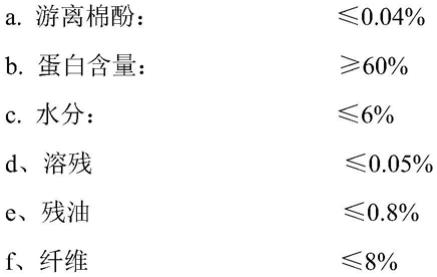
1.本发明涉及棉籽加工技术领域,具体涉及一种脱酚浓缩棉籽蛋白萃取工艺。
背景技术:2.中国是世界产棉大国,据统计2020年产棉花600万吨,棉籽600多万吨,用于榨油、浸出可得200多万吨蛋白饲用原料,棉籽蛋白在质量上近似于豆类蛋白质,其营养价值比豆类蛋白质高。从棉籽蛋白氨基酸的组成看,除蛋氨酸稍低外,其余必须氨基酸均达到联合国粮农组织(fao)推荐的标准,因而棉籽蛋白是一种很好的蛋白质食品和饲料资源,可用来替代鱼粉和豆粕等,并且脱酚浓缩棉蛋白价格相对于浓缩大豆蛋白、鱼粉来说比较低,拥有很强的市场竞争优势。因此研究和开发脱酚浓缩脱毒棉蛋白资源,前景广阔,具有可再生蛋白资源持续发展的战略意义。
3.普通棉粕含有较高的游离棉酚(国家规定1200ppm以下),游离棉酚本身具有毒性,降低了日粮中氨基酸利用率,影响畜禽造血功能,使动物生长受阻。并且,其本身不易排泄,作为饲料原料对牲畜和家禽的肝脏及雄性生殖系统损害较大,在使用时会影响动物的繁殖机能,甚至造成动物不育,因有毒游离棉酚的存在,很大程度限制了其作为蛋白资源的广泛应用和使用量。
4.棉籽加工简介如下:
5.(1)传统加工技术:
6.传统的棉籽加工生产属于高温生产工艺,主要是通过液压、螺旋压榨法、预榨(膨化)浸出法和直接溶剂法等方法来制取油脂和饼粕,提取的棉籽油是传统工艺主要产品,传统的棉籽加工业产品结构为:棉籽油、棉饼(棉粕)、油泥(皂脚),在榨油或预榨浸出后得到的棉饼(棉粕)仍含有大量棉酚毒性,同时通过高温、高水分蒸炒,游离棉酚迅速和赖氨酸反应,有效氨基酸便降低,再高温、高压压榨使得蛋白变性,水溶性蛋白含量通常较低,所以棉饼(棉粕)只能作为棉籽加工业的低级产品,在饲料、食品行业的使用受到限制,除了把少量的脱脂饼粕用于饲料喂反刍动物外,很多地区只得将其作为肥料,失去了其原有的价值,这在目前人类饲用和食用蛋白日感缺乏的情况下是蛋白资源的浪费。
7.(2)传统的脱毒技术有:
8.a、加热法即棉酚在一定温度下能与棉籽蛋白之中的氨基酸结合形成固束棉酚,这种办法不能使蛋白质充分利用,并降低了棉籽蛋白的营养价值。硫酸铁络合法利用硫酸铁和棉酚中的羟基结合,从而固束棉酚,游离棉酚降到要求指标,但不能工业化生产,再者蛋白质含量降低,粕的饲用价值较差。
9.b、微生物发酵法是将棉粕控制在一定温度下,通过微生物发酵作用,使棉酚发生分解,变成无毒物质,从而降低毒害作用,但工业化生产不多。化学添加剂法——该法根据棉酚在不同条件下存在三种异构体,在加入化学试剂后,是棉酚形成双烯酮式异构体,使其容易热固束和增加水中的溶解度,从而达到脱毒效果。但是此法解决不了蛋白变性,而且要和高温压榨浸出相结合才能实施,不够完善。总而言之,研究脱毒方法很多,但真正适于应
用的不是很多。
10.c、现行较成熟的脱毒技术:一种是混合溶剂法(一步溶剂法),另一种是液
‑
液
‑
固萃取法(两步溶剂法)。传统的混合溶剂法是采用极性溶剂浸出的方法,油脂被浸出的同时,棉酚也被浸出,该法的优点是饼粕蛋白质含量较高,游离棉酚含量低,但棉籽经浸出后大部分游离棉酚变为固束棉酚,仍要损失一小部分氨基酸。
