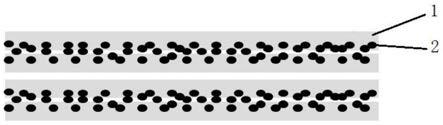
改性环氧树脂中的任意一种或几种的组合。本发明加入固体双官能团环氧树脂主要增加 常温树脂体系的粘度,且固体双官能团环氧树脂熔点较低,树脂体系在较低温度就可以 达到较低的粘度,且粘度平台区较长。固体环氧树脂的加入也增加了树脂体系的成膜特 性,适用于制备热熔法预浸料。
10.进一步的,所述胺类固化剂为双氰胺、4,4
’‑
二氨基二苯基砜、间苯二胺、双胍类 化合物中的任意一种或几种的组合。固化剂采用研磨的方式可以增加粉状固化剂分散均 匀性,不会产生放热集中点或应力集中点。双氰胺固化剂固化速度快,适合于快速固化 体系,且制备热熔法预浸料储存期长,属于潜伏性固化剂。
11.进一步的,所述增韧剂为聚氨酯改性环氧树脂、液态环氧基笼型倍半硅氧烷中的一 种或两种任意比例的组合物。本发明所用增韧剂不是常规增韧剂的选择,热熔法预浸料 所选用增韧剂一般为热塑性树脂,但热塑性树脂劣势在于分子量大,加工过程中会导致 树脂体系的粘度急剧上升,预浸料的工艺性和铺覆性劣化,同时树脂体系对纤维束的浸 润性也会变差。本发明所用两种增韧剂,都为改性环氧树脂的增韧剂,与基体树脂的相 容性较好,不会出现相分离,混合不均匀的效果,在保持能够提高体系粘度的同时,达 到增韧的目的。
12.进一步的,所述聚氨酯改性环氧树脂粘度为40000
‑
60000mpa
·
s,环氧当量 210
‑
250g/eq。所述液态环氧基笼型倍半硅氧烷结构中环氧基团数为2
‑
4,挥发分<0.5%。 本发明所选该性能聚氨酯改性环氧树脂,从粘度上提升树脂体系最终粘度,环氧当量与 主体树脂相近,且该环氧基团数可以增加交联密度,不降低树脂体系的耐热性能。
13.进一步的,所述促进剂为有机脲类促进剂中的一种或两种的组合。本发明所选促进 剂可以降低胺类固化剂的固化温度,提高固化速率。
14.进一步的,环氧树脂组合物常温粘度介于3000
‑
6000pa
·
s之间,粘温流变曲线最 低粘度介于1000
‑
3000mpa
·
s。环氧树脂组合物在常温下有足够高的粘度,在高温下有 足够低的粘度,且粘度平台较长。常温树脂过黏,容易在铺覆过程中包裹大量空气,且 堵塞排气通道,粘度高则预浸料铺覆性太差。而在升温固化过程中,树脂要有足够的流 动性以充分浸润纤维,所达到的最低黏度应适宜,最低粘度过低,则树脂流动过快,可 能导致夹杂气体有效导出前树脂已将导气通道堵塞,如果最低粘度过高,则在有限的一 个大气压下,树脂流动性不足,不足以充分浸润纤维,复合材料孔隙率会增加。另外树 脂应该在合适的粘度区域保持一段时间,以保证足够的时间让夹杂气体和挥发物排出。
15.进一步的,所述环氧树脂组合物粘温曲线的最低粘度平台区较长。因此凝胶时间较 长,最低粘度平台区仍能保持在8000mpa
·
s以下,能保证粘度较低时间内充分浸润纤 维,降低复合材料内部的孔隙。
16.第二方面,本发明还涉及一种ooa成型热熔法预浸料用快速固化高韧性环氧树脂组 合物的制备方法,按下述步骤进行:
17.s1、将5
‑
15份液态双官能团环氧树脂、50
‑
70份固体双官能团环氧树脂和10
‑
20 份增韧剂混合,在105
‑
115℃温度下加热熔融并搅拌30
‑
60min,得到透明均匀的混合物 a;
18.s2、将5
‑
20份胺类固化剂和0.5
‑
2份促进剂与5
‑
15份液态双官能团环氧树脂混合 搅拌并研磨,得到胺类固化剂分散均匀的混合物b;
19.s3、将油浴锅中料温的温度降至80
‑
