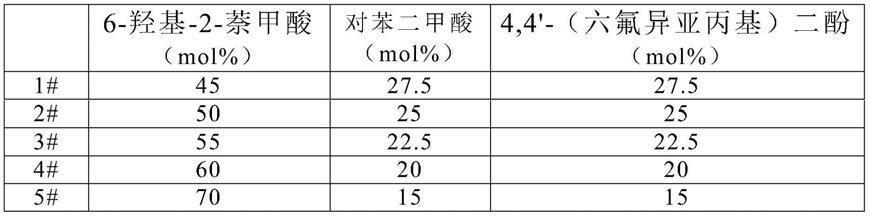
1.本发明属于高分子聚合物技术领域,具体涉及一种低介电常数液晶聚合物薄膜及其制备方法。
背景技术:2.液晶聚合物(liquid crystal polymer,lcp)是上世纪80年代初期发展起来的一种新型高性能特种工程塑料,属于全芳香族聚酯,其在一定条件下能以液晶相形式存在,分子具有高分子量和自发取向的特征,使得液晶聚合物显现出优异的性能,如高强度、高模量、低介电损耗、低吸湿性、高耐弯折性、良好的加工流动性等,是一种极具应用潜质的高新材料。液晶聚合物薄膜因其优良的耐热性、低的吸湿性以及低的介电常数和介电损耗,可作为印制电路中的绝缘基材。介电常数是影响信号传播速度的主要因素,介电常数越小,越有利于信号的传输,随着5g高频高速时代的来临,电子信息技术对液晶聚合物薄膜的介电常数提出了更高的要求。
3.现有技术专利cn111320848a公开了一种低介电常数液晶聚合物组合物,该液晶聚合物组合物通过液晶聚合物类别筛选和相应功能组分的协同作用,得到了介电常数较低的复合材料,但该聚合物组合物主要是在低频条件下表现出了较低的介电常数,难以满足5g时代高频高速的传输需求,并且该聚合物组合物的组分和相应的加工过程较为复杂,各组分之间进行混合时存在混合不均的问题,同时,公开内容并未记载相应液晶聚合物薄膜的制备,本领域技术人员无法知晓该液晶聚合物组合物是否可以制作薄膜。专利cn112080291a公开了一种用于5g通信柔性覆铜板的液晶聚合物薄膜及其制备方法,其制备方法包括:将聚四氟乙烯原料进行液氮冷冻粉碎,得到聚四氟乙烯粉料;将液晶聚合物溶液与所述聚四氟乙烯粉料进行混合,得到混合物;将所述混合物涂覆于基材上,然后进行退火处理,得到所述液晶聚合物薄膜。通过上述物理共混方式虽然可以制备得到较低介电常数、较低介电损耗且表面光滑、具有一定力学强度的液晶聚合物薄膜,但是其制膜采用的是溶致性液晶聚合物,溶致性液晶聚合物通过涂布方进行制膜时,涂布得到的薄膜厚度较薄,且溶剂难以挥发完全,在后续加工中容易起泡。此外,液氮冷冻粉碎后得到的聚四氟乙烯粒径难以精确控制。
4.鉴于上述问题,发明人通过引入新型单体进行化学共聚,制备得到低介电常数的热致性液晶聚合物薄膜。
技术实现要素:5.本发明的目的是针对现有技术中存在的上述问题,提供一种低介电常数液晶聚合物薄膜,通过在液晶聚合物中引入新型单体4,4'
‑
(六氟异亚丙基)二酚可有效降低液晶聚合物薄膜的介电常数,满足5g高频高速的使用需求。
6.本发明的上述目的可以通过下列技术方案来实现:一种低介电常数液晶聚合物薄膜,包括液晶聚合物,所述的液晶聚合物由以下单体制成:6
‑
羟基
‑2‑
萘甲酸、对苯二甲酸、
4,4'
‑
(六氟异亚丙基)二酚,所述的各单体中6
‑
羟基
‑2‑
萘甲酸的摩尔百分比为45
‑
70mol%,对苯二甲酸和4,4'
‑
(六氟异亚丙基)二酚的摩尔百分比之和为30
‑
55mol%,三种单体的摩尔百分比之和等于100mol%。
7.作为优选,所述对苯二甲酸与4,4'
‑
(六氟异亚丙基)二酚的摩尔比为1:1。
8.本发明的第二个目的是提供一种上述液晶聚合物薄膜的制备方法,所述的制备方法具体包括以下步骤:
9.s1:将单体6
‑
羟基
‑2‑
萘甲酸、对苯二甲酸、4,4'
‑
(六氟异亚丙基)二酚,乙酰化试剂乙酸酐,催化剂2,5
‑
二氨基吡啶,抗氧化剂氯化亚锡,投至哈氏合金聚合釜中进行预聚合,制备出预聚物;
10.s2:将预聚物从哈氏合金釜排出,经过粉碎,在氮气保护下进行固相缩聚,制得高分子量的液晶聚合物;
11.s3:将制得的液晶聚合物经过双螺杆挤出机混炼、排气;熔融挤出,侧吹风冷却;牵伸,卷绕,制得初生液晶聚合物薄膜;
