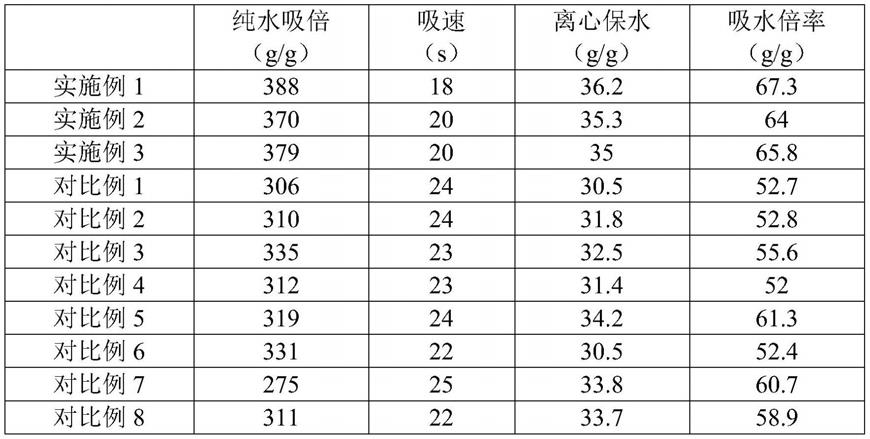
1.本发明属于高吸水性树脂领域,具体涉及一种反相悬浮工艺制备高纯水吸倍的高吸水性树脂。
背景技术:2.高吸水性树脂(sap)是一种适度交联具备三维网状结构的高分子化合物,能够吸收自身百倍甚至千倍的水。由于其强大的吸水及加压下保持水份的能力被广泛应用于纸尿裤、卫生巾、宠物垫以及电缆用阻水材料以及农林保水剂。
3.应用在纸尿裤复合芯体下层和宠物垫方向的高吸水性树脂因需在一定时间内快速吸收大量水分对纯水吸倍性能有更高要求。为了提升纯水吸倍性能不同生产工艺进行了技术升级,如增大吸水树脂颗粒比表面积、增加吸水树脂中和度、对吸水树脂进行改性等。而如何突破树脂颗粒结构限制得到更加优异的纯水吸倍性能成为其中关键。
4.江苏斯尔邦石化(cn111499914a)采用uv辅助氧化还原引发低温聚合制得高分子吸水凝胶,然后将吸水凝胶进行多次造粒制得凝胶颗粒,再进行干燥和表面交联处理得到所需的高吸水性树脂颗粒。上述发明中制得吸水树脂颗粒为不规则片状或块状,比表面积小吸水速率慢,同时采用低温聚合工艺能耗大成本高。
5.住友精化(cn103739744a)采用二步或多步间歇反相悬浮聚合工艺,在石油烃中加入水相不饱和单体溶液构建反相悬浮体系,在一步反相聚合结束后进行降温使得分散剂析出,再加入二步不饱和单体水溶液进行团聚和二步悬浮聚合,再进行脱水和石油烃脱除处理,最后经干燥得到所需制备的高吸水性树脂。这种反相悬浮生产工艺得到吸水树脂颗粒为球状凝聚体,受球体几何形状限制比表面积无法进一步提升,纯水吸收性能存在瓶颈。
6.日本触媒(cn1934170a)采用水溶液或反相悬浮聚合工艺,再经后中和、控制交联密度的方法制备一种耐尿劣化的吸水树脂,特点之处在于吸水树脂耐劣化同时具备较佳的吸水性能。这种工艺所述细颗粒再生和团粒为简单物理混合,将细颗粒与水(或含微量助剂)混合后依靠表面张力和氢键粘附在一起,结构为细颗粒与细颗粒的结团,细颗粒经此方法处理后再次挤压造粒吸水性能大大降低,同时细颗粒间简单物理粘结经后处理搅拌和管线运输非常容易造成二次破损,循环产生细粉。
7.日本触媒(cn112119114a)通过干燥和细粉造粒两个工序,干燥工序将含水凝胶干燥至颗粒,本发明关键主要在细粉造粒工艺,生产线中研磨产生细粉经过细粉造粒设备与造粒助剂(含交联剂)混合后制得胶粒,然后再将细粉胶粒与正常造粒胶粒混合达到回收细粉得目的。该发明所述的细粉造粒回收工艺非常成熟,目前万华sap工业化装置正在使用的就是该工艺,同时日触、卫星等也是该工艺。该细粉回收工艺缺点较多:细粉经造粒后性能损失较大,保水、吸倍性能很差,影响产品性能;细粉造粒后进入研磨系统会再次产生细粉,在系统循环导致细粉量大;细粉造粒后胶粒因粒子比正常造粒胶粒小,易造成干燥不均或过干燥。
8.陶氏化学(us5342899)提出一种细粉回收工艺,该工艺将细粉颗粒加入不饱和单
体水溶液中,细粉粉体与反应液溶胀后加入助剂然后混合并进行聚合反应。该工艺特点在于细粉与反应液先混合,使得聚合胶体与细粉颗粒充分结为一体,降低细粉对产品影响,同时减少细粉二次产生。但该发明对细粉性能没有提升,相反经过两次造粒挤压和干燥后对最终产品性能有负面影响同时该细粉颗粒与反应液混合溶胀过程混合均匀程度要求高,如出现局部粉体浓度高会导致产品性能损失。该发明制备的高吸水性树脂与常规树脂结构上完全相同,没有形成特殊的吸水树脂结构,同时吸水树脂结构和性能没有提升。
