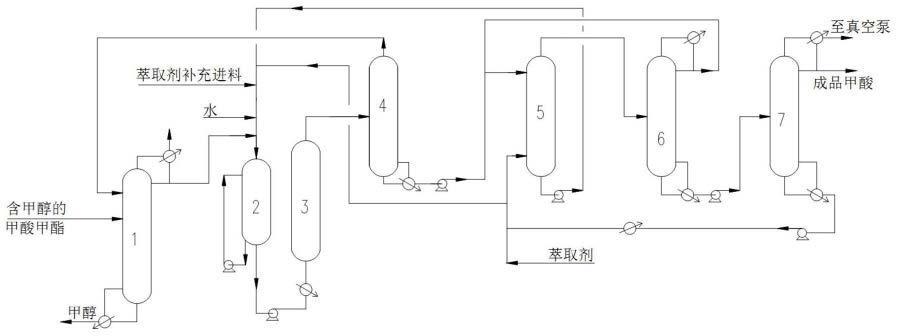
1.本发明涉及甲酸生产技术领域,尤其涉及一种甲酸的生产系统及生产工艺。
背景技术:2.这里的陈述仅提供与本发明相关的背景技术,而不必然地构成现有技术。
3.甲酸是一种重要的化工原料,可广泛用于化工、医药、农药、皮革、纺织、橡胶、塑料等行业。通过甲酸甲酯水解制取甲酸是目前普遍采用的方法。但由于甲酸甲酯水解平衡常数较低,水解得到的甲酸和甲醇在精馏分离过程中很容易发生再酯化反应又重新生成甲酸甲酯;同时以反应产物甲酸作催化剂抑制了正反应的进行,转化率较低,大量的甲酸甲酯需精馏分离后循环使用,导致负荷较大,能耗较高。
4.此外,甲酸(沸点为100.8℃)与水的沸点接近,二者易形成共沸物,导致精馏提纯困难。采用加(常)压精馏与减压精馏多塔串联的方法虽然能实现甲酸和水的有效分离,得到较高浓度的甲酸,但该方法对加热蒸汽的消耗量大,且需要较大的设备投资及操作费用。
技术实现要素:5.针对现有技术存在的不足,本发明的目的是提供一种甲酸的生产系统及生产工艺,在甲酸甲酯的水解过程中加入萃取剂,萃取剂的加入不仅能打破甲酸甲酯水解平衡,促进甲酸甲酯单程转化率,同时实现混合物料中甲酸和大部分水的直接分离,解决多塔串联精馏,蒸汽消耗量大的问题。
6.为了实现上述目的,本发明是通过如下的技术方案来实现:
7.第一方面,本发明提供一种甲酸的生产系统,包括预混合器和水解反应器,所述预混合器的进口分别与甲酸甲酯源、萃取剂源和水源连接,预混合器的出口与所述水解反应器连接。
8.第二方面,本发明提供一种甲酸的生产方法,包括如下步骤:
9.甲酸甲酯、萃取剂和水混合后投加至水解反应器中进行催化水解,其中所述萃取剂为弱碱性铵盐,优选为n,n-二丁基甲酰胺。
10.上述本发明的一种或多种实施例取得的有益效果如下:
11.(1)在甲酸甲酯水解之前,加入一定比例的萃取剂,能有效控制水解过程混合物料中甲酸的浓度,一方面萃取剂与部分甲酸发生螯和,缓解了反应产物中甲酸浓度过高对正反应的抑制作用,另一方面一定浓度甲酸含量保证了对水解反应的催化作用,提高了甲酸的水解转化率。
12.(2)萃取塔中过量萃取剂的加入实现了甲酸与大部分水的直接分离,解决了甲酸和水共沸精馏分离难度大的问题,与传统的工艺流程相比,采用该工艺制取高浓度甲酸,吨甲酸蒸汽量消耗明显降低。
13.(3)萃取剂由减压精馏塔底采出,可循环使用,整个工艺过程,基本无损耗,长时间运转仅需少量补充,降低了投资。
14.(4)此工艺为连续操作,提高了生产能力,能耗降低效果明显。
附图说明
15.构成本发明的一部分的说明书附图用来提供对本发明的进一步理解,本发明的示意性实施例及其说明用于解释本发明,并不构成对本发明的不当限定。
16.图1是本发明根据一个或多个实施方式的甲酸生产系统的整体结构示意图。
17.图中:为显示各部位位置而夸大了互相间间距或尺寸,示意图仅作示意使用;
18.其中,1-甲酯精馏塔,2-预混合器,3-水解反应器,4-脱酯塔,5-萃取塔,6-脱水塔,7-减压精馏塔。
具体实施方式
19.应该指出,以下详细说明都是例示性的,旨在对本发明提供进一步的说明。除非另有指明,本发明使用的所有技术和科学术语具有与本发明所属技术领域的普通技术人员通常理解的相同含义。
20.第一方面,本发明提供一种甲酸的生产系统,包括预混合器和水解反应器,所述预混合器的进口分别与甲酸甲酯源、萃取剂源和水源连接,预混合器的出口与所述水解反应器连接。
21.在一些实施例中,所述水解反应器内设置有加热盘管,盘管为上下分层布置,层与层间隔为4-5.5米。利于控制反应温度,减小反应器内上下温差,保证水解过程平稳进行,提高甲酸单程转化率,反应温度80~120℃。