12.s4:对步骤s3中制得的初生薄膜进行热处理,制得液晶聚合物薄膜。
13.作为优选,所述乙酸酐的添加量为6
‑
羟基
‑2‑
萘甲酸和4,4'
‑
(六氟异亚丙基)二酚中羟基总摩尔数的1.0
‑
2.3倍。
14.作为优选,所述2,5
‑
二氨基吡啶的添加量为6
‑
羟基
‑2‑
萘甲酸、对苯二甲酸、4,4'
‑
(六氟异亚丙基)二酚总重量的20
‑
400ppm。
15.作为优选,所述氯化亚锡的添加量为6
‑
羟基
‑2‑
萘甲酸、对苯二甲酸、4,4'
‑
(六氟异亚丙基)二酚总重量的0.1%
‑
0.25%。
16.作为优选,所述步骤s1具体为:将原料投入哈氏合金聚合釜后于135
‑
160℃下保持2
‑
10h;以0.35
‑
1.0℃/min的速度升温至300
‑
320℃,保温2
‑
3h;向聚合釜中冲入0.1
‑
1.0mpa氮气,反应物料经过直径2
‑
4mm的8
‑
10孔放料阀门放出,粉碎,过20
‑
30目筛,经130
‑
160℃干燥1
‑
5h后制得预聚物。
17.作为优选,所述步骤s2具体为:将制得的预聚物在氮气保护下,于195
‑
320℃的旋转窑中固相缩聚10
‑
46h,制得液晶聚合物。
18.作为优选,所述步骤s3中双螺杆挤出机的挤出温度为280
‑
345℃。
19.作为优选,所述步骤s3中侧吹风温度为20
‑
50℃,牵伸速度为8
‑
36m/min。
20.作为优选,所述步骤s4中热处理温度为210
‑
305℃,时间为12
‑
55h。
21.本发明制得的高分子液晶聚合物的重均分子量为30000~42000。
22.本发明所用催化剂为2,5
‑
二氨基吡啶,而传统的催化剂如:醋酸锌、醋酸锰、醋酸钠、醋酸钾、醋酸钴、醋酸锂、钛酸酯、月桂酸二丁基锡、氧化二丁基锡、三氧化二锑或乙二醇锑中的一种或几种的组合几乎不能使反应发生,或转化率较低,不能形成高分子量的聚合物,从而无法制备出高性能的液晶聚合物薄膜。
23.与现有技术相比,本发明具有如下有益效果:
24.本发明通过引入新型单体4,4'
‑
(六氟异亚丙基)二酚,在其拉伸强度、介电损耗、吸水率皆可与现有液晶聚合物薄膜媲美的同时,还可有效降低液晶聚合物薄膜的介电常数,制得的液晶聚合物薄膜具有优异的绝缘性能,可满足于5g高频高速的使用需求。此外,无需使用填料,薄膜厚度加工窗口大,制备过程简单易控。
具体实施方式
25.以下是本发明的具体实施例,对本发明的技术方案作进一步的描述,但本发明并不限于这些实施例。本发明如无特别说明,则所用原料或试剂为常规原料或试剂,所用方法为常规方法。
26.实施方式
27.一种低介电常数液晶聚合物薄膜,其包括液晶聚合物,所述的液晶聚合物包括以下单体:6
‑
羟基
‑2‑
萘甲酸、对苯二甲酸、4,4'
‑
(六氟异亚丙基)二酚,所述的各单体中6
‑
羟基
‑2‑
萘甲酸的摩尔百分比为45
‑
70mol%,对苯二甲酸和4,4'
‑
(六氟异亚丙基)二酚的摩尔百分比之和为30
‑
55mol%,三种单体的摩尔百分比之和等于100mol%。
28.上述液晶聚合物薄膜的制备方法包括以下步骤:
29.s1:将单体6
‑
羟基
‑2‑
萘甲酸、对苯二甲酸、4,4'
‑
(六氟异亚丙基)二酚,乙酰化试剂乙酸酐,催化剂2,5
‑
二氨基吡啶,抗氧化剂氯化亚锡,投至哈氏合金聚合釜中进行预聚合,制备出预聚物;
30.s2:将预聚物从哈氏合金釜排出,经过粉碎,在氮气保护下进行固相缩聚,制得高分子量的液晶聚合物;
31.s3:将制得的液晶聚合物经过双螺杆挤出机混炼、排气;熔融挤出,侧吹风冷却;牵伸,卷绕,制得初生液晶聚合物薄膜;
32.s4:对步骤s3中制得的初生薄膜进行热处理,制得液晶聚合物薄膜。
33.上述制备方法中,优选地,乙酸酐的添加量为6
