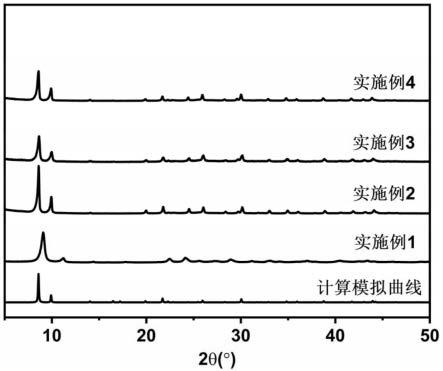
1.本发明属于碳捕获技术领域,具体涉及一种多孔配位聚合物及其绿色制备方法和应用。
背景技术:2.随着生产力和社会经济的不断发展,尤其是工业革命后,人类社会对化石能源(煤、石油、天然气)和生物质能源的消费快速增长,造成二氧化碳(co2)的排放量显著上升,远远超出了自然界的固碳能力,导致大气中co2的浓度持续上升,从而引起了一系列全球气候环境问题;而这些气候环境问题已经严重威胁到人类社会的可持续发展,积极应对气候变化已成为全球普遍共识和大势所趋。
3.为应对气候变化,世界几大主要经济体均已明确扩大可再生和低碳能源的供应、最大化利用能源、碳捕集利用和封存等科技手段已成为解决碳减排问题的关键和共识。
4.目前,二氧化碳捕获技术主要包括化学吸收法、膜分离法和吸附分离法等,其中吸附分离法是基于固体吸附剂对不同气体的吸附能力不同而达到吸附分离气体的目的,是一种非常高效的技术手段。吸附分离法是所利用的吸附分离材料主要包括碳材料、分子筛及多孔有机材料(如多孔配位聚合物),其中多孔配位聚合物是由有机配体与金属离子/团簇通过配位键相连自组装形成的一类多孔晶体材料,其不仅具有较大的比表面积和孔隙率,而且可以在较大范围内对结构与孔道性质进行调控,以实现对客体分子的精确捕获,使得其成为了气体吸附领域的理想材料之一。
5.但是目前用于co2吸附及分离的多孔配位聚合物大多存在合成成本极高、合成条件苛刻且无法实现大批量制备、合成过程中用到的有机溶剂为非绿色溶剂、易污染环境等制约因素。
技术实现要素:6.本发明的发明目的是提供一种多孔配位聚合物及其绿色制备方法和应用,该多孔配位聚合物可实现对二氧化碳的高效吸附,且制备成本低,制备条件温和,绿色无污染,生产周期短,产率高,可实现大批量制备。
7.为实现上述发明目的,本发明的技术方案为:
8.一种多孔配位聚合物,由有机配体和锆盐进行配位后制得,所述的有机配体为结构式如式(ⅰ)、式(ⅱ)和式(ⅲ)所示有机羧酸中的至少一种,
[0009][0010]
其中,r1、r2、r3、r4、r5、r6、r7、r8和r9同时或不同时地为氢、氨基、羟基、巯基、c
1-c4烷基、c
1-c3酰基或卤素。
[0011]
本发明选用的有机配体均为商业化且低成本的有机羧酸配体,极大地降低了合成成本;而且上述有机羧酸配体可溶于水,因此反应过程中无需使用到有机溶剂。
[0012]
采用上述有机羧酸配体制得的多孔配位聚合物中富含很强的锆-氧配位键,因此具有超高的化学/热力学稳定性;而且呈现出具有丰富一维孔道的三维框架结构,孔径分布均匀,具有较高的比表面积和特殊的孔道环境,因此,多种气体表现出优异的吸附选择性;尤其对二氧化碳的吸附能力和吸附选择性更强,在25℃、100kpa下,该多孔配位聚合物对二氧化碳的吸附能力可达52.1cm3/g,吸附选择性大于500,在碳捕获领域具有重要的应用价值。
[0013]
作为优选,在上述的多孔配位聚合物中,所述的有机配体为丁二酸、天门冬二酸、2-甲基琥珀酸、n-乙酰-dl-天冬氨酸、n-甲基天冬氨酸、谷氨酸、戊二酸、2-甲基戊二酸、己二酸、3-甲基己二酸或3-氨基己二酸中的至少一种。
[0014]
作为优选,在上述的多孔配位聚合物中,所述的锆盐为氯化锆、硫酸锆、硝酸锆和氯氧化锆中的至少一种;更优选为氯化锆、硫酸锆和硝酸锆中的至少一种。
[0015]
