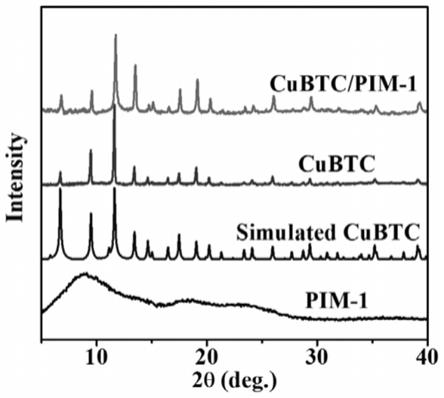
1.本发明属于新型功能材料技术领域,主要提供了一种超疏水金属有机骨架材料及其制备方法与应用。
背景技术:2.近年,金属有机骨架材料作为一种由金属离子或金属团簇与有机连接体配位而成的多孔晶体材料,展现出众多特性如简易的合成方法,较大的比表面积、独特的多孔结构和化学多样性等,被广泛应用于气体存储、分子分离、催化、能量贮存和生物医学等。金属有机骨架材料的功能及应用与其固有的物理和化学性质密切相关。大部分金属有机骨架材料,面临着水敏感性,耐酸碱性差以及可加工性弱的瓶颈,如cubtc、mof
‑
5、mil
‑
53等,当其处于潮湿环境下或长期暴露在空气中时,金属与有机连接体的配位键极易水解,进而导致晶体结构的瓦解,比表面积下降,功能性减弱,极大限制金属有机骨架材料的实际应用。因此,开发高稳定性的金属有机骨架材料具有较大的实际应用价值及意义。
3.迄今为止,研究者开发出多种提高金属有机骨架材料水稳定性的策略,主要有(1)采用高价金属阳离子或疏水性的配体以形成键能更大的金属配位键或构建疏水系统,但寻求合适的金属离子和配体需耗费大量时间。(yuan et al,adv.mater.,2018,30,1704303;furukawa et al,j.am.chem.soc.2014,136,4369
‑
4381.)(2)疏水性官能团的引入,将疏水官能团与分子结构中的活性位点反应,将其引入到金属有机骨架材料中以增强疏水性。然而,研究者难以获得合适的疏水官能团与配体或活性位点进行反应,且在官能团引入的同时,会改变金属有机骨架材料固有的孔隙率和物理化学特性。(sun et al,angew.chem.int.ed.,2019,58,7405;nguyen at al,j.am.chem.soc.,2010,132,4560.)(3)构建表面疏水保护层,通过将疏水性分子或聚合物沉积在金属有机骨架材料表面提升其水稳定性。然而,无孔的疏水涂层会降低金属有机骨架材料的比表面积和表面传质速度。(carn
é‑
s
á
nchez et al,adv.mater.,2015,27,869;zhang et al,j.am.chem.soc.,2014,136,16978.)综上,探索和开发一种简便通用的金属有机骨架改性方法以提高其疏水性,并保持金属有机骨架材料固有的多孔特性,对其实际应用具有重要意义。
技术实现要素:4.为了克服上述现有技术的缺点与不足,本发明的首要目的在于提供一种超疏水金属有机骨架材料的制备方法。
5.本发明另一目的在于提供上述方法制备得到的超疏水金属有机骨架材料。
6.本发明再一目的在于提供上述超疏水金属有机骨架材料在气体储存、分子分离、催化、传感等中的应用。
7.本发明的目的通过下述方案实现:
8.一种超疏水金属有机骨架材料的制备方法,所述方法按如下步骤进行:
9.(1)制备疏水性微孔聚合物:将单体a、单体b、碳酸钾与有机溶剂混合后,进行加热
反应,反应完成后得到疏水性微孔聚合物;
10.(2)制备金属有机骨架材料:将金属盐、有机配体和溶剂,混合均匀后得到合成溶液,随后在密闭条件下进行加热反应,反应结束后,获得金属有机骨架颗粒;
11.(3)构建超疏水金属有机骨架材料:将步骤(1)中合成的疏水性微孔聚合物溶解在溶剂中,得到微孔聚合物溶液,随后将步骤(2)制备出的金属有机骨架颗粒,加入上述微孔聚合物溶液中,并进行搅拌,获得金属有机骨架/微孔聚合物混合溶液,分离出混合颗粒干燥后获得具备疏水微孔聚合物涂层的超疏水金属有机骨架材料。
12.步骤(1)所述单体a为5,5’,6,6
’‑
四羟基
‑
3,3,3’,3
’‑
四甲基
‑
1,1
’‑
螺旋双茚满、2,2’,3,3
’‑
四羟基
‑
1,1
’‑
联萘和1,2,4,5
‑
四羟基苯中的至少一种;
13.步骤(1)所述单体b为四氟对苯二腈、十氟联苯和十氟联苯酮中的至少一种;
