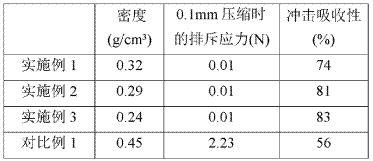
1.本发明涉及汽车零部件加工领域。具体地,本发明涉及用于制备零部件的组合物以及由其制备的零部件。
背景技术:2.碰撞吸能区的概念是梅塞德斯
•
奔驰在20世纪60年代首次提出来的,其设计为在发生撞击时汽车车身发生逐渐变形,以吸附事故中产生的绝大部分(如果不是全部)的撞击能量。车身改为这种可以变形的设计后,乘员所承受的强烈的撞击力就可以大大减小。
3.人们常将汽车的碰撞分为“一次碰撞”,而将人体与车内部件的碰撞成为“二次碰撞”。这样来分的话汽车可分为两类区域,即乘员安全区和缓冲吸能区。
[0004]“一次碰撞”在很大程度上决定了“二次碰撞”的剧烈程度,因此“一次碰撞”对人体损害有很大影响。控制好“一次碰撞”,对减少人体损伤有重要意义,合理设计汽车结构的缓冲与吸能材料特性是控制好“一次碰撞”的关键。
[0005]
仅从乘员不被汽车碰撞变形后产生挤压受伤的角度看,乘员安全区在碰撞中的变形越小越好。要使乘员安全区变形小,就要求缓冲吸能区有较大的总体刚度,但缓冲吸能区的刚度过大又会影响汽车的缓冲吸能性能。从缓冲吸能角度看,缓冲吸能区的刚性应足够小,变形应足够大,这就导致了乘员安全区变形小与缓冲吸能区变形大的矛盾。
[0006]
为解决这一矛盾,除了对汽车吸能结构设计进行改进外,吸能材料的研发也可以起到事半功倍的效果。通常制备传统的吸能材料使用低沸点液体进行发泡或制孔,加工条件繁琐且效率低下,吸能效果不明显。
[0007]
因此,希望寻求新的吸能材料,用其加工零部件工艺简单、生产效率高且所得零部件具有良好的冲击吸收性能。
技术实现要素:[0008]
本发明的目的在于提供一种新的吸能材料,用其加工零部件工艺简单、生产效率高且所得零部件具有良好的冲击吸收性能。
[0009]
根据第一方面,本发明提供一种用于制备零部件的组合物,其特征在于,包含:容纳有致孔剂的聚苯乙烯微胶囊;聚苯乙烯树脂;和线性低密度聚乙烯。
[0010]
根据第二方面,本发明提供一种用于制备零部件的方法,其特征在于,包括将上述组合物进行热压成型。
[0011]
根据第三方面,本发明提供一种零部件,其特征在于,其采用上述组合物制备。
[0012]
由本发明的组合物加工零部件工艺简单、生产效率高,适合于大规模生产,且所得零部件具有良好的冲击吸收性能。
附图说明
[0013]
下面结合附图对本发明进行更详细地说明和解释,其中:图1为实施例1中制备的微胶囊的扫描电镜照片。
[0014]
图2为实施例1中制备的零部件截面的扫描电子显微镜图。
[0015]
图3为实施例2中制备的零部件截面的扫描电子显微镜图。
具体实施方式
[0016]
在下文中,将更全面地体现本发明的各方面以及更进一步的目的、特征和优点。
[0017]
根据第一方面,本发明提供一种用于制备零部件的组合物,其特征在于,包含:容纳有致孔剂的聚苯乙烯微胶囊;聚苯乙烯树脂;和线性低密度聚乙烯。
[0018]
在本技术中,术语“聚苯乙烯微胶囊”与术语“聚苯乙烯树脂”不同。聚苯乙烯微胶囊是由聚苯乙烯形成的空心壳体。聚苯乙烯树脂是实心聚苯乙烯。
[0019]
在本技术中,术语“聚苯乙烯微胶囊”与术语“容纳有致孔剂的聚苯乙烯微胶囊”不同。当提及前者时,聚苯乙烯微胶囊中未容纳致孔剂。
[0020]
就聚苯乙烯微胶囊和聚苯乙烯树脂而言,所述聚苯乙烯可以为通常用于加工汽车零部件所使用的那些。
