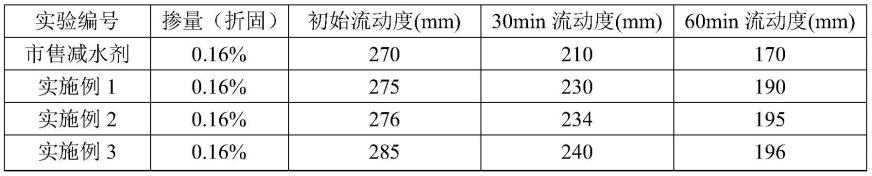
1.本发明涉及混凝土外加剂技术领域,具体涉及一种降粘型固体聚羧酸减水剂的制备方法。
背景技术:2.聚羧酸系减水剂(pc)作为第四代高性能减水剂,具有减水率高、坍落度损失小、对环境负荷小等优点,广泛应用于一些国家重点建设工程。pc的优异性能主要是由其特殊的分子结构决定的,其主链、支链和阴离子基团可以通过改变反应原料来进行调整,聚羧酸高性能减水剂分子结构呈梳型,主链较短,侧链较长,主链一般为聚乙烯链,侧链一般含有烷基、羧基、磺酸基、聚氧烷基以及酰胺基等,其分子结构不仅空间自由度大,各链段可设计性强。聚羧酸减水剂作为第三代减水剂,以其高减水、性能多样化且制备容易等优点广泛应用在建筑领域,聚羧酸减水剂一般为10-60%含固量的液体,长距离的运输会造成物流成本的上升,而且在特殊领域如灌浆料不能适用;另外现有的聚羧酸减水剂由于其粘度高,在使用之后,在高掺合材、低水胶比混凝土配制中,导致整个混凝土粘度高,使得施工过程很麻烦,不利于施工的进行。
3.为了解决这一问题,研究人员开发出了固体聚羧酸,目前固体聚羧酸的开发思路主要有两种,即喷雾干燥法及自由基本体聚合法,喷雾干燥法是目前比较通用的制备粉剂或固体聚羧酸产品的方法。专利cn109535340a公开了一种粉末状早强型聚羧酸减水剂及其制备方法,该发明在聚合体系中引入刚性基团和高分子量聚醚链,并与钙-硅复合氧化物杂化制得聚合物,随后通过喷雾干燥法制得粉末状早强型聚羧酸减水剂。但是喷雾干燥成本不低,制备固体聚羧酸减水剂的传统高温喷粉工艺能耗高、易结块;添加其它组分可防止粉末结块并增强流动性,但会使粉剂中的有效组分含量降低。
4.自由基本体聚合法是另一种主要的固体聚羧酸合成方法,和水剂聚羧酸产品相比,固含量较高甚至不加入任何溶剂,反应机理与液体聚羧酸产品类似。专利cn109928661a通过自由基本体聚合制备一种降粘型固体聚羧酸减水剂,由不饱和聚氧乙烯醚大单体、不饱和小单体、引发剂、还原剂以及链转移剂在60-90℃通过自由基聚合反应制成,优点是可以不添加其他组分直接制备固体聚羧酸;专利cn109694446a公开了一种固体聚羧酸减水剂的合成方法,具体方法是先通过液体聚醚a和邻苯二甲酸酐制得邻苯二甲酸单聚醚酯,随后将部分邻苯二甲酸单聚醚酯和不饱和聚醚大单体混合作为打底液,接着将引发剂与羧酸单体分别滴加到上述打底液中,从而制得固体聚羧酸减水剂。上述专利均是通过自由基本体聚合制备的固体聚羧酸减水剂,而自由基本体聚合存在性能差于减水剂水剂的情况,且该类型的反应体系粘度较大,对反应传动设备有着很大的考验,粘度上升也会导致聚合物分子量不易控制等问题,对聚羧酸减水剂质量有着不利影响。
技术实现要素:5.本发明克服现有技术中聚羧酸减水剂由于粘度高,在使用之后,在高掺合材、低水
胶比混凝土配制中,导致整个混凝土粘度高,使得施工过程很麻烦,不利于施工的进行,且无法根据实际需要做到结构性、功能性可调等不足之处,本发明提供了一种降粘型固体聚羧酸减水剂的制备方法,具体技术方案如下:一种降粘型固体聚羧酸减水剂的制备方法,包括以下步骤:上述降粘型固体聚羧酸减水剂由两种不同分子量的聚乙二醇单甲醚分别与二异氰酸酯类化合物发生加成反应,所得产物再分别与丙烯酸以及含羟基不饱和单体聚合获得;上述不同分子量的聚乙二醇单甲醚分别为小分子量聚乙二醇单甲醚和大分子量聚乙二醇单甲醚,上述小分子量聚乙二醇单甲基醚的分子量为600-2000,上述大分子量聚乙二醇单甲基醚的分子量为2000-6000。
