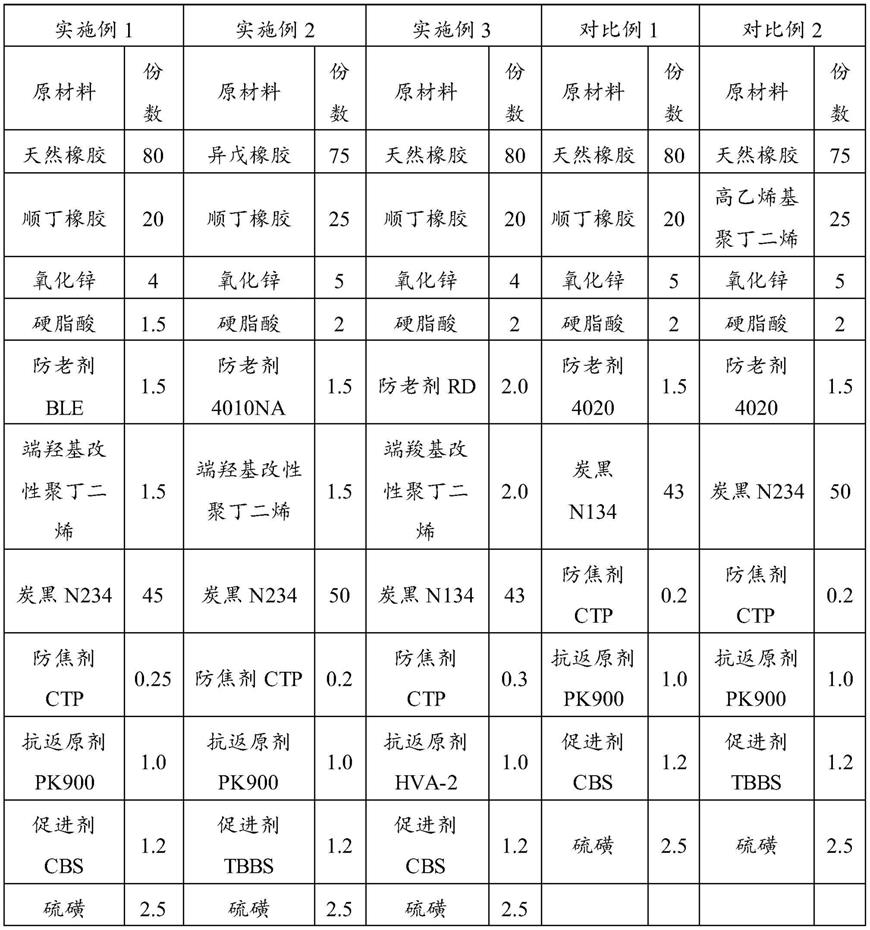
1.本技术涉及胎面橡胶材料技术领域,具体涉及一种能够用于航空轮胎制造的胎面橡胶材料,即是一种航空轮胎用胎面橡胶材料及应用。
背景技术:2.航空轮胎被誉为轮胎工业“皇冠上的明珠”,作为航空器与地面接触的唯一部件,航空轮胎需要满足高速度、超高载荷、超高冲击三大极端工况下的使用要求。因此,与乘用车轮胎注重操控性、节能性、舒适性等诸多综合因素的平衡不同,航空轮胎对于安全性、可靠性、稳定性三大要素有着极端追求。胎面作为轮胎与地面直接接触的唯一部位,会首当其冲地受到极端工况的考验,所以胎面胶性能的优劣会对航空轮胎使用性能产生直接、显著的影响。
3.为了保障航空器和航空轮胎的安全性,胎面胶在机械性能方面需要具备极其优异的耐磨、耐刺扎、耐切割性能。另外,由于航空轮胎承载高、下沉量大,胎面部位在使用过程中的形变很大,势必会造成胎面部位的快速生热和升温,而高的生热会与机械应力作用耦合在一起,加速胎面部位的机械破坏。因此,在提高配方胶料机械性能的同时,抑制或降低动态生热,这对于高性能胎面胶和高端航空轮胎的开发大有裨益。
4.其中,炭黑作为橡胶配方中最重要的主要原材料之一,对于橡胶的补强和机械性能的提升具有决定性的作用。对于在极端工况下使用,对机械性能有着极端追求的航空轮胎胎面部位而言,在进行配方开发设计时,通常会选择小粒径、高结构度的高耐磨甚至超耐磨炭黑,作为补强填料。这种设计思路能够极大提高航空轮胎在行驶过程中的耐磨损、耐刺扎性能,提高航空轮胎的安全性、可靠性、稳定性和使役寿命。但是随着炭黑粒径的降低、结构度的提高,胶料的生热会显著增加,这对于航空轮胎整体性能的提升会产生负面作用。降低小粒径、高结构度炭黑的用量显然能够降低生热,但毫无疑问在一定程度上会牺牲胎面的机械性能。
技术实现要素:5.本发明旨在开发一种能够用于航空轮胎制造的胎面橡胶材料,所述的航空轮胎用胎面橡胶材料具有较高的机械性能,同时兼具低生热特性,利于在高性能航空轮胎中的应用。
6.本发明提供一种航空轮胎用胎面橡胶材料,其主要由如下配方原料制备得到:
7.100重量份的橡胶组分;
8.0.5-10重量份的端基改性聚丁二烯;
9.35-65重量份的补强炭黑;
10.以及氧化锌、硬脂酸、防老剂、防焦剂、抗返原剂、促进剂和硫磺;
11.所述橡胶组分为天然橡胶/顺丁橡胶并用胶或异戊橡胶/顺丁橡胶并用胶;所述补强炭黑为细粒子补强炭黑,依astmd1765分类的吸碘值不低于100mg/g;所述端基改性聚丁
二烯的改性基团为羟基或羧基。
12.在本发明的实施例中,所述橡胶组分为天然橡胶/顺丁橡胶并用胶或异戊橡胶/顺丁橡胶并用胶,并用胶中二者总份数按100重量份计,顺丁橡胶为10~50重量份,优选为15~35重量份。
13.在本发明的实施例中,所述端基改性聚丁二烯的羟值高于0.4mmol/g或羧基值高于0.3mmol/g,所述端基改性聚丁二烯用量优选为1~5重量份。
14.在本发明的实施例中,所述补强炭黑的压缩吸油值不低于100cm3/100g,所述补强炭黑用量优选为40~55重量份。
15.在本发明的实施例中,所述氧化锌用量为3~10重量份,优选为4~8重量份;所述硬脂酸用量为1~5重量份,优选为1.5~3.5重量份。
16.在本发明的实施例中,所述防老剂为对苯二胺类和喹啉类并用型防老剂;所述防老剂总量为1~5重量份,优选为1.5~3.5重量份。