9.纳尔科化学(us4950692)提供了一种吸水树脂细粉单独生产吸速树脂颗粒的工艺,该工艺不进行回掺,单独将细粉通过造粒、干燥、研磨再制得吸水树脂颗粒。该发明无实际应用意义,因为细粉性能远低于正常树脂颗粒,简单造粒和干燥得到产品性能低下市场无法接受,不如将细粉回收至产品中具备实际应用意义。
10.us5264495将吸水树脂细粉与不饱和单体溶液溶液混合后进行聚合反应,所述操作在捏合机内进行,同时该发明制备高吸水性树脂性能专注于抗盐性提升。该发明制备的吸水树脂结构与常规吸水树脂差异,性能具备较佳的抗盐性能,在吸水性能发明无明显提升。
11.现有高吸水性树脂颗粒形貌有不规则片状或块状、凝聚球体状和单个珠滴状,受本身结构限制,比表面积无法进一步提升情况下吸水树脂纯水吸倍性能存在瓶颈。同时,生产过程中产生细粉如何高效回收并且不影响产品性能一直是业界难题。
技术实现要素:12.本发明涉及一种高吸水型树脂及其制备方法。所述高吸水树脂具有特定形貌,主颗粒外围粘附若干细粒径颗粒,具备更大的比表面积和吸水触点,吸纯水性能更加优异,并且使用生产过程中产生细粉成品,产生经济效益。
13.为实现上述发明目的,本发明采用以下技术方案:
14.一种高吸水性树脂,所述高吸水性树脂颗粒形貌为主颗粒外围粘附细粒径颗粒,所述主颗粒粒径为200-550微米,所述细颗粒粒径为30-140微米,主颗粒与细粒径颗粒质量比为5-12。
15.本发明的技术方案采用反相悬浮工艺制备吸水树脂主颗粒,再将被不饱和单体溶液溶胀的细粉加入悬浮溶液中进行分散及聚合反应,使细粉聚合于主颗粒表面,提升高吸水性树脂比表面积,制得具备高纯水吸倍的特定形貌的高吸水性树脂。
16.主颗粒粒径如果太小吸水倍率偏低,如主颗粒粒径过大吸速偏慢,无法满足应用性能要求。细颗粒粒径如果粒径太小起到增加纯水吸倍功能太弱不足以达到目的,如细颗粒粒径过大则负面影响整体吸水倍率,无法满足应用性能要求。
17.一种制备本发明所述高吸水树脂的方法,包括以下步骤:
18.(1)反相悬浮体系构建:使用溶有不饱和单体、内交联剂、引发剂的水溶液与溶有分散剂的石油烃构建以石油烃为连续相,以不饱和单体、内交联剂、引发剂水溶液为悬浮相的反相悬浮体系;
19.(2)细颗粒溶胀:取细粒径吸水树脂颗粒成品加入溶有内交联剂、引发剂的不饱和单体水溶液中进行溶胀;
20.(3)分散及聚合:对反相悬浮体系升温开始聚合,水相悬浮颗粒聚合4-10min后将
步骤(2)所得溶胀后细颗粒加入反相悬浮体系中,在搅拌和分散剂作用下细颗粒分散在主颗粒液滴表面,控温至反应温度进行聚合反应;
21.(4)后处理及干燥:对聚合后的颗粒脱除一定量的水,然后向悬浮液中添加表面交联剂进行聚合颗粒的表面交联处理,再蒸馏脱除石油烃并干燥处理,得到主颗粒外表面粘附细颗粒的高吸水性树脂。
22.本发明所述不饱和单体为水溶性乙烯基不饱和单体,合适的例子包括但不限于丙烯酸、甲基丙烯酸、丙烯酰胺、甲基丙烯酰胺、丙烯腈、醋酸乙烯酯的一种或多种。
