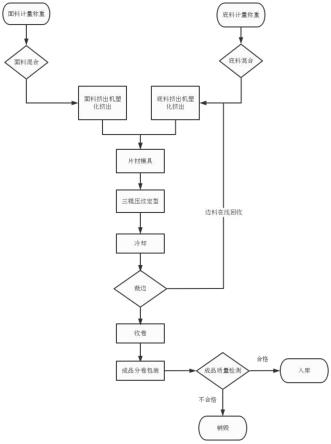
1.本发明属于发泡材料技术领域,具体涉及一种发泡软质材料及其制备方法。
背景技术:2.目前,发泡软质片材主要由压延法和离型纸法生产。压延法主要包括压延发泡层、压延面层、表面处理和发泡炉高温发泡等工艺流程,得到的片材的厚度不超过0.5mm,发泡后单层厚度最大为1mm,更大厚度的产品则需要多层贴合,能耗高,效率低,还会产生大量voc气体。
3.离型纸法是将不同性能的面层和底层配合液利用刮刀涂覆在离型纸上,面料经过干燥和冷却后涂覆粘合层底料,将基材与底料复合,经过干燥和冷却后将片材和离型纸分别成卷。离型纸法生产聚氨酯片材包括干法聚氨酯片材和湿法聚氨酯片材。干法聚氨酯片材是将溶剂型聚氨酯树脂中的溶剂挥发后将得到的多层薄膜加上底布得到的;湿法聚氨酯片材是将溶剂型聚氨酯采用水中成膜法得到的,具有良好的透气性和透湿性。但是,离型纸法生产中使用的多个烘箱的总长度在40~55米,烘箱温度都在180℃以上,同样存在能耗大、成本高和大量voc气体排放的问题。
技术实现要素:4.本发明的目的在于提供一种发泡软质材料及其制备方法,本发明提供的方法能耗小、成本低且voc气体排放少,而且可以采用二次料和回收料,得到的发泡软质材料的综合力学性能良好。
5.为了实现上述目的,本发明提供如下技术方案:
6.本发明提供了一种发泡软质材料的制备方法,包括以下步骤:
7.(1)将树脂、增塑剂、碳酸钙、稳定剂、氧化聚乙烯蜡、硬脂酸、三氧化二锑、抗氧剂、紫外线吸收剂、色料和发泡剂混合,得到底料预混物;
8.(2)将树脂、增塑剂、碳酸钙、稳定剂、氧化聚乙烯蜡、硬脂酸、三氧化二锑、抗氧剂、紫外线吸收剂和色料混合,得到面料预混物;
9.(3)将所述底料预混物和面料预混物双层挤出后冷却定型,得到发泡软质材料;
10.本发明对所述步骤(1)和步骤(2)的先后顺序没有要求。
11.优选的,所述双层挤出包括:将所述底料预混物加入底料挤出机,将所述面料预混物加入面料挤出机,然后共同通过双层挤出模具挤出。
12.优选的,所述面料挤出机设置有5个加热区,按照原料通过的顺序,依次记为a1区、a2区、a3区、a4区和a5区,所述a1~a4区的温度独立地为120~200℃,所述a5区的温度为140~220℃;
13.优选的,所述底料挤出机设置有5个加热区,按照原料通过的顺序,依次记为b1区、b2区、b3区、b4区和b5区,所述b1区~b5区的温度独立地为120~200℃;
14.优选的,所述双层挤出模具设置有10个加热区,按照原料通过的顺序,依次记为c1
区、c2区、c3区、c4区、c5区、c6区、c7区、c8区、c9区和c10区,所述c1区~c10区的温度独立地为120~200℃。
15.优选的,所述步骤(1)和步骤(2)中混合的温度独立地为50~120℃。
16.优选的,所述冷却定型在三辊压光机中进行,所述三辊压光机的下辊温度为15~90℃、中辊温度为15~90℃且上辊温度为15~90℃。
17.优选的,所述底料预混物包括以下质量份数的组分:树脂100份,增塑剂30~100份,碳酸钙10~300份,稳定剂1~8份,氧化聚乙烯蜡0.1~2份,硬脂酸0.1~2份,三氧化二锑0.1~10份,抗氧剂0.1~5份,紫外线吸收剂0.1~5份,色料0.01~10份和发泡剂0.1~10份。
18.优选的,所述面料预混物包括以下质量份数的组分:树脂100份,增塑剂30~100份,碳酸钙10~300份,稳定剂1~10份,氧化聚乙烯蜡0.01~3份,硬脂酸0.1~3份,三氧化二锑0.1~10份,抗氧剂0.1~5份,紫外线吸收剂0.1~5份和色料0.01~10份。
