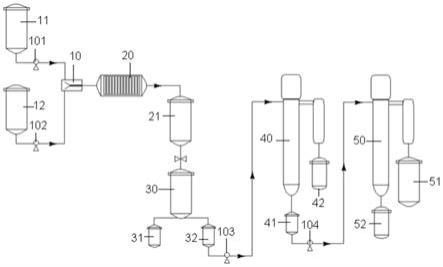
1.本发明涉及有机合成领域,具体而言,涉及一种通过微反应器合成氧杂环丁烷衍生物的合成方法。
背景技术:2.以3
‑
乙基
‑3‑
羟甲基氧杂环丁烷为原料,与卤代有机化合物在碱作用下进行醚化反应可得到一系列的氧杂环丁烷衍生物,可作为光固化阳离子体系中的单体,应用于光固化油墨、涂料、胶黏剂等领域,代表性的产品有3
‑
乙基
‑3‑
[(环氧乙烷基
‑2‑
甲氧基)甲基]氧杂环丁烷、双[1
‑
乙基(3
‑
氧杂环丁基)甲基]醚和3
‑
苄氧甲基
‑3‑
乙基氧杂环丁烷。这些氧杂环丁烷产品由于粘度低、稀释性佳、交联速度快、成膜后性能优异,成为阳离子光固化领域最具市场潜力的原材料之一。
[0003]
以3
‑
乙基
‑3‑
[(环氧乙烷基
‑2‑
甲氧基)甲基]氧杂环丁烷为例,其工业生产是以3
‑
乙基
‑3‑
羟甲基氧杂环丁烷和环氧氯丙烷为原料,在固体氢氧化钠作用下进行醚化反应制得,由于反应体系为液
‑
固非均相,传质较困难,为了保证转化率,环氧氯丙烷和氢氧化钠需要过量50%以上,以2m3反应釜生产,反应过程约12h,后处理包括过滤、精馏等工序需要约30h,生产过程中分批投加固体氢氧化钠操作繁琐且存在飞温等安全隐患。
[0004]
鉴于上述问题的存在,有必要提供一种反应时间短、传质效率高、安全性好的氧杂环丁烷衍生物的合成方法。
技术实现要素:[0005]
本发明的主要目的在于提供一种通过微反应器合成氧杂环丁烷衍生物的合成方法,以解决现有的氧杂环丁烷衍生物的合成方法中存在的反应时间长、操作繁琐及安全性差的问题。在实现连续化生产的同时确保了醚化反应的选择性,提高产物收率。
[0006]
为了实现上述目的,本发明提供了一种通过微反应器合成氧杂环丁烷衍生物的合成方法,氧杂环丁烷衍生物具有式(ⅰ)所示的结构:
[0007][0008]
其中,r为c2~c
12
的直链或支链烷基、含有环氧乙烷结构的烷基、含有氧杂环丁烷结构的烷基、苯基、甲苯基、苯甲基或联苯基,n为1
‑
4;上述通过微反应器合成氧杂环丁烷衍生物的合成方法包括:将3
‑
乙基
‑3‑
羟甲基氧杂环丁烷、原料ha、催化剂、碱输送至微反应器中进行醚化反应,得到醚化产物体系,原料ha的通式为r
‑
(x)
n
,x为卤素;及将醚化产物体系进行分离,得到氧杂环丁烷衍生物。
[0009]
进一步地,微反应器的反应通道内径为200~10000μm。
[0010]
进一步地,碱为碱金属化合物或碱金属化合物的水溶液,碱金属化合物选自氢氧
化锂、氢氧化钠、氢氧化钾和氢氧化钙组成的组中的一种或多种;优选地,碱金属化合物为氢氧化钠;碱金属化合物的水溶液的浓度为10%~20%;催化剂选自聚醚类、环状聚醚类和季胺盐类组成的组中的一种或多种。
[0011]
进一步地,催化剂选自聚乙二醇、聚乙二醇烷基醚、18
‑
冠
‑
6、15
‑
冠
‑
5、四乙基溴化铵、四丁基溴化铵、四丁基氯化铵、三辛基甲基氯化铵、十二烷基三甲基氯化铵和十四烷基三甲基氯化铵组成的组中的一种或多种。
[0012]
进一步地,催化剂选自聚乙二醇二甲醚、18
‑
冠
‑
6和四丁基溴化铵组成的组中的一种或多种。
[0013]
进一步地,以占3
‑
乙基
‑3‑
羟甲基氧杂环丁烷重量的重量百分含量计,催化剂添加量为0.1~5%。
[0014]
