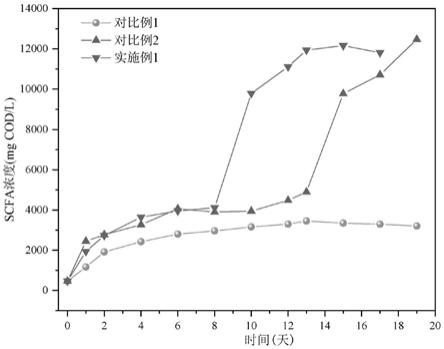
1.本发明属于废弃生物质处理及资源化利用领域,具体涉及一种提高剩余污泥和废油脂共发酵体系短链脂肪酸产量和纯度的方法。
背景技术:2.污水处理设施的生物处理单元通常会排放出大量的剩余污泥,这部分污泥如若处理处置不当则可能引发人畜疾病,存在巨大的环境风险。传统的处理处置技术成本较高,收益甚低。
3.以剩余污泥为底物发酵产短链脂肪酸(scfa)的技术实践近年来受到关注。scfa市场需求大,在环保、化工等领域有着广泛的用途:1)作为外加碳源提高污水处理厂脱氮除磷效率;2)作为微生物的底物合成绿色化工产品,如生物可降解塑料;3)作为醇类、氢气等清洁能源的合成前驱物,缓解能源危机。
4.然而,我国剩余污泥有机质比例低,碳氮比一般在7:1左右,远低于厌氧发酵合适的碳氮比20:1~30:1,作为单一发酵底物可能存在限制产酸微生物的增殖和潜在的氨氮抑制等问题。目前,补加富碳物质调节剩余污泥碳氮比的做法被广泛采用。
5.我国餐饮行业每年产生约500万吨的废油脂,丧失食用价值且具有健康风险的此类废油脂的资源化利用一直是一个巨大的挑战。废油脂富碳,可以通过将废油脂与剩余污泥共发酵的形式解决剩余污泥发酵产酸过程碳氮比失衡的问题,且废油脂几乎不含氮元素,易于调控复合底物的碳氮比。但是通过废油脂厌氧降解的相关研究发现,废油脂代谢过程产生的如油酸、棕榈酸等长链脂肪酸(long
‑
chain fatty acid,lcfa)容易发生积累对厌氧微生物有着强抑制作用。剩余污泥和废油脂碱性共发酵体系中,随着废油脂水解产物lcfa积累底物的水解酸化过程受到严重抑制。虽然lcfa通过β氧化可转化为scfa,但是在碱性发酵系统中缺乏相应的功能菌群,所以lcfa的厌氧降解难以进行,scfa产量受到严重抑制。
技术实现要素:6.本发明的目的在于克服现有技术的不足,提供一种提高剩余污泥和废油脂共发酵体系短链脂肪酸产量和纯度的方法。
7.为实现上述目的,本发明采用的技术方案是:
8.提高剩余污泥和废油脂共发酵体系短链脂肪酸产量和纯度的方法,包括以下步骤:
9.s1、将取自污水厂的剩余污泥浓缩,接着在反应容器中将浓缩的剩余污泥与废油脂混合,得到发酵底物,发酵底物中的c、n元素质量比为100~110:5;
10.s2、在步骤s1得到的发酵底物中加入硫酸钠,得到初级调制发酵底物,初级调制发酵底物中的c、s元素质量比为8~10:1;
11.s3、在步骤s2得到的初级调制发酵底物中加入颗粒活性炭,得到目标调制发酵底物;
12.s4、通过发酵装置调控反应容器内的反应温度和ph分别为30~35℃和9~10,然后在搅拌状态下进行厌氧发酵,发酵周期为15~20天,发酵完成后过滤,得到发酵液。
13.优选的,步骤s3中,所述颗粒活性炭的投加量与步骤s1中的废油脂添加量的质量比为2~4:1。
14.优选的,步骤s3中,所述颗粒活性炭的目数为60~100。
15.优选的,步骤s4中,所述反应容器的初始容积负荷为20
±
5g vs/(l
·
d)。
16.优选的,步骤s4中,所述搅拌速率设置为600~650rmp。
17.优选的,步骤s4中,所述发酵液过滤过程,先通过滤网对发酵液中的颗粒活性炭进行过滤并回收,然后再通过陶瓷膜对滤液进行再次过滤。
18.进一步优选的,所述滤网的目数大于颗粒活性炭的目数。
19.本发明与现有技术相比,其有益效果在于:
20.(1)本发明提供的提高剩余污泥和废油脂共发酵体系短链脂肪酸产量和纯度的方法,在碱性发酵的基础上,通过引入外源电子受体硫酸盐,强化硫酸盐还原代谢过程,进而协同强化厌氧发酵体系中长链脂肪酸向乙酸的分解代谢,在缓解长链脂肪酸抑制的同时显著提升末端发酵液中短链脂肪酸的产量和纯度,能够有效推进含油脂废弃生物质发酵产酸的规模化应用;
21.(2)本发明通过投加颗粒活性炭(gac),竞争性吸附废油脂水解产生的lcfa,减少微生物表面lcfa吸附量,进一步缓解lcfa对功能菌群的抑制作用,能够显著加快发酵体系scfa的生成速率,提升共发酵系统的产酸效能,对于剩余污泥和餐饮废油脂的资源化利用具有积极的推动作用;
22.(3)本发明不仅适用于废油脂与剩余污泥的共发酵体系,也适用于废油脂作为单一发酵底物的发酵体系以及和其它废弃生物质的共发酵体系中产酸效能的提升;
23.(4)本发明有利于解决污水厂污泥、餐厨废油脂处理处置两大难点问题,回收的scfa可为污废水处理提供廉价碳源,在碳中和背景下具有明显的碳补偿效果,环境效益、社会效益明显。
附图说明
24.图1为本发明实施例1、对比例1和对比例2中所产生的发酵液中的scfa的产量变化图;
25.图2为本发明实施例1、对比例1和对比例2中所产生的发酵液中的scfa产量达到最大时scfa组分的结构比例图。
26.图3为本发明实施例1、对比例1和对比例2中发酵液中scfa产量达到最大时的酸化率和酸产率。
27.图4为本发明实施例1发酵液中的lcfa含量变化图。
28.图5为本发明实施例1和对比例2中的so
24
‑
浓度变化图。
具体实施方式
29.为了使本发明的目的、技术方案及优点更加清楚明白,以下结合附图及实施例,对本发明进行进一步详细说明。应当理解,此处所描述的具体实施例仅用以解释本发明,并不用于限定本发明,以下实施例中所采用的试剂均为市售。
30.以下实施例中的剩余污泥来自于市政污水处理厂的剩余污泥,废油脂为餐厨废油脂,具体取自某炸鸡店,基本理化性质为:碘值108g/100g,酸价2.3mg/g,皂化值197.5%,过氧化氢值0.21g/100g,固定碳3.57%,含水率0.0030%。
31.以下实施例和对比例的发酵过程中均在发酵装置中进行,发酵装置为市售,厂家为北京满仓科技有限公司,型号mc
‑
acph
‑
30a。
32.实施例1
33.本发明实施例提供了一种提高剩余污泥和废油脂共发酵体系短链脂肪酸产量和纯度的方法,具体包括以下步骤:
34.s1、将取自某污水厂的剩余污泥浓缩至9000mg/l(vss计),接着将浓缩的剩余污泥与废油脂在有效容积为500ml的反应容器中混合,得到发酵底物,发酵底物中的c、n元素质量比为105:5;
35.s2、在步骤s1得到的发酵底物中加入硫酸钠,得到初级调制发酵底物,初级调制发酵底物中的c、s元素质量比为9:1;
36.s3、在步骤s2得到的初级调制发酵底物中加入颗粒活性炭,得到目标调制发酵底物;
37.其中,颗粒活性炭的投加量与步骤s1中的废油脂添加量的质量比为3:1,颗粒活性炭的目数为80;
38.s4、通过发酵装置调控反应容器内的反应温度和ph分别为35℃和10,然后在搅拌状态下进行厌氧发酵,发酵周期为19天,发酵完成后,收集发酵液,将发酵液过滤,得到富含短链脂肪酸且以乙酸为主体的发酵液。
39.其中,反应容器的初始容积负荷为20g vs/(l
·
d),搅拌速率设置为600rmp,发酵液过滤是先通过目数大于颗粒活性炭的目数的滤网过滤回收发酵液中的颗粒活性炭,然后再通过陶瓷膜过滤去除悬浮不溶物。
