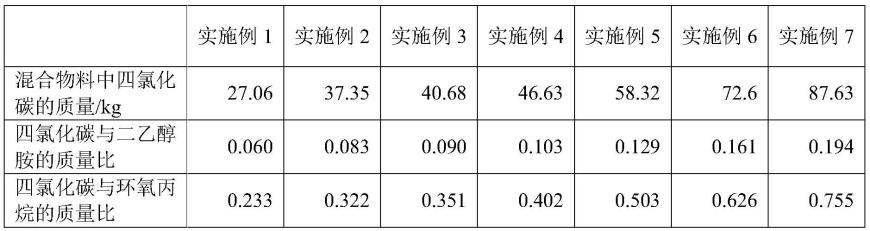
1.本技术涉及水泥外加剂生产的领域,尤其是涉及一种二乙醇单异丙醇胺的生产工艺。
背景技术:2.二乙醇单异丙醇胺是一种应用广泛的化工原料以及中间品,大量的使用在水泥外加剂以及二氧化碳捕捉剂,对此使用过程中对二乙醇单异丙醇胺纯度要求较高,行业对二乙醇单异丙醇胺的生产工艺从工艺路线、物料混合、产品的分离提纯等角度进行研究。
3.目前较为热门的研究方向是以二乙醇胺与环氧丙烷作为原料进行生产。以反应釜为反应器,向温度低于10℃的环氧丙烷中加入二乙醇胺,将两者混合,以低温抑制副反应发生产生高沸点的副反应产物。待二乙醇胺溶解或均匀分散在环氧丙烷内后再升温进行反应,使得在反应器内反应位置几乎是均匀分布在混合物料中的,反应接触更为充分,主反应速率快,副反应环氧丙烷发生少,最后通过减压蒸馏后得到的产品二乙醇单丙醇胺。
4.针对上述中的相关技术本技术发明人试验中发现:由于常压下二乙醇胺的熔点为28℃,二乙醇胺与10℃以下的温度的环氧丙烷混合,二乙醇胺接触到环氧丙烷后快速降温凝固,导致二乙醇胺与环氧丙烷之间的混溶速度慢,同时混合过程中还需要外界供冷控制反应器内温度,也是进一步制约了混溶速度,即使现有工业技术提供机械搅的情况下,也需要较长的时间来完成二乙醇胺与环氧丙烷的混合,导致了实际生产周期长的问题。
技术实现要素:5.为了提高二乙醇胺与环氧丙烷合成二乙醇单异丙醇胺的生产效率,本技术提供一种二乙醇单异丙醇胺的生产工艺。
6.本技术提供的一种二乙醇单异丙醇胺的生产工艺采用如下的技术方案:一种二乙醇单异丙醇胺的生产工艺,包括以下步骤:s1:将温度为2~4℃的环氧丙烷加入反应器中,以惰性气体调压,反应器内压力为0.1~0.12mpa,再向反应器内加入混合物料,混合物料的温度为28~30℃,所述混合物料中二乙醇胺与四氯化碳总质量占比大于99wt%,且所述混合物料中二乙醇胺与四氯化碳的质量比为1:(0.06~0.2),保持对反应器制冷,维持反应器内温度为4~6℃,混合环氧丙烷和混合物料直至混合均匀,得到反应物料;s2:升温反应物料至30℃,保持搅拌升温至68~72℃,维持温度68~72℃,继续保温反应2~3h,得到二乙醇单异丙醇胺粗品。
7.通过采用上述技术方案:二乙醇胺与四氯化碳先混合成混合物料,在混合物料升温至28~30℃的过程中,四氯化碳溶解二乙醇胺,加速二乙醇胺融化;混合成液态的混合物料后,四氯化碳降低了混合物料的凝固点,减缓混合物料接触低温的环氧丙烷而凝固的现象;
混合物料与环氧丙烷混合时,四氯化碳可促进环氧丙烷和二乙醇胺互溶,即使在反应器温度维持于4~6℃时,四氯化碳就可促进环氧丙烷、二乙醇胺快速高效的混合,显著缩短混合时间,缩短生产周期及降低制冷能耗耗能。
8.另一方面,混合物料与环氧丙烷混合均匀得到反应物料后,反应物料升温,环氧丙烷与二乙醇胺合成二乙醇单异丙醇胺的主反应快速发生,该反应为放热反应,随反应发生反应物料温度不断上升。实际生产过程中虽有冷却装置控制反应器内温度,但受反馈机制决定,所控制的反应温度实际是反应器内整体温度或多个反应器内位点温度的反映结果,反应器内依旧存在主反应在局部位点过烈导致的局部温度过高的情况,局部温度过高会使副反应在该局部同样加剧发生。这种局部温度过高的发生难以阻止——由于某一区域浓度富集,导致局部反应过烈、随反应进行浓度降低,反应减缓,温度下降,现有技术无法做到单个分子与单个分子间级别的混合配制、局部反应过烈必然出现但无法预料。
9.本技术中加入的四氯化碳,在本技术工艺压力下与反应控制的最佳温度相近并高于反应控制的最佳温度、低于二乙醇胺和二乙醇单异丙醇胺的沸点,故而在局部反应过烈导致的局部温度过高,该区域内的四氯化碳快速吸收区域内的热能作为潜化热,由液态转化为等同温度的气态,转移二乙醇单异丙醇胺生成的反应热,抑制局部反应继续过烈,减少局部温度过高发生,进而减少副反应的产生,提高产品纯度和收率。
10.进一步选择的,还包括:s3:二乙醇单异丙醇胺粗品通过减压精馏在内的提纯步骤,得到二乙醇单异丙醇胺产品;所述减压蒸馏先后包含分离四氯化碳及其他轻组分的轻组分分离、分离二乙醇胺的精分离。