进一步地,以占3
‑
乙基
‑3‑
羟甲基氧杂环丁烷重量的重量百分含量计,催化剂添加量为0.5~2%。
[0015]
进一步地,醚化反应的反应温度为10~60℃,物料停留时间为2~5min。
[0016]
进一步地,分离的步骤采用的装置包括:二级薄膜蒸发装置或精馏塔。
[0017]
进一步地,微反应器的反应通道内径为500~8000μm。
[0018]
应用本发明的技术方案,相对于常规反应器,微反应器具有传热传质系数高,混合性能好,温度容易控制和过程安全可控等优点。利用微反应器的优势制备氧杂环丁烷衍生物,可大幅提高反应体系传质传热性,减少反应时间提高生产效率,提高了产品收率,并实现过程的连续化、自动化,提高过程安全性。将微反应器的反应通道的孔径限定在上述范围内有利于提高醚化反应的选择性,从而有利于提高氧杂环丁烷衍生物的转化率。此外,上述合成过程所需的反应装置体积小,生产场地占用面积小,所需人力资源少,安全性高。
附图说明
[0019]
构成本技术的一部分的说明书附图用来提供对本发明的进一步理解,本发明的示意性实施例及其说明用于解释本发明,并不构成对本发明的不当限定。在附图中:
[0020]
图1示出了根据本发明的一种典型的实施方式提供的氧杂环丁烷衍生物的制备装置的结构示意图。
[0021]
其中,上述附图包括以下附图标记:
[0022]
10、微混合器;11、有机物原料储罐;12、碱溶液储罐;20、微反应器;21、缓冲罐;30、分相罐;31、废水储罐;32、有机相储罐;40、一级薄膜蒸发器;41、粗产品储罐;42、回收原料储罐;50、二级薄膜蒸发器;51、成品储罐;52、重沸物储罐;
[0023]
101、有机物原料进料泵;102、原料进料泵;103、一级薄膜蒸发器进料泵;104、二级薄膜蒸发器进料泵。
具体实施方式
[0024]
需要说明的是,在不冲突的情况下,本技术中的实施例及实施例中的特征可以相互组合。下面将结合实施例来详细说明本发明。
[0025]
正如背景技术所描述的,现有的氧杂环丁烷衍生物的合成方法中存在的反应时间长、操作繁琐及安全性差的问题。为了解决上述技术问题,本技术提供了一种通过微反应器
合成氧杂环丁烷衍生物的合成方法,氧杂环丁烷衍生物具有式(ⅰ)所示的结构:
[0026][0027]
其中,r为c2~c
12
的直链或支链烷基、含有环氧乙烷结构的烷基、含有氧杂环丁烷结构的烷基、苯基、甲苯基、苯甲基或联苯基,n为1
‑
4;该氧杂环丁烷衍生物的合成方法包括:将3
‑
乙基
‑3‑
羟甲基氧杂环丁烷、原料ha、催化剂、碱输送至微反应器中进行醚化反应,得到醚化产物体系,原料ha的通式为r
‑
(x)
n
,其中x为卤素;及将醚化产物体系进行分离,得到氧杂环丁烷衍生物。
[0028]
相对于常规反应器,微反应器具有传热传质系数高,混合性能好,温度容易控制和过程安全可控等优点。利用微反应器的优势制备氧杂环丁烷衍生物,可大幅提高反应体系传质传热性,减少反应时间提高生产效率,提高了产品收率,并实现过程的连续化、自动化,提高过程安全性。此外,上述合成过程所需的反应装置体积小,生产场地占用面积小,所需人力资源少,安全性高。
[0029]
优选地,微反应器的反应通道内径为200~10000μm。将微反应器的反应通道的孔径限定在上述范围内有利于进一步提高醚化反应的选择性,并进一步提高氧杂环丁烷衍生物的转化率。比如微反应器的反应通道内径为200μm、500μm、4000μm、6000μm、8000μm、10000μm,更优选地,微反应器的反应通道内径为500~8000μm。
