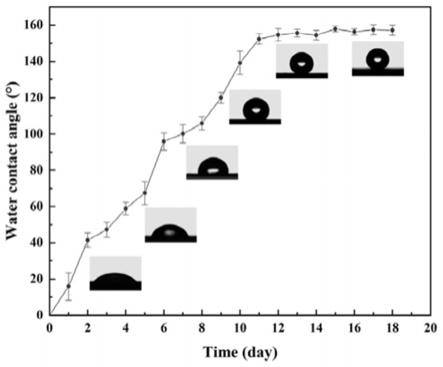
一种在塑料表面制备cu
‑
cnts超疏水镀层的方法
技术领域
1.本发明属于疏水镀层领域,具体涉及一种在塑料表面制备cu
‑
cnts超疏水镀层的方法。
背景技术:2.塑料由于质量轻、化学稳定性好以及优异的加工性能被广泛应用于航空航天、汽车、通讯设备和日常生活用品中。塑料表面金属化工艺可以结合塑料和金属的优点,使材料获得优良的综合性能,保持塑料低密度的同时赋予其金属的特性,如导电性、耐磨性、电磁屏蔽性以及装饰性等。
3.在微电子、汽车等行业,电镀法是最常用的塑料表面金属化方法,通过在表面电镀铜,可使材料表面获得金属的特性,从而实现导电、耐摩擦等各种性能,但纯铜镀层表面易吸附腐蚀介质导致化学腐蚀、电化学腐蚀。超疏水表面是指水滴在表面的接触角大于等于150
°
,滚动角小于等于10
°
的表面,超疏水表面表现出憎水性,当表面呈一定倾斜角时水滴会滚落,超疏水表面可以有效减少材料与水滴的接触面积,从而抑制腐蚀行为的发生。
4.一般而言,制备超疏水表面需要两个步骤:一是在材料表面通过物理或者化学的方法构造一个微纳粗糙结构;二是通过含氟等低表面能物质对所构造的粗糙表面进行修饰,降低材料表面能。但是目前的工艺往往需要复杂昂贵的设备和含氟类有害物质,因此限制了超疏水表面的工业化应用。
5.综上所述,针对现有技术的不足,发展一种工艺简单、成本低、制作周期短的超疏水表面制备方法有利于超疏水表面的工业化应用。
技术实现要素:6.为了解决现有超疏水表面制作周期长、生产工艺复杂的特点,本发明提供一种在塑料表面制备cu
‑
cnts超疏水镀层的方法。该处理过程易于实现,制作周期短、生产成本低、适于工业化规模生产。
7.本发明的目的通过下述技术方案实现。
8.一种在塑料表面制备cu
‑
cnts超疏水镀层的方法,包括以下步骤:
9.(1)电镀cu
‑
cnts复合镀层:将预镀银处理后的塑料置于复合镀液中,通过电镀法制备cu
‑
cnts复合镀层;所述复合镀液由碳纳米管(cnts)、十二烷基硫酸钠、五水硫酸铜、硫酸和水组成;
10.(2)cu
‑
cnts复合镀层的浸润性转变:将步骤(1)所得cu
‑
cnts复合镀层进行清洗,随后放置于空气中或进行干燥,cu
‑
cnts复合镀层由亲水状态转变为超疏水状态。
11.优选的,步骤(1)所述复合镀液组成成分为:碳纳米管1~2.5g/l、十二烷基硫酸钠0.5~1.5g/l、五水硫酸铜180~240g/l、硫酸20~40ml/l。
12.优选的,步骤(1)所述电镀的温度为20~30℃,电流密度为0.5~2.5a/dm2,电镀时间为3~10分钟。电流密度进一步优选为1~2.5a/dm2。
13.优选的,所述电镀的过程附加500r/min的磁力搅拌。
14.优选的,步骤(2)中,所述干燥的温度为70~90℃,时间为48~72小时;所述放置于空气中的时间大于等于11天。
15.优选的,步骤(1)所述碳纳米管为羧基化的多壁碳纳米管,且直径小于8nm,长度为10~30μm。
16.优选的,步骤(1)所述复合镀液通过如下方法制备:
17.将五水硫酸铜溶解于去离子水中,加入硫酸,得到电镀液;取碳纳米管和十二烷基硫酸钠在去离子水中超声分散均匀,再加入到电镀液中,在超声作用下混合均匀,得到cu
‑
cnts复合镀液。
18.优选的,步骤(1)所述塑料为丙烯腈
‑
丁二烯
‑
苯乙烯(abs)塑料。
19.优选的,步骤(1)所述预镀银处理包括以下步骤:
20.将abs塑料清洗之后依次置于硅烷偶联剂溶液和敏化液中进行表面改性处理和敏化处理,随后置于化学镀银液中进行预镀银处理;以上每一步处理之后都需用去离子水和无水乙醇清洗;
21.所述的硅烷偶联剂溶液为3
‑
巯基丙基三乙氧基硅烷(mptes)的酒精溶液,其中3
‑