11.通过采用上述技术方案,二乙醇单异丙醇胺粗品的减压蒸馏提纯将四氯化碳及其他轻组分的分离与二乙醇胺的分离划分为两步进行,降低了设备要求,避免在单个精馏塔/精馏柱内实现轻组分、四氯化碳、二乙醇胺、二乙醇单异丙醇胺的同时分离,避免了“巨型精馏塔”(直径大于5m)或“细高精馏塔”(直径小于1m,高度大于60m)等不合适、不合理的设备设计要求,同时精馏塔的塔板分离效率更高,组分分离效果更好,尤其是分离出的二乙醇胺纯度高,四氯化碳含量少,回收利用时配制混合物料时更为方便,无需对每批次二乙醇胺均进行检测。
12.进一步选择的,所述反应器内环氧丙烷用量为100kg~200kg时,四氯化碳与二乙醇胺的用量质量比为(0.103-0.129):1。
13.进一步选择的,所述反应器内环氧丙烷用量为1~2t时,四氯化碳与二乙醇胺的用量质量比为(0.161-0.194):1。
14.通过采用上述技术方案,本技术发明人在小试、中试过程中发现本技术工艺中四氯化碳的投入量与生产规模、环氧丙烷/二乙醇胺比例相关,且并非四氯化碳投入量越多越好。例如:对生产周期和能耗而言,反应物料中四氯化碳的用量增加,会增强促进环氧丙烷、二乙醇胺混合的效果;但随四氯化碳的量超过一个阈值后,促进环氧丙烷、二乙醇胺混合效果的提升明显减缓甚至不在继续提升,对混合时间的缩短效果不在提升,此后四氯化碳用量的继续增加,对混合物料加入反应器前加热的能耗、反应器内混合时维持温度的制冷能耗、后续分离时加热能耗、物料成本、输送动力成本而言并不能得到正向的收益,另一方面
因四氯化碳的稀释作用导致反应速率下降,反应需要的时长会加长;对产品纯度和收率而言,反应物料中四氯化碳的用量增加,因四氯化碳对局部反应过烈的抑制效果,产品纯度和收率会提高,而后用量继续增大,四氯化碳对局部反应过烈的抑制效果提升反映在产品存纯度上的提升趋于极限,纯度达到峰值后出现较弱趋势的降低,本技术发明人认为加大可能是由于四氯化碳用量过多,对环氧丙烷、二乙醇胺合成二乙醇单丙醇胺原料稀释导致主反应反应进度降低的影响大于混合均匀提高主反应反应进度的影响;收率也是呈相同的反应结果,但收率反降低的峰值与纯度峰值出现的四氯化碳用量并不相同;同时不同体量的生产规模量级下,受搅拌混合现有技术影响,不同生产规模下的混合流体模型不同,对二乙醇单异丙醇胺生产效率、产品纯度的较优方案,在不同生产规模量级时四氯化碳、二乙醇胺、环氧丙烷之间的比例关节节点是不同的。
15.本技术发明人在研究过程中确定了,二乙醇胺与环氧丙烷混合时,四氯化碳受二乙醇胺与环氧丙烷之间的比例、二乙醇胺与环氧丙烷总用量为主影响,对生产而言在相同生产周期下产品纯度、收率较为重要,以四氯化碳对副反应产物产生的抑制影响考虑,副反应主要由于环氧丙烷聚合导致,环氧丙烷在生产过程中又趋于反应完毕,故环氧丙烷的量反映了反应过程中发热的量以及副反应产物可能产生的量,故本技术发明人以环氧丙烷作为四氯化碳用量的第二关联对象,进行了试验,最终得出:反应器内环氧丙烷用量为1~2t时,反应物料中四氯化碳与二乙醇胺的用量质量比为(0.161-0.194):1,在短生产周期下可获得较优的产品纯度、收率;反应器内环氧丙烷用量为100kg~200kg时,四氯化碳与二乙醇胺的用量质量比为(0.103-0.129):1,在短生产周期下可获得较优的产品纯度、收率;本技术工艺生产规模逐步发大过程中,产品纯度、收率的效益最佳点所用的四氯化碳用量比是增大的。
16.进一步选择的,所述混合物料中还混合有石墨粉末,所述石墨粉末占混合物料质量的0.048~0.062wt%,所述石墨粉末粒径为1~8μm。
17.通过采用上述技术方案,在大量级生产规模时,在混合物料中混入石墨粉末有利于增效二乙醇胺和环氧丙烷混合——石墨粉末在混合过程中在液体中上下游走,撞击液相界面,增效液相混合,以抑制副反应发生的方式提高产品的纯度和收率。
18.进一步选择的,还包括:s3:二乙醇单异丙醇胺粗品通过减压精馏、固体物过滤在内的提纯步骤后,得到二乙醇单异丙醇胺产品;所述减压蒸馏先后包含分离四氯化碳及其他轻组分的轻组分分离、分离二乙醇胺的精分离;所述固体物过滤包括对二乙醇胺单异丙醇胺粗品精分离后的液相中固体物质过滤分离。
19.生产过程中发现混合物料中混入石墨粉末后,二乙醇胺单异丙醇胺粗品精分离后的液相底部有固体沉淀,固体沉淀成分主要为石墨粉末、高沸点副反应产物。
20.通过采用上述技术方案,石墨粉末还以辅助高沸点副反应产物从产品中脱离的方式提高产品纯度。轻组分分离后物料中主要成分为二乙醇单异丙醇胺、二乙醇胺,还有微量的高沸点的副反应产物杂质。精分离时二乙醇胺不断被分离,高沸点的副反应产物杂质被
