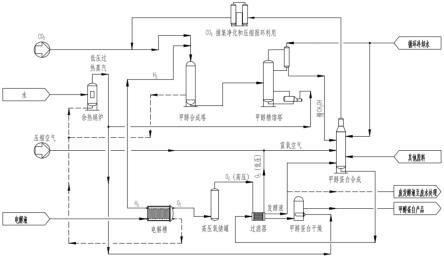
1.本发明涉及生物工程技术领域,特别涉及一种甲醇蛋白的工业化生产方法和系统。
背景技术:2.甲醇蛋白是以甲醇为碳源生产的单细胞蛋白。甲醇蛋白的主要成分为粗蛋白、脂肪、赖氨酸、蛋氨酸、胱氨酸、矿物质和维生素,其中粗蛋白质量分数平均在70%以上。甲醇蛋白被称为第二代单细胞蛋白,与天然植物蛋白相比,甲醇蛋白含有更丰富的氨基酸、矿物质和维生素,可以部分代替鱼粉、大豆、肉类及脱脂奶粉等喂养家禽。发展甲醇蛋白是解决我国养殖业及食品工业蛋白质短缺问题的重要途径之一,对解决我国的粮食安全问题具有重大意义。
3.甲醇蛋白生产不受气候条件影响、合成速度快、质量稳定,因此当前世界各国都十分重视开辟蛋白质资源和研究其应用技术,并已取得了很大进展,其中工业化最快的是单细胞蛋白生产,被认为是解决人类蛋白质资源匮乏最有效途径之一。以甲醇、氨、硫酸和磷酸等为原料作为培养基,通过微生物发酵在甲醇基体中生长,消耗甲醇,生长成许多单细胞菌体,成为菌体单细胞蛋白,简称scp。目前来看,甲醇蛋白生产仍存在以下问题:
4.(1)发酵生产过程中水、电、气消耗较大,不能实现高密度发酵,生产效率低,生产成本较高;
5.(2)原料甲醇消耗大量碳源,并排放大量co2,同时发酵生产过程也排放大量co2,构成严重的碳排放问题。
技术实现要素:6.针对上述情况,为克服现有技术缺陷,本发明之目的就是提供一种甲醇蛋白的工业化生产方法,即甲醇蛋白高效绿色的生产方法。本发明的另一目的是提供该方法所采用的生产系统。
7.本发明为实现上述目的所采取的技术方案为:甲醇蛋白高效低碳生产方法,其特征是,采用电解制氢副产氧气与空气复配得到氧气含量在30%~70%的富氧空气通入发酵罐,以提高菌种新陈代谢效率,相应地提高甲醇蛋白的生产效率;甲醇蛋白合成的副产co2经净化压缩回收后补充参与反应合成甲醇,实现零碳排放;水电解制氢、甲醇合成反应热经余热锅炉处理,产生低压过热蒸汽分别用于粗甲醇精馏、后续甲醇蛋白干燥,精甲醇用于甲醇蛋白合成,能量充分利用,更加节能环保,具体包括如下步骤:
8.s0、采用电解单元的电解制氢为原料,与co2反应合成甲醇,后续步骤甲醇蛋白合成的副产co2经捕集、净化压缩回收后补充参与反应合成甲醇,实现co2回收利用;电解制氢副产氧气与空气复配得到富氧含量在30%~70%的富氧空气用于后续步骤通入发酵罐;
9.s1、摇瓶种子培养
10.选取嗜甲醇菌接种到试管中,加入2%葡萄糖作为碳源、2%胰蛋白胨作为蛋白质、
增塑剂和水,摇床振荡培养,得到摇瓶种子;上述所有试剂和试管均需蒸汽消毒;
11.s2、一级种子培养
12.一级种子培养在50l的发酵罐中进行;首先按照步骤s1所述成分及配比,在发酵罐中配制30l菌株营养液,对此进行蒸汽灭菌;与此同时对空气过滤器和取样口进行灭菌;灭菌结束后,打开进气阀,向发酵罐中通入步骤s0制备的无菌富氧空气,富氧含量在30%~70%,使罐体内富氧空气压力一直要高于罐体外大气压,打开发酵罐夹套冷却水,降低罐内营养液温度至25-35℃时,开始接种;从发酵罐接种口倒入含嗜甲醇菌摇瓶种子1000ml,随后控制发酵温度在28~30℃,转速150rpm,溶氧40%~50%,培养20~24h后,得一级种子;
13.s3、二级种子培养
