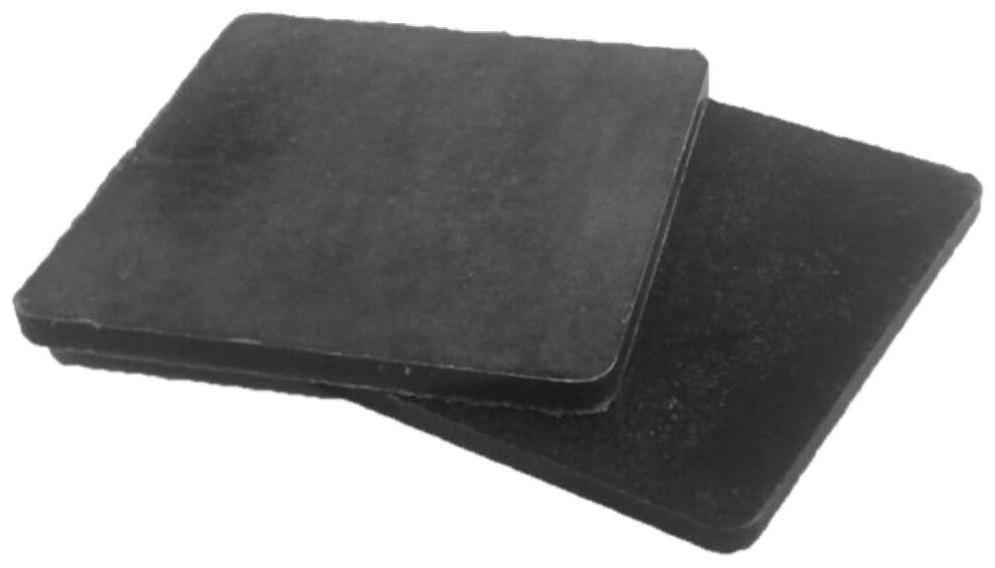
1.本发明属于人造板技术领域,具体涉及一种壳聚糖改性高强度抗菌木塑复合板的制备方法。
背景技术:2.木塑复合板一种主要由木材(木纤维素、植物纤维素)为基础材料与热塑性高分子材料(塑料)和加工助剂等,混合均匀后再经模具设备加热挤出成型而制成的高科技绿色环保新型装饰材料,兼有木材和塑料的性能与特征,是能替代木材和塑料的新型板材。传统木塑复合板的生产通常利用木纤维与塑料的自粘结,而这类木塑复合板在其贮存和使用过程中会导致膨胀、开裂或收缩变形。随着经济的发展和人们生活水平的提高,人们更注重板材的性能和品质。
3.若想从根本上解决木纤维与塑料自结合差的问题,最直接有效的方法就是在木塑复合板的制备中添加界面相容剂。近年来,科学家们尝试了化学或物理预处理等多种方法来提高木塑复合板的性能,然而目前这些方法工艺都很复杂的,不能有效地生产高性能木塑复合板。
技术实现要素:4.本部分的目的在于概述本发明的实施例的一些方面以及简要介绍一些较佳实施例。在本部分以及本技术的说明书摘要和发明名称中可能会做些简化或省略以避免使本部分、说明书摘要和发明名称的目的模糊,而这种简化或省略不能用于限制本发明的范围。
5.本发明其中一个方面,本发明提供一种壳聚糖改性高强度抗菌木塑复合板的制备方法,其由以下步骤组成,
6.1)原料预处理:将杨木废料粉碎得到杨木粉末,将所述杨木粉末浸入氢氧化钠和亚硫酸钠的混合溶液中,加热浸渍,冲洗,取出所述杨木粉末,蒸煮,烘干;将丙烯腈-丁二烯-苯乙烯塑料及壳聚糖分别粉碎;
7.2)将步骤1)处理后的杨木粉末、丙烯腈-丁二烯-苯乙烯塑料粉末、壳聚糖粉末均匀混合得到混合粉末;
8.3)将步骤2)得到的混合粉末加入到热压机预压,得到板坯;
9.4)将步骤3)得到的板坯热压成板,得到高强度抗菌木塑复合板。
10.作为本发明所述的壳聚糖改性高强度抗菌木塑复合板的制备方法的一种优选方案:步骤1)中,所述将杨木废料粉碎得到杨木粉末,其中,所述杨木粉末的粒径为60-80目。
11.作为本发明所述的壳聚糖改性高强度抗菌木塑复合板的制备方法的一种优选方案:步骤1)中,所述将杨木粉末浸入氢氧化钠和亚硫酸钠的混合溶液中,其中,氢氧化钠在混合溶液中的质量百分比为1~1.5%,所述亚硫酸钠在混合溶液中的质量百分比为0.5~0.8%;所述杨木粉末与混合溶液的料液比为1:20~40。
12.作为本发明所述的壳聚糖改性高强度抗菌木塑复合板的制备方法的一种优选方
案:步骤1)中,所述加热浸渍,为在96℃下浸渍4h。
13.作为本发明所述的壳聚糖改性高强度抗菌木塑复合板的制备方法的一种优选方案:步骤1)中,所述蒸煮,为在110~120℃蒸煮35~40min;所述烘干,为烘至水分含量为3~5wt%
14.作为本发明所述的壳聚糖改性高强度抗菌木塑复合板的制备方法的一种优选方案:步骤2)中,杨木粉末、丙烯腈-丁二烯-苯乙烯塑料粉末、壳聚糖粉末的质量比为8:2:0.5~2.0。
