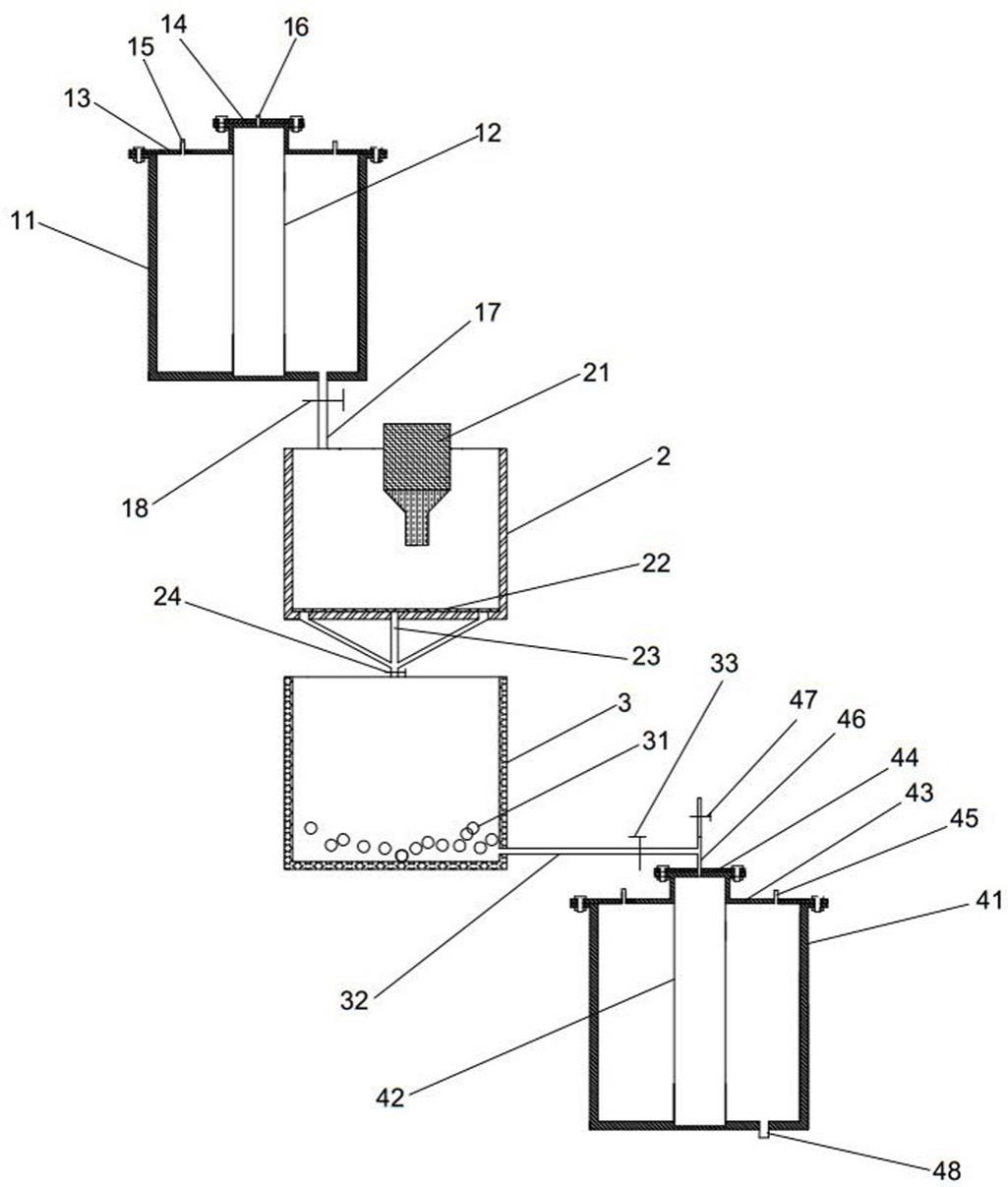
1.本发明属于微生物发酵生物制氢技术领域,具体涉及一种同步糖化暗-光联合生物发酵制氢方法及系统。
背景技术:2.氢能是一种高热值、燃烧清洁的绿色能源。在制氢的方法中,微生物发酵产氢技术由于整个过程反应条件温和(在常温常压下即可进行),发酵原料来源广(富含碳水化合物的农业废弃物,畜禽粪便、城市生活垃圾等均可以作为发酵原料)等特点,在可再生能源领域得到了广泛的研究。以农业废弃物为原料进行生物厌氧发酵产氢从而将氢能的生产和废弃物的处理相结合,实现双重目标是现行发酵产氢研究的热点。
3.生物制氢可以分为暗发酵生物制氢和光合发酵生物制氢,其中暗发酵生物制氢是在无光源的状态下利用有机物进行代谢产氢,但是在产气的过程中会伴随着一些副产物的产生,如挥发性脂肪酸、乙醇等,这些副产物不能被暗发酵细菌利用,最终残留在发酵液中造成整个发酵系统底物转化效率低。
4.光合细菌在光照的情况下可以以挥发性脂肪酸为碳源进行发酵并释放出氢气,从而分解暗发酵的副产物,通过暗-光联合生物制氢技术可以显著提高底物的转化效率。但是暗发酵结束的尾液中除了含有一些挥发性脂肪酸外,还有高浓度的氨根离子以及残留的暗发酵菌株,若直接加入到光合发酵产氢装置中,高浓度的氨根离子会导致光合细菌固氮酶的活性降低,最终造成光合细菌代谢活动不旺盛,同时残留的暗发酵菌也会以残留的小分子酸为碳源进行生长代谢使光合细菌利用的碳源减少。所以,如何使暗-光发酵两个阶段的有效衔接是目前的研究的热点。
5.另外,需要考虑的是在暗发酵产氢过程中为了维持酶水解环境以及发酵环境的缓冲能力,需要加入柠檬酸-柠檬酸钠缓冲液,而在光合发酵产氢过程中为了维持酶水解环境以及发酵环境的缓冲能力,需要加入柠檬酸-柠檬酸钠缓冲液,如果能使暗发酵产氢的尾液作为光合发酵产氢碳源的同时也能作为光发酵产氢阶段的缓冲液来维持光合发酵产氢过程的缓冲性能,将实现提高底物的转化率的同时减少化学试剂的用量的目的,进而降低成本。
6.基于此,本技术通过设计一种暗-光联合生物制氢系统,在以农业秸秆为原料进行产氢,首先进行酶解预处理,在纤维素酶的作用下,纤维素被分解成糖类等碳水化合物,然后使用得到的酶解液进行产氢实验,并且把酶水解和产氢发酵耦合于同一个装置,避免了在酶解过程中糖类的累积抑制纤维酶的活性,造成底物水解不彻底的现象,另外,纤维素生物质在被水解成糖的同时糖也被产氢菌消耗,促进了酶水解的正向进行,同时减少了反应器的数量,降低了成本,从而提高产氢效率。
技术实现要素:7.本发明提供一种同步糖化暗-光联合生物发酵制氢方法及系统,通过在产氢过程
中,以农业秸秆为原料进行产氢,并把酶水解和产氢发酵耦合于同一个装置,避免了在酶解过程中糖类的累积抑制纤维酶的活性,造成底物水解不彻底的现象,从而提高产氢效率,同时减少了柠檬酸钠等试剂的用量。
