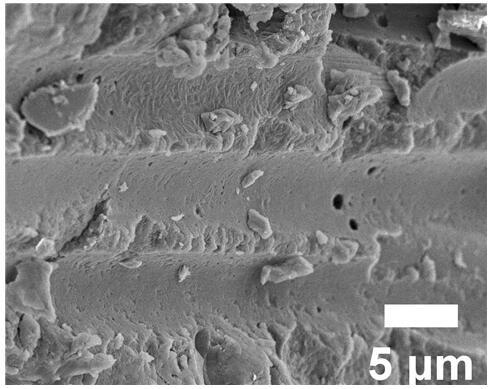
1.本发明涉及一种碳纤维增强尼龙-6微孔发泡复合材料的制备方法,属于发泡材料制备领域。
背景技术:2.汽车行业的发展十分迅速,而汽车的生产制造不可避免地造成了物质资源和能量资源的浪费。随着节能减排要求的提出,汽车轻量化技术应运而生,这一技术囊括了汽车的各个零部件,主要途径是在确定满足各项力学性能和安全性能的前提下,通过合理的结构设计优化和采用轻质材料(复合材料、高强度钢、镁铝合金、塑料等)降低结构重量,从而达到节能环保的要求。
3.微孔发泡聚合物材料是一种泡孔直径为1 μm ~ 10 μm,泡孔密度为10
9 ~ 10
12 个/cm3的闭孔结构发泡材料,与未发泡聚合物材料制品相比,它具有质轻、成本低、导热率小、比强度高、隔热性能好等众多优点,被广泛应用于汽车、包装、建筑等国民经济领域。
4.聚合物微孔发泡是一个复杂的过程,其基本原理是经惰性气体饱和的聚合物体系通过快速升温和卸压形成热力学不稳定状态并发生相分离,从而在聚合物基体中诱导形成大量气泡核,然后经泡孔生长与定型得到微孔结构。一般可分为4个阶段:聚合物/气体均相体系的形成;气泡核的形成;泡孔生长;泡孔固化定型。其中,气泡核的形成阶段对材料的制备起着关键作用,直接决定其泡孔密度和泡孔分布。在泡孔生长和固化定型阶段,通过调节发泡温度、发泡时间等工艺参数能够有效控制材料的微观形态和宏观性能。
5.尼龙-6(pa6)是一种高性能的通用热塑性树脂,具有优良的耐热性、耐磨性和自润滑性,在汽车各结构部件中,pa6已经被广泛应用。随着汽车轻量化趋势的发展,采用微孔发泡工艺实现pa6部件的轻量化已经成为重要的研究方向,但是由于pa6的材料自身力学强度相对较差,在经过微孔发泡之后,其力学承载性能大幅降低,难以满足次承力结构件的使用要求。而以高聚物为基体,利用高模量、高强度的碳纤维填充的聚合物发泡材料是一种含有碳纤维、基体以及气体的三相共存的新型复合材料,能够大幅度提高聚合物发泡材料的弹性模量、压缩模量、拉伸强度,同时还能使材料的收缩率显著降低。将其作为加强内衬用于汽车车架中的某些关键部位,可显著增加车身的刚度、吸收更多的冲击能量,充分满足了汽车轻量化及安全性的双重需求。
6.将碳纤维增强发泡材料引入pa6部件的制备技术中,能在保证复合材料基本性能的前提下降低材料的密度、节省原料用量,应用前景广阔。避免气泡在碳纤维与基体界面处成核、防止气体过分逃逸、抑制泡孔的合并与塌陷是微孔发泡过程中需要考虑的关键技术问题,也是制备具有良好微观结构和宏观性能碳纤维增强pa6微孔发泡材料的有力保证。目前可用于该微孔发泡复合材料的方法鲜有报道。
技术实现要素:7.本发明旨在提供一种碳纤维增强尼龙-6微孔发泡复合材料的制备方法,利用热压
成型加工方法,在模具中首先将部件加热定型,然后再发泡。该方法设备简单、易于操作、成本低廉、适应性强,能够规模化生产。
8.本发明使用热压机完成材料的发泡及成型,增强相碳纤维的形态影响泡孔在界面处的成核。同时,本发明通过调节热压机的温度控制发泡剂的分解、添加成核剂防止气体逃逸、抑制泡孔合并及塌陷。
9.本发明提供了一种碳纤维增强尼龙-6微孔发泡复合材料的制备方法,包括以下步骤:步骤一,将基体材料pa6、抗氧化剂、发泡剂、成核剂溶于溶剂甲酸中,于50 ~ 70℃下搅拌2 ~ 3 h,所得溶液备用;步骤二,将碳纤维浸渍到步骤一所得溶液中,超声处理40 ~ 60 min,于室温下挥发甲酸,然后将浸渍液置于50 ~ 70℃的真空干燥箱中干燥10 ~ 12 h,充分除去甲酸,得到碳纤维预浸料;步骤三,在模具中涂抹脱模剂,将步骤二所得预浸料平铺到模具中,合模,模具置于200 ~ 215℃的热压机上预热5 ~ 15 min,然后提高温度至230 ~ 250℃,施加5 ~ 8 mpa的压力,经过15 ~ 30 min的发泡过程,卸压,冷却,将发泡材料从模具中取出。
10.进一步,所述步骤一中抗氧化剂为抗氧化剂168,发泡剂为对甲苯磺酰氨基脲、5-苯基四氮唑中的一种,成核剂为3000目、5000目滑石粉中的一种,甲酸的密度为1.22 g/ml。
