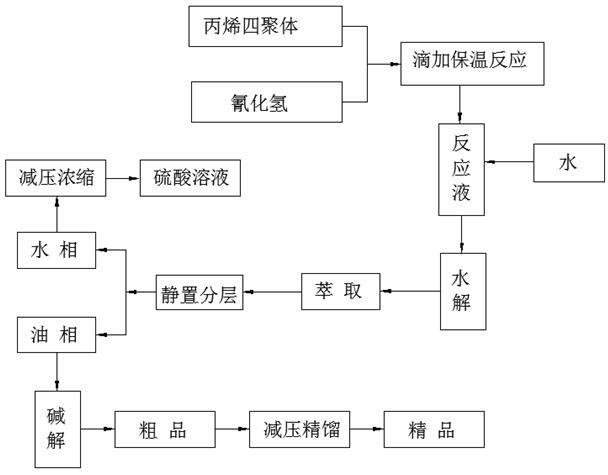
一种c12叔烷基伯胺的制备方法
技术领域
1.本发明属于化合物制备技术领域,特别涉及一种c12叔烷基伯胺的制备方法。
背景技术:2.c12叔烷基伯胺是一种带有多支链烷基的脂肪伯胺,其氨基中的氮原子与一个叔碳官能团相连接形成叔烷基结构。这种物质具有独特的化学性质和物理性质,主要用途是作为高级燃油、润滑油添加剂使用。
3.叔烷基伯胺的制备方法是根据著名的ritter反应为原理,其化学反应过程是已知的。目前成熟工艺是将有机原料与氰化物在酸性条件下反应生成中间产物,这种有机原料是带有异丁烯基的多碳直链烷基烯烃或者带有支链烯烃化合物为原料,分子式为r-c3h6,然后加入甲醇和水进行酯交换反应,生成甲酸甲酯和叔烷基伯胺,最后加入过量的碱性化合物中和体系中的硫酸,分层后得到油相粗产品,粗产品经过蒸馏提纯得到产品。
4.us5527949a提出的制备方法中,其两步反应过程都是在硫酸水溶液中进行,水解过程需加入甲醇,会生成含氰化氢的甲酸甲酯废液,同时催化剂硫酸采用氨水中和掉,产生大量的硫酸铵废水,工业用途非常局限。尽管cn1223254a和cn105051002a对此已经做过改进,但生产方法过于繁琐,需进行两步反应,所述两步反应仍然是以ritter反应为原理,ritter反应是在硫酸催化下进行,第一步反应后,硫酸继续为第二步水解反应提供酸性环境,是不进行硫酸分离的,这样就导致需要消耗过量的碱性化合物进行中和硫酸,会产生大量的含有多种阳离子、阴离子的碱性废水,废水处理难度较大,成本较高。
技术实现要素:5.本发明的目的在于提供一种可减少酸和碱用量,降低产生的废水量,节约成本的c12叔烷基伯胺的制备方法,以解决上述背景技术中提出的问题。
6.为达到上述技术目的,本发明的技术方案:一种c12叔烷基伯胺的制备方法,包括以下步骤:(1)滴加保温反应:取丙烯四聚体,缓慢滴入硫酸溶液,所述硫酸与所述丙烯四聚体的摩尔比为1.0~1.5:1,再缓慢滴入氰化氢,所述氰化氢与所述丙烯四聚体的摩尔比为1.0~1.5:1,控制所述硫酸溶液和所述氰化氢的滴入温度为0~30℃,搅拌,进行阶梯升温保温反应,所述阶梯升温保温反应包括三个阶段:第一阶段温度为25~35℃、反应时间为0.5~2h;第二阶段温度为35~45℃、反应时间为0.5~2h;第三阶段温度为50~70℃、反应时间为0.5~2h;(2)水解、萃取及分离:保温反应结束后,先将水加入反应液中,所述水的加入量为所述丙烯四聚体重量的1~3倍,于80~95℃搅拌2~6h,再将萃取剂加入所述反应液中,所述萃取剂的加入量为所述丙烯四聚体重量的0.3~5倍,搅拌0.5~2h,静置半小时后分层,得油相层和水相层,所述油相层经减压蒸馏、分离,得所述萃取剂和中间产物,所述水相层经减压浓缩后回套至步骤(1);
(3)碱解精馏:向所述中间产物加入碱进行碱解反应,所述碱与所述丙烯四聚体的摩尔比为0.5~1.5:1,所述碱解反应温度为80~90℃,碱解反应时间为2~6h,反应结束后,静置分层,得粗品叔烷基伯胺,再经减压精馏,得成品叔烷基伯胺。
7.ritter反应(包括滴加保温和水解反应):碱解反应:其中,r1为(ch2)9ch3;r2为h。
8.作为一种改进,步骤(1)中,所述硫酸溶液的质量浓度为60~90%,优选为80%。
