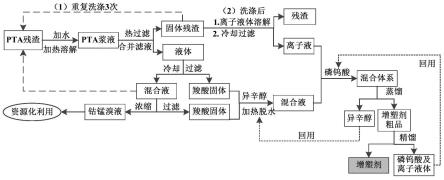
一种pta残渣提纯制备增塑剂的方法
技术领域
1.本发明属于废弃化工残渣的回收利用技术领域,尤其是涉及一种pta残渣提纯制备增塑剂的方法。
背景技术:2.精对苯二甲酸(purified terephthalic acid,pta)是重要的大宗有机原料之一。pta残渣主要由生产过程中的氧化残渣、精制残渣和水池废料组成。
3.pta氧化残渣中的组分复杂,主要成分有苯甲酸、对苯二甲酸、以及其他芳香酸,同时含有需回收利用的钴、锰溴盐。pta残渣产量巨大,据统计,2019年全球pta产能约9520 万吨,我国产能4869万吨,按每生产1吨pta产生30kg残渣计算,每年需处理残渣约150 万吨。因此,pta残渣无害化、资源化处理是一个亟待解决的问题。现有工艺多是进行有机物(苯羧酸)或者无机物(钴、锰溴盐)的回收利用,并未综合考虑pta氧化残渣整体资源化利用工艺。关于pta氧化残渣有机物利用的报道较多,如:专利cn 111205182 b中利用 pta残渣与过量异辛醇反应得到混合酯,然后通过精馏得到苯甲酸异辛酯和混合型增塑剂,苯甲酸异辛酯继续与二甘醇反应得到环保型增塑剂,该反应的钛酸四丁酯催化剂遇水极易分解,反应活性不高且无法重复使用;冯利民和张侦祥提出了以甲基苯磺酸为催化剂,催化苯二甲酸残渣与2-乙基己醇经酯化、减压蒸馏制取优质增塑剂,但该工艺只适用于单苯二甲酸酯化,对应复杂苯羧酸体系并不适用;专利cn100400499 c公开了利用二次甲酯化反应、精馏分离、重结晶精制、酯交换反应来生产混合酯的方法,反应后处理过程复杂。因pta氧化残渣成分复杂,如不提纯直接酯化不仅反应效率不高,且后处理会非常复杂,如专利cn 112299994b将pta氧化残渣用醇溶剂溶解萃取,然后将萃取液过滤,滤液到酯化釜反应生成混合酯,滤渣用于回收钴锰残渣,但残渣中组分复杂含有较多残留有机物,不仅不利用后续钴锰回收,且有机物只能焚烧处理,并未资源化利用。
4.上述专利文献,均通过酯化反应回收pta氧化残渣中的苯羧酸,但普遍存在催化剂腐蚀设备,遇水易分解,反应过程复杂等问题,尤其pta残渣中含有钴锰资源,将残渣直接酯化生成混合酯,得到的酯化残渣往往要经焚烧、酸溶、有机溶剂萃取等后续步骤才能回收其中的钴锰资源,反应过程复杂,且容易产生大量废水、废气、废渣,回收处理成本高。
技术实现要素:5.为了解决上述问题,本发明提供了一种pta残渣纯化分离及制备增塑剂的方法,高效、高纯度分离纯化pta残渣,资源化利用制备增塑剂的同时有效分离残渣中钴锰溴盐,便于后期回收利用,具有很高的应用前景。
6.本发明pta残渣纯化制备增塑剂的方法包括以下步骤:
7.(1)水洗:将pta残渣加入热水中,保温搅拌,然后趁热过滤,收集滤液、残渣备用;残渣重复多次洗涤,合并滤液,冷却、固体析出,过滤收集固体沉淀,即为混合羧酸固体;
8.(2)离子液体处理:水洗剩余残渣进一步加入到离子液体中加热溶解,然后冷却、
过滤,收集离子液体;
9.(3)酯化:将步骤(1)所得混合羧酸固体、步骤(2)所得离子液体、以及异辛醇混合,加热脱水,然后加入催化剂进行酯化反应,反应结束后,过滤收集液体、提纯,得到增塑剂。
10.在本发明的一种实施方式中,步骤(1)中,所述pta残渣与热水的质量比为1:6~1:15;优选为1:10。
11.在本发明的一种实施方式中,步骤(1)中,重复的次数为1~4次,优选水洗3次。
12.在本发明的一种实施方式中,步骤(1)中,热水的温度维持在90~95℃。