23.本发明所述内交联剂为丙二醇、丙三醇、季戊四醇、三羟甲基丙烷、乙二醇二缩水甘油醚、甘油二缩水甘油基醚、三烯丙胺酯、聚乙二醇双丙烯酸酯和季戊四醇三烯丙基醚中的一种或多种。
24.本发明所述引发剂为过硫酸钠、过硫酸钾、过硫酸铵、叔丁基过氧化氢、二叔丁基过氧化物和过氧化氢中的一种或多种。
25.本发明所述分散剂为蔗糖脂肪酸酯、三聚甘油单硬脂酸酯、十八烷基单磷酸酯和脱水山梨糖醇脂肪酸酯中的一种或多种。
26.本发明所述所述石油烃为环戊烷、环己烷、正庚烷、正己烷、正辛烷、2-甲基己烷和苯、甲苯、二甲苯中的一种或多种。
27.作为一个优选的方案,本发明所述细粒径吸水树脂颗粒成品为反相悬浮工艺制备高吸水性树脂过程中经筛分得到的成品细粉,粒径范围30-140微米。
28.本发明所述步骤(2)中,细粒径吸水树脂颗粒成品与用于溶胀的不饱和单体水溶液中的不饱和单体的质量比为2-4.8:1。
29.本发明所述表面交联剂为乙二醇二缩水甘油醚、甘油二缩水甘油醚、聚丙三醇、聚乙二醇二缩水甘油醚、甘油、丙二醇、乙二醇、1,4-丁二醇、二乙醇胺、三乙醇胺中的一种或多种。
30.优选地,本发明所述步骤(1)中,用于制备主颗粒的所述水溶液中内交联剂用量为不饱和单体质量的0.06%-0.7%。
31.优选地,本发明所述步骤(2)中,用于溶胀细粒径吸水树脂颗粒成品的不饱和单体水溶液中的内交联剂用量为不饱和单体质量的0.02-0.25%。
32.优选地,本发明所述步骤(1)中,引发剂的用量为不饱和单体质量的0.02%-0.55%。
33.优选地,本发明所述步骤(1)中,所述反相悬浮体系中分散剂用量为不饱和单体质量的0.3%-2%。
34.优选地,本发明所述步骤(2)中,引发剂的用量为不饱和单体质量的0.02%-0.55%。
35.优选地,所述表面交联剂用量为不饱和单体(制备方法中所用不饱和单体总量)质量的0.08%-0.4%。
36.所述制备方法为不饱和单体溶液溶胀细颗粒成品后与主颗粒不饱和单体溶液在反相悬浮体系中聚合,细颗粒粘附于吸水树脂主颗粒表面。
37.本发明所述步骤(1)中,制备主颗粒的水溶液中不饱和单体的质量浓度为25%-34%,优选地,不饱和单体使用碱,例如氢氧化钠或者氢氧化钾中和至70-85mol%中和度。
38.本发明所述步骤(2)中,溶胀细颗粒的不饱和单体水溶液中的不饱和单体的质量浓度为18%-30%,优选地,不饱和单体使用碱,例如氢氧化钠或者氢氧化钾中和至70-85mol%中和度。
39.本发明所述步骤(3)中,分散操作时搅拌转速非常重要,优选为400-800rpm,转速过低时细颗粒粒径无法均匀分布至主颗粒表面,转速过快时剪切过大产生凝胶沉降。
40.本发明所述步骤(3)中,聚合温度为78-92℃,主颗粒反应时间为4-10min,使得主颗粒部分聚合颗粒强度适中,如反应时间过短水相悬浮液滴还未充分聚合形成高分子结构,主颗粒强度不够,加入的细颗粒将会溶胀进入主颗粒内部无法得到目标结构;如主颗粒反应时间过长,主颗粒聚合充分强度过高,细颗粒无法在主颗粒表面溶胀,细颗粒不能稳定粘附在主颗粒表面。
41.本发明所述步骤(4)中,脱水温度为110-135℃,表面交联温度为70-95℃,干燥温度为120-180℃。