作为优选,在上述的多孔配位聚合物中,所述的锆盐与所述的有机配体的摩尔比为1:1~1:20;更优选为1:1~1:10。
[0016]
本发明还提供了上述的多孔配位聚合物的绿色制备方法,该绿色制备方法依次包括以下步骤:
[0017]
(1)将有机配体分散到溶剂中,获得悬浮液;(2)按预设的摩尔比,将锆盐加入到所述的悬浮液中,获得混合液;
[0018]
(3)经加热回流反应获得沉淀物,将该沉淀物洗涤、干燥后,获得所述的多孔配位聚合物。
[0019]
本发明选择的有机羧酸配体使得多孔配位聚合物的制备方法无需在高温高压条件下进行,只需在常压下进行加热回流反应即可,反应条件更加温和,对设备要求低,步骤简单,易于工业化放大生产。
[0020]
本发明的制备方法生产周期短,产率高(可达86%);且已实现百克级放大合成,可进一步放大至百公斤甚至吨级合成,实现大批量制备。
[0021]
在上述的多孔配位聚合物的绿色制备方法中,步骤(1)中,所述的有机配体与溶剂
的摩尔比为1:1~1:50。
[0022]
可以采用超声或搅拌等手段将有机配体均匀地分散到溶剂中,超声或搅拌处理的时间为1~60min,优选1~10min;而后再将锆盐加入到悬浮液中,避免锆盐因过早地与有机配体在不适宜的条件(如温度不足)下反应而使产物结晶性差、无法形成框架结构。
[0023]
作为进一步优选,步骤(1)中,所述的有机配体与溶剂的摩尔比为 1:5~1:20。
[0024]
在上述的多孔配位聚合物的绿色制备方法中,步骤(1)中,所述的溶剂为水、乙醇、丙酮和n,n-二甲基甲酰胺中的至少一种;作为进一步优选,所述的溶剂为水。与其他溶剂相比,水更加环保、绿色无污染。
[0025]
在上述的多孔配位聚合物的绿色制备方法中,步骤(2)中,在加热回流反应前向混合液中再次加入溶剂,溶剂与有机配体的摩尔比为 1:1~100:1。
[0026]
再次加入溶剂的目的,一方面是为了将粘附在反应器(如烧瓶)内壁上的锆盐尽可能多地冲洗至混合液中,一方面是为了混合液中的有机配体和锆盐保持在适宜的浓度下。
[0027]
作为进一步优选,步骤(2)中,在加热回流反应前向混合液中再次加入溶剂,溶剂与有机配体的摩尔比为1:1~20:1。
[0028]
在上述的多孔配位聚合物的绿色制备方法中,步骤(3)中,所述的加热回流反应在50~150℃下进行,反应时间为1~10小时;进一步优选为在 70-120℃在反应1~3h。
[0029]
在上述的多孔配位聚合物的绿色制备方法中,步骤(3)中,将沉淀物在50~100℃下干燥处理10-50h;优选为在60~80℃下干燥处理20~30h。
[0030]
本发明还提供了上述的多孔配位聚合物在气体吸附分离或气体储存中的应用,其中,所述的气体吸附分离是采用多孔配位聚合物对乙烯和乙烷混合气、乙炔和丙炔混合气、丙烯和丙烷混合气或二氧化碳和氮气混合气进行分离;进行吸附分离时,优选在0-50℃、混合气总压为10kpa至1000 kpa的条件下进行。
[0031]
所述的气体储存是将多孔配位聚合物用于储存甲烷、氢气或二氧化碳中的至少一种。
[0032]
与现有技术相比,本发明的有益效果体现在:
[0033]
(1)本发明选用的有机配体均为商业化且低成本的有机羧酸配体,极大地降低了合成成本;而且上述有机羧酸配体可溶于水,因此反应过程中无需使用到有机溶剂,更加绿色环保。
[0034]