9.作为一种改进,步骤(1)中,所述硫酸与所述丙烯四聚体的摩尔比为1.2:1。
10.作为一种改进,步骤(1)中,所述氰化氢与所述丙烯四聚体的摩尔比为1.1:1。
11.作为一种改进,步骤(1)中,控制所述硫酸溶液和所述氰化氢的滴入温度为20~25℃。
12.作为一种改进,步骤(2)中,所述水的加入量为所述丙烯四聚体重量的1倍,所述萃取剂的加入量为所述丙烯四聚体重量的1倍。
13.作为一种改进,步骤(2)中,所述萃取剂为戊烷、己烷、庚烷、辛烷及其异构体类烷烃、苯、甲苯、二氯甲烷或四氯化碳中的一种。
14.作为一种改进,步骤(3)中,所述碱与所述丙烯四聚体的摩尔比为0.6:1。
15.作为一种改进,步骤(3)中,所述碱为氢氧化钠、氢氧化钾或氨水中的一种。
16.由于采用上述技术方案,本发明的有益效果:本发明提供的制备方法,采用阶梯升温,既可以保证氰化氢和丙烯四聚体反应完全,又可以稳定产物的胺值和颜色;将水解反应生成的中间产物通过萃取分离法进行分离,回收第一步中加入的硫酸溶液,硫酸溶液的回收套用量可达原始用量的70%以上;碱解反应在碱性条件下进行,由于大部分硫酸已经被萃取分离出来,因此可以减少中和硫酸所需要的碱的量,减少用量约为原碱用量的50%。本发明减少了酸和碱的单耗,废水总量可降低75%以上,降低了单耗,节约了成本,降低了废水总量,从而减少了对环境的污染。
附图说明
17.图1是本发明提供的工艺流程图。
具体实施方式
18.下面结合具体实施方式及附图对本发明作进一步的说明。
19.实施例1
(1)有机原料和氰化氢滴加保温反应称取100g丙烯四聚体(纯度为99%以上)于反应容器中,将95g质量分数为80%硫酸溶液(新配置或者回套的)通过恒压滴液漏斗向反应容器滴加,1min左右后,将18.5g氰化氢通过恒压滴液漏斗加入反应容器中,控制冷却温度和滴加速度,确保反应液温度在30℃以下;硫酸溶液和氰化氢滴加设定好滴加速度,基本可以同时滴加完毕,滴加完毕后,开始阶梯升温,分别30℃、40℃、50℃左右各保温1h。
20.(2)水解、萃取、分离保温结束后,反应液加入100g水,90℃搅拌5小时,加入甲苯100g,搅拌半小时,然后用分液漏斗分离油水相,油相经减压蒸馏,分离得甲苯和有机相,有机相进行下一步反应;水相溶液可通过浓缩,得硫酸溶液进行循环使用,硫酸溶液浓缩后可以获得80%含量硫酸溶液69.1g,回套率为72.7%。
21.(3)碱解精馏然后通过滴液漏斗将81.8g氢氧化钠溶液(质量分数为32%)加入有机相中,加热进行碱解反应,反应温度为80℃,反应6h后,静置分层,分出油相,油相经减压精馏,得到产品101.2 g,产品胺值283,色号10。
22.实施例2(1)有机原料和氰化氢滴加保温反应称取100g丙烯四聚体(纯度为99%以上)于反应容器中,将112g质量分数为80%硫酸溶液(新配置或者回套的)通过恒压滴液漏斗向反应容器滴加,1min左右后,将18.5g氰化氢通过恒压滴液漏斗加入反应容器中,控制冷却温度和滴加速度,确保反应液温度30℃以下;硫酸溶液和氰化氢滴加设定好滴加速度,基本可以同时滴加完毕,滴加完毕后,开始阶梯升温,分别25℃、35℃、60℃左右各保温2h。