14.二级种子培养在5m3发酵罐中进行;在发酵罐内配制3m3营养液,二级种子营养液配制成分包括:85wt%磷酸45l,二水硫酸钙1.2kg,硫酸钾24kg,七水硫酸镁18kg,甘油108kg和微量元素溶液9l,其余为水;所述的微量元素溶液为:五水硫酸铜14g/l,碘化钾0.08g/l,一水硫酸锰4g/l,二水钼酸钠0.1g/l,硼酸0.1g/l,六水合氯化钴1g/l;
15.按照步骤s2灭菌方法对二级种子营养液进行蒸汽灭菌,灭菌完成后,用35wt%的氨水调营养液ph值至4.8~5.0,然后将培养好的一级种子30l接种到3m3的营养液中,接种量为1%;接种前应检查一级种子质量,镜检种子菌体整齐,健壮,无杂菌污染,接种时二级种子罐罐压在0.1~0.3barg,一级种子罐罐压在0.5~1.0barg,通过富氧空气压力将一级种子从一级种子罐压到二级种子罐中,接种完成后,保持二级种子罐温度30~32℃,通风比1:1~1.5vol,罐压0.5barg,ph5.0~5.5,培养24~30h,得二级种子;
16.s4、发酵罐甲醇蛋白生产
17.按照步骤s3的蒸汽灭菌方法、及所需成分和配比,制备含二级种子的营养液2罐共10m3,然后以3~4m3/h的进料速度,泵打含二级种子营养液至层流罐中,同时打开蒸汽阀门,将蒸汽与发酵营养液混合,使发酵培养基温度达到121~125℃,进入在层流罐中维持20min后,进入100m3发酵罐中,总进料量为发酵罐体积的10%,即10m3;接种完毕后,关闭进料阀,并将100m3发酵罐温度维持在121℃30min,此时,用蒸汽对与100m3发酵罐相连的富氧空气过滤器、发酵罐取样口、出料口、排气口管道进行灭菌,保证100m3发酵罐及与之相连管道呈无菌状态,灭菌结束后,对100m3发酵罐内的发酵营养液降温到30℃~35℃;用40wt%的氨水调发酵营养液至ph5.0后开始发酵,发酵温度30~32℃,通风比1:1.5~2vol,罐压0.4barg,ph5.0~5.5,培养16~20h;在此过程中蒸汽灭菌后富氧空气不断通入发酵罐底部,并通过搅拌促进氧气溶解;待罐内料液中的甘油消耗完,溶氧开始持续上升,罐内菌体od600达到36~40,发酵液密度达到100~120g/l,向100m3发酵罐内流加甲醇,甲醇流加量为5~6克/升.小时,当溶氧高于60%以上时,加大甲醇流加量,最大流加量达到10~15克/升.小时,发酵过程中,每8小时补加一次微量元素溶液,每次流加15升,直至发酵结束,发酵72~84小时后,取样测定菌体湿重达550~600g/l,发酵结束,得发酵液;甲醇蛋白合成的副产co2与电解单元的电解制氢,反应合成粗甲醇,反应热用于下游粗甲醇精馏辅热,甲醇精馏塔中通入甲醇合成塔中反应合成的粗甲醇,精甲醇用于上述甲醇蛋白合成过程;
18.s5、发酵液出料及细菌处理
19.发酵结束后,调整含粗产品发酵液的ph值使细菌凝聚,再利用罐压将发酵液导入到发酵液储罐中,静置沉降4~8小时,沉降液经卧螺离心机离心分离得菌泥,滤液灭菌后返
回发酵罐使用,菌泥经闪蒸脱水、干燥得到甲醇蛋白产品,蛋白含量达到75wt%以上。
20.所述嗜甲醇菌为巴斯德毕赤酵母hgd-01菌株。
21.所述步骤s2中对菌株营养液进行蒸汽灭菌条件为:灭菌温度121℃,灭菌时间30min;对空气过滤器和取样口进行灭菌10min即可。
22.所述的甲醇蛋白高效低碳生产方法采用的系统,其特征是,包括电解单元、富氧空气制备单元、精甲醇制备单元、甲醇蛋白合成单元、甲醇蛋白干燥单元、余热处理单元,所述电解单元下游分别连接富氧空气制备单元、精甲醇制备单元,所述富氧空气制备单元下游依次连接甲醇蛋白合成单元、甲醇蛋白干燥单元,所述精甲醇制备单元下游连接甲醇蛋白合成单元,所述余热处理单元回收电解单元、精甲醇制备单元的反应热,并将处理得到的低压过热蒸汽分别输入精甲醇制备单元、甲醇蛋白干燥单元。