富集,小于1μm粒径的石墨粉末作为核点,高沸点的副反应产物杂质以石墨粉末为核聚集,从液相中脱离,形成沉淀,被后续的过滤去除,故而从商品中去除石墨粉末和高沸点副反应产物,提高产品纯度。
21.进一步选择的,二乙醇单异丙醇胺粗品减压蒸馏前,先过滤从液相中分离粒径大于1μm的石墨粉末。
22.通过采用上述技术方案,石墨粉末在减压蒸馏前进行过滤,截留粒径大于1μm的石墨粉末,而小于1μm粒径的石墨粉末继续随物料进入减压蒸馏。提前过滤分离较大粒径(粒径不小于1μm)的石墨粉末,避免石墨粉末在减压蒸馏塔塔底富集影响物料循环和输送,另一方面减少了精分离后过滤的固体物质量。
23.进一步选择的,二乙醇单异丙醇胺粗品减压蒸馏前过滤的石墨粉末回收利用。
24.本技术中石墨粉末对高沸点副反应产物的脱除,是需要石墨粉末随反应物料一同在反应过程中混合,使石墨粉末表面发生改性后才具备的,对二乙醇单异丙醇胺粗品减压蒸馏前过滤的石墨粉末,其表面未附着高沸点的副反应产物沉淀,可回收利用,降低成本。
25.综上所述,本技术包括以下至少一种有益技术效果:1.本技术中二乙醇胺与四氯化碳先混合成混合物料并融化,再与低温的环氧丙烷混合均匀,在此过程中四氯化碳促进二乙醇胺融化、促进环氧丙烷与二乙醇胺快速高效的混合显著缩短混合时间,缩短生产周期及降低制冷能耗耗能,同时四氯化碳在本技术工艺压力下,抑制局部反应继续过烈,减少局部温度过高发生,进而减少副反应的产生,提高产品纯度和收率;2.本技术生产工艺在大量级生产规模时,在混合物料中混入石墨粉末,可增效物料混合以抑制副反应、辅助高沸点副反应产物分离,两方面进一步提高产品的纯度和收率。
具体实施方式
26.实施例1一种二乙醇单异丙醇胺的生产工艺,包括以下步骤:s1:将温度为3℃的环氧丙烷加入反应器中,反应器为反应釜,反应釜内容积为1.15m3,内直径为1.15m,选用锚式搅拌浆,浆直径d为0.95m,浆高h为0.9m;环氧丙烷加入量为116kg,使用氮气调压,调节反应釜内压力为0.1mpa,再向反应器内加入混合物料;混合物料的温度为29℃,混合物料为预先混合好的二乙醇胺和四氯化碳,其中二乙醇胺用量为451kg,四氯化碳用量为27.06kg;混合混合物料与环氧丙烷,搅拌速度为50r/min,保持对反应器制冷,维持反应器内温度为5
±
1℃,混合20min后得到反应物料;s2:升温反应物料至30℃,保持搅拌升温至70℃,维持温度70
±
1℃,继续保温反应2h,得到二乙醇单异丙醇胺粗品;s3:二乙醇单异丙醇胺粗品加入蒸馏釜中利用精馏柱分离装置进行轻组分分离,精馏柱规格:内管h=50cm、内径φ=3cm、填料为θ环、填料高度为32cm,塔顶真空度为0.09mpa,塔釜温度为70℃,分离四氯化碳和其他轻组分后得到初分离物料;s4:初分离物料加入另一蒸馏釜中利用精馏柱分离装置进行精分离,精馏柱规格:
内管h=180cm、内径φ=5cm、填料为θ环、填料高度为95cm,塔顶真空度为0.09mpa,塔釜温度为156
±
3℃,塔顶温度65~68℃,回流比为2:1,分离二乙醇胺后得到产品二乙醇单异丙醇胺。
27.实施例2-实施例7一种二乙醇单异丙醇胺的生产工艺,基于实施例1的基础上,调节了四氯化碳的用量,包括反应器规格在内的工艺参数相同。
28.实施例1~7的部分工艺参数如下表表1所示。
29.表1.实施例1~7的工艺参数表对比例1一种二乙醇单异丙醇胺的生产工艺,包括以下步骤:s1:将温度为3℃的环氧丙烷加入反应器中,反应器为反应釜,反应釜内容积为1.15m3,内直径为1.15m,选用锚式搅拌浆,浆直径d为0.95m,浆高h为0.9m;环氧丙烷加入量为116kg,使用氮气调压,调节反应釜内压力为0.1mpa,再向反应器内加入二乙醇胺;二乙醇胺的温度为29℃,用量为451kg;混合二乙醇胺与环氧丙烷,搅拌速度为50r/min,保持对反应器制冷,维持反应器内温度为5
±
1℃,混合20min后得到反应物料;s2:升温反应物料至30℃,保持搅拌升温至70℃,维持温度70
±
1℃,继续保温反应2h,得到二乙醇单异丙醇胺粗品;s3:二乙醇单异丙醇胺粗品加入蒸馏釜中利用精馏柱分离装置进行分离,精馏柱规格:内管h=50cm、内径φ=3cm、填料为θ环、填料高度为32cm,塔顶真空度为0.09mpa,塔釜温度为70℃,分离轻组分后得到初分离物料;s4:初分离物料加入另一蒸馏釜中利用精馏柱分离装置进行分离,精馏柱规格:内管h=180cm、内径φ=5cm、填料为θ环、填料高度为95cm,塔顶真空度为0.09mpa,塔釜温度为156