14.步骤(1)所述有机溶剂为n
‑
甲基吡咯烷酮、n
‑
n二甲基甲酰胺、n,n
‑
二甲基乙酰胺、n,n
‑
二乙基甲酰胺和甲苯中的至少一种;
15.步骤(1)所述碳酸钾与有机溶剂之比为0.01~10g/ml,优选0.1~1g/ml;
16.步骤(1)所述单体a与单体b的物质的量之比为1:0.5~5,优选1:1~2;
17.步骤(1)所述加热反应为在100~200℃搅拌10~60min。优选的,所述加热反应在氮气氛围下进行。
18.步骤(1)所述加热反应完成后还包括提纯步骤,具体为将所得产物加入甲醇中,随后用水和丙酮搅拌洗涤,最后在80~150℃下真空干燥24~72h。
19.步骤(2)所述金属盐中的金属元素为v、zn、ti、cr、cu、co、fe、ni、mg、cd、sr、zr、nb、mo、ba、mg、mn、al和gd中的至少一种;优选的所述金属盐中的金属元素为zn、al、cu、cr和zr中的至少一种;所述的金属盐为金属的硝酸盐、氯化盐、硫酸盐和醋酸盐中的至少一种;更优选的,所述金属盐具体优选为硝酸锌、硝酸铜、氯化锆、硝酸铬和硝酸铝中的至少一种。
20.步骤(2)所述的有机配体为均苯三甲酸、苯二甲酸和2
‑
甲基咪唑中的至少一种;
21.步骤(2)所述溶剂为甲醇、乙醇、丙醇、异丙醇、叔丁醇、乙二醇、丙三醇、吡咯烷酮、n
‑
n二甲基甲酰胺、n,n
‑
二甲基乙酰胺和n,n
‑
二乙基甲酰胺中的至少一种;
22.步骤(2)所述金属盐与有机配体的物质的量之比为1:0.5~5,优选1:1~2;
23.步骤(2)所述金属盐与溶剂的物质的量之比为1:50~600,优选1:100~300;
24.步骤(2)所述加热反应为在100~220℃下热处理5~48h。
25.优选的,步骤(2)所述加热反应完成后,还包括提纯步骤,将合成的粉末用溶剂洗涤,并在50~100℃进行真空干燥6~24h。
26.步骤(3)所述溶剂为二氯甲烷、三氯甲烷和四氢呋喃中的至少一种;所述微孔聚合物溶液的浓度为0.01~10wt%,优选0.1~2wt%;
27.步骤(3)所述搅拌的时间为1
‑
10h。
28.优选的,步骤(3)的操作过程在室温下进行。
29.一种超疏水金属有机骨架材料,通过上述方法制备得到。
30.所述超疏水金属有机骨架材料在气体储存、分子分离、催化、传感等中的应用。
31.本发明相对于现有技术,具有如下的优点及有益效果:
32.(1)通过简单高效的涂覆方法,在金属有机骨架材料表面构建疏水性涂层,解决金属有机骨架材料水稳定性差的问题。
33.(2)超薄的微孔聚合物涂层,不仅显著提高金属有机骨架材料的疏水性能,同时其多孔特性能够维持金属有机骨架材料原有的孔道结构及比表面积。
34.(3)本发明方法具有广泛的通用性,可以适用于多种金属有机骨架材料,具有很好的应用价值和前景。
附图说明
35.图1为本发明实施例1制备的超疏水cubtc/pim
‑
1复合材料和对比实施例中cubtc的接触角图。
36.图2为本发明实施例1制备的超疏水cubtc/pim
‑
1复合材料和对比实施例中cubtc以及模拟的cubtc的xrd图。
37.图3为本发明实施例1制备的超疏水cubtc/pim
‑
1复合材料和对比实施例中cubtc的xps图。
38.图4为本发明实施例1制备的超疏水cubtc/pim
‑
1复合材料的tem图;
39.图5为本发明实施例1制备的超疏水cubtc/pim
‑
1复合材料和对比实施例中cubtc在水处理前后氮气吸附
‑
脱附图。
40.图6为本发明实施例1制备的超疏水cubtc/pim
‑
1复合材料和对比实施例中cubtc在水处理后的电子照片和sem图。
41.图7为本发明实施例1制备的超疏水cubtc/pim
‑
1复合材料和对比实施例中cubtc在水处理后的xrd图。
具体实施方式
42.下面结合实施例和附图对本发明作进一步详细的描述,但本发明的实施方式不限于此。本发明所述室温和未指明的温度为20~35℃。
