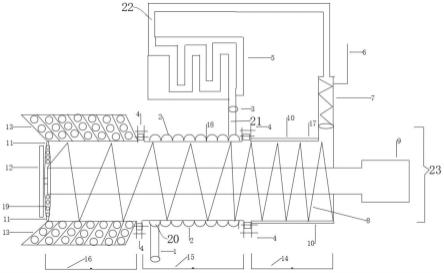
1.本发明属于高吸收性树脂制备领域,涉及一种连续化本体聚合高吸收性树脂制备方法。
背景技术:2.能耗双控是实现碳达峰的重要举措,实行目的在于建设环境友好型社会,创建绿色发展的经济环境,以更少的能源消耗来满足社会可持续性发展的需要。
3.目前高吸收性树脂制备方法主要有水溶液聚合工艺和反相悬浮聚合工艺,这两种工艺聚合前单体中都需引入大量的水,聚合后再把水全部烘干出来,造成高吸收性树脂工业增加值能耗强度高,很有必要创新生产工艺,大幅度降低工业增加值能耗强度,实现节能降耗的目标。
4.为了大幅度降低高吸收性树脂工业增加值能耗强度,同时满足高吸收性树脂技术指标要求,本发明人进行了大量实验和深入研究,创造性地发明了一种连续化本体聚合高吸收性树脂的制备方法。
5.综上所述,为解决现有技术上的不足,本发明设计了一种不仅能够大幅度降低高吸收性树脂制备过程中的能耗、还能同时满足高吸收性树脂的技术指标要求的连续化本体聚合高吸收性树脂制备方法。
技术实现要素:6.本发明为解决现有技术存在的问题,提供了一种连续化本体聚合高吸收性树脂制备方法中,通过该制备系统制备的高吸收性树脂不仅能够大幅度降低工业增加值能耗强度,完成节能降耗的任务,还能够同时满足高吸收性树脂技术指标的要求。
7.本发明的目的可通过以下技术方案来实现:
8.一种连续化本体聚合高吸收性树脂制备方法,其特征在于,包括:
9.步骤一:乙烯基单体(盐)、两官能团以上交联剂、分散剂、金属离子螯合剂配置成混合物a;
10.步骤二:混合物a经过柱塞泵打入聚合反应器进料预热排管中,从预热排管出来后,混合物a进入恒温加热器中加热,再进入静态混合器与引发剂进行混合,最终进入聚合反应器的内腔,内腔的中心为螺旋状推进器,混有引发剂的混合物a在快速搅拌和加热控温的条件下进行本体聚合反应;
11.步骤三:聚合物从聚合反应器的出口挤出后经旋转切刀切粒或切段,再进入熟化器中继续反应与冷却,得到聚合物b;
12.步骤四:聚合物b经过粉碎或研磨、筛分、表面处理得到最终的产品c。
13.作为本方案的进一步改进,步骤一中所述的乙烯基单体(盐)选自含有双键的羧酸(盐)基、磺酸(盐)基、磷酸(盐)基、羟基的至少一种。
14.作为本方案的进一步改进,步骤一中所述的两官能团以上交联剂选自聚多元醇二
缩水甘油醚、聚多元醇(二~四)丙烯酸酯、多元醇(二~四)丙烯酸酯、多元醇(二~四)烯丙基醚、聚多元醇(二~四)烯丙基醚、多元醇二缩水甘油醚的至少一种;
15.作为本方案的进一步改进,步骤二中所述的预热排管进口到出口混合物a 的温度升高范围为8℃~32℃,混合物a在恒温加热器出口的温度控制范围为 82℃~125℃。
16.作为本方案的进一步改进,步骤二中所述的聚合反应器由三段组成,三段之间用绝热垫片隔开。
17.作为本方案的进一步改进,聚合反应器的内腔的第一段为引发段、第二段为热交换段、第三段为强换热段。
18.作为本方案的进一步改进,物料在聚合反应器内腔中停留时间为32秒~150 秒。
19.作为本方案的进一步改进,聚合反应器的引发段、热交换段螺旋的螺距比为1:1.2~1:2.2,聚合反应器的引发段、强冷却段螺旋的螺距比为1:1.2~ 1:2.2。
20.作为本方案的进一步改进,步骤二中所述的熟化器为风冷网板链条循环式,物料在熟化器中的的停留时间控制为1分钟~6分钟,熟化器出口处物料的温度控制范围为70℃~30℃。
21.作为本方案的进一步改进,风冷网板上为排列圆孔,圆孔径为1.2~5.5mm,风冷网板的开孔率为22%~41%。
22.与现有技术相比,本发明结构设计合理,具备下述有益效果:
23.1)步骤2中,预热排管起到了聚合放热撤出和混合物a预热的两个作用,充分利用了聚合热,从预热排管出来后,混合物a进入恒温加热器中加热,再进入静态混合器与引发剂进行混合,最终进入聚合反应器的内腔,内腔的中心为螺旋状推进器,混有引发剂的混合物a在快速搅拌和加热控温的条件下进行本体聚合反应,聚合反应器后段有强换热用于控制本体聚合反应的最高温度,防止最高温度太高,引起聚合物分子量小和分布宽,以及高温引起的聚合物氧化与黄变,聚合物从聚合反应器的出口挤出后经旋转切刀切粒或切段,再进入熟化器中继续反应与冷却,得到聚合物b;
24.2)步骤二中所述的聚合反应器由三段组成,三段之间用绝热垫片隔开减少金属内腔三段之间热量的乱窜,内腔的第一段为引发段,有加热控温功能;第二段为热交换段,一部分聚合放热引起物料自身升温加速聚合,另一部分传递给外壁预热排管中的混合物a;第三段为强换热段,主要作用是控制本体聚合反应的最高温度在96℃~135℃,物料在聚合反应器内腔中停留时间为32秒~150 秒;
25.3)本发明提供的一种连续化本体聚合高吸收性树脂的制备方法,每吨高吸收性树脂产品具有明显的能耗低和二氧化碳排放少的优势,外观颜色、离心保水率和加压吸收率指标可以保持相当。不仅能够大幅度降低高吸收性树脂制备过程中的能耗、还能同时满足高吸收性树脂的技术指标要求。
附图说明
26.图1是本发明连续化本体聚合高吸收性树脂制备系统的结构示意图。
27.图2是本发明熟化器的结构示意图。
28.图3是本发明熟化器内部的结构示意图。
29.图中,
30.1-预热排管进口,2-预热排管,3-预热排管出口,4-绝热垫片,5-恒温加热器,6-引发剂加入,7-静态混合器,8-螺旋状推进器,9-电机,10-引发段加热控温,11-聚合反应器出口,12-旋转切刀,13-强冷却排管单元,14-引发段, 15-热交换段,16-强冷却段17-引发段物料温度监测装置,18-热交换段物料温度监测装置,19-聚合反应器出口物料温度监测装置,20-预热排管进口温度监测装置,21-预热排管出口温度监测装置,22-恒温加热器出口温度监测装置, 23-聚合反应器;
31.24-熟化器,241-熟化器入口,242-熟化器出口,243-冷却风,244-风冷网板,245-风冷网板圆孔,246-熟化器旋转圆盘。
具体实施方式
32.下面结合实施例及附图,对本发明的技术方案作进一步的阐述。
33.实施例与比较例产物性能测试方法如下:
34.(1)离心保水率
35.离心保水率(centrifuge retention capacity,简称“crc”)是指在一定时间内单位质量的高吸收性树脂在0.9%氯化钠盐水中自由溶胀后,用离心机甩去部分水分后的吸水保持倍率。
36.具体是指,用茶叶袋称取0.2000g高吸收性树脂,浸入0.9wt%氯化钠水溶液30分钟使其自由膨胀,之后用离心机(离心力为250g)甩去部分水分后的吸水保持倍率(单位;g/g)。离心保水率=(m离心后-m样-m空白)/m样。
37.(2)加压吸收率
38.加压吸收率(absorption under pressure,简称“aup”)是指单位质量的高吸收性树脂在一定时间、一定压力作用下的吸水倍率。具体是指,在0.7psi 的负重下,使吸水性树脂0.9000g在0.9wt%氯化钠水溶液中溶胀1小时后的吸水倍率(单位:g/g)。加压吸收率=(m吸水后-m吸水前)/m样。
39.本发明的一种连续化本体聚合高吸收性树脂制备系统的具体结构为:包括:
40.预热排管2,若干平行且连续设置的预热排管2,该预热排管2用于混合物 a的预热;
41.恒温加热器5,恒温加热器5与预热排管2连通,预热后的混合物a通过恒温加热器5进行控温;
42.静态混合器7,静态混合器7与恒温加热器5的出料口相连通,静态混合器 7的一侧设有引发剂加入口6;
43.聚合反应器23,聚合反应器23包括反应内腔,反应内腔内设有螺旋状推进器8,螺旋状推进器8的一端设有驱动装置,静态混合器7设置于靠近驱动装置的一端且与聚合反应器23连通;螺旋状推进器8的螺距由靠近驱动装置的一端至远离驱动装置的一端逐渐增大。
44.其中,聚合反应器23的反应内腔包括依次设置的引发段14、热交换段15、强冷却段16,引发段14的螺距为a、热交换段15的螺距为b、强冷却段16的螺距为c,满足数量关系:a<b<c。
