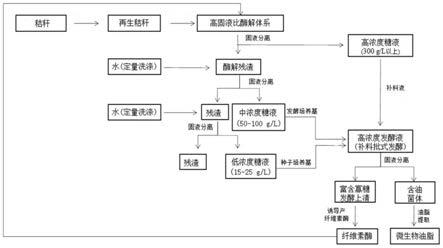
1.本发明属于木质纤维素资源转化利用及生物炼制技术领域,尤其涉及一种利用秸秆资源制备微生物油脂的方法。
背景技术:2.随着煤炭、石油和天然气的日益枯竭,环境污染的日趋严重,有关燃料乙醇及生物柴油等清洁可再生能源的研究开始兴起。木质纤维类生物质由于其储量丰富、成本低廉、分布广泛等诸多优点,被认为是制备生物能源的重要原料之一。其中农作物秸秆就是一类典型的木质纤维素类生物质,将秸秆资源转化为微生物油脂,可以为生物柴油的生产提供稳定且廉价的原料。简单来说,木质纤维素转化制微生物油脂的一般步骤为:粉碎—预处理—酶水解—油脂发酵—油脂提取。虽然木质纤维素制油脂已经被广泛地研究,但目前仍没有成套技术被大规模商业化应用。当前木质纤维类生物质制微生物油脂仍然存在着预处理、酶水解及发酵成本较高的问题。
3.木质纤维类生物质预处理是通过物理作用或化学试剂,或者是两者协同作用,使木质纤维素的天然结构发生改变,木质素及半纤维素等阻碍酶水解的结构被部分溶解或解聚,并降低纤维素及半纤维素的聚合度,便于后续的酶水解。但就目前而言,生物质的预处理技术依然存在着一些尚未克服的缺点,例如处理成本过高、碳水化物损失、产生的抑制剂和预处理介质毒性较大对后续酶解及发酵过程产生负面影响。
4.酶水解是指将木质纤维素中的糖类高聚物水解成可发酵性糖的过程,需借助纤维素酶来进行水解。在木质纤维素的生物转化过程中,生物质的酶解糖化过程十分重要。而在酶解过程中,体系的固体含量又是影响整个过程经济可行性的重要因素。常规生物质转化工艺中,固体含量一般较低,导致水解液糖浓度低,设备利用率低,废水排放量大,资金成本较高。
5.对于油脂发酵过程而言,一般涉及到种子培养基与发酵培养基两种培养基,这两种培养液由于其功能不同,因此在浓度及营养成分上有着较大差异。通常种子培养基所要求的糖浓度较低,一般15~25g/l即可;而发酵培养基对糖的浓度要求稍高一些,但不宜超过100g/l。为了提高发酵效率,发酵过程中一般会采用高密度发酵方式,需要尽可能地控制补料过程中发酵液的体积,对补料液的糖浓度的要求也相对较高,由此可见,有必要制备出高浓度的糖液,但是目前在不影响酶水解前提下,制备出高浓度的糖液也是个难题。
6.因此,目前木质纤维素转化制微生物油脂工艺中,木质纤维素制备高浓度糖液得率低,发酵效率不高,而且工艺中所需的纤维素酶采用商品酶,种子培养基与发酵培养是采用商品原料进行配制,需要分三次来分别生产种子培养基、发酵培养基和高浓度补料液这三种不同浓度要求的糖液,现有方式显然不够经济,会明显提高工艺成本。
技术实现要素:7.鉴于上述问题,本发明的目的在于提供一种利用秸秆资源制备微生物油脂的方
法,旨在解决现有工艺方法发酵效率低、成本高的技术问题。
8.本发明采用如下技术方案:
9.所述利用秸秆资源制备微生物油脂的方法,包括下述步骤:
10.步骤s1、预处理秸秆;
11.步骤s2、取一定量预处理秸秆置入酶解反应器中并加入纤维素酶,调整初始固液比启动酶水解,将纤维素酶液均匀地喷洒于预处理的秸秆中并充分混合得到含酶秸秆,然后采用流加补料的方式,以一定速率持续地将含酶秸秆补加至酶解反应器中,至固液比达到目标值,酶水解一段时间后结束;
12.步骤s3、酶水解结束后进行固液分离,得到高浓度糖液和酶解残渣,将酶解残渣进行两次定量水洗涤,具体的,第一次定量水洗涤固液分离收集到的洗涤水为中浓度糖液,收集到的酶解残渣进行第二次定量水洗涤,固液分离收集到低浓度糖液和富含木质素残渣;
13.步骤s4、取低浓度糖液添加适量营养物质得到种子培养基,挑取一环产油酵母接种于种子培养基中培养,得到种子液;取中浓度糖液添加适量营养物质得到发酵培养基,将所述种子液接种至发酵培养基中培养,当还原糖浓度低于10g/l时向其中补入所述高浓度糖液进行补料批式发酵;
14.步骤s5、发酵结束后固液分离,菌体用于提取微生物油脂,调整发酵上清液的糖浓度至5~15g/l,添加适量营养物质后作为产酶培养基,接种产酶真菌培养,收获的纤维素酶。
