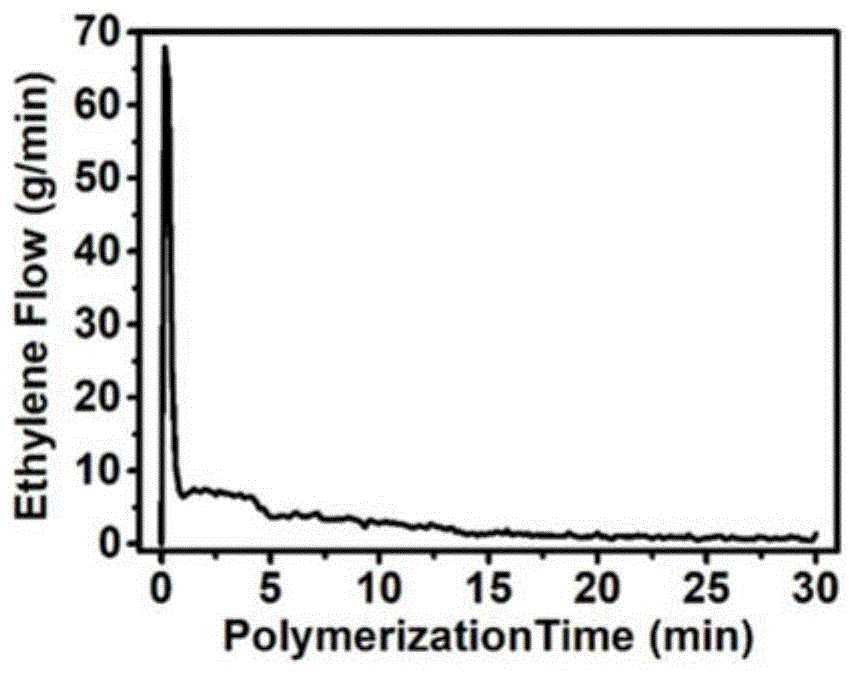
本发明属于高分子聚合物制备领域,特别涉及一种连续制备分子量分布窄、共聚单体含量高且分布均匀的聚烯烃弹性体的方法及产品。
背景技术:
:聚烯烃弹性体(poe)因为其共聚单体含量高、分子链支链链长、分子量分布窄的特点,赋予其优异的性能和产品价值。α-烯烃支链产生的柔软链卷曲结构可以形成具有橡胶弹性的无定型区(橡胶相),而聚乙烯链段的结晶区(塑料相)则起到物理交联点的作用。正是由于这种交联状态的可逆性,使得poe兼有橡胶和热塑性塑料的性质,常温下表现出橡胶的高弹性,而在高温下能够塑化成型。因此poe具有优异的耐寒性和耐老化性能、良好的力学性能和加工能力,广泛应用于汽车配件、电线电缆护套、发泡材料、增韧改性剂、透明薄膜等领域。poe弹性体的主要产品为乙烯和1-丁烯共聚物、乙烯和1-己烯共聚物及乙烯和1-辛烯共聚物,其中,乙烯和1-辛烯共聚物的性能最佳。目前,乙烯辛烯共聚物poe弹性体的生产大多采用茂金属催化剂和溶液聚合工艺。美国陶氏dow公司开发的限制几何构型催化剂(cgc催化剂)结合dowlex工艺或者insite工艺,可以生产出不同共聚单体含量、不同分子量分布、不同共聚单体分布的poe弹性体材料。然而,虽然cgc催化剂展现出极高的催化活性(高达350000kg/(mol·h),accountsofchemicalresearch,2015,48,2004和欧洲专利ep416815a2,1991),但是在溶液聚合工艺的高温条件下(120-160℃),也存在着催化剂活性衰减很快的缺点(如图1)。因此,陶氏公司的dowlex工艺中,催化剂在两个反应釜内的总停留时间不超过30min,在单一反应釜内的停留时间不超过15min,并且为了能够实现共聚单体分布和含量可调的特点,需要采用双釜串联工艺生产(如图2的dowlex工艺)。第一个反应釜温度160℃,压力2.55mpa,乙烯转化率为88%;第二个反应釜温度160℃,压力1.82mpa,乙烯转化率为50%;总停留时间为30min。陶氏dowlex工艺的双釜串联技术,在第二个反应釜中也需加入适量催化剂、乙烯、共聚单体和溶剂组分,用来提高乙烯-辛烯共聚物中的共聚单体含量。采用双釜串联工艺的目的,一是为了避免催化剂的过快失活,提升经济性,二是为了降低体系粘度、提高共聚单体在反应釜中的含量以及增强传质效应,增强催化剂的共聚效果,促进共聚单体在poe分子链的均匀分布,从而提高产品性能。上述双釜串联工艺存在的显著问题有:1)两个反应釜内物料体系粘度差别较大,乙烯和共聚单体的传质和浓度差别大;2)两个反应釜内催化剂的活性差别大;3)两个反应釜内催化剂的共聚性能差别大,poe产物分子链上共聚单体的分布不均匀;4)双釜串联易导致两个反应釜内产物物性差别较大,分子量分布变宽。微通道反应器技术可以有效增强物料体系的传质效果,并将大规模的反应过程小型化、微型化,可以生产得到纯度更高、性能更优、物性更加均衡稳定的反应产物。微通道反应器技术的组合和生产形式多样,生产单元可调节性强、组成灵活多样,可轻松实现物料体系浓度、压力、温度的快速调节,最终实现产物性质的灵活调节。出于上述问题的考虑,本发明的发明人进行了研究,目的是解决相关领域现有技术所暴露出来的问题,期望提供一种能够连续制备分子量分布窄、共聚单体含量高且分布均匀的聚烯烃弹性体的方法及产品。