13.在本发明的一种实施方式中,步骤(1)中,冷却至15-30℃
14.在本发明的一种实施方式中,步骤(2)中,所述的离子液体选自如下任意一种或多种: 1-乙基-3甲基咪唑溴盐、1-丁基-3甲基咪唑溴盐、1-乙基-3甲基咪唑双三氟甲磺酰亚胺盐、 1-丁基-3甲基咪唑双三氟甲磺酰亚胺盐、1-乙基-3-甲基咪唑甲磺酸盐、1-丁基-3-甲基咪唑甲磺酸盐、1-乙基-3-甲基咪唑三氟甲烷磺酸盐、1-丁基-3-甲基咪唑三氟甲烷磺酸盐;优选为1
‑ꢀ
乙基-3甲基咪唑双三氟甲磺酰亚胺盐、1-丁基-3甲基咪唑双三氟甲磺酰亚胺盐。
15.在本发明的一种实施方式中,步骤(2)中,水洗剩余残渣与离子液体的用量条件为100 g:50-100ml;优选100g:80ml。
16.在本发明的一种实施方式中,步骤(2)中,步骤(1)所述pta氧化残渣与离子液体的用量条件为100g:10-20ml;优选100g:12ml。
17.在本发明的一种实施方式中,步骤(2)中,加热的温度为40-50℃。
18.在本发明的一种实施方式中,步骤(3)中,异辛醇与pta氧化残渣的质量比为1.5~2.5: 1;优选1.5~1.6:1。
19.在本发明的一种实施方式中,步骤(3)中,催化剂选自如下任意一种或多种:磷钨酸、钛酸四丁酯、硫酸、对甲苯磺酸、磷钼酸、五氯化铌、五氧化二铌;优选为磷钨酸。
20.在本发明的一种实施方式中,步骤(3)中,催化剂相对pta残渣的添加量为0.05mmol/100 g~0.4mmol/100g;优选为0.2mmol/100g。
21.在本发明的一种实施方式中,步骤(3)中,酯化反应的时间为1~6h;优选为5h。
22.在本发明的一种实施方式中,步骤(3)中,酯化反应的温度为200~210℃。
23.在本发明的一种实施方式中,步骤(3)中,加热脱水的时间为0.5-2h。
24.在本发明的一种实施方式中,所述方法具体包括如下步骤:
25.1)在反应器中加入pta残渣,分次加入热水,加热搅拌维持一定温度洗涤后趁热过滤,将剩余固体继续重复上述操作循环洗涤反复多次,合并滤液备用,固体残渣加入一定量的离子液体加热一定温度溶解,后冷却过滤离子液备用。
26.2)将步骤1)所得的滤液自然放置冷却至室温,后过滤分离,得到混合羧酸固体备用,混合液可继续用于步骤1)中煮pta残渣,多次循环使用后将滤液蒸发浓缩,蒸发浓缩水可重复用于步骤1)中洗涤pta残渣,后过滤分离得到残留羧酸固体和含钴锰溴盐浓缩液;
27.3)在反应器中加入步骤2)得到的羧酸固体混合与异辛醇加热煮沸脱水,得到的水可循环用于步骤1)中洗涤pta残渣;脱水后与步骤1)所得离子液混合,加入催化剂,升温至200~ 210℃反应一段时间,通过测定反应体系酸值确定反应终点,反应完成后,液体进一步提纯;
28.4)将步骤3)所得油状液体于精馏塔中进行提纯,首先回收异辛醇回用于步骤3),精馏得到增塑剂(苯甲酸异辛酯、苯二甲酸二异辛酯(对位和间位)、偏苯三甲酸三异辛酯),后剩余液体冷却过滤,固体为催化剂,经水洗、蒸发、干燥、活化后回用,液体为离子液体,可重新回用。
29.在本发明的一种实施方式中,步骤2)中,滤液循环使用次数为1~3次,浓缩体积为原体积的1/5~1/4。
30.本发明基于上述方法制备提供了一种增塑剂。
31.本发明还提供了上述方法在废水、废气、废渣回收处理领域中的应用。
32.有益效果:
33.本发明利用pta残渣纯化分离、制备增塑剂,高效、高纯度分离纯化pta残渣,资源化利用制备增塑剂的同时有效分离残渣中钴锰溴盐,便于后期回收利用,具有很高的应用前景。本发明方法可以实现羧酸回收率大于99%,并且酯化制备增塑剂的酯化率也大于99%。