90℃,将混合物b加入混合物a中搅拌混合 8
‑
10min,得到所述环氧树脂组合物。
20.进一步的,步骤s2中研磨时,是将液态环氧树脂中的一种当母料进行研磨。所述 胺类固化剂需使用前述液态双官能团环氧树脂的一种当母料过三辊研磨机,才可将胺类 固化剂在组合物体系中分散均匀,不会产生颗粒团聚现象,因此制备成树脂浇铸体没有 应力集中点,相比于未研磨性能优。
21.进一步的,研磨使用三辊研磨机进行研磨,研磨不少于3遍。
22.其中,搅拌混合的搅拌速度为1000
‑
2000r/min,搅拌时间8
‑
10min。使胺类固化剂 能够充分分散均匀,经过充分混合后得到所述一种ooa成型热熔法预浸料用快速固化高 韧性环氧树脂组合物。
23.进一步的,步骤s2中的液态双官能团环氧树脂选用双酚f型环氧树脂。
24.第三方面,本发明还涉及一种上述环氧树脂组合物在ooa成型中的应用,所述环氧 树脂组合物在成型过程中与纤维配合使用形成预留气道,预留气道的构建方法采用方法 一或方法二:
25.方法一:制备树脂胶膜,采用上下双面覆膜的方法,制备得到半浸渍热熔法预浸料, 使得碳纤维不会被完全浸透,中间还存在未浸区域,未浸区域在成型过程中形成预留气 道;
26.方法二:制备树脂胶膜,采用上下双面覆膜的方法,碳纤维完全浸透制得全浸渍预 浸料;在成型过程中,铺层时在树脂胶膜层间覆纳米纤维膜,使得层与层之间形成预留 气道。
27.方法一中,制备树脂胶膜的温度为65
‑
75℃。胶膜在纤维上下双面覆膜复合时,辊 1、辊2、辊3的温度分别为80℃、75℃、75℃。
28.方法二中,制备树脂胶膜的温度为65
‑
75℃。胶膜在纤维上下双面覆膜复合时,辊 1、辊2、辊3的温度分别为105℃、100℃、100℃。
29.方法一中半浸渍预浸料复合温度比全浸渍预浸料复合温度低25℃。方法二中制备全 浸渍预浸料,在铺层过程中,采用层间覆纳米纤维膜的方法,使得层与层之间预留气道, 不仅达到排气的目的,而且起到层间增韧的作用。
30.本发明适用于ooa成型工艺的环氧树脂组合物,与现有热压罐成型和模压成型相比, 本发明的有益效果在于:
31.1)本发明的适用于ooa成型工艺环氧树脂组合物,不仅增加了树脂体系的韧性, 提高复合材料结构件的成型质量、成型效率降低工艺成本,而且缩短了树脂的固化时间, 制备高性能树脂体系,扩宽复合材料的使用领域,特别适用于ooa成型。
32.2)本发明的适用于ooa成型工艺环氧树脂组合物中,所用的固体双官能团环氧树 脂可以有效调节该组合物的粘度达到ooa成型环氧树脂的粘度要求。
附图说明
33.通过阅读参照以下附图对非限制性实施例所作的详细描述,本发明的其它特征、目 的和优点将会变得更明显:
34.图1为ooa半浸渍预浸料示意图;
35.图2为全浸渍预浸料夹层示意图;
搅拌速度为1500r/min),搅拌时间9min,使固体胺类固化剂能够充分分散均匀,经过 充分混合后得到所述适用于ooa成型工艺热熔法预浸料用环氧树脂组合物,在110℃下 脱泡30min,随后升温至160℃固化30min,得到固化的环氧树脂组合物。
51.实施例4
52.将15份e51环氧树脂、44份e20环氧树脂、21份704环氧树脂和10份聚氨酯改 性环氧树脂四种物质混合,在110℃油浴锅中加热熔融搅拌30min,得到透明均匀的混 合物a;
53.将10份双氰胺固化剂和1份ur300促进剂与10份的双酚f环氧树脂混合搅拌,过 三辊研磨机不少于3遍,得到双氰胺固化剂分散均匀的混合物b;