15.进一步的,所述步骤s5收获的纤维素酶用于步骤s1的秸秆高固液比酶水解。
16.进一步的,所述初始固液比为5~10%w/v,含酶秸秆的补料速率为5~6.5g/l/h,所述固液比的目标值为50%w/v,当固液比达到目标值后,酶水解96~144h后结束。
17.进一步的,高浓度糖液的糖浓度大于300g/l,中浓度糖液的糖浓度为50~100g/l,低浓度糖液的糖浓度为15~25g/l。
18.进一步的,纤维素酶液均匀地喷洒于预处理秸秆的酶载量为5
‑
25fpu/g秸秆。
19.进一步的,发酵上清液中残留有聚合度>2的可溶性纤维寡糖和木寡糖,作为真菌纤维素酶生产的诱导剂。
20.进一步的,所述产油酵母为可以直接利用葡萄糖、木糖及可溶性寡糖的产油酵母。
21.进一步的,所述秸秆为玉米秸秆、小麦秸秆、稻草、棉花秸秆或油菜秸秆。
22.本发明的有益效果是:
23.1、本发明以纤维素酶液喷洒至秸秆上的方式进行连续流加补料至酶解反应器,实现了最终固液比超过50%,实现了高固相酶水解,最终得到的高浓度糖液的糖浓度达到300g/l以上。
24.2、通过简单两次定量洗涤酶解残渣,实现中浓度和低浓度糖液的定向制备,显著降低了固液分离过程对过滤/离心设备性能的要求,同时避免了酶解残渣中因吸附残留无法收集的糖损失,显著降低了糖液的分离成本,几乎完全回收了水解的碳水化合物。
25.3、高固相酶水解产生的糖液中,会不可避免地产生约占总糖10~20%左右的可溶性寡糖,补料批式发酵结束后,培养基中聚合度较高的可溶性寡糖未被利用,这些寡糖可以作为优良的诱导剂,诱导产酶真菌生产大量的纤维素酶,从而实现纤维素酶的自产自用,显著降低酶成本。
26.4、本发明通过补料批式发酵耦合纤维素酶的生产,可以实现对水解液中碳水化合物的高效彻底利用,其中的单糖和二糖可以被产油酵母代谢并转化为微生物油脂,更高聚合度的可溶性寡糖可作为诱导剂,诱导真菌大量生产纤维素酶,最终实现了对水解液中碳水化合物的充分利用。显著降低了成本,显著提升了秸秆制微生物油脂的技术经济性。
附图说明
27.图1是本发明提供的利用秸秆资源制备微生物油脂的方法的流程图。
具体实施方式
28.为了使本发明的目的、技术方案及优点更加清楚明白,以下结合附图及实施例,对本发明进行进一步详细说明。应当理解,此处所描述的具体实施例仅仅用以解释本发明,并不用于限定本发明。
29.为了说明本发明所述的技术方案,下面通过具体实施例来进行说明。
30.如图1示出了本发明提供的利用秸秆资源制备微生物油脂的方法的流程,包括下述步骤:
31.步骤s1、预处理秸秆。
32.将秸秆自然干燥,机械粉碎至直径低于5mm,选择与后续油脂发酵相契合的预处理方法,包括物理、化学、物理化学等方法,如蒸汽爆破、氨纤维爆破、有机溶剂预处理、甘油预处理、深共晶溶剂预处理等处理秸秆,具体预处理过程,本步骤不赘述。预处理结束后,固液分离收集秸秆。本发明的秸秆资源包括玉米秸秆、小麦秸秆、稻草、棉花秸秆、油菜秸秆等,其主要成分为纤维素、半纤维素和木质素。
33.步骤s2、取一定量预处理秸秆置入酶解反应器中并加入纤维素酶,调整初始固液比启动酶水解,将纤维素酶液均匀地喷洒于预处理的秸秆中并充分混合得到含酶秸秆,然后采用流加补料的方式,以一定速率持续地将含酶秸秆补加至酶解反应器中,至固液比达到目标值,酶水解一段时间后结束。
34.本步骤直接将纤维素酶液均匀地喷洒于预处理的秸秆上,而常规方法是,直接在酶解反应器中添加预处理秸秆和纤维素酶。本发明喷洒方式,可以使得高浓度的纤维素酶液与秸秆预混合,可以充分接触,有利于提高在酶解反应器中的酶解效率。纤维素酶为木霉、青霉、曲霉等产纤维素酶真菌生成。纤维素酶载酶量为5~25fpu/g秸秆。
35.首先调整酶解反应器的初始固液比为5~10%w/v启动秸秆酶水解,这里w/v为质量体积比,酶解温度为50℃,ph为4.8,水解3h后,采用低剂量连续流加方式,以5~6.5g/l/h的速率补加均匀喷洒了纤维素酶的秸秆原料,同时稳定ph控制在4.8左右,直至酶解体系固液比达到目标值(目标值为50%w/v),酶水解96~144h后结束。