15.作为本发明所述的壳聚糖改性高强度抗菌木塑复合板的制备方法的一种优选方案:步骤2)中,杨木粉末、丙烯腈-丁二烯-苯乙烯塑料粉末、壳聚糖粉末的质量比为8:2:1~1.5。
16.作为本发明所述的壳聚糖改性高强度抗菌木塑复合板的制备方法的一种优选方案:步骤3)中,所述预压,温度100~110℃,压力为25~30mpa,预压时间为8~10min。
17.作为本发明所述的壳聚糖改性高强度抗菌木塑复合板的制备方法的一种优选方案:步骤4)中,所述热压成板,温度170~180℃,压力为45~55mpa,热压时间为65~75min。
18.作为本发明所述的壳聚糖改性高强度抗菌木塑复合板的制备方法的一种优选方案:所述丙烯腈-丁二烯-苯乙烯塑料粉末的粒径为140~160目;所述壳聚糖粉末的粒径为100~120目。
19.本发明的有益效果:本发明使用氢氧化钠和亚硫酸钠的混合溶液处理杨木粉末中的纤维素,加快了半纤维素的分解,将其刻蚀为微纤维,进而由于壳聚糖的加入,促进了木纤维与塑料之间的结合,有利于板材热压成型,提高了木塑复合板的强度。由于壳聚糖的引入,制备的木塑复合板具有优异的抗菌性能。本发明制备的木塑复合板不含甲醛等对人体有害物质,也不加入粘结剂等。本发明将杨木废渣变废为宝,提高了资源的利用率,解决了废弃塑料的处理问题,对于环境保护具有重要意义。
20.本发明制得的木塑复合板拉伸强度、抗弯强度、弹性模量、吸水率和吸水厚度膨胀率等性能数据的测试,制得的木塑复合板的性能数据均比较优异,满足现在市场上的加工要求。
附图说明
21.为了更清楚地说明本发明实施例的技术方案,下面将对实施例描述中所需要使用的附图作简单地介绍,显而易见地,下面描述中的附图仅仅是本发明的一些实施例,对于本领域普通技术人员来讲,在不付出创造性劳动性的前提下,还可以根据这些附图获得其它的附图。其中:
22.图1为实施例2制备的木塑复合板的照片。
23.图2为实施例2制备的木塑复合板的显微图片。
具体实施方式
24.为使本发明的上述目的、特征和优点能够更加明显易懂,下面结合具体实施例对本发明的具体实施方式做详细的说明。
25.在下面的描述中阐述了很多具体细节以便于充分理解本发明,但是本发明还可以
采用其他不同于在此描述的其它方式来实施,本领域技术人员可以在不违背本发明内涵的情况下做类似推广,因此本发明不受下面公开的具体实施例的限制。
26.实施例1:
27.1)原料预处理:分别称取15g杨木废料粉碎至60目得到杨木粉末;将杨木粉末浸入400ml氢氧化钠和亚硫酸钠的混合溶液中,在96℃下浸渍4h,其中,氢氧化钠在混合溶液中质量百分比为1%,亚硫酸钠在混合溶液中质量百分比为0.6%,浸渍完成后,用去离子水冲洗10min,冲洗完成后,取出杨木粉末在120℃蒸煮35min,烘干至水分为5wt%;将丙烯腈-丁二烯-苯乙烯塑料粉碎至140目,壳聚糖粉碎至100目;