42.本发明的积极效果在于:
43.(1)通过反相悬浮工艺制备特定形貌的吸水树脂颗粒,其形貌为主颗粒外围粘附若干细粒径颗粒,具备更大的比表面积和吸水触点,将吸水树脂应用性能显著提升,较现有工艺具备更加优异吸收性能,纯水吸倍量提升10%以上。
44.(2)本发明使用生产过程中产生细粉,将细粉经不饱和单体溶液溶胀后进行反相悬浮聚合回用到吸水树脂颗粒中,高效回收细粉并且不影响产品性能,产品经济价值。
附图说明
45.图1为实施例1制备的吸水树脂颗粒形貌图片。
具体实施方式
46.以下通过具体实施例对本发明方法做进一步说明,但本发明不限于所列出的实施例,还应包括在本发明的权利要求范围内其他任何公知的改变。
47.主要原料信息如下:
48.丙烯酸:万华化学集团股份有限公司,工业品;
49.32%wt浓度氢氧化钠溶液:万华化学集团股份有限公司,工业品;
50.正庚烷:山东伟明化工有限公司,工业品;
51.蔗糖脂肪酸酯:三菱化学(上海)有限公司,牌号s-370;
52.成品细粉:反相悬浮工艺制备高吸水性树脂过程中经筛分得当的成品细粉颗粒。
53.分析仪器:pixact-200在线粒径成像测试仪;
54.主要表征方法如下:
55.(1)、纯水吸倍(g/g)
56.向盛有250ml纯水的烧杯中,加入0.5g(精确至0.01g)烘干的高吸水性树脂样品,并开始用秒表计时,1min时,将该烧杯内的高吸水性树脂样品和水搅拌均匀并立即导入滤袋中,稍微将自由水滴净后,称量滤袋的重量m2,将高吸水性树脂样品从滤袋中取出称量滤袋的重量m1,高吸水性树脂样品的1min纯水吸收量(g/g)=(m2-m1)/0.5,此数值反映了吸水树脂在单位时间内的纯水吸收量,数值越高说明单位时间吸水能力越大。
57.(2)、吸水倍率(g/g)
58.称量0.200
±
0.005g样品,装入茶袋中,用热封口机封口,将装有样品的茶袋及空白茶袋放入装有1000ml生理盐水的塑料容器中,开始计时30分钟后,将装有样品的茶袋及空白茶袋取出,悬挂滴水10分钟后称量,记重量分别为w2和w1。吸液倍率(g/g)=(w2-w1)/0.2。此数值反映了吸水树脂自由状态下吸收液体的能力,数值越高说明吸液能力越大。
59.(3)、离心保水(g/g)
60.将上述称重后装有样品的茶袋及空白茶袋放入离心机中,250g下离心脱水3分钟,脱水结束后,对装有样品的茶袋及空白茶袋分别称重,记重量为w4和w3。保水量(g/g)=(w4-w3)/0.2。此数值反映了吸水树脂在离心力作用下吸收液体的能力,数值越高说明保持水分能力越大。
61.(4)、吸速(s)
62.将50ml生理盐水倒入玻璃烧杯中,然后放入转子调节磁力搅拌器的搅拌速度至600rpm,称量2.0g sap样品加入溶液中,样品放入溶液中立即用秒表开始计时,观察到溶液表面的漩涡消失时,停止计时,记录下所用时间。此数值反映了吸水树脂吸收液体的快慢,数值越低说明吸液速率越快。
63.实施例1
64.准备1台装有搅拌器、回流冷凝器、温度计的1l四口圆底烧瓶,将其置于可控温水浴中,向其中加入正庚烷320g并升温至60℃,然后再加入蔗糖脂肪酸酯0.28g,搅拌一定时间使其均匀溶解分散,然后降温至45℃备用。