±
3℃,塔顶温度65~68℃,回流比为2:1,分离二乙醇胺后得到产品二乙醇单异丙醇胺。
30.对比例2~6一种二乙醇单异丙醇胺的生产工艺,与对比例1的区别之处在于对比例2~6中二乙醇胺与环氧丙烷在5
±
1℃下的混合时间不同,具体如下表2所示。
31.表2.对比例1~6中二乙醇胺与环氧丙烷在5
±
1℃下混合时间 对比例1对比例2对比例3对比例4对比例5对比例6混合时间/min203045556575
对实施例1~7和对比例1~3的中间物料以及二乙醇单异丙醇胺进行检测,检测内容如下。
32.反应物料混合情况检测对每一例的制备好的反应物料进行取样检测,取样位点随机,每一例取样20个样品,由于不同温度压力下液体体积有微量的变化以及环氧丙烷易挥发,故检测对象确定为二乙醇胺的质量百分比。以20个样品的二乙醇胺的质量百分比作为抽样值、以二乙醇胺完全混合均匀情况下的理论值为平均值,计算相对平均偏差,以相对平均偏差作为衡量混合情况的反映指标,相对平均偏差越小,混合均匀程度越好,反之混合均匀程度越差。
33.纯度、收率检测对所得的二乙醇单异丙醇胺纯度进行检测并计算收率。
34.实施例1~7和对比例1~6的反应物料、二乙醇单异丙醇胺检测结果如下表表3所示。
35.表3.实施例1~7和对比例1~6反应物料、二乙醇单异丙醇胺检测结果表由对比例1~6可知,现有工艺中无四氯化碳添加情况下,随混合时间增长,反应物料的混合均匀情况越好,产品的纯度和收率随混合时间增长而提高,在混合时间为65~75min时,其产品纯度和收率达到较好的效益,此时产品纯度为95.23~95.34wt%,产品收率为89.52~89.87wt%。
36.对比实施例1~7和对比例1~6。
37.实施例1与对比例1对比,相同混合时间时,实施例1的物料混合情况产品纯度、产品收率均明显优于对比例1。
38.实施例1与对比例3对比,实施例1在较短的混合用时(20min)内达到与对比例3混合用时45min的相近的混合均匀程度,而实施例1产品纯度和收率优于显著对比例3。
39.对比例1~6中产品纯度、收率最优的对比例6,混合用时75min为实施例1混合用时的3.75倍,其产品纯度虽优于本技术实施例1但其产品收率低于实施例1;而且对比例6的产品纯度依旧低于实施例2。
40.对比实施例1~7可知,实施例1~7随四氯化碳的用量增加,混合均匀情况不断提高;产品纯度和收率在四氯化碳用量达到46.63kg前,随四氯化碳的用量增加而提高,在四氯化碳用量超过46.63kg后,产品纯度和收率出现缓慢的回落,但实施例7的产品纯度、收率依旧优于对比例6。
41.作为较优方案的实施例4,混合用时为20min,其产品纯度(97.21wt%)、产品收率(93.5wt%)远远高于相同混合时间的对比例1的产品纯度(85.2wt%)、产品收率(75.7wt%),而且还优于混合用时75min的对比例6产品纯度(95.34wt%)、产品收率(89.87wt%)。
42.故而本技术生产工艺中预先将四氯化碳和二乙醇胺混合成混合物料,再以混合物料与环氧丙烷混合,本工艺可促进环氧丙烷和二乙醇胺混合,显著缩短混合时间,降低制冷负荷,减少生产周期,同时还提高产品了纯度和产率。
43.实施例8-实施例14一种二乙醇单异丙醇胺的生产工艺,基于实施例1的基础上,调节了环氧丙烷、四氯化碳、二乙醇胺的用量,其他包括反应器规格在内的工艺参数均相同。环氧丙烷、四氯化碳、二乙醇胺的用量具体如下表4所示。
44.表4.实施例8-实施例14的环氧丙烷、四氯化碳、二乙醇胺用量参数 实施例8实施例9实施例10实施例11实施例12实施例13实施例14环氧丙烷的用量/kg100100100100100100100二乙醇胺的用量/kg388.79388.79388.79388.79388.79388.79388.79四氯化碳的用量/kg23.3332.2035.0740.2050.2862.5975.54
对比例7一种二乙醇单异丙醇胺的生产工艺,与对比例1的区别之处在于对比例7中环氧丙烷用量为100kg,二乙醇胺用量为388.79kg。
45.实施例15-实施例21一种二乙醇单异丙醇胺的生产工艺,基于实施例1的基础上,区别在于反应器为反应釜,反应釜内容积为1.85m3,内直径为1.35m,选用锚式搅拌浆,浆直径d为1.2m,浆高h为1.1m,并调节环氧丙烷、四氯化碳、二乙醇胺的用量,其他工艺参数均相同。
