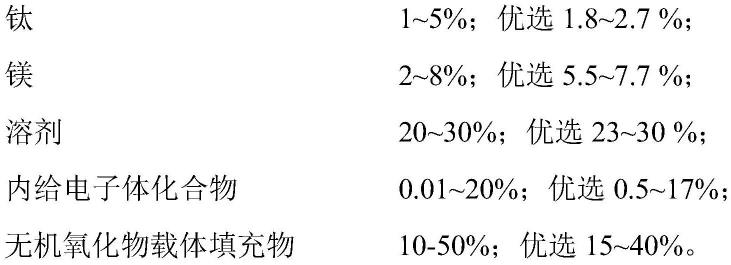
1.本发明涉及烯烃聚合用催化剂领域,进一步地说,是涉及一种用于烯烃聚合的催化剂组分、制备方法及其应用、催化剂及其应用。
背景技术:2.众所周知,烯烃聚合高效齐格勒-纳塔(ziegler-natta)催化剂由主催化剂和助催化剂两部分组成。主催化剂由在周期表中位于第四到第八主族的过渡金属化合物构成,助催化剂则为在周期表中位于第一到第三主族的金属有机化合物。通常,主催化剂又可以分为两个部分:惰性载体及其负载的活性组份。主催化剂的制备一般采用钛的卤化物与有晶格缺陷的镁的卤化物反应成型或把反应物负载在惰性载体上制备而成。而其中镁的化合物以具有晶格缺陷的镁的卤化物为好,而具有晶格缺陷的镁的卤化物可以由镁的化合物生成,也可以用醇、醚、酯等给电子体与镁的卤化物反应,然后再脱除部分醇、醚、酯等给电子体得到。
3.在乙烯的聚合反应或乙烯与α-烯烃的共聚合反应中,催化剂的性能影响着聚合物的性能。一般情况下,聚合反应器中氢/烯提高会使得催化剂的活性降低,催化剂既具有高的催化剂活性,同时具有好的氢调性能是聚合所希望的。较高氢/烯比的条件下催化剂活性高有利于较高熔融指数树脂的生产,特别是有利于较高熔融指数、较高密度的树脂牌号的生产。尤其是在两个串联的双反应器生产工艺,在生产高熔融指数的反应器中,催化剂的氢调性能提高和较高的反应活性,同时,在生产低熔融指数的反应器中,催化剂的氢调性能不提高或提高幅度不大和较高的反应活性有利于反应器平稳控制,这些是聚合所希望的。催化剂微粒含量更低和给电子体或溶剂含量较低对生产有利,因为,给电子体或溶剂含量高,在聚合时会适用较高的助催化剂烷基铝的用量,既使得成本升高,又使得树脂中残存的铝含量升高,使得树脂灰分升高,在生产薄膜时雾度升高。在聚合过程中,聚合物微粒主要来自于催化剂中的微粒、催化剂中的活性粒子及催化剂聚合过程中产生的破碎。聚合物微粒不利于聚合过程,因为聚合物微粒造成与床水平控制、与循环气夹带有关的问题,从而会造成设备故障、可操作性受损和效率降低。因此,希望烯烃聚合过程中使聚合物微粒最少化,减少这种聚合物微粒的一个因素是通过消除或减少那些产生聚合物微粒的前催化剂微粒。
4.随着技术不断发展,齐格勒-纳塔型烯烃聚合催化剂的活性、氢调敏感度、共聚性能及其聚合粉料的堆积密度、熔融指数、分子量分布、细粉含量、共聚单元分布等性能参数均得到了显著的优化。但是,为了能够更好地适应工业生产的需求,得到性能更优异的聚烯烃产品,此类催化剂及其聚合粉料的上述性能参数还需进一步提高。
5.在现有技术中,如cn1958620a、cn102295717a和cn103772536a采用在溶液中析出沉降的方法,分别引入了硅氧烷类给电子体、邻位烷氧基取代的苯甲酸酯/羧酸酯(或二醚)复配给电子体、苯甲酸酯类给电子体,用以改善催化剂的氢调敏感度;ep0180420b1采用在溶液中析出沉降制备载体、然后载体负载活性中心的方法,引入胺、酰胺、醚、芳酯、膦、硫等
给电子体,用以改善催化剂的共聚性能。如cn1726230a、cn1798774a和cn101050248a采用浸渍负载的方法,在高速搅拌低温冷凝成型的氯化镁—醇的加合物球形载体中,引入醇、酮、胺、酰胺、腈、烷氧基硅烷、脂肪族醚和脂肪族羧酸酯等给电子体,用以改善催化剂的共聚性能。如cn102807638a采用浸渍负载的方法,在高速搅拌低温冷凝成型的氯化镁—醇的加合物球形载体中,引入复配的长碳链单酯类/短碳链单酯类给电子体来提高催化剂的活性。如cn1103406a采用外给电子体的方法,向聚合釜中与催化剂同时引入二醚,尤其是1,3-二醚类给电子体,用以得到较窄分子量分布的聚乙烯产品。如ep0219998b1采用在溶液中析出沉降的方法,在得到颗粒悬浮液后,引入适量的水这种给电子体,用以改善所得聚乙烯粉料的粒度及其分布,减少细粉含量。
