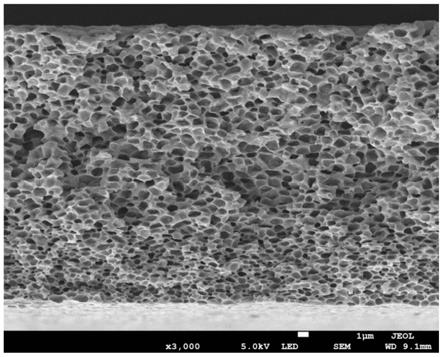
1.本发明属于高分子材料领域,涉及一种多孔膜及其制备方法。具体而言,涉及一种长碳链聚酰胺多孔膜及其制备方法。
背景技术:2.多孔膜是一类重要的多孔材料,广泛应用于分离、纯化、隔膜等多个领域。聚酰胺是一种综合性能优异的高分子材料,在工程塑料、纤维、薄膜等领域应用广泛。在薄膜领域,聚酰胺6及其与其他高分子经过挤出、流延、双拉、吹塑等技术制备的双向拉伸薄膜、吹塑薄膜、复合薄膜,在食品包装、等领域应用。多孔膜也已在实验室、工业、生活的过滤处理中得到了广泛应用。由于聚酰胺含有极性的酰胺基团,容易与环境中的水分以氢键结合,导致此类材料具有一定的吸水率。酰胺基团密度越高,材料的吸水性越高。吸水后聚酰胺的机械性能和尺寸稳定性发生变化,很大程度地限制了其使用寿命及在某些特定领域的应用。
[0003]“长碳链聚酰胺”是指相邻酰胺基团之间亚甲基数量大于10的聚酰胺品种,较长的亚甲基链和极性酰胺基团使其兼具聚烯烃和聚酰胺的双重特性。长碳链聚酰胺中柔性的亚甲基链和较低密度的酰胺基团使其具有韧性良好、吸水率低、尺寸稳定性好、耐低温冲击和介电性能优良等独特优势,在汽车、电子电器、航空航天、输油、输醇、输气等领域有重要应用,是国内外特种工程塑料材料的重要研究与开发领域。
[0004]
目前制备聚合物多孔膜最常用的方法为“非溶剂诱导相分离法(non-solvent induce phase separation,nips)”。其主要的工艺流程是将聚合物溶于溶剂中形成均相溶液,再浸入与溶剂互溶的非溶剂(即凝固浴)中,形成以聚合物为连续相、溶剂为分散相的两相结构。进行干燥后,即可得到具有多孔结构的材料。
[0005]
现有技术中,大多利用nips原理制备多孔膜,例如:
[0006]
申请号为cn201810619027.7的中国专利公开了一种基于嵌段共聚物非溶剂诱导相分离制备多孔膜的方法(南京工业大学);申请号为cn201510403751.2的中国专利公开了一种高强度高通量芳香聚酰胺多孔膜的制备方法(河南工程学院);申请号为cn202010000567.4的中国专利公开了一种热塑性聚氨酯多孔膜的制备方法(中山大学);申请号为cn202110723971.9的中国专利公开了一种通过非溶剂致相分离法制备多孔间位芳纶隔膜的方法(中海油天津化工研究设计院有限公司);申请号为cn201310297902.1的中国专利公开了一种中空纤维膜制备方法、中空纤维膜及潜溶剂组合物(博天环境规划设计研究院(北京)有限公司,北京中环膜材料科技有限公司,博天环境集团股份有限公司)。
[0007]
以上专利的多孔膜都是利用“非溶剂诱导相分离”方法制备,其最为关键的步骤是利用非溶剂的“凝固浴”实现湿膜的相反转,从而形成膜材料的多孔结构。然而利用“非溶剂诱导相分离”方法制备多孔膜,需要凝固浴的相关设备及制剂,方法较为复杂,产生的废液多,不节能,不环保。
[0008]
因此,倘若能够提供一种简单易行,环保高效的多孔膜的制备方法,则具有重要的意义。
[0009]
有鉴于此特提出本发明。
技术实现要素:[0010]
本发明要解决的技术问题在于克服现有技术的不足,提供一种长碳链聚酰胺多孔膜及其制备方法,该方法无需凝固浴,步骤简单,易于操作,简单高效,绿色环保,制备得到的长碳链聚酰胺多孔膜的孔洞分布均匀、孔隙率高。
[0011]
为解决上述技术问题,本发明采用技术方案的基本构思是:
[0012]
本发明的第一目的是提供一种长碳链聚酰胺多孔膜的制备方法,包括:
[0013]
(1)将长碳链聚酰胺与极性溶剂混合,溶胀;然后加入非极性溶剂,搅拌溶解,得到长碳链聚酰胺溶液;
[0014]
(2)将所述长碳链聚酰胺溶液进行脱泡、刮膜或涂膜,得到湿膜;
[0015]
