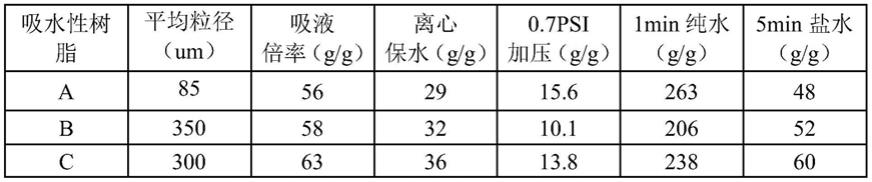
1.本发明提供一种包含反相悬浮聚合工艺异常粒径吸水性树脂再利用方法。
背景技术:2.高吸水性树脂(sap,superabsorbent polymers)是一种轻度交联的高分子化合物,由于其强大的吸水与保水能力,被广泛用于纸尿裤、卫生巾等的卫生材料领域,电缆、光缆用阻水材料以及农林、园艺专用的保水剂等。作为卫生材料用的吸水性树脂,已知有聚丙烯酸部分中和物、淀粉-丙烯酸接枝聚合物的中和物、淀粉-丙烯腈接枝聚合物的水解物、乙酸乙烯酯-丙烯酸酯共聚物的皂化物等。
3.目前,使用最为广泛的是聚丙烯酸及其钠盐的系列产品,其中,约有95%是采用水溶液聚合工艺制备,另外约有5%是采用反相悬浮聚合工艺制备。一般来讲,用在生理卫生领域的吸水性树脂的粒径要在150-710um以内,平均粒径在300-400um且要求有合适的粒径分布。但是在实际生产过程中,无论对于水溶液聚合还是反相悬浮聚合工艺来讲,不可避免的会产生粒径小于150um的细粉和粒径大于710um的大颗粒(称之为异常品),而粒径分布处于这两个范围的吸水性树脂的综合性能存在较大的缺陷,如何有效利用这些粒径异常的吸水性树脂来提升生产效率并降低成本显得十分关键。
4.在水溶液聚合工艺领域,我们可以将粒径异常的吸水性树脂研磨成粒径分布在150-710um之间的正常颗粒以及粒径小于150um的细粉,正常粒径范围的产品可以按照比例直接共混再利用,而围绕吸水性树脂的细粉问题,人们一般将其用水将其溶胀,然后加入其它助剂进行细粉造粒(中国专利cn 100333826c、cn 1636629a、欧洲专利ep 0309187和ep 0844270),重新获得粒径在150-710微米之间的正常品,或者直接加入到丙烯酸中和液中进行再聚合(中国专利cn 105131314b、cn 106574006a和美国专利us 4950692),也可以将之加入到聚合形成的水凝胶中,经过造粒工序,得到吸收速率优异且不牺牲其他性能的吸水性树脂,例如lg化学专利cn 106574006a。在反相悬浮聚合领域,由于聚合过程中的搅拌以及散热问题,使得聚合过程中不可避免的出现粘釜与缠桨问题,这部分得到的吸水性树脂的形貌不是颗粒状且性能劣化严重,加之就算正常粒径的吸水性树脂由于后续并没有相应的研磨工序,两方面原因造成亦会存在部分颗粒偏大的异常吸水性树脂。而这些异常产品如何处理,几乎很少被报道,几乎全部集中在正常粒径的简单共混与细粉颗粒的造粒工艺。住友精化专利cn1175962a报道了一种采用反相悬浮聚合工艺将不同吸收速率的吸水性树脂共混来获得既能减少被吸收液的回流量,又能提升被吸收液的扩散性的方法,日本触媒专利cn 1517410a报道了一种将两种不同聚合工艺制备的吸水性树脂按照不同的比重混合在一定,得到不同堆积比重的吸水性树脂粒子,表现出优异的加压下吸收和较低的返湿量。为提升吸水性树脂细粉的利用率,万华化学专利cn106893119b公布了一种将小于150um的细粉加入到反相悬浮聚合前的单体液滴中进行搅拌与聚并来获得合适粒径与优异吸收速率的吸水性树脂颗粒的方法,紧接着cn 111621039a又公开了一种将反相悬浮聚合工艺与水溶液聚合工艺得到的细粉共混进行细粉造粒,来制备具有差异化形貌与性能的吸水性树
脂的工艺。
5.基于已有的这些报道主要是针对简单的细粉造粒和物理共混,实际应用价值有待商榷。因此,如何高效的利用反相悬浮工艺制备的异常产品需要引起我们的关注与重视。本发明提供一种异常粒径吸水性树脂(包含细粉与大颗粒)的回收再利用工艺,一方面提升了反应固含量,降低了后处理成本;另一方面,使得颗粒团聚与表面交联更加均匀,获得更加可控的粒径分布和平衡产品性能。