65.室温搅拌下,将104.2g32%naoh水溶液加入到123g丙烯酸单体的水溶液中(其中含丙烯酸75g),通过水浴移除中和热将温度降至35℃,然后向其中加入0.03g过硫酸钠、0.06g乙二醇二缩水甘油醚,得到制备主颗粒用丙烯酸单体水溶液。
66.室温搅拌下,将4.69g32%naoh水溶液加入到12.19g丙烯酸单体的水溶液中(其中含丙烯酸3.38g),通过水浴移除中和热将温度降至35℃,然后向其中加入0.0017g过硫酸钠、0.002g乙二醇二缩水甘油醚,充分搅拌至混合均匀,得到溶胀用不饱和单体水溶液。
67.取13.8g中值粒径为130微米的细粉,将其加入到不饱和单体水溶液中并使用玻璃棒快速搅拌,使得不饱和单体水溶液将细粉颗粒均匀溶胀。
68.将配制好的制备主颗粒用丙烯酸单体水溶液加入到上述1l四口圆底烧瓶中,开启搅拌使水相溶液分散于油相连续相中形成均匀分布的悬浮珠滴颗粒,然后将悬浮体系升温至80℃反应5min,然后在持续搅拌下加入溶胀后细粉颗粒,控制搅拌转速600rpm,继续维持反应温度80℃反应20min。反应结束后,继续升温度至110℃进行共沸脱水,共脱除101g水。控制悬浮溶液温度80℃,加入表面交联剂1,4-丁二醇0.078g,然后脱除体系中正庚烷,再将脱除溶剂后的颗粒放入130℃干燥机中进行干燥处理50min,最终得到要制备的主颗粒外围粘附若干细粒径颗粒的高吸水性树脂。
69.实施例2
70.准备1台装有搅拌器、回流冷凝器、温度计的1l四口圆底烧瓶,将其置于可控温水浴中,向其中加入正庚烷320g并升温至60℃,然后再加入蔗糖脂肪酸酯0.61g,搅拌一定时间使其均匀溶解分散,然后降温至45℃备用。
71.室温搅拌下,将95.05g32%naoh水溶液加入到162.9g丙烯酸单体的水溶液中(其
中含丙烯酸75g),通过水浴移除中和热将温度降至35℃,然后向其中加入0.1875g过硫酸钾、0.465g乙二醇二缩水甘油醚,得到制备主颗粒用丙烯酸单体水溶液。
72.室温搅拌下,将2.22g32%naoh水溶液加入到3.81g丙烯酸单体的水溶液中(其中含丙烯酸1.75g),通过水浴移除中和热将温度降至35℃,然后向其中加入0.0044g过硫酸钾、0.0042g乙二醇二缩水甘油醚,充分搅拌至混合均匀,得到溶胀用不饱和单体水溶液。
73.取6.2g中值粒径为80微米的成品细粉,将其加入到不饱和单体水溶液中并使用玻璃棒快速搅拌,使得不饱和单体水溶液将细粉颗粒均匀溶胀。
74.将配制好的制备主颗粒用丙烯酸单体水溶液加入到上述1l四口圆底烧瓶中,开启搅拌使水相溶液分散于油相连续相中形成均匀分布的悬浮珠滴颗粒,然后将悬浮体系升温至85℃反应8min,然后在持续搅拌下加入溶胀后细粉颗粒,控制搅拌转速440rpm,继续维持反应温度85℃反应20min。反应结束后,继续升温度至115℃进行共沸脱水,共脱除129.6g水。控制悬浮溶液温度75℃,加入表面交联剂乙二醇二缩水甘油醚0.17g,然后脱除体系中正庚烷,再将脱除溶剂后的颗粒放入120℃干燥机中进行干燥处理50min,最终得到要制备的主颗粒外围粘附若干细粒径颗粒的高吸水性树脂。
75.实施例3
