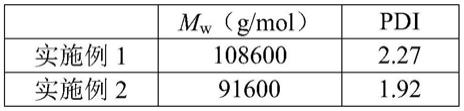
一种高分子量可生物降解聚对苯二甲酸
‑
己二酸
‑
乙二醇酯的制备方法
技术领域
1.本发明涉及可降解聚酯领域,尤其涉及一种高分子量可生物降解聚对苯二甲酸
‑
己二酸
ꢀ‑
乙二醇酯的制备方法。
背景技术:2.聚对苯二甲酸乙二醇酯(pet)是一种高性价比聚酯产品,被广泛应用于纺织、矿泉水瓶、食品包装、集成电路和工程塑料等领域。然而大量的pet废弃后,给自然界带来了严重的污染。芳香族聚酯如pet等与一定含量的易降解脂肪族聚酯共聚后得到的脂肪
‑
芳香共聚酯,可实现在自然界中的生物降解。脂肪
‑
芳香共聚酯中的聚对苯二甲酸
‑
己二酸
‑
乙二醇酯 (peat),是由对苯二甲酸、己二酸和乙二醇熔融缩聚而得,相对于目前市场上的聚对苯二甲酸
‑
己二酸
‑
丁二醇酯(pbat),生产过程中无四氢呋喃副产物生成,同时乙二醇原料成本低。
3.聚合物的分子量与性能之间有非常密切的关系,一般而言,分子量越高,聚合物的拉伸强度和冲击强度越高,更易满足后续纺丝、吹膜和注塑等工艺要求。脂肪
‑
芳香共聚酯因为含有柔性的脂肪族链段,结晶性和物理性能会降低,因而相对原先的pet需要更高的分子量,以满足纺丝和吹膜的使用要求。为提高脂肪
‑
芳香共聚酯分子量,人们常在聚合反应完成后,用六亚甲基二异氰酸酯、邻苯二甲酸酐、均苯四甲酸酐等扩链剂与聚酯末端的羟基或羧基反应,提高分子量。
4.例如,申请号为cn201210190249.4的发明专利申请公开了一种高分子量脂肪族
‑
芳香族共聚酯及其制备方法,其在缩聚反应完成后在双螺杆挤出机上采用扩链剂进行扩链,得到了mn=10000~100000的高分子量pbat。该方法存在以下问题:需要在聚合反应后增加扩链工序,成本高;并且,当采用异氰酸酯作为扩链剂时,在扩链和使用的过程中,散发的残余异氰酸酯容易对人体产生危害。
技术实现要素:5.为了解决上述技术问题,本发明提供了一种高分子量可生物降解聚对苯二甲酸
‑
己二酸
ꢀ‑
乙二醇酯的制备方法。本发明选择锡类催化剂,并加入稳定剂与之配合,能减少副反应的发生,使制得的聚酯具有较高的分子量。
6.本发明的具体技术方案为:一种高分子量可生物降解聚对苯二甲酸
‑
己二酸
‑
乙二醇酯的制备方法,包括以下步骤:以对苯二甲酸、己二酸和乙二醇为原料,加入锡类催化剂和稳定剂,经缩聚后,获得高分子量可生物降解聚对苯二甲酸
‑
己二酸
‑
乙二醇酯。
7.相较于锑类催化剂而言,本发明采用锡类催化剂,能加快缩聚反应速率,减少反应体系在高温反应容器内的停留时间,降低副反应所导致的分子量增加困难;而钛类催化剂虽然比锡类催化剂具有更高的催化活性,但其催化反应过程中产生的副产物较多,同样会导致分子量增加困难。因此,本发明选择锡类催化剂催化聚酯合成,能有效提高聚酯的分子
量。同时,本发明在反应体系中加入稳定剂,其与锡类催化剂配合,能进一步减少副反应的发生,促进聚酯分子量的增加。
8.作为优选,所述锡类催化剂为辛酸亚锡、异辛酸亚锡、草酸亚锡、氯化亚锡、氧化亚锡中的一种或多种。
9.作为优选,所述稳定剂为磷酸、烷基磷酸酯、磷酸三苯酯、烷基二芳基磷酸酯和混合烷基芳基磷酸酯中的一种或多种。
10.作为优选,所述对苯二甲酸和己二酸的摩尔比为1:0.1~10。