技术实现要素:鉴于以上现有技术的不足,本发明的目的之一在于提供一种连续制备分子量分布窄、共聚单体含量高且分布均匀的聚烯烃弹性体的方法,其不仅能够显著增强反应物料体系的混合及传质效果,还能在保持催化剂活性的基础上,增加共聚单体在共聚物中的含量、且共聚单体在共聚物分子链上的分布更加均匀。利用本方法所制备的聚合物还具有分子量分布窄的特点,该聚合物可以广泛应用于乙烯基聚合物或丙烯基聚合物的增强增韧改性。本发明的另一目的在于在不改变催化剂的基础上或者催化剂在高温下失活较快的情况下,在生产工艺上实现聚烯烃弹性体性能的高端化。本发明所述的催化剂可以选自限制几何构型催化剂(cgc催化剂)、茂金属催化剂、后过渡金属催化剂、半茂金属催化剂和ziegler-natta催化剂中的一种或者多种。相应的,本发明所述的助催化剂可以选自三乙基铝、三丙基铝、三正丁基铝、三异丁基铝、三正己基铝、三正辛基铝、甲基铝氧烷、改性甲基铝氧烷、三(五氟苯基)硼、三苯碳四(五氟苯基)硼酸盐等硼酸盐中的一种或多种。本发明所述的微通道反应器技术制备聚烯烃弹性体的方法,基于微通道反应器内极佳的传热和传质能力,具有反应单体消耗速率快、易于温度控制的特点,因此特别适合于催化活性释放快(无等待期)、活性高且活性失活较快的催化体系,与环管反应器所采用的慢失活、高活性催化体系具有本质区别。根据本发明的一个方面,本发明提供了一种连续制备分子量分布窄、共聚单体含量高且分布均匀的聚烯烃弹性体的方法,其特征在于采用微通道反应器技术,具体包括如下步骤:1)催化剂及助催化剂在溶剂中先进行预混合溶解并活化得到预混合溶液a;乙烯单体与溶剂进行预混合预溶解得到预混合溶液b,共聚单体与溶剂进行预混合预溶解得到预混合溶液c;2)预混合溶液a、预混合溶液b和预混合溶液c经过预加热处理达到各自的预设定温度,再经过微混合装置ⅰ进行微混合,微混合后的溶液体系增压至1-15mpa压力,并被分散至一个或多个聚合基础单元进行聚合反应;3)每个聚合基础单元内具有多个乙烯补充注入点和多个共聚单体补充注入点,聚合基础单元内物系温度为80-200℃,体系压力为1-15mpa,反应物料在单个聚合基础单元内的总停留时间为3-180min,反应物料在相邻两个共聚单体补充注入点之间的停留时间为0.5-25min,反应物料在相邻两个乙烯补充注入点之间的停留时间为0.5-20min;4)聚合基础单元生产得到的乙烯聚合物溶液进行脱气和脱溶剂,再经造粒得到最终产品。根据本发明的一个实施例,所述溶剂选自甲苯、二甲苯、乙苯、二乙苯、己烷、庚烷、戊烷、环己烷、辛烷、壬烷、癸烷、isopare等线性烷烃或异构烷烃中的一种或多种。所述溶剂可以根据共聚物特性进行不同比例的掺混调节,调节的目的是为了提高共聚物在溶剂中的溶解度,降低体系粘度,从而降低微通道反应器管路内发生堵塞的可能性。根据本发明的一个实施例,所述共聚单体选自丙烯、1-丁烯、1-戊烯、1-己烯、1-庚烯、1-辛烯、1-壬烯、1-癸烯、醋酸乙烯酯、乙烯醇、丙烯酸乙酯、1,4-丁二烯、戊二烯中的一种或多种。所述共聚单体优选为1-丁烯、1-己烯、1-辛烯和1-癸烯中的一种或多种。更优选为1-丁烯、1-己烯和1-辛烯中的一种或多种。由此可以制备得到侧链为长支链的烯烃共聚物,所述烯烃聚合物具有更好的弹性和韧性。根据本发明的一个实施例,所述聚合基础单元为微通道反应器单元;聚合基础单元的反应物料温度控制为110-180℃,优选为115-165℃。