45.更具体的为,聚合反应器23的内腔直径范围为305mm~865mm,包括依次设置的引发段14、热交换段15、强冷却段16,引发段14的长度范围为560mm~2500mm,螺距为a范围为
52mm~75mm、热交换段15的长度范围为600mm~2650mm,螺距为b范围为95mm~155mm、强冷却段16的长度范围为650mm~2750mm,,螺距为c范围为95mm~195mm,数值满足数量关系:a<b<c。
46.聚合反应器的引发段14、热交换段15螺旋的螺距比为1:1.2~1:2.2,聚合反应器的引发段14、强冷却段16螺旋的螺距比为1:1.2~1:2.2。聚合反应器23的反应内腔的引发段14、热交换段15、强冷却段16三段之间用绝热垫片隔开。聚合反应器23的末端设有聚合反应器出口11,聚合反应器出口11处设置有旋转切刀12,该旋转切刀用于将聚合物切粒或切段。
47.更具体的为,三段外筒使用法兰连接,法兰之间装有绝热垫片,起到防止三段之间热量乱窜,聚合反应器的内腔是连通的,中间为螺旋推进器,物料依靠螺旋推进器在内腔入口传送到出口。
48.聚合反应器出口11处还设有强冷却排管单元13。
49.更具体的为,强冷却排管单元13实现聚合反应器强冷却段的强冷却功能,由传热性能良好的紫铜材质制备而成,结构为矩阵式环形排管环绕而成,排管内部流通的是低温冷冻液从而实现强冷却功能。
50.在本发明的制备系统中,温控方面的具体设置为:引发段14设置有引发段加热控温10;引发段14处还设置有引发段物料温度监测装置17;热交换段设置有热交换段物料温度监测装置18;聚合反应器出口处设有聚合反应器出口物料温度监测装置19;预热排管进口处设有预热排管进口温度监测装置20;预热排管出口处设有预热排管出口温度监测装置21;恒温加热器出口处设有恒温加热器出口温度监测装置22。
51.更具体的,该引发段加热控温装置10为筒壁上设置有电加热组件。以上温度监测相当于温度检测点,显示温度数值,满足工艺条件各处温度和温度差值范围要求。
52.如图2所示,还包括熟化器24,熟化器24上设有熟化器入口241和熟化器出口242,熟化器24的内部设有熟化器旋转圆盘246和风冷网板244,在熟化器旋转圆盘246的驱动下,风冷网板244对聚合物进行冷却和传送。风冷网板 244上设置有通孔,该通孔为圆孔。所述圆孔的孔径为1.2~5.5mm。所述风冷网板244的开孔率为22%~41%。
53.由上述制备系统和配料釜采用连续化本体聚合方法,制备高吸收性树脂。
54.1)预热排管起到了聚合放热撤出和混合物a预热的两个作用,充分利用了聚合热,从预热排管出来后,混合物a进入恒温加热器中加热,再进入静态混合器与引发剂进行混合,最终进入聚合反应器的内腔,内腔的中心为螺旋状推进器,混有引发剂的混合物a在快速搅拌和加热控温的条件下进行本体聚合反应,聚合反应器后段设置有强换热用于控制本体聚合反应的最高温度,防止最高温度太高,引起聚合物分子量小和分布宽,以及高温引起的聚合物氧化与黄变,聚合物从聚合反应器的出口挤出后经旋转切刀切粒或切段,再进入熟化器中继续反应与冷却,得到聚合物b;
55.2)聚合反应器由三段组成,三段之间用绝热垫片隔开减少金属内腔三段之间热量的乱窜,三段之间热量的乱窜不利于各段的控温和能耗损失。聚合反应器第一段为引发段,有加热控温功能;聚合反应器第二段为热交换段,一部分聚合放热引起物料自身升温加速聚合,另一部分传递给外壁预热排管中的混合物a;聚合反应器第三段为强换热段,主要功能是控制本体聚合反应的最高温度为96℃~135℃,物料在聚合反应器内腔中停留时间为
