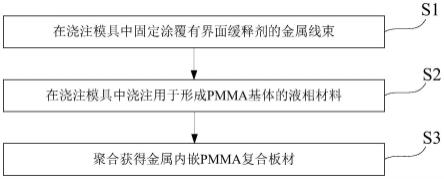
金属内嵌pmma复合板材的制造方法、金属内嵌pmma复合板材
技术领域
1.本技术涉及复合材料技术领域,具体涉及一种金属内嵌pmma复合板材的制造方法、金属内嵌pmma复合板材。
背景技术:2.聚甲基丙烯酸甲酯(polymethyl methacrylate,pmma),作为一种综合性能优异的透明高分子材料,在交通隔音屏障、建筑透明/隔热幕墙、飞行器舷窗、特大桥风障等领域获得了广泛应用。具体而言,以高铁或市域轨道降噪设施为例,若单独使用预设厚度的pmma板材作为声障主体材料,则存在交通安全与生态环境方面的双重隐患,前者主要体现在因pmma材料的硬质脆性使其在受到撞击后,易产生大量飞行碎片,危及附近道路或下方(如高架)的行人与车辆安全;后者主要考虑鸟类难以识别透明pmma板材而在飞行过程中的误撞风险。
3.现有技术,一般通过在pmma制造过程中,以适宜间距内嵌黑色尼龙线束的方式,形成加线束pmma复合材料,在适度提升耐冲击性能的同时,形成一定的拖曳效果而减少碎片飞溅或坠落,且易于鸟类辨识,从而解决以上隐患。尽管如此,尼龙材质相比金属,仍在拉伸强度与耐冲击性上有较大差距,即在同等情况下,金属线束替代尼龙后,相应pmma复合板材的撞击后坠落风险将显著改善,然而在制造金属内嵌pmma复合板材时,始终无法解决pmma的单体聚合引起的体积收缩与金属线束的体积变化之间的差异、以及提前发生相界面咬合,导致所得到的复合板材弯曲,形成了pmma复合板材制造领域的技术壁垒,难以突破。
技术实现要素:4.针对上述技术问题,本技术提供一种金属内嵌pmma复合板材的制造方法、金属内嵌pmma复合板材,避免因液相材料聚合过程中的体积收缩与金属线束的体积变化不匹配、以及提前发生相界面咬合,而导致复合板材弯曲的问题。
5.为解决上述技术问题,本技术提供一种金属内嵌pmma复合板材的制造方法,包括以下步骤:
6.步骤s1,在浇注模具中固定涂覆有界面缓释剂的金属线束;
7.步骤s2,在所述浇注模具中浇注用于形成pmma基体的液相材料;
8.步骤s3,聚合获得金属内嵌pmma复合板材。
9.可选地,所述界面缓释剂在20℃与1个标准大气压条件下,在mma(methyl methacrylate,甲基丙烯酸甲酯)溶剂中的溶解度为0.01g/100g mma~10g/100g mma。
10.可选地,所述界面缓释剂包括正辛烷、正壬烷、正癸烷、十二烷、十三烷、十四烷、十五烷、十六烷、十七烷、十八烷、正辛醇、正壬醇、正癸醇、十二醇、1-十三醇、十四醇、1-十五醇、十六醇、十七醇、十八醇、丁醚、正戊醚、己基醚、庚醚、正辛醚、正辛酸、壬酸、正癸酸、十一酸、十二酸苯酯、2-羟基十二烷酸、3-羟基十二烷酸、12-羟基十二酸、12-氨基十二酸、十二酸甲酯、硬脂酸、棕榈蜡、切片石蜡、液体石蜡中的一种或几种。
11.可选地,所述步骤s1,包括:
12.提供浇注模具,所述浇注模具中设有定位支架,所述定位支架设有用于穿过所述金属线束的定位通孔;
13.将所述金属线束穿过所述定位支架上的定位通孔;
14.在所述金属线束的表面涂覆界面缓释剂。
15.可选地,所述定位支架为pmma材质,所述定位通孔与所述金属线束之间间隙配合。
16.可选地,所述浇注模具包括环状胶条、上模板及下模板,所述环状胶条夹设于所述上模板与所述下模板之间,与所述上模板、所述下模板共同形成一型腔,所述定位支架位于所述型腔中,所述环状胶条的位于所述定位支架长度方向两侧的部分设有安装通孔,所述金属线束的端部穿出所述安装通孔。