由此可以在高温下以溶液状态制备长支链的烯烃共聚物,提高聚合温度可以显著降低反应物系的粘度,增强各个物系的传质效果,这种溶液法工艺可以连续制备长支链的烯烃共聚物,提高生产效率。根据本发明的一个实施例,所述聚合基础单元为微通道反应器单元;聚合基础单元的反应体系压力控制为1-10mpa,优选为1.2-7mpa,更优选为1.5-5mpa。由此可以在高温下尽量提高催化剂的催化活性,降低产物中的催化剂和助催化剂灰分,提高产品质量和应用范围。根据本发明的一个实施例,所述反应物料在单个聚合基础单元内的总停留时间为3-150min,优选为5-100min,更优选为10-60min。由此可以延长催化剂的聚合生命周期,可以尽量提高催化剂的催化活性,降低产物中的催化剂和助催化剂灰分含量,提高产品质量和应用范围。根据本发明的一个实施例,所述反应物料在相邻两个共聚单体补充注入点之间的停留时间为2-20min,优选为4-18min;反应物料在相邻两个乙烯补充注入点之间的停留时间为1-15min,优选为1-10min。由此,在整个聚合基础单元(微通道反应器单元)内,可以多次对消耗量大的乙烯和共聚单体组分进行补充,并利用微通道反应器进行高效混合,以达到增强传质和稳定反应物系内各反应物浓度的作用,使得共聚单体在各个乙烯或共聚单体补充注入点之间的浓度保持稳定,且共聚单体在各个乙烯或共聚单体补充注入点之间参加共聚反应的比例保持稳定,从而可以保持烯烃共聚物分子链上共聚单体的均匀分布和分子量窄分布特点。根据本发明的一个实施例,所述聚合基础单元为微通道反应器单元,单个微通道反应器单元的长度为100-50000m,优选为500-30000m;微通道反应器单元的内径范围为0.5-5mm,优选为0.7-3mm;反应物料在微通道反应器单元的运动速度为1-15m/s,优选为2-10m/s;微通道反应器单元所采用的管道横截面为圆形;微通道反应器管道为弯管与直管的组合,或弯管与弯管的组合,弯管部分反应物料进口方向与出口方向的夹角为60-180°,优选为90-180°。根据本发明的一个实施例,所述聚合基础单元为微通道反应器单元,单个微通道反应器单元的各项可调节参数可以根据产物需要单独设定,如反应物料温度、压力、总停留时间、相邻两个共聚单体补充注入点的距离、相邻两个乙烯补充注入点的距离、微通道反应器长度、内径和反应物料的运动速度等。由此可以制备得到一系列不同共聚单体含量、不同分子量分布、不同共聚单体插入率、不同熔融指数、不同拉伸强度、不同拉伸模量、不同冲击强度等特性的乙烯共聚物,这些乙烯共聚物可以采用多个聚合基础单元,实现不同比例的共混,以实现不同特性产品的定制和多牌号开发。根据本发明的一个实施例,所述每个聚合基础单元内相邻两个共聚单体补充注入点的距离或相邻两个乙烯补充注入点的距离可以等距排列或者非等距排列。根据本发明的一个实施例,所述聚合基础单元内相邻两个共聚单体补充注入点的共聚单体注入量为前一段共聚单体消耗量的40-180wt%,优选为70-130wt%,更优选为80-110wt%;相邻两个乙烯补充注入点的乙烯注入量为前一段乙烯消耗量的30-200wt%,优选为50-150wt%,更优选为80-120wt%。由此,可以保持共聚单体在各个乙烯或共聚单体补充注入点之间参加共聚反应的比例保持稳定,从而可以制备共聚单体均匀分布和分子量窄分布的烯烃共聚物。根据本发明的一个实施例,所述聚合基础单元的材料选自塑料材料、或塑料材料与玻璃、不锈钢、铝镁合金、陶瓷的组合材料;所述塑料材料选自聚四氟乙烯(ptfe)、乙烯-四氟乙烯共聚物(etfe)、少量全氟丙基全氟乙烯基醚与聚四氟乙烯的共聚物(pfa)或全氟乙烯丙烯共聚物(fep)中的一种或多种。