11.d、传统的两步溶剂法是采用两种溶剂分别在两种萃取设备内完成,非极性溶剂首先萃取出棉籽中的棉籽油,然后极性溶剂萃取出棉籽中的游离棉酚,两步法开发应用是较早、较广泛的一种棉籽脱毒方法,对棉籽加工行业来说是一场全新的技术革命,给企业和社会带来了巨大的经济效益和社会效益。
12.脱毒浓缩棉蛋白功能与应用如下:
13.脱毒浓缩棉蛋白去除了多种抗原、寡糖和皂素,抗原损害消化道并指过敏反应,寡糖引起胃肠胀气影响养分消化,皂素含异味至适口性差。含极低的脂肪、还原糖及水分和生菌数,储存不易变质,品质维持稳定。
14.(1)饲料上脱酚棉籽蛋白可替代豆粕、鱼粉等蛋白原料,在畜禽、反刍动物、水产饲料中广泛应用,主要是过瘤胃性能好,蛋白含量高,微量元素丰富,而且棉籽蛋白基本上不属于转基因植物,能维持各种饲养动物的快速生长和健康,能取代饲料中的贵重蛋白源来降低配方成本,能确保肉、蛋、奶、鱼、虾食品的安全。
15.a、脱毒浓缩棉籽蛋白具有相似于脫脂奶粉的促仔猪生长功能,並能部份取代血漿蛋白来节省饲料成本。
16.b、脱毒浓缩棉籽蛋白能有效地用于水产飼料。在最适添加水平,能维持鱼虾的正常生长表現,并尤其能改善幼苗的成活率。
17.c、脱毒浓缩棉籽蛋白是犊牛的常用优质、价廉、易消化代乳品。
18.d、脱毒浓缩棉籽蛋白可被宠物饲料所选用是因为它的经济实用性、综合功能性、营养全面性。
19.(2)食品上与大豆蛋白相比,不含蛋白酶抑制剂,也不含有血凝素活性物,风味清淡,温和,无异味,能与其他食品原料。
20.棉籽加工多年来一般采用传统的物理压榨、浸出和膨化、浸出来生产棉粕,这类加工造成蛋白有效营养成分损失,使用效率低,逐渐会被淘汰,更加先进的加工技术逐渐出现,代替旧的加工技术,近些年来脱酚浓缩蛋白(蛋白含量50%)加工异军突起,其作用和功能逐渐得到饲料业和社会的认可,此技术有效提高蛋白活性和降低蛋白毒性,增加了棉籽蛋白的价值,但是工艺和设备技术参差不齐,甚至差别和差距非常大,造成加工成本和产品质量(蛋白醇变性和蛋白高温变性)不一而同,严重影响到棉籽蛋白产品的使用和推广,相对来说这种蛋白含量和营养功能还是低。
技术实现要素:21.为解决现有技术的问题,本发明提供一种脱酚浓缩棉籽蛋白萃取工艺。
22.本发明的目的通过以下技术方案来实现:一种脱酚浓缩棉籽蛋白萃取工艺,包括如下步骤:
23.(一)棉籽预处理的工艺过程:
24.(1)光棉籽经过清理,去除杂质,即把不孕籽、轻杂、泥土和重杂从棉籽中除掉,含棉仁粉的轻杂进行分离,回收棉仁粉,处理过的轻杂、泥土和重杂回收处理,灰尘二级处理,环境卫生、干净,而保持原料干净,保证产品质量。
25.(2)对经过清理后的光棉籽进行分级处理,分离出小棉籽、坏棉籽和霉棉籽的不可用棉籽,并另行处理回收,得到高质量的均质棉籽,保证了高产品风味和口感。
26.(3)对分级后的光棉籽进行剥壳、破碎,利用多级筛分系统对棉仁、棉壳经过多次分离,得到合格的棉仁。
27.进一步的,经过分级后的光棉籽经剥壳后进行破碎,光棉籽破碎为2
‑
4瓣,减少粉末度(2%以下),破碎成合适的混合物料,棉仁、棉壳混合物经过多级联筛处理分离,筛上物棉壳(含仁量0.5%以下)输送至壳库包装,筛下物仁、壳再次利用筛分系统分离手段,进行精选,筛上棉壳去壳库包装,筛下的棉仁去调质,精选后的仁粉再次利用粉碎和筛分分级系统进行分离,得到合适的仁粉,总之棉仁中含棉壳量小于1%。
