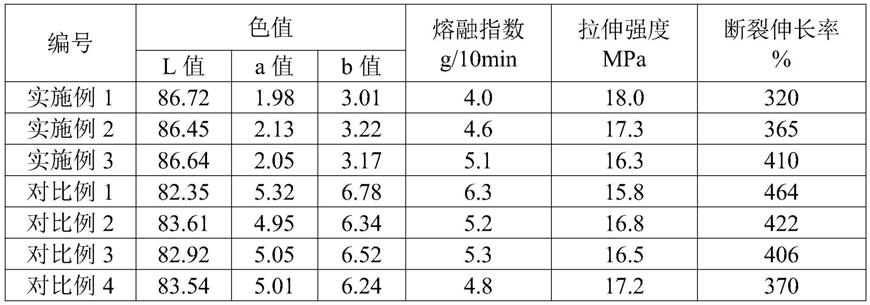
一种高热稳定性的pbat材料制备方法
技术领域
1.本发明属于高分子材料领域,具体地说是一种高热稳定性的pbat材料制备方法。
背景技术:2.塑料自发明以来,在生活中被大量使用。然而塑料在给生活带来极大便利的同时,大量的不可降解塑料也给环境造成了严重的污染。此外,由于传统塑料主要来源于石油,这也给能源危机蒙上了阴影。发展生物降解材料替代传统塑料逐渐成为行业发展趋势。如何应对日益严重的环境污染问题,实现可持续发展,已经成为全球关注的焦点。大力研究开发环境友好的生物降解塑料,被认为是解决当前问题的有效途径,更是实现全球经济可持续发展的战略选择。
3.聚己二酸/对苯二甲酸丁二酯(pbat)是脂肪族和芳香族的共聚物,综合了脂肪族聚酯的优异降解性能和芳香族聚酯的良好力学性能,既有较好的延展性和断裂伸长率,也能够被微生物降解为水和二氧化碳,是目前生物降解塑料研究中非常活跃和市场应用最好降解材料之一。
4.pbat的聚合方法主要包括一步法和两步法,pbat合成过程都是由酯化反应与缩聚反应两个过程组成。在聚合过程中由于温度过高、催化剂活性高、反应速度快等问题会导致副产物增加,造成聚合物产物热稳定性和色泽较差,使产品的货架期变短,影响使用效果。
技术实现要素:5.本发明提供一种高热稳定性的pbat材料制备方法,用以解决现有技术中的缺陷。
6.本发明通过以下技术方案予以实现:
7.一种高热稳定性的pbat材料制备方法,包括如下步骤:
8.步骤一:将pta/bdo加入0.3wt%催化剂,在195℃的温度下酯化反应2
‑
3h;
9.步骤二:将aa/bdo加入0.3wt%催化剂,在160℃的温度下酯化反应*1
‑
2h;
10.步骤三:将步骤一所得酯化物和步骤二所得酯化物混合,加入0.4wt%催化剂,在160
‑
220℃温度,酯化率达到95%以上,结束酯化反应,得混合酯化物;
11.步骤四:将步骤三中酯化完成的混合酯化物先进行预聚合,预聚合完成后加入0.2wt%催化剂,0.2
‑
5wt%的稳定剂在250℃下进行终聚合反应1.5h,得pbat熔体;
12.步骤五:步骤四所得pbat熔体进行增粘操作得到高分子量的pbat熔体;
13.步骤六:步骤五所得的高分子量的pbat熔体进入切粒系统得到pbat树脂。
14.如上所述的一种高热稳定性的pbat材料制备方法,所述的步骤一中pta/bdo与步骤二中aa/bdo添加质量比为0.8
‑
1.4:0.9
‑
1.3。
15.如上所述的一种高热稳定性的pbat材料制备方法,所述的步骤一至步骤四中的催化剂为钛系主催化剂(如钛酸四丁酯)和金属盐(三氧化二锑)等助催化剂。
16.如上所述的一种高热稳定性的pbat材料制备方法,所述的步骤二中所得混合酯化物的酯化率大于95%。
17.如上所述的一种高热稳定性的pbat材料制备方法,所述的步骤四中预聚合的操作为:低聚物通过反应釜进入到预聚釜内,在真空作用下,反应脱出小分子,从而聚合度不断增加,形成预聚物。
18.如上所述的一种高热稳定性的pbat材料制备方法,所述的稳定剂的包括受阻胺类稳定剂与酚类抗氧剂。
19.如上所述的一种高热稳定性的pbat材料制备方法,所述的受阻胺类稳定剂与酚类抗氧剂的重量配比为1:5
‑
7:1。
20.如上所述的一种高热稳定性的pbat材料制备方法,所述的受阻胺类稳定剂为稳定剂uv
‑
944、稳定剂uv
‑
770、稳定剂uv
‑
119fd其中的任意一种或任意两种以任意比例混合的混合物。
21.如上所述的一种高热稳定性的pbat材料制备方法,所述的酚类抗氧剂为抗氧剂1098、抗氧剂245、抗氧剂3114其中的任意一种或任意两种以任意比例混合的混合物。
22.如上所述的一种高热稳定性的pbat材料制备方法,所述的所述的受阻胺类稳定剂与酚类抗氧剂的重量配比为1:3
‑
4:1。
23.如上所述的一种高热稳定性的pbat材料制备方法,所述的步骤五的增粘操作为:高聚物通过泵体输送到增粘装置内,利用高真空环境,使得bdo小分子不断脱出,bdo蒸汽通过真空系统不断排除,保证了缩聚反应的进一步发生,从而实现产品的增粘要求。
24.如上所述的一种高热稳定性的pbat材料制备方法,所述的步骤五制备的高分子量的pbat熔体的分子量为80000
‑
130000。
25.本发明的优点是:本发明采用受阻胺类稳定剂与酚类抗氧剂复配使用,从而改善通过酯化聚合方法得到的pbat的色泽缺陷,使pbat树脂的lab值中l值提高,a和b值降低,制备的产品性能更稳定,从而保证产品在后期改性、使用过程中的稳定性。
附图说明