根据本发明的一个实施例,当所述聚合基础单元有多个时,每个聚合基础单元生产得到的乙烯聚合物溶液经过微混合装置ⅱ混合再进行脱气和脱溶剂;脱气和脱溶剂处理得到的气体和溶剂经过纯化再生后循环利用。本发明采用的方法制备的聚乙烯弹性体,其呈现出共聚单体含量高、分子量分布窄、共聚单体在聚乙烯链段分布均匀的特点,聚乙烯弹性体中共聚单体含量为1-25mol%,优选3-20mol%;分子量分布为1.1-2.9,优选为1.2-2.7。本发明采用的方法制备的聚乙烯弹性体,可以被广泛应用于乙烯基聚合物或丙烯基聚合物的增强增韧改性。附图说明为了更清楚地说明本发明实施例中的技术方案,下面将对实施例描述中所需要使用的附图做简单地介绍,显而易见,下面简述中的附图仅仅是本发明的一些实施例,对于本领域普通技术人员来讲,在不付出创造性劳动的前提下,还可以根据这些附图获得其他的附图。图1表示cgc催化剂的催化动力学曲线;图2表示dow公司dowlex溶液聚合工艺流程图;图3表示本发明方法的一个实施例中使用的cgc催化剂结构图;图4表示为本发明方法的实施例中使用的聚烯烃弹性体在微通道反应器技术(包含微混合装置ⅰ)中连续制备的工艺流程图,其中下列组分的预混合和预加热过程并未在图中有所展示,包括:催化剂及助催化剂在溶剂中进行预混合溶解并活化得到预混合溶液a;乙烯单体与溶剂进行预混合预溶解得到预混合溶液b,共聚单体与溶剂进行预混合预溶解得到预混合溶液c;。图5表示为本发明方法的一个实施例中使用的多个聚合基础单元并联的微通道反应器技术及微混合装置ⅱ示意图。图6表示为本发明方法的一个实施例中使用的聚合基础单元中微通道反应器的结构示意图,微通道反应器结构为直管部分和弯管部分的组合(乙烯和共聚单体补充注入点未在图上有所显示)。图7表示为本发明方法的另一个实施例中使用的聚合基础单元中微通道反应器的结构示意图,微通道反应器结构为弯管部分和弯管部分的组合(乙烯和共聚单体补充注入点未在图上有所显示)。具体实施方式下面将结合实施例对本发明的实施方案进行详细描述,但是本领域技术人员将会理解,下列实施例仅用于说明本发明,而不应视为限定本发明的范围。实施例中未注明具体条件者,按照常规条件或制造商建议的条件进行。所用试剂或仪器未注明生产厂商者,均为可以通过市购获得的常规产品。聚合物结构及性能的表征方法(1)熔融指数:根据gb/t-3682-2000条件(190℃、2.16kg的负荷)测定熔体流动速率,通常记为mi2.16。(2)密度:根据gb/1033-1986方法测定。(3)拉伸强度、杨氏模量和断裂伸长率:根据gb/t1040-2006测定。(4)重均分子量及分子量分布:采用高温渗透凝胶色谱ht-gpc测定。(5)共聚单体插入率:根据13c-nmr测定并计算。(6)熔点和结晶度:采用差式扫描量热仪dsc测定。实施例1本实施例采用微通道反应器技术,微通道反应器的流程和结构如图4、图5和图6所示。详细地,本实施例采用的催化剂为图3所示cgc催化剂,助催化剂为硼烷、助催化剂的[al]/[ti]比为6,溶剂为isopare异构烷烃,聚合温度为125℃,压力为2.3mpa,共聚单体为1-辛烯,初始加入量为200ml,反应物料在微通道反应器内的总停留时间为60min,反应物料在相邻两个共聚单体补充注入点之间的停留时间为12min,反应物料在相邻两个乙烯补充注入点之间的停留时间为8min。