54.将油浴锅中料温的温度降至80℃,将混合物b加入混合物a中高速搅拌混合(优选 搅拌速度为2000r/min),搅拌时间8min,使固体胺类固化剂能够充分分散均匀,经过 充分混合后得到所述适用于ooa成型工艺热熔法预浸料用环氧树脂组合物,在110℃下 脱泡30min,随后升温至160℃固化30min,得到固化的环氧树脂组合物。
55.实施例5
56.将5份e51环氧树脂、44份e20环氧树脂、21份704环氧树脂和20份液态环氧基 笼型倍半硅氧烷四种物质混合,在110℃油浴锅中加热熔融搅拌30min,得到透明均匀 的混合物a;
57.将6份双氰胺固化剂和1份ur300促进剂与10份的双酚f环氧树脂混合搅拌,过 三辊研磨机不少于3遍,得到双氰胺固化剂分散均匀的混合物b;
58.将油浴锅中料温的温度降至80℃,将混合物b加入混合物a中高速搅拌混合(优选 搅拌速度为1000r/min),搅拌时间8min,使固体胺类固化剂能够充分分散均匀,经过 充分混合后得到所述适用于ooa成型工艺热熔法预浸料用环氧树脂组合物,在110℃下 脱泡30min,随后升温至160℃固化30min,得到固化的环氧树脂组合物。
59.实施例6
60.将5份e51环氧树脂、44份e20环氧树脂、21份704环氧树脂、10份聚氨酯改性 环氧树脂、10份液态环氧基笼型倍半硅氧烷五种物质混合,在110℃油浴锅中加热熔融 搅拌30min,得到透明均匀的混合物a;
61.将6份双氰胺固化剂和1份ur300促进剂与10份的双酚f环氧树脂混合搅拌,过 三辊研磨机不少于3遍,得到双氰胺固化剂分散均匀的混合物b;
62.将油浴锅中料温的温度降至80℃,将混合物b加入混合物a中高速搅拌混合(优选 搅拌速度为1000r/min),搅拌时间8min,使固体胺类固化剂能够充分分散均匀,经过 充分混合后得到所述适用于ooa成型工艺热熔法预浸料用环氧树脂组合物,在110℃下 脱泡30min,随后升温至160℃固化30min,得到固化的环氧树脂组合物。
63.实施例7
64.将5份e51环氧树脂、44份e20环氧树脂、21份704环氧树脂、20份聚氨酯改性 环氧树脂四种物质混合,在110℃油浴锅中加热熔融搅拌30min,得到透明均匀的混合 物a;
65.将6份双氰胺固化剂和1份ur500促进剂与10份的双酚f环氧树脂混合搅拌,过 三辊研磨机不少于3遍,得到双氰胺固化剂分散均匀的混合物b;
66.将油浴锅中料温的温度降至80℃,将混合物b加入混合物a中高速搅拌混合(优选 搅拌速度为1000r/min),搅拌时间8min,使固体胺类固化剂能够充分分散均匀,经过 充分
为65℃
‑
75℃之间,通过两步法制备热熔法预浸料,半浸渍预浸料胶膜与纤维复合温度 辊1、辊2、辊3分别为80℃、75℃、75℃,全浸渍预浸料胶膜与纤维复合温度辊1、 辊2、辊3分别为105℃、100℃、100℃,相对于全浸渍预浸料,半浸渍预浸料复合温 度比全浸渍预浸料复合温度低25℃,使得纤维不会被完全浸透,中间还存在未浸区域, 如图1所示,碳纤维2为被树脂胶膜1完全浸渍,未浸区域充当成型过程中夹杂气体的 气道,这是其中一种制备热熔法预浸料过程中达到ooa成型的方法,便于夹杂气体的排 出。
77.实施例10
78.采用实施例9中制备的全浸渍预浸料,热熔法预浸料层与层之间铺45gsm的纳米纤 维膜,如图2所示,纳米纤维膜3将浸渍碳纤维2的树脂胶膜层与层之间隔出一定微小 间隙,充当气道的作用,且纳米纤维膜铺在层间,具有层间增韧的效果,对于复合层合 板层间的增韧效果要比增韧本体树脂效果优,使得复合材料层间抗损伤容限提升。