36.本步骤目的是制备出高浓度糖液,采用高固相酶解,发酵过程采用补料的方式来实现高密度发酵。为尽可能地控制补料过程中发酵液的体积,对补料液的糖浓度的要求也相对较高。常规的脉冲式补料批式法并不利于酶水解的进行,本发明采用小剂量而持续地补料可以缓解酶解体系的负荷压力,且使酶与底物的接触更为充分,能有效提高酶解效果。
37.步骤s3、酶水解结束后进行固液分离,得到高浓度糖液和酶解残渣,将酶解残渣进行两次定量水洗涤,具体的,第一次定量水洗涤固液分离收集到的洗涤水为中浓度糖液,收
curvatus、斯达氏油脂酵母lipomyces starkeyi、皮状丝孢酵母trichosporon cutaneum、发酵性丝孢酵母trichosporon fermentans、圆红冬孢酵母rhodosporidium toruloides、解脂耶氏酵母yarrowia lipolytica等。本发明中的产纤维素酶的真菌包括木霉trichoderma.sp、青霉penicillium.sp、曲霉aspergillus.sp等。
50.将种子液接种至发酵培养基中培养,同时监测发酵培养基中还原糖含量,当浓度低于10g/l时,将含高浓度糖液补料至发酵罐中至浓度达到25~70g/l。补料3~8次后,当可发酵性糖被消耗殆尽时终止发酵。
51.步骤s5、发酵结束后固液分离,菌体用于提取微生物油脂,调整发酵上清液的糖浓度至5~15g/l,添加适量营养物质后作为产酶培养基,接种产酶真菌培养,收获的纤维素酶。
52.发酵结束后离心收集菌体,使用有机溶剂浸提产油酵母胞内油脂,提取的微生物油脂可用于制备油脂化学品,也可作为生物柴油的制备原料。
53.补料批式发酵结束时,发酵液中聚合度较高的可溶性寡糖没有被代谢而残留在发酵上清液中,因此发酵上清液中必然会残留有聚合度>2的可溶性纤维寡糖和木寡糖,可以作为真菌纤维素酶生产的诱导剂,用于培养产酶真菌。本发明将发酵上清液中寡糖浓度调整至5~15g/l,添加适量营养成分后作为产酶培养基,接种一定量的产酶真菌至发酵罐中进行补料批式发酵产纤维素酶,发酵5~10天结束发酵,发酵结束后固液分离,收集上清液适当浓缩后,收获纤维素酶粗酶液。进一步可提纯至商品酶。
54.本发明中,上述步骤s2采用的纤维素酶可以为商品酶,优选的,可以直接使用本发明得到的粗酶液,粗酶液用于高固液比酶水解,实现纤维素酶的自产自用。
55.本发明高固液比酶解制备高浓度糖液的过程,由于酶解固液比过高,残渣量大,酶解体系粘度较大,因而产品的分离过程成本较高一直是一个亟待解决的问题。通过简单的定量洗涤方法,可获得补料批式发酵所需的种子培养基、发酵培养基和补料培养基。这种方法对滤饼的含水率要求不必太过苛刻,因此对高固酶解后的固液分离过程的设备要求大大降低,可以显著降低糖液的分离成本,几乎完全回收水解的碳水化合物。
56.高固液比酶水解不可避免地产生部分可溶性的寡糖。本发明通过补料批式发酵耦合纤维素酶的生产,可以实现对水解液中碳水化合物的高效彻底利用,其中的单糖和二糖被产油酵母转化为微生物油脂,而大部分聚合度>2的水溶性寡糖作为诱导剂,诱发产酶真菌生产纤维素酶,用于高固液比酶水解。
57.下面通过具体实施例来对本发明进行说明,以下实施例选取了典型的秸秆材料培养典型产油微生物的例子,有助于了解本发明,但不以任何形式限制将本发明应用于其他材料或产油菌株。
58.实施例1:
59.1)玉米秸秆的预处理:参照文献(yuan,w.,et al.bioresour technol,2018,265:464
–
470),将1kg naoh加入20l甲醇中,充分溶解后加入10kg过2mm筛的玉米秸秆,充分混合均匀,于80℃处理60min,预处理秸秆按1:5的比例用甲醇洗涤3次后,原位蒸发回收甲醇,秸秆储存备用。
60.2)50%(w/v)固液比玉米秸秆水解液的制备:取1kg预处理玉米秸秆加入反应器中,充分混合,按15fpu/g加入纤维素酶,调节ph至4.8,并补加水至总体系为10l,在50℃下
