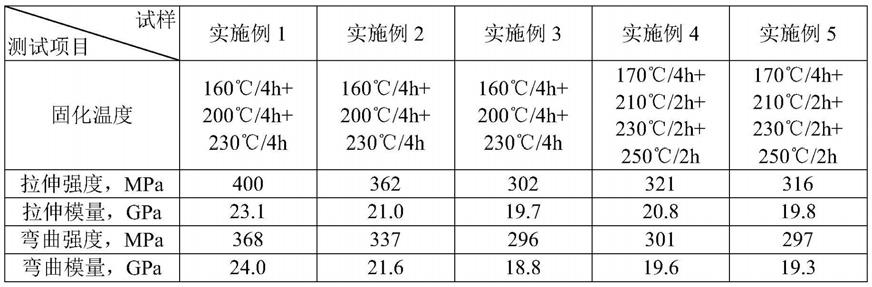
1.本发明属于酚醛树脂改性技术领域,涉及一种高韧性、低固化温度的石墨烯改性酚醛树脂及其制备方法和在制备复合材料中的应用。
背景技术:2.酚醛树脂因具有耐热、耐烧蚀、介电常数低、工艺性良好等优点而被广泛应用于航空航天等尖端国防领域。价格较低的优势使得酚醛树脂同样可以应用于汽车制造、建筑、通讯等民用领域。
3.酚醛树脂通常分为线型酚醛和体型酚醛。通常情况下,苯酚与甲醛的摩尔为0.8∶1,在酸性条件下得到线性酚醛,线性酚醛具有热塑性;苯酚与甲醛的摩尔比为1.3∶1,在碱性条件下得到体型酚醛,体型酚醛具有热固性。
4.酚醛树脂中含有大量易被氧化的羟基,且在固化过程中树脂体积收缩率大,交联度的增加使得生成的树脂脆性大。收缩率高、小分子副产物多,容易造成复合材料内部出现空洞或脱黏等问题。而且,酚醛树脂固化温度较高,对设备及生产状况有严格要求。这些缺点,严重制约了酚醛树脂在高端领域的应用。
5.随着航空航天等高端领域的迅速发展,对树脂材料的要求越来越高,酚醛树脂的脆性极大地限制了其在高端领域的广泛应用,因此,需要通过一定的方法来改善酚醛树脂的综合性能。
技术实现要素:6.本发明针对酚醛树脂脆性大,力学性能差,固化工艺温度高等问题。首先,使用文献报道的hummer法制备氧化石墨烯,再通过还原的方法将氧化石墨烯还原成石墨烯粉末。其次,通过溶液共混的方法将石墨烯溶液均匀地分散到酚醛树脂中,除去有机溶剂后,得到改性酚醛树脂。最后,利用所述改性酚醛树脂通过树脂传递模塑(rtm)工艺制备得到复合材料。由本发明方法制得石墨烯改性酚醛树脂复合材料的弯曲性能比未改性材料弯曲强度提高20%以上,固化温度有显著的降低。
7.本发明针对酚醛树脂脆性大,力学性能差,固化工艺温度高等问题。首先,使用文献报道的hummer法制备氧化石墨烯,再通过还原的方法将氧化石墨烯还原成石墨烯粉末。其次,通过溶液共混的方法将石墨烯溶液均匀地分散到酚醛树脂中,除去有机溶剂后,得到改性酚醛树脂。最后,利用所述改性酚醛树脂通过树脂传递模塑(rtm)工艺制备得到复合材料。由本发明方法制得石墨烯改性酚醛树脂复合材料的弯曲性能比未改性材料弯曲强度提高20%以上,固化温度有显著的降低。
8.于是,本发明在第一方面提供给了一种石墨烯改性酚醛树脂的制备方法,所述方法包括如下步骤:
9.(1)将石墨烯加入到丁醇中并混合均匀,制得石墨烯溶液;
10.(2)将酚醛树脂熔化,得到熔化酚醛树脂;
11.(3)向所述石墨烯溶液中加入所述熔化酚醛树脂并混合均匀,得到复合溶液;
12.(4)将所述复合溶液升温并超声分散,得到分散液;
13.(5)将所述分散液加热以在去除溶剂的同时完成改性反应,得到改性酚醛树脂。
14.本发明在第二方面提供了根据本发明第一方面所述的方法制得的石墨烯改性酚醛树脂。
15.本发明在第三方面提供给了一种制备石墨烯改性酚醛树脂复合材料的方法,其中利用本发明第二方面所述的改性酚醛树脂浸渍纤维预制体并固化,制得所述石墨烯改性酚醛树脂复合材料。
16.本发明在第四方面提供了根据本发明第三方面所述的方法制得的石墨烯改性酚醛树脂复合材料。
17.相对于现有技术,本发明具有如下技术优势:
18.(1)本发明制得的石墨烯改性酚醛树脂能够降低了整体固化温度(各个固化工序的温度均有明显降低)。本发明采用的改性后酚醛树脂由于引入了石墨烯尤其是本发明方法制得的石墨烯粉末,增加了酚醛树脂的活性,降低了固化温度。这在一定程度上节约能源,降低对设备、模具、密封条等的耐高温性的依赖。
19.(2)本发明制备复合材料的方法简化了固化步骤。在预固化工序中,由于石墨烯的加入,虽然固化时间,但是简化了固化步骤,提高了工艺可操作性。