附图说明
34.图1为水洗pta残渣制备增塑剂的工艺流程。
35.图2为水洗萃取pta残渣工艺。
具体实施方式
36.本发明按gb/t 1668-2008《增塑剂酸值及酸度的测定》测定反应体系酸值,酯化率ea= (1-x/x0)
×
100%,x0和x分别为反应前后反应物的酸值。
37.本发明涉及的pta残渣来自于江苏某处理厂,主要组分及含量如表1所示。
38.表1江苏某处理厂pta残渣中主要组分及含量
[0039][0040]
本发明利用液相色谱-质谱仪测定,利用纯品定标后测试计算含量,得到羧酸回收率。
[0041]
实施例1:
[0042]
水洗:取100g pta氧化残渣置于反应器,然后加入1000ml 95℃水,加热搅拌,维持温度为90~95℃搅拌10min,趁热过滤,得到滤液和残渣,滤液静置自然放置冷却至20℃后,有固体析出,过滤得到固体备用;剩余液体回用继续洗涤残渣,重复上述操作,洗涤三次,三次水洗后剩余固体残渣进行下一步离子液体萃取;液体浓缩至原体积的1/5,冷却,固体析出分离,与三次洗涤所得固体合并,经液相色谱检测及固体称重计算苯羧酸回收率80-81.6%。回收固体用于下步增塑剂的制备,剩余液体用于钴锰催化剂的制备。
[0043]
离子液萃取:将上述水洗后的残渣(约15g)中加入12ml 1-丁基-3甲基咪唑双三氟甲磺酰亚胺盐离子液,加热45℃搅拌溶解,后降至室温,滤去残渣,剩余混合离子液用于下一步酯化;水洗及离子液体萃取测试计算羧酸回收率大于99%;
[0044]
酯化:在反应器中加入水洗得到的固体与离子萃取液,后加入180ml异辛醇,加热脱水 1h,后加入0.2mmol磷钨酸,升温至210℃反应5h(通过测定体系酸值确定反应终点),酯化率99%以上,反应完成后,冷却至室温,过滤分离催化剂,液体为增塑剂粗产物,后经精馏塔提纯,得增塑剂;
[0045]
酯化液精馏:第一级精馏的蒸发相冷凝后得到苯甲酸异辛酯,纯度大于99%,第二级精馏塔的蒸发相冷凝后得得到苯二甲酸异辛酯和偏苯三甲酸三异辛酯,纯度均大于98%,二级精馏釜剩余液体冷却过滤,固体为催化剂,经水洗、蒸发、干燥、活化后回用,液体为离子液体,可重新回用。
[0046]
对比例1:
[0047]
不进行水洗-离子液萃取操作,直接利用固体pta残渣制备增塑剂。
[0048]
酯化:在反应器中加入100g pta残渣,后加入180ml异辛醇,加热脱水1h,后加入 0.2mmol磷钨酸,升温至210℃反应6h,根据酸值测试酯化率为82%。
[0049]
实施例2
[0050]
分别以pta残渣和pta残渣水洗萃取处理后的原料(实施例1)为底物进行反应,以相同的条件酯化,实例1和实例2不同时间对比结果如表2所示。
[0051]
表2是否经水洗萃取的pta残渣的反应效率影响比较
[0052][0053]
反应条件:pta残渣100g,异辛醇180ml,磷钨酸为0.2mmol,反应温度210℃。
[0054]
水洗萃取后的残渣在同样条件下反应速率明显提高,水洗萃取提纯后的残渣反应效率优势明显。
[0055]
实施例3
[0056]
酯化过程中催化剂用量的探究:
[0057]
反应以100g pta残渣和180ml异辛醇为原料,分别加入0.05~0.4mmol的磷钨酸作催化剂,在210℃反应5h。结果如表3所示,当催化剂量达到0.5g以上时,酯化率到达98.5%以上。
[0058]
表3催化剂用量的筛选
[0059][0060]
实施例4
[0061]
水洗过程中水洗固液比的探究:
[0062]