6.喷雾干燥法是一种制备烯烃聚合高效齐格勒-纳塔催化剂的有效方法。该法是用气体将溶解液体或悬浮液体通过特别设计的喷嘴喷至热惰性气体干燥室中干燥,被分散的雾状微液滴干燥成粉末或颗粒状产品。雾滴一旦与干燥的载气接触,蒸发便在迅速建立起的液滴表面上的饱和蒸汽膜上进行。在蒸发期间,雾滴的尺寸分布要发生变化,不同的产品显示出不同的特性。在蒸发过程中,雾滴容易造成膨胀、崩溃、破碎或分裂,导致产生多孔性的、不规则的形状,这与喷雾工艺中形成的液滴特性有关。可以由雾滴组成、体积及尺寸的变化影响粒子的结构改造。调整喷雾干燥工艺的条件,可以获得大、小或聚集的粒子。
7.中国专利cn1085915a中,公开了一种齐格勒-纳塔催化剂体系的制备方法。在四氢呋喃中由金属镁还原四氯化钛制得ticl3的四氢呋喃溶液,后将氯化镁在四氢呋喃中溶解,把这两种溶液充分混合,过滤掉未反应的镁和未溶解的氯化镁,把经过滤的溶液与硅胶充分混合,然后进行喷雾干燥,得到催化剂的分散颗粒。该催化剂钛含量高,活性也高,在催化乙烯与α-烯烃聚合时可成倍地减少己烷可提取物。但是,该催化剂制备中收率较高时,其d
10
较小,要保持较大的d
10
需要降低催化剂的总收率,这样会产生较多的催化剂微粒,既提高了生产成本,又产生了较多的废渣。
8.中国专利cn104761665a公开了一种喷雾干燥的齐格勒-纳塔催化剂组合物,该催化剂包括无机氧化物粒子、卤化镁、给电子体化合物、硅烷偶联剂、卤化钛,硅烷偶联剂改善了二氧化硅载体的表面性能,催化剂具有活性高、氢调敏感性好、细粉含量少等特点。
9.中国专利cn100368440c公开了一种喷雾干燥的聚合催化剂和采用该聚合催化剂的聚合方法,该催化剂包括惰性多孔填料和如下物质反应产物的喷雾干燥组合物:卤化镁、溶剂、给电子体化合物、过渡金属化合物的混合物或反应产物。该催化剂含有一种醇化合物作为给电子体,活性提高;使用球形的平均粒度为1μm~12μm惰性多孔填料用以减少催化剂中小催化剂粒子,进而减少聚合物中的微粒含量,但氢调性能没有提高。
10.中国专利cn1993391a公开了一种强喷雾干燥的齐格勒-纳塔催化剂组合物,该催化剂包括惰性多孔填料、卤化镁、溶剂或稀释剂、路易斯碱给电子体化合物、过渡金属化合物的混合物或反应产物,其中卤化镁化合物在溶剂或稀释剂中存在的量是饱和浓度的至少90%,经过喷雾干燥所得催化剂颗粒具有10~70μm的平均直径(d
50
),其中至少5%的颗粒具有基本或完全被单一的表面层(壳)包围的内部空隙体积,所述层特征在于颗粒直径大于30μm的颗粒有sem技术测定的平均壳厚度/颗粒粒径(厚度比)大于0.2。该催化剂通过减少催化剂破碎或破碎后催化剂碎片仍然较大而减少聚合物微粒,同时催化剂的活性和氢调性能稍有提高。
11.上述的各类催化剂有的仅能够提高烯烃聚合催化剂在某一方面的性能,有的虽然能提高几项性能,但是,仍然不够理想。因此,有必要研发一种更全面提高催化剂及其聚合粉料性能参数的催化剂。
技术实现要素:12.为解决现有技术中出现的问题,本发明提供了一种用于烯烃聚合的催化剂组分、制备方法及其应用、催化剂及其应用。该催化剂用于烯烃聚合尤其是用于乙烯与
ɑ-烯烃聚合时,具有活性高、氢调性能好、催化剂微粒含量和溶剂含量低、所得聚合物粉料堆积密度高、聚合物粉料细粉含量低的特点。
13.本发明的目的之一是提供一种用于烯烃聚合的催化剂组分,该催化剂组分包括:
14.以催化剂组分总重为100%计,
15.钛0.1~5%;优选1~5%;更优选1.8~2.7%;
16.镁0.2~10.2%;优选2~8%;更优选5.5~7.7%;
17.溶剂15~40%;优选20~30%;更优选23~30%;
18.内给电子体化合物0.01~30%;优选0.01~20%;更优选0.5~17%;
19.无机氧化物载体填充物1~70%;优选10-50%;更优选15~40%。
20.其中,所述内给电子体化合物为通式(i)的化合物,
