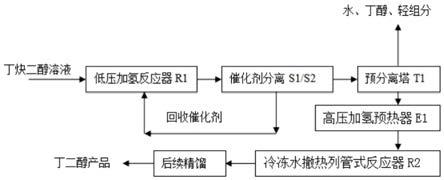
1.本发明涉及1,4-丁二醇生产方法,具体属于一种1,4-丁炔二醇加氢制1,4-丁二醇的方法。
背景技术:2.1,4
‑ꢀ
丁二醇( 简称bdo) 是一种重要的有机和精细化工原料, 它被广泛应用于医药、化工、纺织、造纸、汽车和日用化工等领域。由1,4
‑ꢀ
丁二醇可以生产四氢呋喃( thf) 、聚对苯二甲酸丁二醇酯( pbt) 、γ-丁内脂( gbl) 和聚氨酯树脂( pu resin) 、涂料和增塑剂等,以及作为溶剂和电镀行业的增亮剂等。
3.第二次世界大战前,德国已采用雷佩法以乙炔和甲醛为原料合成1,4-丁二醇。该法解决了乙炔在高压下操作的危险性,至今仍是1,4-丁二醇最主要的生产方法。60年代,日本三菱油化公司开发了由顺丁烯二酸酐催化加氢制备1,4-丁二醇的工艺,70年代该公司又开发了丁二烯乙酰氧基化法的新工艺。1971年,日本东洋曹达工业公司建立了丁二烯氯化法的生产装置。此外,美国和日本又相继研究了以丙烯或乙烯为原料的各种合成法。
4.雷佩法生产过程不太复杂,成本较低。目前,此法的生产能力接近各种方法的总能力的90%,今后此法发展的关键是乙炔原料的供应和价格。
5.顺丁烯二酸酐加氢法,反应分两步进行,联产四氢呋喃。此法原料价高,但反应步骤少、投资低、可调节所得的联产品,因此许多国家仍在加紧进行研究开发。
6.1,4-二氯丁烯法,由丁二烯生产氯丁二烯过程中,1,4-二氯丁烯是中间产物。东洋曹达工业公司开发的方法是将1,4-二氯丁烯在约110℃下用过量甲酸钠水解生成2-丁烯-1,4-二醇,转化率接近100%,选择性大于90%。水解后,游离甲酸用氢氧化钠中和。然后将2-丁烯-1,4-二醇在100℃、27mpa和镍-铝催化剂存在下加氢得 1,4-丁二醇。此法公用工程费用大,生产成本较高。
7.我国拥有丰富的煤炭资源。相较于其余生产工艺,雷佩法的原料主要为煤炭后加工供应。因此雷佩法在我国的1,4-丁二醇生产更具有实际意义。
8.现有的雷佩法生产工艺中第一步1,4-丁炔二醇合成基本一致,只是催化剂的使用方式略有区别。而在加氢工段区别较大,第一种工艺为整个体系全部为高压固定床加氢,采用大流量30wt%~40wt%1,4-丁炔二醇水溶液循环加氢;另一种工艺为两段法,先进行低压加氢后加成产物再进行高压加氢彻底转化;两种方法相比,第二种在保证转化率和产品质量的情况下节约了加氢工段能量消耗;传统的两步法加氢制1,4-丁二醇的过程如下:第一步(也称为一段加氢)一般采用悬浮床(或鼓泡淤浆床),使用雷尼-镍催化剂,在50~80℃,1~3mpa氢气压力下进行低压加氢,将浓度30wt%~40wt%1,4-丁炔二醇水溶液加氢为1,4-丁二醇水溶液,同时溶液中含有正丁醇,不饱和加氢产物1,4-丁烯二醇,1,4-丁烯二醇异构化产物4-羟基丁醛及醛与醇经缩合反应得到的缩醛及其他高沸物和低沸物;由于4-羟基丁醛及缩醛及1,4-丁烯二醇无法通过精馏的方法脱除,存在产品中影响产品纯度与质量,需要进行进一步的高压加氢脱除;
第二步(二段加氢)将一段的产物溶液采用固定床反应器,以负载镍为催化剂,在反应温度110~160℃,氢气压力12~21mpa下进行加氢,主要涉及物料中少量的1,4-丁烯二醇、异构化产物羟基丁醛及缩醛的进一步加氢转化,以提高1,4-丁二醇的产率和减少杂质的存在。
9.以上过程在现有技术中已被多次公开,但是以上工艺在第二段加氢的过程中因为传统固定床滴流反应体系的撤热要求,仍然采用低浓度、大流量的加氢过程,体系中存在大量的水(60wt%~70wt%),因而增加了体系的能耗。
技术实现要素:10.本发明要解决的技术问题是提供一种1,4-丁炔二醇加氢制1,4-丁二醇的方法,通过提前分离以达到降低能耗的目的。