76.准备1台装有搅拌器、回流冷凝器、温度计的1l四口圆底烧瓶,将其置于可控温水浴中,向其中加入正庚烷320g并升温至60℃,然后再加入蔗糖脂肪酸酯1.4g,搅拌一定时间使其均匀溶解分散,然后降温至45℃备用。
77.室温搅拌下,将108g32%naoh水溶液加入到133.1g丙烯酸单体的水溶液中(其中含丙烯酸75g),通过水浴移除中和热将温度降至35℃,然后向其中加入0.375g过硫酸钠、0.225g季戊四醇三烯丙基醚,得到制备主颗粒用丙烯酸单体水溶液。
78.室温搅拌下,将4.27g32%naoh水溶液加入到5.92g丙烯酸单体的水溶液中(其中含丙烯酸2.96g),通过水浴移除中和热将温度降至35℃,然后向其中加入0.015g过硫酸钠、0.003g季戊四醇三烯丙基醚,充分搅拌至混合均匀,得到溶胀用不饱和单体水溶液。
79.取6.3g中值粒径为40微米的成品细粉,将其加入到不饱和单体水溶液中并使用玻璃棒快速搅拌,使得不饱和单体水溶液将细粉颗粒均匀溶胀。
80.将配制好的制备主颗粒用丙烯酸单体水溶液加入到上述1l四口圆底烧瓶中,开启搅拌使水相溶液分散于油相连续相中形成均匀分布的悬浮珠滴颗粒,然后将悬浮体系升温至90℃反应10min,然后在持续搅拌下加入溶胀后细粉颗粒,控制搅拌转速750rpm,继续维持反应温度90℃反应20min。反应结束后,继续升温度至130℃进行共沸脱水,共脱除111.8g水。控制悬浮溶液温度90℃,加入表面交联剂1,4-丁二醇0.3g,然后脱除体系中正庚烷,再将脱除溶剂后的颗粒放入170℃干燥机中进行干燥处理35min,最终得到要制备的主颗粒外围粘附若干细粒径颗粒的高吸水性树脂。
81.对比例1
82.准备1台装有搅拌器、回流冷凝器、温度计的1l四口圆底烧瓶,将其置于可控温水浴中,向其中加入正庚烷320g并升温至60℃,然后再加入蔗糖脂肪酸酯0.6g,搅拌一定时间使其均匀溶解分散,然后降温至45℃备用。
83.室温搅拌下,将104.2g32%naoh水溶液加入到145g丙烯酸单体的水溶液中(其中含丙烯酸75g),通过水浴移除中和热将温度降至35℃,然后向其中加入0.15g过硫酸钠、
0.38g乙二醇二缩水甘油醚,得到制备主颗粒用丙烯酸单体水溶液。
84.将上述丙烯酸单体水溶液加入到1l四口圆底烧瓶中,开启搅拌使水相溶液分散于油相连续相中形成均匀分布的悬浮珠滴颗粒,然后将悬浮体系升温至80℃反应20min。反应结束后,继续升温度至120℃进行共沸脱水,共脱除119.7g水。
85.控制悬浮溶液温度80℃,加入表面交联剂1,4-丁二醇0.15g,然后脱除体系中正庚烷,再将脱除溶剂后的颗粒放入130℃干燥机中进行干燥处理50min,最终得到单个珠滴形貌的高吸水性树脂。
86.对比例2
87.此对比例与实施例1的区别在于:细粉未使用丙烯酸单体水溶液溶胀。
88.对比例3
89.此对比例与实施例1的区别在于:主颗粒聚合时间为2min。
90.对比例4
91.此对比例与实施例1的区别在于:主颗粒聚合时间为15min。
92.对比例5
93.此对比例与实施例1的区别在于:细粉分散搅拌转速为250rpm。
94.对比例6
95.此对比例与实施例1的区别在于:细粉分散搅拌转速为1000rpm。