32秒~150秒,聚合反应器的引发段、热交换段螺旋的螺距比为1:1.2~1:2.2,聚合反应器的引发段、强冷却段螺旋的螺距比为1:1.2~1:2.2,聚合反应器设计成三段是为了实现本发明自由基聚合的链引发,即初期要加热让引发剂引发形成自由基,中间为链增长阶段,部分散热来控制聚合反应的速率和强度,最后为链终止和链转移,强换热降温来控制聚合反应的终止。聚合反应器的引发段、热交换段、强冷却段螺距不同,是为了物料在聚合反应器各段的停留时间进行控制,螺旋推进器相同转速时,螺距短则物料停留时间长,螺距长则物料停留时间短,引发段螺距短,是因为自由基聚合链引发慢需要时间长的原因,热交换段和强冷却段螺距短,是因为自由基聚合链增长快和链终止快的原因;
56.3)熟化器为风冷网板链条循环式,物料在熟化器中的的停留时间控制为1 分钟~6分钟,熟化器出口处物料的温度控制范围为70℃~30℃,从而实现聚合反应的完全和冷却两个功能。风冷网板上为排列圆孔,圆孔径为1.2~5.5mm,风冷网板的开孔率(网板上所有开孔的面积之和
÷
网板的总面积)为22%~41%。圆孔径大小不能让物料从圆孔中漏出,又要保证冷风的穿透来冷却。风冷网板的开孔率平衡了冷风的穿透和风冷网板结构力学。
57.实施例1:
58.配料釜中加入300kg的丙烯酸钠和丙烯酸(丙烯酸钠占摩尔分数75%)、两官能团交联剂聚乙二醇(600)二丙烯酸酯0.9kg和分散剂气相法二氧化硅3kg,金属离子螯合剂乙二胺四乙酸二钠盐0.04kg,在配料釜中搅拌成混合物a,测量混合物a当时的温度为22℃,混合物a通过柱塞泵以102kg/h的量打入特制的聚合反应器预热排管中,从预热排管出口温度检测显示此时混合物a温度为 43℃,混合物a进入恒温加热器中加热到95℃,再进入静态混合器与引发剂过硫酸钠0.32kg/h进行混合后,进入聚合反应器内腔,聚合反应器内腔的最高温度显示为123℃,物料在内腔中的停留时间为96秒,从聚合反应器的出口出来经旋转切刀切粒,再进入熟化器2.1分钟后得到52℃的聚合物b,聚合物b 经过粉碎或研磨、筛分、表面处理得到最终的产品c。
59.对比例1
60.配料釜中加入300kg的丙烯酸钠和丙烯酸(丙烯酸钠占摩尔分数75%)、两官能团交联剂聚乙二醇(600)二丙烯酸酯0.9kg和分散剂气相法二氧化硅3kg,金属离子螯合剂乙二胺四乙酸二钠盐0.04kg,在配料釜中搅拌成混合物,测量混合物当时的温度为22℃,混合物a通过柱塞泵以102kg/h的量打入恒温加热器中加热到95℃,再进入静态混合器与引发剂过硫酸钠0.32kg/h进行混合后,进入一段式等螺距的螺旋推进器组成的聚合反应器停留时间控制为96秒,测量聚合反应器内物料的最高温度显示为152℃,从聚合反应器的出口出来经旋转切刀切粒(粒子颜色发黄,因聚合反应器内物料温较高,引起丙烯酸中带入的阻聚剂对羟基苯甲醚氧化变黄),再进入熟化器2.1分钟后得到102℃的黄色聚合物,聚合物经过粉碎或研磨、筛分、表面处理得到最终黄色产品。
61.对比例2
62.在配料釜中加入300kg的丙烯酸钠和丙烯酸(丙烯酸钠占摩尔分数75%)、 301.2kg的去离子水、n,n-亚甲基双丙烯酰胺0.9kg,开启配料釜的搅拌,控温到82℃
±
2℃,用泵以215kg/h的里输送到静态混合器中,同时添加1%过硫酸钠水溶液20.8kg,进入循环链条的硅胶反应器中进行聚合反应得到聚合凝胶,聚合凝胶经过造粒、烘干、粉碎或研磨、筛分、表面处理得到最终的产品。
63.实施例1、对比例1、对比例2得到的高吸收性树脂,详见下表1:
64.表1实施例1、对比例1、对比例2性能测试结果
[0065][0066]
由表1分析可见,本发明提供的一种连续化本体聚合高吸收性树脂的制备方法,每吨高吸收性树脂产品具有明显的能耗低和二氧化碳排放少的优势,外观颜色、离心保水率和加压吸收率指标可以保持相当。不仅能够大幅度降低高吸收性树脂制备过程中的能耗、还能同时满足高吸收性树脂的技术指标要求。
[0067]
本文中所描述的仅为本发明的优选实施方式,但本发明的保护范围并不局限于此。本发明所属领域的技术人员对所描述的具体实施例进行的修改或补充或采用类似的方式替换,均应涵盖于本发明的保护范围之内。