11.作为优选,所述对苯二甲酸和己二酸的总摩尔量与乙二醇的摩尔量之比为1:1.1~1.6。
12.作为优选,所述锡类催化剂的用量为对苯二甲酸和己二酸总摩尔量的0.005~0.02%。
13.作为优选,所述稳定剂的用量为锡类催化剂摩尔量的0.5~2倍。
14.作为优选,所述制备方法的具体过程如下:(1)将对苯二甲酸、己二酸和乙二醇投入反应容器中,在惰性气体氛围、160~220℃下进行第一阶段酯化,至停止出水;(2)加入占总用量30~40wt%的锡类催化剂和稳定剂后,加压至50~400kpa并升温至 220~260℃,进行第二阶段酯化,至出水量达到理论值的95%以上;(3)加入剩余的锡类催化剂和稳定剂后,抽真空至100pa以内,升温至230~270℃,进行缩聚反应,获得高分子量可生物降解聚对苯二甲酸
‑
己二酸
‑
乙二醇酯。
15.在步骤(1)和(2)中,采用逐级升温的分步酯化方式,能使易分解、易酯化的己二酸部分优先与乙二醇发生酯化反应生成低聚物,进而提高耐热能力,减少副反应的发生,促进分子量的增加。
16.在步骤(2)和(3)中,将锡类催化剂和稳定剂分成两批分别在特定阶段加入,即在第一阶段酯化后先加入部分锡类催化剂和稳定剂,进行第二阶段酯化,而后再加入剩余的锡类催化剂和稳定剂进行缩聚,作用在于:锡类催化剂一方面能够加快反应速率,减少聚酯在高温反应容器内的停留时间,从而减少副反应,但另一方面,其催化活性也会造成副反应增加,阻碍分子量的提高,因此,本发明在第一阶段酯化后加入部分锡类催化剂和稳定剂,能够缩短聚酯在高温反应容器内的停留时间,并且,第一阶段酯化后已形成耐热能力较高的低聚物,在此时加入锡类催化剂和稳定剂,能够减少因催化剂的催化活性而造成的副产物增加,因而能够促进聚酯分子量的提高。
17.此外,第一批加入的锡类催化剂和稳定剂过多或过少均造成聚酯分子量较低,原因在于:若第一批加入的锡类催化剂和稳定剂过多,则会由于催化剂对副反应的促进作用而导致第二阶段酯化时生成的副产物过多,阻碍聚酯分子量的增加;若第一批加入的锡类催化剂和稳定剂过少,则难以有效缩短聚酯在高温反应容器内的停留时间,同样会导致聚酯分子量较低。本发明将第一批加入的锡类催化剂和稳定剂控制在总质量的30~40wt%范围内,能够较大限度地减少副产物的生成,从而获得分子量更高的聚酯。
18.作为优选,步骤(3)中,所述抽真空的具体过程如下:在0.5~1.5h内将反应容器内的真空度提高到100pa以内。
19.进一步地,步骤(1)中,所述第一阶段酯化的温度为180~210℃,第二阶段酯化的
温度为230~250℃。
20.进一步地,步骤(3)中,所述缩聚反应的温度为230~250℃。
21.作为优选,步骤(3)中,缩聚反应开始1~2h后,加入4个羟基被保护基团保护的葡萄糖,所述4个羟基被保护基团保护的葡萄糖的摩尔量为对苯二甲酸和己二酸总摩尔量的 0.5~1.0%,继续进行缩聚反应,获得改性聚酯;将改性聚酯中羟基上的保护基团脱去,获得高分子量可生物降解聚对苯二甲酸
‑
己二酸
‑
乙二醇酯。
22.在聚对苯二甲酸
‑
己二酸
‑
乙二醇酯中,由于端羧基对酯键断裂的催化作用,会导致聚酯耐老化性能降低,但端羧基含量的减少又会导致聚酯生物降解性能的下降。为解决该问题,本发明在聚对苯二甲酸
‑
己二酸
‑
乙二醇酯的端羧基上接枝葡萄糖,使端羧基转变成酯键,从而提高聚酯的耐老化性能。当聚对苯二甲酸