[0021][0022]
式(i)中r1,r2,r3,r4,r5任选其一为ro基团,其余彼此相同或不同,各自独立地选自氢、1~18碳的直链烷基或支链烷基、环烷基、芳基、烷芳基或芳烷基,r选自1~18碳的直链烷基或支链烷基、环烷基、芳基、烷芳基或芳烷基。可以明确地地看出,通式(i)的所述内给电子体化合物是酚、醚双官能团化合物。
[0023]
本发明中,钛、镁指的是催化剂组分中含有的钛元素、镁元素。
[0024]
优选地,
[0025]
所述镁和钛的摩尔比大于2:1,优选大于5:1,更优选为镁和钛的摩尔比大于5:1,小于12:1;和/或,
[0026]
所述内给电子体化合物与镁的摩尔比为(0.01~0.6):1,优选为(0.08~0.5):1;更优选为(0.08~0.4):1;和/或,
[0027]
所述溶剂与镁的摩尔比小于3:1;优选小于2.5:1;更优选小于2:1。
[0028]
优选地,
[0029]
所述内给电子体化合物选自对甲氧基苯酚、邻甲氧基苯酚、间甲氧基苯酚、对乙氧基苯酚、邻乙氧基苯酚、间乙氧基苯酚、对丙氧基苯酚、邻丙氧基苯酚、间丙氧基苯酚、对丁氧基苯酚、邻丁氧基苯酚、间丁氧基苯酚、对己氧基苯酚、邻己氧基苯酚、间己氧基苯酚、对
辛氧基苯酚、邻辛氧基苯酚、间辛氧基苯酚、对壬烷氧基苯酚、间壬烷氧基苯酚、邻壬烷氧基苯酚、邻苯氧基苯酚、间苯氧基苯酚、对苯氧基苯酚、十二烷氧基苯酚、十四烷氧基苯酚、十八烷氧基苯酚或羟基苯基苄基醚中的至少一种。
[0030]
在本发明中,十二烷氧基苯酚、十四烷氧基苯酚、十八烷氧基苯酚表示邻、间、对位的上述化合物均可以,优选4-十二烷氧基苯酚,4-十四烷氧基苯酚、4-十八烷氧基苯酚。
[0031]
在本发明中,包括但不限于上述化合物,符合所述内给电子体化合物通式(i)的化合物这里没有穷尽列举。
[0032]
本发明所加入的内给电子体化合物在喷雾干燥的蒸发过程中,可以抑制雾滴的膨胀、崩溃、破碎或分裂,从而减少多孔性的、不规则形状的、薄壁空心的催化剂组分微粒的产生,进而减少在催化剂生产输送过程中和催化剂在聚合过程中因催化剂破碎带来的聚合物细粉含量,同时,加入的内给电子体化合物有利于降低催化剂组份粒子中的溶剂含量。
[0033]
根据本发明,优选地,所述溶剂为酯、醚或酮中的至少一种,优选自c1~c4饱和脂肪羧酸的烷基酯、c7~c8芳香羧酸烷基酯、c2~c6脂肪醚、c3~c4环醚和c3~c6饱和脂肪酮中的至少一种;
[0034]
更优选地,所述溶剂选自甲酸甲酯、甲酸乙酯、甲酸异丙酯、甲酸正丙酯、乙酸甲酯、乙酸乙酯、乙酸正丙酯、乙酸异丙酯、乙酸正丁酯、乙酸异丁酯、乙醚、丙醚、己醚、四氢呋喃、丙酮和甲基异丁基酮中的至少一种;进一步优选为甲酸甲酯、乙酸乙酯、乙酸丁酯、乙醚、己醚、四氢呋喃、丙酮以及甲基异丁基酮中的至少一种,这些溶剂可以单独使用,也可以混合使用,最优选四氢呋喃。
[0035]
根据本发明,所述无机氧化物载体填充物为硅的氧化物和/或铝的氧化物,粒径为0.01~10微米,优选为0.01~5微米,更优选为0.1~1微米;最优选为0.1~1微米的二氧化硅。
[0036]
硅的氧化物或铝的氧化物为惰性载体,喷雾干燥中使用惰性载体有助于控制催化剂粒子的形状和组成,并且生成的催化剂粒形好,强度高,不易破粹。
[0037]
作为优选方案,无论选择哪一种无机氧化物载体填充物(填料),其应该是干燥的,即没有吸收的水分。通过在低于填料材料的烧结或熔点的温度下加热一段时间将填料干燥(但是,有些填料例如热解法二氧化硅由于其特定的制造方法,天然地具有低的残余湿气含量);通常,使用至少100℃的温度进行干燥,当可以接受延长的干燥时间或当填料具有低的熔化或烧结温度时可以使用更低的温度;无机填料材料通常在200~800℃的温度下进行干燥;同时,填料材料可以用任选1~10wt%的一种或多种路易斯酸(例如,三烷基铝化合物、氯烷基铝化合物或有机氯硅烷)进行处理,以除去包括水或羟基的极性杂质。
