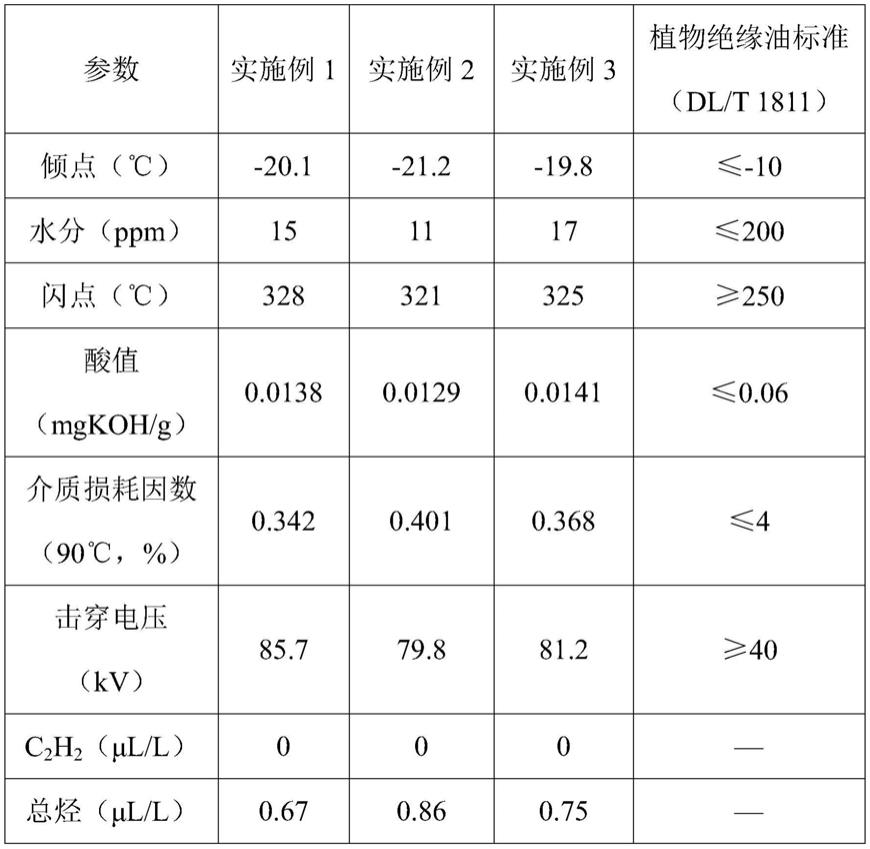
1.本发明属于植物绝缘油技术领域,具体涉及植物绝缘油精炼技术领域,特别涉及一种基于短时超声分散技术的间歇式植物绝缘油精炼工艺。
背景技术:2.作为电网核心设备,油浸式变压器通常采用矿物绝缘油作为冷却绝缘介质,但矿物绝缘油属于不可再生资源,存在不易降解、燃点低且难以回收等缺点,随着每年万吨废旧变压器油的回收难题、变压器漏油引起的环境污染、石油资源短缺及变压器故障引起的大面积停电等问题日益凸显,传统的矿物绝缘油已无法满足新形势下绿色电网对电气设备的要求。
3.植物绝缘油作为一种高燃点、可降解的环保型难燃液体电介质,被认为是矿物绝缘油的良好替代品,符合我国节能减排、低碳经济和电力工业绿色创新发展的趋势。现在挂网运行的植物绝缘油变压器已超过200万台,正逐步应用于大型油浸式电力变压器中,已经取得了良好的环境、经济和社会效益。
4.植物绝缘油精炼工艺是在传统食用油精炼工艺基础上发展起来的,但是目前国内植物绝缘油精炼工艺尚不成熟。现有的传统植物油精炼工艺主要针对食用植物油的精炼,无法突破植物绝缘油酸值和介质损耗因数难以降低的技术瓶颈。传统的植物油精炼工艺主要是采用碱炼脱酸工艺(一次碱中和及一次水洗工艺),然后进行脱色、脱臭、脱水后加入抗氧化剂即可,仅可以满足人们对食用油品质的要求,但是无法满足绝缘液体的技术要求。传统的精炼工艺存在着以下不足:
5.(1)酸值较高:传统精炼工艺制备的植物油只能满足食用植物油卫生标准的要求。对于未使用过的植物绝缘油酸值要求≤0.06mgkoh/g,但是目前大多数的一级食用植物油酸值要求≤0.2mgkoh/g,远不能达到植物绝缘油的技术要求。酸值高会降低植物绝缘油绝缘强度,加速变压器中绝缘材料老化,进而缩短变压器使用寿命。
6.(2)介质损耗因数较高:介质损耗因数反映了植物绝缘油精炼程度的好坏,油中残留的有机酸、金属粒子、胶体、微生物及其它极性杂质含量越少,介质损耗因数越小,绝缘性能也就越好。未使用过的植物绝缘油介质损耗因数要求≤4%,但是食用植物油精炼工艺并没有考虑改善植物油的电气性能,大多数一级食用油介质损耗因数往往大于10%,甚至可以达到50%以上,无法满足植物绝缘油的电气绝缘要求。
7.(3)水分较高:绝缘油中的含水量是衡量电力变压器绝缘效果的重要参数。当绝缘油中的含水量超过一定值,局部放电起始电压和击穿强度也随绝缘系统含水量增加而急剧降低,对设备运行构成威胁,严重时可导致绝缘击穿、烧毁设备等重大事故。植物绝缘油明确规定投入运行前含水量≤200ppm。现有的传统食用油精炼工艺可以有效地降低植物绝缘油中的水分,但是并不能满足植物绝缘油对含水量的要求。
8.中国专利cn104232302a公开了植物绝缘油处理全套工艺,该发明首先对植物油进行碱炼、水洗、脱色、脱臭处理,然后对精炼后的植物油进行过滤、脱水处理,最后脱水后的
植物油再进行吸附处理,吸附处理后脱水并加入抗氧化剂。该方法整个工艺操作周期长、工艺流程复杂、生产损耗较大,成本较高,不适合工业化生产。
9.中国专利cn108485810a公开了一种植物油的超声波辅助精炼方法,该发明在超声波辅助下对植物油进行脱酸脱色处理,之后在间歇式超声波作用下,通过两段式降温使油脂中的蜡质结晶,经过滤、脱臭得到精炼植物油。该方法只适用于食用植物油加工领域,并没有给出具体的性能指标,且植物油加工技术不考虑油品的电气绝缘性能,无法满足绝缘油的技术要求。