‑
己二酸
‑
乙二醇酯被填埋后,由于葡萄糖端基上具有较多亲水性的羟基,能促进聚对苯二甲酸
‑
己二酸
‑
乙二醇酯与葡萄糖端基之间的酯键断裂,生成的游离葡萄糖能作为碳源而促进土壤微生物的生长繁殖;同时,聚对苯二甲酸
‑
己二酸
‑
乙二醇酯与葡萄糖端基之间的酯键断裂后会形成端羧基,对聚对苯二甲酸
‑
己二酸
‑
乙二醇酯的降解起到催化作用。通过以上方式,聚酯在正常使用时不易老化,而当聚酯被填埋后,能迅速在土壤微生物的作用下降解。
23.此外,本发明采用4个羟基被保护基团保护的葡萄糖,而非采用葡萄糖直接对端羧基进行接枝改性,原因在于:由于葡萄糖中存在多个羟基,能与多个端羧基反应,导致聚酯交联化,而聚酯的降解是从端基开始,交联导致聚酯端基减少,因而会导致聚酯降解缓慢。
24.进一步地,所述4个羟基被保护基团保护的葡萄糖为2,3,4,6
‑
四
‑
o
‑
乙酰基
‑
β
‑
d
‑
吡喃葡萄糖;将改性聚酯中羟基上的保护基团脱去的具体过程如下:将改性聚酯溶于有机溶剂中,向其中加入甲醇钠的甲醇溶液,反应3~6h后,分离产物,获得长链支化可降解聚酯。
25.与现有技术相比,本发明具有以下优点:(1)选择锡类催化剂,并加入稳定剂与之配合,能减少副反应的发生,使得到的聚酯具有较高的分子量;(2)采用逐级升温的分步酯化方式,能减少副反应,促进分子量的增加;(3)通过在端羧基上接枝葡萄糖,能提高聚对苯二甲酸
‑
己二酸
‑
乙二醇酯的耐老化性能,且当聚酯被填埋后,能迅速在土壤微生物的作用下降解。
具体实施方式
26.下面结合实施例对本发明作进一步的描述。
27.总实施例一种高分子量可生物降解聚对苯二甲酸
‑
己二酸
‑
乙二醇酯的制备方法,包括以下步骤:(1)将对苯二甲酸、己二酸和乙二醇投入反应容器中,在惰性气体氛围、160~220℃下进行第一阶段酯化,至停止出水;所述对苯二甲酸和己二酸的摩尔比为1:0.1~10;所述对苯二甲酸和己二酸的总摩尔量与乙二醇的摩尔量之比为1:1.1~1.6;(2)加入占总用量30~40wt%的锡类催化剂和稳定剂后,加压至50~400kpa并升
温至 220~260℃,进行第二阶段酯化,至出水量达到理论值的95%以上;所述锡类催化剂为辛酸亚锡、异辛酸亚锡、草酸亚锡、氯化亚锡、氧化亚锡中的一种或多种;所述锡类催化剂的用量为对苯二甲酸和己二酸总摩尔量的0.005~0.02%;所述稳定剂为磷酸、烷基磷酸酯、磷酸三苯酯、烷基二芳基磷酸酯和混合烷基芳基磷酸酯中的一种或多种;所述稳定剂的用量为锡类催化剂摩尔量的0.5~2倍;(3)加入剩余的锡类催化剂和稳定剂后,在0.5~1.5h内将反应容器内的真空度提高到100pa 以内,升温至230~270℃,进行缩聚反应,获得高分子量可生物降解聚对苯二甲酸
‑
己二酸
‑ꢀ
乙二醇酯。
28.可选地,步骤(3)中,缩聚反应开始1~2h后,加入4个羟基被保护基团保护的葡萄糖,所述4个羟基被保护基团保护的葡萄糖的摩尔量为所有有机酸总摩尔量的0.5~1.0%,继续进行缩聚反应,获得改性聚酯;将改性聚酯中羟基上的保护基团脱去,获得长链支化可降解聚酯。
29.实施例1一种高分子量可生物降解聚对苯二甲酸
‑
己二酸
‑