[0030]
上述合成方法中碱为碱金属化合物或碱金属化合物的水溶液。碱金属化合物可以选用本领域常用的种类。优选地,碱金属化合物包括但不限于氢氧化锂、氢氧化钠、氢氧化钾和氢氧化钙组成的组中的一种或多种;更优选地,碱金属化合物为氢氧化钠;碱金属化合物的水溶液的浓度为10~20%。
[0031]
上述合成方法中催化剂可以采用本领域常用的种类,催化剂包括但不限于聚醚类、环状聚醚类和季胺盐类组成的组中的一种或多种。优选地,催化剂包括但不限于聚乙二醇、聚乙二醇烷基醚、18
‑
冠
‑
6、15
‑
冠
‑
5、四乙基溴化铵、四丁基溴化铵、四丁基氯化铵、三辛基甲基氯化铵、十二烷基三甲基氯化铵和十四烷基三甲基氯化铵组成的组中的一种或多种。相比于其它催化剂,采用上述几种催化剂有利于进一步提高醚化反应的反应速率,缩短反应周期。更优选地,催化剂包括但不限于聚乙二醇二甲醚、18
‑
冠
‑
6和四丁基溴化铵组成的组中的一种或多种。
[0032]
在一种优选的实施例中,以占3
‑
乙基
‑3‑
羟甲基氧杂环丁烷重量的重量百分含量计,催化剂添加量为0.1~5%。催化剂的用量包括但不限于上述范围,而将其限定在上述范围内有利于进一步提高醚化反应的反应速率。比如以占3
‑
乙基
‑3‑
羟甲基氧杂环丁烷重量的重量百分含量计,催化剂添加量可以为0.1%、0.5%、1%、1.5%、2%、3%、4%。更优选地,以占3
‑
乙基
‑3‑
羟甲基氧杂环丁烷重量的重量百分含量计,催化剂添加量为0.5~2%。
[0033]
在一种优选的实施例中,3
‑
乙基
‑3‑
羟甲基氧杂环丁烷和原料ha中卤素的摩尔比为1:(1.0~1.2)。3
‑
乙基
‑3‑
羟甲基氧杂环丁烷和原料ha中卤素的摩尔比包括但不限于上述范围,而将其限定在上述范围内有利于提高3
‑
乙基
‑3‑
羟甲基氧杂环丁烷的转化率。
[0034]
在一种优选的实施例中,醚化反应的反应温度为10~60℃,物料停留时间为2~
5min。醚化反应的反应温度和物料停留时间包括但不限于上述范围,而将其限定在上述范围内有利于进一步提高醚化产物的产率。比如醚化反应的反应温度可以为10℃、20℃、30℃、40℃、50℃、60℃。
[0035]
上述分离步骤可以采用本领域常用的装置进行。优选地,分离的步骤采用的装置包括:二级薄膜蒸发装置或精馏塔。
[0036]
以下结合具体实施例对本技术作进一步详细描述,这些实施例不能理解为限制本技术所要求保护的范围。
[0037]
实施例采用图1所示的装置制备氧杂环丁烷衍生物,合成方法包括:
[0038]
(1)将计量的3
‑
乙基
‑3‑
羟甲基氧杂环丁烷(mox101)和原料r
‑
(x)n混合均匀装入有机物原料储罐11中,碱溶液和催化剂混合均匀装入碱溶液储罐12。
[0039]
(2)微反应器20、一级薄膜蒸发器40、二级薄膜蒸发器50调节至设定温度,开启有机物原料进料泵101和原料进料泵102,使原料进入微混合器10中进行混合,在微反应器20中停留一定时间后进入缓冲罐21,取有机相gc检测转化率。
[0040]
(3)在缓冲罐21中积累一定物料后进入分相罐30,静置分离有机相和水相,两相分别进入废水储罐31和有机相储罐32中。