17.可选地,所述安装通孔与所述金属线束之间过盈配合,所述金属线束采用单向锁紧卡扣固定,所述单向锁紧卡扣与所述上模板及下模板的侧面相抵。
18.可选地,所述步骤s3,包括:
19.低温阶段:在45~65℃加热2~72h;
20.高温阶段:在95~125℃加热1~12h。
21.可选地,所述界面缓释剂与mma的相溶性满足以下条件:
22.在所述低温阶段结束时,所述金属线束表面的界面缓释剂未扩散完成;
23.在所述高温阶段结束时,所述金属线束表面的界面缓释剂扩散完成。
24.本技术还提供一种金属内嵌pmma复合板材,采用如上任一项所述的金属内嵌pmma复合板材的制造方法制造得到。
25.本技术的金属内嵌pmma复合板材的制造方法,包括以下步骤:在浇注模具中固定涂覆有界面缓释剂的金属线束;在所述浇注模具中浇注用于形成pmma基体的液相材料;聚合获得金属内嵌pmma复合板材。还涉及采用上述制造方法制造得到的金属内嵌pmma复合板材。本技术在金属线束的表面涂覆界面缓释剂,可以在液相材料聚合过程中缓慢改变金属线束和聚合产物之间的隔离状态直至形成力学咬合,保证金属线束的原有空间位置在聚合过程中基本不发生改变,避免因液相材料聚合过程中的体积收缩与金属线束的体积变化不匹配、以及提前发生相界面咬合,而导致复合板材弯曲的问题。
附图说明
26.图1是根据第一实施例示出的金属内嵌pmma复合板材的斜视图;
27.图2是根据第一实施例示出的金属内嵌pmma复合板材的内部构造示意图;
28.图3是根据第一实施例示出的金属内嵌pmma复合板材的横截面局部结构示意图;
29.图4是根据第二实施例示出的金属内嵌pmma复合板材的制造方法的流程示意图;
30.图5是根据第二实施例示出的金属内嵌pmma复合板材的制造方法中所涉及的界面缓释剂扩散过程示意图;
31.图6是根据第二实施例示出的金属内嵌pmma复合板材的制造方法中所涉及的定位支架及其与金属线束空间关系的俯视图;
32.图7是根据第二实施例示出的单向锁紧卡扣的使用过程示意图;
33.图8是根据第二实施例示出的单向锁紧卡扣的工作原理示意图;
34.图9是现有技术与第二实施例得到的金属内嵌pmma复合板材的效果对比图;
35.图10是根据工艺1、工艺2及工艺3中相应复合板材的冲击强度数据对比。
具体实施方式
36.以下由特定的具体实施例说明本技术的实施方式,熟悉此技术的人士可由本说明书所揭露的内容轻易地了解本技术的其他优点及功效。
37.在下述描述中,参考附图,附图描述了本技术的若干实施例。应当理解,还可使用其他实施例,并且可以在不背离本技术的精神和范围的情况下进行机械组成、结构、电气以及操作上的改变。下面的详细描述不应该被认为是限制性的,这里使用的术语仅是为了描述特定实施例,而并非旨在限制本技术。
38.虽然在一些实例中术语第一、第二等在本文中用来描述各种元件,但是这些元件不应当被这些术语限制。这些术语仅用来将一个元件与另一个元件进行区分。
39.再者,如同在本文中所使用的,单数形式“一”、“一个”和“该”旨在也包括复数形式,除非上下文中有相反的指示。应当进一步理解,术语“包含”、“包括”表明存在所述的特征、步骤、操作、元件、组件、项目、种类、和/或组,但不排除一个或多个其他特征、步骤、操作、元件、组件、项目、种类、和/或组的存在、出现或添加。此处使用的术语“或”和“和/或”被解释为包括性的,或意味着任一个或任何组合。因此,“a、b或c”或者“a、b和/或c”意味着“以下任一个:a;b;c;a和b;a和c;b和c;a、b和c”。仅当元件、功能、步骤或操作的组合在某些方式下内在地互相排斥时,才会出现该定义的例外。
40.第一实施例