开始进行酶解。在秸秆储罐中,将待补加秸秆原料按15fpu/g的载酶量均匀地喷洒上纤维素酶液,水解第3h开始连续补料,补料速率5g/l/h,并维持ph在4.8,酶解144h结束。
61.3)水解液定向收集:水解液压滤收集上清液并记录体积8.2l,还原糖浓度316.2g/l。加入3.1l水混合均匀后再次离心并收集上清液。此时的上清液为还原糖浓度为70g/l的中浓度糖液,同理再洗定量洗涤制备出糖浓度为20g/l的低浓度糖液。
62.4)批次补料发酵:取低浓度糖液(20g/l)0.3l,加入5g/l玉米浆,将ph调节至6.0,121℃下灭菌20min。挑取一环弯曲隐球酵母cryptococcus curvatus atcc 20509接入种子培养基,30℃,200rpm振荡培养24h,得到种子液;取中浓度糖液(70g/l)2.7l,加入10g/l酵母粉及10g/l蛋白胨,装入发酵罐并于121℃下灭菌20min,冷却备用;向发酵培养基中接入0.3l种子液,于30℃,200rpm振荡培养。当还原糖浓度低于10g/l时,补加水解液至发酵液中还原糖浓度为70g/l左右。补料3次后结束发酵,离心收集菌体,最终获得菌体浓度为70.7g/l,采用酸热法提取油脂,油脂浓度为41.3g/l,油脂含量为58.4%。
63.5)纤维素酶的制备:离心收集3)中的发酵上清液,并补加10g/l乳糖,5g/l玉米浆,3g/l(nh4)so4,1g/l mgso4·
7h2o,6g/l kh2po4,0.5g/l cacl2,按10%的接种量接入里氏木霉trichoderma reesei rut
‑
c30,采用补料批式发酵,周期性地补加培养液,6天后离心收集上清液作为粗酶液,测定其纤维素酶的滤纸酶活为47.7fpu/ml。
64.实施例2:
65.1)小麦秸秆的预处理:参照文献(krishnan c,et al.biotechnol bioeng.2010,107:441
–
450),以粉碎过5mm筛的小麦秸秆为原料,加水成150%(w/w)的固液比,按2:1(w/w)混合氨水和小麦秸秆,140℃氨膨胀处理30min,冷却至50℃备用。
66.2)50%(w/v)固液比小麦秸秆水解液的制备:取0.5kg小麦秸秆,加入0.16l实施例1中收集的粗酶液,加入适量水充分混合,调节ph至4.8,并补加水至总体系为10l,于50℃下开始进行酶解。在秸秆储罐中,将待补加秸秆原料按20fpu/g的载酶量均匀地喷洒上纤维素酶液,水解第3h后按照补料速率6.5g/l/h持续补加含酶秸秆原料,直至固液比达到50%,酶解120h结束。
67.3)水解液定向收集:通过压滤收集上清液,获得还原糖浓度为315g/l的水解液8.8l。通过定量洗涤2次,最终分别得到2.7l糖浓度为100g/l的中浓度糖液及3.5l糖浓度为15g/l的低浓度糖液。
68.4)水解液批次补料发酵:取低浓度糖液(15g/l)0.4l,加入5g/l酵母粉及5g/l蛋白胨,将ph调节至6.0,121℃下灭菌20min。冷却后挑取一环已活化的斯达氏油脂酵母lipomyces starkeyi as 2.1560,接入培养基,30℃,200rpm振荡培养40h,得到种子液;取中浓度糖液3.6l(100g/l),加入25g/l酵母粉及25g/l蛋白胨,在发酵罐中并于121℃下灭菌,冷却备用;向发酵培养基中接入0.4l种子液,于30℃,200rpm振荡培养。当还原糖浓度低于10g/l时,用高浓度糖液进行补料至发酵液中还原糖浓度为50g/l左右。补料7次后结束发酵,离心收集菌体,最终获得菌体浓度为102.8g/l,采用酸热法提取油脂,油脂浓度为62.7g/l,油脂含量为61.0%。
69.5)纤维素酶的制备:离心收集上清液,将寡糖浓度调整至10g/l,并补加10g/l乳糖,5g/l玉米浆,3g/l(nh4)so4,1g/l mgso4·
