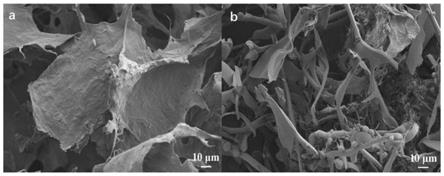
1.本发明属于微/纳米纤维素干燥领域,具体涉及一种改善微/纳米纤维素干燥过程中絮聚的方法。
背景技术:2.微/纳米纤维素是一种从植物纤维中分离的可再生天然高聚物,具有高强度、低密度、高比表面积、高生物相容性等特点,使其在化学性质和物理性质方面均表现出特异性,在新能源、新材料、食品、药品、化妆品、轻工造纸等领域展现出巨大的潜在应用价值。微/纳米纤维素表面有较多的水分子结合位点,易于在水体系中与水分子形成氢键结合,使微/纳米纤维素呈现出凝胶特性,从而导致目前微/纳米纤维素的制备浓度普遍偏低,一般为0.1~3.0wt%,极大的增加了微/纳米纤维素的运输和存储成本,探索合适的微纳米纤维素干燥技术,减少微/纳米纤维素在干燥过程中结构和性能的变化,改善微/纳米纤维素凝胶的团聚,对微纳米纤维素工业化生产和应用具有重要意义。
3.目前改善微/纳米纤维素凝胶团聚的方法,主要是对微/纳米纤维素进行接枝改性,如酯化、乙酰化、甲硅烷基化、聚合物接枝等方法,在微/纳米纤维素上接枝疏水基团,提高微/纳米纤维素的疏水性能,进而改善其絮聚或者团聚。这类方法改变了微纳米纤维素的天然化学结构,限制了微纳米纤维素在部分领域应用,且增加其成本。
技术实现要素:4.为了克服现有技术的不足,本发明的目的在于提供一种改善微/纳米纤维素干燥过程中絮聚的方法。该方法基于微/纳米纤维素较大的比表面积,易于与水分子形成氢键结合的特点,利用大分子木质素磺酸盐大分子屏蔽微/纳米纤维素表面的部分氢键,减少微/纳米纤维素在干燥过程中纤维内部和纤维之间相互结合而导致的絮聚,从而保证干燥后微/纳米纤维素的特性和性能得以保持。
5.本发明的目的通过以下技术方案实现。
6.一种改善微/纳米纤维素干燥过程中絮聚的方法,包括以下步骤:
7.将木质素磺酸盐加入微/纳米纤维素悬浮液中,混合均匀,得混合悬浮液;再冷冻所述混合悬浮液,然后干燥。
8.优选的,所述木质素磺酸盐的添加量相对于绝干微/纳米纤维素的0.5~25.0wt%。
9.优选的,所述木质素磺酸盐的添加量相对于绝干微/纳米纤维素的0.5~10.0wt%。
10.优选的,所述微/纳米纤维素悬浮液的浓度为0.2~3.0wt%。
11.优选的,所述冷冻的温度为-195℃~-20℃,冷冻时间为10~20h,低温可以实现混合悬浮液的快速冷冻,减少悬浮液中粒子的移动。
12.优选的,所述微/纳米纤维素悬浮液是将木质纤维素原料通过机械研磨或者酶预
处理/机械研磨工艺制备得到;所述机械研磨是采用纳米均质机、超微粒粉碎机、纳米微射流均质机中的至少一种研磨至稳定的悬浮凝胶液状态;所述酶预处理为纤维素酶预处理、内切纤维素酶预处理和木聚糖酶预处理中的一种或多种。
13.优选的,所述超微粒粉碎机机械研磨时,研磨浓度为0.2~3.0wt%,研磨10~30次,优选的1.0~2.0wt%,研磨20~30次。
14.优选的,所述内切纤维素酶预处理工艺为3.0~9.0mg/g基质,45~55℃,处理1~3h,溶液ph为4.8~7.0。
15.优选的,所述木质素磺酸盐添加入微/纳米纤维素悬浮液后,采用高速机械搅拌的方式至体系均匀,搅拌速率为5000~10000r/min。
16.优选的,所述干燥后再将微/纳米纤维素分散,获得较稳定的微/纳米纤维素悬浮液。
17.优选的,所述干燥后再将微/纳米纤维素进行机械再分散,分散后微/纳米纤维素的浓度为0.2~2.0wt%,分散方法采用高速乳化机、纳米均质机、超微粒粉碎机和纳米微射流均质机中的一种或多种。
18.优选的,所述干燥后的微/纳米纤维素悬浮液再分散的高速乳化机转速10000~12000r/min,分散时间3~10min。