参照实施例1,,将加入水量分别替换为600ml、800、1000、1200、1500ml,即调整改变水洗过程的水洗固液比分别为1:6、1:8、1:10、1:12、1:15,测定水洗处理后的羧酸回收结果。结果如表4所示。
[0063]
表4水洗固液比对羧酸回收量的影响
[0064][0065]
表5水洗固液比对羧酸回收率的影响
[0066][0067]
根据表1中pta残渣中苯羧酸含量,结合表4苯羧酸回收量,计算得到苯羧酸回收率(回收量/含量),如表5所示。由表5可知,当固液比为1:10时,苯羧酸回收率为80%左右,继续增大固液比,苯羧酸回收率变化不大,因此,选择1:10为最佳固液比。
[0068]
实施例5
[0069]
水洗过程中水洗次数的探究:
[0070]
参照实施例1,调整改变水洗过程的次数,固液比为1:10时,循环1~4次洗涤后苯羧酸回收情况,。结果如表6所示。
[0071]
表6循环水洗不同次数对苯羧酸回收率的影响
[0072][0073]
由表6可知,在循环洗涤3次时苯羧酸回收率为80%以上,继续增加循环洗涤次数,苯羧酸回收率提升很低;因此,选择水洗3次为最佳循环水洗次数。
[0074]
实施例6
[0075]
离子液体萃取过程中离子液体用量的探究:
[0076]
参照实施例1,调整改变离子液体萃取过程的用量,其他不变,提纯制备增塑剂。结果如表7所示。
[0077]
表7离子液体用量对羧酸回收率的影响
[0078][0079]
注:反应水洗剩余残渣100g。
[0080]
实施例7
[0081]
离子液体萃取过程中离子液体种类的探究对比:
[0082]
水洗:同实施例1;
[0083]
离子液萃取:将上述水洗后的残渣中加入12ml 1-乙基-3甲基咪唑双三氟甲磺酰亚胺盐离子液,加热40-50℃搅拌溶解,后降至室温,滤去残渣,剩余混合离子液用于下一步酯化;水洗及离子液体萃取测试计算有机酸回收率约95%;
[0084]
酯化:在反应器中加入水洗得到的固体与离子萃取液,后加入180ml异辛醇,加热脱水 1h,后加入0.2mmol磷钨酸,升温至200~210℃反应5h(通过测定体系酸值确定反应终点),酯化率约97%,反应完成后,冷却至室温,过滤分离催化剂,液体为增塑剂粗产物,后经精馏塔提纯,得增塑剂;
[0085]
酯化液精馏:同实施例1。
[0086]
将离子液体替换为1-乙基-3甲基咪唑溴盐、1-丁基-3甲基咪唑溴盐、1-乙基-3-甲基咪唑甲磺酸盐、1-丁基-3-甲基咪唑甲磺酸盐、1-乙基-3-甲基咪唑三氟甲烷磺酸盐、1-丁基-3-甲基咪唑三氟甲烷磺酸盐,其余方法如对比例1,结果如表8:
[0087]
表8不同离子液体对回收及催化的影响
[0088][0089]
目前酯化制备增塑剂领域中,提高2%-3%是一个非常显著的进步。
[0090]
实施例8
[0091]
酯化过程中催化剂种类的探究对比:
[0092]
以pta残渣100g为原料,水洗、离子液萃取及精馏工艺如实例1;
[0093]
酯化:在反应器中加入水洗得到的固体与离子萃取液,后加入180ml异辛醇,加热脱水 1h,后加入0.2mmol钛酸四丁酯,升温至210℃反应5h(通过测定体系酸值确定反应终点),酯化率约97%,反应完成后,冷却至室温,过滤分离催化剂,液体为增塑剂粗产物,后经精馏塔提纯,得增塑剂。
[0094]
将酯化催化剂替换为0.2mmol钛酸四丁酯、硫酸、对甲苯磺酸、磷钼酸、五氯化铌及五氧化二铌,结果如表9:
[0095]
表9不同催化剂对催化的影响
[0096][0097]
目前酯化制备增塑剂领域中,提高2%-3%是一个非常显著的进步。