7h2o,6g/l kh2po4,0.5g/l cacl2,按10%的接种量接入绿色木霉trichoderma viride qm9414,采用补料批式发酵,周期性地补加培养
基,培养7天后,离心收集上清作为粗酶液,测定其纤维素酶的滤纸酶活为71fpu/ml。
70.实施例3:
71.1)稻草秸秆的预处理:参照文献(varga e,et al.appl biochem biotechnol,2004,113,509
–
523)的气爆方法,称取10kg过40目筛的稻草秸秆,进行气爆预处理。
72.2)50%(w/v)固液比稻草秸秆水解液的制备:取0.5kg秸秆,加入0.1l实施例2中收集的的粗酶液,加入适量水充分混合,调节ph至4.8,并补加水至总体系为10l,于50℃下开始进行酶解。在秸秆储罐中,将待补加秸秆原料按20fpu/g的载酶量均匀地喷洒上纤维素酶液,水解第3h后按照补料速率6.5g/l/h持续补加含酶秸秆原料,直至固液比达到50%,酶解120h结束。
73.3)水解液定向收集:通过离心收集上清液,获得还原糖浓度为315g/l的水解液9.5l。通过定量洗涤2次,分别得到4.2l糖浓度为100g/l的中浓度糖液及2.5l糖浓度为15g/l的低浓度糖液。
74.4)水解液批次补料发酵:取低浓度糖液(15g/l)0.4l,加入5g/l酵母粉及10g/l蛋白胨,将ph调节至6.0,121℃下灭菌20min。挑取一环弯曲隐球酵母cryptococcus curvatus atcc 20509,接入培养基,30℃,200rpm振荡培养24h,得到种子液;取中浓度糖液3.6l(100g/l),加入25g/l酵母粉及25g/l蛋白胨,在发酵罐中并于121℃下灭菌,冷却备用;向发酵培养基中接入0.4l种子液,于30℃,200rpm振荡培养。当还原糖浓度低于10g/l时,用高浓度糖液进行补料至发酵液中还原糖浓度为50g/l左右。补料8次后结束发酵,离心收集菌体,最终获得菌体浓度为117.2g/l,采用酸热法提取油脂,油脂浓度为79.7g/l,油脂含量为68.0%。
75.5)纤维素酶的制备:离心收集上清,将寡糖浓度调整至15g/l,并补加5g/l乳糖,5g/l玉米浆,5g/l(nh4)so4,0.5g/l mgso4·
7h2o,2.7g/l kh2po4,0.5g/l cacl2,2g/l tween 80,按10%的接种量接入黑曲霉aspergillus niger atcc 16888,采用补料批式发酵,周期性地补加培养基,培养5天后,离心收集上清作为粗酶液,测定其纤维素酶的滤纸酶活为32fpu/ml。
76.实施例4:
77.1)玉米秸秆的预处理:参照文献(zhang j,et al.bioresour technol,2011,102:4480
–
4488),以玉米秸秆为原料,干燥,粉碎过40目筛,并用2.5%的硫酸浸渍18h,190℃蒸汽处理3min后立刻泄压,待用。
78.2)50%(w/v)固液比玉米秸秆水解液的制备:取1kg秸秆于反应皿中,加入0.2l实施例2收集的粗酶液,加入适量水充分混合,调节ph至4.8,并补加水至总体系为10l,于50℃下开始进行酶解。在秸秆储罐中,将待补加秸秆原料按20fpu/g的载酶量均匀地喷洒上纤维素酶液,水解第3h后按照补料速率6.0g/l/h持续补加含酶秸秆原料,直至固液比达到50%,酶解132h结束。
79.3)收集水解液:通过压滤收集上清液,获得还原糖浓度为315g/l的水解液9.2l。通过稀释最终分别得到4.5l浓度为100g/l的水解液及2.7l浓度为20g/l的水解液。
80.4)批次补料发酵:取20g/l水解液0.5l,加入3g/l酵母粉及3g/l蛋白胨,将ph调节至5.5,121℃下灭菌20min。挑取一环解脂耶氏酵母yarrowia lipolytica po1g,接入培养基,30℃,200rpm振荡培养24h,得到种子液;取中浓度糖液4.5l(100g/l),加入20g/l酵母粉