17.进一步地,所述对苯二胺类防老剂为防老剂4010、防老剂4010na和防老剂4020中的一种或多种的混合物。
18.进一步地,所述喹啉类防老剂为防老剂ble、防老剂aw、防老剂rd中的一种或多种的混合物。
19.在本发明的实施例中,所述防焦剂为ctp,用量为0.1~0.4重量份,优选为0.2~0.3重量份;所述抗返原剂用量为0.5~2重量份,优选为0.8~1.5重量份。
20.进一步地,所述抗返原剂为间苯撑双马来酰亚胺(hva-2)、二水合六亚甲基-1,6-二硫代硫酸二钠盐(hts)或1,3-双(柠糠酰亚胺甲基)苯(pk900)中的一种。
21.在本发明的实施例中,所述促进剂为次磺酰胺类促进剂,用量为0.5~2重量份,优选为0.8~1.5重量份;所述硫磺用量为1~4.5重量份,优选为1.5~2.5重量份。
22.进一步地,所述次磺酰胺类促进剂为tbbs、cbs、cbbs、dcbs中的一种或多种的混合物。
23.在本发明的实施例中,所述航空轮胎用胎面橡胶材料的拉伸强度高于27mpa,压缩生热测试值低于39℃。
24.本发明提供如前文所述的航空轮胎用胎面橡胶材料在制造航空轮胎中的应用。
25.与现有技术相比,本发明实施例提供的航空轮胎胎面胶配方包括:天然橡胶或异戊橡胶、顺丁橡胶、端基改性聚丁二烯、细粒子补强炭黑、氧化锌、硬脂酸、防老剂、防焦剂、抗返原剂、促进剂和硫磺;其中,所述端基改性聚丁二烯为0.5~10重量份,其改性基团为羟基或羧基,而且所述细粒子补强炭黑用量为35~65重量份。在本发明配方体系中,在不降低小粒径、高结构度补强炭黑用量,保证胎面胶足够高的机械性能的同时,以少量的端羧基(或羟基)改性聚丁二烯作为助剂,能提高橡胶与炭黑的界面相互作用,抑制炭黑粒子的聚集和炭黑网络的形成,从而降低胎面胶在动态使用过程中由于炭黑网络破坏-重组而引发的滞后损失及最终导致的快速生热。本发明基于补强炭黑粒子表面含有的少量羟基、羧基、环氧基等基团,通过炭黑与端基改性的聚丁二烯之间的偶联反应,改善橡胶与炭黑的界面作用,控制胎面胶的动态生热,利于在高性能航空轮胎中的应用。
具体实施方式
26.下面对本技术实施例中的技术方案进行清楚、完整地描述,显然,所描述的实施例仅仅是本技术一部分实施例,而不是全部的实施例。基于本技术中的实施例,本领域普通技术人员在没有做出创造性劳动前提下所获得的所有其他实施例,都属于本技术保护的范围。
27.本技术提供了一种航空轮胎用胎面橡胶材料,其主要由如下配方原料制备得到:
28.100重量份的橡胶组分;
29.0.5-10重量份的端基改性聚丁二烯;
30.35-65重量份的补强炭黑;
31.以及氧化锌、硬脂酸、防老剂、防焦剂、抗返原剂、促进剂和硫磺;
32.所述橡胶组分为天然橡胶/顺丁橡胶并用胶或异戊橡胶/顺丁橡胶并用胶;所述补强炭黑为细粒子补强炭黑,依astmd1765分类的吸碘值不低于100mg/g;所述端基改性聚丁二烯的改性基团为羟基或羧基。
33.本发明的目的主要在于提供一种可以获得超高机械性能,且兼具低生热特性的航空轮胎胎面胶配方。
34.在本发明的实施例中,该胎面胶配方包括:天然橡胶或异戊橡胶、顺丁橡胶、端基改性聚丁二烯、补强炭黑、氧化锌、硬脂酸、防老剂、防焦剂、抗返原剂、促进剂和硫磺;优选仅采用上述原料制备,配方组成简单。