巯基丙基三乙氧基硅烷的浓度为10~30ml/l,酒精溶液由体积分数为1:9的去离子水和无水乙醇组成;所述表面改性处理为将工件置于硅烷偶联剂溶液中浸泡50~70分钟;
22.所述敏化液为氯化亚锡与盐酸的水溶液,其中氯化亚锡浓度为15~25g/l,盐酸浓度为30~50ml/l,所用盐酸为37wt%的盐酸溶液;敏化条件为将工件在常温的敏化液中浸泡5~15分钟;
23.所述预镀银处理为将工件放置在40~50℃的银氨溶液中,加入同等体积的还原剂溶液施镀5~15分钟,其中银氨溶液由15~20g/l的硝酸银溶液滴加氨水至澄清制成,还原剂为7.5~10g/l的葡萄糖的水溶液。
24.由以上任一项所述的方法制备的cu
‑
cnts超疏水镀层;该cu
‑
cnts超疏水镀层具备良好导电性和超疏水性能(水接触角大于150
°
,滚动角小于10
°
)。
25.与现有技术相比,本发明具有如下的优点及效果:
26.(1)本发明在abs塑料表面制备cu
‑
cnts超疏水镀层的方法最快只需3分钟即可在导电表面制备超疏水膜层,制备周期短,生产成本低,适于工业化规模生产;
27.(2)本发明的超疏水膜层制备方法可以通过镀层在空气中对低表面能物质的吸附来完成亲水到疏水的浸润性转变,无需进一步对其进行低表面能物质修饰;
28.(3)本发明制备cu
‑
cnts超疏水镀层的方法,无需使用特殊的设备,其制备方法简单,处理工艺易于控制,避免了含氟有害物质的使用,复合镀液成分简单,易于处理,对环境危害较小。
附图说明
29.图1为实施例1所制备的cu
‑
cnts超疏水镀层的扫描电子显微镜图与接触角测试结果图;
30.图2为实施例2所制备的cu
‑
cnts超疏水镀层的扫描电子显微镜图与接触角测试结果图;
31.图3为实施例3所制备的cu
‑
cnts超疏水镀层的扫描电子显微镜图与接触角测试结果图。
32.图4为对比例1所制备的铜
‑
石墨烯复合镀层的接触角测试结果图。
33.图5为实施例2所制备的cu
‑
cnts复合镀层浸润性转变测试结果图。
具体实施方式
34.下面结合实施例及附图对本发明作进一步详细的描述,但本发明的实施方式不限于此。
35.实施例1
36.一种在abs塑料表面制备cu
‑
cnts超疏水镀层的方法,具体操作步骤如下:
37.步骤一:abs塑料硅烷偶联剂改性处理
38.将清洗后的尺寸为30
×
40
×
1(mm)的abs塑料置入100ml硅烷偶联剂溶液中浸泡50分钟;取出后用去离子水和无水乙醇冲洗吹干待用;其中硅烷偶联剂(mptes)浓度为10ml/l。
39.步骤二:abs塑料敏化处理
40.将步骤一中得到的abs塑料置入100ml敏化液中于室温浸泡5分钟;取出后用去离子水和无水乙醇冲洗吹干待用;敏化液为15g/l氯化亚锡和30ml/l盐酸(37wt%)混合溶液。
41.步骤三:abs塑料化学镀银
42.将步骤二中得到的abs塑料浸泡到100ml银氨溶液中,加入同等体积的还原剂溶液在40℃条件下均匀混合5分钟取出,用去离子水和无水乙醇冲洗吹干待用;所述银氨溶液由15g/l硝酸银溶液滴加氨水至澄清制成,所述还原剂溶液为7.5g/l的葡萄糖溶液。
43.步骤四:cu
‑
cnts复合镀液的配制
44.将180g五水硫酸铜溶解于1l去离子水中,加入20ml浓硫酸(98%),得到电镀液;取50ml去离子水加入1g碳纳米管和0.5g十二烷基硫酸钠超声分散均匀,再加入到950ml电镀液中,在超声作用下混合均匀,得到cu
‑
cnts复合镀液。
45.步骤五:abs塑料电镀cu
‑
cnts超疏水镀层
46.将步骤三中得到的表面镀银的abs塑料置于步骤四得到的复合镀液中电镀处理,电镀温度为20℃,电流密度为1a/dm2,电镀时间3分钟,电镀过程需附加500r/min的磁力搅拌。
47.步骤六:干燥处理
48.将步骤五中得到的样品用去离子水和无水乙醇冲洗吹干后,置于70℃干燥箱中干燥处理48小时,即可在abs表面得到cu
