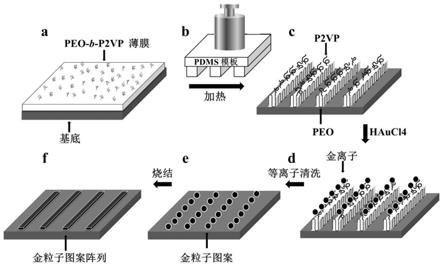
1.本发明属于微纳米加工技术领域,具体涉及一种制备二维贵金属微纳图案大规模阵列的方法。
背景技术:2.贵金属微纳图案具有高电导率、表面等离子共振效应和优良的催化活性等特点,在纳米光电器件、表面增强谱学和生物传感器等领域的研究与应用日益广泛。相比于无序的微纳米贵金属图案,阵列图案的量子效应更加突出,因此其表现出更加优异的性能。目前,大多太阳能电池是通过旋涂法或者沉积法等方法在其表面覆盖一层贵金属图案阵列,然而其阵列形态多集中在线阵列、球阵列和点阵列等几种特定图案阵列,关于二维贵金属图案阵列较少被报道。
3.虽然通过嵌段共聚物结晶模板法能够获得二维微纳米贵金属图案,但二维贵金属图案形状、大小,尤其是位置的调控仍然是一个挑战性课题。近年来,pdms软模板已被用于研究嵌段共聚物薄膜在微纳米横向形貌尺度的约束下所表现结晶行为。然而其应用多是关于复形图案,即聚合物被压印后还有抗刻蚀层的存在。为了调控聚合物晶体的位置需要将抗刻蚀层全部清除完全,因此如何利用pdms软模板调控晶体位置尚未被解决。
技术实现要素:4.本发明提出了一种制备二维贵金属微纳图案大规模阵列的方法,该方法首先通过旋涂聚氧化乙烯
‑
b
‑
聚2
‑
乙烯基吡啶(peo
‑
b
‑
p2vp)溶液制备薄膜,采用pdms软模板热压薄膜,改变热压温度和热压压力可以得到不同宽度的结晶图案阵列。随后通过选择性“熔融和溶解”进一步构筑出大小和位置可控的peo
‑
b
‑
p2vp结晶图案阵列,最后选用金离子与p2vp发生络合反应制备金粒子图案阵列。本发明方法在微纳米尺度上实现了对贵金属图案尺寸和位置的调控。本发明在实际中能够用于太阳能电池、纳米光电器件设计和传感器。
5.本发明的技术方案为:一种制备二维贵金属微纳图案大规模阵列的方法,包括以下步骤:步骤1:将嵌段共聚物peo
‑
b
‑
p2vp作为原料完全溶于溶剂中配置得到溶液;步骤2:将peo
‑
b
‑
p2vp/toluene溶液置于热台上加热数小时直至溶质充分溶解;步骤3:以做过表面处理的硅片为基底,利用匀胶机制备超薄膜;步骤4:使用丙酮、酒精、水依次超声清洗pdms模板表面;步骤5:将peo
‑
b
‑
p2vp超薄膜样品放置在热台上,加热消除超薄膜的热历史;步骤6:将清洗干净的pdms软模板放置在peo
‑
b
‑
p2vp超薄膜上,然后在软模板上放置不同质量的砝码,热压一段时间;步骤7:热压结束后,卸去压力,将热压好的peo
‑
b
‑
p2vp样品从pdms模板上取下,最后将样品置于铝板上淬冷至室温,等温结晶,得到条纹状peo
‑
b
‑
p2vp结晶图案阵列,热压和等温结晶调控了peo
‑
b
‑
p2vp结晶图案阵列的位置;
步骤8:通过选择性熔融进一步调控peo
‑
b
‑
p2vp结晶图案阵列的位置、大小和形态;步骤9:通过选择性溶解冲洗掉peo
‑
b
‑
p2vp结晶模板周围的低温晶体,调控其形态和大小;步骤10:通过金离子与p2vp发生络合反应制备金粒子图案阵列。
6.在进一步的方案中,步骤1中所述使用的peo
‑
b
‑
p2vp其数均分子量为4000
‑
2000g/mol,溶解peo
‑
b
‑
p2vp的溶剂为甲苯,混合溶液溶质的质量分数为0.5 wt
‑
%。
7.在进一步的方案中,步骤2中所述将配制好的混合溶液置于105℃热台中加热3小时以充分溶解溶质。
8.在进一步的方案中,步骤3中的亲水基底是通过紫外臭氧处理基底而得到的,其中紫外灯管的功率为30 w,处理时间为30 min。