(2)本发明的多孔配位聚合物中富含很强的锆-氧配位键,因此具有超高的化学/热力学稳定性;而且呈现出具有丰富一维孔道的三维框架结构,孔径分布均匀,具有较高的比表面积和特殊的孔道环境,因此,多种气体表现出优异的吸附选择性;尤其对二氧化碳的吸附能力和吸附选择性更强,在25℃、100kpa下,该多孔配位聚合物对二氧化碳的吸附能力可达52.1cm3/g,吸附选择性大于500,在碳捕获领域具有重要的应用价值。
[0035]
(3)本发明选择的有机羧酸配体使得多孔配位聚合物的制备方法无需在高温高压条件下进行,只需在常压下进行加热回流反应即可,反应条件更加温和,对设备要求低,步骤简单,易于工业化放大生产。
[0036]
(4)本发明的制备方法生产周期短,产率高(可达86%);且已实现百克级放大合成,可进一步放大至百公斤甚至吨级合成,实现大批量制备。
附图说明
[0037]
图1为本发明实施例1至实施例4的多孔配位聚合物的粉末x射线衍射图;
[0038]
其中,2θ(
°
)表示衍射角(度),下同;
[0039]
图2为本发明实施例1至实施例4的多孔配位聚合物的红外光谱图;
[0040]
其中,wavenumber(cm-1
)表示波长(cm-1
),transmittance(%)表示透射比(百分比);下同;
[0041]
图3为本发明实施例1的多孔配位聚合物的扫描电镜图;
[0042]
图4为本发明实施例2的多孔配位聚合物的扫描电镜图;
[0043]
图5为本发明实施例3的多孔配位聚合物的扫描电镜图;
[0044]
图6为本发明实施例4的多孔配位聚合物的扫描电镜图;
[0045]
图7为本发明实施例1的多孔配位聚合物在77k下的氮气吸脱附等温线;
[0046]
其中,p/p0表示相对压力,其中p为气体真实压力,p0表示气体在测量温度下的饱和蒸汽压,quantity adsorbed(cm3/g stp)表示吸附量(cm3/g stp),s
bet
表示通过bet方程计算得到的材料比表面积;下同;
[0047]
图8为本发明实施例2的多孔配位聚合物在77k下的氮气吸脱附等温线;
[0048]
图9为本发明实施例3的多孔配位聚合物在77k下的氮气吸脱附等温线;
[0049]
图10为本发明实施例4的多孔配位聚合物在77k下的氮气吸脱附等温线;
[0050]
图11为本发明实施例1的多孔配位聚合物在25℃下对二氧化碳和氮气的吸附等温线;
[0051]
其中,pressure(kpa)表示压力(千帕);下同;
[0052]
图12为本发明实施例2的多孔配位聚合物在25℃下对二氧化碳和氮气的吸附等温线;
[0053]
图13为本发明实施例3的多孔配位聚合物在25℃下对二氧化碳和氮气的吸附等温线;
[0054]
图14为本发明实施例4的多孔配位聚合物在25℃下对二氧化碳和氮气的吸附等温线;
[0055]
图15为本发明实施例1的多孔配位聚合物在氮气氛围下的热重图;
[0056]
其中,temperature(℃)表示温度(℃),weight(%)表示重量(百分比),下同;
[0057]
图16为本发明实施例2的多孔配位聚合物在氮气氛围下的热重图;
[0058]
图17为本发明实施例3的多孔配位聚合物在氮气氛围下的热重图;
[0059]
图18为本发明实施例4的多孔配位聚合物在氮气氛围下的热重图。
具体实施方式
[0060]
下面结合附图和具体实施方式对本发明的技术方案做进一步详细说明。
[0061]
