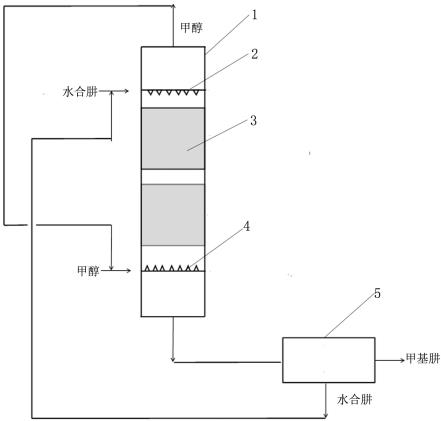
1.本发明涉及甲基肼制备技术领域,具体地来说,涉及一种催化合成甲基肼的新工艺。
背景技术:2.甲基肼,又名一甲基肼,在医药、农药、染料等行业应用广泛,同时因其具备冰点低、热稳定性好和燃烧过程稳定等优点,被认定位航空和导弹领域的高价值化合物。
3.目前,国内生产工艺成熟且应用广泛的合成甲基肼的工艺是盐酸甲醇水合肼法工艺,如中国专利cn102516117a所述,在惰性气体保护下,以盐酸肼与甲醇反应,再以水合肼游离甲基肼盐酸盐,再经过蒸馏和精馏工艺获得甲基肼;该工艺的原料易得、相对成本低,但甲基化程度低,副产物比较多,生成的大量副产物比如偏二甲基肼、1,2-二甲基肼以及其水合肼的其他剧毒衍生物,大量复杂的副产物导致后续分离难度大,生产能耗高,且处理剧毒衍生物导致环境污染严重,更浪费了资源。
4.针对上述问题,中国专利cn106543026 a,公开了一种一步法制备甲基肼的方法,该方法是在惰性气体保护下,将水合肼与甲醇在催化剂作用下进行烷基化反应一步合成甲基肼,在反应过程中保持甲醇过量,将反应结束后的混合液通过精馏得到高纯度的甲基肼溶液;该工艺虽然具备副产物少,原材料价格低廉的优点,但是该工艺需以在亚硫酸氢钠和对甲苯磺酸钠为催化剂,催化剂腐蚀性较强,对设备的耐腐蚀性要求高,同时仍然存在着盐酸肼转化率及甲基肼选择性一般的技术问题。
5.而中国专利cn 114292208 a,公开了一种固体酸催化制备甲基肼的方法,文中提出“在水热釜中加入一定量的盐酸肼、甲醇、水以及固体酸催化剂,一定温度下反应1小时以上,反应结束后冷却至室温,分离出催化剂,再加入水合肼游离出甲基肼,并通过精馏得到甲基肼水溶液,所述固体酸催化剂选自钨基催化剂、离子交换树脂、γ-al2o3、zsm-5分子筛中的一种或者多种的组合”;该现有技术虽然使用固体酸为催化剂,降低了设备要求,并在一定程度上提高了盐酸肼转化率及甲基肼选择性,但是其整体反应效率仍然较为一般,且其中的甲醇无法进行循环利用,作为优选的钨基催化剂需要稀土金属制备,生产成本高,整体操作步骤繁琐,不利于大规模化工业生产。
6.为此,需要一种新的技术方案解决上述技术问题。
技术实现要素:7.本发明的目的在于提供一种催化合成甲基肼的新工艺,以解决上述背景技术提出的现阶段制备甲基肼的工艺,其在提高甲基肼收率的同时,无法兼顾提升催化合成甲基肼时的反应效率,同时其生产成本高,整体操作步骤繁琐,不利于大规模化工业生产的技术问题。
8.为实现上述技术问题,本发明采取以下技术方案:一种催化合成甲基肼的新工艺,包括以下步骤:
s1、将固体酸催化剂γ-al2o3采用溶胶凝胶法负载在金属基填料的表面,制得催化填料,所述金属基填料为鲍尔环填料、西塔环填料或金属丝网波纹填料;s2、将催化填料以乱堆形式堆积成上下两个0.45m的催化床层,催化床层安装于反应器的中部,在催化床层的上方和下方分别设置液体分布器和气体分布器;s3、在0.2~0.6mpa、100~140℃的条件下,使液态的水合肼和气态的甲醇在催化床层逆流接触,经过反应、分离,制得甲基肼;其中,所述步骤s1的具体操作方法如下:首先,将金属基填料清理干净,浸入含20%alooh的溶胶中,90s后缓慢提出,并在室温下干燥12h;然后,将金属基填料放入烘箱中,以50℃
·h-1
的速率升温至120℃,再保温2h;最后,将金属基填料放入马弗炉中,以35℃
·h-1
的速率升温至550℃,再保温2h;所述步骤s3中,水合肼从反应器的上部经液体分布器以3m3·
m-2
·h-1
的流量进入催化床层,甲醇从反应器的下部经气体分布器以85 m3·
m-2
·h-1
的流量进入催化床层,未反应的水合肼、反应生成的甲基肼和水,以混合液体的形式从反应器的底部流出后,进入精馏塔进行分离,分别得到甲基肼和水合肼,其中,水合肼经液体分布器进入催化床层循环套用,未反应的甲醇以气态的形式从反应器的顶部流出后,经气体分布器进入催化床层循环套用。
9.与现有技术相比,本发明的有益效果是:1.本发明中通过将固体酸催化剂γ-al2o3负载采用溶胶凝胶法在具有较高的比表面积和空隙率的金属基填料的表面,制得催化填料,然后将催化填料以乱堆形式堆积成上下两个催化床层,再使液态的水合肼和气态的甲醇在催化床层逆流接触,并严格控制水合肼和甲醇的温度及压力,在大幅度地提升水合肼转化率及甲基肼选择性,抑制副产物1,1-二甲基肼的大量生成,从而提升甲基肼收率的同时,以逆流的方式增强了水合肼和甲醇的气液传质,提高了对于催化床层的利用率,配合利用催化床层的金属基填料具有高比表面积和空隙率的特点,极大地提高了整体的反应效率,在此基础上,本发明为利用水合肼与甲醇一步法制备甲基肼,反应过程简单,原料易得,生产成本低,利于大规模化工业生产;2.本发明中的固体酸催化剂直接负载在金属基填料的表面,与现有技术中与反应产物混合在一起,后续需过滤去除相比,循环利用更为方便,简化了操作步骤,进一步降低了生产成本;同时,固体酸催化剂采用包括浸渍、煅烧步骤的溶胶凝胶法负载在金属基填料的表面,与金属基填料的结合效果更强,从而进一步增强了对于催化床层的利用率,提升了甲基肼的收率和反应效率;3. 本发明中将未反应的甲醇和反应产物中精馏分离出的未反应的水合肼进行循环套用,有效地降低了生产成本。
