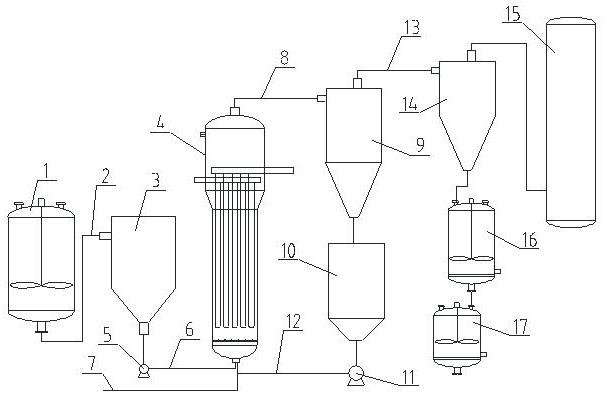
1.本发明属于有废弃资源综合利用技术领域,具体涉及一种有机硅单体合成过程中废硅粉的综合利用方法。
背景技术:2.当前,有机硅单体的合成主要采用直接法,即将氯甲烷和工业硅在催化剂作用下,在流化床内以流化态的形式反应得到以二甲基二氯硅烷((ch3)2sicl2)为主体的粗单体,在上述的氯甲烷和工业硅进行流化反应的过程中,工业硅经磨粉机磨碎后会呈现出一定的粒径分布,当氯甲烷气体从流化床底部向上将工业硅粉进行混合吹旋的时候,较大的硅粉颗粒由于重力的作用无法从流化床的顶部带出继续留在流化床内不断反应,而较细的硅粉颗粒则被未反应的氯甲烷气体以及粗单体带出。在现有的技术中,为了提高硅粉的利用率,一般都是在流化床的出口处安装旋风分离器,通过旋风分离器的离心分离作用将未反应的氯甲烷、粗单体和较细硅粉颗粒进行分离,但是,在上述旋风分离过程中,由于较细的硅粉颗粒由于其粒度较细,依旧会有很大一部分的细硅粉跟随气相粗单体及氯甲烷排出,造成浪费,基于此,大部分有机硅单体合成厂家都在流化床的反应后端设计使用两级旋风分离设备,第一级旋风分离设备所分离得到的工业硅粉往往粒径较大,可以直接回床使用,第二旋风分离设备分离出来的较细硅粉颗粒很细,将其返回工业级流化床或在工业硅生产过程直接回炉使用不切实际,一方面是由于粒径较细,容易被氧化而变为二氧化硅,另一方面在工业级流化床及冶炼过程中高速气流会将这些细硅粉带走,达不到回用的效果和目的。所以,将二级旋风分离设备分离出细硅粉直接排放不仅会污染环境,会对人类健康造成一定程度的危害,故还需要对这些细硅粉进行进一步的处理,以保证资源环境和人体的健康,当前,对于细硅粉的处理有以下几种,一种是填埋储藏,如通过液压方式运至污泥池,或存储在露天区域,这些大量堆积的硅粉都会造成土地资源的浪费,第二种方法是将含有cu的废硅铜触体通过酸浸的方法进行提铜处理,但酸浸会造成环境污染,另外一种处理方法是将这些细硅粉用于混凝土、水泥、耐火材料等领域, 但在实际应用中,由于各厂家细硅粉质量参差不齐,导致细硅粉使用量占比较低。因此,研制开发一种工艺合理、既能提高硅粉的回收利用率、又能够实现连续化规模生产的有机硅单体合成过程中废硅粉的综合利用方法是客观需要的。
技术实现要素:3.为了解决背景技术中存在的问题,本发明的目的在于提供一种工艺合理、既能提高硅粉的回收利用率、又能够实现连续化规模生产的有机硅单体合成过程中废硅粉的综合利用方法。
4.本发明所述的有机硅单体合成过程中废硅粉的综合利用方法,包括以下步骤:
①
活化搅拌:将工业级生产有机硅单体合成过程中产生的废硅粉和废硅铜触体加入到活化罐内,搅拌配制成含铜量在1~20%的铜硅粉混合料,之后再在活化罐内加入活化
剂,活化剂按照每千克铜硅粉混合料添加0.0001~100g的比例进行添加,然后将活化罐内的铜硅粉混合料和活化剂进行搅拌活化制得硅铜粉活化料,随后将硅铜粉活化料通过输送管输送到发送罐内;
②