9.在进一步的方案中,步骤3中所述匀胶机的旋膜条件为:在氮气气氛的保护下以4000 rpm的速度旋转120s制备超薄膜。
10.在进一步的方案中,步骤4中所述的清洗pdms模板表面,按照如下方法进行:将模板放入丙酮中,超声7~10min,再将模板放入乙醇中,超声7~10min,然后放入去离子水中,超声7~10 min,最后使用高纯氮气吹干pdms模板表面残余的液体。
11.在进一步的方案中,步骤5中所述的消除薄膜的热历史具体为:使用热台将peo
‑
b
‑
p2vp超薄膜加热到60℃~110℃,保温10min。最优加热温度为90℃。
12.在进一步的方案中,步骤6中所述的热压具体为:使用热台将peo
‑
b
‑
p2vp超薄膜加热到60℃~110℃,施加压力为0.2bar~1.5bar,保压10 s。
13.在进一步的方案中,步骤7中的等温结晶具体为:将步骤6得到的peo
‑
b
‑
p2vp热压薄膜置于linkam热台上,在氮气保护气氛下,将peo
‑
b
‑
p2vp薄膜放置在24℃条件下等温结晶24h,得到条纹状的peo
‑
b
‑
p2vp树枝晶。
14.在进一步的方案中,步骤8中的选择性熔融具体为:将步骤7得到的条纹状的peo
‑
b
‑
p2vp树枝晶置于linkam热台上,在氮气保护气氛下,以1℃/min~5℃/min的升温速率由24℃升温至部分熔融温度47℃~48℃,在部分熔融温度下保温3 min,然后以5℃/min的降温速率由部分熔融温度降温至42℃,在42℃条件下等温结晶3 min。
15.在进一步的方案中,步骤9所述的选择性溶解法的步骤为:取10℃的甲苯溶剂,将其直接滴涂在旋涂仪上的晶体样品表面,待溶剂与样品充分接触1s~3s后,开启旋涂仪,以5000 rpm的转速旋转120 s,旋涂结束之后,使用高纯氮气吹净样品表面残余的溶剂。
16.在进一步的方案中,步骤10所述的金离子与p2vp进行络合反应过程是:将冲洗完全的样品浸没于1.0%的氯金酸/正辛醇溶液中避光保存24h以确保金离子的充分搭载,然后使用正辛醇纯溶剂反复冲洗样品以冲洗掉沉积在硅片表面上的未搭载的金粒子。
17.在进一步的方案中,将步骤10搭载完金离子的样品用等离子清洗机进行清洗,其中,清洗的参数:气体为空气、流量为20sccm、功率为80w、时间为5min。
18.本发明的有益效果为:本发明方法是基于高分子薄膜结晶与pdms软模板热压相结合构筑贵金属图案阵列,该方法利用超薄膜中高分子在结晶过程中得到折叠链片晶的稳定性存在差异,并结合pdms软模板热压,在微纳尺度上实现了对嵌段共聚物结晶图案阵列位置、形状和大小的控
g/mol,t
g
约为87℃。硅片为浙江立晶光电科技有限公司生产的型号为p100硅片。旋膜仪为中国科学院微电子研究所生产的kw
‑
4a型。所用的偏光显微镜(pom)型号为:olympus bx
‑
61,相应配套的热台型号为:linkam lts420。采用的原子力显微镜(afm)购置于美国bruker公司,型号为:icon,采用的椭偏仪为美国j.a.woollam co.公司的alpha
‑
se。
32.实施例1热压温度对peo
‑
b
‑
p2vp结晶图案阵列的影响采用旋涂法制备peo
‑
b
‑
p2vp超薄膜:首先将规格为6ml的样品瓶和盖子用铝箔包裹起来并用高纯氮气吹净;随后将peo
‑
b
‑
p2vp(4000
‑
2000g/mol)与甲苯(分析纯)配成浓度为0.5wt
‑
%的溶液;再将溶液放置于105℃的热台上加热3h,并通过不断搅拌直至溶质充分溶解。之后将干净的硅片放置于旋涂仪(型号:kw
‑
4a型,购自于中国科学院微电子研究所),取16μl的peo
‑
b
‑