附图说明
10.图1为本发明的工作原理示意图;图中:1、反应器,2、液体分布器,3、催化床层,4、气体分布器,5、精馏塔。
具体实施方式
11.下面将结合实施例和附图,对本发明的技术方案进行清楚、完整地描述。
12.实施例1
甲基肼的制备:s1、将固体酸催化剂γ-al2o3采用溶胶凝胶法负载在金属基填料(本实施例选择鲍尔环填料)的表面,制得催化填料,具体地,将鲍尔环填料清理干净,浸入含20%alooh的溶胶中,90s后缓慢提出,并在室温下干燥12h;然后,将鲍尔环填料放入烘箱中,以50℃
·h-1
的速率升温至120℃,再保温2h;最后,将鲍尔环填料放入马弗炉中,以35℃
·h-1
的速率升温至550℃(根据实际的需要,可以为450~800℃,升温速率也可以此为基准进行调整),再保温2h,制得催化填料;s2、将步骤s1制备的催化填料以乱堆形式堆积成上下两个0.45m的催化床层3,催化床层3安装于反应器1的中部,在催化床层3的上方和下方分别设置液体分布器2和气体分布器4;s3、先浸湿催化床层3的表面,然后,使110℃,5.0mpa的液态的水合肼,从反应器1的上部经液体分布器2进入催化床层3,以1.5m3·
m-2
·h-1
的流量从催化床层3由上往下流动,同时,使110℃,5.0mpa的甲醇,从反应器1的下部经气体分布器4进入催化床层3,以50m3·
m-2
·h-1
的流量从催化床层3由下往上流动;s4、甲醇与水合肼在催化床层3的表面逆流接触,未反应的水合肼、反应生成的甲基肼和水,以混合液体的形式从反应器1的底部流出后,进入精馏塔5进行分离,分别得到甲基肼和水合肼,其中,水合肼经液体分布器2进入催化床层3循环套用,未反应的甲醇以气态的形式从反应器1的顶部流出后,经气体分布器4进入催化床层3循环套用。
13.实施例2本实施例与实施例1基本相同,不同之处在于,金属基填料选择金属丝网波纹填料。
14.实施例3本实施例与实施例1基本相同,不同之处在于,金属基填料选择西塔环填料。
15.检测实施例1 ~3 的收率,结果见表1。
16.表1由表1可知,金属基填料选择西塔环填料,得到的甲基肼的收率最高,1,1-二甲基肼收率的最低;因此,在以下实施例中,金属基填料选择西塔环填料。
17.实施例4本实施例与实施例3基本相同,不同之处在于,改变甲醇和水合肼的流量。
18.实施例5本实施例与实施例4基本相同,不同之处在于,改变甲醇和水合肼的流量。
19.实施例6本实施例与实施例4和5基本相同,不同之处在于,改变甲醇和水合肼的流量。
20.实施例7本实施例与实施例4、5和6基本相同,不同之处在于,改变甲醇和水合肼的流量。
21.实施例8本实施例与实施例4、5、6和7基本相同,不同之处在于,改变甲醇和水合肼的流量。
22.检测实施例4 ~8的收率,结果见表2。
23.表2由表2可知,实施例4~6中,同时增加甲醇和水合肼的流量,其中实施例6的甲基肼的收率有所降低,可能是液膜厚度比较大,造成收率降低;而实施例7~8中,增加甲醇的流量,两者收率变化不大,因而选用实施例7为优化实施例,在以下实施例中,甲醇和水合肼的流量与实施例7相同,水合肼的流量为3m3·
m-2
·h-1
,甲醇的流量为85m3·
m-2
·h-1
。
24.实施例9本实施例与实施例7基本相同,不同之处在于,改变步骤s3反应时的温度和压力。
25.实施例10本实施例与实施例9基本相同,不同之处在于,改变步骤s3反应时的温度和压力。
26.实施例11本实施例与实施例9和10基本相同,不同之处在于,改变步骤s3反应时的温度和压力。
27.实施例12本实施例与实施例9、10和11基本相同,不同之处在于,改变步骤s3反应时的温度和压力。
28.实施例13本实施例与实施例9、10、11和12基本相同,不同之处在于,改变步骤s3反应时的温度和压力。
29.检测实施例9 ~13的收率,结果见表3。
30.表3
由表3可知,实施例9~11中,降低温度,甲基肼的收率也会降低,提高温度,甲基肼的收率变化不大,但副产品1,1-二甲基肼的收率有了较大的增加,因此,优选温度为实施例10的130℃;实施例12~13中,保持温度在130℃,降低压力,甲基肼的收率有较大降低,提高压力,甲基肼的收率变化不大,但副产品1,1-二甲基肼的收率有了较大的增加。