23.所述电解单元采用承压壳式电解槽。
24.所述富氧空气制备单元包括压缩空气、高压氧储罐,所述高压氧储罐中通入电解单元副产氧气,所述压缩空气与增压后的氧气复配得到富氧空气,氧气含量在30%~70%。
25.所述精甲醇制备单元包括甲醇合成塔、甲醇精馏塔,所述甲醇合成塔中分别通入甲醇蛋白合成的副产co2及电解单元的电解制氢,反应合成粗甲醇,反应热用于下游粗甲醇精馏辅热,所述甲醇精馏塔中通入甲醇合成塔中反应合成的粗甲醇,精甲醇用于甲醇蛋白合成。
26.所述甲醇蛋白合成的副产co2通入甲醇合成塔前经脱碳捕集、净化压缩后回收利用。
27.所述甲醇蛋白合成单元包括一级种子发酵罐、二级种子发酵罐、过滤器,所述一级种子发酵罐为50l发酵罐,所述二级种子发酵罐为5m3发酵罐,发酵液经过滤器过滤使湿甲醇蛋白与发酵液分离,发酵液循环使用5批,再全部更换,废发酵液至废水处理单元处理。
28.所述余热处理单元采用余热锅炉回收水电解制氢、甲醇合成反应热,产出的低压过热蒸汽分别用于粗甲醇精馏、甲醇蛋白的干燥。
29.本发明具备以下有益效果:
30.1、如附图1,本发明采用电解制氢副产氧气与空气复配得到富氧空气,富氧含量在30%~70%之间,这相应增加了发酵营养液中的氧气溶解度,促进嗜甲醇菌新陈代谢效率提高1~3倍,相应提高了发酵产品细菌密度,使甲醇蛋白的生产效率提高1~3倍。同时本发明将电解制氢的副产氧气用于甲醇蛋白生产,提高了电解制氢装置的经济效益。作为对比,目前甲醇蛋白普遍采用压缩空气发酵生产,发酵营养液中溶氧难度低,嗜甲醇菌新陈代谢效率低,导致单罐生产效率较低。
31.2、如附图1,本发明公开了一种甲醇蛋白高效低碳生产的系统和方法,即甲醇蛋白生产的副产co2通过脱碳捕集、净化压缩,与电解制氢反应合成甲醇,实现了零碳排放。
32.3、如附图1,碱液循环水电解制氢的工作压力为2.5mpag,可通过膨胀驱动菌泥压滤脱水。
33.4、水电解制氢、甲醇合成反应热经余热锅炉处理,产生低压过热蒸汽分别用于粗甲醇精馏、后续甲醇蛋白干燥,精甲醇用于甲醇蛋白合成,能量充分利用,更加节能环保。
附图说明
34.图1为甲醇蛋白高效低碳生产方法工艺流程图。
具体实施方式
35.以下参照附图与具体实施例对发明的进一步详细说明。
36.实施例1
37.如图1所示,甲醇蛋白高效低碳生产系统,包括电解单元、富氧空气制备单元、精甲醇制备单元、甲醇蛋白合成单元、甲醇蛋白干燥单元、余热处理单元,所述电解单元下游分别连接富氧空气制备单元、精甲醇制备单元,所述富氧空气制备单元下游依次连接甲醇蛋白合成单元、甲醇蛋白干燥单元,所述精甲醇制备单元下游连接甲醇蛋白合成单元,所述余热处理单元回收电解单元、精甲醇制备单元的反应热,并将处理得到的低压过热蒸汽分别输入精甲醇制备单元、甲醇蛋白干燥单元。
38.所述电解单元采用承压壳式电解槽。
39.所述富氧空气制备单元包括压缩空气、高压氧储罐,所述高压氧储罐中通入电解单元副产氧气,所述压缩空气与增压后的氧气复配得到富氧空气,富氧含量在30%~70%。
40.所述精甲醇制备单元包括甲醇合成塔、甲醇精馏塔,所述甲醇合成塔中分别通入甲醇蛋白合成的副产co2及电解单元的电解制氢,反应合成粗甲醇,反应热用于下游粗甲醇精馏辅热,所述甲醇精馏塔中通入甲醇合成塔中反应合成的粗甲醇,精甲醇用于甲醇蛋白合成,所述co2通过脱碳捕集、净化压缩后回收利用。