实施例1
[0062]
本实施例一种多孔配位聚合物,其制备方法依次包括以下步骤:
[0063]
(1)将有机配体分散到溶剂中,获得悬浮液;
[0064]
具体地,将丁二酸(2.48g)加入到圆底烧瓶中,并加入5ml去离子水,超声1min,使丁二酸充分分散在水中,获得悬浮液;
[0065]
(2)按预设的摩尔比,将锆盐加入到悬浮液中,获得混合液;
[0066]
具体地,将氯化锆(2.33g)分批加入到溶液中,搅拌均匀,并再次加入5ml去离子水,获得混合液;
[0067]
(3)经加热回流反应获得沉淀物,将该沉淀物洗涤、干燥后,获得本实施例的多孔配位聚合物;
[0068]
具体地,将圆底烧瓶在120℃下加热回流1h,反应结束后冷却至室温,离心取沉淀物,去离子水洗涤后,置于60℃下干燥30h,即得到本实施例的多孔配位聚合物。
[0069]
实施例2
[0070]
本实施例一种多孔配位聚合物,其制备方法依次包括以下步骤:
[0071]
(1)将有机配体分散到溶剂中,获得悬浮液;
[0072]
具体地,将2-甲基琥珀酸(2.78g)加入到圆底烧瓶中,并加入5ml 去离子水,超声1min,使丁二酸充分分散在水中,获得悬浮液;
[0073]
(2)按预设的摩尔比,将锆盐加入到悬浮液中,获得混合液;
[0074]
具体地,将氯化锆(2.33g)分批加入到溶液中,搅拌均匀,并再次加入5ml去离子水,获得混合液;
[0075]
(3)经加热回流反应获得沉淀物,将该沉淀物洗涤、干燥后,获得本实施例的多孔配位聚合物;
[0076]
具体地,将圆底烧瓶在120℃下加热回流1h,反应结束后冷却至室温,离心取沉淀物,去离子水洗涤后,置于80℃下干燥20h,即得到本实施例的多孔配位聚合物。
[0077]
实施例3
[0078]
本实施例一种多孔配位聚合物,其制备方法依次包括以下步骤:
[0079]
(1)将有机配体分散到溶剂中,获得悬浮液;
[0080]
具体地,将l-天冬氨酸(2.81g)加入到圆底烧瓶中,并加入5ml去离子水,超声1min,使丁二酸充分分散在水中,获得悬浮液;
[0081]
(2)按预设的摩尔比,将锆盐加入到悬浮液中,获得混合液;
[0082]
具体地,将氯化锆(2.33g)分批加入到溶液中,搅拌均匀,并再次加入5ml去离子水,获得混合液;
[0083]
(3)经加热回流反应获得沉淀物,将该沉淀物洗涤、干燥后,获得本实施例的多孔配位聚合物;
[0084]
具体地,将圆底烧瓶在120℃下加热回流1h,反应结束后冷却至室温,离心取沉淀物,去离子水洗涤后,置于50℃下干燥50h,即得到本实施例的多孔配位聚合物。
[0085]
实施例4
[0086]
本实施例一种多孔配位聚合物,其制备方法依次包括以下步骤:
[0087]
(1)将有机配体分散到溶剂中,获得悬浮液;
[0088]
具体地,将n-乙酰-dl-天冬氨酸(3.68g)加入到圆底烧瓶中,并加入5ml去离子水,超声1min,使丁二酸充分分散在水中,获得悬浮液;
[0089]
(2)按预设的摩尔比,将锆盐加入到悬浮液中,获得混合液;
[0090]
具体地,将氯化锆(2.33g)分批加入到溶液中,搅拌均匀,并再次加入5ml去离子水,获得混合液;
[0091]
(3)经加热回流反应获得沉淀物,将该沉淀物洗涤、干燥后,获得本实施例的多孔配位聚合物;
[0092]