41.如图1与图2所示,本技术提供一种金属内嵌pmma复合板材,包括金属线束100与pmma基体120。
42.请一并参考图3,金属线束位100沿pmma基体120的长度或宽度方向间隔平行设置,优选地,在pmma基体120厚度方向的居中位置、长度或宽度方向为预设间距平行排列,也即b1=b2,a1=a2。
43.金属线束100的材质,可以为铁、铝及其合金中的一种,其形态包括多股绞线或单股棒材,其直径为0.5~5mm,其排列间距为2~20cm。
44.此外,基于本技术的第二实施例的制造方法,本技术的金属内嵌pmma复合板材的pmma基体120中还分散有界面缓释剂,界面缓释剂主要分布在金属线束100的周围区域。一些实施例中,pmma基体120中还可包含用于对金属线束位100进行支撑定位的定位支架。关于界面缓释剂和定位支架将在第二实施例中进行详细说明。
45.第二实施例
46.图4是根据第二实施例示出的金属内嵌pmma复合板材的制造方法的流程示意图。如图4所示,本技术的金属内嵌pmma复合板材的制造方法,包括以下步骤:
47.步骤s1,在浇注模具中固定涂覆有界面缓释剂的金属线束;
48.步骤s2,在浇注模具中浇注用于形成pmma基体的液相材料;
49.步骤s3,聚合获得金属内嵌pmma复合板材。
50.可选地,界面缓释剂为线型的饱和脂肪链或杂链,具体化学结构可以为:
[0051][0052]
其中,r1为ch3、cooch3中的一种;r2为oh、ch3、cooh、nh2中的一种;x1为nh、o、ch2、ch-oh、ch-nh2,n为6~30的正整数。在20℃与1个标准大气压条件下,界面缓释剂在mma溶剂中的溶解度为0.01g/100g mma~10g/100g mma,从而使得在常温下,界面缓释剂基本不会或很少扩散至用于形成pmma基体的液相材料中。
[0053]
本实施例中,界面缓释剂包括正辛烷、正壬烷、正癸烷、十二烷、十三烷、十四烷、十五烷、十六烷、十七烷、十八烷、正辛醇、正壬醇、正癸醇、十二醇、1-十三醇、十四醇、1-十五醇、十六醇、十七醇、十八醇、丁醚、正戊醚、己基醚、庚醚、正辛醚、正辛酸、壬酸、正癸酸、十一酸、十二酸苯酯、2-羟基十二烷酸、3-羟基十二烷酸、12-羟基十二酸、12-氨基十二酸、十二酸甲酯、硬脂酸、棕榈蜡、切片石蜡、液体石蜡中的一种或几种。
[0054]
可选地,液相材料由用于聚合形成pmma的高分子溶液和引发剂组成为本领域常用技术,本技术不做特殊限定,可根据实际情况相宜选用,如可参照申请人在《蓝相增效pmma耐热板材的制造方法及蓝相增效pmma耐热板材》,申请号为202210285151.0中相关过程:用于形成pmma基体的液相材料,其组成可包括聚甲基丙烯酸甲酯、甲基丙烯酸甲酯及引发剂,其中由聚甲基丙烯酸甲酯与甲基丙烯酸甲酯组成的溶液在本技术中定义为高分子溶液,所述高分子溶液可以通过控制反应进程方式的甲基丙烯酸甲酯本体聚合过程阶段性中止而获得(中止点采用黏度指标为判断依据,具体黏度以25℃时涂4杯流出时间50~135s为宜),也可以通过将商购pmma树脂母粒溶于甲基丙烯酸甲酯,制成适宜黏度(以25℃时涂4杯流出时间50~135s为宜)获得,引发剂的添加阶段在以上两种方式形成高分子溶液且冷却至室温后,计算添加量时,原有本体聚合或树脂母粒中的残留引发剂含量不予考虑。
[0055]
可选地,液相材料的物质组成比例,聚甲基丙烯酸甲酯的质量占比为5~20%,引发剂的质量占比≤1%,其余为甲基丙烯酸甲酯,其中聚甲基丙烯酸甲酯和甲基丙烯酸甲酯组成所述的高分子溶液,引发剂选用临界温度在45~100℃,且半衰期在100~101h中的一种或几种,具体包括bpo、aibn、abvn、甲基乙烯基酮、安息香、二甲苯酮、荧光素、曙红中的至少一种,即可以选用单一引发剂、也可选用组合引发剂。