28.2)将8g步骤1)处理后的杨木粉末,2g丙烯腈-丁二烯-苯乙烯塑料粉末及0.5g壳聚糖粉末经搅拌机均匀混合备用;
29.3)将步骤2)得到的混合粉末加入到热压机预压,温度100℃,压力25mpa,预压10min,得到板坯;
30.4)将步骤3)得到的板坯,传输到热压机进行热压成板,温度180℃,压力45mpa,热压70min,即得到高强度抗菌木塑复合板。
31.实施例2:
32.1)原料预处理:分别称取15g杨木废料粉碎至60目得到杨木粉末;将杨木粉末浸入400ml氢氧化钠和亚硫酸钠的混合溶液中,在96℃下浸渍4h,其中,氢氧化钠在混合溶液中质量百分比为1%,亚硫酸钠在混合溶液中质量百分比为0.6%,浸渍完成后,用去离子水冲洗10min,冲洗完成后,取出杨木粉末在120℃蒸煮35min,烘干至水分为5%;将丙烯腈-丁二烯-苯乙烯塑料粉碎至140目,壳聚糖粉碎至100目;
33.2)将8g步骤1)处理后的杨木粉末,2g丙烯腈-丁二烯-苯乙烯塑料粉末及1g壳聚糖粉末经搅拌机均匀混合备用;
34.3)将步骤2)得到的混合粉末加入到热压机预压,温度100℃,压力25mpa,预压10min,得到板坯;
35.4)将步骤3)得到的板坯,传输到热压机进行热压成板,温度180℃,压力45mpa,热压70min,即得到高强度抗菌木塑复合板。
36.实施例3:
37.1)原料预处理:分别称取15g杨木废料粉碎至60目得到杨木粉末;将杨木粉末浸入400ml氢氧化钠和亚硫酸钠的混合溶液中,在96℃下浸渍4h,其中,氢氧化钠在混合溶液中质量百分比为1%,亚硫酸钠在混合溶液中质量百分比为0.6%,浸渍完成后,用去离子水冲洗10min,冲洗完成后,取出杨木粉末在120℃蒸煮35min,烘干至水分为5%;将丙烯腈-丁二烯-苯乙烯塑料粉碎至140目,壳聚糖粉碎至100目;
38.2)将8g步骤1)处理后的杨木粉末,2g丙烯腈-丁二烯-苯乙烯塑料粉末及1.5g壳聚糖粉末经搅拌机均匀混合备用;
39.3)将步骤2)得到的混合粉末加入到热压机预压,温度100℃,压力25mpa,预压10min,得到板坯;
40.4)将步骤3)得到的板坯,传输到热压机进行热压成板,温度180℃,压力45mpa,热压70min,即得到高强度抗菌木塑复合板。
41.实施例4:
42.1)原料预处理:分别称取15g杨木废料粉碎至60目得到杨木粉末;将杨木粉末浸入400ml氢氧化钠和亚硫酸钠的混合溶液中,在96℃下浸渍4h,其中,氢氧化钠在混合溶液中质量百分比为1%,亚硫酸钠在混合溶液中质量百分比为0.6%,浸渍完成后,用去离子水冲洗10min,冲洗完成后,取出杨木粉末在120℃蒸煮35min,烘干至水分为5%;将丙烯腈-丁二烯-苯乙烯塑料粉碎至140目,壳聚糖粉碎至100目;
43.2)将8g步骤1)处理后的杨木粉末,2g丙烯腈-丁二烯-苯乙烯塑料粉末及2g壳聚糖粉末经搅拌机均匀混合备用;
44.3)将步骤2)得到的混合粉末加入到热压机预压,温度100℃,压力25mpa,预压10min,得到板坯;
