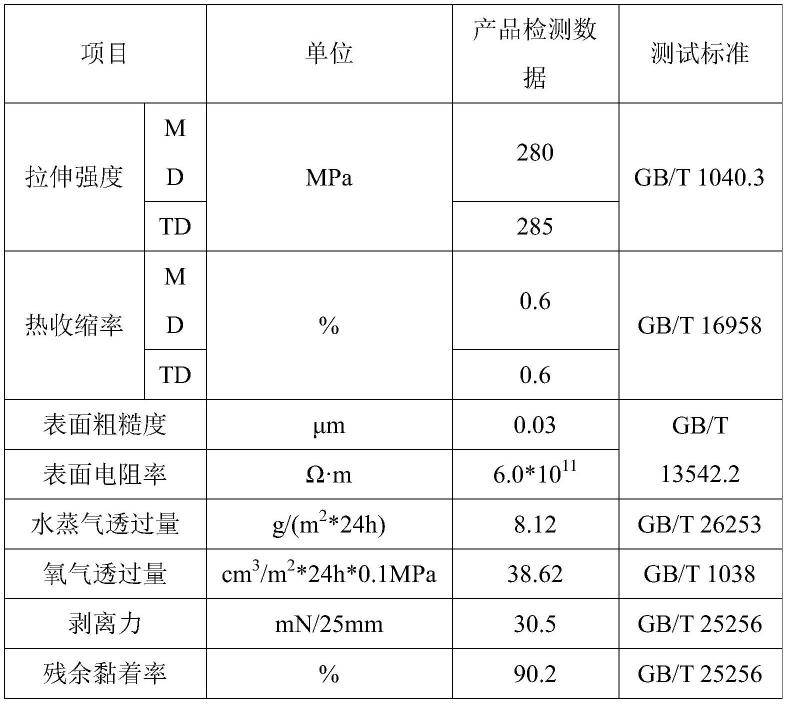
1.本发明涉及薄膜技术领域,具体涉及一种双向拉伸聚酯薄膜及其制备方法。
背景技术:2.bopet离型膜广泛应用于新型显示、集成电路、汽车建筑窗膜、电子电器、胶粘制品、激光防伪、反光材料等领域产品的表面离型保护,应用领域广阔。bopet离型膜根据加工工艺及应用领域不同,对基材薄膜的品质要求也不同,薄膜品质的高低主要取决于薄膜表面性能、光学性能、热稳定性、阻隔性能等。
3.目前市场上普通bopet薄膜需要进行2遍涂布,首先涂布一层抗静电层,然后涂布一层离型剂,工艺较为繁琐,溶剂型涂布液有一定的vocs排放,存在环境污染问题;且离型层涂布不均匀;薄膜纵横向热平衡性差,薄膜受热边部翘曲,影响保护效果;且水氧阻隔性能差;存在较为严重的硅转移,残余黏着率低。
技术实现要素:4.为避免上述现有技术所存在的不足之处,本发明的目的在于提供一种本征抗静电,并经过水性硅基离型在线涂布的双向拉伸聚酯薄膜及其制备方法,避免了离线涂布的vocs问题和残余接着率低的问题。
5.一种双向拉伸聚酯薄膜,该薄膜是由外表层、次表层、芯层和内表层组成的四层结构。其特征在于:
6.所述外表层是硅基离型涂层;
7.所述次表层由以下组分按重量份构成:聚酯抗粘连母料3~10份、聚酯抗静电母料3~10份、附着力增强改性聚酯母料5~30份、聚对苯二甲酸乙二醇酯50~89份;
8.所述芯层是由以下组分按重量份构成:聚萘二甲酸乙二醇酯母料20~40份,聚对苯二甲酸乙二醇酯60~80份;
9.所述内表层是由以下组分按重量份构成:聚酯抗粘连母料3~10份、聚酯抗静电母料3~10份,聚对苯二甲酸乙二醇酯母料80~94份。
10.进一步方案,所述外表层的离型剂涂布干重为5~30g/m2,所述次表层厚度为0.5~5μm,所述内表层厚度为0.8~8μm。
11.进一步方案,所述聚酯抗粘连母料是由组分一、组分二两种组分按2:1混合而成。组分一质量分数95%对苯二甲酸乙二醇酯和质量分数5%、粒径分布为0.5~1.0μm、平均粒径0.8μm多孔球形二氧化硅,经混合、双螺杆挤出机熔融挤出、切粒;组分二为质量分数95%对苯二甲酸乙二醇酯和质量分数5%、粒径分布为0.3~0.8μm、平均粒径0.5μm无定型二氧化硅,经混合、双螺杆挤出机熔融挤出、切粒。
12.进一步方案,所述聚酯抗静电母料为质量分数10%~30%的聚噻吩、10%~30%的聚吡咯、40~80%聚对苯二甲酸乙二醇酯,经混合、双螺杆挤出机熔融挤出、切粒。
13.进一步方案,所述附着力增强改性聚酯母料为质量分数50%~99%马来酸酐改性
支化聚酯、1%~50%的对苯二甲酸乙二醇酯经混合、双螺杆挤出机熔融挤出、切粒。马来酸酐改性支化聚酯制备过程为:在装有惰性气体的反应釜中,加入60%~80%超支化聚酯和10%~40%的n,n-二甲基甲酰胺,缓慢升温至80~85℃,支化聚酯完全溶解后,加入1~5%的n,n,n-三乙基乙铵溴化物,充分搅拌混合,加入10%~60%的马来酸酐,充分反应后,经水洗、干燥、粉碎。
14.本发明的另一个目的是提供上述双向拉伸聚酯薄膜薄膜的制备方法,其步骤如下:
15.(1)按配比,将芯层材料输送至流化床干燥结晶,以130~150℃干燥4~8小时,干燥后输送至单螺杆主挤出机中加热熔融,并经8~20μm碟片式过滤器,形成芯层熔体;