11.为解决以上技术问题,本发明采用的技术方案是:一种1,4-丁炔二醇加氢制1,4-丁二醇的方法,包括:步骤一,经过加压的30wt%~40wt%的1,4-丁炔二醇水溶液进入低压反应器,在雷尼镍-铝-x催化剂作用下,进行第一步加氢反应,产物经过减压后进入常压的旋风分离器,分离器底部分离出雷尼镍-铝-x催化剂,顶部采出反应液,反应液通过袋式过滤器进一步去除催化剂颗粒;步骤二,反应液进入预分离塔;在真空状态下反应液被切分,水、正丁醇、轻组分从塔顶馏出,从塔底出来含有1,4-丁二醇、1,4-丁烯二醇、羟基丁醛、缩醛和重组分的混合水溶液;步骤三,从预分离塔顶部分离出的水、正丁醇、轻组分进入下一分离工段提取副产品正丁醇;步骤四,从预分离塔底部分离出的混合水溶液通过加压和高压加氢预热器预热后进入冷冻水撤热列管式反应器中,将1,4-丁烯二醇、羟基丁醛及缩醛在催化剂作用下转化为1,4-丁二醇,反应物从反应器底部采出,再经过蒸馏后得1,4-丁二醇产品。
12.进一步地,步骤一中,低压反应器中所用的雷尼镍-铝-x催化剂由组成为镍铝质量比为(0.5-1):1、x 的添加量为镍铝总质量的1wt%-2wt %的金属粉末经25%的naoh处理后得到;其中 x 为mg、b、sr、cr、s、ti、la、sn、w、mo、fe 中的任意一种。优选地,x为mg。
13.进一步地,步骤一中,低压反应器进口溶液为30wt%~40wt%的1,4-丁炔二醇水溶液,入口温度为40℃~45℃,入口压力为1.1~4.1mpa,液体空速为1~4h-1
;入口气体为99.99wt%的氢气,入口压力为1.1~4.1mpa,气体空速为11~1.5 h-1
;液体出口压力为0.4~0.8mpa,出口温度为60℃~75℃。
14.进一步地,低压反应器为带有夹套撤热系统的淤浆床反应器。
15.进一步地,步骤二中,所述的预分离塔,其理论板数为3~5,操作压力为15kpa~25kpa;操作温度为60℃~75℃。
16.进一步地,步骤四中,所述的高压加氢预热器为管壳式换热器,液体入口温度为60℃~75℃,出口温度为95℃~140℃。
17.进一步地,步骤四中,冷冻水撤热列管式反应器所装填催化剂的组成为:镍含量11-22 wt%,促进剂含量1~6 wt%,其余为氧化铝,所述的促进剂是镧、铜、镁元素中的一种。
18.进一步地,冷冻水撤热列管式反应器r为列管式反应器,催化剂装填在列管内,壳
程由冷冻水撤热,反应温度控制在95℃~140℃;反应压力控制在10.0~30.0mpa; 反应器液体空速0.5~2.5h-1
。
19.进一步地,从袋式过滤器分离出的催化剂和旋风分离器底部分离出的催化剂循环至低压反应器再次参加反应。
20.本发明中,本发明人通过催化剂比选试验、活性评价、理论计算和软件模拟,掌握了低压1,4-丁炔二醇加氢和高压把关加氢反应的反应规律,筛选出了适合于中压1,4-丁炔二醇加氢合适的催化剂和高浓度下高压把关加氢催化剂的合理反应形式,将现有两段式1,4-丁炔二醇加氢过程中存在的高能耗问题,通过提前分离和改变加氢反应器形式,达到即完成工艺目标,又降低能耗的目的。
21.具体而言,本发明与现有技术相比具有如下优点:(1) 现有技术低压反应器物料出口温度为60℃~75℃,高压加氢前需将含有60%左右的水、丁醇等组分的物料加热到95℃~140℃,耗费大量的能量。本发明无需加热条件下,提前分离低压加氢过后的溶液,在高压加氢前去除了60wt%左右的反应液重量,进而大大的降低了高压加氢工段的能量消耗。同时,高压加氢段的物料处理量相应下降,相同的1,4-丁二醇处理量时,整个高压加压设备的尺寸减小,投资大幅下降。