43.实施例中所用试剂如无特殊说明均可从市场常规购得。
44.实施例1
45.疏水性微孔聚合物为pim
‑
1,金属有机骨架为cubtc,合成的超疏水金属有机骨架为cubtc/pim
‑
1。
46.制备方法:
47.(1)疏水性微孔聚合物的合成:采用高温合成法,将5,5’,6,6
’‑
四羟基
‑
3,3,3’,3
’‑
四甲基
‑
1,1
’‑
螺旋双茚满(3.404g)、四氟对苯二腈(2.001g)和碳酸钾(3.414g)加入到三口烧瓶中,通入氮气30min后,加入n
‑
甲基吡咯烷酮(20ml)和甲苯(10ml),随后将上述混合物转移至160℃的油浴锅中搅拌40min。待反应结束后,得到的粘性液体倒至甲醇中,随后用去离子水和丙酮搅拌洗涤,最后在120℃下真空干燥48h,即可获得疏水性微孔聚合物。
48.(2)金属有机骨架cubtc的合成:采用金属有机骨架常用的水热合成法,将硝酸铜(4.154g)加入到去离子水(30ml)中,在室温下搅拌10min;将均苯三甲酸(2.0g)加入到n,n
‑
二甲基甲酰胺(30ml)和乙醇(30ml)中,在室温下搅拌10min;随后将上述两种澄清溶液进行搅拌混合均匀后转移至衬有聚四氟乙烯的不锈钢高压釜中,放进烘箱中在100℃热处理10h,反应结束待到室温冷却后,将得到的粉末用n,n
‑
二甲基甲酰胺和甲醇搅拌洗涤。最后,在80℃下进行真空干燥12h,得到金属有机骨架cubtc(图1为接触角图,图2为其xrd图,图3
为其xps图,图5为氮气吸附
‑
脱附图),备用。
49.(3)超疏水cubtc/pim
‑
1的制备:将步骤(1)合成的微孔聚合物pim
‑
1(0.015g)加入到三氯甲烷(10ml)中,在室温下搅拌20min使其溶解,随后将步骤(2)得到的金属有机骨架cubtc(0.5g)加入到上述微孔聚合物溶液中,室温下搅拌5h,均匀涂覆后,通过离心分离得到复合颗粒,在80℃下真空干燥12h即可得到超疏水cubtc/pim
‑
1(图1为接触角图,图2为其xrd图,图3为其xps图,图4为其tem图,图5为氮气吸附
‑
脱附图)。
50.如图1所示,对比cubtc而言,cubtc/pim
‑
1材料展现出其超疏水性;如图2中xrd图谱所示,所制备得到的金属有机骨架cubtc和cubtc/pim
‑
1材料的xrd图与模拟出的xrd图极其类似,表明在该实验条件下可以成功制备出金属有机骨架cubtc,同时在进行微孔聚合物涂覆后,其晶体结构保持不变;图3所示的xps图,对比cubtc而言,超疏水cubtc/pim
‑
1材料出现了新的c
‑
o
‑
c峰,阐明了cubtc/pim
‑
1的成功制备;对于图4的tem而言,通过简单的涂覆方法可在cubtc表面得到超薄均匀的疏水性聚合物层。同时对cubtc/pim
‑
1材料进行氮气吸附
‑
脱附实验,实验结果如图5所示,表明在涂覆改性后依然能够维持cubtc原有的孔道结构及比表面积。最后,对cubtc和cubtc/pim
‑
1材料在进行三天水环境处理后,从实验结果图5、图6和图7所示,其晶体结构和内部孔径结构保持不变。
51.实施例2
52.疏水性微孔聚合物为pim
‑
1,金属有机骨架为uio
‑
66
‑
nh2,合成的超疏水金属有机骨架为uio
‑
66
‑
nh2/pim
‑
1。
53.制备方法:
54.(1)疏水性微孔聚合物的合成:采用高温合成法,将5,5’,6,6
’‑
四羟基
‑
3,3,3’,3
’‑
四甲基
‑
1,1
’‑
螺旋双茚满(5.106g)、四氟对苯二腈(3.002g)和碳酸钾(5.121g)加入到三口烧瓶中,通入氮气40min后,加入n
‑
甲基吡咯烷酮(30ml)和甲苯(15ml),随后将上述混合物转移至150℃的油浴锅中搅拌40min。待反应结束后,得到的粘性液体倒至甲醇中,随后用去离子水和丙酮搅拌洗涤,最后在110℃下真空干燥36h,即可获得疏水性微孔聚合物。
