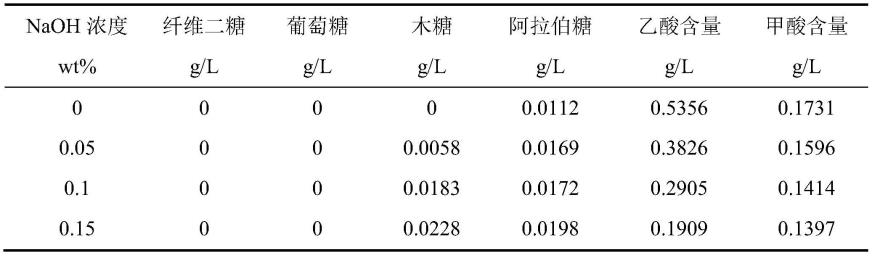
1.本发明属于纤维素基气凝胶多孔材料制备技术领域,具体为一种木质纤维全组分超疏水气凝胶材料的制备方法。
背景技术:2.近年来,石油化工行业生产和运输中的有机化学品泄漏和漏油事故对生态环境和人类健康构成了巨大的威胁。在众多方法中,物理吸附法在从油/水混合物中回收油类和有机溶剂方面引起了广泛关注。其中,无机矿物、有机合成材料和天然有机产品作为吸油材料已被研究。一些无机矿物,如沸石和活性炭,被用来沉降浮油,但由于其浮力小,吸附能力低,在水环境中并不理想。由聚乙烯和聚氨酯制备的有机合成材料是最广泛使用的,但由于它们的非生物降解性,它们对环境影响不容忽视。
3.最近,天然聚合物在材料应用中得到了广泛的应用。天然聚合物不仅减少环境污染,而且也表现出优异的性能。此外,这些聚合物可用于解决许多材料安全问题。特别是天然植物多糖,如纤维素,可作为制备高质量气凝胶的原料。用纤维素制备气凝胶一般可分为三个步骤:纤维素溶解、再生以及水凝胶转化为气凝胶。由于木质素的存在以及紧密排列的分子结构和较强的分子内和分子间氢键,木质纤维素很难在常规溶剂中溶解。因此,在大多数关于可再生气凝胶材料的报道中,纤维素、半纤维素或木质素首先通过繁琐而昂贵的化学处理从木质纤维素中分离出来,然后单独用于合成,这也会导致环境污染。因此,更理想的方法是直接从木质纤维素制备气凝胶,而不是纤维素或任何其他单一成分。
技术实现要素:4.本发明的目的是提供一种木质纤维全组分超疏水气凝胶材料的制备方法。本发明首先使用碱溶液对木质纤维素进行去乙酰化处理,然后使用无机熔融盐水合物溶解木质纤维素得到木质纤维全组分水凝胶;随后通过透析、溶剂交换和冷冻干燥得到木质纤维全组分气凝胶;最后使用改性剂对木质纤维全组分气凝胶进行疏水改性得到木质纤维全组分超疏水气凝胶。
5.为了实现上述目的,本发明的技术方案如下:
6.一种木质纤维全组分超疏水气凝胶材料的制备方法,所述方法包括以下步骤:
7.步骤一:将木质纤维素加入碱溶液中,在50~80℃下反应0.5~2h,随后过滤,洗涤至ph值为7,干燥,得到碱处理后的木质纤维素;
8.步骤二:将步骤一得到的碱处理后的木质纤维素和无机熔融盐水合物在135~145℃和磁力搅拌下反应0.5~1h,倒入模具中得到木质纤维全组分水凝胶,随后用去离子水透析去除无机熔融盐水合物,经溶剂交换后在-40~-50℃下冷冻干燥24h,得到木质纤维全组分气凝胶;
9.步骤三:将步骤二得到的木质纤维全组分气凝胶和改性剂加入到反应釜中,在110℃下反应3h,随后真空干燥12h,得到木质纤维全组分超疏水气凝胶。
10.优选地,所述步骤一中碱溶液为氢氧化钠溶液、氢氧化钾溶液、氢氧化钙溶液、氢氧化钡溶液中的一种。
11.优选地,所述步骤一中碱溶液的浓度为0.2~1wt%;所述木质纤维素与碱溶液的重量比为1:100。
12.优选地,所述步骤一中木质纤维素为木材、竹子、芦苇、稻草中的一种。
13.优选地,所述步骤二中还包括碱处理后的木质纤维素的预处理步骤,所述预处理步骤为:将碱处理后的木质纤维素粉碎、过60~100目筛。
14.优选地,所述碱处理后的木质纤维素与无机熔融盐水合物的质量比为1:12.5。
15.优选地,所述步骤二中无机熔融盐水合物为libr
·
3h2o。
16.优选地,所述步骤二中溶剂交换是先采用乙醇交换木质纤维全组分水凝胶中的水,再用叔丁醇交换乙醇。
17.优选地,所述步骤三中改性剂为甲基三乙氧基硅烷、十六烷基三甲氧基硅烷、十八烷基三氯硅烷中的一种。
18.优选地,所述步骤三中木质纤维全组分气凝胶与改性剂的质量比为1:0.5~2。
19.本发明的有益效果为:
20.(1)本发明方法适用于从各种原材料提取制备的不同形貌的木质纤维素,易于大规模推广。
21.(2)本发明提供的木质纤维全组分超疏水气凝胶材料的制备方法,以生物基材料为制备原料,得到了木质纤维全组分超疏水气凝胶,充分利用了植物纤维原料的三大组分,并且具有环境友好性。