回床反应:先将回床反应器以及与回床反应器连通的全部管线用惰性气体进行置换,之后向回床反应器的换热管内通入导热油,利用导热油将回床反应器内的温度控制在260~320℃,然后将发送罐内的硅铜粉活化料利用送料泵通过进料管输送至流化床反应器内,并同时利用导向管从活化床反应器的底部向流化床反应器内通入氯甲烷,使铜硅粉活化料和氯甲烷在流化床反应器内进行流化反应,流化反应生产的气料混合颗粒从流化床反应器的顶部排出;
③
分离处理:将从流化床反应器顶部排出的气料混合颗粒通过出料管输送至一级旋风分离器内进行一级分离,一级分离得到的粒径大于400目的粗颗粒物从一级旋风分离器的底部排出进入到存储罐内,再经过返料泵和回料管导入到流化床反应器内继续进行流化反应,而一级分离得到的气料混合颗粒通过连通管进入到二级旋风分离器内进行二级分离,二级分离得到含尘气体通二级旋风离器的顶部排出输送至洗涤塔内,而二级分离得到的粒径小于1000目的超细颗粒物则从二级旋风分离器的底部排出输送至细粉储罐内;
④
硅粉浸出处理:在装有超细颗粒物的细粉储罐内加入酸性溶液,搅拌浸泡得到混合液,超细硅粉颗粒与酸性溶液的固液比为1:5~10ml/g,待浸泡反应完全后,再向混合液中加入混合液质量0.1~100倍的还原铁粉进行置换反应,待置换反应结束后,将混合液进行过滤分离得到金属产品和硅粉浸出液;金属产品中含有铜、锌和锡等元素;
⑤
硅粉回收:将经步骤
④
分离得到的硅粉浸出液输送至中和罐内,接着向中和罐加入碱性剂对中和罐内的硅粉浸出液进行中和处理,待中和反应结束后,将中和浸出的固体硅粉再次进行酸洗和过滤后就能够回收得到硅粉产品。
5.本发明产生的有益效果是:一是本发明先将有机硅合成过程中产生的废硅粉和废铜触体先利用活化剂进行活化,之后,再将活化后的废硅粉和废铜触体送入到流化床反应器内,利用氯甲烷再次与活化后的废硅粉和废铜触体进行流化反应,通过进一步的流化反应,不仅能够有效的提高硅粉的转化率,达到硅粉再次利用的目的,减少了废硅粉的再次产生,而且提高了提高了甲基氯硅烷的产量;二是本发明采用二级旋风分离的方式对未反应完全的废硅粉和废铜进行了单独的分离处理,这样使废硅粉的使用率得到了大幅的提高么,进一步的的减少了废硅粉的产生,避免了造成环境污染和损害人体健康的现象;三是本发明对二级旋风分离后的废硅粉进行了再次的分离回收,铜和废硅粉的单独回收,能够产生较好的经济效益。综上,本发明的工艺技术简单、运行成本低,通过对废硅粉和废硅铜触体的分级利用,一方面将粒度相对较大的废硅粉和废硅铜触体进行了活化再生成有机硅甲基单体,整体上在工业级有机硅甲基单体合成方面减轻了活性相对较低的细硅粉回床压力,提升了大床的运行效率,提高了整体有机硅甲基单体合成效率,延长了大床的开车周期,能够给企业带来良好的生产效益,同时能够实现废硅粉和废铜触体的连续化生产,具有较好的推广利用价值;另一方面针对较细的废硅粉和废硅铜触体中的有价金属离子进行了还原提取,不仅避免了细硅粉及废铜触体对环境的污染和对人体的损害,实现了对废硅粉及废铜触体的资源化利用,其中废铜的回收率达到了85%以上,废锌的回收率达到了80%以上。
附图说明