[0041]
(4)开启进入一级薄膜蒸发器进料泵103,有机相经一级薄膜蒸发器40分离回收过量的原料,得粗产品,回收的原料储存在回收原料储罐42中,粗产品储存在粗产品储罐41中;开启二级薄膜蒸发器的进料泵104,粗产品进入二级薄膜蒸发器50提纯得产品,成品储存在成品储罐51中,重沸物储存在重沸物储罐52中。实施例1至9中的工艺参数见表1和表2。
[0042]
表1
[0043]
[0044][0045]
表2
[0046]
[0047][0048]
实施例10
[0049]
与实施例1的区别为:微反应器的反应通道内径为200μm。
[0050]3‑
乙基
‑3‑
[(环氧乙烷基
‑2‑
甲氧基)甲基]氧杂环丁烷的选择性为90.5%,收率为74.6%。
[0051]
实施例11
[0052]
与实施例1的区别为:微反应器的反应通道尺寸为10000μm。
[0053]3‑
乙基
‑3‑
[(环氧乙烷基
‑2‑
甲氧基)甲基]氧杂环丁烷的选择性为95.2%,收率为76.7wt%。
[0054]
实施例12
[0055]
与实施例1的区别为:催化剂添加量为1.0%,催化剂为聚乙二醇二甲醚,物料停留时间为5min。
[0056]3‑
乙基
‑3‑
[(环氧乙烷基
‑2‑
甲氧基)甲基]氧杂环丁烷的选择性为94.4%,收率为82.4wt%。
[0057]
实施例13
[0058]
与实施例1的区别为:催化剂添加量为1.0%,催化剂为18
‑
冠
‑
6,物料停留时间为4min。
[0059]3‑
乙基
‑3‑
[(环氧乙烷基
‑2‑
甲氧基)甲基]氧杂环丁烷的选择性为95.2%,收率为81.9wt%。
[0060]
实施例14
[0061]
与实施例1的区别为:催化剂添加量为1.0%,催化剂为聚乙二醇,物料停留时间为4min。
[0062]3‑
乙基
‑3‑
[(环氧乙烷基
‑2‑
甲氧基)甲基]氧杂环丁烷的选择性为96.2%,收率为80.5wt%。
[0063]
实施例15
[0064]
与实施例1的区别为:催化剂添加量为1.0%,催化剂为十四烷基三甲基氯化铵,物料停留时间为5min。
[0065]3‑
乙基
‑3‑
[(环氧乙烷基
‑2‑
甲氧基)甲基]氧杂环丁烷的选择性为95.4%,收率为82.4wt%。
[0066]
实施例16
[0067]
与实施例1的区别为:醚化反应的反应温度为30℃。
[0068]3‑
乙基
‑3‑
[(环氧乙烷基
‑2‑
甲氧基)甲基]氧杂环丁烷的选择性为92.8%,收率为72.4wt%。
[0069]
实施例17
[0070]
与实施例1的区别为:微反应器的反应通道尺寸为12000μm。
[0071]3‑
乙基
‑3‑
[(环氧乙烷基
‑2‑
甲氧基)甲基]氧杂环丁烷的选择性为90.8%,收率为67.5wt%。
[0072]
实施例18
[0073]
与实施例1的区别为:将计量的3
‑
乙基
‑3‑
羟甲基氧杂环丁烷(mox101)、片碱、催化剂混合均匀装入有机物原料储罐11中,环氧氯丙烷装入原料储罐12。微反应器的反应通道内径为500μm。
[0074]3‑
乙基
‑3‑
[(环氧乙烷基
‑2‑
甲氧基)甲基]氧杂环丁烷的选择性为95.0%,收率为
80.6%。
[0075]
实施例19
[0076]
与实施例1的区别为:将计量的3
‑
乙基
‑3‑