41.所述甲醇蛋白合成单元包括一级种子发酵罐、二级种子发酵罐、过滤器,所述一级种子发酵罐为50l发酵罐,所述二级种子发酵罐为5m3发酵罐,发酵液经过滤器过滤使湿甲醇蛋白与发酵液分离,发酵液循环使用5批,再全部更换,废发酵液至废水处理单元处理。
42.所述余热处理单元采用余热锅炉回收水电解制氢、甲醇合成反应热,产出的低压过热蒸汽分别用于粗甲醇精馏、甲醇蛋白的干燥。
43.实施例2
44.采用实施例1所述系统的甲醇蛋白高效低碳生产方法,如图1所示,采用电解制氢为原料,副产氧气与空气复配得到富氧含量在30%~70%的富氧空气通入发酵罐,以提高菌种新陈代谢效率,相应地提高甲醇蛋白的生产效率;甲醇蛋白合成的副产co2经脱碳捕集、净化压缩回收后补充参与反应合成甲醇,实现零碳排放;水电解制氢、甲醇合成反应热经余热锅炉处理,产生低压过热蒸汽分别用于粗甲醇精馏、后续甲醇蛋白干燥,精甲醇用于甲醇蛋白合成,能量充分利用,更加节能环保,具体包括如下步骤:
45.s0、电解单元采用承压壳式电解槽,电解制氢为原料,与co2反应合成甲醇,后续步骤甲醇蛋白合成的副产co2经净化压缩回收后补充参与反应合成甲醇,实现co2回收利用;电解制氢副产氧气与空气复配得到富氧含量在30%~70%的富氧空气用于后续步骤通入发酵罐;
46.s1、摇瓶种子培养
47.选取巴斯德毕赤酵母hgd-01菌株接种到试管中,加入2%葡萄糖作为碳源、2%胰蛋白胨作为蛋白质、增塑剂和水,摇床振荡培养,得到摇瓶种子;上述所有试剂和试管均需蒸汽消毒;
48.s2、一级种子培养
49.一级种子培养在50l的发酵罐中进行;首先按照步骤s1所述成分及配比,在发酵罐中配制30l菌株营养液,对此进行蒸汽灭菌,灭菌条件为:灭菌温度121℃,灭菌时间30min;与此同时对空气过滤器和取样口进行灭菌,灭菌10min即可;灭菌结束后,打开进气阀,向发酵罐中通入步骤s0制备的无菌富氧空气,富氧含量在30%,使罐体内富氧空气压力一直要高于罐体外大气压,打开发酵罐夹套冷却水,降低罐内营养液温度至25℃时,开始接种;从发酵罐接种口倒入含嗜甲醇菌摇瓶种子1000ml,随后控制发酵温度在28℃,转速150rpm,溶氧40%,培养24h后,得一级种子;
50.s3、二级种子培养
51.二级种子培养在5m3发酵罐中进行;在发酵罐内配制3m3营养液,二级种子营养液配制成分包括:85wt%磷酸45l,二水硫酸钙1.2kg,硫酸钾24kg,七水硫酸镁18kg,甘油108kg和微量元素溶液9l,其余为水;所述的微量元素溶液为:五水硫酸铜14g/l,碘化钾0.08g/l,一水硫酸锰4g/l,二水钼酸钠0.1g/l,硼酸0.1g/l,六水合氯化钴1g/l;
52.按照步骤s2灭菌方法对二级种子营养液进行蒸汽灭菌,灭菌完成后,用35wt%的氨水调营养液ph值至4.8,然后将培养好的一级种子30l接种到3m3的营养液中,接种量为1%;接种前应检查一级种子质量,镜检种子菌体整齐,健壮,无杂菌污染,接种时二级种子罐罐压在0.1barg,一级种子罐罐压在0.5barg,通过富氧空气压力将一级种子从一级种子罐压到二级种子罐中,接种完成后,保持二级种子罐温度30℃,通风比1:1vol,罐压0.5barg,ph5.0,培养30h,得二级种子;
53.s4、发酵罐甲醇蛋白生产