10.中国专利cn102222537a公开了一种用于变压器的植物绝缘油及其制备方法,该发明通过超声脱胶、超声碱炼、离心分离、交替脱色后进入真空滤油机,进行过滤除杂、脱水获得植物绝缘油。该方法仅对脱胶和碱炼过程辅以超声振荡,虽然缩短了反应时间,但是没有考虑到超声能量过大会使得植物绝缘油发生裂解产生可燃有机气体等问题。
11.中国专利cn 110669583 a公开了一种以菜籽油为原料的植物绝缘油精炼工艺,该发明通过对菜籽油进行甲酯化改性并对其进行脱胶、水洗、初次脱酸、减压蒸馏、常压脱色、脱臭的初步精炼;然后对初步精炼后菜籽油进行二次碱炼脱色处理以及减压蒸馏,获得精制菜籽油;再向精制后菜籽油加入抗氧化剂和抗凝剂获得以菜籽油为原料的植物绝缘油。该方法工艺操作周期长、生产损耗较大、成本较高,而且多次碱炼过程中会产生大量废水,中性油损失较大,精炼率偏低。此外,该发明仅仅适用于菜籽油为原料的植物绝缘油精炼,且采用的“甲酯化”已经涉及到化学改性,精炼得到的改性植物绝缘油在性能和成分组成上与非改性植物绝缘油存在着质的区别。
技术实现要素:12.针对现有技术中存在的不足,本发明的目的是提供一种基于短时超声分散技术的间歇式植物绝缘油精炼工艺。该工艺不同的工序阶段均采用了短时间歇式超声分散技术,有效提高了植物绝缘油的精炼效果,而且精炼后的植物绝缘油性能优良、稳定性好。
13.为了实现上述发明目的,本发明采用如下技术方案:
14.一种基于短时超声分散技术的间歇式植物绝缘油的精炼工艺,包括以下工序:a)碱炼脱酸;b)真空脱色、脱臭;c)萃取脱酸;d)真空过滤;e)干法分提。
15.进一步的,一种基于短时超声分散技术的间歇式植物绝缘油精炼工艺,包括以下步骤:
16.a)碱炼脱酸处理,操作步骤如下:
17.1)首先在搅拌条件下将植物油加热并进行超声处理,然后加入碱液,延时停止超声处理后,持续进行搅拌,静置一段时间后排出所述植物油底部的皂脚;
18.2)在搅拌条件下将所述步骤1)中去除皂脚后的植物油进行加热和超声处理,加入纯水后停止超声并持续进行搅拌,静置一段时间后排出所述植物油底部的废水;
19.3)重复步骤2)直至步骤2)中排放的废水ph值在7~7.5之间,然后在真空和搅拌条件下将所述植物油加热并进行真空脱水处理;
20.b)真空脱色、脱臭处理,操作步骤如下:
21.向所述步骤a)经过真空脱水后的植物油中加入复合脱色剂进行脱色处理,同时进行间歇式超声处理,持续搅拌一定时间后进行真空过滤,然后将经过真空过滤后的植物油
加热升温,进行真空脱臭处理;
22.c)萃取脱酸处理,操作步骤如下:
23.将所述步骤b)经过真空脱色、脱臭处理后的植物油在搅拌条件下进行降温,然后加入与所述植物油相同温度的乙醇溶液进行萃取处理,同时进行间歇式超声处理,持续搅拌一定时间后静置,排去所述植物油中的乙醇废液,在一定真空和搅拌条件下将所述植物油加热去除其中残留的乙醇溶液;
24.d)真空过滤处理,操作步骤如下:
25.在搅拌条件下,提高真空度将所述步骤c)经过萃取脱酸处理后的植物油进行双级真空循环脱水,同时进行间歇式超声处理,直至所述植物油中水分低于20ppm后停止超声,采用精滤滤芯对所述植物油进行循环过滤,然后真空冷却至室温;
