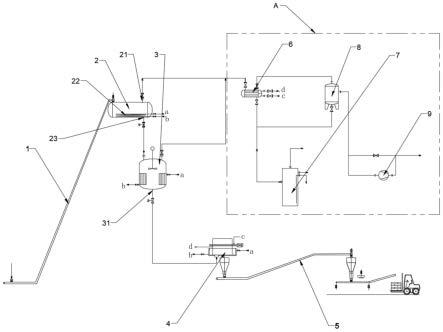
1.本发明涉及工业芴加工技术领域,更具体而言,涉及一种工业芴熔融循环干燥方法及其干燥系统。
背景技术:2.洗油加工得到的富含芴馏份经过结晶、分离可得到芴的晶体,这种芴的晶体含有一定的水分和溶剂,称为湿工业芴;作为商品对水分和溶剂含量有严格要求,目前工业上普遍采用对湿工业芴晶体颗粒直接干燥的方法去除水分和溶剂。这种方法存在的突出问题是:由于芴的熔点为114.77℃,为了防止干燥过程芴熔化,只能在较低温度下进行干燥,用热水作为干燥的加热介质,一般控制干燥温度不大于100℃,而湿工业芴中溶剂的沸点135
‑‑
145℃,存在着温度控制低了水和溶剂脱出效果不好,满足不了市场要求,温度控制高了造成芴晶体颗粒熔化不能正常生产的状况,严重影响生产。为了提高干燥效果满足市场需求,很多企业在工业芴干燥过程当中采取以下措施:降低处理量;向干燥机内通惰性气体;进行二次干燥。以上措施存在以下问题:向干燥机内通惰性气体,排放出的尾气污染环境;降低处理量和进行二次干燥会影响产量;市场需求含湿量更低的工业芴时,上述措施仍然达不到要求,工业芴的干燥成了工业芴生产过程的瓶颈。
3.因此,有必要开发一种新型的湿工业芴干燥工艺,以解决湿工业芴脱溶剂脱水效果不好的问题以及对环境的影响。
技术实现要素:4.为了克服现有技术中存在的不足,提供一种干燥效果好、处理能力大、环保的工业芴熔融循环干燥方法及其干燥系统。
5.为了解决上述技术问题,本发明采用的技术方案为:
6.一种工业芴熔融循环干燥方法,包括:
7.s1、将工业芴结晶过程产生的湿工业芴晶体输送至熔化槽加热熔化;
8.s2、熔化后的湿工业芴靠位差自流到熔融干燥器,熔融干燥器内自上而下依次安装有搅拌器、加热管束和中心管,液态工业芴在搅拌器作用下强制流动,流至加热管束和中心管内,因受热程度不同形成自然流动,脱除溶剂和水分;
9.s3、熔化槽和熔融干燥器顶部的汽相物料通过管道进入冷凝冷却器被冷凝冷却为水和溶剂的混合液;混合液靠位差自流到油水分离器中;通过比重差进行静置分离,分离后的溶剂靠位差自流到溶剂储槽循环使用;分离的水进入污水处理装置;
10.s4、冷凝冷却器中未冷凝的气体物料携带部分液滴进入真空罐并被捕集下来,再送入油水分离器中,与冷凝冷却器冷凝冷却的混合液一起进行油水分离;真空罐中的不凝气经真空泵输送到尾气处理系统进行处理;
11.s5、脱除溶剂和水分的工业芴依靠位差自流至切片机底部,被凝固并切成片状,经包装入库。
12.优选的,所述熔化槽的融化温度为120-140℃,熔化槽压力为0kpa至负60kpa。
13.优选的,熔融干燥器干燥温度130
‑‑
180℃,干燥压力为0kpa至负60kpa。
14.优选的,所述工业芴在熔融干燥器内停留时间为2
‑‑
6小时。
15.一种工业芴熔融循环干燥系统,包括冷凝冷却器、油水分离器以及依次连接的上料装置、熔化槽、熔融干燥器、切片机和出料装置;所述熔化槽的液相物料出口ⅰ与熔融干燥器的进料口连接,所述熔融干燥器的液相物料出口ⅱ与切片机的进料管道连接;所述熔化槽的气相物料出口ⅰ与冷凝冷却器的气相物料入口ⅰ连接,所述冷凝冷却器的液相物料出口ⅲ与油水分离器的物料入口连接,所述冷凝冷却器内设置有冷却水管路ⅰ。
16.为了进一步的的优化,还包括真空罐,真空罐的气相物料进口ⅱ与冷凝冷却器的气相物料出口ⅱ连通,真空罐的液相物料出口ⅳ与油水分离器的物料入口连接。
17.为了实现熔融干燥,所述熔化槽内安装有加热盘管ⅰ,所述加热盘管ⅰ的加热介质为蒸汽或导热油,所述熔融干燥器内设置有加热盘管ⅱ和搅拌器,所述加热盘管ⅱ的加热介质为蒸汽或导热油;
18.所述上料装置和出料装置均采用管链式输送机,所述上料装置的上料端设置在地面上,所述出料装置的下料端连接有包装机组;所述熔融干燥器内安装有搅拌器、加热管束和中心管,中心管截面积是熔融干燥器截面积的40%
‑‑
60%。