6.图1为本发明的结构示意图;图中:1-活化罐,2-输送管,3-发送罐,4-回床反应器,5-送料泵,6-进料管,7-导向管,8-出料管,9-一级旋风分离器,10-存储罐,11-返料泵,12-回料管,13-连通管,14-二级旋风分离器,15-洗涤塔,16-细粉储罐,17-中和罐。
具体实施方式
7.下面结合实施例和附图说明对本发明作进一步的说明,但不以任何方式对本发明加以限制,基于本发明教导所作的任何变换或替换,均实施例属于本发明的保护范围。
8.实施例1本实施例1所述的有机硅单体合成过程中废硅粉的综合利用方法,包括以下步骤:
①
活化搅拌:将工业级生产有机硅单体合成过程中产生的废硅粉和废硅铜触体加入到活化罐1内,活化罐1内带有搅拌器,利用搅拌器将废硅粉和废铜触体搅拌配制成含铜量在1%的铜硅粉混合料,之后再在活化罐1内加入活化剂,活化剂按照每千克铜硅粉混合料添加0.0001g的比例进行添加,所述活化剂为锡粉、锌粉、铝粉、氯化钠、氯化钾的混合物,活化剂中锡粉和锌粉的质量比为1:1,铝粉的含量少于0.1wt.%,氯化钠和氯化钾的含量少于50ppm,利用活化剂对铜硅粉混合料进行催化活化,然后将活化罐1内的铜硅粉混合料和活化剂进行搅拌活化制得硅铜粉活化料,随后将硅铜粉活化料通过输送管2输送到发送罐3内;
②
回床反应:先将回床反应器4以及与回床反应器4连通的全部管线用惰性气体进行置换,所述惰性气体为氩气,利用氩气对回床反应器4和全部管线进行置换,是为了能够保证流化床反应器4内的废硅粉与氯甲烷的高效接触,提高甲基氯硅烷的产品质量,之后向回床反应器4的换热管内通入导热油,利用导热油将回床反应器4内的温度控制在260℃,通过温度的控制能够控制流化床反应器4内的废硅粉与氯甲烷反应的激烈程度,从而在保证甲基氯硅烷产品质量的同时,进一步的提高废硅粉的使用率,然后将发送罐3内的硅铜粉活化料利用送料泵5通过进料管6输送至流化床反应器4内,并同时利用导向管7从活化床反应器4的底部向流化床反应器4内通入氯甲烷,使铜硅粉活化料和氯甲烷在流化床反应器4内进行流化反应,硅铜粉活化料的进料量控制在80kg/h,氯甲烷的进料量控制在320kg/h,流化反应生产的气料混合颗粒从流化床反应器4的顶部排出,气料混合颗粒中含有甲基氯硅烷、硅、铜、锡和锌等成分;
③
分离处理:将从流化床反应器4顶部排出的气料混合颗粒通过出料管8输送至一级旋风分离器9内进行一级分离,一级分离得到的粒径大于400目的粗颗粒物从一级旋风分离器9的底部排出进入到存储罐10内,粗颗粒物返回到流化床反应器4内继续反应,可以降低流化反应过程中硅粉的消耗,进一步的减少废硅粉的产生,再经过返料泵11和回料管12导入到流化床反应器4内继续进行流化反应,而一级分离得到的气料混合颗粒通过连通管13进入到二级旋风分离器14内进行二级分离,二级分离得到含尘气体通二级旋风离器14的顶部排出输送至洗涤塔15内,而二级分离得到的粒径小于1000目的超细颗粒物则从二级旋风分离器14的底部排出输送至细粉储罐16内,超细颗粒物料的性能满足不了硫化反应的需求,通过后续的分离处理实现铜和硅粉的单独回收;
④
