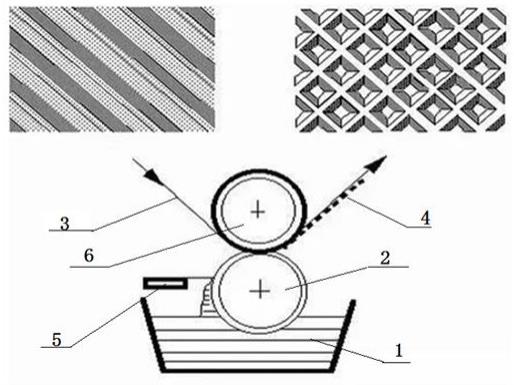
1.本发明涉及石墨烯的涂布成形技术领域,特别涉及一种用于石墨烯载体的压延离型膜及其制备方法。
背景技术:2.随着工业化进程的加快,电子产品在要求快速散热,快速导电的这一方向,能快速导热成为电子产品硬性需求。近几年来,在电子电气领域,由于集成技术和组装技术的发展,电子元器件的体积成千成万倍的缩小,则更需要高导热性能的小体积的材料。特别是在现代化的移动通信及5g基站的发展,对电子产品及材料超高导热及导电的要求日益加强。从而引发在上游中的一些产品供应商不断的开发及寻求新型材料来满足客户的需求。在电子辅材领域,对辅材的要求也变得相当的精细化。不同的厂家都在寻求新的材料,很多公司在原来石墨材料上进行深挖,开发出比石墨更加优秀的导热材料
‑‑‑‑
石墨烯。因为石墨烯在制做工艺上的特殊化,需要将天然石墨粉进行调配,里面需要加入一些其它材料进行液态化。使其变为浆料,方便涂布在载体上,可根据需要调节涂布所需要的厚度,然后再经过一系列的工艺达到所要石墨烯片材。为了达到表面光泽的效果,还需要对石墨烯片材进行压光均厚的工艺处理,在此工艺处理中需要用到载体及离型膜,且由于工艺的需要,离型膜需要跟石墨烯片材进行有效的结合。石墨烯的制做工艺是在一条线上完成,这就对载体及压延离型膜有更多性能上的要求。随着散热效果的快速提高,很多石墨厂家开始研究超厚度的石墨烯进行导热,普通石墨烯是通过烧结后直接将成型的石墨烯卷料通过压延机器附着在专用的离型膜上进行压光处理的一种工艺,这种石墨烯有一个特点就石墨烯的厚度难以提高,市场上超厚石墨烯的都是通过两层石墨烯复合而成,此工艺复杂,成本较高。针对现在市场超厚度的石墨烯产品(100um以上),目前市场上的离型膜产品大多都是硅油性质类的涂层离型膜,大都在1μm左右的厚度,太薄容易压不住发生脱膜现象,且石墨烯涂布在其上会有缩孔,涂布性不好,不耐高温,剥离克重重且不稳定,无法满足超厚石墨烯产品。
技术实现要素:3.发明目的:针对现有技术中存在的问题,本发明提供一种用于石墨烯载体的压延离型膜及其制备方法,该离型膜厚度较厚,与石墨烯的表面亲和力较好,一种厚度的离型膜能够适用于压制不同厚度的石墨烯,且该离型膜对石墨烯具有较好的吸附力。
4.技术方案:本发明提供了一种用于石墨烯载体的压延离型膜,包括基材层和粘合在所述基材层表面的离型层,其特征在于,所述离型层的涂布料液由以下重量份的组分配制而成:28~50份苯基硅油、28~35份硅胶树脂和1~3份甲基硅树脂混合后,加入35~43份的有机溶剂充分搅伴分散,最后加入1~3份交联助剂、1~2份附着助剂和2~3份铂金催化助剂整体混合而成。
5.优选地,所述有机溶剂为120号溶剂油。
6.本发明还提供了一种用于石墨烯载体的压延离型膜的制备方法,包括以下步骤:
将所述的离型层的涂布料液通过网辊涂布到经电晕处理、达因值大于48的基材层表面,所述离型层的涂布料液通过所述网辊的网格转移到所述基材层的表面,从而形成具有网格的离型层;其中,在将所述网辊的网格转移到所述基材层的表面时,刮刀的角度为40-43
°
,橡胶辊的气压设置在3.0~4.0pa;涂布量为0.5~0.65g/m2;在涂布时六节烘箱的烘烤温度分别为:115~125℃、135~145℃、145~155℃、135~145℃、115~125℃、95~105℃,涂布时所述基材层的传输速度为45~55m/min;总涂布的烘烤时长为40~50s。
7.优选地,所述基材层的厚度为50um~70um。
8.优选地,所述离型层的厚度为3.5~4.5μm。
9.优选地,所述网辊的网格尺寸为150目。
10.优选地,所述基材层为pet膜。
11.有益效果:本离型膜以厚度50um~70um的pet为基材,对基材进行表面电晕处理后,使其表面达因值大于48;通过对本离型层配方中苯基硅油、硅胶树脂和甲基硅树脂比例的调整,达到对表面涂层性能的优化,表面能高,表面软硬度与石墨稀表面能有很好的亲合,石墨烯涂布至该离型膜表面表现出很好的涂布效果,石墨烯在涂布时不会有缩孔现象。
12.该离型膜的离型层厚度控制在4μm左右,离型层的涂层中每平方米含10克以上的干硅量,离型克重比普通的压延膜(离型克重为500-700)要轻100-150克,但是压延后的效果要比普通好。
13.利用该离型膜的离型层较厚的这一特点,能有效的满足超厚石墨烯材料的载体涂布和压延工艺,且由于与石墨烯表面的亲和力较好,一种离型膜能适用于压延多种厚度的石墨烯。