[0056]
可选地,在金属线束上涂覆界面缓释剂的方式可以是浸涂、擦涂、喷涂中的一种。结合图5,界面缓释剂涂于金属线束表面后,形成具有d0厚度的包覆层500。在步骤s2进行浇注时,由于室温下,界面缓释剂向液相材料118的扩散速率极其轻微,故厚度d1基本不发生改变(其中,d1≈d0),之后,在步骤s3中,伴随聚合反应的发生,界面缓释剂逐步向四周缓慢扩散(箭头600表示界面缓释剂的扩散方向),界面缓释剂的厚度逐渐降低至d2,此时,液相材料118基本转变为初步固相介质119,至聚合反应结束时,界面缓释剂的厚度进一步降低至d3(其中,d3≈0),初步固相介质119变为完全或基本完全的固相介质120,从而完成整个聚合过程。在上述聚合过程中,界面缓释剂的扩散速率为自发过程,受温度控制,即扩散速率为以温度为自变量的增函数,令界面缓释剂的扩散过程与聚合时间相适应,从而,在聚合前期与中期,聚合产物与金属线束为非接触状态,难以对其形成力学咬合,保证金属线束与mma或pmma高分子链在聚合过程中的适度物理隔离,进入聚合后期,界面缓蚀剂在金属线束表面基本无残留,使得金属线束与已初步固化的pmma基体发生直接接触,利用残留单体mma在界面处的聚合反应而形成力学咬合,以此保证金属线束的原有空间位置基本不发生改
变。可见,通过合理使用本技术中的界面缓释剂,可以在液相材料聚合过程中缓慢改变金属线束和聚合产物之间的隔离状态直至形成力学咬合,保证金属线束的原有空间位置在聚合过程中基本不发生改变,避免了因液相材料聚合过程中的体积收缩与金属线束的体积变化不匹配、以及提前发生相界面咬合而导致复合板材弯曲的问题。参考图1或图2,制造得到的板材中,金属线束平行排列于pmma基体之中,板材表面平整光洁,无肉眼可见的弯曲。
[0057]
可选地,为更好地控制聚合过程与界面缓释剂的扩散过程,提高生产效率,步骤s3,包括:
[0058]
低温阶段:在45~65℃加热2~72h;
[0059]
高温阶段:在95~125℃加热1~12h。
[0060]
可选地,界面缓释剂与mma的相溶性满足以下条件:
[0061]
在低温阶段结束时,金属线束表面的界面缓释剂未扩散完成;
[0062]
在高温阶段结束时,金属线束表面的界面缓释剂扩散完成。
[0063]
其中,请继续参考图5,聚合过程中,在低温阶段,伴随聚合反应的发生,界面缓释剂逐步向四周缓慢扩散(箭头600表示界面缓释剂的扩散方向),至低温阶段结束,厚度降低至d2(其中,d2<d1),聚合反应主体完成,液相介质118变为初步固相介质119,体积缩小程度明显,此时由于界面缓释剂的存在,聚合产物与金属线束为非接触状态,难以对其形成力学咬合,保证金属线束与mma或pmma高分子链在聚合过程中的适度物理隔离,避免金属线束的体积变化与聚合产物的体积收缩不适配、以及提前发生相界面咬合而导致的弯曲。然后进入高温阶段直至聚合反应结束,厚度进一步降低至d3(其中,d3≈0),初步固相介质119变为完全或基本完全的固相介质120,完成整个聚合过程,此时由于界面缓蚀剂在金属线束表面基本无残留,使得金属线束与已初步固化的pmma基体发生直接接触,利用残留单体mma在界面处的聚合反应形成力学咬合,从而保证金属线束的原有空间位置基本不发生改变。最终,所获得的金属内嵌pmma复合板材基本不发生弯曲。可以理解,步骤s3也可以仅包括低温阶段,此时,可以延长加热时间,直至整个聚合过程完成。
[0064]
可选地,步骤s1,可具体包括:
[0065]