(3)将所述湿膜在一定的温度下进行溶剂挥发和干燥,得到长碳链聚酰胺多孔膜。
[0016]
长碳链聚酰胺具有吸水率低、韧性好等特点,其多孔膜在过滤、分离、隔膜等领域有着应用价值。本发明针对长碳链聚酰胺,提出了一种不同于“非溶剂诱导相分离”的方法,可以简易、高效地制备长碳链聚酰胺的多孔膜。本发明的方法通过混合溶剂(极性溶剂和非极性溶剂)将长碳链聚酰胺进行溶解,利用溶剂挥发速度差异调控长碳链聚酰胺从溶剂中析出时发生液固之间的“旋节线解离相分离(spinodal decomposition)”,待溶剂全部挥发之后即可得到具有均匀孔洞的膜材料。本发明方法与传统“非溶剂诱导相分离”法的最大区别是,无需使用凝固浴,具有简单易行、绿色环保的优点。
[0017]
本发明中,先将长碳链聚酰胺加入极性溶剂中充分搅拌,保证长碳链聚酰胺充分溶胀。之后加入非极性溶剂充分搅拌至溶液澄清透明,得到配置好的聚合物溶液,从而使长碳链聚酰胺充分、均匀的溶解在混合溶剂中。其中长碳链聚酰胺可以是一种或几种的共混物,极性溶剂可以是一种或几种混合,非极性溶剂也可以是一种或几种混合。将聚酰胺溶液脱泡处理,然后在干燥、洁净的固态平面基质上,通过刮涂或者旋涂得到湿膜。之后,将湿膜放入烘箱,通过温度控制溶剂挥发速率,得到长碳链聚酰胺的多孔膜。该过程步骤简单,易于操作和控制,可以快速高效地制备长碳链聚酰胺多孔膜。
[0018]
进一步的方案,步骤(1)中,所述长碳链聚酰胺溶液中,长碳链聚酰胺的质量分数为0.5wt%-50wt%。
[0019]
优选的,所述长碳链聚酰胺溶液中,长碳链聚酰胺的质量分数为0.5wt%-50wt%。
[0020]
进一步的方案,步骤(1)中,所述极性溶剂和非极性溶剂的质量比为1:9-9:1。
[0021]
本发明经过试验发现,制备的长碳链聚酰胺溶液中,当长碳链聚酰胺的质量分数在0.5wt%-50wt%范围,极性溶剂和非极性溶剂的质量比在1:9-9:1的范围时,制备的长碳链聚酰胺多孔膜的孔洞分布均匀、孔隙率高。
[0022]
进一步的方案,步骤(1)中,所述的长碳链聚酰胺为主链重复单元中至少包含一段亚甲基数量等于或大于10的长碳链的聚酰胺;
[0023]
优选的,所述的长碳链聚酰胺选自pa610、pa612、pa11、pa1012、pa12、pa1212、pa1214中的至少一种;
[0024]
更优选的,所述的长碳链聚酰胺选自pa1012、pa11、pa12、pa1212。
[0025]
进一步的方案,所述的长碳链聚酰胺为纯长碳链聚酰胺、含助剂和填料添加剂的
长碳链聚酰胺、聚酰胺合金中的一种或几种。所述助剂和填料添加剂可以为现有技术中可添加的任何种类。聚酰胺合金可以为现有技术中可添加的任何种类。
[0026]
进一步的方案,所述的长碳链聚酰胺熔点为180℃-230℃,熔融指数为0.5-20g/10min,优选的,熔融指数为1-10g/10min。
[0027]
进一步的方案,所用长碳链聚酰胺的数均分子量为10,000-100,000kg/mol,优选为20,000-60,000kg/mol。
[0028]
进一步的方案,步骤(1)中,所述的极性溶剂选自甲醇、乙醇、异丙醇、丙三醇、n,n-二甲基甲酰胺、二甲基亚砜、丙酮、盐酸、硫酸、硝酸、甲酸、乙酸、三氟乙酸、乙腈、四氢呋喃、二氧六环、乙酸乙酯中的至少一种。
[0029]
进一步的方案,步骤(1)中,所述的非极性溶剂选自石油醚、正己烷、环己烷、甲苯、苯、二氯甲烷、氯仿、四氯化碳、1,2-二氯乙烷、乙腈、三氯乙烷、正己烷、二苯醚、正丁醚、异丙醚、乙醚中的至少一种。
[0030]
进一步的方案,步骤(2)中,通过刮涂工艺得到湿膜,所述刮涂的速度为1mm/s-1000mm/s;
[0031]
或者,通过旋涂工艺得到湿膜,甩膜速度为100转/分钟-2000转/分钟。
[0032]