[0038]
本发明目的之二是提供本发明目的之一的用于烯烃聚合的催化剂组分的制备方法,所述制备方法包括以下步骤:
[0039]
步骤s1,母液制备:在惰性气氛下,将溶剂、卤化镁、含钛化合物和内给电子体化合物进行接触,反应制备母液;
[0040]
步骤s2,载体掺混:在惰性气氛下,在步骤s1进行过程中或之后加入无机氧化物载体填充物进行掺混,得到淤浆悬浮液;
[0041]
步骤s3,喷雾成型:将步骤s2得到的淤浆悬浮液进行喷雾干燥,得到所述催化剂组分。
[0042]
在本发明中,催化剂在惰性气氛下制备,惰性气体选自实验室及工业上常用的惰性气体即可,如氩气,氮气等易得、价格便宜的气体。
[0043]
其中,对原料的用量不做特别限定,技术人员可根据实际情况进行调整,以最终制得的催化剂组分中各组分的用量在以上所述范围内既可。
[0044]
本发明中,可以参考按以下原料用量制备:
[0045]
以原料总量为100%计:
[0046][0047][0048]
根据本发明的催化剂组分,所述卤化镁、含钛化合物和溶剂及内给电子体化合物的反应产物负载于所述无机氧化物载体填充物上。
[0049]
根据本发明,优选地,所述含钛化合物为卤化钛、铝还原卤化钛的产物、镁还原卤化钛的产物中的至少一种。
[0050]
优选地,所述含钛化合物中的卤化钛为三溴化钛、四溴化钛、三氯化钛或四氯化钛中的至少一种;所述含钛化合物中的铝还原卤化钛的产物通式为tixm·
nalx
p
,其中,0<n≤1,0<m≤3,0<p≤3,x是溴或氯;所述含钛化合物中的镁还原卤化钛的产物通式为tixm·
qmgxr,其中,0<q≤1,0<m≤3,0<r≤2,x是溴或氯。所述铝还原卤化钛的产物优选ticl3·
1/3alcl3,所述镁还原卤化钛的产物优选为ticl3·
1/2mgcl2。一般的,其它还原剂也可以作为还原卤化钛的还原剂,如,氢化铝锂、铜、铁、锌、锡等。
[0051]
根据本发明,优选地,所述卤化镁选自二氯化镁、二溴化镁或二碘化镁中的至少一种,进一步优选为二氯化镁;
[0052]
根据本发明,所述铝还原卤化钛的产物、镁还原卤化钛的产物可通过本领域常规方法制得。
[0053]
无机氧化物载体填充物掺混可以在母液制备的任何时候加入,例如,在溶剂中将卤化镁、无机氧化物载体填充物、含钛化合物和内给电子体化合物进行掺混、反应,得到淤浆液料,将得到的淤浆液进行喷雾干燥,得到所述催化剂组分。
[0054]
作为优选方案,载体掺混为:将制备的母液与无机氧化物载体填充物进行掺混,得到淤浆悬浮液。
[0055]
根据本发明,所述步骤s1中,反应温度为常温~85℃,反应时间不低于0.1小时,和/或,
[0056]
根据本发明,所述步骤s3中的喷雾条件包括:进口温度为100~240℃,优选为120~160℃;出口温度为60~130℃,优选为90~115℃。
[0057]
在上述制备方法中,应当将足够数量的无机氧化物载体填充物与母液相混合,形成适合于进行喷雾干燥的淤浆液。
[0058]
本发明目的之三是提供本发明目的之一的用于烯烃聚合的催化剂组分在制备用
于烯烃聚合的催化剂中的应用。
[0059]
本发明目的之四是提供一种用于烯烃聚合的催化剂。
[0060]
所述催化剂由包含以下原料的组分制备得到:
[0061]
(a)本发明目的之一的催化剂组分;
[0062]
(b)通式为a1rbx’3-b
的有机铝化合物,其中,r为氢或碳原子数为1-20的烃基,x’为卤素,优选为氯、溴或碘,0<b≤3。
[0063]
作为优选方案,在通式a1rbx’3-b
中,可以选择1<b≤3。
[0064]
优选地,所述有机铝化合物优选自一氯二乙基铝和/或三乙基铝、三异丁基铝、三正己基铝、三正辛基铝中的至少一种。
[0065]