提供浇注模具,浇注模具中设有定位支架,定位支架设有用于穿过金属线束的定位通孔;
[0066]
将金属线束穿过定位支架上的定位通孔;
[0067]
在金属线束的表面涂覆界面缓释剂。
[0068]
其中,在浇注模具中使用定位支架,可以增加金属线束拉直状态以及空间位置(居中与平行排列)的可靠性。使用定位支架时,定位支架保持尽可能的等间距平行排列,并与金属线束排列方向相垂直。请参考图6,定位支架的定位通孔及其与金属线束的空间关系,其中,定位支架的定位通孔分为两种,一种为镜像圆台300、一种为圆柱310,当定位通孔为镜像圆台300时,在金属线束穿过定位通孔时,在定位通孔的最细截面301处,金属线束的直径与该截面301的直径相适配,为间隙配合,金属线束与定位支架在垂直向的间距,沿金属线束水平方向,随和截面301的距离呈递增变化,此时液相材料在聚合过程中不易在金属线束与定位支架之间的重叠空间内形成气泡;当定位通孔为圆柱310时,考虑到液相材料的浸润充分性及气泡有效排出,其直径也应略大于所使用的金属线束的直径,亦为间隙配合。
[0069]
可选地,定位支架为pmma材质,因此在复合板材的成型过程中,可与形成pmma基体
的液相材料发生一定程度的互溶,即定位支架的表层会被mma单体适度溶解,与聚合产生的pmma高分子形成互穿网络,消弭液-固界面相。聚合完成后,定位支架形成于pmma复合板材中、且与pmma基体成为一个通透整体,无法用肉眼分辨。定位支架在本实施例中可以使用,也可以不使用,使用时数量与金属线束最终在pmma复合板材中的居中与平行排列效果呈正相关,但数量越多操作时间越长。实际应用时,一般以3个为宜。在使用定位支架时,优选在金属线束穿过定位支架上的定位通孔后,再于金属线束的表面涂覆界面缓释剂,以避免界面缓释剂在金属线束穿过定位通孔过程中被刮落。
[0070]
可选地,浇注模具包括环状胶条、上模板及下模板,环状胶条夹设于上模板与下模板之间,与上模板、下模板共同形成一型腔,定位支架位于型腔中,环状胶条的位于定位支架长度方向两侧的部分设有安装通孔,金属线束的端部穿出安装通孔,从而可以对金属线束的端部进行固定。其中,浇注模具为用于浇注成型的玻璃模具,其制造过程详见专利《适用于高分子快速浇注的模具》(zl 202120435162.3)及《高分子浇注模具的紧固机构及高分子浇注装置》(zl 202120246569.1)中的相关说明,在此不再赘述,主要区别在于,环状胶条的位于定位支架长度方向两侧的部分设有安装通孔,以供金属线束的端部穿出环状胶条后进行固定。可选地,安装通孔与金属线束之间过盈配合,由于胶条具有一定弹性,可对过盈状态的金属线束形成径向挤压,使安装通孔处于封闭状态,保证聚合过程中,胶条与模板形成的型腔中的液相材料不会经此通孔溢出。胶条的材质,不做特殊限定,一般具有适度弹性的高分子材料均可以,如pvc、有机硅橡胶等,胶条的截面形状,可以为圆形、椭圆形或矩形,在实际使用中发现,对矩形胶条打孔时,不易滑动,孔位精度更高,安装通孔常位于和胶条受玻璃模具夹持向的平行居中处,故矩形胶条的便利性较为突出。为了改善相同材质下胶条的受压弹性,可采用空心结构胶条,同时也降低了原材料的使用成本。定位支架预先置于浇注模具的胶条围成的框内,此步骤中为胶条已与玻璃模具的下模板嵌套锁定后进行,然后在相应对位的安装通孔中依次穿入涂有界面缓释剂的金属线束(端部分别穿入,非一端穿入后的拉伸方式),若包含定位支架,则亦同时穿过定位支架的相应通孔(且该步骤发生于穿入安装通孔之前),再将上模板覆盖其上,紧固件锁紧模具四周,进入下一个阶段。
[0071]