19.优选的,所述底料预混物中的树脂包括pvc、tpo、tpu和tpe中的一种或几种;所述增塑剂包括邻苯二甲酸二(2-丙基庚)酯、dphp、dotp、dinp、dbp和dinch中的一种或几种;所述稳定剂为钙锌稳定剂;所述氧化聚乙烯蜡为高密度氧化聚乙烯蜡;所述抗氧剂为高温抗氧剂;所述紫外线吸收剂为[2-羟基-4-(辛氧基)苯基]苯基酮;所述色料包括塑料用色粉和色母中的一种或几种;所述发泡剂包括化学发泡剂和物理发泡剂中的一种或几种。
[0020]
优选的,所述面料预混物中的树脂、增塑剂、碳酸钙、稳定剂、氧化聚乙烯蜡、硬脂酸、三氧化二锑、抗氧剂、紫外线吸收剂和色料的种类与底料预混物一致。
[0021]
本发明还提供了上述方案所述制备方法得到的发泡软质材料,包括面层和底层,所述面层包括树脂、增塑剂、碳酸钙、稳定剂、氧化聚乙烯蜡、硬脂酸、三氧化二锑、抗氧剂、紫外线吸收剂和色料,所述底层包括树脂、增塑剂、碳酸钙、稳定剂、氧化聚乙烯蜡、硬脂酸、三氧化二锑、抗氧剂、紫外线吸收剂、色料和发泡剂。
[0022]
本发明提供了一种发泡软质材料的制备方法。本发明提供的制备方法采用挤出的方法,通过在底料中加入发泡微球来实现发泡,不用二次加温或高温烘箱发泡定型,能耗低,传统压延工艺用电量14000~16000度/天,燃气用量2000~3500立方米/天,传统离型纸法工艺用电量4000~6000度/天,燃气用量2000~3500立方米/天,而本发明提供的制备方法用电量2000~3000度/天,燃气用量500~800立方米/天,相较于压延工艺能耗降低70%,相较于离型纸工艺能耗降低50%;本发明提供的制备方法采用挤出发泡一次成型,生产效率高,相较于压延工艺效率提高50~70%,相较于离型纸工艺效率提高40~60%;传统压延工艺总投资1500~2000万,传统离型纸法工艺设备总投资600~800万,本发明提供的制备方法设备总投资200~300万,设备投资小,相较于压延工艺减少80%设备投资,相较于离型纸工艺减少50%设备投资;并且,传统工艺采用开放式塑化方法和烘箱二次塑化发泡方法,本发明提供的制备方法塑化发泡均在挤出机内完成,通过挤出和片材模具的各区温度控制发泡效果,不排放voc气体,并且出模具后立即冷却定型,大大减少了voc气体和固废的排放,相较于传统工艺voc气体排放可减少70~80%。本发明提供的制备方法可以用于生产塑料软质发泡片材/卷材/人造革/地板革,比如pvc车用发泡地板革、pvc人造革、pvc发泡地材、pvc运动地板、tpo发泡卷材/片材、tpo发泡车用地板革、tpo发泡地材、tpu人造革、tpu发泡卷材/片材和tpu发泡地材等。
[0023]
本发明还提供了上述方案所述制备方法得到的发泡软质材料,包括面层和底层,所述面层包括树脂、增塑剂、碳酸钙、稳定剂、氧化聚乙烯蜡、硬脂酸、三氧化二锑、抗氧剂、紫外线吸收剂和色料,所述底层包括树脂、增塑剂、碳酸钙、稳定剂、氧化聚乙烯蜡、硬脂酸、三氧化二锑、抗氧剂、紫外线吸收剂、色料和发泡剂。本发明提供的发泡软质材料的面层为耐磨层,未经发泡,结构密实,具有很好的耐磨性能;底层为发泡层,通过加入微球发泡剂,并控制微球发泡剂的用量来调整发泡倍率,具有良好的弹性和吸音效果。本发明得到的发泡软质材料强度高,拉伸延长率高,耐磨性良好,综合力学性能优异,其纵向和横向拉伸强度均大于300n,纵向和横向直角撕裂强度均大于120n,纵向和横向剥离强度均大于45n,邵氏硬度大于55n,纵向和横向拉伸延长率均大于230%,并且耐低温性能优异,耐摩擦色牢度高,成本低廉,具有广泛的应用前景。
附图说明
[0024]
为了更清楚地说明本发明实施例或现有技术中的技术方案,下面将对实施例中所需要使用的附图作简单地介绍,显而易见地,下面描述中的附图仅仅是本发明的一些实施例,对于本领域普通技术人员来讲,在不付出创造性劳动性的前提下,还可以根据这些附图获得其他的附图。
[0025]
图1为本发明的发泡软质材料的制备流程图。
具体实施方式
[0026]
本发明提供了一种发泡软质材料的制备方法,包括以下步骤:
[0027]