优选地,在所述催化剂中,组分(b)中所含的铝与组分(a)中所含的钛的摩尔比为(5:1)~(1000:1),也可以进一步优选为(10:1)~(200:1)。
[0066]
为了使喷雾干燥后得到的固体催化剂组分适用于生产烯烃聚合物,必须采用活化剂组分有机铝化合物对所述催化剂组分进行活化处理。优选地,在烃类溶剂中,将本发明得到的固体催化剂组分与活化剂组分进行反应,得到催化剂;或者在聚合过程中将本发明得到的固体催化剂组分与活化剂组分进行反应,从而引发烯烃聚合反应。
[0067]
作为优选方案,所述烃类溶剂为异戊烷、己烷、庚烷、甲苯、二甲苯、石脑油或矿物油中的至少一种。
[0068]
本发明目的之五是提供本发明目的之四的催化剂在烯烃聚合特别是乙烯均聚合或共聚合反应中的应用。
[0069]
本发明的催化剂尤其适用于乙烯的均聚合或乙烯与一种或多种α-烯烃的共聚合,其中的α-烯烃选用丙烯、丁烯、戊烯、己烯、辛烯、4-甲基戊烯-1中的一种或其中几种的混合物。其聚合工艺适合采用气相法、淤浆法和溶液法,更适合于气相聚合。
[0070]
本发明与已有技术相比,具有如下优点:
[0071]
本发明的用于烯烃聚合或共聚合的催化剂,其采用无机氧化物载体填充物做载体,用溶剂对卤化镁进行溶解,并加入一定比例的含钛化合物和内给电子体化合物,用喷雾干燥的方法制备。该催化剂组份粒子中的溶剂含量低,催化剂微粒子少。该催化剂用于催化乙烯聚合,催化剂活性高、氢调性能好、所得聚合物粉料堆积密度高、聚合物粉料细粉含量低。尤其是一定范围内随内给电子体化合物加入,催化剂的活性提高;在较高氢/烯比的条件下,所得聚合物熔融指数提高幅度大,在较低氢/烯比的条件下,所得聚合物熔融指数变化幅度小。
具体实施方式
[0072]
下面结合具体实施例对本发明进行具体的描述,有必要在此指出的是以下实施例只用于对本发明的进一步说明,不能理解为对本发明保护范围的限制,本领域技术人员根据本发明内容对本发明做出的一些非本质的改进和调整仍属本发明的保护范围。
[0073]
测试方法:
[0074]
1、活性:用每克催化剂所得聚合物粉料的重量表示;
[0075]
2、聚合物熔融指数(mi):参照astm d1238-99,载荷2.16kg,190℃下确定。
[0076]
3、聚合物表观堆积密度(bd):参照astmd1895-69标准进行测试。
[0077]
4、筛分分析数值:参照astmd-1921标准。
[0078]
5、催化剂粒径:采用mastersizer2000粒度仪测定,用术语d
10
、d
50
、d
90
表示,即标准对数粒径分布的特殊百分分布,如催化剂粒径具有d
50
的24μm,则其中间粒径为24μm;d
10
的7μm表示10%的颗粒直径小于7μm;d
90
的45μm表示90%的颗粒粒径小于45μm。
[0079]
6、钛、镁含量:采用spectrumlab 752s紫外可见分光光度计测定;固体催化剂组分的内给电子体含量采用液体核磁1h-nmr。
[0080]
7、thf含量:采用agilent technologies 7890a gc system测定。
[0081]
实施例中所用原料均为市售。
[0082]
实施例1
[0083]
(1)催化剂组分的制备
[0084]
向一个装有温度控制器、搅拌器、回流冷凝器的、经过氮气吹排并保护的250ml的四口烧瓶中,在搅拌下先后加入100ml(89克)四氢呋喃(thf)、3.73克氯化镁、0.89ml(1.54克)的ticl4,0.2克对甲氧基苯酚,搅拌下升温至68℃,在此温度下恒温回流反应2小时,得到母液。在此过程中一直保持在氮气氛围中(<5ppmh2o);
[0085]
向一个装有温度控制器、搅拌器、回流冷凝器的、经过氮气吹排并保护的250ml的四口烧瓶中,加入6.5克硅胶(cabot corporation ts-610,粒径为0.1~1微米),在搅拌下将上述母液加入,在68℃继续恒温回流搅拌2小时,使硅胶完全分散于母液中,得到淤浆悬浮液。在此过程中一直保持在氮气氛围中(<5ppmh2o);