11.进一步,所述步骤一中pa6、抗氧化剂、发泡剂、成核剂的质量比为100:(0.2 ~ 0. 6):(0.5 ~ 6):(0 ~ 10),pa6在甲酸中的浓度为8 ~ 16 wt%。
12.进一步,所述步骤二中碳纤维为短切碳纤维和碳纤维毡中的一种,短切碳纤维的长度为3 ~ 6 mm,碳纤维毡的密度为0.13 ~ 0.18 g/cm3,厚度为1 ~ 10 mm,pa6与碳纤维的质量比为100:(30 ~ 60)。
13.进一步,所述步骤二中超声处理的频率为30 ~ 50 khz。
14.进一步,所述步骤三中脱模剂为硅酮脱模剂。
15.进一步,所述步骤三中制备的碳纤维增强尼龙-6微孔发泡复合材料的泡孔直径为0.2 ~ 4 μm。
16.本发明的有益效果:本发明在超声作用下使基体材料完全浸渍碳纤维,采用热压法制备碳纤维增强pa6微孔发泡复合材料,通过提高热压机的温度加速发泡剂的分解,使产生的气体快速扩散,减少加工时间,提高了加工效率。该制备方法仅利用普通的热压机进行加工,操作简单、材料制造成本低、易于工业放大,有利于汽车轻量化发展。
附图说明
17.图1为本发明实施例1制备的碳纤维增强pa6微孔发泡复合材料的扫描电镜图。
18.图2为本发明实施例2制备的碳纤维增强pa6微孔发泡复合材料的扫描电镜图。
19.图3为本发明实施例3制备的碳纤维增强pa6微孔发泡复合材料的扫描电镜图。
20.图4为本发明实施例4制备的碳纤维增强pa6微孔发泡复合材料的扫描电镜图。
21.图5为本发明实施例5制备的碳纤维增强pa6微孔发泡复合材料的扫描电镜图。
22.图6为本发明实施例6制备的碳纤维增强pa6微孔发泡复合材料的扫描电镜图。
23.图7为本发明对比例1制备的碳纤维增强pa6复合材料的扫描电镜图。
24.图8为本发明对比例2制备的碳纤维增强pa6复合材料的扫描电镜图。
25.图9为基体pa6以及本发明对比例2和实施例6制备的复合材料的动态热机械性能(dma)图。
具体实施方式
26.下面结合具体实施例对本发明进行进一步的阐述。应该说明的是,下述说明仅是为了解释本发明,并不对其内容进行限定。
27.实施例1一种碳纤维增强pa6微孔发泡复合材料的制备方法,包括以下步骤:步骤1,将 10 g基体材料pa6、0.05 g抗氧化剂168 、0.1 g发泡剂对甲苯磺酰氨基脲溶于100 ml甲酸(甲酸的密度为1.22 g/ml)中,于60℃下搅拌2 h,所得溶液备用。
28.步骤2,将3 mm短切碳纤维浸渍到步骤1所得溶液中,40 khz超声处理50 min,于室温下挥发甲酸,然后将浸渍液置于60℃的真空干燥箱中干燥12 h,充分除去甲酸,得到碳纤维预浸料。
29.步骤3,在模具中涂抹硅酮脱模剂,将步骤2所得预浸料平铺到模具中,合模,模具置于210℃的热压机上预热10 min,然后提高温度至240℃,施加5 mpa的压力,经过20 min的发泡过程,卸压,冷却,将发泡材料从模具中取出。该微孔发泡复合材料的扫描电镜图如图1所示,泡孔主要分布在碳纤维与pa6的界面处,直径小于1 μm。
30.实施例2一种碳纤维增强pa6微孔发泡复合材料的制备方法,包括以下步骤:步骤1,将10 g基体材料pa6、0.05 g抗氧化剂168 、0.1 g发泡剂5-苯基四氮唑溶于100 ml甲酸中,于60℃下搅拌2 h,所得溶液备用。
31.步骤2,将3 mm短切碳纤维浸渍到步骤1所得溶液中,40 khz超声处理50 min,于室温下挥发甲酸,然后将浸渍液置于60℃的真空干燥箱中干燥12 h,充分除去甲酸,得到碳纤维预浸料。
32.步骤3,在模具中涂抹硅酮脱模剂,将步骤2所得预浸料平铺到模具中,合模,模具置于210℃的热压机上预热10 min,然后提高温度至240℃,施加5 mpa的压力,经过20 min的发泡过程,卸压,冷却,将发泡材料从模具中取出。该微孔发泡复合材料的扫描电镜图如图2所示,泡孔主要分布在碳纤维与pa6的界面处,直径小于1 μm。
