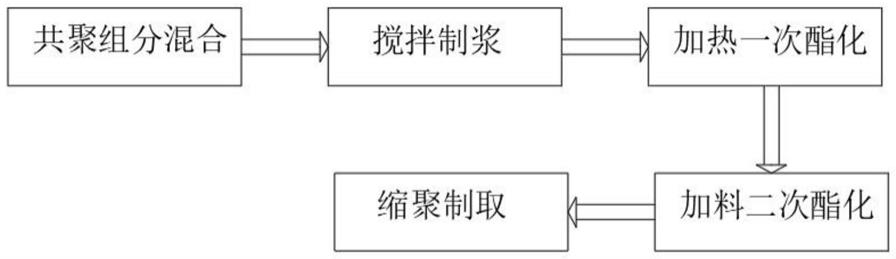
1.本发明涉及聚酯制备领域,特别涉及一种中高黏度分散染料常压可染共聚酯的制备方法。
背景技术:2.为了改善常规聚酯的染色性能,一般采用共聚的方法来制取共聚酯,共聚组分需满足结晶能力适当,玻璃化温度降低,以保证制取的纤维能常压染色,共聚的组分较常见的是间苯二甲酸和聚乙二醇,聚乙二醇是柔性脂肪族化合物,作为共聚组分,能使共聚酯达到常压沸染的染色效果,但是聚乙二醇的热稳定性较差,通常在150℃开始分解,导致在制取中高黏度共聚酯时会降低共聚酯的耐热性能,导致共聚酯的切片色值偏高,不利于后续纺织纤维的顺利进行。
技术实现要素:3.本发明的目的在于提供一种中高黏度分散染料常压可染共聚酯的制备方法,以解决上述背景技术中提出的问题。
4.为实现上述目的,本发明提供如下技术方案:一种中高黏度分散染料常压可染共聚酯的制备方法,包括如下步骤:
5.步骤一:将苯二甲酸、乙二醇、间苯二甲酸和催化剂加入打浆釜,对打浆釜内的苯二甲酸、乙二醇、间苯二甲酸和催化剂充分搅拌,直到混合均匀,制成浆料;
6.步骤二:通过浆料泵将打浆釜内混匀的浆料注入第一酯化反应釜中,对第一酯化反应釜进行加热,使得第一酯化反应釜内的浆料在常压下进行酯化反应,制成酯化产物;
7.步骤三:将酯化产物注入第二酯化反应釜中,加入聚己内酯二元醇、聚乙二醇、稳定剂和抗氧化剂,并对第二酯化反应釜内的混合物搅拌30分钟;
8.步骤四:将第二酯化反应釜中制备的混合物倒至缩聚反应釜中,对缩聚反应釜中的混合物进行搅拌,并将缩聚反应釜内部进行抽真空处理;
9.步骤五:搅拌完毕后,制得分散染料常压可染共聚酯,向缩聚反应釜内注入保护气解除真空,即可对缩聚反应釜内制成的分散常压可染共聚酯进行出料。
10.优选的,所述苯二甲酸和乙二酸的质量比为2~2.2:1。
11.优选的,所述催化剂为磷酸三甲酯。
12.优选的,所述聚乙二醇和聚已内酯二元醇的分子量比为6~4:3。
13.优选的,所述稳定剂为乙二醇锑。
14.优选的,所述抗氧化剂为抗氧剂1010。
15.优选的,所述缩聚反应釜内搅拌时抽真空至压力为20pa。
16.优选的,所述保护气为氮气。
17.优选的,所述分散常压可染共聚酯出料的压力为0.45mpa。
18.本发明的技术效果和优点:
19.本发明利用聚已内酯二元醇的设置,通过聚已内酯二元醇来替代或部分替代聚乙二醇,因聚己内酯二元醇具有较高的热稳定性,使得制取共聚酯的热稳定性明显提高,且聚己内酯二元醇的染色性能与聚乙二醇接近,制取的分散染料常压可染共聚酯的特性黏度达到0.78
‑
0.84dl/g,其切片色值偏低,有利于后续纺织纤维的顺利进行。
附图说明
20.图1为本发明制备流程示意图。
具体实施方式
21.下面将结合本发明实施例中的附图,对本发明实施例中的技术方案进行清楚、完整地描述,显然,所描述的实施例仅仅是本发明一部分实施例,而不是全部的实施例。基于本发明中的实施例,本领域普通技术人员在没有做出创造性劳动前提下所获得的所有其他实施例,都属于本发明保护的范围。
22.本发明提供了如图1所示的一种中高黏度分散染料常压可染共聚酯的制备方法,包括如下步骤:
23.步骤一:将苯二甲酸、乙二醇、间苯二甲酸和催化剂加入打浆釜,对打浆釜内的苯二甲酸、乙二醇、间苯二甲酸和催化剂充分搅拌,直到混合均匀,制成浆料,苯二甲酸和乙二酸的质量比为2~2.2:1,催化剂为磷酸三甲酯;
24.步骤二:通过浆料泵将打浆釜内混匀的浆料注入第一酯化反应釜中,对第一酯化反应釜进行加热,使得第一酯化反应釜内的浆料在常压下进行酯化反应,制成酯化产物,酯化温度在240℃~260℃,压力为常压状态;
25.步骤三:将酯化产物注入第二酯化反应釜中,加入聚己内酯二元醇、聚乙二醇、稳定剂和抗氧化剂,并对第二酯化反应釜内的混合物搅拌30分钟,聚乙二醇和聚已内酯二元醇的分子量比为6~4:3,稳定剂为乙二醇锑,抗氧化剂为抗氧剂1010;