[0086]
在闭路循环气流式喷雾干燥器(如mini spray dryerb-290)上,将载气进口温度145℃的氮气引入喷雾干燥器中,向循环干燥器中加入43℃的所得淤浆悬浮液,调整淤浆悬浮液进料速度和室温的喷雾气体(n2)流量分别为27ml/min和350l/h左右,调整载气(n2)流量,使出口温度98℃,得到固体催化剂组分。所得催化剂组分具有所希望的粒径d
50
=20~23微米左右。所得催化剂组分参数见表1。
[0087]
(2)乙烯淤浆聚合
[0088]
低氢/烯比聚合:将经过先氮气、后氢气吹排的2升聚合釜中加入1升己烷,同时加入1毫升1mmol的三乙基铝和20毫克催化剂组分,升温至70℃加入氢气至0.28mpa,加氢完毕后加入乙烯至1.03mpa,升温到85℃,在85℃恒温、恒压反应2小时后,降温出料。聚合结果见表2。
[0089]
高氢/烯比聚合:将经过先氮气、后氢气吹排的2升聚合釜中加入1升己烷,同时加入1毫升1mmol的三乙基铝和20毫克催化剂组分,升温至70℃加入氢气至0.68mpa,加氢完毕后加入乙烯至1.03mpa,升温到85℃,在85℃恒温、恒压反应2小时后,降温出料。聚合结果见表2。
[0090]
实施例2
[0091]
(1)催化剂组分的制备
[0092]
向一个装有温度控制器、搅拌器、回流冷凝器的、经过氮气吹排并保护的250ml的四口烧瓶中,在搅拌下先后加入100ml(89克)四氢呋喃(thf)和0.33克镁粉(平均粒径80~100微米)然后,用时0.5小时缓慢加入4ml(6.9克)的ticl4,加热到50℃,恒温搅拌6小时,得到三氯化钛、氯化镁与四氢呋喃的溶液。在此过程中一直保持在氮气氛围中(<5ppmh2o);
[0093]
向一个装有温度控制器、搅拌器、回流冷凝器的、经过氮气吹排并保护的250ml的
四口烧瓶中,在搅拌下先后加入77ml(68.5克)四氢呋喃(thf)、3.79克氯化镁、33.3ml(32.04克)静置1小时的上述三氯化钛、氯化镁与四氢呋喃溶液的上层清液,0.4克对甲氧基苯酚,搅拌下升温至68℃,在此温度下恒温回流反应2小时,得到母液。在此过程中一直保持在氮气氛围中(<5ppmh2o);
[0094]
向一个装有温度控制器、搅拌器、回流冷凝器的、经过氮气吹排并保护的250ml的四口烧瓶中,加入5克硅胶(cabot corporation ts-610,粒径为0.1~1微米),在搅拌下将上述母液加入,在68℃继续恒温回流搅拌2小时,使硅胶完全分散于母液中,得到淤浆悬浮液。在此过程中一直保持在氮气氛围中(<5ppmh2o);
[0095]
在闭路循环气流式喷雾干燥器(如mini spray dryerb-290)上,将载气进口温度145℃的氮气引入喷雾干燥器中,向循环干燥器中加入43℃的所得淤浆悬浮液,调整淤浆悬浮液进料速度和室温的喷雾气体(n2)流量分别为24ml/min和330l/h左右,调整载气(n2)流量,使出口温度102℃,得到固体催化剂组分。所得催化剂组分具有所希望的粒径d
50
=20~23微米左右。所得催化剂组分参数见表1。
[0096]
(2)乙烯淤浆聚合
[0097]
低氢/烯比聚合:将经过先氮气、后氢气吹排的2升聚合釜中加入1升己烷,同时加入1毫升1mmol的三乙基铝和20毫克催化剂组分,升温至70℃加入氢气至0.28mpa,加氢完毕后加入乙烯至1.03mpa,升温到85℃,在85℃恒温、恒压反应2小时后,降温出料。聚合结果见表2。
[0098]
高氢/烯比聚合:将经过先氮气、后氢气吹排的2升聚合釜中加入1升己烷,同时加入1毫升1mmol的三乙基铝和20毫克催化剂组分,升温至70℃加入氢气至0.68mpa,加氢完毕后加入乙烯至1.03mpa,升温到85℃,在85℃恒温、恒压反应2小时后,降温出料。聚合结果见表2。