28.(4)棉仁经湿热调质处理后再进行加热软化处理,之后用轧坯机进行轧坯,得到厚度合适的片状物,即坯片;同时破坏油籽的细胞结构,棉酚和油脂外露,以利于浸出。
29.进一步的,调质处理时间20
‑
30分钟,温度为95℃
‑
100℃,调质处理后棉仁的水分为8%
‑
13%。
30.进一步的,软化处理时间为15
‑
20分钟,温度为115℃
‑
120℃,软化处理后棉仁的水分为10%以下。
31.进一步的,坯片的厚度为0.25mm以下。
32.(5)烘干、冷却:坯片经过烘干和冷却,调整适合浸出的水分和温度;其中冷却后坯片的水分为4%
‑
6%,温度为55℃
‑
65℃。
33.进一步的,烘干的条件为:温度98℃
‑
100℃,时间20
‑
25分钟;冷却到65℃以下。
34.(二)、棉坯浸油、脱酚工艺过程
35.(1)预处理来的料坯(坯片)进入刮板式连续浸出器,先经非极性溶剂进行多阶段,设备分上下层,物料在这两层内完成多级浸泡,浸泡温度为55℃
‑
60℃、总时间为4小时
‑
5小时,得到浓混合油;
36.浸泡过的湿坯再用两相混合溶剂(极性溶剂)进行多级浸泡,浸泡温度为40℃
‑
50℃、总时间为40分钟
‑
60分钟,得到清混合油、混合酚液和湿坯,清混合油继续回到浸出器萃取油脂;其中所述两相混合溶剂为正己烷和甲醇的混合物,正己烷和甲醇的质量比(4
‑
6):1。
37.进一步的,所述非极性溶剂为清混合油,所述清混合油为正己烷和棉籽油的混合物,混合物中棉籽油的浓度为3%
‑
5%;
38.进一步的,所述非极性溶剂浸泡的级数为7级,所述两相混合溶剂浸泡的级数为3级。
39.进一步的,浓混合油经过三级净化(沉淀、离心分离、机械过滤)后,经一蒸发和二蒸发两级负压蒸发(节能降耗,节省蒸汽25%以上),再经过脱溶设备汽提脱溶,得到成品油,蒸发出来的溶剂汽经冷凝后循环利用。
40.进一步的,一蒸发的温度为50℃
‑
60℃,负压为
‑
0.038—0.050mpa,二蒸发的温度为60℃
‑
70℃,负压为
‑
0.038—0.050mpa两级负压蒸发。
41.进一步的,所述机械过滤得过滤网为200目
‑
400目。
42.进一步的,所述浓混合油在蒸发过程中结合使用混合油精炼技术,能够降低成品油颜色(r≤2)和提高成品油得率(97%以上)。
43.进一步的,所述混合酚液经过滤、沉淀、净化后进行精馏,精馏废物浓缩、提纯处理,精馏出来的甲醇汽冷凝后重新循环利用。
44.(2)湿粕经物理挤压机挤压处理后(含湿量≤40%),进入两级多层烘干机进行烘干;利用间接蒸汽加热进行低温脱溶,混合溶剂汽经冷凝,再循环使用;
45.其中,一级烘干正己烷,条件为:温度72℃
‑
75℃,时间10分钟
‑
20分钟,二级烘干条件为:温度100℃,时间10分钟
‑
30分钟,真空度300
‑
380mmhg。
46.(3)烘干后的物料进行调质,得到棉籽脱酚浓缩蛋白。
47.进一步的,调质为采用气体(惰性气体)进行汽提,压力为0.05mpa以下,继续提取物料内的溶剂,时间为10分钟。
48.进一步的,将棉籽脱酚浓缩蛋白输送至磨粉车间冷却(40℃以下),磨粉、筛分(可根据市场实际需求合理调节,如40目、80目、120目等)处理后,成品包装入库。