8.基于上述目的,本发明采取如下技术方案:一种同步糖化暗-光联合生物发酵制氢系统,包括同步糖化暗发酵产氢装置、暗发酵细菌细胞粉碎和过滤装置、氨根吸附装置和同步糖化光合产氢发酵装置;所述同步糖化暗发酵产氢装置包括第一外壳体以及设置于第一外壳体内的第一内壳体;第一外壳体顶端设有第一顶盖,第一顶盖与第一外壳体可拆卸连接;第一顶盖中间设有向上延伸的第一通道,第一通道顶端开口,且第一通道顶端开口处设有与第一通道可拆卸连接的第二顶盖;第一顶盖上设有第一通气管,通过第一通气管实现第一顶盖内外的贯通;第二顶盖上设有第二通气管,通过第二通气管实现第二顶盖内外的贯通;第一内壳体的底端与第一外壳体底壁相顶接,第一内壳体的顶端向上延伸,并伸入第一通道内,并且与第二顶盖相顶接,第一内壳体顶端伸入第一通道内的侧壁紧贴第一通道的内壁;第一外壳体的底端设有第一出液管,第一出液管的出口端与暗发酵细菌细胞粉碎和过滤装置的顶端相连通;所述同步糖化暗发酵产氢装置的材质为非透明材质,在同步糖化暗发酵产氢装置中进行暗发酵产氢的时候,能够防止光线进入,形成暗发酵条件;第一内壳体的侧壁由微米级的第一滤网构成;暗发酵细菌细胞粉碎和过滤装置内设有超声细胞粉碎机暗发酵细菌细胞粉碎和过滤装置的底端还设有第二出液管,第二出液管的出口端与氨根吸附装置的顶端相连通;氨根吸附装置内底部设有沸石,氨根吸附装置的底端还设有第三出液管;同步糖化光合产氢发酵装置包括第二外壳体以及设置于第二外壳体内的第二内壳体;第二外壳体顶端设有第三顶盖,第三顶盖与第二外壳体可拆卸连接;第三顶盖中间设有向上延伸的第二通道,第二通道顶端开口,且第二通道顶端开口处设有与第二通道可拆卸连接的第四顶盖;第三顶盖上设有第三通气管,通过第三通气管实现第三顶盖内外的贯通;第二内壳体的底端与第二外壳体底壁相顶接,第二内壳体的顶端向上延伸,并伸入第二通道内,并且与第四顶盖相顶接,第二内壳体顶端伸入第二通道内的侧壁紧贴第二通道的内壁;第四顶盖上设有第四通气管,通过第四通气管实现第四顶盖内外的贯通,第三出液管的出口端与第四通气管的侧壁相连通;第二外壳体的底端设有第四出液管;所述同步糖化光合产氢发酵装置的材质为透明材质,可以透过光线,实现光发酵;第二内壳体的侧壁由微米级的第二滤网构成。
9.进一步的,第一顶盖和第一外壳体的侧壁上均设有螺纹通孔,通过在螺纹通孔中穿设螺栓,实现第一顶盖与第一外壳体的可拆卸连接。
10.进一步的,第二顶盖和第一通道的侧壁上均设有螺纹通孔,通过在螺纹通孔中穿设螺栓,实现第二顶盖与第一通道的可拆卸连接。
11.进一步的,所述第一内壳体为圆筒状。
0.1 g/l,ch3coona 2.0 g/l,k2hpo
4 1.5 g/l,酵母膏1.0 g/l。
22.步骤1)中生物质原料的添加量(即底物浓度,又称有机负荷)为20-35g/l(添加适量的底物能够促进反应进行,过多导致发酵液酸化抑制产氢,过少会阻碍产氢的进行);步骤1)中以加入的生物质原料、纤维素酶、柠檬酸-柠檬酸钠缓冲液、暗发酵细菌和产氢培养基作为暗发酵液,加入的柠檬酸-柠檬酸钠缓冲液体积占暗发酵液总体积的50-60%;步骤1)中加入的纤维素酶添加量(酶负荷)为120-150mg/g生物质原料;步骤1)中加入的暗发酵细菌体积具体为30-40 ml;具体的,产氢培养基添加量为40-45 ml。
23.具体的,步骤2)中,暗发酵液和沸石31的比例为2:1(v/w),吸附时间2h,吸附后暗发酵液的氨根浓度为2.12
±
0.32 mm。
24.具体的,步骤3)的光发酵生物制氢反应过程中,发酵底物为经过60目筛选的生物质原料和暗发酵液,底物浓度为35mg/ml,纤维素酶(绿色木霉)的添加量(酶负荷)为150mg/g生物质原料。