19.为了对分离后的溶剂回收利用,所述油水分离器的溶剂油出口管道连接有溶剂油储槽,油水分离器的分离水出口管路与污水处理系统连接。
20.进一步的,所述熔化槽安装高度为10~12m,所述熔融干燥器的安装高度为6.5~8.5m,所述切片机安装在地面上;
21.所述冷凝冷却器的安装高度为9~11m,所述油水分离器的安装高度为4~6m,所述真空罐的安装高度为9~11m。
22.进一步的,所述切片机为不锈钢材质,切片机中设置有冷却水管路,切片机的受料盘入口处设置有液封装置,受料盘底部设置有加热夹层;
23.所述真空罐连接有真空泵,所述真空泵安装在地面上,真空泵的出口管道与尾气处理系统连接。
24.本发明与现有技术相比所具有的有益效果为:
25.1、本发明采用熔融干燥器在负压和较高温度下进行脱水、脱溶剂,操作灵活、干燥效果好、提高了处理能力、提高了成品工业芴质量,干燥过程没有氮气进入系统,环境污染小。对高温煤焦油230-300℃馏份油蒸馏过程得到的富含芴组分再经过结晶得到湿工业芴,用熔融加热的方法脱除湿工业芴中残留溶剂和水分,并对脱除了溶剂和水分的液态工业芴进行切片包装。
26.2、与现有技术相比,本发明的工业芴熔融干燥的生产工艺具有自动化水平高、操作简单、产量高、环保等优点;工业芴含湿由原来的1.0%降至0.3%,效果非常明显。
附图说明
27.下面将通过附图对本发明的具体实施方式做进一步的详细说明。
28.图1为本发明结构示意图;
29.图2为图1中a的局部放大图。
30.图中:1-上料装置,2-熔化槽,21-气相物料出口ⅰ,22-加热盘管ⅰ,23-液相物料出口ⅰ,3-熔融干燥器,31-液相物料出口ⅱ,4-切片机,5-出料装置,6-冷凝冷却器,61-气相物料入口ⅰ,62-液相物料出口ⅲ,63-冷却水管路ⅰ,64-气相物料出口ⅱ,7-油水分离器,71-物料入口,72-溶剂油出口管道,73-分离水出口管路,8-真空罐,81-气相物料进口ⅱ,82-液相物料出口ⅳ,9-真空泵,91-出口管道。
具体实施方式
31.下面将结合本发明实施例中的附图,对本发明实施例中的技术方案进行清楚、完整地描述,显然,所描述的实施例仅仅是本发明一部分实施例,而不是全部的实施例。基于本发明中的实施例,本领域普通技术人员在没有做出创造性劳动前提下所获得的所有其他实施例,都属于本发明保护的范围。
32.实施例1:
33.如图1至图2所示,一种工业芴熔融循环干燥方法,包括:
34.s1、将通过芴结晶工序后过来的湿工业芴由管链式输送机输送至熔化槽2,熔化槽2内安装有加热盘管,加热盘管内通蒸汽或导热油,熔化槽2内的湿工业芴被间接加热熔化;
35.s2、熔化了的湿工业芴靠位差由熔化槽2自流到熔融干燥器3,熔融干燥器3内安装有搅拌器、加热管束和中心管;在熔融干燥器3上部,液态工业芴在搅拌器作用下强制流动,熔融干燥器3下部,由于液态工业芴在加热管束和中心管内受热程度不同形成自然流动,湿工业芴中的溶剂和水分在搅动状态下被加热汽化;
36.s3、熔化槽2和熔融干燥器3顶部的汽相物料是溶剂和水的混合汽,进入冷凝冷却器6后被冷凝冷却,冷凝冷却后的水和溶剂混合液通过冷凝冷却器6底部靠位差自流到油水分离器7,混合液在油水分离器7内靠比重差进行静置分离,分离后的溶剂靠位差自流到溶剂储槽循环使用;分离水进入污水处理装置;
37.s4、在冷凝冷却器6未冷凝的气体物料携带部分液滴进入真空罐8,被携带的液滴在真空罐8被捕集下来,通过底部液体物料出口进入油水分离器7,与冷凝冷却器6底部的混合液一起进行油水分离;真空罐8的不凝气经真空泵9输送到尾气处理系统进行处理。
38.s5、脱除溶剂和水分的工业芴,靠位差由熔融干燥器3自流至切片机4底部,液体工业芴经切片机4被冷却凝固并切成片状由成品工业芴管链输送机输送至包装机组,经包装、运输入库或出厂。
39.所述熔化槽2材质为不锈钢,加热介质为蒸汽或导热油;熔化槽至熔融干燥器3的熔融工业芴管道为不锈钢材质。所述熔融干燥器3材质为不锈钢,加热介质为蒸汽或导热油;熔融干燥器3至切片机4的干燥后工业芴管道为不锈钢材质。所述切片机4材质为不锈钢,其受料盘底部有加热夹层,加热介质为蒸汽或导热油,冷却介质为循环水。
