施例中始终为至少30英尺/秒(大约9.15米/秒)。
45.在附加实施例中,在重量比重量(w/w)的基础上,反应器202中的催化剂与进料流的比率范围可以为5到100。在一些实施例中,比率可以在10到40的范围内,如12到36,或12到24。
46.在附加实施例中,上游反应器区段250中的催化剂通量可以为1磅每平方英尺-秒(lb/ft
2-s)(约4.89kg/m
2-s)到20lb/ft
2-s(到约97.7kg/m
2-s),并且下游反应器区段230中的催化剂通量可以为10lb/ft
2-s(约48.9kg/m
2-s)到100lb/ft
2-s(约489kg/m
2-s)。
47.仍然参考图2,在操作中,催化剂可以通过下游反应器区段230(从上游反应器区段250)向上移动,并且进入分离装置220。可以经由催化剂分离区段210的气体出口端口216处的管道420从反应器系统102中去除分离的蒸气。根据一个或多个实施例,分离装置220可以包含一个或多个分离单元,本文称为初级和二级分离单元,其可以为两级或更多级旋流分离。应当了解,图2示意性地描绘了作为通用分离装置220的单个旋风分离器。然而,如图1所描绘,可以利用多个串联的分离装置,如旋风分离器或过滤器。在其中分离装置220包含多于一个分离装置的实施例中,流化流进入的第一个分离装置被称为初级分离装置。来自初级分离装置的流化流出物可以进入二级分离装置中以进一步分离。初级分离装置可以包括例如初级旋风分离器和可以名称vss(可以购自uop)、ld2(可以购自史威公司(stone and webster))和rs2(可以购自史威公司)商购的系统。初级分离装置描述于例如美国专利第4,579,716号;第5,190,650号;和第5,275,641号,它们各自以全文引用的方式并入本文中。在利用初级旋风分离器作为初级旋流分离装置的一些分离系统中,可以利用一组或多组附加分离装置(即,二级分离装置和/或三级分离装置)来使催化剂与产物气体进一步分离。应当理解,任何初级分离装置和/或二级分离装置,以任何组合,都可以用于本发明的实施例中。
48.仍然参考图2,骤冷流296可以接触初级分离装置的气体流出物并形成中温脱氢产物。在上文参考图1示出和描述骤冷流296的内容物。
49.根据一些实施例,在分离装置220中将催化剂与蒸气分离后,催化剂通常可以移动通过汽提器224到达反应器催化剂出口端口222,其中催化剂经由竖管426从反应器部分200中转移出去并进入催化剂处理部分300。任选地,催化剂还可以经由竖管422直接往回转移到上游反应器区段250中。替代地,催化剂可以与输送提升管430中的经处理的催化剂预混合。
50.如根据图2的实施例详细所述,根据一个或多个实施例,可以通过以下一个或多个步骤对催化剂进行处理:将催化剂从反应器202传递到燃烧器350中;在燃烧器350中燃烧补充燃料源或来自失活的催化剂的焦炭;并且将经过加热的催化剂从燃烧器350传递到反应器202。
51.现在参考催化剂处理部分300,如图2所描绘,催化剂处理部分300的燃烧器350可以包括一个或多个下部反应器部分入口端口352并且可以与提升管330流体连通。燃烧器350可以经由竖管426与催化剂分离区段210流体连通,所述竖管可以将废催化剂从反应器部分200供应到催化剂处理部分300以用于再生。燃烧器350可以包括附加下部反应器区段入口端口352,其中空气入口428连接到燃烧器350。空气入口428可以供应反应性气体,其可以与废催化剂或补充燃料反应以至少部分地再生催化剂。举例来说,催化剂可以在上游反应器区段250中的反应后焦化,并且焦炭可以通过燃烧反应从催化剂中去除(即,再生催化剂)。举例来说,可以经由空气入口428将氧化剂(如空气)进料到燃烧器350中。替代地或另外,如当在催化剂上未形成大量焦炭时,可以将补充燃料注入燃烧器350中,可以燃烧所述补充燃料以加热催化剂。在燃烧后,经处理的催化剂可以在催化剂分离区段310中分离,并且经由竖管424递送回到反应器部分200中。