46.环氧丙烷、四氯化碳、二乙醇胺的用量具体如下表5所示。
47.表5.实施例15-实施例21的环氧丙烷、四氯化碳、二乙醇胺用量参数 实施例15实施例16实施例17实施例18实施例19实施例20实施例21环氧丙烷的用量/kg200200200200200200200二乙醇胺的用量/kg777.59777.59777.59777.59777.59777.59777.59四氯化碳的用量/kg46.6664.4070.1480.40100.55125.17151.09
对比例8一种二乙醇单异丙醇胺的生产工艺,基于对比例1的基础上,区别在于对比例7中反应釜内容积为1.85m3,内直径为1.35m,选用锚式搅拌浆,浆直径d为1.2m,浆高h为1.1m,环氧丙烷用量为200kg,二乙醇胺用量为777.59kg。
48.对实施例8~21和对比例7~8的中间物料以及二乙醇单异丙醇胺进行检测,检测结果如下表6。表6.实施例8~21和对比例7~8反应物料、二乙醇单异丙醇胺检测结果表
ꢀ
反应物料混合情况相对平均偏差产品纯度wt%产品收率wt%实施例80.086095.6991.77实施例90.025796.8492.96实施例100.019997.4793.38实施例110.015397.4493.71实施例120.013197.2693.52实施例130.011397.1593.49实施例140.011097.0693.33对比例70.309086.7077.20实施例150.099090.5990.52实施例160.035991.6291.76实施例170.025891.9192.17实施例180.020392.1292.24实施例190.016592.1192.35实施例200.015291.9292.27实施例210.014191.7592.11对比例80.374083.5074.30
49.对比实施例8-14和对比例7可知,在100kg的环氧丙烷用量规划下本技术的方案依旧可在较短的混合时间,达到良好的混合效果,并得到优于现有技术的产品纯度和收率。
50.对比实施例15-21和对比例8可知,在200kg的环氧丙烷用量规划下本技术的方案依旧可在较短的混合时间,达到良好的混合效果,并得到优于现有技术的产品纯度和收率。
51.结合实施例1-21可知,本技术生产工艺在小规模试验生产(100kg-200kg环氧丙烷用量),本工艺可促进环氧丙烷和二乙醇胺混合,显著缩短混合时间,降低制冷负荷,减少生产周期,同时还提高产品了纯度和产率。
52.根据实施例1-21中产品纯度随四氯化碳用量、占比的增加先增加后减小,产品收率也随随四氯化碳用量、占比的增加先增加后减小,但两者趋势相同,但实际的最大峰值并不在同一四氯化碳用量、占比上。
53.就实施例1-7而言,产品产率、纯度在实施例4的四氯化碳用量、占比附近达到最优;就实施例8-14而言,产品纯度在实施例10的四氯化碳用量、占比附近达到最优,产品在实施例12的四氯化碳用量、占比附近达到最优;就实施例15-21而言,产品纯度在实施例18的四氯化碳用量、占比附近达到最优,产品在实施例19的四氯化碳用量、占比附近达到最优;故就四氯化碳用量、占比而言在不同用量下会发生变化,综合考虑用料成本,本技术在100-200kg的环氧丙烷用量规模下,四氯化碳与二乙醇胺的用量为(0.103-0.129):1。
54.实施例22一种二乙醇单异丙醇胺的生产工艺,包括以下步骤:s1:将温度为3℃的环氧丙烷加入反应器中,反应器为反应釜,反应釜内容积为9m3,内直径为2.3m,选用锚式搅拌浆,浆直径d为2.1m,浆高h为1.95m;环氧丙烷加入量为1.16t,使用氮气调压,调节反应釜内压力为0.12mpa,再向反应
器内加入混合物料;混合物料的温度为29℃,混合物料为预先混合好的二乙醇胺和四氯化碳,其中二乙醇胺用量为4.51t,四氯化碳用量为270.6kg;混合混合物料与环氧丙烷,搅拌速度为50r/min,保持对反应器制冷,维持反应器内温度为5
±
1℃,混合40min后得到反应物料;s2:升温反应物料至30℃,保持搅拌升温至70℃,维持温度70
±