[0099]
实施例3
[0100]
(1)催化剂组分的制备
[0101]
向一个装有温度控制器、搅拌器、回流冷凝器的、经过氮气吹排并保护的250ml的四口烧瓶中,在搅拌下先后加入100ml(89克)四氢呋喃(thf)、5.3克氯化镁、2.1克ticl3·
1/3alcl3(tosoh finechem corporation,ticl
3-aa),0.8克对甲氧基苯酚,搅拌下升温至68℃,在此温度下恒温回流反应2小时,得到母液。在此过程中一直保持在氮气氛围中(<5ppmh2o);
[0102]
向一个装有温度控制器、搅拌器、回流冷凝器的、经过氮气吹排并保护的250ml的四口烧瓶中,加入6.6克硅胶(cabot corporation ts-610,粒径为0.1~1微米),在搅拌下将上述母液加入,在68℃继续恒温回流搅拌2小时,使硅胶完全分散于母液中,得到淤浆悬浮液。在此过程中一直保持在氮气氛围中(<5ppmh2o);
[0103]
在闭路循环气流式喷雾干燥器(如mini spray dryerb-290)上,将载气进口温度145℃的氮气引入喷雾干燥器中,向循环干燥器中加入43℃的所得淤浆悬浮液,调整淤浆悬浮液进料速度和室温的喷雾气体(n2)流量分别为23ml/min和330l/h左右,调整载气(n2)流量,使出口温度103℃,得到固体催化剂组分。所得催化剂组分具有所希望的粒径d
50
=20~23微米左右。所得催化剂组分参数见表1。
[0104]
(2)乙烯淤浆聚合
[0105]
低氢/烯比聚合:将经过先氮气、后氢气吹排的2升聚合釜中加入1升己烷,同时加入1毫升1mmol的三乙基铝和20毫克催化剂组分,升温至70℃加入氢气至0.28mpa,加氢完毕后加入乙烯至1.03mpa,升温到85℃,在85℃恒温、恒压反应2小时后,降温出料。聚合结果见表2。
[0106]
高氢/烯比聚合:将经过先氮气、后氢气吹排的2升聚合釜中加入1升己烷,同时加入1毫升1mmol的三乙基铝和20毫克催化剂组分,升温至70℃加入氢气至0.68mpa,加氢完毕后加入乙烯至1.03mpa,升温到85℃,在85℃恒温、恒压反应2小时后,降温出料。聚合结果见表2。
[0107]
实施例4
[0108]
与实施例2相比,只是在步骤(1)催化剂组分的制备中将对甲氧基苯酚加入量由0.4克改为1.5克;在步骤(2)乙烯淤浆聚合中增加中氢/烯比聚合:将经过先氮气、后氢气吹排的2升聚合釜中加入1升己烷,同时加入1毫升1mmol的三乙基铝和20毫克催化剂组分,升温至70℃加入氢气至0.50mpa,加氢完毕后加入乙烯至1.03mpa,升温到85℃,在85℃恒温、恒压反应2小时后,降温出料。其它与实施例2相同。所得催化剂组分参数见表1,聚合结果见表2。
[0109]
实施例5
[0110]
与实施例2相比,只是在步骤(1)催化剂组分的制备中将0.4克对甲氧基苯酚改为0.4克邻甲氧基苯酚,其它与实施例2相同。所得催化剂组分参数见表1,聚合结果见表2。
[0111]
实施例6
[0112]
与实施例2相比,只是在步骤(1)催化剂组分的制备中将0.4克对甲氧基苯酚改为0.4克对乙氧基苯酚,其它与实施例2相同。所得催化剂组分参数见表1,聚合结果见表2。
[0113]
实施例7
[0114]
与实施例3相比,只是在步骤(1)催化剂组分的制备中将0.8克对甲氧基苯酚改为0.80克对苯氧基苯酚,其它与实施例3相同。所得催化剂组分参数见表1,聚合结果见表2。
[0115]
实施例8
[0116]
与实施例3相比,只是在步骤(1)催化剂组分的制备中将2.1克ticl3·
1/3alcl3改为1.1克ticl3·
1/3alcl3,其它与实施例3相同。所得催化剂组分参数见表1,聚合结果见表2。
[0117]
实施例9
[0118]
与实施例3相比,只是在步骤(1)催化剂组分的制备中将2.1克ticl3·