25.具体的,步骤3)的光发酵生物制氢反应过程中,通过采用暗发酵液代替部分柠檬酸-柠檬酸钠缓冲液,来减少产氢过程中柠檬酸-柠檬酸钠缓冲液的用量,其中暗发酵液与柠檬酸-柠檬酸钠缓冲液的体积比为1:2。
26.具体的,步骤3)光发酵制氢时所用菌种为光合细菌hau-m1,主要由深红红螺菌 (r.hodospirillum rubrum) 、荚膜红假单胞菌 (r.capsulata) 、沼泽红假单胞菌(r.pulastris) 、类球红细菌(r.hodobacter sphaeroides) 、荚膜红细菌(rhodobacter capsulatus)组成。
27.步骤3)中以加入的柠檬酸-柠檬酸钠缓冲液、生物质原料、纤维素酶、光合细菌hau-m1、产氢培养基和暗发酵液作为光发酵液,光合细菌hau-m1和光发酵液的体积比为1:5;步骤3)中加入的暗发酵液与柠檬酸-柠檬酸钠缓冲液体积比为1:(1~3);步骤3)中加入的纤维素酶添加量(酶负荷)为120-150mg/g生物质原料;步骤3)中加入的光合细菌hau-m1体积为30-40 ml;步骤3)中加入的产氢培养基为40-44ml。
28.具体的,步骤3)光发酵制氢过程中使用到的光发酵产氢培养基的组成为: nh4cl 0.4g/l;mgcl
2 0.2g/l;酵母膏0.1g/l;k2hpo
4 0.5g/l;nacl 2g/l;谷氨酸钠3.56g/l。
29.具体的,步骤1)中和步骤3)中的生物质原料为芦竹、玉米秸秆或者小麦秸秆。
30.具体的,柠檬酸-柠檬酸钠缓冲液的ph为4.8。
31.与现有技术相比,本技术的优势在于:1、利用本发明所述同步糖化暗-光联合生物发酵制氢系统进行的同步糖化暗-光联合发酵制氢工艺,通过在产氢过程中,以农业秸秆为原料进行产氢,把酶水解和产氢发酵耦合于同一个装置,避免了在酶解过程中糖类的累积抑制纤维酶的活性,造成底物水解不彻底的现象。
32.2、采用同步糖化技术显著提高了暗发酵产氢过程的产氢量,在光合产氢阶段,酶解单元添加暗发酵液的实验组产氢量显著高于未添加暗发酵液的实验组,在光合产氢酶解
单元加入一定量暗发酵液来替代部分缓冲液能够保证酶解的有效进行的同时也保证光合产氢过程的缓冲性能,这种联合方式有效减少了柠檬酸钠试剂的用量。
33.3、在本发明的工艺中,纤维素生物质在被水解成糖的同时糖也被产氢菌消耗,促进了酶水解的正向进行,同时减少了反应器的数量,降低了成本,从而提高产氢效率。
附图说明
34.图1是实施例1所述同步糖化暗-光联合生物发酵制氢系统的结构图;图2为产氢过程发酵液ph变化图,对照组为光发酵时只添加柠檬酸-柠檬酸钠缓冲液;图3为产氢效果图,对照组为光发酵时只添加柠檬酸-柠檬酸钠缓冲液。
具体实施方式
35.为使本发明的上述目的、特征和优点能够更加明显易懂,下面结合附图对本发明的具体实施方式做详细的说明。在下面的描述中阐述了很多具体细节以便于充分理解本发明。但是本发明能够以很多不同于在此描述的其他方式来实施,本领域技术人员可以在不违背本发明内涵的情况下做类似改进,因此本发明不受下面公开的具体实施的限制。