硅粉浸出处理:在装有超细颗粒物的细粉储罐16内加入酸性溶液,搅拌浸泡得到混合液,所述酸性溶液为浓度0.1~41wt.%的盐酸溶液,超细硅粉颗粒与酸性溶液的固液比为1:5ml/g,待浸泡反应完全后,再向混合液中加入混合液质量0.1倍的还原铁粉进行置换反应,待置换反应结束后,将混合液进行过滤分离得到金属产品和硅粉浸出液;金属产品中含有铜、锌和锡等元素;
⑤
硅粉回收:将经步骤
④
分离得到的硅粉浸出液输送至中和罐17内,接着向中和罐17加入碱性剂对中和罐17内的硅粉浸出液进行中和处理,碱性剂为纯碱,待中和反应结束后,将中和浸出的固体硅粉再次进行酸洗和过滤后就能够回收得到硅粉产品。
9.本实施例1的工艺技术简单、运行成本低,通过对废硅粉和废硅铜触体的分级利用,一方面将粒度相对较大的废硅粉和废硅铜触体进行了活化再生成有机硅甲基单体,整体上在工业级有机硅甲基单体合成方面减轻了活性相对较低的细硅粉的回床压力,提升了大床的运行效率,提高了整体有机硅甲基单体合成效率,延长了大床的开车周期,能够给企业带来良好的生产效益,同时能够实现废硅粉和废硅铜触体的连续化生产,具有较好的推广利用价值;另一方面针对较细的废硅粉和触体中的有价金属离子进行了还原提取,不仅避免了细硅粉及废铜触体对环境的污染和对人体的损害,实现了对废硅粉及废铜触体的资源化利用,废铜的回收率达到了88.5.6%,废锌的回收率达到了82.7%。
10.实施例2本实施例2所述的有机硅单体合成过程中废硅粉的综合利用方法,包括以下步骤:
①
活化搅拌:将工业级生产有机硅单体合成过程中产生的废硅粉和废硅铜触体加入到活化罐1内,活化罐1内带有搅拌器,利用搅拌器将废硅粉和废铜触体搅拌配制成含铜量在15%的铜硅粉混合料,之后再在活化罐1内加入活化剂,活化剂按照每千克铜硅粉混合料添加50g的比例进行添加,所述活化剂为锡粉、锌粉、铝粉、氯化钠、氯化钾的混合物,活化剂中锡粉和锌粉的质量比为1:1.5,铝粉的含量少于0.1wt.%,氯化钠和氯化钾的含量少于50ppm,利用活化剂对铜硅粉混合料进行催化活化,然后将活化罐1内的铜硅粉混合料和活化剂进行搅拌活化制得硅铜粉活化料,随后将硅铜粉活化料通过输送管2输送到发送罐3内;
②
回床反应:先将回床反应器4以及与回床反应器4连通的全部管线用惰性气体进行置换,所述惰性气体为氮气,利用氮气对回床反应器4和全部管线进行置换,是为了能够保证流化床反应器4内的废硅粉与氯甲烷的高效接触,提高甲基氯硅烷的产品质量,之后向回床反应器4的换热管内通入导热油,利用导热油将回床反应器4内的温度控制在300℃,通过温度的控制能够控制流化床反应器4内的废硅粉与氯甲烷反应的激烈程度,从而在保证甲基氯硅烷产品质量的同时,进一步的提高废硅粉的使用率,然后将发送罐3内的硅铜粉活化料利用送料泵5通过进料管6输送至流化床反应器4内,并同时利用导向管7从活化床反应器4的底部向流化床反应器4内通入氯甲烷,使铜硅粉活化料和氯甲烷在流化床反应器4内进行流化反应,硅铜粉活化料的进料量控制在300kg/h,氯甲烷的进料量控制在1200kg/h,流化反应生产的气料混合颗粒从流化床反应器4的顶部排出,气料混合颗粒中含有甲基氯硅烷、硅、铜、锡和锌等成分;
③