49.本发明是以清理、分级、破碎、多级分离、调质、软化、轧坯、烘干后的物料为原料,以非极性溶剂和极性溶剂为萃取剂,两种溶剂前后投入,混合萃取棉酚、棉籽糖和棉籽油,混合液充分萃取棉酚和棉籽糖,取出分离,极性溶剂经过分离、提纯,循环使用,低浓度非极性混合油继续萃取棉籽油,经过低温浸提、分离得到浓混合油、混合酚液和湿粕,浓混合油经多级分离,浓混合油经负压蒸发、混合油精炼、得到成品油和非极性溶剂,成品油罐装保存,非极性溶剂循环使用,湿物料经物理挤压、真空烘干脱溶和真空调质,得到脱酚(200ppm以下)和水溶性蛋白高的棉籽脱酚浓缩高蛋白(水溶性氮指数65%以上)。
50.本发明的有益效果:
51.脱酚浓缩蛋白中含量为60%以上的棉籽蛋白,使用甲醇和溶剂多效多级萃取,提取出其中油脂、可溶性糖分、棉酚和甾醇,加工的浓缩棉籽蛋白不但具有较好的色泽、较小的毒性,还减少了多种抗营养因子的危害,同时提高了产品的蛋白含量和功能性,物料经过物理挤压和真空热处理降低蛋白湿、热变性,物料蒸脱采用有效气体真空汽提系统脱除残留溶剂和甲醇,极大改善了氨基酸的可消化利用性。
52.本发明脱毒浓缩棉籽蛋白技术进一步提升棉籽蛋白性能的使用,提高产品中的蛋白含量,高达60%以上,并降低了产品中的棉酚、棉籽糖和皂素含量,因而扩展了产品的使用范围和使用途径,同时提取和分离出棉籽中的植物活性物质,延长了企业深加工产业链。
53.总之提高蛋白质量,降低蛋白毒素(游离棉酚),提高蛋白饲料使用幅度和使用量,前景非常看好。
附图说明
54.图1为棉籽预处理的工艺过程流程图;
55.图2为棉坯浸油、脱酚工艺过程流程图。
具体实施方式
56.下述非限定性实施例可以使本领域的普通技术人员更全面地理解本发明,但不以
任何方式限制本发明。
57.实施例1
58.如图1、2所示,一种脱酚浓缩棉籽蛋白萃取工艺,包括如下步骤:
59.1、棉籽预处理的工艺过程
60.(1)符合标准的光棉籽用清理设备把不孕籽、轻杂、泥土和重杂从棉籽中除掉,含棉仁粉的轻杂进行分离,回收棉仁粉,处理过的轻杂、泥土和重杂回收处理,灰尘二级处理,环境卫生、干净,而保持原料干净,保证产品质量。为了有效地达到清选效果,工艺中将配备高效清籽机、沙克龙和棒条机联合使用来清理轻杂、泥土和重杂;为了保证车间有良好操作环境,工艺设计将配置系统除尘装置,采用旋风分离式除尘器和二次除尘系统。
61.(2)分级处理光棉籽,分离出小棉籽、坏棉籽和霉棉籽,并另行处理回收,高质量的均质棉籽保证了高产品风味和口感。分级处理采用振动筛分级设备,并配置除尘系统,分离出大小均匀的颗粒,进行加工。
62.(3)分级后的光棉籽采用对辊棉籽剥壳机(快转速650rpm,慢转速325rpm,速差比1:2),利用齿形、运动和辊径,可以保持较高的整仁率(粉末度2%)和剥壳效率。
63.(4)光棉籽经剥壳后,进入破碎和分离系统进行加工处理,经过破碎系统破碎光棉籽(2
‑
4瓣),减少粉末度(2%以下),破碎成合适的混合物料,棉仁、棉壳混合物经过多级联筛处理进行分离,筛上物棉壳(含仁量0.5%以下)输送至壳库包装,筛下物棉仁、棉壳再次利用筛分系统分离手段,进行精选,筛上棉壳去壳库包装,筛下的棉仁去调质,精选后的仁粉再次利用粉碎和筛分分级系统进行分离,得到合适的仁粉,总之棉仁中含棉壳量小于1%。分离设备采用高速多级连筛(200rpm)、平转筛、帮条(200rpm)和重力式分离器联合处理分离,可以保证棉壳中含棉仁(含棉仁率0.5%以下)和棉仁中棉含壳(含壳率1%以下)都达到工艺设定指标。