‑
羟基
‑2‑
萘甲酸和4,4'
‑
(六氟异亚丙基)二酚中羟基总摩尔数的1.0
‑
2.3倍。
34.上述制备方法中,优选地,2,5
‑
二氨基吡啶的添加量为6
‑
羟基
‑2‑
萘甲酸、对苯二甲酸、4,4'
‑
(六氟异亚丙基)二酚总重量的20
‑
400ppm。
35.上述制备方法中,优选地,氯化亚锡添加量为6
‑
羟基
‑2‑
萘甲酸、对苯二甲酸、4,4'
‑
(六氟异亚丙基)二酚总重量的0.1%
‑
0.25%。
36.上述制备方法中,优选地,s1具体为:将原料投入哈氏合金聚合釜后于135
‑
160℃下保持2
‑
10h;以0.35
‑
1.0℃/min的速度升温至300
‑
320℃,保温2
‑
3h;向聚合釜中冲入0.1
‑
1.0mpa氮气,反应物料经过直径2
‑
4mm的8
‑
10孔放料阀门放出,粉碎,过20
‑
30目筛,经130
‑
160℃干燥1
‑
5h后制得预聚物。
37.上述制备方法中,优选地,s2具体为:将制得的预聚物在氮气保护下,于195
‑
320℃的旋转窑中固相缩聚10
‑
46h,制得液晶聚合物。
38.上述制备方法中,优选地,步骤s3中双螺杆挤出机的挤出温度为280
‑
345℃。
39.上述制备方法中,优选地,所述步骤s3中侧吹风温度为20
‑
50℃,牵伸速度为8
‑
36m/min。
40.上述制备方法中,优选地,所述步骤s4中热处理温度为210
‑
305℃,时间为12
‑
55h。
41.通过下述实施例及对比例对本发明实施方式进行详细说明。本发明实施例1
‑
5的单体配比如表1所示:
42.表1:实施例1
‑
5中单体配比
[0043][0044]
实施例1
[0045]
按照1#单体配比将6
‑
羟基
‑2‑
萘甲酸、对苯二甲酸、4,4'
‑
(六氟异亚丙基)二酚、占6
‑
羟基
‑2‑
萘甲酸和4,4'
‑
(六氟异亚丙基)二酚中羟基总摩尔数1.0倍的乙酸酐、占三种单体总重量20ppm的2,5
‑
二氨基吡啶及占三种单体总重量0.10%的氯化亚锡投入哈氏合金聚合釜,然后于135℃下保持2h;以0.35℃/min的速度升温至300℃,保温2h;向聚合釜中冲入0.1mpa氮气,反应物料经过直径2mm的8孔放料阀门放出,粉碎,过20目筛,经130℃干燥1h后制得预聚物;
[0046]
将制得的预聚物在氮气保护下,于195℃的旋转窑中固相缩聚10h,制得液晶聚合物,其重均分子量为30000;
[0047]
将制得的液晶聚合物经过双螺杆挤出机于280℃下进行辊炼、排气;以50kg/h吐出量熔融挤出,20℃侧吹风冷却;于23m/min速度牵伸,卷绕,制得平均厚度为50μm的初生液晶聚合物薄膜;
[0048]
将上述初生液晶聚合物薄膜和厚度50μm的铝箔在270℃的加热状态以压力10kg/cm2、速度3m/min的条件压接于安装有耐热橡胶辊和加热金属辊的热辗压制装置上,制作热塑性液晶聚合物薄膜/铝箔构成的层叠体,将该层叠体于290℃的热处理炉中放置30s;在氮气保护下,将其在210℃下热处理12h;之后,剥离铝箔,得到厚度为50μm的液晶聚合物薄膜。
[0049]
实施例2
[0050]
按照2#单体配比将6
‑
羟基
‑2‑
萘甲酸、对苯二甲酸、4,4'
‑
(六氟异亚丙基)二酚、占6
‑
羟基
‑2‑
萘甲酸和4,4'
‑
(六氟异亚丙基)二酚中羟基总摩尔数1.3倍的乙酸酐、占三种单体总重量90ppm的2,5
‑
二氨基吡啶及占三种单体总重量0.15%的氯化亚锡投入哈氏合金聚合釜,然后于143℃下保持4h;以0.48℃/min的速度升温至305℃,保温2h;向聚合釜中冲入0.4mpa氮气,反应物料经过直径3mm的8孔放料阀门放出,粉碎,过25目筛,经140℃干燥2h后制得预聚物;