(1)将树脂、增塑剂、碳酸钙、稳定剂、氧化聚乙烯蜡、硬脂酸、三氧化二锑、抗氧剂、紫外线吸收剂、色料和发泡剂混合,得到底料预混物;
[0028]
(2)将树脂、增塑剂、碳酸钙、稳定剂、氧化聚乙烯蜡、硬脂酸、三氧化二锑、抗氧剂、紫外线吸收剂和色料混合,得到面料预混物;
[0029]
(3)将所述底料预混物和面料预混物双层挤出后冷却定型,得到发泡软质材料;
[0030]
本发明对所述步骤(1)和步骤(2)的先后顺序没有要求。
[0031]
本发明将树脂、增塑剂、碳酸钙、稳定剂、氧化聚乙烯蜡、硬脂酸、三氧化二锑、抗氧剂、紫外线吸收剂、色料和发泡剂混合,得到底料预混物。在本发明中,所述树脂优选包括pvc、tpo、tpu和tpe中的一种或几种;所述pvc优选为pvc sg3;所述增塑剂包括邻苯二甲酸二(2-丙基庚)酯、dphp、dotp、dinp、dbp和dinch中的一种或几种;所述碳酸钙的粒径优选为200~50000目,更优选为1000~30000目,进一步优选为5000~10000目;所述稳定剂优选为钙锌稳定剂;所述钙锌稳定剂优选为9106稳定剂;所述氧化聚乙烯蜡优选为高密度氧化聚乙烯蜡;所述高密度氧化聚乙烯蜡优选为316a氧化聚乙烯蜡;所述抗氧剂优选为抗氧剂pep-8t;所述紫外线吸收剂优选为[2-羟基-4-(辛氧基)苯基]苯基酮;所述色料优选包括塑料用色粉和色母中的一种或几种;所述发泡剂优选包括化学发泡剂和物理发泡剂中的一种或几种;所述物理发泡剂优选为可膨胀微球发泡剂;所述化学发泡剂优选为ac-13型发泡剂;
[0032]
按质量份数计,本发明中所述底料预混物优选包括树脂100份,增塑剂30~100份,更优选为40~80份,进一步优选为50~70份,碳酸钙10~300份,更优选为50~250份,进一
步优选为100~200份,稳定剂1~8份,更优选为2~7份,进一步优选为3~5份,氧化聚乙烯蜡0.1~2份,更优选为0.5~1.5份,进一步优选为0.7~1.2份,硬脂酸0.1~2份,更优选为0.5~1.5份,进一步优选为0.8~1.3份,三氧化二锑0.1~10份,更优选为1~7份,进一步优选为3~6份,抗氧剂0.1~5份,更优选为0.5~3份,进一步优选为1~2份,紫外线吸收剂0.1~5份,更优选为0.5~4份,进一步优选为1~3份,色料0.01~10份,更优选为1~8份,进一步优选为3~7份,以及发泡剂0.1~10份,更优选为1~6份,进一步优选为5~6份。本发明提供的制备方法也可以采用二次料、回收料和本发明生产中产生的的边料和废料,很大程度上避免材料的浪费,实现生产成本的进一步降低。
[0033]
在本发明中,步骤(1)中所述混合的温度优选为50~120℃,更优选为70~100℃,进一步优选为80~90℃;所述混合的装置优选为高混机;所述高混机的速率优选为1200~1600r/min,更优选为1300~1500r/min,进一步优选为1350~1450r/min。
[0034]
本发明将树脂、增塑剂、碳酸钙、稳定剂、氧化聚乙烯蜡、硬脂酸、三氧化二锑、抗氧剂、紫外线吸收剂和色料混合,得到面料预混物。在本发明中,所述面料预混物中的树脂、增塑剂、碳酸钙、稳定剂、氧化聚乙烯蜡、硬脂酸、三氧化二锑、抗氧剂、紫外线吸收剂和色料的种类与底料预混物一致。按质量份数计,本发明中所述面料预混物优选包括以下质量份数的组分:树脂100份,增塑剂30~100份,更优选为40~80份,进一步优选为50~70份,碳酸钙10~300份,更优选为50~250份,进一步优选为100~200份,稳定剂1~10份,更优选为2~8份,进一步优选为3~6份,氧化聚乙烯蜡0.01~3份,更优选为0.1~2份,进一步优选为0.8~1.5份,硬脂酸0.1~3份,更优选为0.5~2.2份,进一步优选为0.8~1.5份,三氧化二锑0.1~10份,更优选为1~7份,进一步优选为3~6份,抗氧剂0.1~5份,更优选为0.5~3份,进一步优选为1~2份,紫外线吸收剂0.1~5份,更优选为0.5~4份,进一步优选为1~3份,色料0.01~10份,更优选为0.1~8份,进一步优选为1~6份,以及发泡剂0.1~10份,更优选为1~6份,进一步优选为4~6份。