6.上述二异氰酸酯类化合物为甲苯二异氰酸酯、异佛尔酮二异氰酸酯、二苯基甲烷二异氰酸酯、二环己基甲烷二异氰酸酯、六亚甲基二异氰酸酯中的任一种,上述二异氰酸酯类化合物与聚乙二醇单甲基醚的摩尔比为(1
±
0.05):1。
7.上述含羟基不饱和单体为丙烯酸羟乙酯、丙烯酸羟丙酯、丙烯酸羟丁酯、甲基丙烯酸羟乙酯、甲基丙烯酸羟丙酯、甲基丙烯酸羟丁酯中的任一种。
8.一种降粘型固体聚羧酸减水剂的制备方法,具体有如下工艺步骤:(1)将二异氰酸酯类化合物与小分子量聚乙二醇单甲基醚进行加成反应,得到组分a1;(2)将二异氰酸酯类化合物与大分子量聚乙二醇单甲基醚进行加成反应,得到组分a2;(3)将链转移剂、引发剂加入到溶剂中搅拌均匀形成打底液,随后将丙烯酸与含羟基不饱和单体混合后滴加到打底液中,反应结束后将溶剂抽真空去除,制备得组分b;(4)将步骤(1)制备得到的组分a1和步骤(2)制备得到的组分a2混合均匀后加入到步骤(3)所得的组分b中,混合搅拌均匀,反应结束后冷凝切片,即制备得到降粘型固体聚羧酸减水剂。
9.上述步骤(1)和步骤(2)中的反应条件均为反应温度50℃-120℃,反应时间4h-10h。
10.上述步骤(1)和步骤(2)反应过程中均需使用催化剂,且所用催化剂均为三乙胺、三亚乙基二胺、二月桂酸二丁基锡、钛酸四异丁酯中的任一种,且催化剂的用量为小分子量聚乙二醇单甲基醚或大分子量聚乙二醇单甲基醚摩尔数的0.1%-5%。
11.上述步骤(3)中的引发剂为偶氮二异丁腈、过硫酸铵、偶氮二异丁脒盐酸盐中的任一种。
12.上述步骤(3)中的链转移剂为巯基乙醇或巯基丙酸。
13.上述步骤(3)中丙烯酸与含羟基不饱和单体的摩尔比为(3-8):1。
14.上述步骤(3)中引发剂与含羟基不饱和单体的摩尔比为(0.02-0.04):1。
15.上述步骤(3)中链转移剂与含羟基不饱和单体的摩尔比为(0.01-0.06):1。
16.本发明相比现有技术具有以下优点:
17.1、本发明将主链分子(组分b)及侧链分子(组分a1、组分a2)分别合成后再通过简单高效的有机反应,将主链和侧链组合起来制备聚羧酸减水剂;组分a1和组分a2均采用相同的制备方法,通过采用两种不同长度的聚醚分子来制备聚羧酸减水剂,通过长链聚醚和短链聚醚在主链上的配合,可实现在保证减水剂减水效果的同时降低减水剂分子的粘性;通过该方法制备得到的聚羧酸减水剂结构易调,反应很容易进行,且反应收率较高;与自由基聚合相比,该制备方法不受单体聚合活性影响,扩大了聚醚分子的选择范围,而且丰富了固体聚羧酸领域的合成方法;
18.2.本发明选用两种不同长度的聚醚分子来制备聚羧酸减水剂,可以增强减水剂的降粘性能和减水效果;单独使用大分子量聚乙二醇单甲基醚为原料来制备得到的减水剂具有较好的减水效果,但是减水剂的粘性过差,不利于商品混凝土的施工;单独使用小分子量聚乙二醇单甲基醚为原料来制备得到的减水剂具有较好的降粘效果,但是减水剂的减水效果不好,不利于商品混凝土的施工;本发明通过长短链聚醚的配合,使减水剂具有较好的减水效果的同时能够有效降低混凝土的粘度。
19.3.本发明采用有机反应制备聚羧酸减水剂,在保证环保无污染的情况下,避免了本体自由基聚合分子量不易控制等问题,制备的减水剂性能要优于本体聚合制备的减水剂,且可根据实际需要做到结构性、功能性可调;同时制备工艺绿色环保,明显有利于大规模工业化生产。