因此,本实施例中共聚单体补充注入点有4个,乙烯补充注入点有7个,具体的共聚单体和乙烯注入量见表1。聚合基础单元(微通道反应器单元)的长度为1000m,内径为0.9mm,反应物料在微通道反应器单元的运动速度为5m/s,微通道反应器单元所采用的管道横截面为圆形;微通道反应器管道为弯管与直管的组合,弯管部分反应物料进口方向与出口方向的夹角为120°。本实施例中微通道反应器单元内相邻两个共聚单体补充注入点的距离或相邻两个乙烯补充注入点的距离等距排列,且本实施例采用三个并联的聚合基础单元(微通道反应器单元)作为聚合总单元。本实施例采用的聚合基础单元(微通道反应器单元)材质为钢衬pfa。本实施例基于微通道反应器技术,具体过程如下:(1)cgc催化剂及助催化剂硼烷在isopare溶剂中先进行预混合溶解并活化得到预混合溶液a;乙烯单体与isopare溶剂进行预混合预溶解得到预混合溶液b,共聚单体与isopare溶剂进行预混合预溶解得到预混合溶液c;(2)预混合溶液a、预混合溶液b和预混合溶液c经过微混合器进行微混合,微混合后的溶剂体系增压至2.3mpa压力,且微混合后的溶液体系再经过多级微混合器分散至3个并联的聚合基础单元(微通道反应器单元)进行聚合反应;(3)经过3个并联的聚合基础单元生产得到的乙烯聚合物溶液再经过微混合装置ⅱ混合进入到后续的脱气&脱溶剂装置,再经过造粒装置得到最终产品。本实施例制备的聚乙烯弹性体产品编号为a,产品各项性质见表5。表1注入点序号1234567乙烯注入量ml151512121110101-辛烯注入量ml30302828///实施例2本实施例采用微通道反应器技术,微通道反应器的流程和结构如图4、图5和图7所示。详细地,本实施例采用的催化剂为图3所示cgc催化剂,助催化剂为硼烷、助催化剂的[al]/[ti]比为5,溶剂为戊烷和己烷混合物,重量比为1:1,聚合温度为130℃,压力为2.6mpa,共聚单体为1-己烯和1-辛烯(重量比为1:6),初始加入量为220ml,反应物料在微通道反应器内的总停留时间为75min,反应物料在相邻两个共聚单体补充注入点之间的停留时间为12min,反应物料在相邻两个乙烯补充注入点之间的停留时间为12min。因此,本实施例中共聚单体补充注入点有6个,乙烯补充注入点有6个,具体的共聚单体和乙烯注入量见表2。聚合基础单元(微通道反应器单元)的长度为1500m,内径为1mm,反应物料在微通道反应器单元的运动速度为4.5m/s,微通道反应器单元所采用的管道横截面为圆形;微通道反应器管道为弯管与弯管的组合,弯管部分反应物料进口方向与出口方向的夹角为130°。本实施例中微通道反应器单元内相邻两个共聚单体补充注入点的距离或相邻两个乙烯补充注入点的距离等距排列,且本实施例采用三个并联的聚合基础单元(微通道反应器单元)作为聚合总单元。本实施例采用的聚合基础单元(微通道反应器单元)材质为钢衬ptfe。本实施例基于微通道反应器技术,具体过程如下:(1)cgc催化剂及助催化剂硼烷在戊烷和己烷混合溶剂中先进行预混合溶解并活化得到预混合溶液a;乙烯单体(b)与戊烷和己烷混合溶剂进行预混合预溶解得到预混合溶液b;1-己烯和1-辛烯(c)与戊烷和己烷混合溶剂进行预混合预溶解得到预混合溶液c;(2)预混合溶液a、预混合溶液b和预混合溶液c经过微混合器进行微混合,微混合后的溶液体系增压至2.6mpa压力,且微混合后的溶液体系再经过多级微混合器分散至4个并联的聚合基础单元(微通道反应器单元)进行聚合反应;(3)经过4个并联的聚合基础单元生产得到的乙烯聚合物溶液再经过微混合装置ⅱ混合进入到后续的脱气&脱溶剂装置,再经过造粒装置得到最终产品。