具体地,将圆底烧瓶在120℃下加热回流1h,反应结束后冷却至室温,离心取沉淀物,去离子水洗涤后,置于100℃下干燥10h,即得到本实施例的多孔配位聚合物。
[0093]
实施例5
[0094]
本实施例一种多孔配位聚合物,其制备方法依次包括以下步骤:
[0095]
(1)将有机配体分散到溶剂中,获得悬浮液;
[0096]
具体地,将n-甲基天冬氨酸(3.09g)加入到圆底烧瓶中,并加入5ml 去离子水,超声1min,使丁二酸充分分散在水中,获得悬浮液;
[0097]
(2)按预设的摩尔比,将锆盐加入到悬浮液中,获得混合液;
[0098]
具体地,将氯化锆(2.33g)分批加入到溶液中,搅拌均匀,并再次加入5ml去离子水,获得混合液;
[0099]
(3)经加热回流反应获得沉淀物,将该沉淀物洗涤、干燥后,获得本实施例的多孔配位聚合物;
[0100]
具体地,将圆底烧瓶在120℃下加热回流1h,反应结束后冷却至室温,离心取沉淀物,去离子水洗涤后,置于100℃下干燥10h,即得到本实施例的多孔配位聚合物。
[0101]
实施例6
[0102]
本实施例一种多孔配位聚合物,其制备方法依次包括以下步骤:
[0103]
(1)将有机配体分散到溶剂中,获得悬浮液;
[0104]
具体地,将戊二酸(2.77g)加入到圆底烧瓶中,并加入5ml去离子水,超声1min,使丁二酸充分分散在水中,获得悬浮液;
[0105]
(2)按预设的摩尔比,将锆盐加入到悬浮液中,获得混合液;
[0106]
具体地,将氯化锆(2.33g)分批加入到溶液中,搅拌均匀,并再次加入5ml去离子水,获得混合液;
[0107]
(3)经加热回流反应获得沉淀物,将该沉淀物洗涤、干燥后,获得本实施例的多孔配位聚合物;
[0108]
具体地,将圆底烧瓶在120℃下加热回流1h,反应结束后冷却至室温,离心取沉淀物,去离子水洗涤后,置于100℃下干燥10h,即得到本实施例的多孔配位聚合物。
[0109]
实施例7
[0110]
本实施例一种多孔配位聚合物,其制备方法依次包括以下步骤:
[0111]
(1)将有机配体分散到溶剂中,获得悬浮液;
[0112]
具体地,将谷氨酸(3.09g)加入到圆底烧瓶中,并加入5ml去离子水,超声1min,使丁二酸充分分散在水中,获得悬浮液;
[0113]
(2)按预设的摩尔比,将锆盐加入到悬浮液中,获得混合液;
[0114]
具体地,将氯化锆(2.33g)分批加入到溶液中,搅拌均匀,并再次加入5ml去离子水,获得混合液;
[0115]
(3)经加热回流反应获得沉淀物,将该沉淀物洗涤、干燥后,获得本实施例的多孔配位聚合物;
[0116]
具体地,将圆底烧瓶在120℃下加热回流1h,反应结束后冷却至室温,离心取沉淀
物,去离子水洗涤后,置于100℃下干燥10h,即得到本实施例的多孔配位聚合物。
[0117]
实施例8
[0118]
本实施例一种多孔配位聚合物,其制备方法依次包括以下步骤:
[0119]
(1)将有机配体分散到溶剂中,获得悬浮液;
[0120]
具体地,将2-甲基戊二酸(3.07g)加入到圆底烧瓶中,并加入5ml 去离子水,超声1min,使丁二酸充分分散在水中,获得悬浮液;
[0121]
(2)按预设的摩尔比,将锆盐加入到悬浮液中,获得混合液;
[0122]
具体地,将氯化锆(2.33g)分批加入到溶液中,搅拌均匀,并再次加入5ml去离子水,获得混合液;
[0123]