[0051]
将制得的预聚物在氮气保护下,于230℃的旋转窑中固相缩聚20h,制得液晶聚合物,其重均分子量为33000;
[0052]
将制得的液晶聚合物经过双螺杆挤出机于300℃下进行辊炼、排气;以50kg/h吐出量熔融挤出,30℃侧吹风冷却;于23m/min速度牵伸,卷绕,制得平均厚度为50μm的初生液晶聚合物薄膜;
[0053]
将上述初生液晶聚合物薄膜和厚度50μm的铝箔在270℃的加热状态以压力10kg/cm2、速度3m/min的条件压接于安装有耐热橡胶辊和加热金属辊的热辗压制装置上,制作热塑性液晶聚合物薄膜/铝箔构成的层叠体,将该层叠体于290℃的热处理炉中放置30s;在氮气保护下,将其在240℃下热处理25h;之后,剥离铝箔,得到厚度为50μm的液晶聚合物薄膜。
[0054]
实施例3
[0055]
按照3#单体配比将6
‑
羟基
‑2‑
萘甲酸、对苯二甲酸、4,4'
‑
(六氟异亚丙基)二酚、占6
‑
羟基
‑2‑
萘甲酸和4,4'
‑
(六氟异亚丙基)二酚中羟基总摩尔数1.6倍的乙酸酐、占三种单体总重量230ppm的2,5
‑
二氨基吡啶及占三种单体总重量0.18%的氯化亚锡投入哈氏合金聚合釜,然后于148℃下保持6h;以0.65℃/min的速度升温至310℃,保温2.5h;向聚合釜中冲入0.6mpa氮气,反应物料经过直径3mm的10孔放料阀门放出,粉碎,过30目筛,经150℃干燥3h后制得预聚物;
[0056]
将制得的预聚物在氮气保护下,于270℃的旋转窑中固相缩聚33h,制得液晶聚合物,其重均分子量为36500;
[0057]
将制得的液晶聚合物经过双螺杆挤出机于330℃下进行辊炼、排气;以50kg/h吐出量熔融挤出,40℃侧吹风冷却;于23m/min速度牵伸,卷绕,制得平均厚度为50μm的初生液晶聚合物薄膜;
[0058]
将上述初生液晶聚合物薄膜和厚度50μm的铝箔在270℃的加热状态以压力10kg/cm2、速度3m/min的条件压接于安装有耐热橡胶辊和加热金属辊的热辗压制装置上,制作热塑性液晶聚合物薄膜/铝箔构成的层叠体,将该层叠体于290℃的热处理炉中放置30s;在氮气保护下,将其在270℃下热处理38h;之后,剥离铝箔,得到厚度为50μm的液晶聚合物薄膜。
[0059]
实施例4
[0060]
按照4#单体配比将6
‑
羟基
‑2‑
萘甲酸、对苯二甲酸、4,4'
‑
(六氟异亚丙基)二酚、占6
‑
羟基
‑2‑
萘甲酸和4,4'
‑
(六氟异亚丙基)二酚中羟基总摩尔数2.0倍的乙酸酐、占三种单体总重量310ppm的2,5
‑
二氨基吡啶及占三种单体总重量0.22%的氯化亚锡投入哈氏合金聚合釜,然后于155℃下保持8h;以0.8℃/min的速度升温至315℃,保温2.5h;向聚合釜中冲入0.8mpa氮气,反应物料经过直径4mm的10孔放料阀门放出,粉碎,过30目筛,经155℃干燥4h后制得预聚物;
[0061]
将制得的预聚物在氮气保护下,于295℃的旋转窑中固相缩聚40h,制得液晶聚合物,其重均分子量为39000;
[0062]
将制得的液晶聚合物经过双螺杆挤出机于360℃下进行辊炼、排气;以50kg/h吐出量熔融挤出,50℃侧吹风冷却;于23m/min速度牵伸,卷绕,制得平均厚度为50μm初生液晶聚合物薄膜;
[0063]
将上述初生液晶聚合物薄膜和厚度50μm的铝箔在270℃的加热状态以压力10kg/cm2、速度3m/min的条件压接于安装有耐热橡胶辊和加热金属辊的热辗压制装置上,制作热塑性液晶聚合物薄膜/铝箔构成的层叠体,将该层叠体于290℃的热处理炉中放置30s;在氮气保护下,将其在290℃下热处理47h;之后,剥离铝箔,得到厚度为50μm的液晶聚合物薄膜。