40.熔化槽的融化温度为120-140℃,熔化槽压力为0kpa至负60kpa,熔融干燥器干燥温度130
‑‑
180℃,干燥压力为0kpa至负60kpa,熔融干燥器3内部搅拌器转速为20-60r/min,熔融干燥器中心管截面积是熔融干燥器3截面积的40%-60%,优选为50%;物料在熔融干燥器3内的停留时间为2-6小时,优选为4小时;所述冷凝冷却器6冷却后的混合液温度小于40℃。
41.实施例2:
42.如图1、图2所示,一种熔融法工业芴干燥系统,可应用于实施例1的一种工业芴熔融循环干燥方法,包括依次连接的上料装置1、熔化槽2、熔融干燥器3、切片机4、出料装置5以及冷凝冷却器6、油水分离器7和真空罐8,上料装置1和出料装置5均采用管链式输送机,上料装置1的上料端设置在地面上,下料端与熔化槽对接,出料装置5的上料端与切片机4对接,出料装置5的下料端可连接包装机组,实现自动包装。
43.熔化槽2用于对由芴结晶工序来的含湿量2%左右的湿工业芴晶体进行融化,熔化槽2上端设置有物料入口和气相物料出口ⅰ21,湿工业芴晶体通过上料装置1进入熔化槽2的物料入口,熔化槽2内安装有加热盘管ⅰ22,加热盘管ⅰ22的进出口接管分别与热介质进出管道连接,加热盘管ⅰ22的加热介质可采用蒸汽或导热油等,通过加热盘管ⅰ22对湿工业芴进行融化,温度为130℃,压力为30kpa,熔化槽2下端设置有液相物料出口ⅰ23。
44.熔融干燥器3上端设置有进料口和气相物料出口,进料口与熔化槽2的液相物料出口ⅰ连通,熔融干燥器3内设置有加热盘管ⅱ32和搅拌器33,加热盘管ⅱ32的加热介质为蒸汽或导热油,熔融干燥器3在150℃、30kpa、搅拌的条件下进行干燥,含湿量降至0.5%以下,熔融干燥器3的下端设置有液相物料出口ⅱ31。
45.切片机4为不锈钢材质,切片机4中设置有冷却水管路,切片机4的受料盘入口处设置有液封装置,受料盘底部设置有加热夹层。熔融干燥器的液相物料出口ⅱ31与液封装置连接,物料经液封装置进入受料盘,经凝固、切片后进入出料装置5。
46.熔化槽2安装高度为10~12m,熔融干燥器3的安装高度为6.5~8.5m,切片机4安装在地面上,熔化槽2、熔融干燥器3、切片机4之间液体物料的传输依靠位差自流。
47.图中a为热介质入口,b为热介质出口;c为冷却水入口,d为冷却水出口。
48.熔化槽2的气相物料出口ⅰ21及熔融干燥器的气相物料出口均与冷凝冷却器6的气相物料入口ⅰ61连接,冷凝冷却器6内设置有冷却水管路ⅰ63,熔化槽2和熔融干燥器3顶部的汽相物料进入冷凝冷却器6被冷凝冷却,冷凝冷却的液体物料是水和溶剂的混合液。
49.冷凝冷却器6的液相物料出口ⅲ62与油水分离器7的物料入口71连接,混合液由冷凝冷却器6底部靠位差自流到油水分离器7内,靠比重差进行静置分离,分离后的溶剂靠位差自流到溶剂储槽循环使用,分离水进入污水处理装置。
50.真空罐8的气相物料进口ⅱ81与冷凝冷却器6的气相物料出口ⅱ64连通,真空罐8的液相物料出口ⅳ82与油水分离器7的物料入口71连接。冷凝冷却器6未冷凝的气体物料携带部分液滴进入真空罐8,被携带的液滴在真空罐8被捕集下来,由底部液体物料出口进入油水分离器,与冷凝冷却器6底部的混合液一起油水分离;真空罐8连接有真空泵9,真空泵9安装在地面上,真空泵9的出口管道91与尾气处理系统连接,真空罐8的不凝气经真空泵输送到尾气处理系统进行处理。
51.冷凝冷却器6的安装高度为9~11m,油水分离器7的安装高度为4~6m,所述真空罐8的安装高度为9~11m,冷却冷凝器6、油水分离器7的液相物料通过位差自流进入油水分离器。
52.上面仅对本发明的较佳实施例作了详细说明,但是本发明并不限于上述实施例,在本领域普通技术人员所具备的知识范围内,还可以在不脱离本发明宗旨的前提下作出各种变化,各种变化均应包含在本发明的保护范围之内。