23.(2)水解、萃取、分离保温结束后,反应液加入100g水,80℃搅拌6小时,加入甲苯30g,搅拌半小时,然后用分液漏斗分离油水相,油相经减压蒸馏,分离得甲苯和有机相,有机相进行下一步反应;水相溶液可通过浓缩,得硫酸溶液进行循环使用,硫酸溶液浓缩后可以获得80%含量硫酸溶液81.2g,回套率为72.5%。
24.(3)碱解精馏然后通过滴液漏斗将81.8g氢氧化钠溶液(质量分数为32%)加入有机相中,加热进行碱解反应,反应温度为85℃,反应4h后,分出油相,油相经减压精馏,得到产品101g,产品胺值285,色号20。
25.实施例3(1)有机原料和氰化氢滴加保温反应称取100g丙烯四聚体(纯度为99%以上)于反应容器中,将76g质量分数为80%硫酸溶液(新配置或者回套的)通过恒压滴液漏斗向反应容器滴加,1min左右后,将18.5g氰化氢通过恒压滴液漏斗加入反应容器中,控制冷却温度和滴加速度,确保反应液温度30℃以下;硫酸溶液和氰化氢滴加设定好滴加速度,基本可以同时滴加完毕,滴加完毕后,开始阶梯升温,分别30 ℃、40℃、70℃左右各保温1.5h。
26.(2)水解、萃取、分离保温结束后,反应液加入100g水,95℃搅拌2小时,加入甲苯200g,搅拌1小时,然后用分液漏斗分离油水相,油相经减压蒸馏,分离得甲苯和有机相,有机相进行下一步反应;水相溶液可通过浓缩,得硫酸溶液循环使用,硫酸溶液浓缩后可以获得80%含量硫酸溶液56.1g,回套率为73.8%。
27.(3)碱解精馏然后通过滴液漏斗将81.8g氢氧化钠溶液(质量分数为32%)加入有机相中,加热进行碱解反应,反应温度为90℃,反应2h后,分出油相,油相经减压精馏,得到产品102.3 g,产品胺值291,色号35。
28.实施例4(1)有机原料和氰化氢滴加保温反应称取100g丙烯四聚体(纯度为99%以上)于反应容器中,将127g质量分数为60%硫酸溶液(新配置或者回套的)通过恒压滴液漏斗向反应容器滴加,1min左右后,将18.0g氰化氢通过恒压滴液漏斗加入反应容器中,控制冷却温度和滴加速度,确保反应液温度25℃以下;硫酸溶液和氰化氢滴加设定好滴加速度,基本可以同时滴加完毕,滴加完毕后,开始阶梯升温,分别35 ℃、45℃、60℃左右各保温0.5h。
29.(2)水解、萃取、分离保温结束后,反应液加入200g水,90℃搅拌4小时,加入戊烷300g,搅拌1小时,然后用分液漏斗分离油水相,油相经减压蒸馏,分离得戊烷和有机相,有机相进行下一步反应;水相溶液可通过浓缩,得硫酸溶液进行循环使用,硫酸溶液浓缩后可以获得60%含量硫酸溶液90.8g,回套率为71.5%。
30.(3)碱解精馏然后通过滴液漏斗将81.8g氢氧化钠溶液(质量分数为32%)加入有机相中,加热进行碱解反应,反应温度为85℃,反应4h后,分出油相,油相经减压精馏,得到产品101.6 g,产品胺值283,色号10。
31.实施例5(1)有机原料和氰化氢滴加保温反应称取100g丙烯四聚体(纯度为99%以上)于反应容器中,将108.6g质量分数为70%硫酸溶液(新配置或者回套的)通过恒压滴液漏斗向反应容器滴加,1min左右后,将16.74g氰化氢通过恒压滴液漏斗加入反应容器中,控制冷却温度和滴加速度,确保反应液温度30℃以下;硫酸溶液和氰化氢滴加设定好滴加速度,基本可以同时滴加完毕,滴加完毕后,开始阶梯升温,分别30 ℃、40℃、50℃左右各保温2h。