36.实施例1如图1所示,一种同步糖化暗-光联合生物发酵制氢系统,包括同步糖化暗发酵产氢装置、暗发酵细菌细胞粉碎和过滤装置2、氨根吸附装置3、同步糖化光合产氢发酵装置;所述同步糖化暗发酵产氢装置包括第一外壳体11以及设置于第一外壳体11内的第一内壳体12;第一外壳体11顶端设有第一顶盖13,第一顶盖13与第一外壳体11可拆卸连接,具体的,本实施例中,第一顶盖13和第一外壳体11的侧壁上均设有螺纹通孔,通过在螺纹通孔中穿设螺栓,实现第一顶盖13与第一外壳体11的可拆卸连接;第一顶盖13中间设有向上延伸的第一通道,第一通道顶端开口,且第一通道顶端开口处设有与第一通道可拆卸连接的第二顶盖14,具体的,本实施例中,第二顶盖14和第一通道的侧壁上均设有螺纹通孔,通过在螺纹通孔中穿设螺栓,实现第二顶盖14与第一通道的可拆卸连接;第一顶盖13上设有第一通气管15,通过第一通气管15实现第一顶盖13内外的贯通,具体的,本实施例中第一通气管15设有两根,两根第一通气管15分别位于第一通道的左侧和右侧;第二顶盖14上设有第二通气管16,通过第二通气管16实现第二顶盖14内外的贯通。
37.所述第一内壳体12为圆筒状,第一内壳体12的底端与第一外壳体11底壁相顶接,第一内壳体12的顶端向上延伸,并伸入第一通道内,并且与第二顶盖14相顶接,第一内壳体12顶端伸入第一通道内的侧壁紧贴第一通道的内壁;第一外壳体11的底端设有第一出液管17,第一出液管17的出口端与暗发酵细菌细胞粉碎和过滤装置2的顶端相连通,第一出液管17上设有第一阀门18。
38.所述同步糖化暗发酵产氢装置的材质为非透明材质,在同步糖化暗发酵产氢装置中进行暗发酵产氢的时候,能够防止光线进入,形成暗发酵条件。
39.所述第一外壳体11作为暗发酵产氢的发酵单元,第一内壳体12作为暗发酵产氢的酶解单元;其中,第一内壳体12的侧壁由微米级的第一滤网构成;进行暗发酵产氢时,打开第二顶盖14,在第一内壳体12内加入经过60目筛选的秸秆粉末、纤维素酶和柠檬酸-柠檬酸钠缓冲液;然后打开第一顶盖13,在第一外壳体11内加入暗发酵细菌发酵液和产氢培养基,暗发酵采用的菌为富集后的厌氧产氢混合菌,暗发酵的发酵液ph为5.5,发酵温度为45℃。
40.在暗发酵的过程中纤维素酶水解秸秆得到的糖类有机物,通过微米级的第一滤网渗入到第一外壳体11(暗发酵产氢的发酵单元)进而被暗发酵细菌利用,糖的不断消耗促进了酶水解的正向进行,提高了底物(秸秆)的酶水解效率。
41.暗发酵细菌细胞粉碎和过滤装置2内设有超声细胞粉碎机21,暗发酵细菌细胞粉碎和过滤装置2的底板上设有微孔吸附棉22;暗发酵细菌细胞粉碎和过滤装置2的底端还设有第二出液管23,第二出液管23的出口端与氨根吸附装置3的顶端相连通;进一步优选的,本实施例中暗发酵细菌细胞粉碎和过滤装置2的底端还设有两根旁路出液管,两根旁路出液管均与第二出液管23相连通,第二出液管23上设有第二阀门24。
42.氨根吸附装置3内底部设有沸石31,氨根吸附装置3的底端还设有第三出液管32,第三出液管32上设有第三阀门33。