20.(3)本发明方法制得的复合材料具有优异的力学性能,拉伸强度、拉伸模量、弯曲强度和弯曲模量得到全面提升,尤其是拉伸强度、弯曲强度和弯曲模量,提升均达到20%以上。
具体实施方式
21.为使本发明实施例的目的、技术方案和优点更加清楚,下面将结合本发明具体实施方式,对本发明实施例中的技术方案进行清楚、完整地描述,显然,所描述的实施方式是本发明的一部分实施方式,而不是全部的实施方式。基于本发明中的实施实施方式,本领域普通技术人员在没有做出创造性劳动的前提下所获得的所有其他实施方式,都属于本发明保护的范围。
22.如上所述,本发明在第一方面提供给了一种石墨烯改性酚醛树脂的制备方法,所述方法包括如下步骤:
23.(1)将石墨烯加入到丁醇中并混合均匀,制得石墨烯溶液;
24.(2)将酚醛树脂熔化,得到熔化酚醛树脂;
25.(3)向所述石墨烯溶液中加入所述熔化酚醛树脂并混合均匀,得到复合溶液;
26.(4)将所述复合溶液升温并超声分散,得到分散液;
27.(5)将所述分散液加热以在去除溶剂的同时完成改性反应,得到改性酚醛树脂。
28.本发明对所采用酚醛树脂没有特别限制,可以为线型酚醛,也可以为体型酚醛。优选的是,所述酚醛树脂是分子量为500至8000的线型酚醛。
29.在一些优选的实施方式中,所述石墨烯为石墨烯粉末,并且通过包括如下步骤的方法制备:
30.(a)将石墨烯、过磷酸钾和五氧化二磷加入到第一浓硫酸中并混合均匀,然后冷却至室温,再洗涤至中性并干燥;
31.(b)将干燥后的产物加入第二浓硫酸中并混合均匀,再加入高锰酸钾并继续混合均匀,将混合物在30℃至35℃(该温度例如为35℃,例如可以在油浴中)保持1.5小时至2.5小时(例如为2小时);
32.(c)向其中加入900ml至950ml(例如为920ml)的水(例如去离子水),静置10至20分钟(例如为15分钟)后,再加入2.5至3.0l(例如2.8l)的0.4质量%至0.6质量%(例如0.5质量%)的双氧水水溶液,然后抽滤,使用8质量%至12质量%(例如为10质量%)的稀硫酸洗涤并干燥,得到所述氧化石墨烯;
33.(d)利用所述氧化石墨烯制备0.2质量%至0.3质量%(例如0.25质量%)的氧化石墨烯水溶液,然后进行超声处理,得到石墨烯胶体溶液;
34.(e)将所述石墨烯胶体溶液加热至75℃至85℃(例如80℃)的温度,然后加入硼氢化钠还原,将所得到的沉淀洗涤、抽滤并干燥,得到所述石墨烯粉末。
35.本发明采用的第一浓硫酸和第二浓硫酸可以为具有通常意义的浓硫酸(cas7664
‑
93
‑
9),并且可以不同,也可以相同,例如浓度均为70质量%。
36.本发明方法采用丁醇例如正丁醇作为溶剂,发现其同时还起到分散剂的作用,不仅具有合适的熔沸点,而且还使得石墨烯均匀分散。采用其他如dmso等高沸点的溶剂或者采用乙醇或丙酮等低沸点的溶剂,无法兼具分散性好和沸点适中的特点。
37.在本发明中,所采用的溶剂丁醇具有合适的沸点,使得可以在80℃至110℃(例如90或100℃)的分散温度实现分散。如果温度过低,酚醛树脂流动性较差,不利于分散;如果分散温度过高,则酚醛树脂有固化风险。于是,在另一些优选的实施方式中,在步骤(1)中,将石墨烯加入到80℃至110℃(例如90或100℃)的丁醇中。
38.在另一些优选的实施方式中,在步骤(2)中,将酚醛树脂预热至90℃至110℃(例如100℃)至完全熔化;
39.在另一些优选的实施方式中,在步骤(4)中,将所述复合溶液的温度升高至125至135℃(例如130℃)并超声分散50分钟至70分钟(例如60分钟),得到分散液;