54.按照步骤s3的蒸汽灭菌方法、及所需成分和配比,制备含二级种子的营养液2罐共10m3,然后以3m3/h的进料速度,泵打含二级种子营养液至层流罐中,同时打开蒸汽阀门,将蒸汽与发酵营养液混合,使发酵培养基温度达到121℃,进入在层流罐中维持20min后,进入100m3发酵罐中,总进料量为发酵罐体积的10%,即10m3;接种完毕后,关闭进料阀,并将100m3发酵罐温度维持在121℃30min,此时,用蒸汽对与100m3发酵罐相连的富氧空气过滤器、发酵罐取样口、出料口、排气口管道进行灭菌,保证100m3发酵罐及与之相连管道呈无菌状态,灭菌结束后,对100m3发酵罐内的发酵营养液降温到30℃;用40wt%的氨水调发酵营养液至ph5.0后开始发酵,发酵温度30℃,通风比1:1.5vol,罐压0.4barg,ph5.0,培养20h;在此过程中蒸汽灭菌后富氧空气不断通入发酵罐底部,并通过搅拌促进氧气溶解;待罐内料液中的甘油消耗完,溶氧开始持续上升,罐内菌体od600达到36,发酵液密度达到100g/l,向100m3发酵罐内流加甲醇,甲醇流加量为5克/升.小时,当溶氧高于60%以上时,加大甲醇流加量,最大流加量达到10克/升.小时,发酵过程中,每8小时补加一次微量元素溶液,每次流加15升,直至发酵结束,发酵84小时后,取样测定菌体湿重达550g/l,发酵结束,得发酵液;甲醇蛋白合成的副产co2与电解单元的电解制氢,反应合成粗甲醇,反应热用于下游粗甲醇精馏辅热,甲醇精馏塔中通入甲醇合成塔中反应合成的粗甲醇,精甲醇用于上述甲醇蛋白合成过程;
55.s5、发酵液出料及细菌处理
56.发酵结束后,调整含粗产品发酵液的ph值使细菌凝聚,再利用罐压将发酵液导入到发酵液储罐中,静置沉降4小时,沉降液经卧螺离心机离心分离得菌泥,滤液灭菌后返回
发酵罐使用,菌泥经闪蒸脱水、干燥得到甲醇蛋白产品,蛋白含量达到75wt%以上。
57.实施例3
58.本实施例中所述甲醇蛋白高效低碳生产方法具体包括如下步骤:
59.s0、电解单元采用承压壳式电解槽,电解制氢与后续步骤甲醇蛋白合成的副产co2反应合成甲醇,实现甲醇蛋白合成副产co2经净化压缩后的回收利用;电解制氢副产氧气与空气复配得到富氧含量在30%~70%的富氧空气用于后续步骤通入发酵罐;
60.s1、摇瓶种子培养
61.选取巴斯德毕赤酵母hgd-01菌株接种到试管中,加入2%葡萄糖作为碳源、2%胰蛋白胨作为蛋白质、增塑剂和水,摇床振荡培养,得到摇瓶种子;上述所有试剂和试管均需蒸汽消毒;
62.s2、一级种子培养
63.一级种子培养在50l的发酵罐中进行;首先按照步骤s1所述成分及配比,在发酵罐中配制30l菌株营养液,对此进行蒸汽灭菌,灭菌条件为:灭菌温度121℃,灭菌时间30min;与此同时对空气过滤器和取样口进行灭菌,灭菌10min即可;灭菌结束后,打开进气阀,向发酵罐中通入步骤s0制备的无菌富氧空气,富氧含量在50%,使罐体内富氧空气压力一直要高于罐体外大气压,打开发酵罐夹套冷却水,降低罐内营养液温度至30℃时,开始接种;从发酵罐接种口倒入含嗜甲醇菌摇瓶种子1000ml,随后控制发酵温度在29℃,转速150rpm,溶氧45%,培养22h后,得一级种子;
64.s3、二级种子培养
65.二级种子培养在5m3发酵罐中进行;在发酵罐内配制3m3营养液,二级种子营养液配制成分包括:85wt%磷酸45l,二水硫酸钙1.2kg,硫酸钾24kg,七水硫酸镁18kg,甘油108kg和微量元素溶液9l,其余为水;所述的微量元素溶液为:五水硫酸铜14g/l,碘化钾0.08g/l,一水硫酸锰4g/l,二水钼酸钠0.1g/l,硼酸0.1g/l,六水合氯化钴1g/l;