22.(2)高压物料的浓缩,反应物浓度增加不仅需要更高的催化剂活性,也使得反应放热加剧,对反应器撤热提出更高的要求。现有技术高压反应采用普通的ni/al2o3催化剂,催化剂活性低,不能满足高浓度反应物料的活性需求。采用的固定床塔式反应器,撤热效率低,很容易造成催化剂床层飞温,导致催化剂不可逆失活。本发明一方面,采用了最新研发的新型高效加氢催化剂,该催化剂镍含量11-22 wt%,促进剂含量1~6 wt%,其余为氧化铝,所述的促进剂是镧、铜、镁元素中的一种。催化剂活性组分镍通过混合盐溶液浸渍的方式被引入到载体中,混合镍盐由无机镍盐与有机镍盐混合而成,由于阴离子间的协同与竞争吸附作用可以促使活性组分均匀沉积到催化剂载体的内表面,得到高分散的催化剂产品。同时,在浸渍液中加入适量的表面活性剂聚乙二醇或ctab,一方面起到增加溶解度的作用,另一方面进一步促进了镍物种的分散,焙烧过程产生的积碳还可以阻止活性组分团聚,同时调节活性组分与载体间的相互作用。由于采用特殊的催化剂制备方法,所得催化剂在较高的活性组分负载量下保持了高的分散度,该催化剂具有适宜的表面酸碱性、合适的孔结构、合适的金属与载体的相互作用。因而在高的加氢中表现出高的催化活性与选择性,并具有长的催化剂使用寿命。(3)针对高浓度物料放热加剧的问题,通过对传统高压加氢反应器类型进行优选,将原来简单的固定床塔式反应器改为撤热效果更好的高压列管式反应器,使在高浓度反应的过程中顺利撤出反应热。
23.本发明通过上述工艺流程之后可得产品纯度≥99.5%,色度≤10ahpa的1,4-丁二醇产品。对公用工程消耗大幅下降,动力电消耗低于420 千瓦时/吨1,4-丁二醇,蒸汽消耗低于4.5 吨/吨1,4-丁二醇,循环冷却水消耗低于320 吨/吨1,4-丁二醇。
附图说明
24.图1为现有技术中1,4-丁炔二醇加氢制1,4-丁二醇的流程图。
25.图2为本发明所述的1,4-丁炔二醇加氢制1,4-丁二醇的流程图。
具体实施方式
26.下面通过一些实施例对本发明要求保护的技术方案作进一步说明。但是,实施例和对比例是用于解释本发明实施方案,并不超出本发明主题的范围,本发明保护范围不受所述实施例的限定。
27.以下实施例中,雷尼镍-铝-x催化剂的制备方法可参考公开号cn 102744083 a的专利文献。冷冻水撤热列管式反应器所装填催化剂的制备方法可参考公开号cn101306368a的专利文献。
28.除非另作特殊说明,本发明中所用材料、试剂均可从本领域商业化产品中获得。
29.实施例1本实施例中,低压反应器r1所用的雷尼镍-铝-x催化剂组成:镍铝质量比为0.5:1,x 的添加量为镍铝总质量的1wt%,其中所述的x为mg。制备过程如下:分别称取 250kg 的 ni 块,500kg 的 al 块以及 7.5kg 的mg置于中大型熔炉中,打开电流,待 ni、al及mg熔化之后,在 900℃保温熔炼 60min 之后,倒入水中冷却 ;冷却后得到的催化剂碾磨至 200 目的粉末 ;分批次称取适量的催化剂粉末分批次加入质量浓度为 25% 的naoh 溶液中混合均匀,随后控制温度在 60℃反应 30min,反应完毕之后,用蒸馏水洗涤 3次、再用无水乙醇洗涤至中性。
30.冷冻水撤热列管式反应器r2所装填的催化剂组成:镍含量11 wt%,促进剂mg含量1 wt%,其余为氧化铝。该催化剂按下述骤制备。取比表面为220 m2·
g-1
,孔容为0.7 cm3·
g-1
,平均孔径为12 nm的氧化铝载体88 kg,取10.6 kg六水合硝酸镁,配制成100 l溶液,将溶液浸渍到氧化铝载体中,静置30 min,后经120℃干燥12 h,500 ℃焙烧6 h后,得到含促进剂mg的载体。将上述载体经150℃抽真空处理10 min,后降至室温备用。称取29.7 kg六水合硝酸镍、21.3 kg四水合硝酸镍以及2 kg聚乙二醇,配制成100 l溶液,浸渍到上述含促进剂mg的载体上,静置20 min,滤去剩余溶液;经80 ℃干燥10 h后,250 ℃焙烧10 h,然后通入氢气450 ℃还原5 h,还原后的催化剂经氧气钝化,备用。