[0035]
在本发明中,步骤(2)中所述混合的温度优选为50~120℃,更优选为60~110℃,进一步优选为80~100℃;所述混合的装置优选为高混机;所述高混机的速率优选为1200~1600r/min,更优选为1250~1500r/min,进一步优选为1300~1400r/min。
[0036]
得到底料预混物和面料预混物后,本发明将所述底料预混物和面料预混物双层挤出后冷却定型,得到发泡软质材料。在本发明中,所述双层挤出优选包括:将所述底料预混物加入底料挤出机,将所述面料预混物加入面料挤出机,然后共同通过双层挤出模具挤出;所述双层挤出模具优选为衣架式片材模具;所述底料预混物和面料预混物进入双层挤出模具前,本发明优选通过分配器对底料预混物和面料预混物的熔体比例进行分配,控制发泡软质材料的面层和底层的厚度比例;所述底料预混物和面料预混物的溶体比例和所述发泡软质材料的面层和底层的厚度比例控制为2:8。
[0037]
在本发明中,所述面料挤出机优选设置有5个加热区,按照原料通过的顺序,依次记为a1区、a2区、a3区、a4区和a5区,所述a1区的温度优选为120~200℃,更优选为140~180℃,进一步优选为150~170℃;所述a2区的温度优选为120~200℃,更优选为140~200℃,进一步优选为160~180℃;所述a3区的温度优选为140~200℃,更优选为150~190℃,进一步优选为160~178℃;所述a4区的温度优选为140~200℃,更优选为160~200℃,进一步优选为170~180℃;所述a5区的温度优选为140~200℃,更优选为150~200℃,进一步优选为
170~190℃。
[0038]
在本发明中,所述底料挤出机优选设置有5个加热区,按照原料通过的顺序,依次记为b1区、b2区、b3区、b4区和b5区,所述b1区的温度优选为120~200℃,更优选为160~200℃,进一步优选为170~185℃;所述b2区的温度优选为120~200℃,更优选为160~190℃,进一步优选为170~180℃;所述b3区的温度优选为120~200℃,更优选为165~200℃,进一步优选为175~190℃;所述b4区的温度优选为120~200℃,更优选为155~195℃,进一步优选为17~185℃;所述b5区的温度优选为120~200℃,更优选为175~200℃,进一步优选为185~195℃。
[0039]
在本发明中,所述双层挤出模具优选设置有10个加热区,按照原料通过的顺序,依次记为c1区、c2区、c3区、c4区、c5区、c6区、c7区、c8区、c9区和c10区,所述c1区~c10区的温度独立地优选为120~200℃;具体的,所述c1区的温度优选为120~200℃,更优选为155~195℃,进一步优选为170~180℃;所述c2区的温度优选为120~200℃,更优选为155~200℃,进一步优选为185~195℃;所述c3区的温度优选为120~200℃,更优选为155~200℃,进一步优选为185~200℃;所述c4区的温度优选为120~200℃,更优选为165~200℃,进一步优选为185~200℃;所述c5区的温度优选为120~200℃,更优选为165~200℃,进一步优选为190~200℃;所述c6区的温度优选为120~200℃,更优选为175~195℃,进一步优选为180~190℃;所述c7区的温度优选为120~200℃,更优选为170~195℃,进一步优选为180~190℃;所述c8区的温度优选为120~200℃,更优选为165~195℃,进一步优选为175~190℃;所述c9区的温度优选为120~200℃,更优选为165~190℃,进一步优选为175~185℃;所述c10区的温度优选为120~200℃,更优选为160~190℃,进一步优选为170~180℃。