52.根据一个或多个实施例,所述反应可以是脱氢反应。根据这类实施例,进料流可以包含乙烷、丙烷、正丁烷、异丁烷或乙苯中的一种或多种。举例来说,如果反应是脱氢反应,则进料流可以包含乙烷、丙烷、正丁烷、异丁烷或乙苯中的一种或多种。根据一个或多个实施例,进料流可以包含至少50wt%、至少60wt%、至少70wt%、至少80wt%、至少90wt%、至少95wt%或甚至至少99wt%的乙烷。在附加实施例中,进料流可以包含至少50wt%、至少60wt%、至少70wt%、至少80wt%、至少90wt%、至少95wt%或甚至至少99wt%的丙烷。
53.在附加实施例中,进料流可以包含至少50wt%、至少60wt%、至少70wt%、至少80wt%、至少90wt%、至少95wt%或甚至至少99wt%的正丁烷或异丁烷。在附加实施例中,进料流可以包含至少50wt%、至少60wt%、至少70wt%、至少80wt%、至少90wt%、至少95wt%或甚至至少99wt%的异丁烷。在附加实施例中,进料流可以包含至少50wt%、至少60wt%、至少70wt%、至少80wt%、至少90wt%、至少95wt%或甚至至少99wt%的乙烷、丙烷、正丁烷和异丁烷的总和。
54.在一个或多个实施例中,脱氢反应可以利用镓和/或铂催化剂作为催化剂。在这类实施例中,催化剂可以包含镓和/或铂催化剂。举例来说,如果反应是脱氢反应,则催化剂可以包含镓和/或铂催化剂。如本文所述,镓和/或铂催化剂包含镓、铂,或两者。镓和/或铂催化剂可以由氧化铝或氧化铝二氧化硅载体携带,并且可以任选地包含钾。这类镓和/或铂催化剂公开于美国专利第8,669,406号中,所述专利以全文引用的方式并入本文中。然而,应
当理解,其他合适的脱氢催化剂可以用于执行脱氢反应。
55.图3示出了图2的反应器部分200的上部的实施例,有时称为反应器容器510,其中分离装置包括初级分离装置520。初级分离装置520含于外壳530内并且具有主体521、入口522、出口524和固体排放料腿526。流体化固体流通过入口522进入初级分离装置520。在初级分离装置520中,从流体化固体流中分离大部分的夹带的固体(例如催化剂颗粒)。分离的固体通过排放料腿526离开初级分离装置,留下初级分离装置流出物,其包含未被初级分离装置520去除的固体以及流体(例如气态产物)。初级分离装置流出物竖直地向上传递并通过出口524从初级分离装置520中传递出,并通过初级分离装置出口管542并且然后通过交叉管道570进入二级分离装置540。二级分离装置540进一步包含主体541、出口544和固体排放料腿546。二级分离装置540进一步从初级分离装置流出物中分离出固体。在二级分离装置540中分离出的固体通过料腿546向下离开。
56.如图3所描绘,骤冷流296可以进入初级分离装置出口管542的上部,其定位于初级分离装置520的正上方。据信,对于骤冷流与初级分离装置540的流出物的适当混合以及减少初级分离装置540的出口和与骤冷流296的混合之间的停留时间而言,这样的布置可能是合乎需要的。
57.现在参考图4,描绘了骤冷流296与初级分离装置出口管542的连接的一个实施例的俯视图。骤冷流296可以经由管道或其他类似导管以基本上竖直的角度直接到达初级分离装置出口管542的顶部中。中温脱氢产物然后可以通过交叉管道570传递到二级分离装置540。
58.二级分离装置出口544流体地连接到第二气室550。第二气室550包含圆柱形裙部552、底板554和第第二气室出口556,其允许二级分离装置流出物从第二气室传递并离开容器510。如图3所示,第二气室容纳于更大、更高容量的第一气室560内。第一气室560包含裙部562和底板564。初级分离装置520可以由第一气室560支撑。
59.也如图3所示,外壳530进一步容纳提升管535。未分离的流化固体颗粒流通过提升管535进入外壳,所述提升管终止于板536。提升管535与初级分离装置520的入口522流体地连接,即允许流化固体颗粒通过,使得未分离的流化固体颗粒流可以从提升管535传递到初级分离装置520中。如果使用多于两个分离级,则来自最终分离级的流出物进入第二气室。应理解,虽然图3示意性地示出了仅一个初级分离装置和一个二级分离装置,但附加的初级和二级分离装置可以围绕提升管的外围放置。举例来说,出口管545可以连接到另一个二级分离装置(未示出),所述二级分离装置又由初级分离装置520或由另一个初级分离装置(未示出)进料。