40.在另一些优选的实施方式中,在步骤(5)中,通过如下方式去除溶剂并实现改性反应:将所述分散液在100℃至120℃的温度保持5小时至7小时(例如6小时),然后再在85至95℃(例如90℃)保持3至5小时(例如4小时),得到改性酚醛树脂。
41.本发明在第二方面提供了根据本发明第一方面所述的方法制得的改性酚醛树脂。
42.本发明在第三方面提供给了一种制备石墨烯改性酚醛树脂复合材料的方法,其中利用本发明第二方面所述的改性酚醛树脂浸渍纤维预制体并固化,制得所述石墨烯改性酚醛树脂复合材料。
43.本发明对纤维预制体没有特别的限制。但是,在一些实施方式中,纤维预制体的纤维体积分数可以30%至80%(例如为40、50、60或70),优选为50%至70%。
44.在另一些优选的实施方式中,所述浸渍和固化通过树脂传递模塑来进行。
45.在另一些优选的实施方式中,所述方法包括如下步骤:
46.(i)根据目标产品的形状和尺寸,提供具有相应型腔的用于树脂传递模塑的模具;
47.(ii)在所述模具中铺放所述纤维预制体并合模;
48.(iii)通过向所述模具中注入本发明第二方面所述的改性酚醛树脂来实施注胶,得到浸渍纤维预制体;
49.(iv)对所述模具中的所述浸渍纤维预制体进行固化,制得所述石墨烯改性酚醛树脂复合材料。
50.在一些实施方式中,优选的是,在步骤(i)之前,可以先对纤维预制体进行脱胶处理。例如,可以将纤维预制体例如玻璃纤维布置于丙酮溶剂中加热至50℃浸泡3小时至5小时(例如4小时),捞出后放置真空烘箱干燥,烘干12h至24h(例如18小时)后取出备用。
51.在另一些优选的实施方式中,在步骤(iii)中,所述注胶在120℃至140℃(例如130℃)的注胶温度和0.04mpa至0.06mpa(例如0.05mpa)的注胶压力下进行。
52.在另一些优选的实施方式中,在步骤(iv)中,在150℃至230℃的温度固化,优选在150℃至220℃的温度进行固化。
53.在另一些优选的实施方式中,所述固化采用包括如下工序的固化工艺进行:(i)固化前熔融工序:在130℃至160℃(例如140或150)的温度保温3.5小时至4.5小时(例如4小时);(ii)预固化工序:在190℃至210℃(例如200℃)保温3.5小时至4.5小时(例如4小时);(iii)二次固化工序:在220℃至230℃(例如225℃)保温3.5小时至4.5小时(例如4小时)。
54.在一个更优选的实施方式中,所述固化采用包括如下工序的固化工艺进行:(i)固化前熔融工序:在160℃的温度保温4小时;(ii)预固化工序:在200℃保温4小时;(iii)在230℃保温4小时。
55.在现有技术中,酚醛气凝胶的固化工艺通常包括如下工序:固化前熔融工序、预固化工序、一次固化工序和二次固化工序。其中,固化前熔融工序需要在170℃保温4小时,其目的是为使得酚醛树脂加热熔融,增加流动性,便于在压力作用下从注胶罐中流入平板模具。预固化工序需要在210℃保温2小时,目的是使酚醛树脂实现预固化。一次固化工序需要在230℃保温2小时,其目的是使大部分酚醛树脂实现固化。二次固化工序在250℃保温2小时,属于后固化处理温度,以便于所有位置的酚醛树脂能够完全固化。其中,预固化工序和一次固化工序为酚醛树脂固化的主要过程。但是,如果温度直接230℃进行固化,固化速度过快,会有爆聚风险。如果都在210℃固化,则固化时间非常长的时间。