35.作为优选,本发明所述的橡胶组分为天然橡胶、异戊橡胶和顺丁橡胶中的至少两种。天然橡胶是一种以聚异戊二烯为主要成分的天然高分子物质,可简称天然胶,具有非常好的机械性能等,其中烟片胶最具代表性;异戊橡胶是由异戊二烯合成的橡胶,可简称异戊胶,其性能接近天然橡胶。顺丁橡胶是顺式1,4-聚丁二烯橡胶的简称,工业生产顺丁橡胶均采用溶液聚合的方法,原材料主要有单体丁二烯、溶剂和催化剂等。本发明采用市售的生胶组分,例如天然胶rss1#,顺丁胶br9000。
36.进一步地,本发明所述配方生胶为天然胶/顺丁胶并用胶,或者异戊胶/顺丁胶并用;并用胶中二者总份数按100重量份计,顺丁胶为10~50重量份,优选为15~35重量份,例如18、20、25、30份。
37.在本发明配方中,使用端基改性聚丁二烯作为一种助剂,所述端基改性聚丁二烯为0.5~10重量份,优选为1~5重量份(其用量较少,不影响生胶自身的动态粘弹性)。具体地,所述端基改性聚丁二烯的主链包含顺式1、4加成,反式1、4加成和1、2加成结构,其中顺式1、4加成为主要主链结构,占比超过90%。本技术实施例所涉及的端基改性聚丁二烯为外购产品;其端基位置的改性基团为羟基或羧基,羟值高于0.4mmol/g或羧基值高于0.3mmol/g,可以自制或购买市售产品。例如,端羟基改性聚丁二烯的羟值为0.67mmol/g,或者,端羧基改性聚丁二烯的羧基值为0.49mmol/g。本发明所用的端基改性聚丁二烯可与炭黑表面极性官能团耦合,提高炭黑与橡胶的界面相互作用,抑制炭黑的集聚、絮凝,减少二次结构的生成,进而在提高胎面胶机械性能的同时降低胶料的动态生热。
38.本发明配方原料包括35-65重量份的补强炭黑;所述补强炭黑为细粒子补强炭黑,依astmd1765分类,炭黑吸碘值不低于100mg/g,同时压缩吸油值不低于100cm3/100g,例如炭黑n234、炭黑134。在本发明中,所述细粒子补强炭黑用量为35~65重量份,优选为40~55
重量份。本发明在不改变常用炭黑类型,不降低炭黑用量的情况下,通过优化调整材料内部结构,降低胶料生热,进一步提高航空轮胎的综合性能。
39.在本发明实施例的配方原料中,所述氧化锌和硬脂酸可以起到活化、润滑等综合作用。所述氧化锌用量为3~10重量份,优选为4~8重量份;所述硬脂酸用量为1~5重量份,优选为1.5~3.5重量份。
40.并且,本发明所述的胎面橡胶材料制备原料包括防老剂、防焦剂和抗返原剂。其中,所述防老剂优选为对苯二胺类和喹啉类并用型防老剂。所述对苯二胺类防老剂为防老剂4010(又名n-环己基-n'-苯基对苯二胺)、防老剂4010na和防老剂4020(n-(1,3-二甲基)丁基-n'-苯基对苯二胺,又称防老剂dmppd)中的一种或多种的混合物;所述喹啉类防老剂为防老剂ble(9,9-二甲基吖啶)、防老剂aw(乙氧基喹啉)、防老剂rd(2,2,4-三甲基-1,2-二氢化喹啉聚合体,又称抗氧剂rd,防老剂224)中的一种或多种的混合物。所述并用型防老剂的总量可为1~5重量份,优选为1.5~3.5重量份。
41.在本发明的具体实施例中,所述防焦剂为ctp,防焦剂ctp的学名是n-环己基硫代邻苯二甲酞亚胺;该品通常在含有次磺酰胺促进剂的胶料中可以改善胶料的焦烧时间,而对硫化速度和硫化胶性能没有明显影响,而胶料的抗焦烧时间在较宽的范围内可以通过其用量的变化加以调节。示例地,本发明所述防焦剂用量可为0.1~0.4重量份,优选为0.2~0.3重量份。
42.另外,所述抗返原剂可为间苯撑双马来酰亚胺(hva-2)、二水合六亚甲基-1,6-二硫代硫酸二钠盐(hts)或1,3-双(柠糠酰亚胺甲基)苯(pk900)中的一种。所述抗返原剂用量可为0.5~2重量份,优选为0.8~1.5重量份。