22.在一些实施例中,所述萃取剂为弱碱性铵盐。
23.优选的,所述萃取剂为n,n-二丁基甲酰胺。该物质引入甲酸甲酯水解过程后,可以通过氢键桥接与甲酸形成一种加成化合物,进而降低系统中游离甲酸浓度,提高甲酸甲酯单程转化率;后续萃取过程大量萃取剂的投入,降低了混合物料脱水的难度,同时通过真空状态下的加热解离,实现了甲酸的提纯制备及萃取剂的循环利用。
24.在一些实施例中,所述甲酸甲酯源为甲酯精馏塔。甲酯精馏塔用于对羰基化反应制备得到的甲酸甲酯进行精馏,以制备得到较为纯净的甲酸甲酯。
25.优选的,还包括脱酯塔,脱酯塔中部与水解反应器的顶部连接。
26.进一步优选的,所述脱酯塔为填料塔。塔釜采出甲酸、萃取剂和水,甲醇及甲酯在塔顶采出,循环至甲酯精馏塔分离。
27.进一步优选的,所述脱酯塔的顶部与所述甲酯精馏塔连接。
28.进一步优选的,还包括萃取塔,脱酯塔塔釜与萃取塔上部进口连接。脱酯塔塔釜采出的甲酸、萃取剂和水的混合液进入萃取塔中进行萃取。
29.再进一步优选的,萃取塔进口与脱水塔的顶部设置的冷却器连接。
30.再进一步优选的,所述萃取塔的塔釜与萃取剂源连接。用于首次投运时,向萃取塔中添加萃取剂。
31.再进一步优选的,萃取塔的顶部与所述脱水塔中部连接。
32.更进一步优选的,萃取塔塔釜与所述预混合器的顶部连接。
33.甲酸与萃取剂螯和形成轻组分,由塔顶溢流进入脱水塔中部;塔釜含有少量萃取
剂的水溶液返回预混合器循环利用。
34.更进一步优选的,还包括脱水塔,脱水塔中部与萃取塔塔顶出口连接。
35.再进一步优选的,所述脱水塔的塔顶与萃取塔的中部进口连接。
36.甲酸与萃取剂中混入的少量水在脱水塔中通过加热精馏的方式实现进一步的分离,分离出来的水中含有少量甲酸,经塔顶冷却器冷凝后,返回萃取塔重新参与萃取过程。萃取剂和甲酸由脱水塔塔底采出,进入减压精馏塔。
37.再进一步优选的,还包括减压精馏塔,减压精馏塔中部与脱水塔塔釜连接。减压精馏塔塔釜采出萃取剂返回至萃取塔或预混合器循环使用,塔顶采出浓度90%以上甲酸产品。
38.优选为,减压精馏塔的塔釜与萃取塔塔釜或和预混合器连接。
39.第二方面,本发明提供一种甲酸的生产方法,包括如下步骤:
40.甲酸甲酯、萃取剂和水混合后投加至水解反应器中进行催化水解,其中所述萃取剂为弱碱性铵盐。
41.其中,甲酸甲酯来源于上一段工序羰基化反应,为获得较高的反应转化率,往往需要添加过量的甲醇。甲酸甲酯通过甲酯精馏塔实现精馏提纯,由塔顶采出,过量的甲醇由塔釜采出,循环回羰基化反应工序与补充的新鲜甲醇继续参与甲酸甲酯的生成。
42.在一些实施例中,所述弱碱性铵盐为n,n-二丁基甲酰胺。
43.在一些实施例中,甲酸甲酯、萃取剂和水的摩尔比为5-6:1:10-18。
44.甲酸甲酯、萃取剂和水的摩尔比可以为5:1:10、6:1:10、5:1:11、5:1:12、5:1:13、5:1:14、5:1:15、5:1:16、5:1:17、5:1:18、6:1:11、6:1:12、6:1:13、6:1:14、6:1:15、6:1:16、6:1:17、6:1:18。
45.水解过程中加入一定量的萃取剂,能有效控制混合物料中甲酸的浓度,一方面保证了甲酸在甲酸甲酯水解过程中的自催化作用,另一方面缓解反应产物中甲酸浓度过高对正反应的抑制作用,提高了甲酸的单程转化率。需要注意的是混合物料中萃取剂占比过大,不利于后续对甲醇、甲酸甲酯的分离,增加了成本,造成不必要的浪费。
46.在一些实施例中,水解反应的温度为80-120℃,水解过程压力控制在1.2-1.5mpa。
47.在一些实施例中,水解产物混合液通过填料塔对甲醇及未反应的甲酸甲酯进行精馏分离,甲酸、萃取剂和水由脱脂塔塔釜采出。甲醇及甲酯在塔顶采出,直接以气相返回至甲酯精馏塔,实现循环利用的同时,进行了余热回收。