32.(2)水解、萃取、分离保温结束后,反应液加入300g水,90℃搅拌5小时,加入辛烷500g,搅拌2小时,然后用分液漏斗分离油水相,油相经减压蒸馏,分离得辛烷和有机相,有机相进行下一步反应;水相溶液可通过浓缩,得硫酸溶液进行循环使用,硫酸溶液浓缩后可以获得70%含量硫酸溶液76.8g,回套率为70.7%。
33.(3)碱解精馏
然后通过滴液漏斗将46.5g氢氧化钠溶液(质量分数为32%)加入有机相中,加热进行碱解反应,反应温度为90℃,反应3h后,分出油相,油相经减压精馏,得到产品101.9 g,产品胺值283,色号10。
34.实施例6(1)有机原料和氰化氢滴加保温反应称取100g丙烯四聚体(纯度为99%以上)于反应容器中,将84.4g质量分数为90 %硫酸溶液(新配置或者回套的)通过恒压滴液漏斗向反应容器滴加,1min左右后,将24.7g氰化氢通过恒压滴液漏斗加入反应容器中,控制冷却温度和滴加速度,确保反应液温度30℃以下;硫酸溶液和氰化氢滴加设定好滴加速度,基本可以同时滴加完毕,滴加完毕后,开始阶梯升温,分别30 ℃、40℃、50℃左右各保温1.5h。
35.(2)水解、萃取、分离保温结束后,反应液加入200g水,90℃搅拌5小时,加入二氯甲烷400g,搅拌2小时,然后用分液漏斗分离油水相,油相经蒸馏分离,分离得二氯甲烷和有机相,有机相进行下一步反应;水相溶液可通过浓缩,得硫酸溶液循环使用,硫酸溶液浓缩后可以获得90%含量硫酸溶液60.1g,回套率为71.2%。
36.(3)碱解精馏然后通过滴液漏斗将38.75g氢氧化钠溶液(质量分数为32%)加入有机相中,加热进行碱解反应,反应温度为83℃,反应5h后,分出油相,油相经减压精馏,得到产品102.1 g,产品胺值286,色号20。
37.实施例7(1)有机原料和氰化氢滴加保温反应称取100g丙烯四聚体(纯度为99%以上)于反应容器中,将95g质量分数为80 %硫酸溶液(新配置或者回套的)通过恒压滴液漏斗向反应容器滴加,1min左右后,将18.0g氰化氢通过恒压滴液漏斗加入反应容器中,控制冷却温度和滴加速度,确保反应液温度30℃以下;硫酸溶液和氰化氢滴加设定好滴加速度,基本可以同时滴加完毕,滴加完毕后,开始阶梯升温,分别30 ℃、40℃、70℃左右各保温2h。
38.(2)水解、萃取、分离保温结束后,反应液加入200g水,90℃搅拌5小时,加入四氯化碳100g,搅拌半小时,然后用分液漏斗分离油水相,油相经减压蒸馏,分离得四氯化碳和有机相,有机相进行下一步反应;水相溶液可通过浓缩,得硫酸溶液循环使用,硫酸溶液浓缩后可以获得80%含量硫酸溶液68.7g,回套率为72.3%。
39.(3)碱解精馏然后通过滴液漏斗将89g氨水(质量分数为25-28%)加入有机相中,加热进行碱解反应,反应温度为83℃,反应4h后,分出油相,油相经减压精馏,得到产品102.0 g,产品胺值283,色号10。
40.产品胺值越高表示反应越彻底,正常要求胺值在280左右,色号越低表示产品纯度越高,正常要求色号在50以下。
41.以上所述本发明的具体实施方式,并不构成对本发明保护范围的限定。任何根据
本发明的技术构思所做出的各种其他相应的改变与变形,均应包含在本发明权利要求的保护范围内。