技术实现要素:6.本发明基于现有细粉造粒技术,克服了简单的物理共混而带来的综合性能缺陷,创造性地提供了吸水性树脂异常品(包含细粉与大颗粒)研磨然后添加到正常反相悬浮工艺不同的聚合工序中,然后进行脱水和表面交联等后处理工序,从而获得兼具正常粒径分布与基本性能吸水性树脂的方法。
7.为达到以上发明目的,本发明的方案如下:
8.一种异常粒径吸水性树脂再利用方法,包含以下步骤:
9.1)研磨与筛分:将异常粒径的吸水性树脂进行研磨与筛分,得到要共混的吸水性树脂颗粒,即粒径范围分布在150um以下和150-500um两个区间;
10.2)共混与脱水:将a份的粒径分布在150um以下的细粉添加到反相悬浮聚合工艺一步聚合后、二步聚合前的工序中,将b份的粒径分布在150-500um之间的颗粒添加到二步聚合后、共沸脱水前的工序中,然后进行脱水与溶剂回流,得到混合与粘连后的水凝胶粒子
11.3)表面交联与后处理:将2)步骤所得的混合液中加入表面交联剂的水溶液,进行表面交联反应,然后除去反应液,继续干燥即可得到吸水性树脂成品。
12.本发明中,所述一步聚合,即为第一次加入单体时的聚合,目的是形成形貌是单个球形颗粒的初级粒子;所述二步聚合,即为一步聚合结束后,再次加入单体进行的聚合,目的是形成具有“葡萄串状”的团聚态次级粒子。
13.本发明中,1)步骤所述异常粒径指的是粒径小于150um的细粉和大于710um的粒状、片状以及其他不规则形状的吸水性树脂,优选通过反相悬浮聚合工艺制备。
14.本发明中,1)步骤所述研磨后的吸水性树脂的颗粒粒径为10-1000um,优选为50-710um,进一步优选为100-500um。
15.本发明中,2)步骤所述a和b的添加比例为0-20%(相对于制备吸水性树脂原料,即丙烯酸单体的总量),优选为0-10%,且0<a+b≤20%。
16.本发明中,2)步骤所述反相悬浮聚合工艺使用的分散剂为hlb值小于7的表面活性剂,优选蔗糖脂肪酸酯、山梨醇酐单硬脂酸酯、山梨醇酐单油酸酯、三聚甘油单硬脂肪酸酯和十八烷基单磷酸酯、马来酸酐改性聚乙烯、马来酸酐改性聚丙烯或马来酸酐改性乙烯-丙烯共聚物中的至少一种,用量为丙烯酸单体质量分数的0.01-5%,优选为0.1-3%。使用的乳化剂选自hlb大于10的水溶性非离子乳化剂,优选蔗糖脂肪酸酯(s-1170与s-1570)、聚氧乙烯辛基苯酚醚-10(op-10)、脱水山梨醇酐单月桂酸酯(span-20)、聚乙二醇或聚乙烯醇中的至少一种,用量为丙烯酸单体质量分数的0.1-3%。使用的油相为石油烃类溶剂,可选自脂肪烃、脂环烃或芳香烃中的至少一种,适宜的脂肪烃选自于正戊烷、正己烷、正庚烷、石油醚等;适宜的脂环烃选自于环戊烷、甲基环戊烷、环己烷、甲基环己烷等;适宜的芳香烃是
苯、甲苯、二甲苯等。使用的水相为丙烯酸及其中和液,中和度优选为60-85%,中和反应中丙烯酸单体的质量浓度优选为20-50%;所述油相与水相的比例为0.5-10:1,优选为1-3:1。
17.本发明中,2)步骤所述反相悬浮聚合的引发剂选自于过硫酸钠、过硫酸钾、过硫酸铵或者2,2'-偶氮二异丁基脒二盐酸盐中的一种或多种,用量为丙烯酸单体质量分数的0.005-5%,优选为0.05-2%。所用内交联剂选自于含羟基的乙二醇、丙二醇、丙三醇、季戊四醇、聚甘油、聚乙烯醇、三羟甲基氨基甲烷中的一种或多种;含环氧基团的乙二醇二缩水甘油醚、丙二醇二缩水甘油醚、聚乙二醇二缩水甘油醚、聚丙二醇二缩水甘油醚、聚甘油缩水甘油醚中的一种或多种;含反应型双键的乙二醇双丙烯酸酯、丙二醇双丙烯酸酯、n,n'-亚甲基双丙烯酰胺、聚乙二醇双丙烯酸酯、聚丙二醇双丙烯酸酯、季戊四醇三烯丙基醚、乙氧基化甘油三丙烯酸酯、三羟甲基丙烷三丙烯酸酯、季戊四醇三丙烯酸酯、三烯丙基胺、季戊四醇四丙烯酸酯、二季戊四醇六丙烯酸酯中的一种或多种,用量为丙烯酸单体质量分数的0.005-1%,优选为0.05-1%。