33.实施例3本实施例在碳纤维增强pa6微孔发泡复合材料的制备过程中,基体材料中发泡剂为对甲苯磺酰氨基脲0.5 g,其他与实施例1相同。该微孔发泡复合材料的扫描电镜图如图3所示,泡孔主要分布在碳纤维与pa6的界面处,直径为0.2 ~ 0.5 μm,分布较均匀。
34.实施例4本实施例在碳纤维增强pa6微孔发泡复合材料的制备过程中,使用密度为0.15 g/cm3,厚度为3 mm的碳纤维毡作为增强体,其他与实施例3相同。该微孔发泡复合材料的扫描电镜图如图4所示,泡孔主要分布在基体pa6处,直径为0.5 ~ 1.2 μm,分布较均匀。
35.实施例5
一种碳纤维增强pa6微孔发泡复合材料的制备方法,包括以下步骤:步骤1,将10 g基体材料pa6、0.05 g抗氧化剂168 、0.5 g发泡剂对甲苯磺酰氨基脲、0.3 g成核剂5000目滑石粉溶于100 ml甲酸中,于60℃下搅拌2 h,所得溶液备用。
36.步骤2,将3 mm短切碳纤维浸渍到步骤1所得溶液中,40 khz超声处理50 min,于室温下挥发甲酸,然后将浸渍液置于60℃的真空干燥箱中干燥12 h,充分除去甲酸,得到碳纤维预浸料。
37.步骤3,在模具中涂抹硅酮脱模剂,将步骤2所得预浸料平铺到模具中,合模,模具置于210℃的热压机上预热10 min,然后提高温度至240℃,施加5 mpa的压力,经过20 min的发泡过程,卸压,冷却,将发泡材料从模具中取出。该微孔发泡复合材料的扫描电镜图如图5所示,泡孔主要分布在碳纤维与pa6的界面处,直径为0.5 ~ 1.8 μm。
38.实施例6本实施例在碳纤维增强pa6微孔发泡复合材料的制备过程中,使用密度为0.15 g/cm3,厚度为3 mm的碳纤维毡作为增强体,其他与实施例5相同。该微孔发泡复合材料的扫描电镜图如图6所示,泡孔主要分布基体pa6处,直径约为3.5 μm,分布均匀。
39.对比例中将提供碳纤维增强pa6复合材料(未添加发泡剂)的制备方法,与添加发泡剂后制备的碳纤维增强pa6微孔发泡复合材料进行比较,观察发泡后复合材料中泡孔的状态并对比二者的性能。
40.对比例1一种碳纤维增强pa6复合材料的制备方法,包括以下步骤:步骤1,将10 g基体材料pa6、0.05 g抗氧化剂168 溶于100 ml甲酸中,于60℃下搅拌2 h,所得溶液备用。
41.步骤2,将3 mm短切碳纤维浸渍到步骤1所得溶液中,40 khz超声处理50 min,于室温下挥发甲酸,然后将浸渍液置于60℃的真空干燥箱中干燥12 h,充分除去甲酸,得到碳纤维预浸料。
42.步骤3,在模具中涂抹硅酮脱模剂,将步骤2所得预浸料平铺到模具中,合模,模具置于210℃的热压机上预热10 min,然后提高温度至240℃,施加5 mpa的压力,经过20 min的发泡过程,卸压,冷却,将复合材料从模具中取出。该复合材料的扫描电镜图如图7所示,从图中可以看出:碳纤维与基体pa6结合状况较好,无泡孔存在。
43.对比例2本对比例在碳纤维增强pa6复合材料的制备过程中,使用密度为0.15 g/cm3,厚度为3 mm的碳纤维毡作为增强体,其他与对比例1相同。该复合材料的扫描电镜图如图8所示,从图中可以看出:碳纤维与基体pa6结合状况较好,无泡孔存在。
44.从图1 ~ 6可以看出,实施例4和实施例6制备的碳纤维毡增强pa6微孔发泡复合材料的泡孔分布在基体pa6处,且泡孔分布均匀、直径符合微孔特征,与实施例1、2、3和实施例5利用短切碳纤维制备的发泡材料相比,避免了泡孔在弱界面处的成核生长,不至于造成材料的缺陷。
45.因此,本发明对基体pa6以及对比例2和实施例6制备的复合材料进行动态热机械分析(dma),得到图9所示的曲线图。从图9(a)和(b)可以看出,对比例2制备的碳纤维毡增强pa6复合材料的储能模量(storage modulus,e’)和损耗模量(loss modulus,e
’’
)约为基体
pa6的2倍和1.3倍,碳纤维的增强效果明显;实施例6制备的碳纤维毡增强pa6微孔发泡复合材料的e’和e
’’
更高,得益于泡孔结构的形成。从图9(c)和(d)可以看出,对比例2中碳纤维的加入能够提高基体pa6的玻璃化转变温度(tg);实施例6制得的微孔发泡复合材料的tg进一步提高至75℃。