[0040]
在本发明中,所述压纹优选在三辊机中进行;所述三辊机的下辊温度优选为15~90℃,更优选为30~80℃,进一步优选为50~60℃;所述三辊机的中辊温度优选为15~90℃,更优选为35~65℃,进一步优选为45~55℃;所述三辊机的上辊温度优选为15~90℃,更优选为30~70℃,进一步优选为40~60℃。在本发明中,所述冷却定型优选为自然冷却;所述冷却定型的终温优选为常温;所述冷却定型的时间优选为1~2min,更优选为1~1.5min,进一步优选为1min。在本发明中,所述冷却定型前优选进行压纹。在本发明中,所述冷却定型后优选对得到的发泡软质材料进行裁边,裁边后收卷和分切,最后入库。本发明优选将裁边得到的边料粉碎后风送到下料口回收使用。
[0041]
本发明还提供了上述方案所述制备方法得到的发泡软质材料,包括面层和底层,所述面层包括树脂、增塑剂、碳酸钙、稳定剂、氧化聚乙烯蜡、硬脂酸、三氧化二锑、抗氧剂、紫外线吸收剂和色料,所述底层包括树脂、增塑剂、碳酸钙、稳定剂、氧化聚乙烯蜡、硬脂酸、三氧化二锑、抗氧剂、紫外线吸收剂、色料和发泡剂。在本发明中,所述面层的厚度优选为0.1~2mm,更优选为1~2mm,进一步优选为1.5~2mm;所述底层的厚度优选为0.8~3mm,更优选为2~3mm,进一步优选为2.5~3mm。
[0042]
为了进一步说明本发明,下面结合附图和实施例对本发明提供的技术方案进行详细地描述,但不能将它们理解为对本发明保护范围的限定。
[0043]
图1为本发明的发泡软质材料的制备流程图,具体的制备流程包括:将底料和面料分别计量称重和混合,然后将底料预混料和面料预混料分别加入底料挤出机和面料挤出机塑化挤出进入片材模具,再依次进行三辊压纹定型和冷却,将得到的材料进行裁边和收卷,
并将裁边产生的边料在线回收,然后将成品分卷包装,最后进行成品质量检测,将合格的产品入库,不合格的产品销毁。
[0044]
实施例1
[0045]
材料配比:以重量份计,底料的组分为:pvc树脂100份,增塑剂邻苯二甲酸二(2-丙基庚)酯70份,碳酸钙150份,9106稳定剂3份,316a氧化聚乙烯蜡0.12份,硬脂酸0.15份,三氧化二锑1份,抗氧剂pep-8t 0.3份,[2-羟基-4-(辛氧基)苯基]苯基酮0.3份,色母2份,ac-13发泡剂3.6份;
[0046]
以重量份计,面料的组分为:pvc树脂100份,增塑剂邻苯二甲酸二(2-丙基庚)酯70份,碳酸钙40份,9106稳定剂3份,316a氧化聚乙烯蜡0.12份,硬脂酸0.15份,三氧化二锑1份,抗氧剂pep-8t 0.3份,[2-羟基-4-(辛氧基)苯基]苯基酮0.3份,色母2份;
[0047]
发泡软质材料的制备:(1)按照配比计量称重底料和面料,利用底料混合机混合底料,混合温度为105℃,得到底料预混物,面料混合机混合面料,混合温度为105℃,得到面料预混物;
[0048]
(2)将底料预混物加入底料挤出机,面料挤出机设置有5个加热区,1区的温度为150℃,2区的温度为170℃,3区的温度为190℃,4区的温度为160℃,5区的温度为160℃;
[0049]
将面料预混物加入面料挤出机,底料挤出机设置有8个加热区,1区的温度为170℃,2区的温度为190℃,3区的温度为180℃,4区的温度为180℃,5区的温度为180℃;
[0050]
(3)将底料预混物和面料预混物通过双层挤出模具双层挤出,双层挤出模具设置有10个加热区,1区的温度为190℃,2区的温度为190℃,3区的温度为200℃,4区的温度为190℃,5区的温度为190℃,6区的温度为200℃,7区的温度为200℃,8区的温度为200℃,9区的温度为200℃,10区的温度为200℃;