[0021]
优选地,所述聚苯乙烯微胶囊的粒径为40μm
‑
60μm。
[0022]
优选地,所述致孔剂选自丙酮、四氢呋喃、及其混合物。
[0023]
所述容纳有致孔剂的聚苯乙烯微胶囊可以通过如下来制备:将聚苯乙烯微胶囊加入致孔剂中,搅拌使聚苯乙烯微胶囊溶胀,从而使致孔剂充满聚苯乙烯微胶囊中;然后将溶胀的聚苯乙烯微胶囊离心、过滤、阴干。
[0024]
优选地,搅拌使得致孔剂充满聚苯乙烯微胶囊的时间可以为大约30分钟以上,例如大约30分钟至60分钟。
[0025]
本领域技术人员可根据实践调节离心工艺参数,例如以3000
‑
4200rpm的离心速度。
[0026]
所述聚苯乙烯微胶囊可以购买获得,也可以自行制备。
[0027]
例如,可以按照如下制备聚苯乙烯微胶囊:(1)将溶有引发剂偶氮二异丁腈的苯乙烯、甲基丙烯酸甲酯和熔融的正十六烷混合均匀,得到溶液a;(2)将聚乙烯醇溶解在去离子水中;(3)将溶液a加入到步骤(2)的体系中,通入氮气保护,然后升温至60℃,以1200
‑
1800r /min的转速搅拌乳化30min;(4)将步骤(3)的体系升温至80℃,转速为400r/min连续搅拌聚合4h;反应结束后,用去离子水清洗并减压抽滤,自然干燥得到聚苯乙烯微胶囊。
[0028]
聚苯乙烯微胶囊制备中各物质以重量份计为:苯乙烯100份、正十六烷100份、甲基丙烯酸甲酯30份,偶氮二异丁腈2份、聚乙烯醇2份、去离子水60份。
[0029]
优选地,所述容纳有致孔剂的聚苯乙烯微胶囊与所述聚苯乙烯树脂的质量比为1:
8至1:11,更优选1:9至1:10。
[0030]
所述线性低密度聚乙烯可以为通常用于加工汽车零部件所使用的那些。
[0031]
优选地,所述线性低密度聚乙烯的密度为0.918
‑
0.935g/cm3。
[0032]
所述线性低密度聚乙烯的密度采用gb1033
‑
1986进行测试。
[0033]
优选地,所述线性低密度聚乙烯与聚苯乙烯树脂的质量比为1:3
‑
1:5。
[0034]
所述组合物可以通过将容纳有致孔剂的聚苯乙烯微胶囊、线性低密度聚乙烯和聚苯乙烯树脂均匀混合而成。
[0035]
通过将致孔剂(如丙酮)包覆在微胶囊中,可以在初混过程使得致孔剂在基质中得到较好的分散,避免后续形成的空洞不均匀,同时可以在基质熔化之前避免了致孔剂的挥发。该组合物的制备工艺简单,适合于大规模生产。
[0036]
根据第三方面,本发明提供一种用于制备零部件的方法,其特征在于,包括将上述组合物进行热压成型。
[0037]
具体地,所述方法包括将上述组合物放置于模具中并热压成型、然后冷却脱模。
[0038]
在一些实施方案中,所述方法还包括制备上述组合物。
[0039]
在一些实施方案中,所述方法还包括制备容纳有致孔剂的聚苯乙烯微胶囊。
[0040]
具体地,在一些实施方案中,所述方法包括:i) 制备容纳有致孔剂的聚苯乙烯微胶囊:将聚苯乙烯微胶囊加入致孔剂中,不断搅拌使聚苯乙烯微胶囊溶胀,从而使致孔剂充满聚苯乙烯微胶囊中;然后将溶胀的聚苯乙烯微胶囊离心、过滤、阴干,得到容纳有致孔剂的聚苯乙烯微胶囊;ii) 制备组合物:将容纳有致孔剂的聚苯乙烯微胶囊、线性低密度聚乙烯和聚苯乙烯树脂均匀混合,得到组合物;iii)热压成型:将组合物放置于模具中并热压成型,得到零部件;和iv) 冷却脱模:将零部件冷却脱模。
[0041]