16.将次表层和内表层的组分按照配比,分别加入两台双螺杆挤出机中经熔融过滤、抽真空去除水分、低聚物等杂质后,形成次表层熔体和内表层熔体;
17.(2)将次表层、芯层和内表层熔体依序加入三层结构模头中汇合挤出得膜片,利用静电吸附将该膜片贴附到激冷辊上急冷形成铸片,贴附电压为8.0~12.5kv,铸片冷却定型温度为10~40℃;
18.(3)将铸片进行经过纵向拉伸为厚片,其预热温度为70~130℃、拉伸温度为105~140℃、拉伸倍率为3.0~4.2倍,纵拉拉伸辊表面粗糙度ra为0.05~0.12μm;
19.(4)将纵拉后的厚片进行电晕处理,处理功率为8w,通过在线涂布机涂布硅基离型层;
20.(5)将涂布后的厚片进行横向拉伸,其预热温度为100~110℃、拉伸温度为120~130℃、定型温度为235~255℃,拉伸倍率为3.0~4.2。
21.(6)将横拉后的薄膜进行牵引冷却、测厚、瑕疵检测,收卷成薄膜母卷。
22.本发明制备的双向拉伸聚酯薄膜能用于新型显示、集成电路、汽车建筑窗膜、电子电器用膜、胶粘制品、激光防伪、反光材料等产品的表面保护,表面抗粘连粒子分布均匀,离型层涂布不均匀,离型力稳定,残余接着率高,耐热性好,尺寸稳定性良好,受热后纵横向收缩均匀,水氧阻隔性能优异。
23.本发明产品配方中双组份小粒径抗粘连母料的适量添加,可有效控制薄膜摩擦系数和表面粗糙度,使得表面粗糙度均一、稳定,离型层涂布均匀,大大改善了离型力的稳定性,并使用双螺杆挤出机充分混合挤出,避免了聚酯聚合过程中添加小粒径母料,因母料密度小,悬浮在聚合反应釜上层,造成团聚的问题。本发明产品配方中聚酯抗静电母料的添加,可在薄膜表面形成网状导电层,大幅降低薄膜表面电阻,使得薄膜无需涂布抗静电涂层。本发明产品配方中附着力增强改性聚酯母料,可大幅提高聚酯薄膜次表层极性基团的分布,提升外表层离型涂布液与薄膜次表层之间的粘结强度和涂布牢度,避免在使用贴合的过程中,离型涂布液中的硅基成分转移到被保护产品上,薄膜残余黏着率高。芯层聚萘二甲酸乙二醇酯的适量添加,可有效提升薄膜耐温性能。配方和加工条件的优化,使得薄膜纵横向收缩率均衡。
附图说明
24.图1为双向拉伸聚酯薄膜的横截面结构示意图。
具体实施方式
25.实施例1:
26.a、制备芯层熔体:将2吨聚萘二甲酸乙二醇酯,8吨聚对苯二甲酸乙二醇酯,经过配比输送至流化床,以135℃干燥7小时,干燥后输送至单螺杆主挤出机中加热熔融,并经15μm碟片式过滤器,形成芯层熔体,挤出机、过滤器设定温度在280℃;
27.制备次表层熔体:30千克聚酯抗粘连母料,30千克聚酯抗静电母料,50千克附着力增强改性聚酯母料,890千克聚对苯二甲酸乙二醇酯,配比后,加入一台双螺杆挤出机中经熔融、抽真空处理除水分杂质后,并过滤形成次表层熔体,挤出机、过滤器设定温度在280℃;
28.制备内表层熔体:30千克聚酯抗粘连母料,30千克聚酯抗静电母料,940千克聚对苯二甲酸乙二醇酯,配比后,加入另一台双螺杆挤出机中经熔融、抽真空处理除水分杂质后,并过滤形成外表层熔体,挤出机、过滤器设定温度在280℃;
29.将次表层、芯层和内表层熔体依序加入三层结构模头中汇合挤出得膜片,利用静电吸附将该膜片贴附到激冷辊上急冷形成铸片,贴附电压为10kv,铸片冷却定型温度为29℃;