羟甲基氧杂环丁烷(mox101)、环氧氯丙烷、催化剂混合均匀装入有机物原料储罐11中,碱溶液装入原料储罐12。微反应器的反应通道尺寸为8000μm。
[0077]3‑
乙基
‑3‑
[(环氧乙烷基
‑2‑
甲氧基)甲基]氧杂环丁烷的选择性为95.6%,收率为82.3wt%。
[0078]
实施例20
[0079]
与实施例1的区别为:醚化反应的反应温度为100℃。
[0080]3‑
乙基
‑3‑
[(环氧乙烷基
‑2‑
甲氧基)甲基]氧杂环丁烷的选择性为94.6%,收率为76.1wt%。
[0081]
实施例21
[0082]
与实施例1的区别为:醚化反应的反应温度为5℃。
[0083]3‑
乙基
‑3‑
[(环氧乙烷基
‑2‑
甲氧基)甲基]氧杂环丁烷的选择性为85.9%,收率为72.4wt%。
[0084]
实施例22
[0085]
与实施例1的区别为:催化剂添加量为0.1%,催化剂为四丁基溴化铵,物料停留时间为5min。
[0086]3‑
乙基
‑3‑
[(环氧乙烷基
‑2‑
甲氧基)甲基]氧杂环丁烷的选择性为90.3%,收率为73.5wt%。
[0087]
实施例23
[0088]
与实施例1的区别为:将计量的3
‑
乙基
‑3‑
羟甲基氧杂环丁烷(mox101)、片碱混合均匀装入有机物原料储罐11中,环氧氯丙烷、催化剂装入原料储罐12。催化剂添加量为5%,催化剂为18
‑
冠
‑
6,物料停留时间为2min。
[0089]3‑
乙基
‑3‑
[(环氧乙烷基
‑2‑
甲氧基)甲基]氧杂环丁烷的选择性为92.1%,收率为78.3wt%。
[0090]
实施例24
[0091]
与实施例1的区别为:将计量的3
‑
乙基
‑3‑
羟甲基氧杂环丁烷(mox101)、片碱混合均匀装入有机物原料储罐11中,环氧氯丙烷、催化剂装入原料储罐12。催化剂添加量为4%,催化剂为四丁基溴化铵,物料停留时间为3min。
[0092]3‑
乙基
‑3‑
[(环氧乙烷基
‑2‑
甲氧基)甲基]氧杂环丁烷的选择性为91.7%,收率为75.3wt%。
[0093]
对比例1至5采用常规的反应器制备氧杂环丁烷衍生物,具体工艺参数见表3,合成方法包括:
[0094]
在四口烧瓶中投入3
‑
乙基
‑3‑
羟甲基氧杂环(mox101)和原料r
‑
(x)n,开启搅拌混合均匀,将碱溶液和催化剂混合均匀滴加至上述四口烧瓶中,滴加完毕后保温,进行反应,取有机层gc检测转化率,转化率不再变化后停止反应。将反应产物体系进行静置分相,然后将其进行精馏得到成品。
[0095]
表3
[0096][0097]
从以上的描述中,可以看出,本发明上述的实施例实现了如下技术效果:
[0098]
比较实施例1至24及对比例1至5可知,选用本技术提供的方法有利于氧杂环丁烷衍生物的选择性和收率。
[0099]
比较实施例1、6、10、11、17至19可知,将微反应器反应通道的内径限定在本技术的范围内有利于提高氧杂环丁烷衍生物的选择性和收率。
[0100]
比较实施例1、16、20和21可知,将醚化反应的反应温度限定在本技术的范围内有利于提高氧杂环丁烷衍生物的选择性和收率。
[0101]
以上所述仅为本发明的优选实施例而已,并不用于限制本发明,对于本领域的技术人员来说,本发明可以有各种更改和变化。凡在本发明的精神和原则之内,所作的任何修改、等同替换、改进等,均应包含在本发明的保护范围之内。