43.作为优选,本发明胎面胶配方中的促进剂为次磺酰胺类促进剂,用量可为0.5~2重量份,优选为0.8~1.5重量份。所述次磺酰胺类促进剂可为tbbs(n-叔丁基-2-苯并噻唑次磺酰胺)、cbs(n-环己基-2-苯并噻唑次磺酰胺)、cbbs(n-环已基双(苯并噻唑)次磺酰亚胺)、dcbs(n,n-二环己基-2-苯并噻唑次磺酰胺,又名促进剂dz)中的一种或多种的混合物。
44.本发明胎面胶组成采用硫磺进行硫化交联;所述硫磺用量优选为1~4.5重量份,更优选为1.5~2.5重量份。
45.本发明实施例中胶料的制备方法为常规方式,主要包括:一段混炼时,设备初始温度优选设置为70℃,混炼时间和混炼排胶温度可分别控制在7-10min和170℃以内;加料顺序依次为生胶、中间物料和炭黑。终炼时设备初始温度优选设置为50℃,混炼时间和混炼排胶温度可分别控制在2-5min和110℃以内。
46.本发明实施例中的关键点在于端基改性聚丁二烯的使用,通过该材料的少量添加能够控制和降低胶料的动态生热,提高胎面胶料的综合性能。所述航空轮胎用胎面橡胶材料的拉伸强度高于27mpa,压缩生热测试值低于39℃。本发明提供如前文所述的航空轮胎用胎面橡胶材料在制造航空轮胎中的应用,利于提升航空轮胎使用性能。
47.为了进一步理解本技术,下面结合实施例对本技术提供的航空轮胎用胎面橡胶材料和应用进行具体地描述。本发明实施例采用市售的原料。
48.实施例1
49.按照表1中的配方组成,一段混炼时,设备初始温度设置为70℃,混炼时间和混炼排胶温度分别控制在8min和170℃以内。加料顺序依次为生胶、中间物料和炭黑。终炼时设
备初始温度设置为50℃,混炼时间和混炼排胶温度分别控制在3min和110℃以内,制备得到胶料。
50.实施例2-3
51.按照表1中的配方组成,制备工艺与实施例1相同,分别得到胶料。
52.对比例1-2
53.按照表1中的配方组成,制备工艺与实施例1相同,分别得到胶料。
54.实施例1-3及对比例1-2的胎面胶组成如下表所示:
55.表1实施例的胎面胶配方组成
[0056][0057]
其中,生胶的各个牌号、性能指标如下;实施例1和2中,端羟基改性聚丁二烯的羟值为0.67mmol/g;实施例3中,端羧基改性聚丁二烯的羧基值为0.49mmol/g。实施例中所采用的端基改性聚丁二烯均为市售产品;高乙烯基聚丁二烯(1,2-pbr)品牌日本曹达,牌号nisso-pb,1,2-乙烯基结构高于85%。
[0058]
表2实施例中的生胶的牌号
[0059] 天然胶异戊胶顺丁胶牌号rss 1#ski-5pmbr9000产地印度尼西亚俄罗斯中国门尼ml
1+4
(100℃)918045
[0060]
实施例1-3及对比例1-2的胎面胶关键性能如下表所示:
[0061]
表3实施例的胎面胶性能
[0062][0063]
由以上实施例可知,本发明所述的航空轮胎用胎面橡胶材料具有较高的机械性能(例如拉伸强度高于27mpa),同时兼具低生热特性(压缩生热测试值低于39℃,低于对比例)。本发明保证了胎面胶足够高的机械性能,同时降低胎面胶在动态使用过程中由于炭黑网络破坏-重组而引发的滞后损失及最终导致的快速生热,利于在高性能航空轮胎中的应用。
[0064]
以上所述仅是本发明的优选实施方式,应当指出,对于使本技术领域的专业技术人员,在不脱离本发明技术原理的前提下,是能够实现对这些实施例的多种修改的,而这些修改也应视为本发明应该保护的范围。