22.(3)本发明方法制得的气凝胶具有高比表面积、高孔隙率、生物可降解性及超疏水性能。
附图说明
23.图1为实施例2中未经改性木质纤维全组分超疏水气凝胶的接触角测试图;
24.图2为实施例2中甲基三乙氧基硅烷改性木质纤维全组分超疏水气凝胶的接触角测试图;
25.图3为实施例2中十六烷基三甲氧基硅烷改性木质纤维全组分超疏水气凝胶的接触角测试图;
26.图4为实施例2中十八烷基三氯硅烷改性木质纤维全组分超疏水气凝胶的接触角测试图。
具体实施方式
27.下面结合具体实施例对本发明做进一步描述,但本发明不局限于以下实施例。
28.下述杨木的原产地为中国,质量均以绝干计。
29.实施例1:确定最优碱处理用量
30.(1)将过60目筛后的20g绝干杨木粉分别加入到2l不同浓度的碱溶液中,在60℃下磁力搅拌1h,反应结束后,过滤,用去离子水洗涤至ph为7,干燥后得到碱处理后的木质纤维素;
31.(2)将步骤(1)得到的碱处理后的木质纤维素在145℃下水解保温30min,取上清液用高效液相离子色谱对乙酸进行定量,以便检测碱处理的效果,实验结果见表1;
32.(3)将步骤(1)得到的碱处理后的木质纤维素和25g libr
·
3h2o加入到耐压瓶中,在145℃和磁力搅拌下反应0.5h后,倒入模具中得到木质纤维全组分水凝胶,再用去离子水透析去除无机熔融盐水合物,先采用乙醇交换木质纤维全组分水凝胶中的水,再用叔丁醇交换乙醇,随后在-50℃下冷冻干燥24h去除叔丁醇,得到木质纤维全组分气凝胶;木质纤维全组分气凝胶的性能见表2。
33.本实施例的碱溶液为naoh溶液。
34.本实施例的naoh溶液浓度为0.05wt%、0.1wt%、0.15wt%、0.2wt%、0.4wt%、0.6wt%、0.8wt%、1.0wt%。
35.本实施例的碱处理后的木质纤维素经过粉碎并且选取60~100目的部分。
36.表1naoh处理浓度对水解液中物质含量的影响
[0037][0038][0039]
由表1得,随着naoh浓度增大,乙酸含量逐渐下降,但是后续得到的木质纤维全组分气凝胶性能逐渐变差(见表2)。
[0040]
表2naoh处理浓度对木质纤维全组分气凝胶的性能
[0041][0042]
注:naoh处理浓度低于0.2wt%时,无法形成木质纤维全组分水凝胶。
[0043]
由表2得在naoh浓度为0.2wt%时,木质纤维全组分气凝胶的bet比表面积与孔容最大,有利于下一步的疏水改性实验以及油水分离实验。
[0044]
综合考虑乙酸含量和木质纤维全组分气凝胶性能,naoh处理浓度为0.2wt%是最优碱处理用量。
[0045]
实施例2:确定最优改性剂
[0046]
步骤一:将过60目筛后的20g绝干杨木粉加入到2l浓度为0.2wt%的naoh溶液中,在60℃下磁力搅拌1h,反应结束后,过滤,用去离子水洗涤至ph为7,干燥后得到碱处理后的木质纤维素;
[0047]
步骤二:将步骤一得到的碱处理后的木质纤维素粉碎、过60~100目筛,随后和25g libr
·
3h2o加入到耐压瓶中,在135℃和磁力搅拌下反应1h后,倒入模具中得到木质纤维全组分水凝胶,再用去离子水透析去除无机熔融盐水合物,先采用乙醇交换木质纤维全组分水凝胶中的水,再用叔丁醇交换乙醇,随后在-50℃下冷冻干燥24h后得到木质纤维全组分气凝胶;
[0048]
步骤三:将木质纤维全组分气凝胶和改性剂加入到反应釜中,在110℃下反应3h,真空干燥12h得到木质纤维全组分超疏水气凝胶。
[0049]
本实施例的改性剂为甲基三乙氧基硅烷、十六烷基三甲氧基硅烷、十八烷基三氯硅烷中的一种,木质纤维全组分气凝胶与改性剂的质量比为1:0.5。
[0050]
用不同的改性剂制备木质纤维全组分疏水气凝胶,得到的木质纤维全组分疏水气凝胶的接触角测试结果见表3。
[0051]
表3改性后木质纤维全组分气凝胶的接触角
[0052][0053]
由表3得,在木质纤维全组分气凝胶与改性剂的质量比为1:0.5的情况下,十六烷
基三甲氧基硅烷的改性效果最佳,可达166
°
,即木质纤维全组分气凝胶已拥有超疏水效果。