分离处理:将从流化床反应器4顶部排出的气料混合颗粒通过出料管8输送至一级旋风分离器9内进行一级分离,一级分离得到的粒径大于400目的粗颗粒物从一级旋风分
离器9的底部排出进入到存储罐10内,粗颗粒物返回到流化床反应器4内继续反应,可以降低流化反应过程中硅粉的消耗,进一步的减少废硅粉的产生,再经过返料泵11和回料管12导入到流化床反应器4内继续进行流化反应,而一级分离得到的气料混合颗粒通过连通管13进入到二级旋风分离器14内进行二级分离,二级分离得到含尘气体通二级旋风离器14的顶部排出输送至洗涤塔15内,而二级分离得到的粒径小于1000目的超细颗粒物则从二级旋风分离器14的底部排出输送至细粉储罐16内,超细颗粒物料的性能满足不了硫化反应的需求,通过后续的分离处理实现铜和硅粉的单独回收;
④
硅粉浸出处理:在装有超细颗粒物的细粉储罐16内加入酸性溶液,搅拌浸泡得到混合液,所述酸性溶液为浓度0.1~41wt.%的硫酸溶液,超细硅粉颗粒与酸性溶液的固液比为1:8ml/g,待浸泡反应完全后,再向混合液中加入混合液质量60倍的还原铁粉进行置换反应,待置换反应结束后,将混合液进行过滤分离得到金属产品和硅粉浸出液;金属产品中含有铜、锌和锡等元素;
⑤
硅粉回收:将经步骤
④
分离得到的硅粉浸出液输送至中和罐17内,接着向中和罐17加入碱性剂对中和罐17内的硅粉浸出液进行中和处理,碱性剂为烧碱,待中和反应结束后,将中和浸出的固体硅粉再次进行酸洗和过滤后就能够回收得到硅粉产品。
11.本实施例2的工艺技术简单、运行成本低,通过对废硅粉和废硅铜触体的分级利用,一方面将粒度相对较大的废硅粉和废硅铜触体进行了活化再生成有机硅甲基单体,整体上在工业级有机硅甲基单体合成方面减轻了活性相对较低的细硅粉的回床压力,提升了大床的运行效率,提高了整体有机硅甲基单体合成效率,延长了大床的开车周期,能够给企业带来良好的生产效益,同时能够实现废硅粉和废硅铜触体的连续化生产,具有较好的推广利用价值;另一方面针对较细的废硅粉和触体中的有价金属离子进行了还原提取,不仅避免了细硅粉及废铜触体对环境的污染和对人体的损害,实现了对废硅粉及废铜触体的资源化利用,废铜的回收率达到了87.6%,废锌的回收率达到了83.5%。
12.实施例3本实施例3所述的有机硅单体合成过程中废硅粉的综合利用方法,包括以下步骤:
①
活化搅拌:将工业级生产有机硅单体合成过程中产生的废硅粉和废硅铜触体加入到活化罐1内,活化罐1内带有搅拌器,利用搅拌器将废硅粉和废铜触体搅拌配制成含铜量在20%的铜硅粉混合料,之后再在活化罐1内加入活化剂,活化剂按照每千克铜硅粉混合料添加100g的比例进行添加,所述活化剂为锡粉、锌粉、铝粉、氯化钠、氯化钾的混合物,活化剂中锡粉和锌粉的质量比为1:2,铝粉的含量少于0.1wt.%,氯化钠和氯化钾的含量少于50ppm,利用活化剂对铜硅粉混合料进行催化活化,然后将活化罐1内的铜硅粉混合料和活化剂进行搅拌活化制得硅铜粉活化料,随后将硅铜粉活化料通过输送管2输送到发送罐3内;
②