56.本发明方法的固化前熔融工序与现有技术中使用改性前的酚醛树脂的固化前熔融工序对应,所不同的是,改性后酚醛树脂的熔融温度降低,在130至160℃树脂已经完全熔融,可以实现顺利注胶。本发明方法的预固化工序实现了酚醛树脂改性前所采用的预固化工序和一次固化工序的效果,所不同的是,该工序所采用的温度固化时间适宜,且没有固化不完全和爆聚风险,不仅降低了固化温度,而且还便于操作。本发明方法的二次固化工序的功能与酚醛树脂改性前所采用的二次固化工序相同,所不同的是,可以采用低达20℃的温度进行,明显降低了固化温度。
57.本发明对石墨烯改性酚醛树脂复合材料的形状和尺寸没有特别的限制,可以根据需要进行调整。在所述石墨烯改性酚醛树脂复合材料为平板构件的情况下,该平板例如可以具有如下尺寸:长度为40cm至60cm(例如为50cm),宽度为20cm至30cm(例如为25cm),厚度为2mm至5mm(例如为3mm)。
58.本发明在第四方面提供了根据本发明第三方面所述的方法制得的石墨烯改性酚醛树脂复合材料。
59.下文将以实施例的形式对本发明进行进一步的说明,但是这些实施例仅出于举例目的,本发明的保护范围不限于这些实施例。
60.制备例:制备石墨烯改性酚醛树脂。
61.制备例1
62.1.石墨烯的制备
63.1.1氧化石墨烯的制备
64.采取改进的hummer法制备氧化石墨烯:将20g天然石墨粉、10g过硫酸钾和10g五氧化二磷加入80℃的浓h2so4(浓度为70质量%)中,搅拌均匀,冷却6h以上,洗涤至中性,干燥。将干燥后的产物加入0℃、230ml浓h2so4(浓度为70质量%)中并混合均匀,再加入60g高锰酸钾并继续混合均匀。将混合物升至20℃,然后放入35℃的油浴中保持2小时后,加入920ml的去离子水。静置15分钟后,再加入2.8l的去离子水(其中含有50ml,浓度为30质量%的双氧水),之后混合物颜色变为亮黄,趁热抽滤,再用5l浓度为10质量%的稀硫酸洗涤3次,干燥后得到氧化石墨烯。
65.1.2石墨烯粉末的制备
66.将0.5g以上制得的氧化石墨烯放入烧杯中,加入200ml去离子水并使氧化石墨烯混合均匀,得到棕黄色石墨烯胶体溶液。将获得的石墨烯胶体溶液放入500ml三口烧瓶中,水浴加热至80℃,加入5g硼氢化钠并混合均匀进行还原反应2小时,最后得到黑色絮状沉淀,经洗涤、抽滤、干燥得到石墨烯粉末。
67.2.溶液共混法制备石墨烯改性酚醛树脂
68.称取步骤二得到的石墨烯5g,酚醛树脂200g(线型酚醛,分子量为500至8000)。将5g石墨烯加入100ml的80℃的正丁醇溶液中并搅拌至完全分散,得到石墨烯溶液。再将酚醛树脂预热至100℃至完全融化,得到熔化酚醛树脂。将熔化酚醛树脂加入到石墨烯溶液中,得到石墨烯/酚醛树脂复合溶液。最后,再将复合溶液升高温度至130℃并搅拌均匀,得到分散液。将得到的分散液置在110℃的环境中保温6小时,使溶剂挥发,然后置于在90℃的真空烘箱(真空度为
‑
0.1mpa)中保持4小时以进一步去除溶剂,从而在去除溶剂的同时完成改性反应,得到改性酚醛树脂。
69.制备例2
70.采用与制备例1基本相同的方式进行,不同之处在于,采用等体积的乙酸(沸点为118℃)代替所述正丁醇。
71.制备例3
72.采用与制备例1基本相同的方式进行,不同之处在于,采用等体积的二甲基亚砜(dmso,沸点189℃)代替所述正丁醇。
73.实施例:制备石墨烯改性酚醛树脂复合材料
74.在如下实施例中,利用制备例中制得的改性酚醛树脂制备石墨烯改性酚醛树脂复合材料,该复合材料的制备以纤维体积分数为53%的玻璃纤维布作为纤维预制体,以长度为55cm,宽度为22cm,厚度为3mm的平板构件作为所要制备的复合材料,通过举例方式进行说明,但是纤维预制体不限于上述纤维布,并且复合材料也不限于上述平板构件。
75.实施例1
76.1.玻璃纤维布的预处理