优选地,在185
‑
205℃的温度和0.5
‑
3mpa的压力下进行热压成型。
[0042]
可以通过空气冷却、水冷却等进行冷却。
[0043]
所述组合物在热压过程中由于聚苯乙烯微胶囊中的致孔剂在挥发过程中会产生小气泡,随着压力增加会在基质中形成不规则蠕虫洞结构,这种不规则虫洞结构可以在受到冲击时很好地吸收冲击带来的能量,使得制备得到的零部件具有良好的冲击吸收性能。
[0044]
根据第三方面,本发明提供一种零部件,其特征在于,其采用上述组合物制备。
[0045]
所述零部件可以例如为汽车前、后保险杠、塑料翼子板、塑料尾门、塑料发舱盖等。
[0046]
在一些实施方案中,所述零部件为选自前、后保险杠、塑料翼子板、塑料尾门和塑料发舱盖的汽车零部件。
[0047]
本技术中所述的“包含”和“包括”涵盖还包含或包括未明确提及的其它要素的情形以及由所提及的要素组成的情形。
[0048]
除非另外限定,本文所使用的所有技术和科学术语具有本发明所属领域技术人员通常理解的相同意义。当本说明书中术语的定义与本发明所属领域技术人员通常理解的意义有矛盾时,以本文中所述的定义为准。
[0049]
除非另有说明,否则在说明书和权利要求书中使用的表达成分的量、温度等的所有数值被理解为在被术语“约”修饰。因此,除非有相反指示,否则在这里阐述的数值参数是
能够根据需要获得的所需性能来变化的近似值。
[0050]
实施例以下将结合实施例和附图对本发明的构思、具体结构及产生的技术效果作进一步说明,以让本领域技术人员充分地了解本发明的目的、特征和效果。本领域技术人员不难理解,此处的实施例仅仅用于示例目的,本发明的范围并不局限于此。
[0051]
部分原料说明:线性低密度聚乙烯:以牌号2645g购自dow公司。
[0052]
聚苯乙烯树脂:以牌号gpps
‑
525购自中信国安公司。
[0053]
实施例1可以按照如下制备聚苯乙烯微胶囊:(1)将溶有引发剂偶氮二异丁腈的苯乙烯、甲基丙烯酸甲酯和熔融的正十六烷混合均匀,得到溶液a;(2)将聚乙烯醇溶解在去离子水中;(3)将溶液a加入到步骤(2)的体系中,通入氮气保护,然后升温至60℃,以1800r /min的转速搅拌乳化30min;(4)将步骤(3)的体系升温至80℃,转速为400r/min连续搅拌聚合4h;反应结束后,用去离子水清洗并减压抽滤,自然干燥得到平均直径为40
‑
60μm之间的聚苯乙烯微胶囊。
[0054]
聚苯乙烯微胶囊制备中各物质以重量份计为:苯乙烯100份、正十六烷100份、甲基丙烯酸甲酯30份、偶氮二异丁腈2份、聚乙烯醇2份、去离子水60份。
[0055]
图1中显示了实施例1中制备的微胶囊的扫描电镜照片。所得聚苯乙烯微胶囊的直径为60μm。
[0056]
将平均直径为60μm的聚苯乙烯微胶囊加入丙酮中,搅拌大约30分钟,使聚苯乙烯微胶囊溶胀,并使丙酮充满聚苯乙烯微胶囊中,得到混合液。
[0057]
将上述混合液在4200rpm下离心、过滤并阴干,得到容纳有丙酮的聚苯乙烯微胶囊。
[0058]
在混合搅拌机中将线性低密度聚乙烯(lldpe)与聚苯乙烯树脂以质量比1:4进行混合,加入容纳有丙酮的聚苯乙烯微胶囊使得容纳有丙酮的聚苯乙烯微胶囊与聚苯乙烯混合物树脂的质量比为1:10,搅拌5min后,得到组合物。
[0059]
将上述组合物放置于热压成型机中,在200℃的温度和2mpa的压力下进行热压成型;开模后将物料冷却,得到零部件。