96.对比例7
97.向5l反应槽中加入605g丙烯酸、750g 32wt%浓度的氢氧化钠溶液、460g水,并加入0.83g季戊四醇三烯丙基醚,得到聚合单体组合物。
98.向前述聚合单体组合物中加入中值粒径为120微米的细粉80g,充分搅拌混合均匀,控制中和液温度为80℃,向反应液加入2.4g过硫酸钠,然后将中和液倒入反应槽中。反应槽放入80℃烘箱中,反应5min后得到聚合物水凝胶,经过造粒机造粒,凝胶颗粒尺寸在2-15mm之间。
99.在170℃烘箱中干燥45min,依次经过研磨、筛分后,得到丙烯酸吸水树脂粉末,粒径在150-710μm之间。取400g初级丙烯酸吸水树脂粉末,向表面均匀喷洒0.9g乙二醇二缩水甘油醚,最后放入130℃的烘箱内干燥45min,得到丙烯酸吸水树脂产品。
100.对比例8
101.准备1台装有搅拌器、回流冷凝器、温度计的1l四口圆底烧瓶,将其置于可控温水浴中,向其中加入正庚烷320g并升温至60℃,然后再加入蔗糖脂肪酸酯0.27g,搅拌一定时间使其均匀溶解分散,然后降温至45℃备用。
102.室温搅拌下,将104.2g32%naoh水溶液加入到123g丙烯酸单体的水溶液中(其中含丙烯酸75g),通过水浴移除中和热将温度降至35℃,然后向其中加入0.042g过硫酸钠、0.06g乙二醇二缩水甘油醚,得到制备主颗粒用丙烯酸单体水溶液。
103.将配制好的制备主颗粒用丙烯酸单体水溶液加入到上述1l四口圆底烧瓶中,开启搅拌使水相溶液分散于油相连续相中形成均匀分布的悬浮珠滴颗粒,然后将悬浮体系升温至80℃反应15min。反应结束后,继续升温度至110℃进行共沸脱水,共脱除101g水。控制悬浮溶液温度80℃,取13.8g中值粒径为130微米的成品细粉,取表面交联剂1,4-丁二醇0.075g,同时将细粉和表面交联剂加入悬浮溶液中进行表面交联。然后脱除体系中正庚烷,
再将脱除溶剂后的颗粒放入130℃干燥机中进行干燥处理50min,最终得到要制备的主颗粒外围环绕若干细粒径颗粒的高吸水性树脂。
104.对比例8中,细粉是聚合后表面处理时加入,细粉依附在主颗粒上,与本发明技术方案中的聚合时加入发生溶胀结合不同,该对比例依附未溶胀,吸速和纯水吸倍均不及实施例。
105.上述实施例和对比例得到的高吸水性树脂各性能如下表1所示:
106.表1实施例和对比例性能参数
[0107][0108]
从表中可以看出来,本发明制备的主颗粒表面粘附细颗粒的特定形貌的吸水性树脂具备更高的纯水吸水倍率、更快的吸收速度,具备更加优异的吸水性能。可见将细粉成品颗粒被不饱和单体溶液溶胀后聚合于吸水树脂颗粒表面的工艺可显著增大最终吸水树脂颗粒的比表面积,增多吸水触点,有利于吸水过程中单位时间内吸收更多的水。
[0109]
本发明制备的高吸水性树脂在其他主要性能如离心保水和吸水倍率表现上倍率达到对比例水平。
[0110]
同时本发明使用生产过程中产生细粉,将细粉经不饱和单体溶液溶胀后进行反相悬浮聚合回用到吸水树脂颗粒中,高效回收细粉并且不影响产品性能,产品经济价值。
[0111]
本领域技术人员可以理解,在本说明书的教导之下,可对本发明做出一些修改或调整。这些修改或调整也应当在本发明权利要求所限定的范围之内。