乙二醇酯的制备方法,包括以下步骤:(1)将415.33g对苯二甲酸、365.35g己二酸和540.73g乙二醇投入2.5l聚合反应釜中,搅拌10min后,充放氮气3次排除釜内空气,然后升温到190℃,在常压下进行第一阶段酯化,至停止出水;(2)在氮气保护下加入0.06g辛酸亚锡催化剂和0.048g磷酸三苯酯稳定剂后,加压至150kpa 并升温至230℃,进行第二阶段酯化,至出水量达到理论值的95%以上;(3)在氮气保护下加入0.14g辛酸亚锡催化剂和0.112g磷酸三苯酯稳定剂后,在1h内将反应容器内的真空度提高到100pa以内,升温至240℃,缩聚反应至搅拌功率达到约68w后,恢复到常压,出料,获得高分子量可生物降解聚对苯二甲酸
‑
己二酸
‑
乙二醇酯。
30.实施例2一种高分子量可生物降解聚对苯二甲酸
‑
己二酸
‑
乙二醇酯的制备方法,包括以下步骤:(1)将415.33g对苯二甲酸、365.35g己二酸和540.73g乙二醇投入2.5l聚合反应釜中,搅拌10min后,充放氮气3次排除釜内空气,然后升温到190℃,在常压下进行第一阶段酯化,至停止出水;(2)在氮气保护下加入0.07g氯化亚锡催化剂和0.04g磷酸甲基二苯基酯稳定剂后,加压至 150kpa并升温至230℃,进行第二阶段酯化,至出水量达到理论值的95%以上;(3)在氮气保护下加入0.12g氯化亚锡催化剂和0.08g磷酸甲基二苯基酯稳定剂后,在1h内将反应容器内的真空度提高到100pa以内,升温至240℃,缩聚反应至预定搅拌功率达到约 68w后,恢复到常压,出料,获得高分子量可生物降解聚对苯二甲酸
‑
己二酸
‑
乙二醇酯。
31.实施例3一种高分子量可生物降解聚对苯二甲酸
‑
己二酸
‑
乙二醇酯的制备方法,包括以下步骤:(1)将166.13g对苯二甲酸、584.56g己二酸和495.67g乙二醇投入2.5l聚合反应釜
中,搅拌10min后,充放氮气3次排除釜内空气,然后升温到180℃,在常压下进行第一阶段酯化,至停止出水;(2)在氮气保护下加入0.08g氧化二丁基锡催化剂和0.064g磷酸三甲酯稳定剂后,加压至 50kpa并升温至230℃,进行第二阶段酯化,至出水量达到理论值的95%以上;(3)在氮气保护下加入0.12g氧化二丁基锡催化剂和0.096g磷酸三甲酯稳定剂后,在1.5h 内将反应容器内的真空度提高到100pa以内,保持釜内温度为230℃,缩聚反应至搅拌功率达到约68w后,恢复到常压,出料,获得高分子量可生物降解聚对苯二甲酸
‑
己二酸
‑
乙二醇酯。
32.实施例4一种高分子量可生物降解聚对苯二甲酸
‑
己二酸
‑
乙二醇酯的制备方法,包括以下步骤:(1)将664.52g对苯二甲酸、146.14g己二酸和675.91g乙二醇投入2.5l聚合反应釜中,搅拌10min后,充放氮气3次排除釜内空气,然后升温到205℃,在常压下进行第一阶段酯化,至停止出水;(2)在氮气保护下加入0.02g草酸亚锡催化剂和0.008g磷酸三甲酯稳定剂后,加压至300kpa 并升温至240℃,进行第二阶段酯化,至出水量达到理论值的95%以上;(3)在氮气保护下加入0.03g草酸亚锡催化剂和0.012g磷酸三甲酯稳定剂后,在0.5h内将反应容器内的真空度提高到100pa以内,升温至250℃,缩聚反应至搅拌功率达到约68w后,恢复到常压,出料,获得高分子量可生物降解聚对苯二甲酸
‑
己二酸
‑
乙二醇酯。
33.实施例5一种高分子量可生物降解聚对苯二甲酸
‑
己二酸
‑