26.e)干法分提处理,操作步骤如下:
27.在搅拌条件下,将所述步骤d)经过真空过滤处理后的植物油缓慢冷却,同时进行间歇式超声处理,冷却至一定温度后持续养晶,然后在搅拌条件下将所述植物油继续进行缓慢冷却,恒温结晶完成后进行恒温过滤,即得到本发明所述的精炼植物绝缘油。
28.进一步的,一种基于短时超声分散技术的间歇式植物绝缘油精炼工艺,包括以下步骤:
29.a)碱炼脱酸处理,具体操作步骤如下:
30.1)首先在50~60r/min的搅拌条件下将植物油加热至60~70℃开始进行超声处理,然后在5~7min内加入高于所述植物油温度3~5℃的naoh溶液,添加所述naoh溶液结束1min后停止超声处理,维持50~60r/min的转速持续搅拌8~10min后,将转速降至25~30r/min再持续搅拌25~30min,静置8h,排出所述植物油底部的皂脚;
31.2)在50~60r/min的搅拌条件下,将步骤1)中去除皂脚后的植物油加热至82~85℃开始进行超声处理,然后在8min内加入高于所述植物油温度8~10℃的纯水,所述纯水添加结束后停止超声处理,维持50~60r/min的转速持续搅拌8~10min,静置2h,排出所述植物油底部的废水;
32.3)重复步骤2)直至步骤2)中排放的废水ph值在7~7.5之间,然后在真空和搅拌条件下,将所述植物油加热至93~95℃进行真空脱水处理;
33.b)真空脱色、脱臭处理,操作步骤如下:
34.向所述步骤a)经过真空脱水后的植物油中加入复合脱色剂进行脱色处理,同时进行间歇式超声处理10~15min,持续搅拌10~12min后进行真空过滤,然后将经过真空过滤后的植物油加热至238~242℃进行真空脱臭处理;
35.c)萃取脱酸处理,操作步骤如下:
36.将所述步骤b)经过真空脱色、脱臭处理后的植物油在80~100r/min的搅拌条件下降温至45~48℃,然后加入与所述植物油相同温度的体积浓度为85%以上的乙醇溶液进行萃取处理,同时进行间歇式超声处理5~8min,持续搅拌10~15min后静置3~4h,排去所述植物油中的乙醇废液,然后在3000~3500pa、80~100r/min的条件下,将植物油加热至68~72℃去除所述植物油中残留的乙醇溶液;
37.d)真空过滤处理,操作步骤如下:
38.维持80~100r/min的搅拌条件,提高真空度至15~30pa将所述步骤c)经过萃取脱
酸处理后的植物油进行双级真空循环脱水,同时进行间歇式超声处理,直至所述植物油中的水分低于20ppm后停止超声处理,采用孔径为0.5μm的精滤滤芯对所述植物油进行循环过滤,然后真空冷却至室温;
39.e)干法分提处理,操作步骤如下:
40.在8~10r/min的搅拌条件下,将所述步骤d)经过真空过滤处理后的植物油缓慢冷却,同时进行间歇式超声处理,冷却至3~5℃后持续养晶8~10h,然后在2~5r/min的搅拌条件下将所述植物油继续缓慢冷却至
‑
3~
‑
1℃,恒温结晶12~16h后进行恒温过滤,即得到本发明所述的精炼植物绝缘油。
41.进一步的,所述工序a)中步骤2)加入纯水的用量为所述植物油油重的12~15%;所述步骤3)中的真空度为
‑
0.098~
‑
0.1mpa,搅拌转速为50~60r/min。