1℃,继续保温反应3h,得到二乙醇单异丙醇胺粗品;s3:二乙醇单异丙醇胺粗品加入蒸馏釜中利用精馏塔分离装置进行轻组分分离,精馏塔规格:内管h=300cm、内径φ=35cm、填料为θ环、填料高度为200cm,塔顶真空度为0.09mpa,塔釜温度为75℃,分离四氯化碳和其他轻组分后得到初分离物料;s4:初分离物料加入另一蒸馏釜中利用精馏塔分离装置进行精分离,精馏塔规格:内管h=420cm、内径φ=50cm、填料为θ环、填料高度为260cm,塔顶真空度为0.09mpa,塔釜温度为156
±
3℃,塔顶温度65~68℃,回流比为2:1,分离二乙醇胺后得到产品二乙醇单异丙醇胺。
55.实施例23~28一种二乙醇单异丙醇胺的生产工艺,基于实施例1的基础上,调节了四氯化碳的用量,包括反应器规格在内的工艺参数相同。
56.实施例22~28的部分工艺参数如下表表7所示。
57.表7.实施例22~28的工艺参数表对比例9一种二乙醇单异丙醇胺的生产工艺,包括以下步骤:s1:将温度为3℃的环氧丙烷加入反应器中,反应器为反应釜,反应釜内容积为9m3,内直径为2.3m,选用锚式搅拌浆,浆直径d为2.1m,浆高h为1.95m;环氧丙烷加入量为1.16t,使用氮气调压,调节反应釜内压力为0.12mpa,再向反应器内加入二乙醇胺;二乙醇胺的温度为29℃,用量为4.51t;混合二乙醇胺与环氧丙烷,搅拌速度为50r/min,保持对反应器制冷,维持反应器内温度为5
±
1℃,混合40min后得到反应物料;s2:升温反应物料至30℃,保持搅拌升温至70℃,维持温度70
±
1℃,继续保温反应3h,得到二乙醇单异丙醇胺粗品;s3:二乙醇单异丙醇胺粗品加入蒸馏釜中利用精馏塔分离装置分离,精馏塔规格:内管h=300cm、内径φ=35cm、填料为θ环、填料高度为200cm,塔顶真空度为0.09mpa,塔釜温度为75℃,分离其他轻组分后得到初分离物料;s4:初分离物料加入另一蒸馏釜中利用精馏塔分离装置进行分离,精馏塔规格:内管h=420cm、内径φ=50cm、填料为θ环、填料高度为260cm,塔顶真空度为0.09mpa,塔釜温度为156
±
3℃,塔顶温度65~68℃,回流比为2:1,分离二乙醇胺后得到产品二乙醇单异丙醇胺。
58.对比例10~14一种二乙醇单异丙醇胺的生产工艺,基于对比例9的基础上,区别之处在于对比例10~14中二乙醇胺与环氧丙烷在5
±
1℃下的混合时间不同,具体如下表8所示。
59.表8.对比例9~14中二乙醇胺与环氧丙烷在5
±
1℃下混合时间 对比例9对比例10对比例11对比例12对比例13对比例14混合时间/min405060708090对实施例22~28和对比例9~14的中间物料以及二乙醇单异丙醇胺进行检测。
60.实施例22~28和对比例9~14的反应物料、二乙醇单异丙醇胺检测结果如下表表9所示。
61.表9.实施例22~28和对比例9~14反应物料、二乙醇单异丙醇胺检测结果表表9.实施例22~28和对比例9~14反应物料、二乙醇单异丙醇胺检测结果表由对比例9~14可知,现有工艺中无四氯化碳添加情况下,在环氧丙烷用量在1.16t的生产规模时,随混合时间增长,反应物料的混合均匀情况越好,产品的纯度和收率随混合时间增长而提高。
62.由实施例22~28和对比例9~14对比,本技术生产工艺在预先将四氯化碳和二乙醇胺混合成混合物料后再与环氧丙烷混合,可在较短时间(40min)达到对比例中混合时间为80min时达到混合均匀程度相近,而同时产品纯度和收率都优于对比例。
63.故而本技术生产工艺在预先将四氯化碳和二乙醇胺混合成混合物料后再与环氧丙烷混合,可促进环氧丙烷和二乙醇胺混合,显著缩短混合时间,降低制冷负荷,减少生产周期,同时还提高产品了纯度和产率。
64.实施例29-实施例35一种二乙醇单异丙醇胺的生产工艺,基于实施例22的基础上,调节了环氧丙烷、四氯化碳、二乙醇胺的用量,其他工艺参数均相同。环氧丙烷、四氯化碳、二乙醇胺的用量具体如下表10所示。
65.表10.实施例29-实施例35的环氧丙烷、四氯化碳、二乙醇胺用量参数 实施例29实施例30实施例31实施例32实施例33实施例34实施例35
环氧丙烷的用量/t1111111二乙醇胺的用量/t3.893.893.893.893.893.893.89四氯化碳的用量/kg233.28321.98350.69401.98502.76625.86755.43
对比例15一种二乙醇单异丙醇胺的生产工艺,基于对比例9的基础上,区别在于对比例15中环氧丙烷用量为1t、二乙醇胺用量为以3.89t。