64.(5)合格的仁、粉混合物经过惰性气体(氮气或者二氧化碳)调质器进行充分的调质(水分8%,温度100℃,时间20分钟),之后进入软化锅(时间20分钟,温度115℃,水分10%)进行加热软化,软化后用轧坯机轧坯,将一定粒度的棉仁做成厚度(0.25mm)合适的片状物,同时破坏棉仁的组织结,油籽棉仁的细胞结构,棉酚和油脂充分外露,以利于后续的浸出(萃取)。
65.(6)坯片进入调整系统,利用烘干设备进行加热烘干(烘干温度98℃
‑
100℃,时间20
‑
25分钟),然后冷却(降温65℃以下),对棉籽坯片物理和调质处理,膨化料进一步后熟,调整适合浸出的水分(水份5%左右)和温度(65℃)的坯片。
66.本工艺路线短、科学实用,设备高效,棉壳、棉仁分离彻底、充分,脱酚有不同于与其他脱酚工艺和方法。
67.2、棉坯浸油、脱酚工艺过程
68.(1)预处理来的料坯(坯片)进入刮板式连续浸出器,先经非极性溶剂(清混合油,即正己烷和棉籽油的混合物,混合物质中棉籽油浓度为5%)多阶段、多级浸泡(设备分上下层,物料在这两层内完成7级浸泡),温度55℃,总时间4小时,得到浓混合油和浸泡过的湿坯;浸泡过的湿坯再用两相混合溶剂(正己烷和甲醇的质量比5:1)多阶段、多级浸泡(3级),温度40℃,总时间40分钟,得到清混合油、混合酚液和湿坯;清混合油继续回到浸出器萃取油脂。采用两相混合溶剂萃取棉酚和糖分,单相溶剂萃取棉籽油,萃取过程使用刮板浸出器
多级喷淋、浸泡、沥干式萃取,使用脱酚蛋白设备脱酚。
69.(2)浓混合油三级净化(沉淀、离心分离、机械过滤,过滤网400目)后,进入蒸发系统,经一蒸发温度50℃,负压为0.050mpa和二蒸发温度60℃,负压为0.050mpa,两级负压蒸发(节能降耗,节省蒸汽25%
‑
30%),再经过脱溶设备汽提脱溶,得到成品油,蒸发出来的溶剂汽经冷凝后循环利用。蒸发系统采用负压蒸发,二次蒸汽利用,节能效果明显;蒸发温度低,油品颜色浅,质量好;使用针对三相溶剂汽二次利用的蒸发设备。
70.(3)浓混合油在蒸发过程中结合使用混合油精炼技术,能够降低成品油颜色(r≤2)和提高成品油得率(97%以上)。尾气处理采用石蜡吸收,系统内负压,跑冒滴漏少,溶耗低,生产安全。系统尾气一般来自物料中所带空气,冷凝器未凝结自由气体,溶剂储存系统的挥发性气体。
71.(4)混合酚液经过滤、沉淀,净化后进行精馏,精馏废物浓缩、提纯处理,得到浓缩干物质,精馏出来的甲醇汽冷凝后重新循环利用;混合液中含大量的棉酚、糖分和蛋白,受高温时,容易在管壁结焦,影响换热效果,蒸汽消耗高,不利于生产,采用负压精馏降低浓缩温度,可防止结焦。