42.进一步的,所述工序a)中步骤1)和步骤2)超声处理条件为:功率100~120w,频率20~24khz。
43.进一步的,所述工序b)中的复合脱色剂用量为所述植物油重的2.3~2.5%;所述复合脱色剂由占所述植物油油重0.15%的硅胶、0.85%的硅藻土和1.3~1.5%的活性白土组成;所述间歇式超声处理条件为:功率200~240w,频率16~20khz,采用“超声分散60~80s,停止80~100s”的循环模式。
44.进一步的,所述工序c)中植物油与乙醇溶液的用量比为1g:5.5~6ml。
45.进一步的,所述工序c)中间歇式超声处理条件为:功率160~200w,频率20~24khz,采用“超声分散30s,停止30s”的循环模式。
46.进一步的,所述工序d)中间歇式超声处理条件为:功率60~100w,频率16~20khz,采用“超声分散60~90s,停止60s”的循环模式。
47.进一步的,所述工序e)中间歇式超声处理条件为:功率150~180w,频率16~18khz,处理时间600~900s,采用“超声分散6~10s,停止60~90s散的循环模式。
48.与现有技术相比,本发明具备的有益效果在于:
49.1)脱酸过程中,利用超声波次级效应产生的强烈振动和搅拌作用,可使得植物油中的游离脂肪酸与碱液和乙醇溶液接触的更加充分,缩短了反应时间,可将植物油酸值降至极低水平。此外,采用“碱炼脱酸+萃取脱酸”相结合的深度脱酸方式克服了传统多次碱炼脱酸工艺造成的大量皂脚和废水的排放问题,也避免了高温脱酸时植物油因高温发生聚合、脱羧和裂解等副反应的问题,减少了中性油的损失,降低了生产成本,完全避免了单纯采用碱炼脱酸、萃取脱酸或物理脱酸的工艺缺陷,脱酸效果更加明显。
50.2)脱色过程中,采用超声波处理有效提高了复合脱色剂在植物油中的均匀分散程度,使其与植物油中的色素接触更加充分,同时采用了硅胶、硅藻土和活性白土三种脱色剂复配技术,三种脱色剂之间的协同增效大幅提升了脱色效果,而且脱色剂添加比例较少,进一步降低了成本,也避免了白土过量添加造成的植物油酸值回升、加速植物油氧化回色等问题。
51.3)真空过滤过程中,采用机械搅拌与超声振荡相结合的方式可增强破乳能力,有效提高脱水的效果,大大缩短脱水时间,而且通过对超声处理参数的精准控制,有效避免了因能量过大导致植物油裂解产生ch4、c2h4等可燃有机气体的问题。
52.4)干法分提过程中,通过对冷却速度、结晶温度、结晶时间及搅拌速率等工艺参数
的精准控制,结合间歇式超声分散处理,能够促进缓慢降温过程中结晶体的形成与均匀长大,使结晶体具有良好的均匀性、稳定性和过滤性,进而加快干法分提的速度,有效降低植物绝缘油中高熔点甘油酯和蜡的含量,显著提升植物绝缘油的低温特性。
53.5)本发明不同工艺阶段均采用了短时间歇式超声分散技术,有效提高了植物绝缘油的精炼效果,减少了碱液、脱色剂和萃取剂等消耗品的用量,简化了工艺流程,降低了生产成本,制备的植物绝缘油性能优良且稳定性好,技术优势显著,易于工业化推广。
具体实施方式
54.下面结合具体实施例,对本发明作进一步详细的阐述,但本发明的实施方式并不局限于实施例表示的范围。这些实施例仅用于说明本发明,而非用于限制本发明的范围。
55.实施例1:
56.一种基于短时超声分散技术的间歇式植物绝缘油精炼工艺,包括以下步骤:
57.a)碱炼脱酸处理,具体操作步骤如下:
58.1)首先在60r/min的搅拌条件下将植物油加热至62℃,开始在功率100w、频率24khz条件下进行超声处理,然后在5min内加入高于所述植物油温度3℃的naoh溶液,所述naoh溶液添加结束1min后停止超声处理,维持60r/min的转速持续搅拌10min后,将转速降至25r/min再持续搅拌30min,静止8h,排出所述植物油底部的皂脚;
59.2)在60r/min的搅拌条件下,将步骤1)中去除皂脚后的植物油加热至85℃后在功率120w、频率22khz的条件下进行超声处理,然后在8min内加入高于所述植物油温度8℃的纯水,所述纯水用量为所述植物油油重的12%,所述纯水添加结束后停止超声,维持60r/min的转速持续搅拌10min,静置2h,排出所述植物油底部的废水;
60.3)重复步骤2)直至步骤2)中排放的废水ph值在7~7.5之间,然后在
‑
0.1mpa的真空度和60r/min的搅拌条件下,将所述植物油加热至95℃进行真空脱水处理;
61.b)真空脱色、脱臭处理,具体操作步骤如下:
62.向所述步骤a)经真空脱水后的植物油中加入占所述植物油油重2.5%的复合脱色剂(其中硅胶占植物油油重比例0.15%、硅藻土占植物油油重比例0.85%、活性白土占植物油油重比例1.5%)进行脱色处理,同时采用“超声分散60s,停止80s”的循环模式进行间歇式超声处理12min,其超声功率200w,超声频率20khz,持续搅拌12min后进行真空过滤,然后将经过真空过滤后的植物油加热至242℃进行真空脱臭处理;
63.c)萃取脱酸处理,具体操作步骤如下:
64.将所述步骤b)经过真空脱色、脱臭处理后的植物油在100r/min的搅拌条件下降温至48℃,然后加入与所述植物油相同温度的体积浓度为85%以上的乙醇溶液进行萃取,所述植物油与乙醇溶液的用量比为1g:6ml,同时采用“超声分散30s,停止30s”的循环模式进行间歇式超声处理8min,其超声功率180w,超声频率24khz,持续搅拌10min后静置4h,排去所述植物油中的乙醇废液;在3000pa和100r/min的条件下,将所述植物油加热至72℃去除其中残留的乙醇溶液;
65.d)真空过滤处理,具体操作步骤如下:
66.维持100r/min的搅拌条件,提高真空度至25pa将所述步骤c)经过萃取脱酸处理后的植物油进行双级真空循环脱水,同时采用“超声分散60s,停止60s”的循环模式进行间歇
式超声处理,其超声功率80w,超声频率20khz,直至所述植物油中的水分低于20ppm后停止超声处理,然后采用孔径为0.5μm的精滤滤芯对所述植物油进行循环过滤,然后真空冷却至室温;
67.e)干法分提处理,具体操作步骤如下:
68.在10r/min的搅拌条件下将所述步骤d)经过真空过滤处理后的植物油缓慢冷却,并采用“超声分散10s,停止90s”的循环模式进行间歇式超声处理600s,其超声功率160w,超声频率18khz,冷却至5℃后持续养晶10h,然后在2r/min的搅拌条件下将所述植物油继续缓慢冷却至
‑
3℃,恒温结晶12h后进行恒温过滤,即得到本发明所述的精炼植物绝缘油。
69.实施例2
70.一种基于短时超声分散技术的间歇式植物绝缘油精炼工艺,包括以下步骤:
71.a)碱炼脱酸处理,具体操作步骤如下:
72.1)首先在50r/min的搅拌条件下将植物油加热至70℃,开始在功率120w,频率22khz条件下进行超声处理,然后在6min内加入高于所述植物油温度5℃的naoh溶液,所述naoh溶液添加结束1min后停止超声处理,维持60r/min的转速持续搅拌8min后,将转速降至30r/min再持续搅拌25min,静止8h,排出所述植物油底部的皂脚;
73.2)在50r/min的搅拌条件下,将步骤1)中去除皂脚后的植物油加热至82℃后在功率100w,频率24khz的条件下进行超声处理,然后在8min内加入高于所述植物油温度10℃的纯水,所述纯水的用量为所述植物油油重的15%,所述纯水添加结束后停止超声,维持50r/min的转速持续搅拌9min,静置2h,排出所述植物油底部的废水;
74.3)重复步骤2)直至步骤2)中排放的废水ph值在7~7.5之间,然后在
‑
0.098mpa的真空度和50r/min的搅拌条件下,将所述植物油加热至93℃进行真空脱水处理;
75.b)真空脱色、脱臭处理,具体操作步骤如下:
76.向所述步骤a)经真空脱水后的植物油中加入占所述植物油油重2.3%的复合脱色剂(其中硅胶占植物油油重比例0.15%、硅藻土占植物油油重比例0.85%、活性白土占植物油油重比例1.3%)进行脱色处理,同时采用“超声分散60s,停止100s”的循环模式进行间歇式超声处理12min,其超声功率240w,超声频率18khz,持续搅拌10min后进行真空过滤,然后将经过真空过滤后的植物油加热升温至240℃进行真空脱臭处理;
77.c)萃取脱酸处理,具体操作步骤如下:
78.将所述步骤b)经过真空脱色、脱臭处理后的植物油在80r/min的搅拌条件下降温至45℃,然后加入与所述植物油相同温度的体积浓度为85%以上的乙醇溶液进行萃取,所述植物油与乙醇溶液的用量比为1g:5.5ml,同时采用“超声分散30s,停止30s”的循环模式进行间歇式超声处理5min,其超声功率200w,超声频率20khz,持续搅拌12min后静置4h,排去所述植物油中的乙醇废液;在3300pa和80r/min的条件下,将所述植物油加热至70℃去除其中残留的乙醇溶液;
79.d)真空过滤处理,具体操作步骤如下:
80.维持80r/min的搅拌条件,提高真空度至18pa将所述步骤c)经过萃取脱酸处理后的植物油进行双级真空循环脱水,同时采用“超声分散90s,停止60s”的循环模式进行间歇式超声处理,其超声功率60w,超声频率18khz,直至所述植物油中的水分低于20ppm后停止超声处理,然后采用孔径为0.5μm的精滤滤芯对所述植物油进行循环过滤,然后真空冷却至
室温;
81.e)干法分提处理,具体操作步骤如下:
82.在8r/min的搅拌条件下将所述步骤d)经过真空过滤处理后的植物油缓慢冷却,并采用“超声分散6s,停止60s”的循环模式进行间歇式超声处理900s,其超声功率180w,超声频率16khz,冷却至3℃后持续养晶8h,然后在3r/min的搅拌条件下将所述植物油继续缓慢冷却至
‑
2℃,恒温结晶16h后进行恒温过滤,即得到本发明所述的精炼植物绝缘油。
83.实施例3
84.一种基于短时超声分散技术的间歇式植物绝缘油精炼工艺,包括以下步骤:
85.a)碱炼脱酸处理,具体操作步骤如下:
86.1)首先在50r/min的搅拌条件下将植物油加热至69℃,开始在功率120w,频率20khz条件下进行超声处理,然后在5min内加入高于所述植物油温度3℃的naoh溶液,所述naoh溶液添加结束1min后停止超声处理,维持50r/min的转速持续搅拌10min后,将转速降至25r/min再持续搅拌30min,静止8h,排出所述植物油底部的皂脚;
87.2)在50r/min的搅拌条件下,将步骤1)中去除皂脚后的植物油加热至83℃后在功率110w,频率20khz的条件下进行超声处理,然后在8min内加入高于所述植物油温度9℃的纯水,所述纯水的用量为所述植物油油重的12%,所述纯水添加结束后停止超声,维持50r/min的转速持续搅拌10min,静置2h,排出所述植物油底部的废水;
88.3)重复步骤2)直至步骤2)中排放的废水ph值在7~7.5之间,然后在
‑
0.098mpa的真空度和60r/min的搅拌条件下,将所述植物油加热至95℃进行真空脱水处理;
89.b)真空脱色、脱臭处理,具体操作步骤如下:
90.向所述步骤a)经真空脱水后的植物油中加入占所述植物油油重2.4%的复合脱色剂(其中硅胶占植物油油重比例0.15%、硅藻土占植物油油重比例0.85%、活性白土占植物油油重比例1.4%)进行脱色处理,同时采用“超声分散80s,停止80s”的循环模式进行间歇式超声处理10min,其超声功率220w,超声频率16khz,持续搅拌10min后进行真空过滤,然后将经过真空过滤后的植物油加热升温至238℃进行真空脱臭处理;
91.c)萃取脱酸处理,具体操作步骤如下:
92.将所述步骤b)经过真空脱色、脱臭处理后的植物油在100r/min的搅拌条件下降温至46℃,然后加入与所述植物油相同温度的体积浓度为85%以上的乙醇溶液进行萃取,所述植物油与乙醇溶液的用量比为1g:5.8ml,同时采用“超声分散30s,停止30s”的循环模式进行间歇式超声处理6min,其超声功率160w,超声频率24khz,持续搅拌15min后静置3h,排去所述植物油中的乙醇废液;在3500pa和100r/min的条件下,将所述植物油加热至72℃去除其中残留的乙醇溶液;
93.d)真空过滤处理,具体操作步骤如下:
94.维持100r/min的搅拌条件,提高真空度至15pa将所述步骤c)经过萃取脱酸处理后的植物油进行双级真空循环脱水,同时采用“超声分散80s,停止60s”的循环模式进行间歇式超声处理,其超声功率80w,超声频率16khz,直至所述植物油中的水分低于20ppm后停止超声处理,然后采用孔径为0.5μm的精滤滤芯对所述植物油进行循环过滤,然后真空冷却至室温;
95.e)干法分提处理,具体操作步骤如下:
96.在8r/min的搅拌条件下将所述步骤d)经过真空过滤处理后的植物油缓慢冷却,并采用“超声分散10s,停止80s”的循环模式进行间歇式超声处理720s,其超声功率150w,超声频率18khz,冷却至5℃后持续养晶10h,然后在5r/min的搅拌条件下将所述植物油继续缓慢冷却至
‑
1℃,恒温结晶16h后进行恒温过滤,即得到本发明所述的精炼植物绝缘油。
97.对比例1
98.一种植物绝缘油精炼工艺,其工艺步骤与实施例1基本相同,不同之处在于:省去工序a)中所有的超声分散处理。