及20g/l玉米浆,在发酵罐中并于121℃下灭菌,冷却备用;向发酵培养基中接入0.5l种子液,于30℃,200rpm振荡培养。当还原糖浓度低于10g/l时,用高浓度糖液进行补料至发酵液中还原糖浓度为70g/l左右。补料5次后结束发酵,离心收集菌体,最终获得菌体浓度为92.7g/l,采用酸热法提取油脂,油脂浓度为55.1g/l,油脂含量为59.4%。
81.5)纤维素酶的制备:离心收集上清,将寡糖浓度调整至8g/l,并补加12g/l乳糖,10g/l玉米浆,2g/l(nh4)so4,1g/l mgso4·
7h2o,6g/l kh2po4,0.5g/l cacl2,1g/l tween 80,按10%的接种量接入黑曲霉a.niger cctcc af 91005,采用补料批式发酵,周期性地补加培养基,培养10天后,离心收集上清作为粗酶液,测定其纤维素酶的滤纸酶活为55.9fpu/ml。
82.实施例5:
83.1)高粱秸秆的预处理:以高粱秸秆为原料,干燥,粉碎过1mm筛,参照文献(ai bl,et al.green chem,2020,22:6372
–
6383)的方法,采用氯化胆碱/甘油深共晶溶剂预处理,固液比30%(w/w),处理温度180℃,停留时间5min,处理结束后,水洗2遍,待用。
84.2)50%(w/v)固液比高粱秸秆水解液的制备:取0.8kg秸秆于反应皿中,加入0.2l实施例2收集的粗酶液,加入适量水充分混合,调节ph至4.8,并补加水至总体系为10l,于50℃下开始进行酶解。在秸秆储罐中,将待补加秸秆原料按20fpu/g的载酶量均匀地喷洒上纤维素酶液,水解第3h后按照补料速率5.5g/l/h持续补加含酶秸秆原料,直至固液比达到50%,酶解144h结束。
85.3)收集水解液:通过压滤收集上清液,获得还原糖浓度为324g/l的水解液9.5l。通过定量洗涤2次,最终分别得到4.7l糖浓度为80g/l的中浓度糖液及3.1l糖浓度为25g/l的低浓度糖液。
86.4)水解液批次补料发酵:取低浓度糖液(25g/l)0.5l,加入10g/l玉米浆,将ph调节至6.0,121℃下灭菌20min。冷却后挑取一环已活化的皮状丝孢酵母trichosporon cutaneum gim 2.67,接入培养基,30℃,200rpm振荡培养40h,得到种子液;取中浓度糖液3.6l(100g/l),加入25g/l酵母粉及25g/l蛋白胨,在发酵罐中并于121℃下灭菌,冷却备用;向发酵培养基中接入0.4l种子液,于30℃,200rpm振荡培养。当还原糖浓度低于5g/l时,用高浓度糖液进行补料至发酵液中还原糖浓度为50g/l左右。补料8次后结束发酵,离心收集菌体,最终获得菌体浓度为117.8g/l,采用酸热法提取油脂,油脂浓度为67.7g/l,油脂含量为57.5%。
87.5)纤维素酶的制备:离心收集上清液,将寡糖浓度调整至10g/l,并补加10g/l乳糖,5g/l玉米浆,3g/l(nh4)so4,1g/l mgso4·
7h2o,6g/l kh2po4,0.5g/l cacl2,按10%的接种量接入绿色木霉t.viride cctcc af 93252,采用补料批式发酵,周期性地补加培养基,培养6天后,离心收集上清作为粗酶液,测定其纤维素酶的滤纸酶活为51.2fpu/ml。
88.实施例6:
89.1)棉花秸秆的预处理:参照文献(perez ja,et al.fuel,2008,87:3640
–
3647)的优化方法,称取50g过2mm筛的棉花秸秆,进行高温水热预处理,固相干燥至含水量低于20%(w/w),待用。
90.2)50%(w/v)固液比棉花秸秆水解液的制备:取1.0kg秸秆于反应器中,加入0.2l实施例2中收集的的粗酶液,加入适量水充分混合,调节ph至4.8,并补加水至总体系为10l,
于50℃下开始进行酶解。在秸秆储罐中,将待补加秸秆原料按20fpu/g的载酶量均匀地喷洒上纤维素酶液,水解第3h后按照补料速率65.0g/l/h持续补加含酶秸秆原料,直至固液比达到50%,酶解144h结束。