20.本发明合成方法与传统方法相比,反应所需原料常见易得,整个合成过程简单可控、高效便捷,反应所用步骤也均为普通操作工艺,无需特殊操作或昂贵助剂,反应条件温和,工艺绿色环保,因此易于实现工业化生产;该合成过程对设备无特殊要求,且具有分子可设计能力强、分子量可控、性能好等优点,具有很好的推广潜力和应用价值。
具体实施方式
21.下面将结合本发明实施例,对本发明的技术方案进行清楚、完整的描述,显然,所描述的实施例仅仅是本发明一部分实施例,而不是全部的实施例。基于本发明中的实施例,本领域普通技术人员在没有做出创造性劳动前提下所获得的所有其他实施例,都属于本发明保护的范围。
22.实施例1:
23.一种降粘型固体聚羧酸减水剂的制备方法,包括如下步骤:
24.(1)将87g甲苯二异氰酸酯与6g二月桂酸二丁基锡混合均匀得到混合液,随后把300g分子量为600的聚乙二醇单甲基醚加入到混合溶液中,在50℃反应条件下反应4h至反应结束后,得到组分a1;
25.(2)将87g甲苯二异氰酸酯与12g二月桂酸二丁基锡混合均匀得到混合液,随后把3000g分子量为6000的聚乙二醇单甲基醚加入到混合溶液中,在50℃反应条件下反应4h至反应结束后,得到组分a2;
26.(3)将4.68g链转移剂巯基乙醇、3.28g引发剂偶氮二异丁腈加入到332g四氢呋喃中搅拌均匀形成打底液,随后将216g丙烯酸与116g丙烯酸羟乙酯混合后缓慢滴加到打底液中,滴加时间控制在2h,在65℃反应条件下,反应1h后,停止反应并将溶剂抽真空去除,制备得组分b;
27.(4)将步骤(1)制备得到的组分a1和步骤(2)制备得到的组分a2混合均匀后加入到步骤(3)所得的组分b中,在100℃反应条件下反应4h,反应结束后冷凝切片,即制备得到降粘型固体聚羧酸减水剂。
28.实施例2:
29.一种降粘型固体聚羧酸减水剂的制备方法,包括如下步骤:
30.(1)将111g异氟尔酮二异氰酸酯与3g二月桂酸二丁基锡混合均匀得到混合液,随后把500g分子量为1000的聚乙二醇单甲基醚加入到混合溶液中,在70℃反应条件下反应6h
至反应结束后,得到组分a1;
31.(2)将111g异氟尔酮二异氰酸酯与6g二月桂酸二丁基锡混合均匀得到混合液,随后把1000g分子量为2000的聚乙二醇单甲基醚加入到混合溶液中,在70℃反应条件下反应6h至反应结束后,得到组分a2;
32.(3)将2.34g链转移剂巯基乙醇、4.92g引发剂偶氮二异丁腈加入到332g四氢呋喃中搅拌均匀形成打底液,随后将288g丙烯酸与130g丙烯酸羟丙酯混合后缓慢滴加到打底液中,滴加时间控制在2h,在70℃反应条件下,反应2h后,停止反应并将溶剂抽真空去除,制备得组分b;
33.(4)将步骤(1)制备得到的组分a1和步骤(2)制备得到的组分a2混合均匀后加入到步骤(3)所得的组分b中,在80℃反应条件下反应6h,反应结束后冷凝切片,即制备得到降粘型固体聚羧酸减水剂。
34.实施例3:
35.一种降粘型固体聚羧酸减水剂的制备方法,包括如下步骤:
36.(1)将125g二苯基甲烷二异氰酸酯与0.19g三乙胺混合均匀得到混合液,随后把500g分子量为1000的聚乙二醇单甲基醚加入到混合溶液中,在90℃反应条件下反应8h至反应结束后,得到组分a1;