66.实施例36-实施例42一种二乙醇单异丙醇胺的生产工艺,基于实施例22的基础上,区别在于反应釜内容积为16m3,内直径为2.8m,选用锚式搅拌浆,浆直径d为2.5m,浆高h为2.3m,并调节环氧丙烷、四氯化碳、二乙醇胺的用量,其他工艺参数均相同。
67.环氧丙烷、四氯化碳、二乙醇胺的用量具体如下表11所示。
68.表11.实施例36-实施例42的环氧丙烷、四氯化碳、二乙醇胺用量参数 实施例36实施例37实施例38实施例39实施例40实施例41实施例42环氧丙烷的用量/t2222222二乙醇胺的用量/t7.787.787.787.787.787.787.78四氯化碳的用量/kg466.55643.97701.38803.971005.521251.721510.86
对比例16一种二乙醇单异丙醇胺的生产工艺,基于对比例9的基础上,区别在于反应釜内容积为16m3,内直径为2.8m,选用锚式搅拌浆,浆直径d为2.5m,浆高h为2.3m,环氧丙烷用量为2t,二乙醇胺用量为7.78t。
69.对实施例29-42和对比例15-16的中间物料以及二乙醇单异丙醇胺进行检测,检测结果如下表12。表12.实施例29~42和对比例15~16反应物料、二乙醇单异丙醇胺检测结果表 反应物料混合情况相对平均偏差产品纯度wt%产品收率wt%实施例290.12189.0990.12实施例300.084294.1591.43实施例310.073195.1991.70实施例320.059896.1391.95实施例330.035597.0292.18实施例340.025197.0792.20实施例350.024397.0792.20对比例150.37285.1174.23实施例360.15781.7388.23实施例370.10891.1690.66实施例380.091693.3391.22实施例390.078794.6991.57实施例400.051296.5792.06实施例410.041296.9192.15实施例420.038896.9792.17对比例160.399181.2271.93
70.对比实施例28-35和对比例15可知,在1t的环氧丙烷用量规划下本技术的方案依旧可在较短的混合时间,达到良好的混合效果,并得到优于现有技术的产品纯度和收率。
71.对比实施例36-42和对比例16可知,在2t的环氧丙烷用量规划下本技术的方案依旧可在较短的混合时间,达到良好的混合效果,并得到优于现有技术的产品纯度和收率。
72.结合实施例22-42可知,本技术生产工艺在小规模试验生产(1t-2t环氧丙烷用量),本工艺可促进环氧丙烷和二乙醇胺混合,减少混合时间,降低制冷负荷,同时减少了副反应,还提高产品纯度和产率,且四氯化碳与二乙醇胺的用量为(0.161-0.194):1。
73.实施例43一种二乙醇单异丙醇胺的生产工艺,基于实施例26的基础上,区别之处在于:s1中的混合物料中还加入了石墨粉末,石墨粉末的粒径为7
±
1μm,石墨粉末的加入量为3.14kg;s2所得的二乙醇单异丙醇胺粗品经过过滤后再进行s3步骤,过滤过程过滤去除粒径不小于1μm的固体物质。
74.实施例44一种二乙醇单异丙醇胺的生产工艺,基于实施例26的基础上,区别之处在于:s1中的混合物料中还加入了石墨粉末,石墨粉末的粒径为1~2μm,石墨粉末的加入量为3.14kg;s2所得的二乙醇单异丙醇胺粗品经过过滤后再进行s3步骤,过滤过程过滤去除粒径不小于1μm的固体物质。
75.实施例45一种二乙醇单异丙醇胺的生产工艺,基于实施例26的基础上,区别之处在于:s1中的混合物料中还加入了3.14kg石墨粉末,石墨粉末由粒径为1~2μm石墨粉末和粒径为7~8μm的石墨粉末按质量比1:1混合而成;s2所得的二乙醇单异丙醇胺粗品经过过滤后再进行s3步骤,过滤过程过滤去除粒径不小于1μm的固体物质;在进行后续的生产步骤。
76.实施例46一种二乙醇单异丙醇胺的生产工艺,基于实施例26的基础上,区别之处在于:石墨粉末用量为3.88kg。
77.实施例47一种二乙醇单异丙醇胺的生产工艺,基于实施例26的基础上,区别之处在于:石墨粉末用量为2.98kg。
78.对实施例43-47过程中,发现在s4步骤精分离二乙醇胺后,物料中出现少许固体絮状沉淀,这是实施例22-42未曾出现的,故对s4步骤精分离二乙醇胺后的物料过滤固体物质,过滤去除固体絮状沉淀后方才是产品。