18.本发明中,2)步骤所述两步反相悬浮聚合的聚合温度均为30-120℃,优先为50-90℃;聚合时间为0.1-5h,优选为0.5-2h。
19.本发明中,2)步骤所述共沸脱水量为50-90%,优选为70-90%。
20.本发明中,3)步骤中表面交联剂为可以与羧基发生形成共价键或离子键的化合物:可形成共价键的化合物包括多醇化合物,环氧化合物以及聚乙烯亚胺,优选为乙二醇、丙二醇、1,4-丁二醇、碳酸亚乙酯、碳酸亚丙酯、(聚)乙二醇二缩水甘油醚、(聚)丙二醇二缩水甘油醚、甘油、三羟甲基氨基甲烷、季戊四醇中的一种或多种;可形成离子键的化合物包括钙、镁、铝、铁、铜、锌多价金属的无机盐;表面交联剂添加量为丙烯酸单体总质量的0.01-2%,优选为0.02-0.2%;表面交联剂水溶液的质量浓度0.1-50%,优选为1-10%。
21.本发明中,2)步骤中共沸脱水温度为80-150℃,时间为1-5h。其中3)步骤中表面交联温度为60-100℃,时间为0.5-2h,干燥温度为100-130℃,时间为1-3h。
22.本发明相对于现有技术的贡献之一在于改变了共混方式,将研磨后的吸水性树脂颗粒加入到共沸脱水(反相悬浮聚合工艺能耗最大的工序)前的工序中去,一方面实现了细粉造粒的目的,另一方面利用该过程的溶剂与水的回流,促进了正常颗粒与研磨共混颗粒间的融合,使得颗粒对于后续表面交联剂的吸附更加均匀有效,最终产品的综合性能更加平衡;其次,加入的研磨共混的吸水性树脂颗粒,相当于增加了水凝胶的固含量,有助于降低体系脱水量,大大的降低能耗,节约生产成本并提升生产效率。因此本发明一方面实现了大粒径异常颗粒的高效回收与再利用和细粉造粒的目的,一方面获得了平衡的产品性能,并且最终节省了能耗并提升了生产效率。
23.本发明所述的吸水性树脂的基本性能指标测试方法如下:
24.其中,吸液倍率、离心保水与加压吸液倍率测试方法执行gb/t 22875-2018和iso 17190-5-2001标准,而5min生理盐水与1min纯水吸收量则按如下方法进行测试。
25.5min生理盐水吸收量(g/g)
26.准确称量0.2g sap样品于一次性茶袋中并密封,使之和空白茶袋完全浸没于23℃(23
±
2℃)的生理盐水中,浸泡5min后,取出并垂直悬挂10min(彼此不要接触),此时称其重量分别为m0和m1,则:sap样品的1min吸液量(g/g)=(m
1-m0)/0.2。
27.1min纯水吸收量(g/g)
28.向盛有250ml去离子水(控制水温23-25℃)的烧杯中,加入0.5g(精确至0.001g)烘干的sap样品,并开始用秒表计时,快到1min时,将水溶液搅拌均匀并立即倒入滤袋中,稍微将自由水滴净后,称量胶体加入时和取出后的滤袋重量,分别为m2和m1,即:sap样品的1min的纯水吸收量(g/g)=(m
2-m1)/0.5。
附图说明
29.图1是吸水性树脂a的sem电镜图。
30.图2是吸水性树脂b的sem电镜图。
31.图3是吸水性树脂c的sem电镜图。
具体实施方式
32.下面将以具体的实施例对本发明进行详细的描述
33.吸水性树脂a、b与c的反相悬浮聚合制备工艺