p2vp溶液于硅片中心,在匀胶机上通过离心力的作用旋涂120s获得膜厚为14.5nm的peo
‑
b
‑
p2vp超薄膜,如图1a。
33.随后将超薄膜置于热台上加热至不同的热压温度(t
p
)60℃~110℃保温10min;将pdms软模板以1bar的热压压力放置于peo
‑
b
‑
p2vp超薄膜上(图1b),待保压10 s使物料被挤进pdms软模板的空腔层内后;将热压后的peo
‑
b
‑
p2vp样品置于铝板上淬冷至室温(脱模温度);然后卸去压力并将pdms软模板从peo
‑
b
‑
p2vp超薄膜上移走。具体热压流程示意图如图1b
‑
c所示。随后将制备好的peo
‑
b
‑
p2vp超薄膜样品放置在惰性气体氮气保护氛围中24℃下结晶24h备用。
34.由图1c和图2a
‑
f可知:被软模板凸起处热压的硅基板上方已经没有物料存在。
35.图2a
‑
f所示为在peo
‑
b
‑
p2vp热压薄膜中不同热压温度(t
p
)60℃~110℃下等温结晶成peo
‑
b
‑
p2vp结晶图案阵列的原子力显微镜图片。由图2a
‑
f所示的结果可知,随着热压温度的升高,热压薄膜中peo
‑
b
‑
p2vp片晶宽度减小,因此可通过调控热压温度调控peo
‑
b
‑
p2vp结晶图案阵列的位置。当t
p = 90 ℃时,该热压温度下得到的片晶宽度与软模板空腔层的宽度一致。
36.实施例2热压压力对peo
‑
b
‑
p2vp结晶图案阵列的影响将膜厚为14.5nm的peo
‑
b
‑
p2vp超薄膜置于热台上加热至90℃热压温度(t
p
)保温10 min;将pdms软模板以0.2bar~1.5bar的热压压力置于peo
‑
b
‑
p2vp超薄膜上,待保压10s使物料被挤进pdms软模板的空腔层内后;将热压后的peo
‑
b
‑
p2vp样品置于铝板上淬冷至室温(脱模温度);然后卸去压力并将pdms软模板从peo
‑
b
‑
p2vp超薄膜上移走。
37.由图3a
‑
e所示结果可知:被软模板凸起处热压的硅基板上方已经没有物料存在。且随着热热压压力的增大,热压薄膜中peo
‑
b
‑
p2vp片晶宽度减小,因此可通过调控热压压力调控peo
‑
b
‑
p2vp结晶图案阵列的位置。当p = 1bar时,该热压压力下得到的片晶宽度与软模板空腔层的宽度一致。
38.实施例3选择性熔融的升温速率对peo
‑
b
‑
p2vp结晶图案阵列的影响在氮气的保护下将热压条件为t
p = 90℃,p = 1 bar的peo
‑
b
‑
p2vp热压薄膜放置在24℃下等温结晶24 h获得条纹状的初始晶体如图2d所示;然后以不同的升温速率(v)1℃/min、2℃/min和5℃/min的速率从24℃升至部分熔融温度(t
s
)47℃保温3min;随后以5℃/min的降温速率降至42℃等温结晶3min;迅速取出样品,并放置到铝板上淬冷至室温。
39.由图4a
‑
c所示结果可知,随着选择性熔融的升温速率的提高,peo
‑
b
‑
p2vp晶体成核密度下降,且集中分布于条形模板中心位置,呈直线形排列,其分布范围由15μm减少至10
μm、5μm,如图4a
‑
c中白色虚线所标识的位置;这是因为当熔融升温速率升高时,peo
‑
b
‑
p2vp条纹晶体的两侧低温晶体来不及增厚就熔融,而稳定性较好的中心位置存留下来,形成直线排列的结晶图案阵列。因此,可通过改变熔融升温速率来调控热压薄膜中peo
‑
b
‑
p2vp结晶图案阵列的分布位置。
40.实施例4 选择性溶解的溶解时间对超薄膜中peo
‑
b
‑
p2vp规则晶体形态和大小的影响在氮气的保护下将14.5nm的peo
‑
b
‑