37.(2)将125g二苯基甲烷二异氰酸酯与0.48g三乙胺混合均匀得到混合液,随后把2000g分子量为4000的聚乙二醇单甲基醚加入到混合溶液中,在90℃反应条件下反应8h至反应结束后,得到组分a2;
38.(3)将1.75g链转移剂巯基乙醇、9.12g引发剂过硫酸铵加入到332gn,n-二甲基甲酰胺中搅拌均匀形成打底液,随后将360g丙烯酸与144g丙烯酸羟丁酯混合后缓慢滴加到打底液中,滴加时间控制在3h,在90℃反应条件下,反应1h后,停止反应并将溶剂抽真空去除,制备得组分b;
39.(4)将步骤(1)制备得到的组分a1和步骤(2)制备得到的组分a2混合均匀后加入到步骤(3)所得的组分b中,在70℃反应条件下反应8h,反应结束后冷凝切片,即制备得到降粘型固体聚羧酸减水剂。
40.实施例4:
41.一种降粘型固体聚羧酸减水剂的制备方法,包括如下步骤:
42.(1)将131g二环己基甲烷二异氰酸酯与0.05g三亚乙基二胺混合均匀得到混合液,随后把1000g分子量为2000的聚乙二醇单甲基醚加入到混合溶液中,在120℃反应条件下反应7h至反应结束后,得到组分a1;
43.(2)将131g二环己基甲烷二异氰酸酯与0.53g三亚乙基二胺混合均匀得到混合液,随后把1500g分子量为3000的聚乙二醇单甲基醚加入到混合溶液中,在120℃反应条件下反应7h至反应结束后,得到组分a2;
44.(3)将1.9g链转移剂巯基丙酸、4.56g引发剂过硫酸铵加入到332gn,n-二甲基甲酰胺中搅拌均匀形成打底液,随后将432g丙烯酸与130g甲基丙烯酸羟乙酯混合后缓慢滴加到打底液中,滴加时间控制在3h,在70℃反应条件下,反应2h后,停止反应并将溶剂抽真空去除,制备得组分b;
45.(4)将步骤(1)制备得到的组分a1和步骤(2)制备得到的组分a2混合均匀后加入到
步骤(3)所得的组分b中,在50℃反应条件下反应7h,反应结束后冷凝切片,即制备得到降粘型固体聚羧酸减水剂。
46.实施例5:
47.一种降粘型固体聚羧酸减水剂的制备方法,包括如下步骤:
48.(1)将84g六亚甲基二异氰酸酯与1.29g钛酸四异丁酯混合均匀得到混合液,随后把1000g分子量为2000的聚乙二醇单甲基醚加入到混合溶液中,在80℃反应条件下反应9h至反应结束后,得到组分a1;
49.(2)将84g六亚甲基二异氰酸酯与3.23g钛酸四异丁酯混合均匀得到混合液,随后把2000g分子量为4000的聚乙二醇单甲基醚加入到混合溶液中,在80℃反应条件下反应9h至反应结束后,得到组分a2;
50.(3)将1.59g链转移剂巯基丙酸、8.1g引发剂偶氮二异丁脒盐酸盐加入到332g水中搅拌均匀形成打底液,随后将504g丙烯酸与144g甲基丙烯酸羟丙酯混合后缓慢滴加到打底液中,滴加时间控制在4h,在60℃反应条件下,反应1h后,停止反应并将溶剂抽真空去除,制备得组分b;
51.(4)将步骤(1)制备得到的组分a1和步骤(2)制备得到的组分a2混合均匀后加入到步骤(3)所得的组分b中,在80℃反应条件下反应9h,反应结束后冷凝切片,即制备得到降粘型固体聚羧酸减水剂。
52.实施例6:
53.一种降粘型固体聚羧酸减水剂的制备方法,包括如下步骤:
54.(1)将87g甲苯二异氰酸酯与1.2g二月桂酸二丁基锡混合均匀得到混合液,随后把500g分子量为1000的聚乙二醇单甲基醚加入到混合溶液中,在90℃反应条件下反应6h至反应结束后,得到组分a1;