‑
cnts超疏水镀层。
49.对所制备的abs表面cu
‑
cnts超疏水镀层进行了如下检测表征:
50.(1)形貌分析:本实施例所制备的cu
‑
cnts复合镀层的扫描电子显微镜图如图1中的(a)所示,复合镀层表面较为粗糙,铜晶粒呈层片状沉积于abs表面,片层之间中留存了大量空气,这种特殊的微观结构赋予其超疏水性能。
51.(2)浸润性测试:本实施例所制备的cu
‑
cnts复合镀层的接触角测试结果如图1中的(b)所示,其水接触角达到了151.4
°
。
52.(3)导电性能测试:本实施例所制备的cu
‑
cnts复合镀层导电性能通过四探针方阻
仪表征,其方阻为0.236ω/sq。
53.实施例2
54.一种在abs塑料表面制备cu
‑
cnts超疏水镀层的方法,具体操作步骤如下:
55.步骤一:abs塑料硅烷偶联剂改性处理
56.将清洗后的尺寸为30
×
40
×
1(mm)的abs塑料置入100ml硅烷偶联剂溶液中浸泡60分钟;取出后用去离子水和无水乙醇冲洗吹干待用;其中硅烷偶联剂(mptes)浓度为20ml/l。
57.步骤二:abs塑料敏化处理
58.将步骤一中得到的abs塑料置入100ml敏化液中于室温浸泡5分钟;取出后用去离子水和无水乙醇冲洗吹干待用;敏化液为20g/l氯化亚锡和40ml/l盐酸(37wt%)混合溶液。
59.步骤三:abs塑料化学镀银
60.将步骤二中得到的abs塑料浸泡到100ml银氨溶液中,加入同等体积的还原剂溶液在45℃条件下均匀混合10分钟取出,用去离子水和无水乙醇冲洗吹干待用;所述银氨溶液由17g/l硝酸银溶液滴加氨水至澄清制成,所述还原剂溶液为8.5g/l的葡萄糖溶液。
61.步骤四:cu
‑
cnts复合镀液的配制
62.将220g五水硫酸铜溶解于1l去离子水中,加入30ml浓硫酸(98%),得到电镀液;取50ml去离子水加入1.5g碳纳米管和1g十二烷基硫酸钠超声分散均匀,再加入到950ml电镀液中,在超声作用下混合均匀,得到cu
‑
cnts复合镀液。
63.步骤五:abs塑料电镀cu
‑
cnts超疏水镀层
64.将步骤三中得到的表面镀银的abs塑料置于步骤四得到的复合镀液中电镀处理,电镀温度为25℃,电流密度为1a/dm2,电镀时间为5分钟,电镀过程需附加500r/min的磁力搅拌。
65.步骤六:干燥处理
66.将步骤五中得到的样品用去离子水和无水乙醇冲洗吹干后,置于80℃干燥箱中干燥处理60小时,即可在abs表面得到cu
‑
cnts超疏水镀层。
67.对所制备的abs表面cu
‑
cnts超疏水镀层进行了如下检测表征:
68.(1)形貌分析:本实施例所制备的cu
‑
cnts复合镀层的扫描电子显微镜图如图2中的(a)所示,复合镀层表面较为粗糙,可以明显地看到其表面的片状结构交错叠加,捕获了大量空气。
69.(2)浸润性转变测试:将本实施例步骤五制备的工件暴露在空气环境中进行浸润性转变测试,所制备的cu
‑
cnts复合镀层刚制备时为超亲水状态(接触角约为0
°
),在空气中放置时会发生浸润性转变成超疏水状态(接触角约为158.7
°
),转变过程如图5所示。以上接触角测试均为在去除表面水分后进行,结果可知,复合镀层的特殊微观形貌使其在空气中放置时发生氧化和吸附空气污染物,导致表面形成有机污染物薄膜,这些非极性的空气污染物具有憎水性可以降低材料表面的自由能,从而赋予其超疏水性能。
70.(3)浸润性测试:本实施例所制备的cu
‑
cnts复合镀层的接触角测试结果如图2中的(b)所示,其水接触角达到了158.7
°
。
71.(4)导电性能测试:本实施例所制备的cu
‑
cnts复合镀层导电性能通过四探针方阻仪表征,其方阻为0.126ω/sq。
72.实施例3
73.一种在abs塑料表面制备cu
‑
cnts超疏水镀层的方法,具体操作步骤如下:
74.步骤一:abs塑料硅烷偶联剂改性处理
75.将清洗后的尺寸为30
×
40
×
1(mm)的abs塑料置入100ml硅烷偶联剂溶液中浸泡70分钟;取出后用去离子水和无水乙醇冲洗吹干待用;其中硅烷偶联剂(mptes)浓度为30ml/l。
76.步骤二:abs塑料敏化处理
77.将步骤一中得到的abs塑料置入100ml敏化液中于室温浸泡15分钟;取出后用去离子水和无水乙醇冲洗吹干待用;敏化液为25g/l氯化亚锡和40ml/l盐酸(37wt%)混合溶液。
78.步骤三:abs塑料化学镀银
79.将步骤二中得到的abs塑料浸泡到100ml银氨溶液中,加入同等体积的还原剂溶液在50℃条件下均匀混合15分钟取出,用去离子水和无水乙醇冲洗吹干待用;所述银氨溶液由20g/l硝酸银溶液滴加氨水至澄清制成,所述还原剂溶液为10g/l的葡萄糖溶液。
80.步骤四:cu
‑
cnts复合镀液的配制
81.将240g五水硫酸铜溶解于1l去离子水中,加入40ml浓硫酸(98%),得到电镀液;取50ml去离子水加入2.5g碳纳米管和1.5g十二烷基硫酸钠超声分散均匀,再加入到950ml电镀液中,在超声作用下混合均匀,得到cu
‑
cnts复合镀液。
82.步骤五:abs塑料电镀cu
‑
cnts超疏水镀层
83.将步骤三中得到的表面镀银的abs塑料置于步骤四得到的复合镀液中电镀处理,电镀温度为30℃,电流密度为2.5a/dm2,电镀时间为5分钟,电镀过程需附加500r/min的磁力搅拌。
84.步骤六:干燥处理
85.将步骤五中得到的样品用去离子水和无水乙醇冲洗吹干后,置于90℃干燥箱中干燥处理72小时,即可在abs表面得到cu
‑
cnts超疏水镀层。
86.对所制备的abs表面cu
‑
cnts超疏水镀层进行了如下检测表征:
87.(1)形貌分析:本实施例所制备的cu
‑
cnts复合镀层的扫描电子显微镜图如图3中的(a)所示,复合镀层表面片状cu不断生长叠加,形成微观粗糙结构。
88.(2)浸润性测试:本实施例所制备的cu
‑
cnts复合镀层的接触角测试结果如图3中的(b)所示,其水接触角达到了153.4
°
。
89.(3)导电性能测试:本实施例所制备的cu
‑
cnts复合镀层导电性能通过四探针方阻仪表征,其方阻为0.031ω/sq。
90.实施例4
91.在实施例2基础上,控制其他条件不变,改变电镀过程中电流密度分别为:0.5a/dm2、1a/dm2、1.5a/dm2、2a/dm2、2.5a/dm2。导电性能与超疏水性能的变化如表1所示:
92.表1
93.[0094][0095]
由表1可知,随电流密度的升高,复合镀层的方阻持续下降。这是由于在其他条件不变的情况下,增大电流密度可以使镀层厚度增加,从而提高镀层的导电性能。
[0096]
另外,可以观察到镀层超疏水性能是随电流密度增加先上升后下降。当电流密度较低时,镀层片状铜颗粒彼此较为分散,无法截留空气足够的空气膜层,难以形成稳定的超疏水模型。当电流密度较大时,片状的铜颗粒易发生聚集,导致超疏水性能下降。因此当电流密度为1a/dm2时,镀层超疏水性能最佳,此时片状的铜颗粒交错重叠,形成了稳定的cassie
‑
baxter模型,在颗粒之间截留大量空气,提高了其憎水性。
[0097]
对比例1
[0098]
在实施例2基础上,控制其他条件不变,将碳纳米管替换为石墨烯材料,在abs塑料表面制备铜
‑
石墨烯复合镀层,并进行如下表征:
[0099]
(1)浸润性测试:本对比例所制备的铜
‑
石墨烯复合镀层的接触角测试结果如图4所示,其水接触角为112.9
°
。可见铜
‑
石墨烯复合镀层无法形成与cu
‑
cnts复合镀层类似的超疏水性能。
[0100]
(2)导电性能测试:本实施例所制备的铜
‑
石墨烯复合镀层导电性能通过四探针方阻仪表征,其方阻为0.016ω/sq。