[0064]
实施例5
[0065]
按照1#单体配比将6
‑
羟基
‑2‑
萘甲酸、对苯二甲酸、4,4'
‑
(六氟异亚丙基)二酚、占6
‑
羟基
‑2‑
萘甲酸和4,4'
‑
(六氟异亚丙基)二酚中羟基总摩尔数2.3倍的乙酸酐、占三种单体总重量400ppm的2,5
‑
二氨基吡啶及占三种单体总重量0.25%的氯化亚锡投入哈氏合金聚合釜,然后于160℃下保持10h;以1.0℃/min的速度升温至320℃,保温3h;向聚合釜中冲入1.0mpa氮气,反应物料经过直径2mm的8孔放料阀门放出,粉碎,过20目筛,经160℃干燥5h后制得预聚物;
[0066]
将制得的预聚物在氮气保护下,于320℃的旋转窑中固相缩聚46h,制得液晶聚合
物,其重均分子量为42000;
[0067]
将制得的液晶聚合物经过双螺杆挤出机于280℃下进行辊炼、排气;以50kg/h吐出量熔融挤出,20℃侧吹风冷却;于23m/min速度牵伸,卷绕,制得平均厚度为50μm的初生液晶聚合物薄膜;
[0068]
将上述初生液晶聚合物薄膜和厚度50μm的铝箔在270℃的加热状态以压力10kg/cm2、速度3m/min的条件压接于安装有耐热橡胶辊和加热金属辊的热辗压制装置上,制作热塑性液晶聚合物薄膜/铝箔构成的层叠体,将该层叠体于290℃的热处理炉中放置30s;在氮气保护下,将其在305℃下热处理55h;之后,剥离铝箔,得到厚度为50μm的液晶聚合物薄膜。
[0069]
对比例1
[0070]
本对比例与实施例4的区别仅在于,三种单体的摩尔量分别为6
‑
羟基
‑2‑
萘甲酸40mol%、对苯二甲酸30mol%、4,4'
‑
(六氟异亚丙基)二酚30mol%,其它均与实施例4相同,聚合反应制得的液晶聚合物重均分子量为33400。
[0071]
对比例2
[0072]
本对比例与实施例4的区别仅在于,三种单体的摩尔百分比分别为6
‑
羟基
‑2‑
萘甲酸75mol%、对苯二甲酸12.5mol%、4,4'
‑
(六氟异亚丙基)二酚12.5mol%,其它均与实施例4相同,聚合反应制得的液晶聚合物重均分子量为32600。
[0073]
对比例3
[0074]
本对比例与实施例4的区别仅在于,将单体4,4'
‑
(六氟异亚丙基)二酚替换成等摩尔百分比的联苯二酚,其它均与实施例4相同,聚合反应制得的液晶聚合物重均分子量为33700。
[0075]
对比例4
[0076]
本对比例与实施例4的区别仅在于,将催化剂2,5
‑
二氨基吡啶替换成等质量的醋酸锰,其它均与实施例4相同,聚合反应制得的液晶聚合物重均分子量为21860。
[0077]
本发明针对上述实施例及对比例进行了如下性能测试,测试结果如表2所示:
[0078]
(1)介电常数和介电损耗因子:spdr,15ghz;
[0079]
(2)拉伸强度:astm d882;
[0080]
(3)吸水率(25℃、水中24h、1mmt):gbt6283
‑
2008。
[0081]
表2:实施例1
‑
5及对比例1
‑
3中制得的液晶聚合物薄膜的性能测试结果
[0082]
[0083][0084]
由表2可知,当单体配方比例或成分发生改变时,均会对液晶聚合物薄膜的性能产生不良影响,影响其最终使用,而采用本发明的配方及工艺获得的液晶聚合物薄膜具有较低的介电常数,同时兼具良好的力学性能、低的介电损耗和吸水率,满足于5g高频高速的使用需求,具有广阔的应用场景。
[0085]
需要说明的是,本领域技术人员可以根据实际需要通过调控液晶聚合物吐出量或牵伸速度获得不同厚度的薄膜,这里不再一一赘述。
[0086]
尽管对本发明已作出了详细的说明并引证了一些具体实施例,但是对本领域熟练技术人员来说,只要不离开本发明的精神和范围,可作各种变化或修正是显然的。