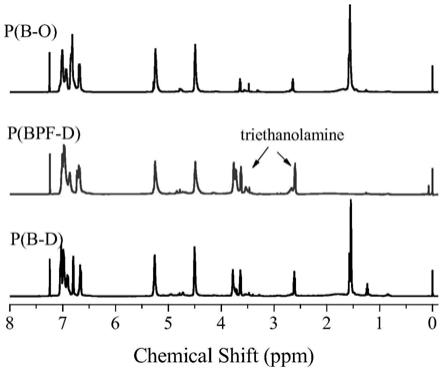
1.本发明涉及一种主链型苯并噁嗪的合成方法,具体涉及一种以二元酚、二元胺和多聚甲醛为原料,在以极性氯代烃为主溶剂,以醇胺为辅助溶剂的混合溶剂中高产率合成具有较高分子量的主链型苯并噁嗪的方法,属于有机合成技术领域。
背景技术:2.主链含有苯并噁嗪环的聚合物(主链型苯并噁嗪)具有低分子量苯并恶嗪典型特性,其固化交联物具有高耐热性、良好的机械强度和低介电常数等优异性能。而且,独特的薄膜加工能力,更好的韧性和柔韧性使这些聚合物适合作为绝缘体、涂料和模塑材料的工业应用。
3.主链型苯并噁嗪的合成可通过sonogashira、suzuki、click等将含有苯并噁嗪环的单体聚合,但从反应的经济性出发,采用便宜的二元胺、二元酚和多聚甲醛,在一定溶剂中通过mannich-type polycondensation合成。但溶剂体系在该反应中影响很大,如果单独以甲苯、二甲苯、二氧六环做溶剂,由于二胺形成三嗪发生交联形成凝胶;以chcl3为溶剂可以得到聚合物,但可能由于chcl3极性大,反应时间过长可导致噁嗪环开环交联;乙醇作为辅助溶剂加入主溶剂甲苯形成混合溶剂,可以通过乙醇的溶剂化效应阻碍三嗪的生成而防止凝胶,然而从报道的数据来看,所得主链型苯并噁嗪的数均分子量(mn)均在4000~5000较小范围,同样在甲醇中沉析得到的固体产品产率也偏低,而且容易在放置过程中发黄。
技术实现要素:4.针对上述现有技术的不足,本发明的目的是在于提供一种合成主链型苯并噁嗪方法,该方法不但能够有效解决主链型苯并噁嗪合成过程中容易出现凝胶的技术问题,而且可以获得较高分子量的主链型苯并噁嗪以及提高主链型苯并噁嗪的产率。
5.为了实现上述技术目的,本发明提供了一种主链型苯并噁嗪的合成方法,该方法是将二元酚、二元芳基胺和多聚甲醛溶于溶剂中,进行缩合反应,即得;所述溶剂包括极性氯代烃和醇胺类化合物。
6.本发明技术方案的关键是在于采用了特殊的组合溶剂来实现高分子量主链型苯并噁嗪的合成以及提高其产率,解决现有主链型苯并噁嗪合成过程中容易出现凝胶的技术问题。本发明技术方案采用的组合溶剂中极性氯代烃作为主溶剂是反应的良性溶剂,能够很好地实现二元酚和二元芳基胺原料的溶解分散,同时极性卤代烃对主链型苯并噁嗪溶解分散性较好,能使其主链充分舒展,有利于聚合链的增长过程,从而提高反应效率和单体转化率,但是采用单一的极性卤代烃仍然难以获得高分子量的主链型苯并噁嗪,主要是基于二元芳基胺中的氨基容易与甲醛之间发生副反应形成三嗪而导致的凝胶现象,且噁嗪容易发生开环,从而导致难以获得高分子量主链型苯并噁嗪,而通过引入醇胺类化合物作为辅助溶剂,其同时具有较好的醇类的溶剂化效应和三乙胺的碱性,不但能够利用其溶剂化效应来提高反应效率,而且利用其碱性加快多聚甲醛分解,提高聚合反应速度、减缓噁嗪环开
环,减少副反应发生,从而提高主链型苯并噁嗪的分子量。
7.作为一个优选的方案,所述氯代烃为三氯甲烷。
8.作为一个优选的方案,所述醇胺类化合物为三乙醇胺、四乙醇甲二胺、四乙醇乙二胺、四乙醇丙二胺中至少一种。醇胺类化合物的具体结构如下:
[0009][0010]
作为一个优选的方案,所述溶剂由氯代烃和醇胺类化合物按照体积比1~6:1组成。进一步优选,所述溶剂由氯代烃和醇胺类化合物按照体积比2~4:1组成。如果醇胺类化合物比例过少,则难以有效抑制二元芳基胺与甲醛之间的副反应易于形成三嗪而导致的凝胶现象,如果醇胺类化合物比例过高则混合溶剂的溶解性下降,易于出现沉淀。
[0011]
作为一个优选的方案,所述二元酚具有以下结构:
[0012][0013]
其中,m为o、-ch
2-或-c(ch3)
2-。
[0014]
作为一个优选的方案,所述二元芳基胺具有以下结构:
[0015][0016]
其中,x为o、-ch
2-或-so
2-。
[0017]