31.(1)经过加压至4.1mpa,40℃的30wt%的1,4丁炔二醇水溶液进入低压反应器r1,保持反应压力控制在4.1mpa,并保持反应温度为60℃,调节反应液体空速为1h-1
,加入氢气(99.99%)的压力为4.1 mpa,气体空速1.5 h-1
,进行第一步加氢;产物经过减压至0.4 mpa进入旋风分离器s1;旋风分离器s1底部分离出的雷尼镍-铝-x催化剂,顶部采出反应液,该反应液通过袋式过滤器s2进一步去除催化剂颗粒;从袋式过滤器s2分离出的催化剂和旋风分离器s1底部分离出的催化剂循环至低压反应器r1再次参加反应;(2)通过上述处理的反应液进入预分离塔t1,理论板数为5块,在15kpa,操作温度保持在75℃。反应液被切分,水、丁醇、轻组分从塔顶馏出,1,4-丁二醇、1,4-丁烯二醇、羟基丁醛及缩醛和重组分的混合水溶液从塔底出来;(3)从预分离塔t1顶部分离出的水、丁醇、轻组分进入下一分离工段提取副产品丁醇;(4)从预分离塔t1底部分离出的混合水溶液通过加压和高压加氢预热器e1预热后加热至120℃、升压至20 mpa,从顶部以滴流方式进入冷冻水撤热列管式反应器r2中,反应温度控制在140℃;反应压力控制在20mpa;空速0.5h-1
;进一步将少量的1,4-丁烯二醇、羟基丁醛及缩醛转化为1,4丁二醇,反应物从反应器r2底部采出。再经过蒸馏后得产品纯度为
99.6%,色度等于5ahpa的1,4-丁二醇产品。动力电消耗400 千瓦时/吨1,4-丁二醇,蒸汽消耗 4.1 吨/吨1,4-丁二醇,循环冷却水消耗 300 吨/吨1,4-丁二醇。
32.对比实施例1本实施例中,采用与实施例1相同的雷尼镍-铝-x催化剂用于低压反应器,以及 镍含量11 wt%,促进剂mg含量1 wt%,其余为氧化铝的高压加氢催化剂。采用现有的加氢工艺:(1)经过加压至4.1mpa,40℃的30wt%的1,4丁炔二醇水溶液进入低压加氢反应器,保持反应压力控制在4.1mpa,并保持反应温度为60℃,调节反应液体空速为1h-1
,加入氢气(99.99%)的压力为4.1 mpa,气体空速1.5 h-1
,进行第一步加氢;产物经过减压至0.4 mpa进入分离器,分离出的催化剂循环至低压反应器再次参加反应;(2)分离出的物料通过加压和高压加氢预热器预热后加热至120℃、升压至20 mpa,从顶部以滴流方式进入固定床反应器中,反应温度控制在140℃;反应压力控制在20mpa;空速0.5h-1
;进一步将少量的1,4-丁烯二醇、羟基丁醛及缩醛转化为1,4丁二醇,反应物从反应器底部采出。再经过蒸馏后得产品纯度为99.5%,色度等于5 ahpa的1,4-丁二醇产品。动力电消耗485 千瓦时/吨1,4-丁二醇,蒸汽消耗 5.3 吨/吨1,4-丁二醇,循环冷却水消耗 353 吨/吨1,4-丁二醇。
33.实施例2本实施例中,低压反应器r1所用的雷尼镍-铝-x催化剂组成:镍铝质量比为0.6:1,x 的添加量为镍铝总质量的1wt%,其中所述的x为mg。制备过程如下:分别称取 300kg 的 ni 块,500kg 的 al 块以及 8kg 的mg置于中大型熔炉中,打开电流,待 ni、al及mg熔化之后,在 900℃保温熔炼 60min 之后,倒入水中冷却;冷却后得到的催化剂碾磨至 200 目的粉末 ;分批次称取适量的催化剂粉末分批次加入质量浓度为25% 的naoh 溶液中混合均匀,随后控制温度在 60℃反应 30min,反应完毕之后,用蒸馏水洗涤 3次、再用无水乙醇洗涤至中性。
34.冷冻水撤热列管式反应器r2所装填的催化剂组成:镍含量13 wt%,促进剂la含量3 wt%,其余为氧化铝。该催化剂按下述步骤制备:取比表面为300 m2·