[0060]
图2为所得零部件截面的扫描电镜图,从图2中可以明显的看出不规则蠕虫洞结构。
[0061]
实施例2参照实施例1中所述制备聚苯乙烯微胶囊,所不同的是在步骤(3)中采用的转速为1200r /min。所得聚苯乙烯微胶囊的直径为40μm。
[0062]
将平均直径为40μm的聚苯乙烯微胶囊加入丙酮中,搅拌大约30分钟,使聚苯乙烯微胶囊溶胀,并使丙酮充满聚苯乙烯微胶囊中,得到混合液。
[0063]
将上述混合液在4200rpm下离心、过滤并阴干,制成容纳有丙酮的聚苯乙烯微胶囊。
[0064]
在混合搅拌机中将线性低密度聚乙烯与聚苯乙烯树脂以质量比1:4进行混合,加入容纳有丙酮的聚苯乙烯微胶囊使得容纳有丙酮的聚苯乙烯微胶囊与聚苯乙烯混合物树脂的质量比为1:10,搅拌5min后,得到组合物。
[0065]
将上述组合物放置于热压成型机中,在200℃的温度和2mpa的压力下进行热压成型;开模后将物料冷却,得到零部件。
[0066]
图3为所得零部件截面的扫描电镜图,从图3中可以明显的看出不规则的蠕虫洞结构。
[0067]
实施例3将平均直径为60μm的聚苯乙烯微胶囊加入丙酮中,搅拌大约30分钟,使聚苯乙烯微胶囊溶胀,并使丙酮充满聚苯乙烯微胶囊中,得到混合液。
[0068]
将上述混合液在4200rpm下离心、过滤并阴干,制成容纳有丙酮的聚苯乙烯微胶囊。
[0069]
在混合搅拌机中将线性低密度聚乙烯与聚苯乙烯树脂以质量比1:4进行混合,加入容纳有丙酮的聚苯乙烯微胶囊使得容纳有丙酮的聚苯乙烯微胶囊与聚苯乙烯混合物树脂的质量比为1:8,搅拌5min后,得到组合物。
[0070]
将上述组合物放置于热压成型机中,在200℃的温度和2mpa的压力下进行热压成型;开模后将物料冷却,得到零部件。
[0071]
对比例1在混合搅拌机中将线性低密度聚乙烯与聚苯乙烯树脂以质量比1:4进行混合,搅拌5min后,得到组合物。
[0072]
将上述组合物放置于热压成型机中,在200℃的温度和2mpa的压力下进行热压成型;开模后将物料冷却,得到零部件。
[0073]
性能表征对实施例1
‑
3和对比例1中所得零部件的密度、0.1mm压缩时的排斥应力和冲击吸收性进行测试。
[0074]
其中0.1mm压缩时的排斥应力按照标准gb/t7757
‑
2009进行测试。
[0075]
冲击吸收性按照如下测试:使用冲击试验装置(摆锤试验机)测定使钢球仅碰撞支撑板时的冲击力(f0)及在将制备的零部件插入到固定夹具和支撑板之间的状态下使钢球碰撞支撑板上时的冲击力(f1),通过式(1)求出冲击吸收性。
[0076]
式(1):冲击吸收性(%)=(f0‑
f1)/f0×
100测试结果汇总于表1中。
[0077]
表1
从图2、图3以及表1可知,聚苯乙烯
‑
线性低密度聚乙烯冲击吸收材料具有明显的不规则蠕虫洞结构,这种结构使得材料本身具有较高的吸收冲击能的效果,这一效果同样可以通过表1中所测得的相应数据得以印证。
[0078]
从表1中可以清楚地看出:通过采用本发明的组合物制备的零部件与对比例1中制备的零部件相比在冲击吸收性方面有显著的提高。
[0079]
以上仅描述了本发明的示例性实施方式或实施例,并不旨在限制本发明。对于本领域技术人员来说,本发明可以由各种更改和变化。凡在本发明的精神和原理之内所作的任何修改、等同替换、改进等,均包含在本技术权利要求范围内。