19.优选的,所述干燥后的微/纳米纤维素悬浮液再分散的超微粒粉碎机的研磨次数5~10次。
20.由以上任一项所述的方法干燥后的微/纳米纤维素。
21.与现有技术相比,本发明具有如下的有益效果:
22.(1)本发明所获得干燥后的微/纳米纤维素絮聚程度较低,保持良好的微纳米纤维形貌,获得稳定的干燥再分散微/纳米纤维素悬浮液。
23.(2)本发明充分利用了微/纳米纤维素与木质素磺酸盐在氢键或者范德华力作用下相互结合的机理,在冷冻干燥前添加木质素磺酸盐,屏蔽微/纳米纤维素表面的部分亲水性羟基,使微/纳米纤维素内部或者纤丝相互之间氢键结合减少,有效减少了微/纳米纤维素在干燥过程中的相互团聚和絮聚,该技术可极大的降低低浓度微/纳米纤维素的存储和制备成本。
附图说明
24.图1为对比例1和实施例3的微/纳米纤维素干燥后的sem图;其中,a为未添加木质素磺酸盐(对比例1),b为添加10.0wt%木质素磺酸盐(实施例3)。
具体实施方式
25.以下结合实例对本发明的具体实施作进一步的具体说明,但本发明的实施方式不限于此。
26.本发明对所用木质纤维素原料的种类、来源并没有特殊的限制,下面以漂白化学热磨机械浆为例。
27.实施例1
28.将漂白化学热磨机械浆充分疏解后进行内切纤维素酶预处理和超微粒粉碎机机
械处理。内切纤维素酶用量为3mg/g基质,50℃,ph=7.0,处理2h。超微粒粉碎机机械处理采用超微粒粉碎机,浓度1.0wt%,研磨20次得到微/纳米纤维素悬浮液,悬浮液的透光率为54.5%,微/纳米纤维素的比表面积为173.0g/m2。向制得的微/纳米纤维素悬浮液中添加0.5wt%(相对于绝干微/纳米纤维素)的木质素磺酸盐,机械搅拌混合均匀。在-75℃下,冷冻混合悬浮液18h,然后置于冷冻干燥机中至微/纳米纤维素干燥。将干燥后的微/纳米悬浮液稀释至0.2wt%,高速乳化机10000转速下搅拌5min,可获得在400nm可见光照射下透光率达到17.1%的稳定微/纳米纤维素悬浮液,微/纳米纤维素的比表面积为158.0
±
1.3g/m2,说明了木素磺酸盐的加入有效的改善了微/纳米纤维素干燥过程中的团聚,保持了微/纳米纤维素的形态结构。
29.实施例2
30.将漂白化学热磨机械浆充分疏解后进行内切纤维素酶预处理和超微粒粉碎机机械处理。内切纤维素酶用量为9mg/g基质,50℃,ph=4.8,处理1h。超微粒粉碎机机械处理采用超微粒粉碎机,浓度1.0wt%,研磨10次得到微/纳米纤维素悬浮液,悬浮液的透光率为57.5%,微/纳米纤维素的比表面积为183.0g/m2。向制得的微/纳米纤维素悬浮液中添加5.0wt%(相对于绝干微/纳米纤维素)的木质素磺酸盐,机械搅拌混合均匀。在-20℃下,冷冻混合悬浮液15h,然后置于冷冻干燥机中至微/纳米纤维素干燥。将干燥后的微/纳米悬浮液稀释至1.0wt%,高速乳化机10000转速下搅拌5min,可获得在400nm可见光照射下透光率达到24.0%的稳定微/纳米纤维素悬浮液,微/纳米纤维素的比表面积为172.0g/m2,说明了木素磺酸盐的加入有效的改善了微/纳米纤维素干燥过程中的团聚,保持了微/纳米纤维素的形态结构。
31.实施例3
32.将漂白化学热磨机械浆充分疏解后进行内切纤维素酶预处理和超微粒粉碎机机械处理。内切纤维素酶用量为6mg/g基质,50℃,ph=4.8,处理3h。超微粒粉碎机机械处理采用超微粒粉碎机,浓度1.0wt%,研磨15次得到微/纳米纤维素悬浮液,悬浮液的透光率为58.5%,微/纳米纤维素的比表面积为186.0g/m2。向制得的微/纳米纤维素悬浮液中添加10.0wt%(相对于绝干微/纳米纤维素)的木质素磺酸盐,机械搅拌混合均匀。在-195℃下,冷冻混合悬浮液10h,然后置于冷冻干燥机中至微/纳米纤维素干燥。干燥后的微/纳米纤维素保持了较好的微纳米级别形态结构,如图1中的b。将干燥后的微/纳米悬浮液稀释至2.0wt%,高速乳化机10000转速下搅拌10min,可获得在400nm可见光照射下透光率达到25.0%的稳定微/纳米纤维素悬浮液,微/纳米纤维素的比表面积为164.5g/m2,说明了木素磺酸盐的加入有效的改善了微/纳米纤维素干燥过程中的团聚,保持了微/纳米纤维素的形态结构。