91.3)收集水解液:通过离心收集上清液,获得还原糖浓度为319.2g/l的水解液9.6l。通过稀释最终分别得到5.4l糖浓度为50g/l的中浓度糖液及3.1l糖浓度为25g/l的低浓度糖液。
92.4)水解液批次补料发酵:取25g/l水解液0.5l,加入10g/l酵母粉及10g/l蛋白胨,将ph调节至5.5,121℃下灭菌20min。挑取一环白色隐球酵母cryptococcus albidus atcc 56298,接入培养基,25℃,200rpm振荡培养24h,得到种子液;取中浓度糖液4.5l(50g/l),加入25g/l酵母粉及25g/l蛋白胨,在发酵罐中并于121℃下灭菌,冷却备用;向发酵培养基中接入0.5l种子液,于25℃,200rpm振荡培养。当还原糖浓度低于10g/l时,用高浓度糖液进行补料至发酵液中还原糖浓度为50g/l左右。补料8次后结束发酵,离心收集菌体,最终获得菌体浓度为104.2g/l,采用酸热法提取油脂,油脂浓度为55.8g/l,油脂含量为53.6%。
93.5)纤维素酶的制备:离心收集上清,将寡糖浓度调整至10g/l,并补加10g/l羧甲基纤维素,5g/l玉米浆,5g/l(nh4)so4,0.5g/l mgso4·
7h2o,2.7g/l kh2po4,0.5g/l cacl2,2g/l tween 80,按5%的接种量接入草酸青霉penicillium oxalicum cgmcc 3.15651,采用补料批式发酵,周期性地补加培养基,培养8天后,离心收集上清作为粗酶液,测定其纤维素酶的滤纸酶活为52.5fpu/ml。
94.实施例7:
95.1)小麦秸秆的预处理:称取5kg过2mm筛的棉花秸秆,参考文献(sun fb,et al.bioresour technol,2008,99:5474
–
5479)的方法,粗甘油预处理,固液比5%(w/w),处理温度220℃,时间为3h。处理完毕后,水洗2遍,固相干燥至含水量低于20%(w/w),待用。
96.2)50%(w/v)固液比小麦秸秆水解液的制备:取0.5kg秸秆于反应皿中,加入0.2l实施例2中收集的的粗酶液,加入适量水充分混合,调节ph至4.8,并补加水至总体系为10l,于50℃下开始进行酶解。在秸秆储罐中,将待补加秸秆原料按20fpu/g的载酶量均匀地喷洒上纤维素酶液,水解第3h后按照补料速率6.5g/l/h持续补加含酶秸秆原料,直至固液比达到50%,酶解120h结束。
97.3)收集水解液:通过压滤收集上清液,获得还原糖浓度为328.3g/l的水解液9.1l。通过稀释最终分别得到5.2l糖浓度为80g/l的中浓度糖液及3.1l糖浓度为25g/l的低浓度糖液。
98.4)水解液批次补料发酵:取低浓度糖液(25g/l)0.5l,加入5g/l酵母粉及5g/l蛋白胨,将ph调节至6.0,121℃下灭菌20min。挑取一环发酵性丝孢酵母trichosporon fermentans cicc 1368,接入培养基,30℃,200rpm振荡培养20h,得到种子液;取中浓度糖液4.5l(80g/l),加入10g/l酵母粉及10g/l玉米浆,在发酵罐中并于121℃下灭菌,冷却备用;向发酵培养基中接入0.5l种子液,于30℃,200rpm振荡培养。当还原糖浓度低于5g/l时,用高浓度糖液进行补料至发酵液中还原糖浓度为25g/l左右。补料8次后结束发酵,离心收集菌体,最终获得菌体浓度为49.1g/l,采用酸热法提取油脂,油脂浓度为25.3g/l,油脂含量为51.5%。
99.5)纤维素酶的制备:离心收集上清,将寡糖浓度调整至5g/l,并补加15g/l纤维素,
5g/l玉米浆,3g/l(nh4)so4,1g/l mgso4·
7h2o,6g/l kh2po4,0.5g/l cacl2,2g/l tween 80,按10%的接种量接入里氏木霉t.reesei cgmcc3.5218,采用补料批式发酵,周期性地补加培养基,培养7天后,离心收集上清作为粗酶液,测定其纤维素酶的滤纸酶活为35.7fpu/ml。