43.同步糖化光合产氢发酵装置包括第二外壳体41以及设置于第二外壳体41内的第二内壳体42;第二外壳体41顶端设有第三顶盖43,第三顶盖43与第二外壳体41可拆卸连接,具体的,本实施例中,第三顶盖43和第二外壳体41的侧壁上均设有螺纹通孔,通过在螺纹通孔中穿设螺栓,实现第三顶盖43与第二外壳体41的可拆卸连接;第三顶盖43中间设有向上延伸的第二通道,第二通道顶端开口,且第二通道顶端开口处设有与第二通道可拆卸连接的第四顶盖44,具体的,本实施例中,第四顶盖44和第二通道的侧壁上均设有螺纹通孔,通过在螺纹通孔中穿设螺栓,实现第四顶盖44与第二通道的可拆卸连接;第三顶盖43上设有第三通气管45,通过第三通气管45实现第三顶盖43内外的贯通,具体的,本实施例中第三通气管45设有两根,两根第三通气管45分别位于第二通道的左侧和右侧。
44.所述第二内壳体42为圆筒状,第二内壳体42的底端与第二外壳体41底壁相顶接,第二内壳体42的顶端向上延伸,并伸入第二通道内,并且与第四顶盖44相顶接,第二内壳体42顶端伸入第二通道内的侧壁紧贴第二通道的内壁;第四顶盖44上设有第四通气管46,通过第四通气管46实现第四顶盖44内外的贯通,第三出液管32的出口端与第四通气管46的侧壁相连通,第四通气管46与第三出液管32的连接处至第四通气管46顶端开口处还设有第四阀门47;第二外壳体41的底端设有第四出液管48。
45.所述同步糖化光合产氢发酵装置12的材质为透明材质,可以透过光线,实现光发酵。
46.所述第二外壳体41作为光发酵产氢的发酵单元,第二内壳体12作为光发酵产氢的酶解单元;其中,第二内壳体12的侧壁由微米级的第二滤网构成,进行光发酵产氢时,打开
第二顶盖14,将吸附后的暗发酵液与柠檬酸-柠檬酸钠缓冲液、经过60目筛选的秸秆粉末、纤维素酶加入到第二内壳体12中进行再次酶解,打开第三顶盖43,在第二外壳体41中加入产氢培养基和光合产氢菌hau-m1,经过再次酶解的酶解液通过微米级的第二滤网渗入到第二外壳体41,进而被光合产氢菌hau-m1利用,进行光发酵生物制氢反应。
47.实施例2利用实施例1所述所述同步糖化暗-光联合生物发酵制氢系统进行的暗-光联合发酵制氢工艺,具体步骤如下:1)暗发酵产氢过程:首先采用同步糖化暗发酵产氢装置进行暗发酵产氢,先打开第二顶盖14,在第一内壳体12内加入经过60目筛选的玉米秸秆粉末5 g、纤维素酶(绿色木霉,酶活10fpu/mg)0.75g和ph为4.8的柠檬酸-柠檬酸钠缓冲液100 ml,然后关闭第二顶盖14进行密封;再打开第一顶盖13,在第一外壳体11加入暗发酵细菌和产氢培养基,其中暗发酵细菌添加体积为发酵有效体积的20%(v/v),即36 ml,产氢培养基添加量为44 ml,暗发酵的发酵液ph为5.5,然后关闭第一顶盖13进行密封,暗发酵细菌为富集后的厌氧产氢混合菌;将同步糖化暗发酵产氢装置置于45℃的水浴锅中,进行48h的暗发酵;步骤1)中所述厌氧产氢混合菌由双发酵副梭菌(para clostridium)、肠球菌(enterococcus)和拟杆菌(bacteroides)组成,所添加的暗发酵细菌菌液中双发酵副梭菌(para clostridium)、肠球菌(enterococcus)和拟杆菌(bacteroides)的浓度分别为45%(v/v)、36%(v/v)、29%(v/v);其中厌氧产氢混合菌(即暗发酵细菌)是采用文献(li y, zhang z, zhang q, et al. enhancement of bio-hydrogen yield and ph stability in photo fermentation process using dark fermentation effluent as succedaneum[j]. bioresource technology, 2020, 297: 122504.)