79.对比例1
80.本对比例提供一种快速固化高韧性环氧树脂组合物,具体步骤与实施例1基本相同, 不同之处仅在于:液态双官能团环氧树脂为ag80四官能团环氧树脂、afg90三官能团环 氧树脂;固体双官能团环氧树脂为噁唑烷酮改性环氧树脂,所得环氧树脂组合物粘度较 大,反应活性较高,很难达到ooa成型工艺粘度与凝胶时间要求。
81.表2
[0082] 最低粘度(mpa
·
s)120℃凝胶时间实施例1135518
′
50
″
对比例134007
′
30
″
[0083]
对比例2
[0084]
本对比例提供一种快速固化高韧性环氧树脂组合物,具体步骤与实施例1基本相同, 不同之处仅在于:增韧剂为端羧基丁腈橡胶。
[0085]
该树脂组合物粘性较大,气泡排除困难,该增韧剂增韧效果明显,但组合物耐热性 下降明显,且力学性能有所降低,达不到工艺性能要求。不采用这种增韧剂原因是会降 低力学性能,降低幅度较大,且耐热性降低。
[0086]
表3
[0087][0088]
对比例3
[0089]
本对比例提供一种快速固化高韧性环氧树脂组合物,具体步骤与实施例1基本相同, 不同之处仅在于:增韧剂为聚丙烯酸酯。
[0090]
不采用这种增韧剂原因为丙烯酸酯类聚合物为小分子,真空下会逸出未反应小分子, 一般航天不采用真空逸气量大的材料,且其玻璃化转变温度较低。
[0091]
对比例4
[0092]
本对比例提供一种快速固化高韧性环氧树脂组合物,具体步骤与实施例1基本相同, 不同之处仅在于:增韧剂为聚醚砜热塑性树脂。
[0093]
热塑性树脂劣势在于分子量大,加工过程中会导致树脂体系的粘度急剧上升,预浸 料的工艺性和铺覆性劣化,同时树脂体系对纤维束的浸润性也会变差,因此不足点明显。
[0094]
对比例5
[0095]
本对比例提供一种快速固化高韧性环氧树脂组合物,具体步骤与实施例1基本相同, 不同之处仅在于:增韧剂选用的聚氨酯改性环氧树脂,25℃粘度为5000
‑
11000mpa
·
s, 环氧当量为240
‑
280g/eq,该聚氨酯改性环氧增韧效果较实施例1差,且树脂粘度较低, 导致组合物粘性较大粘度较低,不符合制备热熔法预浸料树脂粘度粘性的要求。
[0096]
表4
[0097] 断裂韧性(mpa/m
1/2
)组合物室温粘度(pa
·
s)实施例14.13200对比例52.42300
[0098]
对比例6
[0099]
本对比例提供一种快速固化高韧性环氧树脂组合物,具体步骤与实施例1基本相同, 不同之处仅在于:增韧剂选用的液态环氧基笼型倍半硅氧烷,该增韧剂结构中环氧基团 数为5,对组合物的增韧效果不明显。
[0100]
表5
[0101][0102]
对比例7
‑
10
[0103]
对比例7
‑
10分别与实施例1
‑
4一一对应,其组分、步骤基本相同,不同之处仅在 于对比例7
‑
10中胺类粉末固化剂未采用液态双官能团环氧树脂的一种当母料分散过三 辊研磨机。
[0104]
胺类粉末固化剂采用母料分散未过三辊研磨机与过三辊研磨机对比,拉伸树脂浇铸 体断裂面容易出现应力集中点,拉伸性能较差,两者性能对比如表2,且制备预浸料涂 膜过程中容易出现肉眼可见颗粒,影响树脂与复合材料力学性能。
[0105]
表6
[0106][0107]
以上对本发明的具体实施例进行了描述。需要理解的是,本发明并不局限于上述特 定实施方式,本领域技术人员可以在权利要求的范围内做出各种变形或修改,这并不影 响本发明的实质内容。