100.实施例8:
101.1)小麦秸秆的预处理:向反应皿中加入1.2l例1中洗涤回收的甲醇,加入0.6kg过40目筛小麦秸秆,充分混合均匀后密封后于80℃下反应60min。用甲醇洗涤三次后蒸发甲醇并回收,秸秆储存备用。
102.2)50%(w/v)固液比小麦秸秆水解液的制备:取0.5kg秸秆于反应器中,加入0.47l实施例1中收集的粗酶液,加入适量水充分混合,调节ph至4.8,并补加水至总体系为10l,于50℃下开始进行酶解。在秸秆储罐中,将待补加秸秆原料按20fpu/g的载酶量均匀地喷洒上纤维素酶液,水解第3h后按照补料速率6.5g/l/h持续补加含酶秸秆原料,直至固液比达到50%,酶解120h结束。
103.3)收集水解液:通过压滤收集上清液,获得还原糖浓度为319g/l的水解液9.8l。通过稀释最终分别得到4.8l糖浓度为60g/l的中浓度糖液及3.5l糖浓度为20g/l的低浓度糖液。
104.4)水解液批次补料发酵:取低浓度糖液(20g/l)0.4l,加入10g/l玉米浆,将ph调节至5.5,121℃下灭菌20min。挑取一环圆红冬孢酵母rhodosporidium toruloides as 2.1389,接入培养基,30℃,200rpm振荡培养24h,得到种子液;取中浓度糖液3.6l(60g/l),加入20g/l酵母粉及20g/l玉米浆,在发酵罐中并于121℃下灭菌,冷却备用;向发酵培养基中接入0.4l种子液,于30℃,200rpm振荡培养。当还原糖浓度低于10g/l时,用高浓度糖液进行补料至发酵液中还原糖浓度为40g/l左右。补料7次后结束发酵,离心收集菌体,最终获得菌体浓度为87.5g/l,采用酸热法提取油脂,油脂浓度为53.2g/l,油脂含量为60.8%。
105.5)纤维素酶的制备:离心收集上清,将寡糖浓度调整至5g/l,并补加5g/l纤维二糖,3g/l玉米浆,2g/l(nh4)so4,0.5g/l mgso4·
7h2o,1g/l kh2po4,0.5g/l cacl2,1g/l tween 80,按10%的接种量接入里氏木霉t.reesei rut
‑
c30,采用补料批式发酵,周期性地补加培养基,培养6天后,离心收集上清作为粗酶液,测定其纤维素酶的滤纸酶活为40.2fpu/ml。
106.从上述实施例可知,本发明通过小剂量且持续地补料可以缓解酶解体系的负荷压力,且使酶与底物的接触更为充分,能有效提高酶解效果,得到的糖浓度大于300g/l的高浓度糖液。并且通过定量计算,可从酶解残渣中获得的指定浓度和体积的中浓度糖液和低浓度糖液,高、中、低糖浓度糖液的浓度和体积可根据发酵的实际需求进行灵活调配。可以将制备出的三种浓度糖液在补料批式发酵中组合利用,实现了水解液制备与补料批式发酵完美契合。本发明方法能够彻底高效利用秸秆高固液比酶水解的碳水化合物生产微生物油脂和纤维素酶,提高油脂产量和得率,显著降低成本。
107.综上,本发明以高浓度糖液的制备为核心,设计出一条将秸秆资源系统地进行生物转化的方法,包括持续流加补料对预处理秸秆进行高固相酶水解,使最终水解液糖浓度达到300g/l以上;结合定量水洗,实现中浓度和低浓度糖液的定向制备,降低了工艺过程中对过滤设备性能的要求,解决了由于吸附作用等残留在酶解残渣中高浓度糖导致的糖损
失;通过这种方法制备出的糖液,浓度和体积可根据发酵的实际需求进行灵活地调配,实现高、中、低三种浓度糖液与补料批式发酵相契合,在补料批式油脂发酵中实现组合利用;此外,高固相酶水解会产生约占总糖质量10~20%左右的可溶性寡糖,补料批式发酵结束后,发酵液中低聚合度的寡糖会被菌株消耗,但会残留一定量聚合度较高的可溶性寡糖,这些寡糖可以作为强诱导剂,诱导产酶真菌生产大量的纤维素酶用于高固液比酶水解,从而实现纤维素酶的自产自用,显著降低酶成本。
108.以上所述仅为本发明的较佳实施例而已,并不用以限制本发明,凡在本发明的精神和原则之内所作的任何修改、等同替换和改进等,均应包含在本发明的保护范围之内。