55.(2)将87g甲苯二异氰酸酯与3.0g二月桂酸二丁基锡混合均匀得到混合液,随后把2500g分子量为5000的聚乙二醇单甲基醚加入到混合溶液中,在90℃反应条件下反应6h至反应结束后,得到组分a2;
56.(3)将1.26g链转移剂巯基丙酸、10.8g引发剂偶氮二异丁脒盐酸盐加入到332g水中搅拌均匀形成打底液,随后将576g丙烯酸与160g甲基丙烯酸羟丁酯混合后缓慢滴加到打底液中,滴加时间控制在4h,在50℃反应条件下,反应2h后,停止反应并将溶剂抽真空去除,制备得组分b;
57.(4)将步骤(1)制备得到的组分a1和步骤(2)制备得到的组分a2混合均匀后加入到步骤(3)所得的组分b中,在80℃反应条件下反应6h,反应结束后冷凝切片,即制备得到降粘型固体聚羧酸减水剂。
58.对比例1:
59.一种降粘型固体聚羧酸减水剂的制备方法,包括如下步骤:
60.(1)在制备组分a1和组分a2时均采用分子量为600的聚乙二醇单甲基醚为原料,制备方法均如下,将87g甲苯二异氰酸酯与6g二月桂酸二丁基锡混合均匀得到混合液,随后把300g分子量为600的聚乙二醇单甲基醚加入到混合溶液中,在50℃反应条件下反应4h至反应结束后,得到组分a1、组分a2;
61.(2)将4.68g链转移剂巯基乙醇、3.28g引发剂偶氮二异丁腈加入到332g四氢呋喃
中搅拌均匀形成打底液,随后将216g丙烯酸与116g丙烯酸羟乙酯混合后缓慢滴加到打底液中,滴加时间控制在2h,在65℃反应条件下,反应1h后,停止反应并将溶剂抽真空去除,制备得组分b;
62.(4)将步骤(1)制备得到的组分a1和a2混合均匀后加入到步骤(3)所得的组分b中,在100℃反应条件下反应4h,反应结束后冷凝切片,即制备得到降粘型固体聚羧酸减水剂。
63.对比例2:
64.一种降粘型固体聚羧酸减水剂的制备方法,包括如下步骤:
65.(1)在制备组分a1和组分a2时均采用分子量为6000的聚乙二醇单甲基醚为原料,制备方法均如下,将87g甲苯二异氰酸酯与12g二月桂酸二丁基锡混合均匀得到混合液,随后把3000g分子量为6000的聚乙二醇单甲基醚加入到混合溶液中,在50℃反应条件下反应4h至反应结束后,得到组分a1、组分a2;
66.(3)将4.68g链转移剂巯基乙醇、3.28g引发剂偶氮二异丁腈加入到332g四氢呋喃中搅拌均匀形成打底液,随后将216g丙烯酸与116g丙烯酸羟乙酯混合后缓慢滴加到打底液中,滴加时间控制在2h,在65℃反应条件下,反应1h后,停止反应并将溶剂抽真空去除,制备得组分b;
67.(4)将步骤(1)制备得到的组分a1和a2混合均匀后加入到步骤(3)所得的组分b中,在100℃反应条件下反应4h,反应结束后冷凝切片,即制备得到降粘型固体聚羧酸减水剂。
68.对比例3:
69.一种降粘型固体聚羧酸减水剂的制备方法,包括如下步骤:
70.(1)在制备组分a1和组分a2时均采用分子量为2000的聚乙二醇单甲基醚为原料,制备方法均如下,将131g二环己基甲烷二异氰酸酯与0.05g三亚乙基二胺混合均匀得到混合液,随后把1000g分子量为2000的聚乙二醇单甲基醚加入到混合溶液中,在120℃反应条件下反应7h至反应结束后,得到组分a1、组分a2;
71.(3)将1.9g链转移剂巯基丙酸、4.56g引发剂过硫酸铵加入到332gn,n-二甲基甲酰胺中搅拌均匀形成打底液,随后将432g丙烯酸与130g甲基丙烯酸羟乙酯混合后缓慢滴加到打底液中,滴加时间控制在3h,在70℃反应条件下,反应2h后,停止反应并将溶剂抽真空去除,制备得组分b;