结合图7和图8,可选地,金属线束穿出环形胶条后,其端部采用单向锁紧卡扣固定,单向锁紧卡扣与环状胶条的外侧或玻璃模具800边缘相抵,固定金属线束两端的步骤可在浇注模具进行紧固之后进行,从而可以进一步保证金属线束处于拉直状态,与定位支架的结合使用,可以避免或减少因金属线束自重塌陷、位移等因素所引起的复合板材弯曲的问题。单向锁紧卡扣700包含径向锁紧单元703、推移活动单元702以及供金属线束穿过的内部通道(图未标识),其使用机理为:金属线束穿入推移活动单元702端,进入其内部通道至露出金属线束,沿金属线束向前推移,至所需位置,单向锁紧卡扣700的单向锁紧功能由径向锁紧单元703提供,例如,径向锁紧单元703包括伸缩弹簧、球形钢珠以及圆台型腔通道,使得金属线束只可沿前方推移(圆台型腔通道的直径递增方向,致使球形钢珠为松弛态),反方向(圆台型腔通道的直径递减方向,致使球形钢珠为压迫态)无法拔出。在本实施例中,金属线束穿过单向锁紧卡扣700后,推动单向锁紧卡扣700至其前端701对称驻留于玻璃模具800边缘、与玻璃模具800的上下模板相互抵接(如图7中b所示),从而锁定金属线束100,使其在模具内部保持拉直状态。考虑玻璃材质的模具与金属材质的单向锁紧卡扣抵接受力时的碎裂风险,可在单向锁紧卡扣的前端701表面适当进行软性材质贴附或包覆,比如橡
胶、聚氨酯等具有适度弹性的高分子材质。由于单向锁紧卡扣的相关构造或运行机理可参考现有产品,在此不再进行赘述。
[0072]
以下列举基于本实施例的制造方法的不同实现工艺:
[0073]
工艺1
[0074]
金属内嵌pmma复合板材的制造方法,厚度15mm。
[0075]
液相材料的物质组成比例,聚甲基丙烯酸甲酯的质量占比为5~15%,引发剂的质量占比≤1%,其余为甲基丙烯酸甲酯,其中聚甲基丙烯酸甲酯和甲基丙烯酸甲酯组成所述的pmma高分子溶液,引发剂选用abvn。步骤s1结束时,形成黏度特征为涂4杯表征流出时间80~120s(25℃)的液相材料。
[0076]
涂覆方式采用擦涂,具体为用无尘布蘸取界面缓释剂,涂覆于金属线束表面。选用的界面缓释剂应与mma具有适度的相溶性,应满足以下条件:在45~65℃/2~72h的低温阶段(水浴)结束时,金属线束100表面仍有少量界面缓释剂(d2>0),至95~125℃/1~12h高温阶段(空气浴)结束时,界面缓释剂已充分扩散至pmma基体。本工艺1中界面缓释剂具体为c
8-20
烷、c
8-20
醇、c
8-20
酸,依次对应组别为α1、α2、α3,另有一组α4中的金属线束为不做界面缓释剂涂覆,工艺1中所使用金属线束的截面直径均相同。
[0077]
定位支架预先置于浇注模具的胶条框内,此时为胶条已与浇注模具的下模板嵌套锁定后进行,然后在定位支架的相应通孔中依次穿入涂有界面缓释剂的金属线束,然后再穿入相应胶条的安装通孔中,再将上模板覆盖其上,紧固件锁紧模具四周。其中,定位支架始终为保持尽可能的等间距平行排列,并与金属线束排列方向相垂直。
[0078]
考虑玻璃材质的模具与金属材质的单向锁紧卡扣抵接受力时的碎裂风险,可在单向锁紧卡扣的前端701表面适当进行聚氨酯弹性材质贴附。
[0079]
聚合过程依次包括低温阶段的45~65℃下的水浴或鼓风空气浴2~72h,及高温阶段的95~125℃下的鼓风空气浴1~12h。
[0080]
工艺2
[0081]
与工艺1不同的是,金属线束替换成等直径的尼龙线束,尼龙线束的表面不涂覆界面缓释剂,其余均保持一致。
[0082]
工艺3
[0083]
空白组,不加线束。
[0084]
制样与结果分析
[0085]