55.(2)金属有机骨架uio
‑
66
‑
nh2的合成:采用金属有机骨架常用的水热合成法,分别称取氯化锆(0.48g)和2
‑
氨基对苯二甲酸(0.372g),随后加入n,n
‑
二甲基甲酰胺(40ml)和去离子水(0.19ml)在室温搅拌15min,随后将上述溶液转移至衬有聚四氟乙烯的不锈钢高压釜中,在120℃条件下热反应结晶24h,待反应体系冷却至室温,通过离心得到粉末,将粉末分别用n,n
‑
二甲基甲酰胺和甲醇洗涤,最后,将上述粉末在85℃进行真空干燥24h即可得到金属有机骨架uio
‑
66
‑
nh2,备用。
56.(3)超疏水uio
‑
66
‑
nh2/pim
‑
1的制备:将步骤(1)合成的微孔聚合物pim
‑
1(0.023g)加入到三氯甲烷(15ml)中,在室温下搅拌30min使其溶解,随后将步骤(2)得到的金属有机骨架uio
‑
66
‑
nh2(0.75g)加入到上述微孔聚合物溶液中,室温下搅拌6h,均匀涂覆后,通过离心分离得到复合颗粒,在75℃下真空干燥12h即可得到超疏水uio
‑
66
‑
nh2/pim
‑
1。
57.实施例3
58.疏水性微孔聚合物为pim
‑
1,金属有机骨架为mil
‑
101,合成的超疏水金属有机骨架为mil
‑
101/pim
‑
1。
59.制备方法:
60.(1)疏水性微孔聚合物的合成:采用高温合成法,将5,5’,6,6
’‑
四羟基
‑
3,3,3’,3
’‑
四甲基
‑
1,1
’‑
螺旋双茚满(6.808g)、四氟对苯二腈(4.002g)和碳酸钾(8.28g)加入到三口烧瓶中,通入氮气50min后,加入n
‑
n二甲基甲酰胺(40ml),随后将上述混合物转移至170℃的油浴锅中搅拌40min。待反应结束后,得到的粘性液体倒至甲醇中,随后用去离子水和丙酮搅拌洗涤,最后在110℃下真空干燥36h,即可获得疏水性微孔聚合物。
61.(2)金属有机骨架mil
‑
101的合成:采用金属有机骨架常用的水热合成法,分别称量硝酸铬(1.2g)和对苯二甲酸(0.5g)放置在铁氟龙中,加入浓度为5mol/l氢氟酸溶液(0.6ml)和去离子水(15ml),随后用玻璃棒进行15min搅拌,将铁氟龙放置在不锈钢高压釜中,在220℃下加热8h,反应结束待到室温冷却后,离心得到粉末,将得到的粉末在40℃下用n,n
‑
二甲基甲酰胺和甲醇搅拌洗涤。最后,在80℃下进行真空干燥24h,得到金属有机骨架mil
‑
101,备用。
62.(3)超疏水mil
‑
101/pim
‑
1的制备:将步骤(1)合成的微孔聚合物pim
‑
1(0.030g)加入到三氯甲烷(20ml)中,在室温下搅拌40min使其溶解,随后将步骤(2)得到的金属有机骨架mil
‑
101(1g)加入到上述微孔聚合物溶液中,室温下搅拌6h,均匀涂覆后,通离心分离得到复合颗粒,在80℃下真空干燥12h即可得到超疏水mil
‑
101/pim
‑
1。
63.实施例4
64.疏水性微孔聚合物为pim
‑
2,金属有机骨架为mil
‑
53,合成的超疏水金属有机骨架为mil
‑
53/pim
‑
2。
65.制备方法:
66.(1)疏水性微孔聚合物的合成:采用高温合成法,将5,5’,6,6
’‑
四羟基
‑
3,3,3’,3
’‑
四甲基
‑
1,1
’‑
螺旋双茚满(3.404g)、十氟联苯(3.341g)和碳酸钾(4.14g)加入到三口烧瓶中,通入氮气40min后,加入n
‑
甲基吡咯烷酮(20ml)和甲苯(10ml),随后将上述混合物转移至160℃的油浴锅中搅拌40min。待反应结束后,得到的粘性液体倒至甲醇中,随后用去离子水和丙酮搅拌洗涤,最后在110℃下真空干燥36h,即可获得疏水性微孔聚合物。
67.(2)金属有机骨架mil
‑
53的合成:采用金属有机骨架常用的水热合成法,将硝酸铝(0.8g)和对苯二甲酸(0.5g)加入n,n