72.(4)将步骤(1)制备得到的组分a1和组分a2混合均匀后加入到步骤(3)所得的组分b中,在50℃反应条件下反应7h,反应结束后冷凝切片,即制备得到降粘型固体聚羧酸减水剂。
73.对比例4:
74.一种降粘型固体聚羧酸减水剂的制备方法,包括如下步骤:
75.(1)在制备组分a1和组分a2时均采用分子量为3000的聚乙二醇单甲基醚为原料,制备方法均如下,将131g二环己基甲烷二异氰酸酯与0.05g三亚乙基二胺混合均匀得到混合液,随后把1500g分子量为3000的聚乙二醇单甲基醚加入到混合溶液中,在120℃反应条件下反应7h至反应结束后,得到组分a1、组分a2;
76.(3)将1.9g链转移剂巯基丙酸、4.56g引发剂过硫酸铵加入到332gn,n-二甲基甲酰胺中搅拌均匀形成打底液,随后将432g丙烯酸与130g甲基丙烯酸羟乙酯混合后缓慢滴加到打底液中,滴加时间控制在3h,在70℃反应条件下,反应2h后,停止反应并将溶剂抽真空去
除,制备得组分b;
77.(4)将步骤(1)制备得到的组分a1和组分a2混合均匀后加入到步骤(3)所得的组分b中,在50℃反应条件下反应7h,反应结束后冷凝切片,即制备得到降粘型固体聚羧酸减水剂
78.对比例5:
79.一种降粘型固体聚羧酸减水剂的制备方法,包括如下步骤:
80.(1)将131g二环己基甲烷二异氰酸酯与0.05g三亚乙基二胺混合均匀得到混合液,随后把250g分子量为500的聚乙二醇单甲基醚加入到混合溶液中,在120℃反应条件下反应7h至反应结束后,得到组分a1;
81.(2)将131g二环己基甲烷二异氰酸酯与0.53g三亚乙基二胺混合均匀得到混合液,随后把1500g分子量为3000的聚乙二醇单甲基醚加入到混合溶液中,在120℃反应条件下反应7h至反应结束后,得到组分a2;
82.(3)将1.9g链转移剂巯基丙酸、4.56g引发剂过硫酸铵加入到332gn,n-二甲基甲酰胺中搅拌均匀形成打底液,随后将432g丙烯酸与130g甲基丙烯酸羟乙酯混合后缓慢滴加到打底液中,滴加时间控制在3h,在70℃反应条件下,反应2h后,停止反应并将溶剂抽真空去除,制备得组分b;
83.(4)将步骤(1)制备得到的组分a1和步骤(2)制备得到的组分a2混合均匀后加入到步骤(3)所得的组分b中,在50℃反应条件下反应7h,反应结束后冷凝切片,即制备得到降粘型固体聚羧酸减水剂。
84.对比例6:
85.一种降粘型固体聚羧酸减水剂的制备方法,包括如下步骤:
86.(1)将131g二环己基甲烷二异氰酸酯与0.05g三亚乙基二胺混合均匀得到混合液,随后把1000g分子量为2000的聚乙二醇单甲基醚加入到混合溶液中,在120℃反应条件下反应7h至反应结束后,得到组分a1;
87.(2)将131g二环己基甲烷二异氰酸酯与0.53g三亚乙基二胺混合均匀得到混合液,随后把3500g分子量为7000的聚乙二醇单甲基醚加入到混合溶液中,在120℃反应条件下反应7h至反应结束后,得到组分a2;
88.(3)将1.9g链转移剂巯基丙酸、4.56g引发剂过硫酸铵加入到332gn,n-二甲基甲酰胺中搅拌均匀形成打底液,随后将432g丙烯酸与130g甲基丙烯酸羟乙酯混合后缓慢滴加到打底液中,滴加时间控制在3h,在70℃反应条件下,反应2h后,停止反应并将溶剂抽真空去除,制备得组分b;