40.实施例2
41.本发明实施例提供的提高剩余污泥和废油脂共发酵体系短链脂肪酸产量和纯度的方法,具体包括以下步骤:
42.s1、将取自某污水厂的剩余污泥浓缩至vs在9000mg/l,接着将浓缩的剩余污泥与废油脂在有效容积为500ml的反应容器中混合,得到发酵底物,发酵底物中的c、n元素质量比为100:5;
43.s2、在步骤s1得到的发酵底物中加入硫酸钠,得到初级调制发酵底物,初级调制发酵底物中的c、s元素质量比为8:1;
44.s3、在步骤s2得到的初级调制发酵底物中加入颗粒活性炭,得到目标调制发酵底物;
45.其中,颗粒活性炭的投加量与步骤s1中的废油脂添加量的质量比为2:1,颗粒活性炭的目数为60;
46.s4、通过发酵装置调控反应容器内的反应温度和ph分别为32℃和10,然后在搅拌状态下进行厌氧发酵,发酵周期为15天,发酵完成后,收集发酵液,将发酵液过滤,得到富含短链脂肪酸且以乙酸为主体的发酵液。
47.其中,反应容器的初始容积负荷为15g vs/(l
·
d),搅拌速率设置为650rmp,发酵液过滤过程是先通过大于颗粒活性炭目数的滤网过滤回收发酵液中的颗粒活性炭,然后再通过陶瓷膜过滤去除悬浮不溶物。
48.实施例3
49.本发明实施例提供的提高剩余污泥和废油脂共发酵体系短链脂肪酸产量的方法,具体包括以下步骤:
50.s1、将取自某污水厂的剩余污泥浓缩至vs在9000mg/l,接着将浓缩的剩余污泥与废油脂在有效容积为500ml的反应容器中混合,得到发酵底物,发酵底物中的c、n元素质量比为110:5;
51.s2、在步骤s1得到的发酵底物中加入硫酸钠,得到初级调制发酵底物,初级调制发酵底物中的c、s元素质量比为10:1;
52.s3、在步骤s2得到的初级调制发酵底物中加入颗粒活性炭,得到目标调制发酵底物;
53.其中,颗粒活性炭的投加量与步骤s1中的废油脂添加量的质量比为4:1,颗粒活性炭的目数为100;
54.s4、通过发酵装置调控调整反应容器内的反应温度和ph分别为30℃和10,然后在搅拌状态下进行厌氧发酵,发酵周期为20天,发酵完成后,收集发酵液,将发酵液过滤,得到富含短链脂肪酸且以乙酸为主体的发酵液。
55.其中,反应罐体的初始容积负荷为25gvs/(l
·
d),搅拌速率设置为650rmp,发酵液过滤过程是先通过目数大于颗粒活性炭的滤网过滤回收发酵液中的颗粒活性炭,然后再通过陶瓷膜过滤去除悬浮不溶物。
56.对比例1
57.对比例1与本发明实施例提供的提高剩余污泥和废油脂共发酵体系短链脂肪酸产量和纯度的方法相同,区别仅在于对比例1提供的方法中未加入硫酸钠和颗粒活性炭。
58.对比例2
59.对比例2与本发明实施例提供的提高剩余污泥和废油脂共发酵体系短链脂肪酸产量和纯度的方法均相同,区别仅在于对比例2提供的方法中未加入颗粒活性炭。
60.下面对实施例1、对比例1和2提供的提高剩余污泥和废油脂共发酵体系短链脂肪酸产量和纯度的方法中所产生的发酵液scfa产量进行分析。通过图1可以看出,对比例1得到的发酵液在第13天scfa产量达到最大,浓度为3452mg cod/l,而对比例2得到的发酵液在第13天前scfa产量缓慢增加,在之后的一周内快速上升,第19天达到最大,约为12477mg/l,是对比例1发酵液中scfa产量的3.60倍。本发明实施例1的发酵液中前期与对比例2同一时刻的scfa产量并无太大差异,但在第8天后远超过对比例2,大约在第13天达到最大,约为11940mg/l,为对比例1的3.45倍。因此,通过添加硫酸盐剩余污泥