p2vp超薄膜放置在24℃下等温结晶24 h获得规则的初始晶体如图5a所示;随后使用10 ℃的甲苯溶解2s~16s,调控peo
‑
b
‑
p2vp晶体的大小和形态。
41.由图5所示结果可知,随着溶解时间的延长,由于peo
‑
b
‑
p2vp的(100)晶面比(120)晶面的溶解速率更快,因此形态由最初的方形溶解成为八边形,再变为六边形,最后溶解为近似长方形,并且尺寸由微米级降至接近纳米级。因此,通过选择性溶解法可以调控超薄膜中peo
‑
b
‑
p2vp结晶图案的形态和大小。
42.实施例5选择性溶解的溶解次数对peo
‑
b
‑
p2vp结晶图案阵列的影响在氮气的保护下将热压条件为t
p = 90℃,p = 1 bar的peo
‑
b
‑
p2vp热压薄膜放置在24℃下等温结晶24 h获得条纹状的初始晶体如图2d所示;然后以1℃/min的升温速率从24℃升至部分熔融温度47℃保温3 min;随后以5℃/min的降温速率降至42℃等温结晶3 min;迅速取出样品,并放置到铝板上淬冷至室温。随后使用10℃的16 μl甲苯溶解一至两次,调控peo
‑
b
‑
p2vp结晶阵列图案的大小和形态。
43.由图6所示结果可知,随着溶解次数的增加,peo
‑
b
‑
p2vp片晶的平均尺寸随溶解次数的增加而逐渐降低。因此,通过选择性溶解法可以调控热压薄膜中peo
‑
b
‑
p2vp结晶图案的形态和大小。
44.实施例6选择性熔融的部分熔融温度对peo
‑
b
‑
p2vp结晶图案阵列的影响在氮气的保护下将热压条件为t
p = 90℃,p = 1 bar的peo
‑
b
‑
p2vp热压薄膜放置在24℃下等温结晶24 h获得条纹状的初始晶体如图2d所示;以1℃/min的升温速率从24℃升至部分熔融温度(t
s
)47℃、47.5℃和48℃保温3 min,;随后以5℃/min的降温速率降至42℃等温结晶3 min;迅速取出样品,并放置到铝板上淬冷至室温。得到peo
‑
b
‑
p2vp结晶模板阵列,如图7a
‑
c所示。然后搭载制备金粒子阵列,如图1d
‑
f所示。
45.图7d
‑
f为图7a
‑
c中的peo
‑
b
‑
p2vp结晶模板阵列通过搭载金离子制备的金粒子图案阵列。
46.由图7所示结果可知,随着部分熔融温度的升高,peo
‑
b
‑
p2vp晶体成核密度下降,且逐渐集中分布于条形模板中心位置,通过搭载金离子可以获得与peo
‑
b
‑
p2vp结晶模板阵列一致的金粒子图案阵列;因此,可通过改变部分熔融温度来调控二维金粒子图案的分布位置。
47.实施例7二维金粒子图案阵列的导电性能测试在氮气的保护下将热压条件为t
p = 90℃,p = 1 bar的peo
‑
b
‑
p2vp热压薄膜放置在24℃下等温结晶24 h获得条纹状的初始晶体如图2d所示;以1℃/min的速率从24℃升至部分熔融温度47℃保温3 min;随后以5℃/min的降温速率降至42℃等温结晶3 min;迅速取出样品,并放置到铝板上淬冷至室温。最后利用p2vp嵌段络合金离子结合烧结工艺,制备金
粒子图案阵列。图8a对应图7e金粒子图案阵列中白色虚线框内的局部放大图。图8b和c对应导电原子力显微镜的pf
‑
tuna模式导电性测试结果图,分别为平均电流图和最高电流图。
48.由实验结果可知:基于peo
‑
b
‑
p2vp结晶阵列模板制备的二维金粒子图案阵列具有良好的导电性能,平均电流达到500 fa,最高电流达到10 pa,且导电性能分布较为均匀。
49.以上所述之实施例,只是本发明的较佳实施例而已,并非限制本发明的实施范围,故凡依本发明专利范围所述的构造、特征及原理所做的等效变化或修饰,均应包括于本发明申请专利范围内。