33.实施例4
34.将漂白化学热磨机械浆充分疏解后进行内切纤维素酶预处理和超微粒粉碎机机械处理。内切纤维素酶用量为9mg/g基质,50℃,ph=7.0,处理1h。超微粒粉碎机机械处理采用超微粒粉碎机,浓度1.0wt%,研磨30次得到微/纳米纤维素悬浮液,悬浮液的透光率为59.0%,微/纳米纤维素的比表面积为181.0g/m2。向制得的微/纳米纤维素悬浮液中添加25.0wt%(相对于绝干微/纳米纤维素)的木质素磺酸盐,机械搅拌混合均匀。在-75℃下,冷冻混合悬浮液20h,然后置于冷冻干燥机中至微/纳米纤维素干燥。将干燥后的微/纳米悬浮
液稀释至1.0wt%,超微粒粉碎机研磨10次。可获得在400nm可见光照射下透光率达到19.2%的稳定微/纳米纤维素悬浮液,微/纳米纤维素的比表面积为165.0g/m2,说明了木素磺酸盐的加入有效的改善了微/纳米纤维素干燥过程中的团聚,保持了微/纳米纤维素的形态结构。
35.对比例1
36.将漂白化学热磨机械浆充分疏解后进行内切纤维素酶预处理和超微粒粉碎机机械处理。内切纤维素酶用量为3mg/g基质,50℃,ph=7.0,处理2h。超微粒粉碎机机械处理采用超微粒粉碎机,浓度1.0wt%,研磨20次得到微/纳米纤维素悬浮液,悬浮液的透光率为54.5%,微/纳米纤维素的比表面积为173.0g/m2。向制得的微/纳米纤维素悬浮液中添加0%(相对于绝干微/纳米纤维素)的木质素磺酸盐,机械搅拌混合均匀。在-75℃下,冷冻混合悬浮液18h,然后置于冷冻干燥机中至微/纳米纤维素干燥。干燥后的微/纳米纤维素具有一定的相互团聚,形成了片状结构,如图1中的a。将干燥后的微/纳米悬浮液稀释至0.2wt%,高速乳化机10000转速下搅拌5min,可获得在400nm可见光照射下透光率为11.2%的稳定微/纳米纤维素悬浮液,微/纳米纤维素的比表面积为144.0g/m2,说明了干燥过程中微/纳米纤维素之间具有较多的团聚,微/纳米纤维素未能保持原有的微纳米结构,比表面积下降明显。
37.对比例2
38.将漂白化学热磨机械浆充分疏解后进行内切纤维素酶预处理和超微粒粉碎机机械处理。内切纤维素酶用量为9mg/g基质,50℃,ph=7.0,处理1h。超微粒粉碎机机械处理采用超微粒粉碎机,浓度1.0wt%,研磨30次得到微/纳米纤维素悬浮液,悬浮液的透光率为59.0%,微/纳米纤维素的比表面积为181.0g/m2。向制得的微/纳米纤维素悬浮液中添加26.0wt%(相对于绝干微/纳米纤维素)的木质素磺酸盐,机械搅拌混合均匀。在-75℃下,冷冻混合悬浮液20h,然后置于冷冻干燥机中至微/纳米纤维素干燥。将干燥后的微/纳米悬浮液稀释至1.0wt%,超微粒粉碎机研磨10次,可获得在400nm可见光照射下透光率为12.9%的稳定微/纳米纤维素悬浮液,微/纳米纤维素的比表面积为155.0g/m2,说明了过量的木素磺酸盐影响了再分散的微/纳米纤维素悬浮液的透光率,打破了微/纳米纤维素原有体系的平衡,不利于微/纳米纤维素保持原有的形态结构。
39.上述实施例为本发明较佳的实施方式,但本发明的实施方式并不受所述实施例的限制,其他的任何未背离本发明的精神实质与原理下所做的改变、修饰、替代、组合、简化,均应为等效的置换方式,都包含在本发明的保护范围之内。