乙二醇酯的制备方法,包括以下步骤:(1)将415.33g对苯二甲酸、365.35g己二酸和540.73g乙二醇投入2.5l聚合反应釜中,搅拌10min后,充放氮气3次排除釜内空气,然后升温到190℃,在常压下进行第一阶段酯化,至停止出水;(2)在氮气保护下加入0.06g辛酸亚锡催化剂和0.048g磷酸三苯酯稳定剂后,加压至150kpa 并升温至230℃,进行第二阶段酯化,至出水量达到理论值的95%以上;(3)在氮气保护下加入0.14g辛酸亚锡催化剂和0.112g磷酸三苯酯稳定剂后,在1h内将反应容器内的真空度提高到100pa以内,升温至240℃,缩聚反应1h后,加入17g 2,3,4,6
‑
四
‑
o
‑ꢀ
乙酰基
‑
β
‑
d
‑
吡喃葡萄糖,继续进行缩聚反应至搅拌功率达到约68w后,恢复到常压,获得改性聚酯;(4)将改性聚酯溶于8l三氯甲烷中,向其中加入1l浓度为30wt%的甲醇钠的甲醇溶液,室温下反应5h后,旋蒸去除溶剂,经水洗、干燥后,获得高分子量可生物降解聚对苯二甲酸
ꢀ‑
己二酸
‑
乙二醇酯。
34.对比例1一种聚对苯二甲酸
‑
己二酸
‑
乙二醇酯的制备方法,包括以下步骤:(1)将415.33g对苯二甲酸、365.35g己二酸和540.73g乙二醇投入2.5l聚合反应釜中,搅拌10min后,充放氮气3次排除釜内空气,然后升温到190℃,在常压下进行第一阶段酯化,至停止出水;
(2)在氮气保护下加入0.06g乙二醇锑催化剂和0.048g磷酸三苯酯稳定剂后,加压至150kpa 并升温至230℃,进行第二阶段酯化,至出水量达到理论值的95%以上;(3)在氮气保护下加入0.14g乙二醇锑催化剂和0.112g磷酸三苯酯稳定剂后,在1h内将反应容器内的真空度提高到100pa以内,升温至240℃,缩聚反应至搅拌功率达到约68w后,恢复到常压,出料,获得聚对苯二甲酸
‑
己二酸
‑
乙二醇酯。
35.对比例2一种聚对苯二甲酸
‑
己二酸
‑
乙二醇酯的制备方法,包括以下步骤:(1)将415.33g对苯二甲酸、365.35g己二酸和540.73g乙二醇投入2.5l聚合反应釜中,搅拌10min后,充放氮气3次排除釜内空气,然后升温到190℃,在常压下进行第一阶段酯化,至停止出水;(2)在氮气保护下加入0.06g钛酸四丁酯催化剂和0.048g磷酸三苯酯稳定剂后,加压至150kpa 并升温至230℃,进行第二阶段酯化,至出水量达到理论值的95%以上;(3)在氮气保护下加入0.14g钛酸四丁酯催化剂和0.112g磷酸三苯酯稳定剂后,在1h内将反应容器内的真空度提高到100pa以内,升温至240℃,缩聚反应至搅拌功率达到约68w后,恢复到常压,出料,获得聚对苯二甲酸
‑
己二酸
‑
乙二醇酯。
36.对比例3一种聚对苯二甲酸
‑
己二酸
‑
乙二醇酯的制备方法,包括以下步骤:(1)将415.33g对苯二甲酸、365.35g己二酸和540.73g乙二醇投入2.5l聚合反应釜中,搅拌10min后,充放氮气3次排除釜内空气,然后升温到190℃,在常压下进行第一阶段酯化,至停止出水;(2)在氮气保护下加入0.06g辛酸亚锡催化剂后,加压至150kpa并升温至230℃,进行第二阶段酯化,至出水量达到理论值的95%以上;(3)在氮气保护下加入0.14g辛酸亚锡催化剂后,在1h内将反应容器内的真空度提高到100pa 以内,升温至240℃,缩聚反应至搅拌功率达到约68w后,恢复到常压,出料,获得聚对苯二甲酸