进一步的方案,步骤(2)中,所述的湿膜是在平整的玻璃、石英、硅片、金属表面中的一种上制备得到的。
[0033]
进一步的方案,步骤(2)中,湿膜的厚度根据长碳链聚酰胺溶液的浓度和制膜工艺决定,薄膜厚度在0.1μm-2000μm之间。
[0034]
进一步的方案,步骤(3)中,湿膜进行溶剂挥发和干燥的温度控制在20℃-150℃。
[0035]
本发明中,将步骤(2)制备的湿膜放入烘箱,通过温度控制溶剂挥发速率,得到长碳链聚酰胺的多孔膜。经试验发现,温度控制在20℃-150℃时,能够形成孔洞分布均匀的长碳链聚酰胺的多孔膜,低于或者超出该温度,则效果下降。
[0036]
作为一种优选的方案,湿膜进行溶剂挥发和干燥采用温度依次升高的梯度升温方式。本发明的干燥方式采用梯度升温,在各梯度温度维持一段时间。前一梯度的温度小于后一梯度的温度,使干燥温度逐渐提升,从而利用溶剂挥发速度差异调控长碳链聚酰胺从溶剂中析出时发生液固之间的“旋节线解离相分离(spinodal decomposition)”,待溶剂全部挥发之后即可得到具有均匀孔洞的膜材料。
[0037]
作为一种具体的优选的实施方式,梯度升温方式的条件为:在40-90℃下加热30-60分钟,然后升高温度至70-150℃,加热30-150分钟。
[0038]
进一步的方案,步骤(1)中还加入抗老剂和/或增强增韧的高分子加工助剂;
[0039]
优选的,所述抗老剂选自受阻酚类抗氧剂、芳香胺类抗氧剂、亚磷酸酯类抗氧剂、硫代酯类抗氧剂、铜盐类抗氧剂中的至少一种;
[0040]
优选的,所述增强增韧的高分子加工助剂选自纳米二氧化硅、炭黑、碳纳米管、纳米碳酸钙、硅酸钙晶须、二氧化钛粉体中的至少一种。
[0041]
本发明的第二目的是提供一种由上述任意所述的制备方法制备的长碳链聚酰胺多孔膜;
[0042]
优选的,所述长碳链聚酰胺多孔膜孔洞分布均匀,孔径为0.02~30μm。
[0043]
采用上述技术方案后,本发明与现有技术相比具有以下有益效果。
[0044]
1、本发明基于“旋节线解离相分离(spinodal decomposition)”原理,利用长碳链聚酰胺在不同比例混合溶剂中溶解性的差异,实现了多孔膜的快速制备。相较于传统的“非溶剂诱导相分离(non-solvent induce phase separation,nips)”成孔,本方法无需使用凝固浴,溶剂易回收,具有节能环保等优点。本发明提供的长碳链聚酰胺多孔膜的制备方法简单、易于操作,有利于提高生产效率。另外,本发明方法中使用的溶剂可以通过适合的冷凝装置进行回收,重复利用,进一步降低制造成本。
[0045]
2、本发明探索得到了合理的长碳链聚酰胺、极性溶剂、非极性溶剂的配比,配合控制适宜的薄膜干燥温度,制备得到的长碳链聚酰胺多孔膜的孔洞分布均匀、孔隙率高。通过本发明方法制备的长碳链聚酰胺多孔膜在分离、电池隔膜等领域具有广阔的应用前景。
[0046]
下面结合附图对本发明的具体实施方式作进一步详细的描述。
附图说明
[0047]
附图作为本发明的一部分,用来提供对本发明的进一步的理解,本发明的示意性实施例及其说明用于解释本发明,但不构成对本发明的不当限定。显然,下面描述中的附图仅仅是一些实施例,对于本领域普通技术人员来说,在不付出创造性劳动的前提下,还可以根据这些附图获得其他附图。在附图中:
[0048]
图1为本发明实施例1提供的扫描电子显微镜照片;
[0049]
图2为本发明实施例2提供的扫描电子显微镜照片;
[0050]
图3为本发明对比例1的扫描电子显微镜照片。
[0051]
需要说明的是,这些附图和文字描述并不旨在以任何方式限制本发明的构思范围,而是通过参考特定实施例为本领域技术人员说明本发明的概念。
具体实施方式
[0052]
为使本发明实施例的目的、技术方案和优点更加清楚,下面将结合本发明实施例中的附图,对实施例中的技术方案进行清楚、完整地描述,以下实施例用于说明本发明,但不用来限制本发明的范围。