26.为了更清楚地说明本发明实施例或现有技术中的技术方案,下面将对实施例或现有技术描述中所需要使用的附图作一简单地介绍,显而易见地,下面描述中的附图是本发明的一些实施例,对于本领域普通技术人员来讲,在不付出创造性劳动性的前提下,还可以根据这些附图获得其他的附图。
27.图1是本发明的工艺流程图;
28.图2是本发明中对比例1制备的pbat树脂;
29.图3是本发明中实施例1制备的pbat树脂;
30.图4是本发明中实施例2制备的pbat树脂熔融指数的测试过程图;
31.图5是本发明中实施例2制备的pbat树脂熔融指数测试后的样品图;
32.图6是本发明中实施例1制备的pbat树脂拉伸测试过程图;
33.图7是本发明中实施例1的拉伸测试报告。
具体实施方式
34.为使本发明实施例的目的、技术方案和优点更加清楚,下面将结合本发明实施例中的附图,对本发明实施例中的技术方案进行清楚、完整地描述,显然,所描述的实施例是
本发明一部分实施例,而不是全部的实施例。基于本发明中的实施例,本领域普通技术人员在没有作出创造性劳动前提下所获得的所有其他实施例,都属于本发明保护的范围。
35.实施例1
36.将pta/bdo和aa/bdo分别加入到第一酯化釜内,加入0.3wt%催化剂,分别在195℃和160℃下进行酯化反应,再将第一酯化釜内的酯化物输送到第二酯化釜,加入0.4wt%催化剂,此时酯化率达到95%以上,然后再将第二酯化釜内的酯化物输送到再进行预聚合终聚反应釜,加入0.2wt%催化剂、1wt%的稳定剂uv
‑
944和抗氧剂1098(质量比为1:4),并在250℃下反应90min,经终聚反应得的pbat熔体输送到增粘反应釜进行增粘得到高分子量的pbat熔体,最后pbat熔体进入切粒系统得到pbat树脂。
37.实施例2
38.将pta/bdo和aa/bdo分别加入到第一酯化釜内,加入0.3wt%催化剂,分别在195℃和160℃下进行酯化反应,再将第一酯化釜内的酯化物输送到第二酯化釜,加入0.4wt%催化剂,此时酯化率达到95%以上,然后再将第二酯化釜内的酯化物输送到再进行预聚合终聚反应釜,加0.2wt%催化剂、0.6wt%的稳定剂uv
‑
119fd和抗氧剂245(质量比为2:1),并在250℃下反应90min,经终聚反应得的pbat熔体输送到增粘反应釜进行增粘得到高分子量的pbat熔体,最后pbat熔体进入切粒系统得到pbat树脂。
39.实施例3
40.将pta/bdo和aa/bdo分别加入到第一酯化釜内,加入0.3wt%催化剂,分别在195℃和160℃下进行酯化反应,再将第一酯化釜内的酯化物输送到第二酯化釜,加入0.4wt%催化剂,此时酯化率达到95%以上,然后再将第二酯化釜内的酯化物输送到再进行预聚合终聚反应釜,加0.2wt%催化剂、0.5wt%的稳定剂uv
‑
770和抗氧剂3114(质量比为1:3),并在250℃下反应90min,经终聚反应得的pbat熔体输送到增粘反应釜进行增粘得到高分子量的pbat熔体,最后pbat熔体进入切粒系统得到pbat树脂。
41.对比例1
42.除不加稳定剂,其他步骤按照实施例1执行。
43.对比例2
44.除了仅采用uv
‑
944为稳定剂(质量分数与实施例相同)之外,其他步骤按照实施例1执行。
45.对比例3
46.除了仅采用抗氧剂1098为稳定剂(质量分数与实施例相同)之外,其他步骤按照实施例1执行。
47.对比例4
48.除了仅采用uv
‑
770为稳定剂(质量分数与实施例2相同)之外,其他步骤按照实施例2执行。
49.以下将通过实施例对本发明进行详细描述
50.实施例中和对比例中:
51.(1)色值测试
52.在本发明中,色值参数通过cm
‑
5分光测色计测得。
53.(2)熔融指数测试
54.在本发明中,熔融指数采用熔融指数测试仪进行测试,测试条件是190℃,2.16kg。
55.(3)拉伸性能测试
56.在本发明中,拉伸性能采用万能拉力试验机进行测试其结果如表一所示。
[0057][0058]
表一
[0059]
从表一中的实验数据可以看到,实施例1
‑
4和对比例1
‑
4。从表格中可以看出,加入复合稳定剂较加入单一加稳定剂的lab值的l值偏高、a值和b值偏低,从图2和图3中也可以看到,对比例1制备的pbat树脂颜色发黄、发红,而实施例制备的pbat树脂外观颜色白度较高,这说明复配稳定剂的使用明显改善了pbat树脂的色泽缺陷。另外,从表1中也可以看到,复配稳定剂的加入对pbat树脂的熔融指数和拉伸性能影响不大。
[0060]
最后应说明的是:以上实施例仅用以说明本发明的技术方案,而非对其限制;尽管参照前述实施例对本发明进行了详细的说明,本领域的普通技术人员应当理解:其依然可以对前述各实施例所记载的技术方案进行修改,或者对其中部分技术特征进行等同替换;而这些修改或者替换,并不使相应技术方案的本质脱离本发明各实施例技术方案的精神和范围。