本实施例制备的聚乙烯弹性体产品编号为b,产品各项性质见表5。表2注入点序号123456乙烯注入量ml1717161615161-己烯/1-辛烯注入量ml383836363435实施例3本实施例采用微通道反应器技术,微通道反应器的流程和结构如图4、图5和图6所示。详细地,本实施例采用的催化剂为图3所示cgc催化剂,助催化剂为硼烷、助催化剂的[al]/[ti]比为8,溶剂为甲苯,聚合温度为135℃,压力为2.2mpa,共聚单体为1-辛烯,初始加入量为260ml,反应物料在微通道反应器内的总停留时间为48min,反应物料在相邻两个共聚单体补充注入点之间的停留时间为12min,反应物料在相邻两个乙烯补充注入点之间的停留时间为8min。因此,本实施例中共聚单体补充注入点有3个,乙烯补充注入点有5个,具体的共聚单体和乙烯注入量见表3。聚合基础单元(微通道反应器单元)的长度为1800m,内径为0.7mm,反应物料在微通道反应器单元的运动速度为6m/s,微通道反应器单元所采用的管道横截面为圆形;微通道反应器管道为弯管与直管的组合,弯管部分反应物料进口方向与出口方向的夹角为110°。本实施例中微通道反应器单元内相邻两个共聚单体补充注入点的距离或相邻两个乙烯补充注入点的距离等距排列,且本实施例采用一个单独的聚合基础单元(微通道反应器单元)作为聚合总单元。本实施例采用的聚合基础单元(微通道反应器单元)材质为钢衬ptfe。本实施例基于微通道反应器技术,具体过程如下:(1)cgc催化剂及助催化剂硼烷在甲苯溶剂中先进行预混合溶解并活化得到预混合溶液a;乙烯单体与甲苯溶剂进行预混合预溶解得到预混合溶液b;1-辛烯(与甲苯溶剂进行预混合预溶解得到预混合溶液c;(2)预混合溶液a、预混合溶液b和预混合溶液c经过微混合器进行微混合,微混合后的溶液体系增压至2.2mpa压力,且微混合后的溶液体系在单独的聚合基础单元(微通道反应器单元)进行聚合反应;(3)经过聚合基础单元生产得到的乙烯聚合物溶液再经过微混合装置ⅱ混合进入到后续的脱气&脱溶剂装置,再经过造粒装置得到最终产品。本实施例制备的聚乙烯弹性体产品编号为c,产品各项性质见表5。表3注入点序号12345乙烯注入量ml18181817151-辛烯注入量ml313127//实施例4本实施例采用微通道反应器技术,微通道反应器的流程和结构如图4、图5和图7所示。详细地,本实施例采用的催化剂为图3所示cgc催化剂,助催化剂为硼烷、助催化剂的[al]/[ti]比为3,溶剂为isopare和己烷混合物,重量比为1:1,聚合温度为140℃,压力为2.1mpa,共聚单体为1-己烯和1-辛烯(重量比为1:3),初始加入量为290ml,反应物料在微通道反应器内的总停留时间为100min,反应物料在相邻两个共聚单体补充注入点之间的停留时间为15min,反应物料在相邻两个乙烯补充注入点之间的停留时间为18min。因此,本实施例中共聚单体补充注入点有6个,乙烯补充注入点有5个,具体的共聚单体和乙烯注入量见表4。聚合基础单元(微通道反应器单元)的长度为2500m,内径为0.6mm,反应物料在微通道反应器单元的运动速度为5.9m/s,微通道反应器单元所采用的管道横截面为圆形;微通道反应器管道为弯管与弯管的组合,弯管部分反应物料进口方向与出口方向的夹角为120°。