34.将220g正庚烷加入到装有搅拌器、回流冷凝器、温度计和氮气入口管的1l四口圆底烧瓶中。向其中加入0.46g蔗糖脂肪酸酯(三菱化学,s-370)和0.46g马来酸酐改性乙烯-丙烯共聚物(三井化学,1105a),升温至80℃并以350rpm的搅拌速度使其均匀溶解分散,然后降温至30℃,得到油相以备用。在边冷却边搅拌条件下,将120g 32%w.t.氢氧化钠水溶液滴加到溶有92g丙烯酸单体与50g去离子水的500ml锥形烧瓶中,待温度降至30℃以下时,其中加入含有0.13g过硫酸钾、9.2mg次亚磷酸钠和含0.08g聚乙二醇400双丙烯酸酯的水溶液36g,充分溶解混合后得到用丙烯酸中和液,即水相以备用。
35.将配置好的水相的一半加入到油相中,边搅拌边用氮气置换30min。然后升温至75℃,在此条件下反应2h进行一段油包水反相悬浮聚合,得到含有一段聚合sap胶粒的悬浮液。
36.继续将此悬浮液冷却至50℃,将0.92g聚氧乙烯辛基苯酚醚-10(op-10)加入到上述配置好的另一半水相中使之充分溶解,然后将之一起加入到降温后的油相中,重复上述步骤进行二段油包水反相悬浮聚合,得到发生团聚作用的含有二段聚合sap胶粒的悬浮液。继续升温至120℃进行共沸脱水并使得正庚烷回流,当水分脱除量为107g(此时水分脱除量为80.5%,用时2.5h)时,加入质量浓度为2%的乙二醇二缩水甘油醚水溶液3.7g并在85℃下反应1.5h,进行表面交联。停止搅拌,发现绝大部分吸水性树脂颗粒(正常品-葡萄串状-90%)沉降在烧瓶底部,还有一部分粘连在搅拌桨和烧瓶内壁(异常品-10%),将上述体系过滤并把得到的两种产品置于130℃下干燥2h。
37.最后用高速研磨机对粒径在710um以上的大颗粒进行研磨并一起用不同目数的筛网对其进行筛分和混合,得到以下三种粒径分布的吸水性树脂,细粉异常品a-10%,大颗粒异常品-15%,团聚态正常品c-75%。
38.表1吸水性树脂a、b与c的基本性能
[0039][0040]
实施例1
[0041]
将220g正庚烷加入到装有搅拌器、回流冷凝器、温度计和氮气入口管的1l四口圆底烧瓶中。向其中加入0.46g蔗糖脂肪酸酯(三菱化学,s-370)和0.46g马来酸酐改性乙烯-丙烯共聚物(三井化学,1105a),升温至80℃并以350rpm的搅拌速度使其均匀溶解分散,然后降温至30℃,得到油相以备用。在边冷却边搅拌条件下,将120g 32%w.t.氢氧化钠水溶液滴加到溶有92g丙烯酸单体与50g去离子水的500ml锥形烧瓶中,待温度降至30℃以下时,其中加入含有0.13g过硫酸钾、9.2mg次亚磷酸钠和含0.08g聚乙二醇400双丙烯酸酯的水溶液36g,充分溶解混合后得到用丙烯酸中和液,即水相以备用。
[0042]
将配置好的水相的一半加入到油相中,边搅拌边用氮气置换30min。然后升温至75℃,在此条件下反应2h进行一段油包水反相悬浮聚合,得到含有一段聚合sap胶粒的悬浮液。
[0043]
继续将此悬浮液冷却至50℃,将0.92g聚氧乙烯辛基苯酚醚-10(op-10)加入到上述配置好的另一半水相中使之充分溶解,然后将之一起加入到降温后的油相中,重复上述步骤进行二段油包水反相悬浮聚合,得到发生团聚作用的含有二段聚合sap胶粒的悬浮液。向所得体系中加入18.4g的吸水性树脂b(质量分数20%),继续升温至120℃进行共沸脱水并使得正庚烷回流,当水分脱除量为102g(此时水分脱除量为80.5%,用时1.6h)时,加入质量浓度为2%的乙二醇二缩水甘油醚水溶液4.6g并在85℃下反应1.5h,进行表面交联。停止搅拌,发现绝大部分吸水性树脂颗粒沉降在烧瓶底部,将上述体系过滤并把得到的置于130℃下干燥2h至含水量低于3%,取粒径分布区间在150-710um的粒子进行性能测试。