45.4)将步骤3)得到的板坯,传输到热压机进行热压成板,温度180℃,压力45mpa,热压70min,即得到高强度抗菌木塑复合板。
46.将实施例1至实施例4制得的高强度抗菌木塑复合板按照标准,分别进行拉伸强度、抗弯强度、弹性模量等性能测试,实验结果如表1所示。
47.表1
[0048] 实施例1实施例2实施例3实施例4密度(g/cm3)1.381.311.351.34拉伸强度(mpa)61.499.498.371.4抗弯强度(mpa)72.979.659.859.1弹性模量(mpa)1530489045102240吸水率(%)3.151.863.043.99吸水厚度膨胀率(%)4.152.212.642.91
[0049]
由表1可知,当杨木粉末、丙烯腈-丁二烯-苯乙烯塑料粉末、壳聚糖粉末三者的质量比为8:2:1时,制备的高强度抗菌木塑复合板拉伸强度、抗弯强度、弹性模量等性能最佳。这是因为木塑复合板热成型过程中壳聚糖的加入使得木纤维和塑料结合紧密,增强了木塑复合板的致密性,且添加量达到上述比例的效果最佳。加入过多的壳聚糖会导致热压后板材松散,机械性能下降,因此壳聚糖添加量需要控制在上述范围。
[0050]
本发明使用氢氧化钠和亚硫酸钠的混合溶液处理杨木粉末中的纤维素,加快了半纤维素的分解,将其刻蚀为微纤维,进而由于壳聚糖的加入,促进了木纤维与塑料之间的结合,有利于板材热压成型,提高了木塑复合板的强度。由于壳聚糖的引入,制备的木塑复合板具有优异的抗菌性能。本发明制备的木塑复合板不含甲醛等对人体有害物质,也不加入粘结剂等。本发明将杨木废渣变废为宝,提高了资源的利用率,解决了废弃塑料的处理问题,对于环境保护具有重要意义。制备的高强度抗菌木塑复合板可以用于食品包装、无菌车间和医疗手术室等。
[0051]
本发明制得的木塑复合板拉伸强度、抗弯强度、弹性模量、吸水率和吸水厚度膨胀率等性能数据的测试,制得的木塑复合板的性能数据均比较优异,满足现在市场上的加工要求。
[0052]
研究例1:
[0053]
为研究氢氧化钠和亚硫酸钠的配比对于制得的木塑复合板的性能影响,相比于实施例2,将氢氧化钠和亚硫酸钠在混合溶液中的质量百分比分别调整为:0.8%和0.3%;
0.9%和0.4%;1.6%和0.9%;1.8%和1.2%;
[0054]
制备的木塑复合板的拉伸强度分别为61.2mpa,72.5mpa,70.6mpa,63.5mpa;抗弯强度分别为63.5mpa,70.6mpa,64.8mpa,59.5mpa。结论:氢氧化钠和亚硫酸钠的浓度和配比对于制得的木塑复合板的机械性能产生明显影响。
[0055]
研究例2:
[0056]
1)原料预处理:分别称取15g杨木废料粉碎至60目得到杨木粉末;将杨木粉末浸入400ml氢氧化钠溶液中,在96℃下浸渍4h,其中,氢氧化钠在混合溶液中质量百分比为1%,浸渍完成后,用去离子水冲洗10min,冲洗完成后,取出杨木粉末在120℃蒸煮35min,烘干至水分为5%;;将丙烯腈-丁二烯-苯乙烯塑料粉碎至140目,壳聚糖粉碎至100目;