1/3alcl3改为4.2克ticl3·
1/3alcl3,其它与实施例3相同。所得催化剂组分参数见表1,聚合结果见表2。
[0119]
实施例10
[0120]
与实施例3相比,只是在步骤(1)催化剂组分的制备中将5.3克氯化镁改为6.3克氯化镁,其它与实施例3相同。所得催化剂组分参数见表1,聚合结果见表2。
[0121]
实施例11
[0122]
与实施例3相比,只是在步骤(1)催化剂组分的制备中将5.3克氯化镁改为2.7克氯化镁,其它与实施例3相同。所得催化剂组分参数见表1,聚合结果见表2。
[0123]
实施例12
[0124]
与实施例3相比,只是在步骤(1)催化剂组分的制备中将对甲氧基苯酚加入量由0.8克改为0.03克;在步骤(2)乙烯淤浆聚合中增加中氢/烯比聚合:将经过先氮气、后氢气吹排的2升聚合釜中加入1升己烷,同时加入1毫升1mmol的三乙基铝和20毫克催化剂组分,升温至70℃加入氢气至0.50mpa,加氢完毕后加入乙烯至1.03mpa,升温到85℃,在85℃恒温、恒压反应2小时后,降温出料。其它与实施例3相同。所得催化剂组分参数见表1,聚合结果见表2。
[0125]
实施例13
[0126]
与实施例3相比,只是在步骤(1)催化剂组分的制备中将对甲氧基苯酚加入量由0.8克改为2.4克,其它与实施例3相同。所得催化剂组分参数见表1,聚合结果见表2。
[0127]
对比例1
[0128]
与实施例1相比,只是在步骤(1)催化剂组分的制备中不再加入0.2克对甲氧基苯酚,其它与实施例1相同。所得催化剂组分参数见表1,聚合结果见表2。
[0129]
对比例2
[0130]
与实施例2相比,只是在步骤(1)催化剂组分的制备中不再加入0.4克对甲氧基苯酚;在步骤(2)乙烯淤浆聚合中增加中氢/烯比聚合:将经过先氮气、后氢气吹排的2升聚合釜中加入1升己烷,同时加入1毫升1mmol的三乙基铝和20毫克催化剂组分,升温至70℃加入氢气至0.50mpa,加氢完毕后加入乙烯至1.03mpa,升温到85℃,在85℃恒温、恒压反应2小时后,降温出料。其它与实施例2相同。所得催化剂组分参数见表1,聚合结果见表2。
[0131]
对比例3
[0132]
与实施例3相比,只是在步骤(1)催化剂组分的制备中不再加入0.8克对甲氧基苯酚,其它与实施例3相同。所得催化剂组分参数见表1,聚合结果见表2。
[0133]
表1催化剂组分参数
[0134][0135]
由表1可知,本发明内给电子体的加入能够有效降低催化剂组分粒子中的四氢呋喃含量,催化剂组份粒子的d
10
变大,微粒子减少。
[0136]
表2聚合物性能
[0137][0138][0139]
续表2聚合物性能
[0140][0141]
本发明表中2,聚合物粉料进行筛分时,由于筛体粘连,会造成称量减少,聚合物粉料粒度分布对应的百分比总和一般会小于100%。上述实施例中出现大于100%的结果,是由于计算过程中对数据进行四舍五入造成的,属于误差允许的范围。
[0142]
由表2可知,本发明催化剂用于催化乙烯聚合,催化剂活性提高,所得聚合物粉料堆积密度高、聚合物粉料细粉含量低,聚合物粉料粒度增加,粒度分布向大粒子方向移动。一般情况下,聚合反应器中氢/烯提高会使得催化剂的活性降低,本发明的催化剂尤其是在较高氢/烯比的条件下,所得聚合物熔融指数提高幅度大,说明本发明的催化剂在较高氢/烯比的条件下仍具有较高的催化剂活性和较好的氢调性能;在较低氢/烯比的条件下,所得聚合物熔融指数变化幅度小,说明本发明的催化剂在在较低氢/烯比下,具有较高的催化剂活性,氢调性能不提高或提高幅度不大,这些是聚合所希望的。
[0143]
以上已经描述了本发明的各实施例,上述说明是示例性的,并非穷尽性的,并且也不限于所披露的各实施例。在不偏离所说明的各实施例的范围和精神的情况下,对于本技术领域的普通技术人员来说许多修改和变更都是显而易见的。