作为一个优选的方案,二元酚、二元芳基胺和多聚甲醛的摩尔比为1:1:4~4.8。最优选的摩尔比为1:1:4.8。
[0018]
作为一个优选的方案,所述主链型苯并噁嗪具有以下结构:
[0019][0020]
其中,
[0021]
m为o、-ch
2-或-c(ch3)
2-;
[0022]
x为o、-ch
2-或-so
2-;
[0023]
n为聚合度(更具体来说n的大小控制其数均分子量在7000~20000以内)。
[0024]
作为一个优选的方案,所述反应的条件为:在温度40~120℃下反应9~48h。进一步优选反应的条件为:在温度70~90℃下反应9~24h。
[0025]
本发明的主链型苯并噁嗪的合成路线如下:
[0026][0027]
相对现有技术,本发明的技术方案的显著优点:
[0028]
1、本发明技术方案通过采用极性氯代烃和醇胺类化合物组合溶剂,能够有效抑制氨基与甲醛之间形成三嗪的副反应,减少凝胶现象。
[0029]
2、本发明技术方案通过主溶剂极性氯代烃和辅助溶剂醇胺类化合物的极性和弱碱性,促进多聚甲醛的分解,促进mannich反应和噁嗪环成环反应,减少副反应发生,从而提高了分子量。
[0030]
3、本发明技术方案通过采用特殊的组合溶剂可以提高单体转化率,降低副反应,提高聚合物分子量,从而提高醇析固体产物的收率。
[0031]
4、本发明技术方案的噁嗪环成环率高、分子量高,使残余的酚羟基和氨基少,产品稳定性好,保存周期长。
附图说明
[0032]
图1为主链型苯并噁嗪的核磁氢谱图;p(b-d):由双酚a、4,4
’‑
二氨基二苯甲烷(ddm)和多聚甲醛合成(实施例4);p(bpf-d):由4,4
’‑
二羟基二苯甲烷(双酚f)、ddm和多聚甲醛合成(实施例5);p(b-o):由双酚a、4,4
’‑
二氨基二苯醚(oda)和多聚甲醛合成(实施例6)。
[0033]
图2为主链型苯并噁嗪的红外光谱图;p(b-d):由双酚a、4,4
’‑
二氨基二苯甲烷(ddm)和多聚甲醛合成(实施例4);p(bpf-d):由4,4
’‑
二羟基二苯甲烷(双酚f)、ddm和多聚甲醛合成(实施例5);p(b-o):由双酚a、4,4
’‑
二氨基二苯醚(oda)和多聚甲醛合成(实施例6)。
[0034]
图3为主链型苯并噁嗪的gpc图;p(b-d):由双酚a、4,4
’‑
二氨基二苯甲烷(ddm)和多聚甲醛合成(实施例4);p(bpf-d):由4,4
’‑
二羟基二苯甲烷(双酚f)、ddm和多聚甲醛合成(实施例5);p(b-o):由双酚a、4,4
’‑
二氨基二苯醚(oda)和多聚甲醛合成(实施例6)。
[0035]
图4为主链型苯并噁嗪的产品稳定性对比;(在空气中放置6个月;左图:chcl3作为溶剂得到的产品(比较例1);中图:toluene/ethanol作为溶剂得到的产品(比较例2);右图:chcl3/triethanolamine作为溶剂得到的产品(实施例4);采用chcl3/triethanolamine作为溶剂反应充分,聚合物中酚羟基含量少,而酚羟基残留多则容易被氧化,因此稳定性差。
具体实施方式
[0036]
下面将结合本发明实施例中的附图,对本发明实施例中的技术方案进行清楚、完整地描述,显然,所描述的实施例仅仅是本发明一部分实施例,而不是全部的实施例。基于本发明中的实施例,本领域普通技术人员在没有作出创造性劳动前提下所获得的所有其它
实施例,都属于本发明保护的范围。
[0037]
实施例1
[0038]
将9.91g ddm和11.40g双酚a及6.0g多聚甲醛加入10ml的三乙醇胺和60ml chcl3中,升温至80℃下搅拌反应,9h后冷却,得到主链型苯并噁嗪溶液。将溶液逐滴加入100ml甲醇中沉析,过滤后干燥,得白色主链型苯并噁嗪固体p1(22.81g,产率93.1%,mn为7306)。
[0039]
实施例2
[0040]