66.按照步骤s2灭菌方法对二级种子营养液进行蒸汽灭菌,灭菌完成后,用35wt%的氨水调营养液ph值至4.9,然后将培养好的一级种子30l接种到3m3的营养液中,接种量为1%;接种前应检查一级种子质量,镜检种子菌体整齐,健壮,无杂菌污染,接种时二级种子罐罐压在0.2barg,一级种子罐罐压在0.75barg,通过富氧空气压力将一级种子从一级种子罐压到二级种子罐中,接种完成后,保持二级种子罐温度31℃,通风比1:1.25vol,罐压0.5barg,ph5.2,培养27h,得二级种子;
67.s4、发酵罐甲醇蛋白生产
68.按照步骤s3的蒸汽灭菌方法、及所需成分和配比,制备含二级种子的营养液2罐共10m3,然后以3.5m3/h的进料速度,泵打含二级种子营养液至层流罐中,同时打开蒸汽阀门,将蒸汽与发酵营养液混合,使发酵培养基温度达到123℃,进入在层流罐中维持20min后,进入100m3发酵罐中,总进料量为发酵罐体积的10%,即10m3;接种完毕后,关闭进料阀,并将100m3发酵罐温度维持在121℃30min,此时,用蒸汽对与100m3发酵罐相连的富氧空气过滤器、发酵罐取样口、出料口、排气口管道进行灭菌,保证100m3发酵罐及与之相连管道呈无菌状态,灭菌结束后,对100m3发酵罐内的发酵营养液降温到32℃;用40wt%的氨水调发酵营养液至ph5.0后开始发酵,发酵温度31℃,通风比1:1.7vol,罐压0.4barg,ph5.2,培养18h;在此过程中蒸汽灭菌后富氧空气不断通入发酵罐底部,并通过搅拌促进氧气溶解;待罐内
料液中的甘油消耗完,溶氧开始持续上升,罐内菌体od600达到38,发酵液密度达到110g/l,向100m3发酵罐内流加甲醇,甲醇流加量为5.5克/升.小时,当溶氧高于60%以上时,加大甲醇流加量,最大流加量达到12.5克/升.小时,发酵过程中,每8小时补加一次微量元素溶液,每次流加15升,直至发酵结束,发酵78小时后,取样测定菌体湿重达570g/l,发酵结束,得发酵液;甲醇蛋白合成的副产co2与电解单元的电解制氢,反应合成粗甲醇,反应热用于下游粗甲醇精馏辅热,甲醇精馏塔中通入甲醇合成塔中反应合成的粗甲醇,精甲醇用于上述甲醇蛋白合成过程;
69.s5、发酵液出料及细菌处理
70.发酵结束后,调整含粗产品发酵液的ph值使细菌凝聚,再利用罐压将发酵液导入到发酵液储罐中,静置沉降6小时,沉降液经卧螺离心机离心分离得菌泥,滤液灭菌后返回发酵罐使用,菌泥经闪蒸脱水、干燥得到甲醇蛋白产品,蛋白含量达到75wt%以上。
71.实施例4
72.本实施例中所述甲醇蛋白高效低碳生产方法具体包括如下步骤:
73.s0、电解单元采用承压壳式电解槽,电解制氢与后续步骤甲醇蛋白合成的副产co2反应合成甲醇,实现甲醇蛋白合成副产co2经净化压缩后的回收利用;电解制氢副产氧气与空气复配得到富氧含量在30%~70%的富氧空气用于后续步骤通入发酵罐;
74.s1、摇瓶种子培养
75.选取巴斯德毕赤酵母hgd-01菌株接种到试管中,加入2%葡萄糖作为碳源、2%胰蛋白胨作为蛋白质、增塑剂和水,摇床振荡培养,得到摇瓶种子;上述所有试剂和试管均需蒸汽消毒;
76.s2、一级种子培养