[0053]
实施例1
[0054]
(1)将聚酰胺1012放入烘箱中干燥,烘干温度为100℃,时间为12小时。
[0055]
(2)将上述聚酰胺1012与四氢呋喃混合,于磁力搅拌器中充分溶胀,聚酰胺1012与四氢呋喃的比例为15:50,搅拌时间为2小时。
[0056]
(3)向上述溶液中加入适量甲苯,在搅拌下充分溶解,其中聚酰胺1012、四氢呋喃、甲苯的比例为15:50:50,溶解时间为12小时。
[0057]
(4)将得到的聚酰胺溶液静置脱泡,然后用刮刀在玻璃板上进行刮涂,得到湿膜。刮刀的狭缝尺寸为200mm,刮膜速度为30mm/s。
[0058]
(5)将湿膜放入烘箱中,在70℃下加热30分钟,然后升高温度至110℃,加热60分钟,使溶剂完全挥发,即得到聚酰胺1012的多孔膜。该多孔膜断面的扫描电子显微镜的结果见图1。
[0059]
从图1中可以看出,在聚酰胺膜的整个厚度范围内,微孔均匀分布,孔径约为1μm。
[0060]
实施例2
[0061]
(1)将聚酰胺1012放入烘箱中干燥,烘干温度为100℃,时间为12小时。
[0062]
(2)将上述聚酰胺1012与二甲基亚砜混合,于磁力搅拌器中充分溶胀,聚酰胺1012与二甲基亚砜的比例为15:60,搅拌时间为2小时。
[0063]
(3)向溶胀好的上述溶液中加入乙腈和三氯乙烷的混合溶剂,在搅拌下充分溶解,其中聚酰胺1012、二甲基亚砜、乙腈/三氯乙烷的比例为15:60:40,溶解时间为12小时。
[0064]
(4)将得到的聚酰胺溶液静置脱泡,然后用刮刀在玻璃板上进行刮涂,得到湿膜。刮刀的狭缝尺寸为200mm,刮膜速度为30mm/s。
[0065]
(5)将湿膜放入烘箱中,在60℃下加热30分钟,然后升高温度至120℃,加热60分钟,使溶剂完全挥发,即得到聚酰胺1012的多孔膜。该多孔膜断面的扫描电子显微镜的结果见图2。
[0066]
从图2中可以看出,在聚酰胺膜的整个厚度范围内,微孔均匀分布,孔径约为1μm。
[0067]
实施例3-14
[0068]
与实施例1相同的操作步骤,具体的工艺参数见表1。
[0069]
表1
[0070]
[0071][0072]
实施例3-10制备的长碳链聚酰胺多孔膜的性状表征如下表2所示。
[0073]
表2
[0074]
[0075][0076]
对比例1
[0077]
(1)将聚酰胺1012放入烘箱中干燥,烘干温度为100℃,时间为12小时。
[0078]
(2)将上述聚酰胺1012与二甲基亚砜混合,于磁力搅拌器中充分溶胀,聚酰胺1012与二甲基亚砜的比例为20:60,搅拌时间为2小时。
[0079]
(3)向溶胀好的上述溶液中加入乙腈和三氯乙烷的混合溶剂,在搅拌下充分溶解,其中聚酰胺1012、二甲基亚砜、三氯乙烷的比例为20:60:40,溶解时间为12小时。
[0080]
(4)将得到的聚酰胺溶液静置脱泡,然后用刮刀在玻璃板上进行刮涂,得到湿膜。刮刀的狭缝尺寸为200mm,刮膜速度为30mm/s。
[0081]
(5)将湿膜放入烘箱中,在170℃下加热30分钟。该条件下聚酰胺1012的薄膜中无明显的孔洞形成。该多孔膜断面的扫描电子显微镜的结果见图3。
[0082]
从图3中可以看出,在聚酰胺膜的整个厚度范围内,没有明显的孔洞结构。
[0083]
以上所述仅是本发明的较佳实施例而已,并非对本发明作任何形式上的限制,虽然本发明已以较佳实施例揭露如上,然而并非用以限定本发明,任何熟悉本专利的技术人员在不脱离本发明技术方案范围内,当可利用上述提示的技术内容作出些许更动或修饰为等同变化的等效实施例,但凡是未脱离本发明技术方案的内容,依据本发明的技术实质对以上实施例所作的任何简单修改、等同变化与修饰,均仍属于本发明方案的范围内。