g-1
,孔容为1.1 cm3·
g-1
,平均孔径为17 nm的氧化铝载体84 kg,取9.4 kg六水合硝酸镧,配制成120 l溶液,将溶液浸渍到氧化铝载体中,静置20 min,后经110℃干燥10 h,400 ℃焙烧6 h后,得到含促进剂la的载体。将上述载体经150℃干燥10 h,后降至室温备用。称取39.6 kg六水合硝酸镍、17.0 kg四水合硝酸镍以及3kg ctab,配制成120 l溶液,浸渍到上述含促进剂la的载体上,静置30 min,滤去剩余溶液;经100 ℃干燥8 h后,450 ℃焙烧6 h,然后通入氢气400 ℃还原5 h,还原后的催化剂经液体保护,备用。
35.(1)经过加压至3.0mpa,40℃的35wt%的1,4丁炔二醇水溶液进入低压反应器r1,保持反应压力控制在3.0mpa,并保持反应温度为60℃,调节反应液体空速为2h-1
,加入氢气(99.99%)的压力为3 mpa,气体空速3 h-1
,进行第一步加氢;产物经过减压后至0.4mpa进入旋风分离器s1;旋风分离器s1底部分离出雷尼镍-铝-x催化剂,顶部采出反应液,该反应液通过袋式过滤器s2进一步去除催化剂颗粒;从袋式过滤器s2分离出的催化剂和旋风分离器s1底部分离出的催化剂循环至低压反应器r1再次参加反应;(2)通过上述处理的反应液进入预分离塔t1,理论板数为4;在20kpa,操作温度保持在70℃。反应液被切分,水、丁醇、轻组分从塔顶馏出,重组分、1,4-丁二醇、1,4-丁烯二
醇、羟基丁醛及缩醛的水溶液从塔底出来;(3)从预分离塔t1顶部分离出的水、丁醇、轻组分进入下一分离工段提取副产品丁醇;(4)从预分离塔t1底部分离出的溶液通过加压和高压加氢预热器e1预热后加热至120℃、升压至25mpa,从顶部以滴流方式进入冷冻水撤热列管式反应器r2中,反应温度控制在130℃;反应压力控制在25mpa;空速1.0h-1
;进一步将少量的1,4-丁烯二醇、羟基丁醛及缩醛转化为1,4丁二醇,反应物从反应器r2底部采出。再经过蒸馏后得产品纯度为99.7%,色度等于3ahpa的1,4-丁二醇产品。动力电消耗400 千瓦时/吨1,4-丁二醇,蒸汽消耗 4.1 吨/吨1,4-丁二醇,循环冷却水消耗 300 吨/吨1,4-丁二醇。
36.实施例3本实施例中,低压反应器r1所用的雷尼镍-铝-x催化剂组成:镍铝质量比为0.7:1,x 的添加量为镍铝总质量的1wt%,其中所述的x为mg。制作过程如下:分别称取 350kg 的 ni 块,500kg 的 al 块以及 8.5kg 的mg置于中大型熔炉中,打开电流,待 ni、al及mg熔化之后,在 900℃保温熔炼 60min 之后,倒入水中冷却 ;冷却后得到的催化剂碾磨至 200 目的粉末 ;分批次称取适量的催化剂粉末分批次加入质量浓度为 25% 的naoh 溶液中混合均匀,随后控制温度在 60℃反应 30min,反应完毕之后,用蒸馏水洗涤 3次、再用无水乙醇洗涤至中性;冷冻水撤热列管式反应器r2所装填的催化剂组成:镍含量19 wt%,促进剂cu含量5 wt%,其余为氧化铝。该催化剂按下述步骤制备:取比表面为150 m2·
g-1
,孔容为1.3 cm3·
g-1
,平均孔径为20 nm的氧化铝载体76 kg,取19.0 kg三水合硝酸铜,配制成100 l溶液,将溶液浸渍到氧化铝载体中,静置30 min,后经110℃干燥10 h,400 ℃焙烧6 h后,得到含促进剂cu的载体。将上述载体经150℃干燥10 h,后降至室温备用。称取49.5 kg六水合硝酸镍、38.1 kg四水合硝酸镍以及2 kg ctab,配制成130 l溶液,浸渍到上述含促进剂cu的载体上,静置30 min,滤去剩余溶液;经100 ℃干燥8 h后,450 ℃焙烧6 h,然后通入氢气400 ℃还原5 h,还原后的催化剂经液体保护,备用。