中的方法获得的;具体的,步骤1)中所述暗发酵细菌是从厌氧污泥和畜禽粪便中富集得到的,富集条件温度为40-45℃,ph为5.5,葡萄糖浓度1g/l。
[0048]
步骤1)中所述厌氧产氢混合菌发酵培养的培养基、以及步骤1)中的产氢培养基均为:蛋白胨 4.0 g/l,nacl 4.0 g/l,mgcl
2 0.1 g/l,ch3coona 2.0 g/l,k2hpo
4 1.5 g/l,酵母膏1.0 g/l;在步骤1)中暗发酵的过程中纤维素酶水解玉米秸秆得到的糖类有机物,通过微米级第一滤网渗入到第一外壳体11(暗发酵产氢的发酵单元)进而被暗发酵细菌利用,糖的不断消耗促进了酶水解的正向进行,提高了底物(秸秆)的酶水解效率,当暗发酵单元基本没有氢气产生时,在产氢过程中,暗发酵的产气从第一通气管15排出,集气并测定暗发酵产氢量,经检测获得的产氢量为72.56 ml/g ts 秸秆;2)细胞超声粉碎和氨根吸附过程:暗发酵结束后,打开第一出液管17上的第一阀门18,暗发酵后的发酵液从第一外壳体11中流入到暗发酵细菌细胞粉碎和过滤装置2中,同时,同步糖化暗发酵产氢装置中也可同步加入下一轮暗发酵的产氢培养基、暗发酵细菌、秸秆粉末、纤维素酶和柠檬酸-柠檬酸钠缓冲液进行暗发酵;当暗发酵后的发酵液进入暗发酵细菌细胞粉碎和过滤装置2中时,开启超声细胞粉碎机21,超声功率400 w,工作30 min,对暗发酵菌的细胞进行粉碎,防止活的暗发酵菌的细胞进入到第二外壳体41(光发酵产氢的发酵单元)消耗碳源,粉碎后的细胞颗粒经过微孔
吸附棉22进行吸附处理,防止破碎的暗发酵菌的细胞进入到第二外壳体41(光发酵产氢的发酵单元)阻碍光发酵,所述超声细胞粉碎机21采用现有技术中的设备即可,且其结构不是本发明的发明点所在,故不再赘述,采用超声细胞粉碎机21替代常用的离心过滤、高温灭菌等复杂工艺,简化了暗发酵液的预处理工序;然后打开第二出液管23上的第二阀门24,经过细胞粉碎后的暗发酵尾液流入到氨根吸附装置3,氨根吸附装置3内底部设有沸石31,在35℃的温度条件下,采用沸石31对发酵液中的氨根进行吸附,其中暗发酵尾液和沸石31的比例为2:1(v/w),吸附时间2h,吸附后暗发酵尾液的氨根浓度为2.12
±
0.32 mm;3)光发酵产氢过程:先打开同步糖化光合产氢发酵装置中第二内壳体42顶端的第四顶盖44,加入67 ml ph为4.8的柠檬酸-柠檬酸钠缓冲液、经过60目筛选的玉米秸秆粉末5g、以及0.75g纤维素酶,并打开第三顶盖43,在第二外壳体41内加入36ml光合细菌hau-m1和44ml产氢培养基;然后打开第三出液管32上的第三阀门33,将33 