回床反应:先将回床反应器4以及与回床反应器4连通的全部管线用惰性气体进行置换,所述惰性气体为氦气,利用氦气对回床反应器4和全部管线进行置换,是为了能够保证流化床反应器4内的废硅粉与氯甲烷的高效接触,提高甲基氯硅烷的产品质量,之后向回床反应器4的换热管内通入导热油,利用导热油将回床反应器4内的温度控制在320℃,通过温度的控制能够控制流化床反应器4内的废硅粉与氯甲烷反应的激烈程度,从而在保证甲基氯硅烷产品质量的同时,进一步的提高废硅粉的使用率,然后将发送罐3内的硅铜粉活
化料利用送料泵5通过进料管6输送至流化床反应器4内,并同时利用导向管7从活化床反应器4的底部向流化床反应器4内通入氯甲烷,使铜硅粉活化料和氯甲烷在流化床反应器4内进行流化反应,硅铜粉活化料的进料量控制在500kg/h,氯甲烷的进料量控制在2000kg/h,流化反应生产的气料混合颗粒从流化床反应器4的顶部排出,气料混合颗粒中含有甲基氯硅烷、硅、铜、锡和锌等成分;
③
分离处理:将从流化床反应器4顶部排出的气料混合颗粒通过出料管8输送至一级旋风分离器9内进行一级分离,一级分离得到的粒径大于400目的粗颗粒物从一级旋风分离器9的底部排出进入到存储罐10内,粗颗粒物返回到流化床反应器4内继续反应,可以降低流化反应过程中硅粉的消耗,进一步的减少废硅粉的产生,再经过返料泵11和回料管12导入到流化床反应器4内继续进行流化反应,而一级分离得到的气料混合颗粒通过连通管13进入到二级旋风分离器14内进行二级分离,二级分离得到含尘气体通二级旋风离器14的顶部排出输送至洗涤塔15内,而二级分离得到的粒径小于1000目的超细颗粒物则从二级旋风分离器14的底部排出输送至细粉储罐16内,超细颗粒物料的性能满足不了硫化反应的需求,通过后续的分离处理实现铜和硅粉的单独回收;
④
硅粉浸出处理:在装有超细颗粒物的细粉储罐16内加入酸性溶液,搅拌浸泡得到混合液,所述酸性溶液为浓度0.1~41wt.%的盐酸溶液与浓度0.1~41wt.%的硫酸溶液的混合物,超细硅粉颗粒与酸性溶液的固液比为1:10ml/g,待浸泡反应完全后,再向混合液中加入混合液质量100倍的还原铁粉进行置换反应,待置换反应结束后,将混合液进行过滤分离得到金属产品和硅粉浸出液;金属产品中含有铜、锌和锡等元素;
⑤
硅粉回收:将经步骤
④
分离得到的硅粉浸出液输送至中和罐17内,接着向中和罐17加入碱性剂对中和罐17内的硅粉浸出液进行中和处理,碱性剂为纯碱,待中和反应结束后,将中和浸出的固体硅粉再次进行酸洗和过滤后就能够回收得到硅粉产品。
13.本实施例3的工艺技术简单、运行成本低,通过对废硅粉和废硅铜触体的分级利用,一方面将粒度相对较大的废硅粉和废硅铜触体进行了活化再生成有机硅甲基单体,整体上在工业级有机硅甲基单体合成方面减轻了活性相对较低的细硅粉的回床压力,提升了大床的运行效率,提高了整体有机硅甲基单体合成效率,延长了大床的开车周期,能够给企业带来良好的生产效益,同时能够实现废硅粉和废硅铜触体的连续化生产,具有较好的推广利用价值;另一方面针对较细的废硅粉和触体中的有价金属离子进行了还原提取,不仅避免了细硅粉及废铜触体对环境的污染和对人体的损害,实现了对废硅粉及废铜触体的资源化利用,废铜的回收率达到了89.2%,废锌的回收率达到了84.6%。