工艺1中,组别分别为α1、α2、α3的复合板材,金属线束均居中平行排列于pmma基体之中,板材表面平整光洁,均无肉眼可见的弯曲(图9中h),具体而言,图9中h1表示横截面透视图、图9中h2表示正视角度透视图,其中的金属线束100为居中、平行状态;组别为α4的复合板材,金属线束存在水平向与垂直向的弯曲(图9中d),呈现横截面下的非居中(图9中d1)、正视角度下的非平行状态(图9中d2),即由pmma基体120与金属线束100所主要构成的板材呈整体弯弧状,难以正常使用。
[0086]
透光率测试通过uv-vis分光光度仪进行,工艺1~3裁成尺寸均为50mm
×
50mm
×
15mm的样品,其中工艺1、工艺2中取样均为不含金属或尼龙线束的透明区域进行相应表征,波长范围250-1100nm,其中透光率测试依据《gb/t 7134-2008浇铸型工业有机玻璃板材》进行,取用420nm波长处的透光率数据。工艺1中,α1、α2、α3、α4的透光率依次为92.31%、
92.29%、92.24%、92.36%;工艺2中,透光率为92.28%;工艺3中,透光率为92.30%。因此,工艺1~3的透光率具有较高的一致性,表明界面缓释剂对pmma复合板材的透明度基本没有影响。
[0087]
玻璃化转变温度(以下简称tg)的测试通过dsc设备进行,选择的加热温度范围为室温~200℃,升温速率为20/min℃。工艺1中组别α1、α2、α3、α4的复合板材,对应的tg分别为106℃、106℃、103℃、107℃;工艺2中复合板材的tg为105℃;工艺3中复合板材的tg为105℃。因此,工艺1~3中相应复合板材的tg值具有较高的一致性,说明界面缓释剂对pmma复合板材的耐温性能基本没有影响。
[0088]
此外,本技术还依据《gb/t 7134-2008浇铸型工业有机玻璃板材》对基础物理性能(拉伸强度、断裂伸长率、简支梁无缺口冲击强度)进行测试与表征。制样中,冲击强度测试用样,工艺1、工艺2取居中含有金属或尼龙线束的区域,其余测试项目均取透明区域。制样尺寸按相应测试的国标要求进行。性能表征的结果统计见表1,可以明显看出,简支梁无缺口冲击强度指标(结合图10),工艺1中样品为110.3~134.1kj/m2,而工艺2、工艺3依次大幅度降低至51.8~64.4kj/m2与20.7~28.4kj/m2,说明金属线束的抗冲击能力显著高于同直径的尼龙,无线束的透明板最低。除了冲击性能以外,工艺1~3的其他基础物理性能均具有统计学意义上的一致性。
[0089]
表1.性能表征结果统计
[0090][0091]
备注:c冲击强度具体为简支梁无缺口冲击强度。
[0092]
本技术还提供一种金属内嵌pmma复合板材,采用如上实施例的金属内嵌pmma复合板材的制造方法制造得到。
[0093]
本技术的金属内嵌pmma复合板材的制造方法,包括以下步骤:在浇注模具中固定涂覆有界面缓释剂的金属线束;在浇注模具中浇注用于形成pmma基体的液相材料;聚合获得金属内嵌pmma复合板材。还涉及采用上述制造方法制造得到的金属内嵌pmma复合板材。本技术在金属线束的表面涂覆界面缓释剂,可以在液相材料聚合过程中缓慢改变金属线束和聚合产物之间的隔离状态直至形成力学咬合,保证金属线束的原有空间位置在聚合过程中基本不发生改变,避免液相材料聚合过程中的体积收缩与金属线束的体积变化不匹配、以及提前发生相界面咬合而导致复合板材弯曲的问题。
[0094]
上述实施例仅例示性说明本技术的原理及其功效,而非用于限制本技术。任何熟悉此技术的人士皆可在不违背本技术的精神及范畴下,对上述实施例进行修饰或改变。因此,举凡所属技术领域中具有通常知识者在未脱离本技术所揭示的精神与技术思想下所完成的一切等效修饰或改变,仍应由本技术的权利要求所涵盖。