将9.91g ddm和11.40g双酚a及6.0g多聚甲醛加入15ml的三乙醇胺和60ml chcl3中,升温至80℃下搅拌反应,9h后冷却,得到主链型苯并噁嗪溶液。将溶液逐滴加入100ml甲醇中沉析,过滤后干燥,得白色主链型苯并噁嗪固体p2(23.08g,产率94.2%,mn为8560)。
[0041]
实施例3
[0042]
将9.91g ddm和11.40g双酚a及6.0g多聚甲醛加入20ml的三乙醇胺和60ml chcl3中,升温至80℃下搅拌反应,9h后冷却,得到主链型苯并噁嗪溶液。将溶液逐滴加入100ml甲醇中沉析,过滤后干燥,得白色主链型苯并噁嗪固体p3(23.64g,产率96.5%,mn为7779)。
[0043]
实施例4
[0044]
将9.91g ddm和11.40g双酚a及7.20g多聚甲醛加入15ml的三乙醇胺和60ml chcl3中,升温至80℃下搅拌反应,24h后冷却,得到主链型苯并噁嗪溶液。将溶液逐滴加入100ml甲醇中沉析,过滤后干燥,得白色主链型苯并噁嗪固体p4(23.79g,产率97.0%,mn为10025)。
[0045]
实施例5
[0046]
将9.91g ddm和10.01g bpf及7.20g多聚甲醛加入15ml的三乙醇胺和60ml chcl3中,升温至80℃下搅拌反应,24h后冷却,得到主链型苯并噁嗪溶液。将溶液逐滴加入100ml甲醇中沉析,过滤后干燥,得白色主链型苯并噁嗪固体p6(22.20g,产率96.1%,mn为9440)。
[0047]
实施例6
[0048]
将10.01g oda和11.40g双酚a及7.20g多聚甲醛加入15ml的三乙醇胺和60ml chcl3中,升温至80℃下搅拌反应,24h后冷却,得到主链型苯并噁嗪溶液。将溶液逐滴加入100ml甲醇中沉析,过滤后干燥,得白色主链型苯并噁嗪固体p5(22.19g,产率90.2%,mn为10526)。
[0049]
实施例7
[0050]
将10.01g oda和11.40g双酚a及7.20g多聚甲醛加入15ml的三乙醇胺和60ml chcl3中,升温至70℃下搅拌反应,24h后冷却,得到主链型苯并噁嗪溶液。将溶液逐滴加入100ml甲醇中沉析,过滤后干燥,得白色主链型苯并噁嗪固体p7(21.77g,产率88.5%,mn为8572)。
[0051]
实施例8
[0052]
将10.01g oda和11.40g双酚a及7.20g多聚甲醛加入15ml的三乙醇胺和60ml chcl3中,升温至100℃下搅拌反应,24h后冷却,得到主链型苯并噁嗪溶液。将溶液逐滴加入100ml甲醇中沉析,过滤后干燥,得白色主链型苯并噁嗪固体p8(21.23g,产率86.3%,mn为8774)。
[0053]
对比实施例1
[0054]
将9.91g ddm和11.40g双酚a及7.20g多聚甲醛加入60ml chcl3中,升温至80℃下
搅拌反应,9h后冷却(延长时间会凝胶),得到主链型苯并噁嗪溶液。将溶液逐滴加入100ml甲醇中沉析,得到粘稠物,干燥后得黄色主链型苯并噁嗪固体p7(13.29g,产率54.2%,mn为5840)。
[0055]
对比实施例2
[0056]
将9.91g ddm和11.40g双酚a及7.20g多聚甲醛加入15ml的乙醇和60ml chcl3中,升温至80℃下搅拌反应,24h后冷却,得到主链型苯并噁嗪溶液。将溶液逐滴加入100ml甲醇中沉析,过滤后干燥,得白色主链型苯并噁嗪固体p8(15.97g,产率65.2%,mn为8490)。
[0057]
与实施例4~6相比,对比实施例2制备的聚合物分子量更小,收率更低。
[0058]
对比实施例3
[0059]
将9.91g ddm和11.40g双酚a及7.20g多聚甲醛加入34ml的乙醇和66ml甲苯中,升温至80℃下搅拌反应,24h后冷却,得到主链型苯并噁嗪溶液。将溶液逐滴加入100ml甲醇中沉析,过滤后干燥,得白色主链型苯并噁嗪固体p9(16.55g,产率67.5%,mn为4239)。