本实施例中微通道反应器单元内相邻两个共聚单体补充注入点的距离或相邻两个乙烯补充注入点的距离等距排列,且本实施例采用三个并联的聚合基础单元(微通道反应器单元)作为聚合总单元。本实施例采用的聚合基础单元(微通道反应器单元)材质为钢衬pfa。本实施例基于微通道反应器技术,具体过程如下:(1)cgc催化剂及助催化剂硼烷在isopare和己烷混合溶剂中先进行预混合溶解并活化得到预混合溶液a;乙烯单体(b)与isopare和己烷混合溶剂进行预混合预溶解得到预混合溶液b;1-己烯和1-辛烯与isopare和己烷混合溶剂进行预混合预溶解得到预混合溶液c;(2)预混合溶液a、预混合溶液b和预混合溶液c经过微混合器进行微混合,微混合后的溶液体系增压至2.1mpa压力,且微混合后的溶液体系再经过多级微混合器分散至5个并联的聚合基础单元(微通道反应器单元)进行聚合反应;(3)经过5个并联的聚合基础单元生产得到的乙烯聚合物溶液再经过微混合装置ⅱ混合进入到后续的脱气&脱溶剂装置,再经过造粒装置得到最终产品。本实施例制备的聚乙烯弹性体产品编号为d,产品各项性质见表5。表4注入点序号123456乙烯注入量ml2122252420/1-己烯/1-辛烯注入量ml424647414640实施例5本实施例采用双釜串联聚合工艺生产聚烯烃弹性体,聚合工艺流程见图1中dowlex溶液聚合工艺。本实施例采用的催化剂为图3所示cgc催化剂,助催化剂为硼烷、助催化剂的[al]/[ti]比为6,溶剂为isopare异构烷烃。双釜均为1l的高压反应釜,第一个反应釜温度150℃,压力2.5mpa,停留时间17min,溶剂加入量为450ml,1-辛烯加入量为200ml;第二个反应釜温度155℃,压力1.8mpa,停留时间13min,溶剂加入量为420ml,1-辛烯加入量为130ml。本实施例基于双釜串联聚合工艺,具体过程如下:(1)cgc催化剂、助催化剂硼烷、共聚单体1-辛烯在isopare溶剂中先进行预混合溶解并活化,在加压乙烯作用下充入第一反应釜;(2)第一反应釜内聚合17min后,转入第二反应釜,并在第二反应釜内加入适量1-辛烯及乙烯,第二反应釜内聚合13min。(3)第二反应釜聚合完成后,反应物料进入脱气、脱溶剂等脱挥装置,再经过造粒装置得到最终产品。本实施例制备的聚乙烯弹性体产品编号为e,产品各项性质见表5。表5实施例1-4为采用微通道反应器技术生产的聚烯烃弹性体,实施例5为采用双釜串联聚合工艺生产的聚烯烃弹性体。从表5中可以看出,采用本发明所述的微通道反应器技术生产的聚烯烃弹性体具有催化活性高、共聚单体插入率高、分子量分布窄、密度低、熔点低和结晶度低的特点。在产物力学性能上,随着共聚单体含量的增加,弹性体的拉伸强度和拉伸模量也会逐渐降低,但是会展现出极其优异的断裂伸长率和韧性。采用本发明制备的聚烯烃弹性体,可以被广泛应用于乙烯基和丙烯基聚合物的增韧,尤其在低温韧性上有极其突出的表现。应当注意的是,以上所述的实施例仅用于解释本发明,并不构成对本发明的任何限制。通过参照典型实施例对本发明进行了描述,但应当理解为其中所用的词语为描述性和解释性词汇,而不是限定性词汇。可以按规定在本发明权利要求的范围内对本发明作出修改,以及在不背离本发明的范围和精神内对本发明进行修订。尽管其中描述的本发明涉及特定的方法、材料和实施例,但是并不意味着本发明限于其中公开的特定例,相反,本发明可扩展至其他所有具有相同功能的方法和应用。当前第1页12