ml吸附后的暗发酵液流入到同步糖化光合产氢发酵装置的第二内壳体42中,并与柠檬酸-柠檬酸钠缓冲液、经过60目筛选的秸秆粉末、纤维素酶在第二内壳体42中进行再次酶解,酶解后的酶解液通过第二内壳体42侧壁上的微米级第二滤网流入到第二外壳体41中,并与产氢培养基和光合产氢菌hau-m1进行光发酵生物制氢反应;光发酵生物制氢反应过程中,发酵底物为经过60目筛选的玉米秸秆和暗发酵尾液,底物浓度为27mg/ml,纤维素酶(绿色木霉)的酶负荷为150mg/g秸秆,采用的缓冲液为ph=4.8的柠檬酸-柠檬酸钠缓冲液与暗发酵尾液的混合液,通过采用暗发酵液代替部分柠檬酸-柠檬酸钠缓冲液,来减少产氢过程中柠檬酸-柠檬酸钠缓冲液的用量,其中暗发酵尾液与柠檬酸-柠檬酸钠缓冲液的体积比为1:2,同步糖化光发酵生物制氢的发酵温度为35℃,初始ph6.5,光合产氢菌接种量为20%(v/v)(即光合产氢菌干重1.26g/l),光照强度为3000lux,发酵周期为60h;在产氢过程中,光发酵产气从第三通气管45排出,集气并测定光发酵产氢量,经检测获得的产氢量为88.66 ml/g ts 秸秆。
[0049]
纤维素酶为绿色木霉,购自上海源叶生物科技有限公司,酶活10fpu/g。
[0050]
所述缓冲液为:ph4.8柠檬酸-柠檬酸钠缓冲液,ph调节剂(5mol/l的koh溶液、5mol/l的盐酸溶液);柠檬酸-柠檬酸钠缓冲液配置方法如下:a液:准确称取c6h8o7.h2o 21.014g于500ml烧杯中,用少量去离子水溶解后,定容至1000ml,得到0.1mol/l柠檬酸溶液;b液:准确称取na3c6h5o7.2h2o 29.412g于500ml烧杯中,用少量去离子水溶解后,定容至1000ml,得到0.1mol/l柠檬酸钠溶液;取a液230ml,b液270ml,充分混合后移入1000ml容量瓶中用去离子水定容至1000ml,充分混合,4℃冰箱中冷藏保存。
[0051]
本发明光发酵制氢时所用菌种为光合细菌hau-m1,所述hau-m1光合菌群是采用文献(韩滨旭.光合产氢菌群的分离鉴定及其产氢特性分析[d].河南农业大学,2011)中的方法获得的,其可以在光照条件下分解有机物进行产氢,主要由深红红螺菌 (r.hodospirillum rubrum) 、荚膜红假单胞菌 (r.capsulata) 、沼泽红假单胞菌(r.pulastris) 、类球红细菌(r.hodobacter sphaeroides) 、荚膜红细菌(rhodobacter capsulatus)组成。
[0052]
hau-m1光合菌群菌液中,深红红螺菌菌液、荚膜红假单胞菌菌液、沼泽红假单胞菌菌液、类球红细菌菌液与荚膜红细菌菌液的体积比分别为27:25:28:9:11;深红红螺菌菌液中活菌数为12.0
×
10
8 个/ml,荚膜红假单胞菌为11.0
×
10
8 个/ml,沼泽红假单胞菌为12.5
×
10
8 个/ml,类球红细菌为4.0
×
10
8 个/ml,荚膜红细菌为5.0
×
10
8 个/ml。
[0053]
所述光合细菌hau-m1由河南农业大学农业农村部可再生能源新材料与装备重点实验室获得。
[0054]
光发酵制氢过程中使用到的培养基和试剂为:生长培养基: nh4cl 0.5g/l;nahco
3 1g/l;酵母膏0.5g/l;k2hpo
4 0.1g/l;ch3coona 2g/l;mgso
4 0.1g/l;nacl 1g/l。
[0055]
产氢培养基: nh4cl 0.4g/l;mgcl