79.对实施例43-47所得中间物料和产品进行检测,检测结果如下表13所示。表13.实施例43~47反应物料、二乙醇单异丙醇胺检测结果表 反应物料混合情况相对平均偏差产品纯度wt%产品收率wt%实施例430.012998.7194.84
实施例440.020199.2194.35实施例450.014699.1494.69实施例460.013399.1394.65实施例470.015199.1294.61
80.本技术中在大量级生产规模时,在混合物料中混入石墨粉末,是为了增效二乙醇胺和环氧丙烷混合——石墨粉末在混合过程中在液体中上下游走,撞击液相界面,增效液相混合,提高产品收率。
81.石墨粉末的加入对产品的纯度还起到了进一步的促进作用。
82.在实施例43-47中过滤出的沉淀物经过成分检测发现,其为残留的石墨粉末(粒径小于1μm)和高沸点的副反应产物,包括环氧丙烷的自聚物。
83.本技术发明人认为在精分离时,二乙醇胺不断被分离,高沸点的环氧丙烷聚合物杂质被富集,小于1μm粒径的石墨粉末此时作为核剂,使高沸点的环氧丙烷聚合物杂质以石墨粉末为核聚集,从液相中脱离,并在后续的过滤中去除。由此,在石墨粉末作用下,结合在精分离和后续的固体物过滤,对产品中沸点高于二乙醇胺的环氧丙烷聚合物杂质进行了去除,提高产品纯度。
84.对此本技术发明人研发过程中还有其他方案:对比例17一种二乙醇单异丙醇胺的生产工艺,基于实施例26的基础上,区别之处在于:s1中的混合物料中还加入了二氧化硅粉末,二氧化硅粉末的粒径为1~2μm,石墨粉末的加入量为3.143kg;s2所得的二乙醇单异丙醇胺粗品经过过滤后再进行s3步骤,过滤过程过滤去除粒径不小于1μm的固体物质。
85.对比例18一种二乙醇单异丙醇胺的生产工艺,基于实施例26的基础上,区别之处在于:s1中的混合物料中还加入了二氧化硅粉末,二氧化硅粉末的粒径为7~8μm,石墨粉末的加入量为3.143kg;s2所得的二乙醇单异丙醇胺粗品经过过滤后再进行s3步骤,过滤过程过滤去除粒径不小于1μm的固体物质。
86.对对比例17-18所得中间物料和产品进行检测,检测结果如下表14所示。表14.对比例17~18反应物料、二乙醇单异丙醇胺检测结果表
87.由上可知,使用二氧化硅粉末对于反应物料混合的效果更好,但对产品纯度和产品收率而言其反而降低了,发明人研究后分析——是由于二氧化硅的表面对副反应活化催化导致的。
88.故而石墨粉末是大规模生产下进一步提高混合情况的添加物较优品。
89.为进一步研究石墨粉末的作用,本技术发明人还进行了如下方案:对实施例45中s4步骤精分离二乙醇胺后物料过滤得到的固体物质内石墨含量进
行检测,检测结果石墨含量为0.0121kg。
90.对比例19一种二乙醇单异丙醇胺的生产工艺,基于实施例26的基础上,区别之处在于:s4:初分离物料内加入0.0121kg、粒径为0.2μm石墨粉末,混合均匀后加入另一蒸馏釜中利用精馏塔分离装置分离,精馏塔规格:内管h=420cm、内径φ=50cm、填料为θ环、填料高度为260cm,塔顶真空度为0.09mpa,塔釜温度为156
±
3℃,塔顶温度65~68℃,回流比为2:1,分离二乙醇胺后,过滤塔釜物料得到产品二乙醇单异丙醇胺。
91.对对比例19的产品纯度进行检测,检测结果为97.31wt%。
92.对比例20一种二乙醇单异丙醇胺的生产工艺,基于实施例26的基础上,区别之处在于:s4:初分离物料内加入0.0121kg、粒径为0.05μm石墨粉末,混合均匀后加入另一蒸馏釜中利用精馏塔分离装置分离,精馏塔规格:内管h=420cm、内径φ=50cm、填料为θ环、填料高度为260cm,塔顶真空度为0.09mpa,塔釜温度为156
±
3℃,塔顶温度65~68℃,回流比为2:1,分离二乙醇胺后,过滤塔釜物料得到产品二乙醇单异丙醇胺。
93.对对比例20的产品纯度进行检测,检测结果为97.23wt%。
94.对比实施例43-45、对比例19-20,对比例19-20的纯度并未达到明显的提升。本技术实施例的方案内初步分离物料中的石墨粉末来源与此前反应过程中石墨粉末破碎的碎屑,碎屑破碎过程中产生了新的表面,该表面直接于反应物料接触,在反应过程中发生了一定的改性,故而才能起到团聚副反应产物,将其转化为沉淀,能够被过滤。
95.以上均为本技术的较佳实施例,并非依此限制本技术的保护范围,故:凡依本技术的结构、形状、原理所做的等效变化,均应涵盖于本技术的保护范围之内。