48.在一些实施例中,脱脂塔塔釜采出的混合物料经过冷却,并向其中补充大量萃取剂后,进行液-液萃取。
49.优选的,液-液萃取温度控制在70-80℃。
50.优选的,甲酸和萃取剂形成的轻组分物料由萃取塔顶部采出,并通过精馏过程进一步脱水。
51.进一步优选的,脱水精馏的温度为120-150℃,运行压力为常压。
52.甲酸与萃取剂中混入的少量水由脱水塔顶部采出,该部分水溶液中因含有少量甲酸,在本方法中,将其返回至萃取步骤,循环参与工艺过程,避免了需单独设置净化工序带来的处理难度和成本。
53.进一步优选的,脱水塔塔釜采出的萃取剂与甲酸的混合液进行减压精馏,将萃取
剂与甲酸分离,得到甲酸产品。
54.进一步优选的,分离得到的萃取剂返回至萃取及水解,循环利用。
55.通过流程的合理优化和设置,在甲酸的生产过程中基本实现了废水、废物的“清零”,具有良好的环境、经济效益。
56.下面结合附图和实施例对本发明作进一步说明。
57.实施例1
58.预混合器2的进口分别与甲酯精馏塔1、萃取剂源和水源连接,预混合器2的出口与所述水解反应器3连接;脱酯塔4为填料塔,其中部与水解反应器3的顶部连接,脱酯塔4的顶部与所述甲酯精馏塔1连接。
59.脱酯塔4塔釜与萃取塔5上部进口连接。脱酯塔4塔釜采出的甲酸、萃取剂和水的混合液进入萃取塔5中进行萃取。
60.水解反应器3内设置有加热盘管,盘管为上下分层布置,层与层间隔不超过5.5米,利于控制反应温度,减小反应器内上下温差,保证水解过程平稳进行,提高甲酸单程转化率,反应温度控制在80~120℃。
61.萃取塔5塔釜与所述预混合器2的顶部连接,甲酸与萃取剂螯和形成轻组分,由塔顶溢流进入脱水塔6;塔底含有少量萃取剂的水溶液返回预混合器2循环利用。
62.脱水塔6顶部设有冷却器,与萃取塔5塔上部进口连接。脱水塔6中部与萃取塔5塔顶出口连接,脱水塔6将甲酸与萃取剂中混入的少量水份进一步分离,分离出来的水返回萃取塔5重新参与萃取过程。萃取剂和甲酸由脱水塔6塔底采出,进入减压精馏塔7。
63.减压精馏塔7中部与脱水塔6塔釜连接。减压精馏塔7塔釜采出萃取剂返回至萃取塔和预混合器循环利用,塔顶采出浓度90%以上甲酸产品。
64.含甲醇的甲酸甲酯进入甲酯精馏塔1分离,回流比3,理论板数45,经分离处理后得到97wt%甲酸甲酯。控制水和甲酸甲酯摩尔比2.6:1,甲酸甲酯与萃取剂n,n-二丁基甲酰胺摩尔比5.5:1,进入水解反应器,反应温度100℃,反应压力1.2mpag,甲酸甲酯单程水解率42.2%;脱酯塔理论板数40,回流比2;萃取塔控制反应温度80℃,萃取剂占比55%;脱水塔理论板数17,回流比0.9;减压精馏塔理论板数15,回流比2.5,最终得到到甲酸产品质量分数95.5%,吨甲酸(以质量分数100%甲酸计)蒸汽量消耗降低约4.65t。
65.实施例2
66.含甲醇的甲酸甲酯进入甲酯精馏塔分离,回流比4,理论板数30,经分离处理后得到97wt%甲酸甲酯;控制水和甲酸甲酯摩尔比3:1,甲酸甲酯与萃取剂n,n-二丁基甲酰胺摩尔比5.7:1,进入水解反应器,反应温度110℃,反应压力1.2mpag,甲酸甲酯单程水解率40.8%;脱酯塔理论板数50,回流比2;萃取塔控制反应温度85℃,萃取剂占比55%;脱水塔理论板数25,回流比1.5;减压精馏塔理论板数25,回流比1.5,最终得到到甲酸产品质量分数97.0%,吨甲酸(以质量分数100%甲酸计)蒸汽量消耗降低约4.95t。
67.实施例3
68.含甲醇的甲酸甲酯进入甲酯精馏塔分离,回流比4,理论板数30,经分离处理后得到95wt%甲酸甲酯;控制水和甲酸甲酯摩尔比3:1,甲酸甲酯与萃取剂n,n-二丁基甲酰胺摩尔比5:1,进入水解反应器,反应温度110℃,反应压力1.2mpag,甲酸甲酯单程水解率42.0%;脱酯塔理论板数50,回流比2;萃取塔控制反应温度85℃,萃取剂占比55%;脱水塔