‑
废油脂共发酵体系短链脂肪酸产量大为提升,而在添加硫酸盐的基础上投加gac还能缩短scfa产量达到最大的时间。
61.图2为实施例1、对比例1和2中的发酵液中的scfa产量达到最大时的scfa组分结构比例图。通过图2可以看出,对比例2和实施例1的scfa以乙酸占绝对优势,对比例2中scfa的组分占比排序为乙酸(80.7%)>异戊酸(5.2%)≈正丁酸(5.1%)>丙酸(4.5%)>异丁酸(3.6%)>正戊酸(0.9%);本发明实施例1发酵液中scfa的组分占比排序乙酸(78.4%)>丙酸(6.9%)>正丁酸(6.4%)>异戊酸(4.2%)>异丁酸(3.3%)>正戊酸(0.9%),而对比例1中scfa中的乙酸占比仅为52.3%,丙酸、异丁酸、异戊酸的占比均在10%以上。可见,硫酸盐明显提升了剩余污泥
‑
废油脂共发酵体系短链脂肪酸中乙酸的纯度,且通过对比例2与本发明实施例1发酵液的组分结构对比可知,本发明实施例1的组分含量比例与对比例2的组分含量并不完全相同,说明本发明实施例1中加入的颗粒活性炭与硫酸盐之间产生了协同作用,从而使得发酵液的组分含量发生变化。
62.图3为实施例1、对比例1和对比2中的scfa产量达到最大时的酸化率和酸产率。对比例1的酸化率和酸产率仅为20.28%和140.91mgcod scfa/g vs,而对比例2则达到了80.43%和618.64mgcod scfa/gvs,实施例1的酸化率则达到了96.60%,酸产率也与对比例2相当,为584.38mgcod scfa/g vs。通过图3结果可以说明,本发明实施例1通过添加硫酸盐显著改善了剩余污泥
‑
废油脂共发酵体系的产酸效能,且通过添加gac进一步提升了发酵液的酸化率。
63.图4为本发明实施例1中发酵液中的lcfa的含量变化图。通过图4可以看出,本发明实施例1的发酵液存在三种主要的lcfa,分别是油酸、亚油酸和棕榈酸,且实施例1中scfa在第8~10天时快速积累,同时主要的lcfa明显减少。
64.本发明实施例1和对比例2中的浓度变化情况如图5所示,本发明实施例1的发酵液在发酵第1~10天时间内,其发酵液中的浓度从4340mg s/l减少至595mg s/l,表明发酵体系的转化与lcfa的降解是同步进行的,硫酸盐的代谢促进了lcfa的β氧化降解。虽然对比例2也同样出现so
24
‑
减少的情况,从3900mg s/l减少至276mg s/l,并且scfa快速积累,但是此过程却发生在发酵第10~16天,通过上述对比例2和本发明实施例1的so
24
‑
浓度变化情况研究,证实了硫酸盐代谢可以促进lcfa的β氧化降解,且本发明实施例1通过颗粒活性炭与硫酸盐相结合,还能够加快发酵体系so
24
‑
的转化与lcfa的降解速率。
65.综上所述,本发明实施例提供的提高剩余污泥和废油脂共发酵体系短链脂肪酸产量和纯度的方法,通过借助的转化为废油脂水解产物的lcfa的β氧化降解创造条件,从而显著提升发酵液中短链脂肪酸的含量,并且提升了产品的纯度和产酸效能,而且投加的颗粒活性炭与硫酸盐相结合,显著加快了发酵体系scfa的生成速率,对于剩余污泥和餐饮废油脂的协同资源化具有积极的推动作用。
66.以上所述实施例仅表达了本发明的具体实施方式,其描述较为具体和详细,但并不能因此而理解为对发明专利范围的限制。应当指出的是,对于本领域的普通技术人员来说,在不脱离本发明构思的前提下,还可以做出若干变形和改进,这些都属于本发明的保护范围。