72.(5)湿粕经物理挤压系统处理后(含湿量≤40%),进入两级浅床多层烘干系统进行烘干,一级烘干正己烷,温度75℃,时间20分钟,二级烘干100℃,时间15分钟,配套真空装置和真空系统,真空度380mmhg,利用间接蒸汽加热进行脱溶,混合溶剂汽经冷凝,再循环使用。湿胚中的溶剂采用链带式输送机,湿胚在运行中受到压迫,溶剂液便回收,同时湿胚中的含溶量降低,减轻烘干系统的负荷。挤压系统采用先进实用的双螺旋挤压机,输送过程压滤出物料中的液体,降低物料中的湿含量,提高水溶性指数和降低棉酚含量效果明显,节省烘干用的蒸汽。烘干系统采用多层立式烘干机,物料在下降过程中被间接汽加热脱溶,并和从下面上来的自由气体进行热交换,达到汽提作用,传热效率高,物料变性小。
73.(6)烘干后的物料送入调质系统,时间10分钟,采用气体(惰性气体,氮气或者二氧化碳)进行汽提,压力为0.05mpa,继续提取物料内的溶剂,调质后,棉籽脱酚浓缩蛋白输送至磨粉车间冷却(40℃以下),磨粉、筛分处理后,成品包装入库。采用调质器进行脱溶调质,利用间接蒸汽和惰性气体(氮气或者二氧化碳)汽提系统综合使用的调质器,在负压状态下,加热和汽提效果非常明显,蛋白产品颜色一致,溶残符合国标要求,保证了产品中的溶剂残留量及产品质量符合国家标准。
74.本工艺采用低温萃取,棉酚萃取时间短,并甲醇投放量小,物料经过物理挤压、低温真空脱溶,真空调质。低温、真空烘干脱溶,蛋白含量高、变性小,混合油负压蒸发,混合油精炼,二次蒸汽利用,节省蒸汽,能够提高油品质和产品出率。
75.3、棉蛋白质量指标
[0076][0077]
4、本发明技术工序特点
[0078]
本发明经深入研究,反复试验,结合生产实践和专业技术知识,开发出一整套新的国内外比较先进的、科学成熟的脱毒浓缩棉蛋白提取技术。该发明工艺简单,实用,布局合理,操作方便,所需厂房小、设备投资少,生产成本低。
[0079]
本发明工艺要求棉籽加工是在低温条件下加工进行的,低温萃取和低温脱溶极大地保留棉籽中的天然活性物质:棉蛋白,并提取出棉酚和棉籽糖,而低温脱毒浓缩棉蛋白中蛋白含量高于65%,棉酚含量低于0.02%。
[0080]
本发明实施的预处理主要工序清理、分级、剥壳、分离、调质、软化、轧坯、烘干,本发明实施的浸出主要工序有低温浸出提油、脱毒、低温脱溶、真空调质、混合油负压蒸发、混合油精炼、混合液精馏。
[0081]
(1)提油和脱酚利用非极性溶剂和极性溶剂,在浸出器里(一次性低温提油、脱酚设备,设备投资小,运转平稳,提油、脱酚效率高,粕中残油低小于0.5%,脱酚后的蛋白含酚量小于0.02%),经喷淋、浸泡、沥干多次循环萃取,非极性溶剂循环萃取棉坯中的棉籽油,混合溶剂混合循环萃取棉坯中的棉酚,沥干后进入脱溶。
[0082]
(2)混合油采用混合油精炼和负压蒸发处理技术,首先净化处理,再经一、二蒸长管蒸发器及降膜汽提处理,得到毛油。一蒸发器热源利用烘干机的二次蒸汽,二次蒸汽的利用,节省约25
‑
30%的蒸汽,负压蒸发技术和混合油精炼技术,带来毛油挥发物低,颜色浅,过氧化值低,改善了油品质量,提高了毛油精炼率。
[0083]
(3)棉酚混合液的分离,极性溶剂萃取棉酚后,进行浓缩精馏,提纯极性溶剂。
[0084]
对于任何熟悉本领域的技术人员而言,在不脱离本发明技术方案范围情况下,都可利用上述揭示的技术内容对本发明技术方案作出许多可能的变动和修饰,或修改为等同变化的等效实施例。因此,凡是未脱离本发明技术方案的内容,依据本发明的技术实质对以上实施例所做的任何简单修改、等同变化及修饰,均应仍属于本发明技术方案保护的范围内。