理论板数25,回流比1.5;减压精馏塔理论板数25,回流比1.5,最终得到到甲酸产品质量分数96.5%,吨甲酸(以质量分数100%甲酸计)蒸汽量消耗降低约5.05t。
69.实施例4
70.含甲醇的甲酸甲酯进入甲酯精馏塔分离,回流比4,理论板数30,经分离处理后得到95wt%甲酸甲酯;控制水和甲酸甲酯摩尔比3.6:1,甲酸甲酯与萃取剂n,n-二丁基甲酰胺摩尔比5:1,进入水解反应器,反应温度110℃,反应压力1.2mpag,甲酸甲酯单程水解率42.3%;脱酯塔理论板数50,回流比2;萃取塔控制反应温度85℃,萃取剂占比58%;脱水塔理论板数25,回流比1.5;减压精馏塔理论板数25,回流比1.5,最终得到到甲酸产品质量分数95.5%,吨甲酸(以质量分数100%甲酸计)蒸汽量消耗降低约4.90t。
71.对比例1
72.含甲醇的甲酸甲酯进入甲酯精馏塔分离,回流比1.5,理论板数55,经分离处理后得到95wt%甲酸甲酯;水解过程不加入萃取剂,控制水和甲酸甲酯摩尔比3:1进入水解反应器,反应温度110℃,反应压力1.2mpag,甲酸甲酯单程水解率20.8%;脱酯塔理论板数50,回流比2;脱水塔理论板数25,回流比1.5;减压精馏塔理论板数25,回流比1.5,最终得到到甲酸产品质量分数81.0%,吨甲酸(以质量分数100%甲酸计)蒸汽量消耗降低约6.55t。
73.对比例2
74.与实施例1的区别在于:水解反应过程中省略萃取剂,其他均与实施例1相同,甲酸甲酯的单程水解率为19.3%。最终得到到甲酸产品质量分数83.5%。吨甲酸(以质量分数100%甲酸计)蒸汽量消耗约6.18t。
75.对比例3
76.与实施例1的区别在于:水解反应过程中,添加的萃取剂替换为甲酸苄脂,其他均与实施例1相同,甲酸甲酯的单程水解率为32.8%。最终得到到甲酸产品质量分数93.5%。吨甲酸(以质量分数100%甲酸计)蒸汽量消耗约5.91t。
77.对比例4
78.与实施例1的区别在于:水解反应过程中,添加的萃取剂替换为乙酸乙酯,其他均与实施例1相同,甲酸甲酯的单程水解率为28.9%。最终得到到甲酸产品质量分数89.0%。吨甲酸(以质量分数100%甲酸计)蒸汽量消耗约5.52t。
79.对比例5
80.与实施例1的区别在于:甲酸甲酯、萃取剂和水的摩尔比为4.5:1:12。其他均与实施例1相同,甲酸甲酯的单程水解率为42.3%。最终得到到甲酸产品质量分数95.5%。吨甲酸(以质量分数100%甲酸计)蒸汽量消耗约5.37t。
81.对比例6
82.与实施例1的区别在于:甲酸甲酯、萃取剂和水的摩尔比为4.5:1:9。其他均与实施例1相同,甲酸甲酯的单程水解率为33.2%。最终得到到甲酸产品质量分数95.0%。吨甲酸(以质量分数100%甲酸计)蒸汽量消耗约5.93t。
83.对比例7
84.与实施例1的区别在于:甲酸甲酯、萃取剂和水的摩尔比为6:1:20。其他均与实施例1相同,甲酸甲酯的单程水解率为35.5%。最终得到到甲酸产品质量分数93.0%。吨甲酸(以质量分数100%甲酸计)蒸汽量消耗约5.44t。
85.对比例8
86.与实施例1的区别在于:甲酸甲酯、萃取剂和水的摩尔比为7:1:12。其他均与实施例1相同,甲酸甲酯的单程水解率为31.8%。最终得到到甲酸产品质量分数95.5%。吨甲酸(以质量分数100%甲酸计)蒸汽量消耗约5.67t。
87.以上所述仅为本发明的优选实施例而已,并不用于限制本发明,对于本领域的技术人员来说,本发明可以有各种更改和变化。凡在本发明的精神和原则之内,所作的任何修改、等同替换、改进等,均应包含在本发明的保护范围之内。