37.(1)经过加压至2.5mpa,40℃的35wt%的1,4-丁炔二醇水溶液进入低压反应器r1,保持反应压力控制在2.5mpa,并保持反应温度为60℃,调节反应液体空速为3h-1
,加入氢气(99.99%)的压力为2.5 mpa,气体空速4 h-1
,进行第一步加氢;产物经过减压后至0.4 mpa进入旋风分离器s1;旋风分离器s1底部分离出的雷尼-镍催化剂,顶部采出反应液,该反应液通过袋式过滤器s2进一步去除催化剂颗粒;从袋式过滤器s2分离出的催化剂和旋风分离器s1底部分离出的催化剂循环至低压反应器r1再次参加反应;(2)通过上述处理的反应液进入预分离塔t1,理论板数为4;在20kpa,操作温度保持在70℃。反应液被切分,水、丁醇、轻组分从塔顶馏出,重组分、1,4-丁二醇、1,4-丁烯二醇、羟基丁醛及缩醛的水溶液从塔底出来;(3)从预分离塔t1顶部分离出的水、丁醇、轻组分进入下一分离工段提取副产品丁醇;(4)从预分离塔t1底部分离出的溶液通过加压和高压加氢预热器e1预热后加热至110℃、升压至25 mpa,从顶部以滴流方式进入冷冻水撤热列管式反应器r2中,反应温度控制在120℃;反应压力控制在25mpa;空速1.5h-1
;进一步将少量的1,4-丁烯二醇、羟基丁醛及
wt%,其余为氧化铝。该催化剂按下述步骤制备:取比表面为150 m2·
g-1
,孔容为1.3 cm3·
g-1
,平均孔径为20 nm的氧化铝载体72 kg,取22.8 kg三水合硝酸铜,配制成100 l溶液,将溶液浸渍到氧化铝载体中,静置30 min,后经110℃干燥10 h,400 ℃焙烧6 h后,得到含促进剂cu的载体。将上述载体经150℃干燥10 h,后降至室温备用。称取74.3 kg六水合硝酸镍、29.7 kg四水合硝酸镍以及2 kg ctab,配制成130 l溶液,浸渍到上述含促进剂cu的载体上,静置30 min,滤去剩余溶液;经100 ℃干燥8 h后,450 ℃焙烧6 h,然后通入氢气400 ℃还原5 h,还原后的催化剂经液体保护,备用。
43.(1)经过加压至2.0mpa,40℃的40wt%的1,4-丁炔二醇水溶液进入低压反应器r1,保持反应压力控制在2.0mpa,并保持反应温度为60℃,调节反应液体空速为4h-1
,加入氢气(99.99%)的压力为2.0 mpa,气体空速11 h-1
,进行第一步加氢;产物经过减压后至0.4 mpa进入旋风分离器s1;旋风分离器s1底部分离出的雷尼-镍催化剂,顶部采出反应液,该反应液通过袋式过滤器s2进一步去除催化剂颗粒;从袋式过滤器s2分离出的催化剂和旋风分离器s1底部分离出的催化剂循环至低压反应器r1再次参加反应;(2)通过上述处理的反应液进入预分离塔t1,理论板数为5;在15kpa,操作温度保持在75℃。反应液被切分,水、丁醇、轻组分从塔顶馏出,重组分、1,4-丁二醇、1,4-丁烯二醇、羟基丁醛及缩醛的水溶液从塔底出来;(3)从预分离塔t1顶部分离出的水、丁醇、轻组分进入下一分离工段提取副产品丁醇;(4)从预分离塔t1底部分离出的溶液通过加压和高压加氢预热器e1预热后加热至140℃、升压至30 mpa,从顶部以滴流方式进入冷冻水撤热列管式反应器r2中,反应温度控制在140℃;反应压力控制在30mpa;空速0.5h-1
;进一步将少量的1,4-丁烯二醇、羟基丁醛及缩醛转化为1,4丁二醇,反应物从反应器底r2部采出。再经过蒸馏后得产品纯度为99.7%,色度等于2ahpa的1,4-丁二醇产品。动力电消耗420 千瓦时/吨1,4-丁二醇,蒸汽消耗 4.5 吨/吨1,4-丁二醇,循环冷却水消耗 320 吨/吨1,4-丁二醇。