26.步骤四:将第二酯化反应釜中制备的混合物倒至缩聚反应釜中,对缩聚反应釜中的混合物进行搅拌,并将缩聚反应釜内部进行抽真空处理,缩聚反应釜内搅拌时抽真空至压力为20pa,缩聚温度控制在280℃~292℃;
27.步骤五:搅拌完毕后,制得分散染料常压可染共聚酯,向缩聚反应釜内注入保护气解除真空,即可对缩聚反应釜内制成的分散常压可染共聚酯进行出料,保护气为氮气,分散常压可染共聚酯出料的压力为0.45mpa;
28.实施例1:
29.将3600kg苯二甲酸、50kg间苯二甲酸、1700kg乙二醇、500ml稳定剂磷酸三甲酯加入打浆釜充分搅拌混合均匀,制成浆料,用浆料泵均匀地加入第一酯化反应釜,控制反应釜内温255℃,分馏柱顶温102℃,浆料输送完毕保持30分钟,分馏柱顶温下降,馏出水量达到规定值,酯化反应结束,将酯化产物移送到第二酯化反应釜,加入75kg聚乙二醇(分子量2000)、100kg聚己内酯二元醇(分子量1500)、2800g催化剂乙二醇锑、10kg抗氧剂1010,停留30分钟后倒入缩聚反应釜,在缩聚反应釜中搅拌逐渐抽真空,40min后进入高真空阶段,升温,继续抽真空直至余压20pa,控制反应终温287℃,当搅拌电机电流达到185a,停止搅拌,充氮气解除真空充压到0.45mpa出料,测得的共聚酯特性黏度为0.805dl/g,熔点为251℃,
色度b值为6.5,热分解起始温度为379℃;
30.实施例2:
31.将3600kg苯二甲酸、50kg间苯二甲酸、1700kg乙二醇、500ml稳定剂磷酸三甲酯加入打浆釜充分搅拌混合均匀,制成浆料,用浆料泵均匀地加入第一酯化反应釜,控制反应釜内温255℃,分馏柱顶温102℃,浆料输送完毕保持30分钟,分馏柱顶温下降,馏出水量达到规定值,酯化反应结束,将酯化产物移送到第二酯化反应釜,加入75kg聚乙二醇(分子量4000)、175kg聚己内酯二元醇(分子量2000)、2800g催化剂乙二醇锑、16kg抗氧剂1010,停留30分钟后倒入缩聚反应釜,在缩聚反应釜中搅拌逐渐抽真空,40min后进入高真空阶段,升温,继续抽真空直至余压20pa,控制反应终温291℃,当搅拌电机电流达到190a,停止搅拌,充氮气解除真空充压到0.45mpa出料,测得的共聚酯特性黏度为0.836dl/g,熔点为250℃,色度b值为7.8,热分解起始温度为373℃;
32.对比例:
33.将3600kg苯二甲酸、50kg间苯二甲酸、1700kg乙二醇、500ml稳定剂磷酸三甲酯加入打浆釜充分搅拌混合均匀,制成浆料,用浆料泵均匀地加入第一酯化反应釜,控制反应釜内温255℃,分馏柱顶温102℃,浆料输送完毕保持30分钟,分馏柱顶温下降,馏出水量达到规定值,酯化反应结束,将酯化产物移送到第二酯化反应釜,加入250kg聚乙二醇(分子量4000)、2800g催化剂乙二醇锑、16kg抗氧剂1010,停留30分钟后倒入缩聚反应釜,在缩聚反应釜中搅拌逐渐抽真空,40min后进入高真空阶段,升温,继续抽真空直至余压20pa,控制反应终温291℃,当搅拌电机电流达到190a,停止搅拌,充氮气解除真空充压到0.45mpa出料,测得的共聚酯特性黏度为0.838dl/g,熔点为250℃,色度b值为11.9,热分解起始温度为357℃;
34.较对比例来看,实施例1和实施例2中的测得的共聚酯色度b值明显小于对比例中所测的值,同时实施例1和实施例2中测得的热分解温度都比对比例中的高20℃左右,使的通过聚己内酯二元醇制得的共聚酯热稳定性更好,不易分解,同时切片色值偏低,便于后续纺织纤维的顺利进行。
35.最后应说明的是:以上所述仅为本发明的优选实施例而已,并不用于限制本发明,尽管参照前述实施例对本发明进行了详细的说明,对于本领域的技术人员来说,其依然可以对前述各实施例所记载的技术方案进行修改,或者对其中部分技术特征进行等同替换,凡在本发明的精神和原则之内,所作的任何修改、等同替换、改进等,均应包含在本发明的保护范围之内。