2 0.2g/l;酵母膏0.1g/l;k2hpo
4 0.5g/l;nacl 2g/l;谷氨酸钠3.56g/l。
[0056]
本发明中具体的产氢测试方法为:使用721分光光度计(上海菁华科技仪器有限公司)测量光合细菌菌液的od
660nm
值,光合细菌被放入50 ml离心管中,以6000 r/min进行离心,然后倒掉上清液,沉积物在105℃温度下进行烘干至恒重后称重,然后绘制光合细菌干重对od
660nm
值的标准曲线。通过测试光合细菌生长过程中od
660nm
值的来计算光合细菌干重变化。
[0057]
气体采用集气袋进行收集,氢气浓度采用7890b型气相色谱仪进行测定。实验数据每12小时进行一次测量。
[0058]
实验结果分析通过生命周期评价数据分析采用暗发酵液代替部分柠檬酸-柠檬酸钠缓冲液,可以降低整个产气过程中温室气体(co2等)排放量,与只用柠檬酸-柠檬酸钠缓冲液的实验组相比(如图3所示,最终产气量为77.16 ml/g ts秸秆),本发明所述方法每生产1ml氢气相对减少了4.90mg co
2-eq(二氧化碳当量,代表温室气体的排放程度)。
[0059]
从图2中可以看出,在以添加柠檬酸钠缓冲液和柠檬酸钠缓冲液与暗发酵尾液混合物液的光合产氢实验组的ph均表现出先下降后上升的趋势,两组发酵体系的ph值在相同的时间点上产别不明显,表明用暗发酵液替代部分柠檬酸钠缓冲液仍可以维持光合产氢发酵系统ph值的正常变化,进一步说明暗发酵尾液保持一定的酸碱缓冲性能。
[0060]
图3为暗发酵产氢和光合发酵产氢过程的产氢量,可以看出光合产氢效果较好,同时采用暗发酵液替代部分柠檬酸钠缓冲液进行光合产氢,可以提高光合产氢过程的产氢量。
[0061]
从图2和图3可以看出,暗发酵尾液可以取代部分柠檬酸钠缓冲液来维持光合产氢体系缓冲性能,并且暗发酵尾液中的有机质被光合细菌利用进行产氢代谢,进而提高了光合产氢阶段的产氢量。
[0062]
利用本发明所述同步糖化暗-光联合发酵制氢工艺,通过在产氢过程中,以农业秸秆为原料进行产氢,首先进行酶解预处理,在纤维素酶的作用下,纤维素被分解成糖类等碳水化合物,然后使用得到的酶解液进行产氢实验,并且把酶水解和产氢发酵耦合于同一个装置,避免了在酶解过程中糖类的累积抑制纤维酶的活性,造成底物水解不彻底的现象。
[0063]
采用同步糖化技术显著提高了暗发酵产氢过程的产氢量,在光合产氢阶段,酶解单元添加暗发酵液的实验组产氢量显著高于未添加暗发酵液的实验组,同时经过ph测试,
可以得出在光合产氢酶解单元加入一定量暗发酵液来替代部分缓冲液能够保证酶解的有效进行的同时也保证光合产氢过程的缓冲性能,这种联合方式有效减少了柠檬酸钠试剂的用量。
[0064]
同时在本发明的工艺中,纤维素生物质在被水解成糖的同时糖也被产氢菌消耗,促进了酶水解的正向进行,同时减少了反应器的数量,降低了成本,从而提高产氢效率。
[0065]
以上所述实施例仅表达了本发明的几种实施方式,其描述较为具体和详细,但并不能因此而理解为对本发明专利范围的限制。应当指出的是,对于本领域的普通技术人员来说,在不脱离本发明构思的前提下,还可以做出若干变形和改进,这些都属于本发明的保护范围。因此,本发明专利的保护范围应以所附权利要求为准。