(3)经加热回流反应获得沉淀物,将该沉淀物洗涤、干燥后,获得本实施例的多孔配位聚合物;
[0124]
具体地,将圆底烧瓶在120℃下加热回流1h,反应结束后冷却至室温,离心取沉淀物,去离子水洗涤后,置于100℃下干燥10h,即得到本实施例的多孔配位聚合物。
[0125]
实施例9
[0126]
本实施例一种多孔配位聚合物,其制备方法依次包括以下步骤:
[0127]
(1)将有机配体分散到溶剂中,获得悬浮液;
[0128]
具体地,将己二酸(3.07g)加入到圆底烧瓶中,并加入5ml去离子水,超声1min,使丁二酸充分分散在水中,获得悬浮液;
[0129]
(2)按预设的摩尔比,将锆盐加入到悬浮液中,获得混合液;
[0130]
具体地,将氯化锆(2.33g)分批加入到溶液中,搅拌均匀,并再次加入5ml去离子水,获得混合液;
[0131]
(3)经加热回流反应获得沉淀物,将该沉淀物洗涤、干燥后,获得本实施例的多孔配位聚合物;
[0132]
具体地,将圆底烧瓶在120℃下加热回流1h,反应结束后冷却至室温,离心取沉淀物,去离子水洗涤后,置于100℃下干燥10h,即得到本实施例的多孔配位聚合物。
[0133]
实施例10
[0134]
本实施例一种多孔配位聚合物,其制备方法依次包括以下步骤:
[0135]
(1)将有机配体分散到溶剂中,获得悬浮液;
[0136]
具体地,将3-氨基己二酸(3.38g)加入到圆底烧瓶中,并加入5ml 去离子水,超声1min,使丁二酸充分分散在水中,获得悬浮液;
[0137]
(2)按预设的摩尔比,将锆盐加入到悬浮液中,获得混合液;
[0138]
具体地,将氯化锆(2.33g)分批加入到溶液中,搅拌均匀,并再次加入5ml去离子水,获得混合液;
[0139]
(3)经加热回流反应获得沉淀物,将该沉淀物洗涤、干燥后,获得本实施例的多孔配位聚合物;
[0140]
具体地,将圆底烧瓶在120℃下加热回流1h,反应结束后冷却至室温,离心取沉淀物,去离子水洗涤后,置于100℃下干燥10h,即得到本实施例的多孔配位聚合物。
[0141]
实施例11
[0142]
本实施例一种多孔配位聚合物,其制备方法依次包括以下步骤:
[0143]
(1)将有机配体分散到溶剂中,获得悬浮液;
[0144]
具体地,将3-甲基己二酸(3.36g)加入到圆底烧瓶中,并加入5ml 去离子水,超声1min,使丁二酸充分分散在水中,获得悬浮液;
[0145]
(2)按预设的摩尔比,将锆盐加入到悬浮液中,获得混合液;
[0146]
具体地,将氯化锆(2.33g)分批加入到溶液中,搅拌均匀,并再次加入5ml去离子水,获得混合液;
[0147]
(3)经加热回流反应获得沉淀物,将该沉淀物洗涤、干燥后,获得本实施例的多孔配位聚合物;
[0148]
具体地,将圆底烧瓶在120℃下加热回流1h,反应结束后冷却至室温,离心取沉淀物,去离子水洗涤后,置于100℃下干燥10h,即得到本实施例的多孔配位聚合物。
[0149]
分别取实施例1-4制备的多孔配位聚合物,作x射线衍射分析,分析结果见图1;作红外光谱分析,分析结果见图2;作扫描电镜分析,分析结果见图3至图6。
[0150]
由图1可见,各多孔配位聚合物的所有衍射峰的位置都与理论计算模拟的衍射峰的位置一一对应,说明本发明制备的多孔配位聚合物与理论计算模拟的结构相同。
[0151]
由图3至图6可见,各多孔配位聚合物形貌均一,说明其具有良好的结晶性。
[0152]