60.实例
61.提供了一个或多个实例,其可以说明所公开的本技术的各个方面。
62.实例1
63.建模用于确定各种烃进料(包括丙烷、正丁烷、乙烷和乙苯)中热裂化反应速率的降低。虽然应了解化学反应的产物也可能发生热裂化,但是流的未反应部分的热裂化为整个流的裂化提供了合理的估算并用于简化模型。所述模型也没有考虑热裂化产物的化学平衡,因为热裂化的反应速率的结果可以忽略不计。应当了解,产物流温度的降低将减少流中产物成分和未反应成分两者的热裂化。来自公开文献的幂律速率表达式用于估算反应物的
热裂化速率。具体来说,丙烷的反应速率数据来自froment在“buekens,a.g.;froment,g.f.丙烷的热裂化(thermal cracking of propane).《i&ec工艺设计和开发(i&ec process design and development)》.第7卷第3期(1968)435-447”中所述的laidler系数。正丁烷的反应速率数据来自“sagert,n.h.;laidler,k.j.正丁烷热解的动力学和机制(kinetics and mechanisms of the pyrolysis of n-butane).《加拿大化学杂志(canadian journal of chemistry)》.第41卷(1963)838-847”。乙烷的反应速率数据来自“bartlit,j.r.;bliss,h.乙烷热解的动力学(kinetics of ethane pyrolysis).《美国化学工程师会志(aiche journal)》.第11卷第3期(1965)”。乙苯的反应速率数据来自“domke,s.b.;pogue,r.f.;van neer,f.j.r.;smith,c.m.;wojciechowski,b.w.使用温度扫描反应器对乙苯热解的动力学的研究(investigation of the kinetics of ethylbenzene pyrolysis using a temperature-scanning reactor).《工业与工程化学研究(industrial&engineering chemistry research)》.第40卷(2001)5878-5884”。
64.所有速率表达式都采用以下形式:
[0065][0066]
其中,i是反应物,ri是以gmol ft-3
s-1
为单位的反应速率,ki是速率常数,n是相对于反应物的反应级数,并且ci是以gmol ft-3
为单位的反应物的气相浓度。ki的单位取决于反应级数。所有速率表达式都假设速率常数为arrhenius形式:
[0067][0068]
其中,ai是指前因子,ei是以kcal gmol-1
为单位的活化能,t是以开尔文为单位的绝对温度,而r是以kcal gmol-1
k-1
为单位的气体常数。ai的单位取决于反应级数。表1提供了上文对于每种反应物所描述的速率参数的文献值。
[0069]
表1.丙烷、正丁烷、乙烷和乙苯的热裂化的动力学参数。
[0070]
参数单位i=丙烷i=正丁烷i=乙烷i=乙苯n
i-1.01.51.01.0eikcal gmol-1
67.159.964.162.3ais-1
,或(ft3)
1/2
gmol-1/2
s-1
2.58e+141.93e+133.16e+134.74e+13
[0071]
然后在目标温度和每种反应物的浓度下使用方程1-2估算热裂化速率。(在所有情况下,假设反应物分压为1.0个大气压(14.7psi)。)表2提供了结果。
[0072]
表2.每种反应物在目标温度和1.0个大气压下的反应速率。
[0073]
说明单位i=丙烷i=正丁烷i=乙烷i=乙苯目标温度℃620600750595rigmol ft-3
s-1
3.8e-034.9e-032.2e-013.9e-03
[0074]
最后,对其中温度相对于表2中列出的目标温度降低10℃至150℃的情况,估算热裂化速率。结果示于图5a和5b中,其描绘了相同的数据,但相对于y轴的比例不同。结果表示为使用以下公式的温度骤冷之后的热裂化速率与目标温度下的热裂化速率的比率:
[0075]
[0076]
其中t2是骤冷之后的温度(例如,在本文中描述为“中温脱氢产物”)并且t1是反应物的相应目标温度(例如,脱氢反应器中的温度)。方程3源自方程1-2,并且只需要知道活化能。在10℃温度骤冷之后,丙烷、正丁烷和乙苯的热裂化速率降低了约33-35%,而乙烷的热裂化速率降低了约27%。在20℃温度骤冷之后,丙烷、正丁烷和乙苯的热裂化速率降低了约55-58%,而乙烷的热裂化速率降低了约47%。在30℃温度骤冷之后,丙烷、正丁烷和乙苯的热裂化速率降低了约71-73%,而乙烷的热裂化速率降低了约61%。
[0077]
实例2
[0078]
计算蒸汽或粗丙烯相对于将初级分离装置的流出物中的产物温度骤冷不同程度所需的裂化气体产物流的百分比并示于图6中,其示出了将流骤冷至特定温度降低所需的蒸汽或粗丙烯的体积/体积百分比。如在图6中可以看出,用于骤冷的粗丙烯始终是骤冷相同的温度降低所需的蒸汽的大约32%。举例来说,为了骤冷10℃,相对于离开初级分离装置的产物流,需要5.5%(体积/体积)的蒸汽。作为比较,相对于离开初级分离装置的产物流,仅需要1.77%(体积/体积)的粗丙烯。当需要较小的设备时,通过粗丙烯骤冷所需的体积流量较小是有利的。在实例2的计算中,假设蒸汽为178℃,并且假设再循环的粗丙烯为45℃(骤冷流温度)。骤冷之前的产物流(有时称为“高温脱氢产物”)的温度假设为620℃。
[0079]
实例3
[0080]
利用建模来说明通过本技术的实施例实现的丙烯选择性和转化率。对于丙烷到丙烯的反应,计算了作为骤冷后停留时间、骤冷介质和温度下降的函数的对丙烯的累积选择性并示于图7中。它表明,在不对工艺流进行骤冷的情况下,以及在初级分离装置的出口和气体-气体换热器的入口之间的停留时间为秒或更长的数量级的情况下,热(非催化)反应将降低对丙烯的累积选择性。举例来说,如果工艺流在未骤冷的情况下离开初级分离装置并且在到达气体-气体换热器之前具有3秒的停留时间,则对丙烯的累积选择性降低约1.7%,并且在骤冷10℃之后累积选择性的降低变为约1.1%,而在骤冷20℃之后变为约0.7%。应当注意,对于相同的温度下降,与使用粗丙烯作为骤冷介质的情况相比,使用蒸汽作为骤冷介质的情况具有选择性优势,因为蒸汽会降低烃的分压并且因此降低进一步热裂化反应的驱动力。然而,与温度变化带来的好处相比,蒸汽稀释带来的附加好处是微不足道的。
[0081]
对初级分离装置出口处的工艺流做出了以下假设:累积丙烯选择性为96.5%,丙烷转化率为46.4%,温度为620℃,并且压力为19psia。假设骤冷流和产物流即刻混合,并且假设所得的流保持等温,直到气体-气体交换器的压降可以忽略不计。假设在初级分离装置的出口和气体-气体交换器的入口之间仅发生热(非催化)反应,因为大部分催化剂在初级分离装置中被分离。使用对应于来自实例1的丙烷的幂律表达式和系数(对于脱氢产物丙烯的热裂化具有相同的假设),对可用的未反应丙烷获取热反应速率。可以参考来自实例2的图6来确定骤冷所需的蒸汽或粗丙烯的量。
[0082]
此外,使用类似的方法,图8描绘了热交换器入口处的丙烷转化率。如图8所示,骤冷后更高的工艺流温度(即“中温脱氢产物”)对应于由于热裂化而引起的更大的丙烷转化率。
[0083]
出于描述和定义本发明的目的,应注意,术语“约”在本文中用于表示可以归因于任何定量比较、值、测量或其他表示的固有不确定度。术语在本文中还被利用来表示在不导
致在所关注的主题的基本功能改变的情况下,定量表示可以从规定的参考变化的程度。
[0084]
应注意,所附权利要求书中的一项或多项利用术语“其中”作为过渡短语。出于定义本发明的目的,应注意,此术语在权利要求中引入为开放的过渡短语,其用于引入结构的一系列特征的引述并且应以与更多常用开放的前导术语“包含”相同的方式解释。
[0085]