77.一级种子培养在50l的发酵罐中进行;首先按照步骤s1所述成分及配比,在发酵罐中配制30l菌株营养液,对此进行蒸汽灭菌,灭菌条件为:灭菌温度121℃,灭菌时间30min;与此同时对空气过滤器和取样口进行灭菌,灭菌10min即可;灭菌结束后,打开进气阀,向发酵罐中通入步骤s0制备的无菌富氧空气,富氧含量在70%,使罐体内富氧空气压力一直要高于罐体外大气压,打开发酵罐夹套冷却水,降低罐内营养液温度至35℃时,开始接种;从发酵罐接种口倒入含嗜甲醇菌摇瓶种子1000ml,随后控制发酵温度在30℃,转速150rpm,溶氧50%,培养20h后,得一级种子;
78.s3、二级种子培养
79.二级种子培养在5m3发酵罐中进行;在发酵罐内配制3m3营养液,二级种子营养液配制成分包括:85wt%磷酸45l,二水硫酸钙1.2kg,硫酸钾24kg,七水硫酸镁18kg,甘油108kg和微量元素溶液9l,其余为水;所述的微量元素溶液为:五水硫酸铜14g/l,碘化钾0.08g/l,一水硫酸锰4g/l,二水钼酸钠0.1g/l,硼酸0.1g/l,六水合氯化钴1g/l;
80.按照步骤s2灭菌方法对二级种子营养液进行蒸汽灭菌,灭菌完成后,用35wt%的氨水调营养液ph值至5.0,然后将培养好的一级种子30l接种到3m3的营养液中,接种量为1%;接种前应检查一级种子质量,镜检种子菌体整齐,健壮,无杂菌污染,接种时二级种子罐罐压在0.3barg,一级种子罐罐压在1.0barg,通过富氧空气压力将一级种子从一级种子罐压到二级种子罐中,接种完成后,保持二级种子罐温度32℃,通风比1:1.5vol,罐压0.5barg,ph5.5,培养24h,得二级种子;
81.s4、发酵罐甲醇蛋白生产
82.按照步骤s3的蒸汽灭菌方法、及所需成分和配比,制备含二级种子的营养液2罐共10m3,然后以4m3/h的进料速度,泵打含二级种子营养液至层流罐中,同时打开蒸汽阀门,将蒸汽与发酵营养液混合,使发酵培养基温度达到125℃,进入在层流罐中维持20min后,进入100m3发酵罐中,总进料量为发酵罐体积的10%,即10m3;接种完毕后,关闭进料阀,并将100m3发酵罐温度维持在121℃30min,此时,用蒸汽对与100m3发酵罐相连的富氧空气过滤器、发酵罐取样口、出料口、排气口管道进行灭菌,保证100m3发酵罐及与之相连管道呈无菌状态,灭菌结束后,对100m3发酵罐内的发酵营养液降温到35℃;用40wt%的氨水调发酵营养液至ph5.0后开始发酵,发酵温度32℃,通风比1:2vol,罐压0.4barg,ph5.5,培养20h;在此过程中蒸汽灭菌后富氧空气不断通入发酵罐底部,并通过搅拌促进氧气溶解;待罐内料液中的甘油消耗完,溶氧开始持续上升,罐内菌体od600达到40,发酵液密度达到120g/l,向100m3发酵罐内流加甲醇,甲醇流加量为6克/升.小时,当溶氧高于60%以上时,加大甲醇流加量,最大流加量达到15克/升.小时,发酵过程中,每8小时补加一次微量元素溶液,每次流加15升,直至发酵结束,发酵72小时后,取样测定菌体湿重达600g/l,发酵结束,得发酵液;甲醇蛋白合成的副产co2与电解单元的电解制氢,反应合成粗甲醇,反应热用于下游粗甲醇精馏辅热,甲醇精馏塔中通入甲醇合成塔中反应合成的粗甲醇,精甲醇用于上述甲醇蛋白合成过程;
83.s5、发酵液出料及细菌处理
84.发酵结束后,调整含粗产品发酵液的ph值使细菌凝聚,再利用罐压将发酵液导入到发酵液储罐中,静置沉降8小时,沉降液经卧螺离心机离心分离得菌泥,滤液灭菌后返回发酵罐使用,菌泥经闪蒸脱水、干燥得到甲醇蛋白产品,蛋白含量达到75wt%以上。