89.(4)将步骤(1)制备得到的组分a1和步骤(2)制备得到的组分a2混合均匀后加入到步骤(3)所得的组分b中,在50℃反应条件下反应7h,反应结束后冷凝切片,即制备得到降粘型固体聚羧酸减水剂。
90.将通过实施例1-6、对比例1-6制备得到的降粘型固体聚羧酸减水剂配成50%含固量的溶液,与市售含固量为50%的聚羧酸减水剂进行砂浆流动度及混凝土新拌性能对比。水泥砂浆流动度测试参照gb/t8077—2012《混凝土外加剂匀质性试验方法》,结果见表1。采用海螺牌p.o42.5r级普通硅酸盐水泥,水灰质量比w/c=0.33,减水剂掺量(以水泥质量为基准)为折固掺量(按固含量折算后的量添加)。混凝土新拌性能参照gb/t50080-2016《普通
混凝土拌合物性能试验方法标准》,结果见表2,混凝土坍落度控制在200-220mm,用倒置坍落度筒法试验来测试混凝土的粘度,混凝土流出倒置坍落度筒的用时越小,表示混凝土的粘度越小。混凝土基础组分配合比为:水泥220kg/m3、粉煤灰80kg/m3、矿粉90kg/m3、砂780kg/m3、石子1080kg/m3、水170kg/m3,水泥为海螺水泥p.o42.5r。
91.表1砂浆分散性能:
[0092][0093][0094]
表2混凝土新拌性能:
[0095][0096]
结论:由表1和表2的测试结果可知,通过实施例1-6制备得到的固体聚羧酸减水剂以及市售减水剂的对比看出本发明合成的固体聚羧酸减水剂相比于市售减水剂具有更大的初始减水、粘性及保坍性能;在控制混凝土初始性能相当的情况下,相比于市售减水剂,本发明合成的聚羧酸减水剂能够有效降低混凝土的粘度,混凝土的和易性有明显改善,有利于商品混凝土的施工。同时实施例1、对比例1、对比例2之间的测定结果表明,对比例2选用长链聚醚分子制备得到的固体聚羧酸减水剂具有足够的减水性能、但是固体聚羧酸的减
水剂的粘性差于实施例1通过长短聚醚的配合来制备得到的固体聚羧酸减水剂的粘性,不利于商品混凝土的施工;对比例1选用短链聚醚分子制备得到的固体聚羧酸减水剂的粘性较好但是减水性能不足;因此可以看出选用两种不同长度的聚醚分子来制备聚羧酸减水剂,可以通过长短聚醚的配合来增强减水剂分子的降粘性能,改善聚羧酸减水剂的适应性,同时保证减水剂的减水性能。通过实施例4与对比例3、对比例6之间的结果对比,可以看出a2组分中原料聚乙二醇单甲基醚分子量选择的合理性;实施例4与对比例4、对比例5的结果对比表明,组分a1中原料聚乙二醇单甲基醚分子量选择在600-2000之间是效果相对较好的。实施例1-6的结果表明本发明可根据实际需要做到结构性、功能性可调,得到的固体聚羧酸减水剂具有优异的减水保坍性能,且能够有效的降低混凝土的粘度,有利于混凝土的施工,同时制备工艺绿色环保,明显有利于大规模工业化生产。本发明合成方法与传统方法相比,反应所需原料常见易得,整个合成过程简单可控、高效便捷,反应所用步骤也均为普通操作工艺,无需特殊操作或昂贵助剂,反应条件温和,工艺绿色环保,因此易于实现工业化生产;该合成过程对设备无特殊要求,且具有分子可设计能力强、分子量可控、性能好等优点,具有很好的推广潜力和应用价值。
[0097]
尽管已经示出和描述了本发明的实施例,对于本领域的普通技术人员而言,可以理解在不脱离本发明的的原理和精神的情况下可以对这些实施例进行多种变化、修改、替换和变型,本发明的范围由所附权利要求及其等同物限定。