‑
二甲基甲酰胺(15ml),在室温下搅拌20min;随后将上述溶液转移至衬有聚四氟乙烯的不锈钢高压釜中,放进烘箱中在120℃热处理24h,反应结束待到室温冷却后,通过离心得到粉末,将得到的粉末在50℃下用n,n
‑
二甲基甲酰胺和甲醇搅拌洗涤。最后,在80℃下进行真空干燥12h,得到金属有机骨架mil
‑
53,备用。
68.(3)超疏水mil
‑
53/pim
‑
2的制备:将步骤(1)合成的微孔聚合物pim
‑
2(0.045g)加入到三氯甲烷(30ml)中,在室温下搅拌60min使其溶解,随后将步骤(2)得到的金属有机骨架mil
‑
53(1.5g)加入到上述微孔聚合物溶液中,室温下搅拌8h,均匀涂覆后,通离心分离得到复合颗粒,在80℃下真空干燥24h即可得到超疏水mil
‑
53/pim
‑
2。
69.实施例5
70.疏水性微孔聚合物为pim
‑
6,金属有机骨架为zif
‑
8,合成的超疏水金属有机骨架为zif
‑
8/pim
‑
6。
71.制备方法:
72.(1)疏水性微孔聚合物的合成:采用高温合成法,将1,2,4,5
‑
四羟基苯(1.421g)、十氟联苯(3.341g)和碳酸钾(4.14g)加入到三口烧瓶中,通入氮气40min后,加入n
‑
甲基吡
咯烷酮(20ml)和甲苯(10ml),随后将上述混合物转移至160℃的油浴锅中搅拌40min。待反应结束后,得到的粘性液体倒至甲醇中,随后用去离子水和丙酮搅拌洗涤,最后在110℃下真空干燥36h,即可获得疏水性微孔聚合物。
73.(2)金属有机骨架zif
‑
8的合成:采用金属有机骨架常用的水热合成法,将硝酸锌(0.3g)和2
‑
甲基咪唑(0.66g)分别加入甲醇(14ml),在室温下搅拌25min,超声30min;随后将上述溶液转移至衬有聚四氟乙烯的不锈钢高压釜中,放进烘箱中在150℃热处理12h,反应结束待到室温冷却后,通过离心得到粉末,将得到的粉末用甲醇洗涤,最后,在80℃下进行真空干燥24h,得到金属有机骨架zif
‑
8,备用。
74.(3)超疏水zif
‑
8/pim
‑
6的制备:将步骤(1)合成的微孔聚合物pim
‑
6(0.050g)加入到三氯甲烷(40ml)中,在室温下搅拌60min使其溶解,随后将步骤(2)得到的金属有机骨架zif
‑
8(2g)加入到上述微孔聚合物溶液中,室温下搅拌8h,均匀涂覆后,通离心分离得到复合颗粒,在80℃下真空干燥24h即可得到超疏水zif
‑
8/pim
‑
6。
75.对比例(原始金属有机骨架材料,不经过疏水改性,直接暴露在水环境中)
76.金属有机骨架材料为cubtc。
77.制备方法:
78.金属有机骨架cubtc的合成:采用金属有机骨架常用的水热合成法,将硝酸铜(4.154g)加入到去离子水(30ml)中,在室温下搅拌10min;将均苯三甲酸(2.0g)加入到n,n
‑
二甲基甲酰胺(30ml)和乙醇(30ml)中,在室温下搅拌10min;随后将上述两种澄清溶液进行搅拌混合均匀后转移至衬有聚四氟乙烯的不锈钢高压釜中,放进烘箱中在100℃热处理10h,反应结束待到室温冷却后,将得到的粉末用n,n
‑
二甲基甲酰胺和甲醇搅拌洗涤。最后,在80℃下进行真空干燥12h,得到金属有机骨架cubtc。
79.由附图可知,原始cubtc在暴露于水环境后,其晶体结构和孔道结构均被破坏(如图5,6,和7所示),展现出较差的水稳定性。综上,结合实施例1和对比例的实验结果,证明通过涂覆法构建的超疏水微孔聚合物涂层,能够显著提升金属有机骨架材料的疏水特性,增强其水稳定性,并保持金属有机骨架材料固有的多孔特性。
80.上述实施例为本发明较佳的实施方式,但本发明的实施方式并不受上述实施例的限制,其他的任何未背离本发明的精神实质与原理下所作的改变、修饰、替代、组合、简化,均应为等效的置换方式,都包含在本发明的保护范围之内。