[0051]
(4)出模具后进入三辊机压纹,冷却定型,三辊机的下辊温度为90℃,中辊温度为90℃,上辊温度为80℃;
[0052]
(5)冷却架冷却1min,冷却到常温后裁边,收卷;
[0053]
(6)分切,检验入库,得到发泡软质材料。
[0054]
利用wdw-10微机控制电子式万能试验机和111n-101-40数显绝对原点卡尺对实施例1的发泡软质材料的拉伸强度进行检测,测试方法为gb/t 1040.3-2006,标距25mm,测试速度100mm/min。测试结果显示,实施例1的发泡软质材料的纵向拉伸强度为320.4n,横向拉伸强度为305.8n。
[0055]
利用wdw-10微机控制电子式万能试验机和111n-101-40数显绝对原点卡尺对实施例1的发泡软质材料的拉伸延伸率进行检测,测试方法为gb/t 1040.3-2006,标距25mm,测试速度100mm/min。测试结果显示,实施例1的发泡软质材料的纵向拉伸延伸率为242%,横向拉伸延伸率为232%。
[0056]
利用wdw-10微机控制电子式万能试验机和111n-101-40数显绝对原点卡尺对实施例1的发泡软质材料的直角撕裂强度进行检测,测试方法为gb/t 529-2008,试样形状为直角无割口,测试速度500mm/min。测试结果显示,实施例1的发泡软质材料的纵向直角撕裂强度为123n,横向直角撕裂强度为121n。
[0057]
利用wdw-10微机控制电子式万能试验机和111n-101-40数显绝对原点卡尺对实施例1的发泡软质材料的剥离强力进行检测,测试方法为gb 8808-1988,试样宽度为30mm,测
试速度200mm/min,剥离角度为180
°
。测试结果显示,实施例1的发泡软质材料的纵向剥离强力为45.9n,横向剥离强力为52.0n。
[0058]
利用ygd-5135taber耐磨试验机对实施例1的发泡软质材料的耐磨性进行检测,测试方法为qb/t 2726-2005(2017),载荷1000g,磨轮型号为cs-10,转速60r/min,转数为500转。测试结果显示,实施例1的发泡软质材料无可视发泡破洞现象。
[0059]
利用lx-a型邵氏硬度计对实施例1的发泡软质材料的邵氏硬度进行检测,测试方法为gb/t 2411-2008,试样厚度为4.10mm,读数时间为15s,层叠数为2层。测试结果显示,实施例1的发泡软质材料的邵氏硬度为a/15:69,不低于55度。
[0060]
利用h-ht-1000lsh可程式恒温恒湿试验机和0-1.50m直尺对实施例1的发泡软质材料进行低温落球冲击测试,将发泡软质材料样品在-40℃下低温处理24h,落球重量为500g,落球直径为50mm,冲击高度为230mm。测试结果显示,实施例1的发泡软质材料的表面无可视开裂或发白等影响产品外观质量的缺陷。
[0061]
利用james h.heal 864马丁代尔耐磨仪对实施例1的发泡软质材料进行耐磨擦色牢度测试,测试方法为qc/t 216-1996第6.9节,测试压力为9.8n,摩擦介质为纯棉衬衫布,循环1000次。测试结果显示,实施例1的发泡软质材料的褪色等级为4~5级,沾色等级为4~5级。
[0062]
由以上实施例可知,本发明提供的制备方法步骤简单,便于操作,不用二次加温发泡或高温烘箱发泡定型,大大减少了能耗,并且一次挤出成型,大大提高了生产效率,生产原料的塑化在挤出机进行,并且通过模具挤出后马上冷却定型,大大减少了voc气体的产生和排放。本发明得到的发泡软质材料强度高,拉伸延长率高,耐磨性良好,硬度大,耐低温性能优异,耐摩擦色牢度高,综合力学性能优异。
[0063]
尽管上述实施例对本发明做出了详尽的描述,但它仅仅是本发明一部分实施例,而不是全部实施例,还可以根据本实施例在不经创造性前提下获得其他实施例,这些实施例都属于本发明保护范围。