分别取实施例1-4制备的多孔配位聚合物,对各多孔配位聚合物在77 k下的氮气吸脱附等温线进行测试,测试结果见图7至图10。
[0153]
由图7至图10可见,经bet方程计算,各多孔配位聚合物均具有较大的比表面积。
[0154]
为了评价上述多孔配位聚合物的气体吸附分离性能,先取100mg上述多孔配位聚合物,在120℃下真空脱气12h,得到活化后的吸附剂;而后在 25℃下,对活化后的吸附剂进行二氧化碳和氮气的单组分吸附等温线测试,测试结果见图11至图14。
[0155]
由图11可见,在25℃、100kpa下,实施例1的多孔配位聚合物对二氧化碳的吸附量达到27.6cm3/g,氮气的吸附量为2.1cm3/g;经亨利定律计算,该多孔配位聚合物对两种气体的吸附选择性达到32。
[0156]
由图12可见,在25℃、100kpa下,实施例2的多孔配位聚合物对二氧化碳的吸附量达到39.5cm3/g,氮气的吸附量为1.8cm3/g;经亨利定律计算,该多孔配位聚合物对两种气体的吸附选择性达到41。
[0157]
由图13可见,在25℃、100kpa下,实施例3的多孔配位聚合物对二氧化碳的吸附量达到51.5cm3/g,氮气的吸附量为0.9cm3/g;经亨利定律计算,该多孔配位聚合物对两种气体的吸附选择性大于500。
[0158]
由图14可见,在25℃、100kpa下,实施例4的多孔配位聚合物对二氧化碳的吸附量达到52.1cm3/g,氮气的吸附量为1.6cm3/g;经亨利定律计算,该多孔配位聚合物对两种气体的吸附选择性大于500。
[0159]
实施例5-10制备的多孔配位聚合物对二氧化碳和氮气的吸附选择性也均大于500。
[0160]
以上结果表明本发明的多孔配位聚合物对二氧化碳具有极高的吸附选择性。
[0161]
对各多孔配位聚合物在氮气氛围下的热重进行分析,分析结果见图15 至图18。
[0162]
如图15至图18可见,在180℃前的失重是由于吸附在孔道内的水分子的脱除,在大约180℃之后,各多孔材料的金属配位键发生断裂,骨架崩塌。
[0163]
实施例12
[0164]
本实施例一种多孔配位聚合物,其制备方法依次包括以下步骤:
[0165]
(1)将有机配体分散到溶剂中,获得悬浮液;
[0166]
具体地,将丁二酸(248g)加入到圆底烧瓶中,并加入500ml去离子水,超声5min,使丁二酸充分分散在水中,获得悬浮液;
[0167]
(2)按预设的摩尔比,将锆盐加入到悬浮液中,获得混合液;
[0168]
具体地,将氯化锆(233g)分批加入到溶液中,搅拌均匀,并再次加入500ml去离子水,获得混合液;
[0169]
(3)经加热回流反应获得沉淀物,将该沉淀物洗涤、干燥后,获得本实施例的多孔配位聚合物;
[0170]
具体地,将圆底烧瓶在120℃下加热回流1h,反应结束后冷却至室温,离心取沉淀物,去离子水洗涤后,置于60℃下干燥30h,即得到本实施例的多孔配位聚合物。
[0171]
经测试,本实施例的多孔配位聚合物的产率达到86%(以有机配体计)。
[0172]
以上各实施例仅用以说明本技术的技术方案,而非对其限制;尽管参照前述各实施例对本技术进行了详细的说明,本领域的普通技术人员应当理解:其依然可以对前述各实施例所记载的技术方案进行修改,或者对其中部分或者全部技术特征进行等同替换;而这些修改或者替换,并不使相应技术方案的本质脱离本技术技术方案的范围。