99.对比例2
100.一种植物绝缘油精炼工艺,其工艺步骤与实施例1基本相同,不同之处在于:省去工序c)萃取脱酸。
101.对比例3
102.一种植物绝缘油精炼工艺,其工艺步骤与实施例1基本相同,不同之处在于:将工序b)中的脱色剂只使用活性白土,且活性白土占植物绝缘油油重比例3.0%。
103.对比例4
104.一种植物绝缘油精炼工艺,其工艺步骤与实施例1基本相同,不同之处在于:工序d)真空过滤中的间歇超声处理条件为:超声功率120w,超声频率24khz,并采用“超声分散120s,停止60s”的循环模式。
105.对比例5
106.一种植物绝缘油精炼工艺,其工艺步骤与实施例1基本相同,不同之处在于:本对比例的工序e)干法分提处理为:
107.在15r/min的搅拌条件下将所述步骤d)经过真空过滤处理后的植物油缓慢冷却,并采用“超声分散10s,停止90s”的循环模式进行间歇式超声处理600s后,其超声功率160w,超声频率18khz,冷却至8℃后持续养晶5h,然后在6r/min的搅拌条件下将所述植物绝缘油继续进行缓慢冷却至
‑
3℃,恒温结晶10h后进行恒温过滤,即得到所述产品。
108.本发明实施例1
‑
3及对比例1
‑
5制备得到的植物绝缘油的主要性能参数如表1和表2所示。
109.表1实施例1
‑
3制备的植物绝缘油主要性能参数
[0110][0111]
表2对比例1
‑
5制备的植物绝缘油主要性能参数
[0112]
[0113][0114]
从表1和表2的数据对比可以看出,对比例1
‑
3制备的植物绝缘油的酸值相较于实施例1要高,主要原因是对比例1中省去了工序a)碱炼脱酸处理中的超声处理步骤,使植物油中游离脂肪酸与碱液接触不充分,碱炼中和反应不够彻底,进而导致植物绝缘油酸值升高;对比例2中省去了工序c)萃取脱酸,使得植物油中的游离脂肪酸去除不够彻底,导致最后植物绝缘油中酸值过高(0.0765mgkoh/g),无法满足植物绝缘油的相关技术标准;对比例3中由于加入了过量的活性白土导致植物油中酸值有了一定程度的回升;对比例4中由于真空过滤时超声功率和频率的加大,导致植物油裂解产生了ch4、c2h4、c2h2等可燃气体,从而使对比例4得到的植物绝缘油中出现了c2h2,而且总烃含量明显增大;对比例5制得的植物绝缘油倾点相较于实施例1要高,导致对比例5制得的植物绝缘油低温流动性要比实施例差,这是由于对比例5在干法分提过程中改变了搅拌速度、结晶温度和结晶时间等参数,不利于低温情况下植物油中结晶体的形成与成长,晶体自身具有缺陷,无法均匀成长,且不具有良好的稳定性和过滤性。
[0115]
综上所述,本发明实施例1
‑
3制备的植物绝缘油综合性能优于对比例1
‑
5,说明本发明的工艺工序和各个工序条件参数都直接影响产品的性能。本发明的工艺工序和各个工序条件参数的合理设置,有效提高了植物绝缘油的精炼效果,显著改善了植物绝缘油的质量,减少了碱液、脱色剂和萃取剂等消耗品的用量,获得了理化、电气、热稳定性、低温流动性等综合性能优良的植物绝缘油。
[0116]
需要申明的是,以上所述实施例仅为本发明进行了详细的描述,并不是为了限制本发明的保护范围。在不脱离本发明的宗旨和范围的情况下,对本发明的技术方案进行修改或者等同替换,均应涵盖在本发明的权利要求范围之内。