14.在使用本离型膜时,是将配制好的石墨烯浆料通过专用的设备进行均匀的涂布在本技术中的离型膜表面,该离型膜承载着石墨烯进行高温烘烤固化,固化后再通过压光机进行压光处理并收卷待用;涂布,固化,压光一次性完成,能有效的节省成本,提高工作效率。通过二次高温后该离型膜还可以具有很好的剥离效果,与石墨烯料液之间不发生任何的交联和残留,耐热效性高,剥离强度好,剥离克重轻,不同体系的树脂材料在涂层里起到不同的效果,苯基硅油起到离型效果,硅胶树脂具有超低微粘力的特性,通过这两种不同比例的调节能有效的具有低微粘力和剥离力的特性。甲基硅树脂具有表面软硬度的调节作用。通过此方法和不同比例所制得的石墨烯载体离型膜剥离数据稳定,不残留,耐酸咸,涂层表面具有微吸附力,透明度好,表面流平性强,能很好的压制超厚度的石墨烯,所压石墨烯的光泽度高。表面吸附性好,涂层较厚,光泽度高,在石墨烯的制作工艺中起着重要的作用。
15.本离型膜由于涂层表面性能优秀,具备微粘与离型双重特性,在石墨烯的制做过程中,能有很好的使用效果,使得石墨烯的载体和压延能够一次性完成。
附图说明
16.图1为本技术中用于石墨烯载体的压延离型膜的涂布工艺示意图;
17.图2为表面具有石墨烯的压延离型膜的示意图。
具体实施方式
18.下面结合附图对本发明进行详细的介绍。
19.以下具体实施方式中使用的原料来源和型号如下:
20.苯基硅油:陶氏公司,型号为9106,分子量在1200-2000;
21.硅胶树脂:埃肯公司,型号为7413;
22.甲基硅树脂:陶氏公司,型号为7210
23.120号溶剂油:一种具有溶解特性的有机溶剂油;
24.交联助剂:陶氏公司,型号为7028;
25.附着助剂:陶氏公司,型号为297;
26.铂金催化助剂:陶氏公司,型号为4000。
27.实施方式1:
28.本实施方式提供了一种用于石墨烯载体的压延离型膜,包括依次层叠粘合的基材层和离型层,该离型层的涂布料液由以下重量份的组分配制而成:30份苯基硅油、30份硅胶树脂和2份甲基硅树脂混合后,加入40份的120号溶剂油充分搅伴分散,最后加入3份含氢体的交联助剂、1.5份附着助剂和2.2份铂金催化助剂整体混合而成。
29.使用上述离型层的涂布料液制备用于石墨烯载体的压延离型膜的方法如下:
30.将上述离型层的涂布料液1通过150目的网辊2涂布到经电晕处理、达因值达到48以上的pet基材层3表面,离型层的涂布料液1通过网辊2的网格转移到基材层3的表面,基材层3厚度为60μm;形成具有网格的厚度为4μm的离型层4。
31.其中,在将网辊2的网格转移到基材层3的表面时,刮刀5的角度为40-43
°
,橡胶辊6的气压设置在3.5pa,涂布量为0.6g/m2;
32.在涂布时六节烘箱的烘烤温度分别为:120℃、140℃、150℃、140℃、120℃、100℃,涂布时基材的传输速度为50m/min;总涂布时间为50s。
33.实施方式2:
34.本实施方式与实施方式1大致相同,不同点仅在于,本实施方式中,用于石墨烯载体的压延离型膜的离型层的涂布料液配方中,苯基硅油为50份。除此之外,本实施方式与实施方式1完全相同,此处不做赘述。
35.实施方式3:
36.本实施方式与实施方式1大致相同,不同点仅在于,本实施方式中,用于石墨烯载体的压延离型膜的离型层的涂布料液配方中,苯基硅油为40份、甲基硅树脂为3份。除此之外,本实施方式与实施方式1完全相同,此处不做赘述。
37.对比例:
38.本实施方式与实施方式1大致相同,不同点仅在于,本实施方式中,用于石墨烯载体的压延离型膜的离型层的涂布料液配方中,苯基硅油为50份、硅胶树脂为30份,甲基硅树脂为2份。除此之外,本实施方式与实施方式1完全相同,此处不做赘述。
39.对上述各实施方式和对比例制备出的用于石墨烯载体的压延离型膜用在厚度分别为100μm、120μm、150μm的石墨烯压延工艺中,然后对压延后得到的石墨烯压延离型膜产品的离型克进行测试,测试结果如下表1:
40.表1
[0041][0042][0043]
从表1可以看出不同比例树脂的加入量,使石墨烯的制作过程中有明显的差别,通过试验可能,按实施方式1的比例所测得的数据最为理想化。表面剥离的力度和表面的光泽程度都有明显和不同。
[0044]
上述实施方式只为说明本发明的技术构思及特点,其目的在于让熟悉此项技术的人能够了解本发明的内容并据以实施,并不能以此限制本发明的保护范围。凡根据本发明精神实质所做的等效变换或修饰,都应涵盖在本发明的保护范围之内。