77.将玻璃纤维布置于丙酮溶剂中加热至50℃浸泡3小时,捞出后放置真空烘箱干燥,烘干12小时后取出备用。
78.2.rtm工艺制备复合材料平板
79.根据所要制备的复合材料(平板构件)的形状和尺寸,制备具有与该复合材料的用于rtm工艺的模具(即rtm模具),在模具内铺放步骤三预处理后的玻璃纤维布,合模,锁模。模具与用于实施rtm工艺的注胶步骤的注胶罐连接并一同放入烘箱中,烘箱温度调至130℃,然后抽真空至rtm模具内部压力为0.05mpa,利用注胶罐将制备例1制得的石墨烯改性酚醛树脂注入模具中,边注边抽真空。待出胶口有胶液流出,关闭阀门,去除注胶罐和模具的连接,将装有经浸渍的纤维预制体的rtm模具置于烘箱中,完成加热固化后脱模处理,得到目标复合材料,其中,采用160℃/4h+200℃/4h+230℃/4h的固化工艺。具体地说,固化工艺包括固化前熔融工序、预固化工序和全固化工序,其中,固化前熔融工序为在160℃的温度保温4小时;预固化工序为在200℃保温4小时;全固化工序为在230℃保温4小时。
80.3.性能测试
81.测试所制得的复合材料在室温下的拉伸强度、拉伸模量、弯曲强度、弯曲模量,结果参见表1。
82.实施例2
83.采用与实施例1基本相同的方式进行,不同之处在于,采用制备例2制得的石墨烯改性酚醛树脂代替实施例1中使用的制备例1制得的石墨烯改性酚醛树脂。
84.实施例3
85.采用与实施例1基本相同的方式进行,不同之处在于,采用制备例3制得的石墨烯改性酚醛树脂代替实施例1中使用的制备例1制得的石墨烯改性酚醛树脂。
86.实施例4
87.采用与实施例1基本相同的方式进行,不同之处在于,采用制备例1所采用的改性前的酚醛树脂(线型酚醛,分子量为500至8000),并采用如下固化工艺:170℃/4h+210℃/2h+230℃/2h+250℃/2h。即,依次进行如下工序:(1)固化前熔融工序:在170℃保温4小时;(2)预固化工序:在210℃保温2小时;(3)一次固化工序:在230℃保温2小时;(4)二次固化工序:在250℃保温2小时。
88.实施例5
89.采用与实施例4基本相同的方式进行,不同之处在于,采用制备例3所制得的改性酚醛树脂代替改性前的酚醛树脂。
90.表1.各实施例制得的复合材料的性能。
91.92.注:各个测试项目的数据为室温条件下的数据。
93.从表中的数据可以看出,实施例获得了比实施例2至4显著优异的性能。具体地说,对比实施例和实施例4的结果可以看出,石墨烯改性酚醛树脂具有较低的固化温度,能够简化固化工艺,获得更好的力学性能。
94.实施例2采用了制备例2制得的石墨烯改性酚醛树脂,其中采用乙酸作为溶剂,但是获得了显著不如实施例1的效果。结果显示,正丁醇尽管与乙酸具有基本相同的沸点,但是在本发明的技术方案,却显示出显著较好的效果,推测可能是因为乙酸作为溶剂时,石墨烯即使在超声处理后,其分散性也不好,酚醛树脂混合后不能更有效分散开,从而在固化时候部分区域固化完全,而部分区域固化不完全。
95.实施例3采用制备例3制得的的石墨烯改性酚醛树脂,其中采用dmso作为溶剂,但是获得了显著不如实施例1的效果。试验发现,在去除溶剂过程中,温度升高至dmso熔点,则酚醛树脂开始凝胶固化,而温度在酚醛凝胶温度以下,一时间难以有效脱出溶剂,从而造成制备的产品有溶剂产生的气泡,
96.最后应说明的是:以上实施例仅用以说明本发明的技术方案,而非对其限制;尽管参照前述实施例对本发明进行了详细的说明,本领域的普通技术人员应当理解:其依然可以对前述各实施例所记载的技术方案进行修改,或者对其中部分技术特征进行等同替换;而这些修改或者替换,并不使相应技术方案的本质脱离本发明各实施例技术方案的精神和范围。