‑
己二酸
‑
乙二醇酯。
37.对比例4一种聚对苯二甲酸
‑
己二酸
‑
乙二醇酯的制备方法,包括以下步骤:(1)将415.33g对苯二甲酸、365.35g己二酸和540.73g乙二醇投入2.5l聚合反应釜中,搅拌10min后,充放氮气3次排除釜内空气,然后升温到250℃进行酯化反应,至出水量达到理论值的95%以上;(2)在氮气保护下加入0.20g辛酸亚锡催化剂和0.16g磷酸三苯酯稳定剂;(3)在1h内将反应容器内的真空度提高到100pa以内,升温至240℃,缩聚反应至搅拌功率达到约68w后,恢复到常压,出料,获得聚对苯二甲酸
‑
己二酸
‑
乙二醇酯。
38.对比例5一种聚对苯二甲酸
‑
己二酸
‑
乙二醇酯的制备方法,包括以下步骤:(1)将415.33g对苯二甲酸、365.35g己二酸和540.73g乙二醇投入2.5l聚合反应釜中,搅拌10min后,充放氮气3次排除釜内空气,然后升温到190℃,在常压下进行第一阶段酯化,至停止出水;(2)加压至150kpa并升温至230℃,进行第二阶段酯化,至出水量达到理论值的
95%以上; (3)在氮气保护下加入0.20g辛酸亚锡催化剂和0.16g磷酸三苯酯稳定剂后,在1h内将反应容器内的真空度提高到100pa以内,升温至240℃,缩聚反应至搅拌功率达到约68w后,恢复到常压,出料,获得高分子量可生物降解聚对苯二甲酸
‑
己二酸
‑
乙二醇酯。
39.对比例6一种聚对苯二甲酸
‑
己二酸
‑
乙二醇酯的制备方法,包括以下步骤:(1)将415.33g对苯二甲酸、365.35g己二酸和540.73g乙二醇投入2.5l聚合反应釜中,搅拌10min后,充放氮气3次排除釜内空气,然后在氮气保护下加入0.06g辛酸亚锡催化剂和 0.048g磷酸三苯酯稳定剂后,升温到190℃,在常压下进行第一阶段酯化,至停止出水;(2)加压至150kpa并升温至230℃,进行第二阶段酯化,至出水量达到理论值的95%以上; (3)在氮气保护下加入0.14g辛酸亚锡催化剂和0.112g磷酸三苯酯稳定剂后,在1h内将反应容器内的真空度提高到100pa以内,升温至240℃,缩聚反应至搅拌功率达到约68w后,恢复到常压,出料,获得高分子量可生物降解聚对苯二甲酸
‑
己二酸
‑
乙二醇酯。
40.对比例7一种聚对苯二甲酸
‑
己二酸
‑
乙二醇酯的制备方法,包括以下步骤:(1)将415.33g对苯二甲酸、365.35g己二酸和540.73g乙二醇投入2.5l聚合反应釜中,搅拌10min后,充放氮气3次排除釜内空气,然后升温到190℃,在常压下进行第一阶段酯化,至停止出水;(2)在氮气保护下加入0.04g辛酸亚锡催化剂和0.032g磷酸三苯酯稳定剂后,加压至150kpa 并升温至230℃,进行第二阶段酯化,至出水量达到理论值的95%以上;(3)在氮气保护下加入0.16g辛酸亚锡催化剂和0.128g磷酸三苯酯稳定剂后,在1h内将反应容器内的真空度提高到100pa以内,升温至240℃,缩聚反应至搅拌功率达到约68w后,恢复到常压,出料,获得高分子量可生物降解聚对苯二甲酸
‑
己二酸
‑
乙二醇酯。
41.对比例8一种高分子量可生物降解聚对苯二甲酸
‑
己二酸
‑