[0057]
2)将8g步骤1)处理后的杨木粉末,2g丙烯腈-丁二烯-苯乙烯塑料粉末及1g壳聚糖粉末经搅拌机均匀混合备用;
[0058]
3)将步骤2)得到的混合粉末加入到热压机预压,温度100℃,压力25mpa,预压10min,得到板坯;
[0059]
4)将步骤3)得到的板坯,传输到热压机进行热压成板,温度180℃,压力45mpa,热压70min,即得到高强度抗菌木塑复合板。
[0060]
制备的木塑复合板拉伸强度为55.6mpa;抗弯强度分别为51.7mpa。仅用氢氧化钠溶液处理,制备的木塑复合板机械强度明显差于氢氧化钠和亚硫酸钠的混合处理。
[0061]
研究例3:
[0062]
1)原料预处理:分别称取15g杨木废料粉碎至60目得到杨木粉末;将杨木粉末浸入400ml氢氧化钠和亚硫酸钠的混合溶液中,在96℃下浸渍4h,其中,氢氧化钠在混合溶液中质量百分比为1%,亚硫酸钠在混合溶液中质量百分比为0.6%,浸渍完成后,用去离子水冲洗10min,冲洗完成后,取出杨木粉末在120℃蒸煮35min,烘干至水分为5%;将丙烯腈-丁二烯-苯乙烯塑料粉碎至140目,壳聚糖粉碎至100目;
[0063]
2)将8g步骤1)处理后的杨木粉末,2g丙烯腈-丁二烯-苯乙烯塑料粉末及1g壳聚糖粉末经搅拌机均匀混合备用;
[0064]
3)将步骤2)得到的混合粉末加入到热压机热压,温度160℃,压力30mpa,预压70min,得到木塑复合板。
[0065]
制备的木塑复合板拉伸强度为76.5mpa;抗弯强度分别为60.8mpa。采用一步热压成型的方法制备的木塑复合板的机械性能差于实施例2分步热压。
[0066]
研究例4:
[0067]
1)原料预处理:分别称取15g杨木废料粉碎至60目得到杨木粉末;将杨木粉末浸入400ml氢氧化钠和亚硫酸钠的混合溶液中,在96℃下浸渍4h,其中,氢氧化钠在混合溶液中质量百分比为1%,亚硫酸钠在混合溶液中质量百分比为0.6%,浸渍完成后,用去离子水冲洗10min,冲洗完成后,取出杨木粉末在120℃蒸煮35min,烘干至水分为5%;将丙烯腈-丁二烯-苯乙烯塑料粉碎至140目,壳聚糖粉碎至100目;
[0068]
2)将8g步骤1)处理后的杨木粉末,2g丙烯腈-丁二烯-苯乙烯塑料粉末及1g壳聚糖粉末经搅拌机均匀混合备用;
[0069]
3)将步骤2)得到的混合粉末加入到热压机热压,温度180℃,压力40mpa,预压70min,得到木塑复合板。
[0070]
制备的木塑复合板拉伸强度为81.7mpa;抗弯强度分别为68.5mpa。
[0071]
应说明的是,以上实施例仅用以说明本发明的技术方案而非限制,尽管参照较佳实施例对本发明进行了详细说明,本领域的普通技术人员应当理解,可以对本发明的技术方案进行修改或者等同替换,而不脱离本发明技术方案的精神和范围,其均应涵盖在本发明的权利要求范围当中。