[0044]
实施例2
[0045]
除了将4.6g吸水性树脂a(质量分数5%)加入到一段聚合结束后、二段聚合结束前的工序中,将9.2g吸水性树脂b(质量分数10%)加入到二段聚合结束后、共沸脱水前的工序中,且共沸脱除103g水(此时水分脱除量为80.5%,用时1.8h)并将表面交联的水溶液改为4.3g外,重复实施例1的操作。
[0046]
实施例3:
[0047]
除了将9.2g吸水性树脂a(质量分数10%)加入到一段聚合结束后、二段聚合结束前的工序中,将4.6g吸水性树脂b(质量分数5%)加入到二段聚合结束后、共沸脱水前的工序中,且共沸脱除103g水(此时水分脱除量为80.5%,用时1.8h)并将表面交联的水溶液改为4.6g外,重复实施例1的操作。
[0048]
实施例4:
[0049]
除了将18.4g吸水性树脂a(质量分数20%)加入到一段聚合结束后、二段聚合结束前的工序中,且共沸脱除102g水(此时水分脱除量为80.5%,用时2.0h)外,重复实施例1的操作。
[0050]
比较例1(直接物理混合):
[0051]
直接将18.4g的吸水性树脂b(质量分数20%)与73.6g吸水性树脂c直接混合均匀,然后取粒径分布区间在150-710um的粒子进行性能测试。
[0052]
比较例2:
[0053]
除了将23.0g吸水性树脂a(质量分25%)加入到一段聚合结束后、二段聚合结束前的工序中,且共沸脱除100g水(此时水分脱除量为80.5%,用时2.2h)并将表面交联的水溶液改为4.4g外,重复实施例1的操作,由于此时的异常细粉加入量过多,影响了体系的混合均一度和聚合的稳定性,最终产品的大颗粒比正常多10%。
[0054]
比较例3:
[0055]
除了将23.0g吸水性树脂b(质量分数25%)加入到二段聚合结束后、共沸脱水前的工序中,且共沸脱除100g水(此时水分脱除量为80.5%,用时1.4h)并将表面交联的水溶液改为4.9g外,重复实施例1的操作。
[0056]
比较例4(共沸脱水后加入):
[0057]
除了将9.2g吸水性树脂a(质量分数10%)与9.2g吸水性树脂b(质量分数10%)加入到共沸脱水后、表面交联前的工序中,重复实施例1的操作,脱水时间2.5h,由于此时的异常细粉和研磨大颗粒是在共沸脱水后加入的,使得粘连效率降低,影响了细粉造粒工序,最终产品的细粉含量比正常多8%。
[0058]
表2所得吸水性树脂组合物的基本性能
[0059][0060]
由实施例和比较例可以看出,将适量的异常细粉和异常大颗粒研磨样品分别加入到一段聚合结束后、二段聚合结束前的工序中和二段聚合结束后、共沸脱水前的工序中,可以获得综合性能优异的吸水性树脂产品,一方面实现了细粉造粒和异常样品的回收再利用;另一方面提升了体系固含,降低了能耗、提升了生产效率。这是由于在这两个工序过程中,存在着体系水的扩散与再分配,促进了异常品自身及和正常品之间物理融合的均匀程度。而对比例中,无论是加入的量过多还是加入的时机不对,都不能获得综合性能优异的产品,造成性能缺失或者粒径分布异常,并且表现为吸液后发粘(粒子的凝胶强度有所下降)。
[0061]
总之,以上所述仅为本发明的代表性实施例且仅用于阐述本发明,而并非对本发明的限制,对本发明的任何改进,包括各原料的等效替换与添加等均属于本发明的涵盖范围,此点本技术领域的相关人员应知悉。本发明的专利保护范围应由权利要求书限定。