30.b、将铸片进行经过纵向拉伸为厚片,其预热温度为95℃、拉伸温度为112℃、拉伸倍率为3.8倍,纵拉拉伸辊表面粗糙度ra为0.07μm;
31.c、将纵拉后的厚片进行电晕处理,处理功率为8kw,通过在线涂布机涂布硅基离型层,涂布干重为5g/m2;
32.d、将纵向拉伸后的厚片进行横向拉伸,其预热温度为110℃、拉伸温度为128℃、定型温度为248℃,拉伸倍率为3.8。
33.e、将步骤d)中所得薄膜经过自然风冷却,进入牵引系统展平、切边、测厚,然后收卷;经过检测合格后,进行分切、卷取、制成成品。
34.实施例1使用的聚酯抗粘连母料、聚酯抗静电母料、附着力增强改性聚酯母料相同,具体制备方法如下:
35.聚酯抗粘连母料由组分一、组分二两种组分按2:1混合而成;组分一为950千克的对苯二甲酸乙二醇酯和50千克、粒径分布为0.5~1.0μm、平均粒径0.8μm多孔球形二氧化硅,经混合、双螺杆挤出机熔融挤出、切粒;组分二为950千克对苯二甲酸乙二醇酯和50千克、粒径分布为0.3~0.8μm、平均粒径0.5μm无定型二氧化硅,经混合、双螺杆挤出机熔融挤出、切粒。
36.聚酯抗静电母料为300千克的聚噻吩、300千克的聚吡咯、400千克的聚对苯二甲酸乙二醇酯,经混合、双螺杆挤出机熔融挤出、切粒。
37.附着力增强改性聚酯母料的制备方法为:800千克马来酸酐改性支化聚酯、200千克的对苯二甲酸乙二醇酯经混合、双螺杆挤出机熔融挤出、切粒。马来酸酐改性支化聚酯制备过程为:在装有惰性气体的反应釜中,加入800千克的超支化聚酯和200千克的n,n-二甲基甲酰胺,缓慢升温至83℃,支化聚酯完全溶解后,加入50千克的n,n,n-三乙基乙铵溴化物,充分搅拌混合,搅拌时间为2小时,加入600千克的马来酸酐,充分反应8小时后,经水洗、干燥、粉碎。
38.实施例1生产产品主要性能检测如下表:
[0039][0040]
实施例2:
[0041]
实施例2与实施例1的区别在于次表层原料组成不同,具体见下表:
[0042]
实施例2生产产品主要性能检测如下表:
[0043]
[0044][0045]
通过上述数据对比可知,次表层中附着力增强改性聚酯母料的用量会对产品的残余黏着率带来影响,随着附着力增强改性聚酯母料用量的增加,薄膜次表层极性基团增加,与外表层涂布液之间的结合力增加,残余黏着率显著提升。
[0046]
实施例3
[0047]
本实施例与实施例1的区别仅在于制备马来酸酐改性支化聚酯的组分用量不同,具体的原料组成见下表:
[0048][0049]
实施例3生产产品主要性能检测如下表:
[0050][0051]
通过上述数据对比可知,制备马来酸酐改性支化聚酯的原料用量比例不同,会对产品的剥离力和残余黏着率带来影响,这主要是由于随着超支化聚酯和马来酸酐用量的降低,接枝效果减弱,薄膜表面极性基团减少,次表层与外表层之间结合力减弱,剥离力降低,薄膜残余黏着率降低。
[0052]
以上实施例仅用以说明本发明的技术方案,而非对其限制;尽管参照前述实施例对本发明进行了详细的说明,本领域的普通技术人员应当理解:其依然能够对前述各实施例所记载的技术方案进行修改,或者对其中部分技术特征进行等同替换;而这些修改或者替换,并不使相应技术方案的本质脱离本发明各实施例技术方案的精神和范围。