通常,本文所述的反应器系统102的任何系统单元的“入口端口”和“出口端口”指代系统单元中的开口、孔、通道、开孔、间隙或其他相似机械特征。举例来说,入口端口允许材料进入特定系统单元并且出口端口允许材料从特定系统单元离开。通常,出口端口或入口端口将定义反应器系统102的系统单元的区域,管道、导管、管子、软管、材料输送管线或相似机械特征附接到所述区域,或定义另一个系统单元直接附接到的系统的一部分。虽然入口端口和出口端口在本文中有时可以描述为功能性地操作,但是其可以具有类似或相同物理特性,并且其在可以操作系统中的相应功能不应被解释为限制其物理结构。
[0086]
对于本领域的技术人员将显而易见的是,在不脱离本发明的精神和范围的情况下,可以对本发明进行各种修改和变化。因为本领域的技术人员可以进行并入本发明的精神和实质的所公开的实施例的修改组合、子组合和变化,所以本发明应被解释为包括在所附权利要求书以及其等效物的范围内的所有事物。
[0087]
在本公开的第一方面,一种用于形成轻质烯烃的方法可以包括将烃进料流引入反应器中,使烃进料流与反应器中的脱氢催化剂反应以形成高温脱氢产物,在初级分离装置中从高温脱氢产物中分离脱氢催化剂的至少一部分,在高温脱氢产物从初级分离装置中离开后,将高温脱氢产物与骤冷流合并以冷却高温脱氢产物并形成中温脱氢产物,以及冷却中温脱氢产物以形成冷却的脱氢产物。脱氢产物可以包括烃进料流的未催化反应的至少一部分。初级分离装置中的脱氢产物和脱氢催化剂的温度可以为至少550℃。骤冷流可以是气流。中温脱氢产物的温度可以比高温脱氢产物的温度低至少10℃。冷却的脱氢产物的一部分可以用作骤冷流的至少一部分。
[0088]
本公开的第二方面可以包括第一方面,其中烃进料可以包括丙烷、正丁烷、异丁烷、乙烷、乙苯或其组合。
[0089]
本公开的第三方面可以包括第一或第二方面中的任一项,其中骤冷流可以比高温脱氢产物的温度低至少300℃。
[0090]
本公开的第四方面可以包括第一至第三方面中的任一项,其中烃进料流的未催化反应的部分在中温脱氢产物中的热裂化速率可以是其在高温脱氢产物中的热裂化速率的小于90%。
[0091]
本公开的第五方面可以包括第一至第四方面中的任一项,其进一步包括将中温产物传递到二级分离装置,在所述二级分离装置中可以从中温产物中去除脱氢催化剂的剩余部分。
[0092]
本公开的第六方面可以包括第一至第五方面中的任一项,其中冷却的脱氢产物可以具有小于或等于150℃的温度。
[0093]
本公开的第七方面可以包括第一至第六方面中的任一项,其中热交换器和/或液体骤冷系统可以将中温脱氢产物冷却成冷却的脱氢产物。
[0094]
本公开的第八方面可以包括第一至第七方面中的任一项,其中骤冷流可以包含小于3wt%蒸汽。
[0095]
本公开的第九方面可以包括第一至第八方面中的任一项,其中脱氢催化剂可以是固体并且高温脱氢产物可以是气体。
[0096]
本公开的第十方面可以包括第一至第九方面中的任一项,其中骤冷流可以包括乙烯、丙烯或丁烯异构体中的一种或多种。
[0097]
本公开的第十一方面可以包括第一至第十方面中的任一项,其中脱氢催化剂可以为镓和/或铂催化剂。
[0098]
在本公开的第十二方面,一种用于形成轻质烯烃的方法可以包括将烃进料流引入反应器中,使烃进料流与反应器中的脱氢催化剂反应以形成高温脱氢产物,在初级分离装置中从高温脱氢产物中分离脱氢催化剂的至少一部分,在高温脱氢产物从初级分离装置中离开后,将高温脱氢产物与骤冷流合并以冷却高温脱氢产物并形成中温脱氢产物,将中温产物传递到二级分离装置,在所述二级分离装置中从中温产物中去除脱氢催化剂的剩余部分,以及冷却中温脱氢产物以形成冷却的脱氢产物。脱氢产物可以包括烃进料流的未催化反应的至少一部分。初级分离装置中的脱氢产物和脱氢催化剂的温度可以为至少550℃。骤冷流可以是气流。中温脱氢产物的温度可以比高温脱氢产物的温度低至少10℃。冷却的脱氢产物的一部分可以用作骤冷流的至少一部分。
[0099]
本公开的第十三方面可以包括第十二方面,其中烃进料可以包括丙烷、正丁烷、异丁烷、乙烷、乙苯或其组合。
[0100]
本公开的第十四方面可以包括第十二或第十三方面中的任一项,其中烃进料流的未催化反应的部分在中温脱氢产物中的热裂化速率可以是其在高温脱氢产物中的热裂化速率的小于70%。
[0101]
本公开的第十五方面可以包括第十二至第十四方面中的任一项,其中冷却的脱氢产物可以具有小于或等于150℃的温度。