乙二醇酯的制备方法,包括以下步骤:(1)将166.13g对苯二甲酸、584.56g己二酸和495.67g乙二醇投入2.5l聚合反应釜中,搅拌10min后,充放氮气3次排除釜内空气,然后升温到180℃,在常压下进行第一阶段酯化,至停止出水;(2)在氮气保护下加入0.10g氧化二丁基锡催化剂和0.08g磷酸三甲酯稳定剂后,加压至50kpa 并升温至230℃,进行第二阶段酯化,至出水量达到理论值的95%以上;(3)在氮气保护下加入0.10g氧化二丁基锡催化剂和0.08g磷酸三甲酯稳定剂后,在1.5h内将反应容器内的真空度提高到100pa以内,保持釜内温度为230℃,缩聚反应至搅拌功率达到约68w后,恢复到常压,出料,获得高分子量可生物降解聚对苯二甲酸
‑
己二酸
‑
乙二醇酯。
42.对比例9一种聚对苯二甲酸
‑
己二酸
‑
乙二醇酯的制备方法,包括以下步骤:(1)将415.33g对苯二甲酸、365.35g己二酸和540.73g乙二醇投入2.5l聚合反应釜中,搅拌10min后,充放氮气3次排除釜内空气,然后升温到190℃,在常压下进行第一阶段酯
化,至停止出水;(2)在氮气保护下加入0.06g辛酸亚锡催化剂和0.048g磷酸三苯酯稳定剂后,加压至150kpa 并升温至230℃,进行第二阶段酯化,至出水量达到理论值的95%以上;(3)在氮气保护下加入0.14g辛酸亚锡催化剂和0.112g磷酸三苯酯稳定剂后,在1h内将反应容器内的真空度提高到100pa以内,升温至240℃,缩聚反应1h后,加入8.79g葡萄糖,继续进行缩聚反应至搅拌功率达到约68w后,恢复到常压,获得聚对苯二甲酸
‑
己二酸
‑
乙二醇酯。
43.测试例1聚酯的分子量对实施例1~5和对比例1~9制得的聚对苯二甲酸
‑
己二酸
‑
乙二醇酯进行重均分子量测试,结果见表1。
44.表1表1从表1可以看出:相较于对比例1~4而言,实施例1的聚酯分子量明显较高。以上结果表明: (1)相较于锑类催化剂(对比例1)和钛类催化剂(对比例2)而言,采用锡类催化剂(实施例1)能提高聚酯的分子量。推测原因在于:相较于锑类催化剂而言,本发明采用锡类催化剂,能加快缩聚反应速率,减少反应体系在高温反应容器内的停留时间,降低副反应所导致的分子量增加困难;而钛类催化剂虽然比锡类催化剂具有更高的催化活性,但其催化反应过程中产生的副产物较多,同样会导致分子量增加困难。
45.(2)相较于不使用稳定剂(对比例3)而言,在聚酯合成过程中加入稳定剂(实施例 1),有助于提高聚酯分子量。推测原因在于:稳定剂与锡类催化剂配合,能进一步减少副反应的发生,促进聚酯分子量的增加。
46.(3)相较于一步酯化(对比例4)而言,采用逐级升温的分步酯化方式(实施例1),能提高聚酯分子量。推测原因在于:分布酯化能使易分解、易酯化的己二酸部分优先与乙二醇发生酯化反应生成低聚物,进而提高耐热能力,减少副反应的发生,促进分子量的增加。
47.(4)相较于在第二阶段酯化后一次性加入所有催化剂和稳定剂(对比例5)而言,将其分成两批分别在第一阶段酯化后和第二阶段酯化后加入(实施例1),能够提高聚酯分子量。推测原因在于:若在第二阶段酯化后一次性加入所有催化剂和稳定剂,则会造成酯化反应速度较慢,导致聚酯在高温反应容器中的停留时间较长,不利于其分子量的增加。
48.(5)相较于将第一批催化剂和稳定剂在第一阶段酯化前加入(对比例6)而言,将其在第一阶段酯化后加入(实施例1),能够提高聚酯的分子量。推测原因在于:由于第一阶段酯化前,易分解、易酯化的己二酸尚未与乙二醇发生酯化反应生成低聚物,因而在此前加入催化剂会导致副反应增加,阻碍聚酯的分子量增长。
49.(6)当第一批加入的催化剂和稳定剂过少(对比例7,将实施例1中第一批加入的锡类催化剂和稳定剂占总用量的比例从30wt%减少到20wt%)时,聚酯的分子量较小。推测原因在于:若第一批加入的锡类催化剂和稳定剂过少,则难以有效缩短聚酯在高温反应容器内的停留时间,进而导致聚酯分子量较低。
50.(7)当第一批加入的催化剂和稳定剂过多(对比例8,将实施例3中第一批加入的锡类催化剂和稳定剂占总用量的比例从40wt%增加到50wt%)时,聚酯的分子量较小。推测原因在于:若第一批加入的锡类催化剂和稳定剂过多,则会由于催化剂对副反应的促进作用而导致第二阶段酯化时生成的副产物过多,阻碍聚酯分子量的增加。
51.2接枝寡糖链的作用热老化测试:参照gb/t 1040.2
‑
2006塑料拉伸性能的测定,对实施例1、5和对比例5制得的聚对苯二甲酸
‑
己二酸
‑
乙二醇酯进行拉伸强度、断裂伸长率测试,并在150℃下老化48h后,再次测试聚对苯二甲酸
‑
己二酸
‑
乙二醇酯的拉伸强度和断裂伸长率,测试结果见表2。
52.土壤降解测试:将实施例1、5和对比例9制得的聚对苯二甲酸
‑
己二酸
‑
乙二醇酯在平板硫化机上热压成0.2mm厚的薄膜,裁剪成1cm
×
1cm大小的薄片,填埋到土壤中,在第5、 10、15周时取出,洗净、烘干,测试失重率,结果见表3。
53.表2表3
ꢀꢀ
5周10周15周实施例16.917.431.4实施例56.225.540.0对比例95.013.224.6从表2和表3可以看出:(1)相较于实施例1而言,实施例5在聚对苯二甲酸
‑
己二酸
‑
乙二醇酯的端羧基上接枝寡糖链后,聚酯的耐老化性能提高,并且,其在前第5周降解较慢,但后续降解速度加快。推测原因在于:在聚酯的端羧基上接枝寡糖链后,端羧基失去对酯键断裂的催化作用,因而能提高聚酯的耐老化性能。当聚酯被填埋后,初期由于无法利用端羧基催化聚酯降解,
故降解速度较慢;而随着时间的推移,由于葡萄糖端基上具有较多亲水性的羟基,能促进聚酯与葡萄糖端基之间的酯键断裂,生成的游离葡萄糖能作为碳源而促进土壤微生物的生长繁殖,同时,聚酯与葡萄糖端基之间的酯键断裂后会形成端羧基,对聚酯的降解起到催化作用,因此聚酯降解速度加快。
54.(2)相较于直接采用葡萄糖对聚酯进行接枝改性(对比例9)而言,采用2,3,4,6
‑
四
‑
o
‑ꢀ
乙酰基
‑
β
‑
d
‑
吡喃葡萄糖对聚酯进行接枝改性后脱保护基(实施例5),聚对苯二甲酸
‑
己二酸
‑ꢀ
乙二醇酯在土壤中的降解速度明显较快。推测原因在于:由于葡萄糖中存在多个羟基,当将其直接接枝到聚酯上时,一个葡萄糖分子能与多个端羧基反应,导致聚酯交联化,而聚酯的降解是从端基开始,交联导致聚酯端基减少,因而会导致聚酯降解缓慢。
55.本发明中所用原料、设备,若无特别说明,均为本领域的常用原料、设备;本发明中所用方法,若无特别说明,均为本领域的常规方法。
56.以上所述,仅是本发明的较佳实施例,并非对本发明作任何限制,凡是根据本发明技术实质对以上实施例所作的任何简单修改、变更以及等效变换,均仍属于本发明技术方案的保护范围。